
УМК МАХП - 2 ч. Жаркова, Митинов
.pdf
К пневмосмесителям относятся аппараты, в которых смешение осу- ществляется в слое псевдоожиженного газом (например, воздухом) зерни- стого материала. Такие аппараты отличаются высокой эффективностью и малым временем смешения, отсутствием вращающихся деталей, но требу- ют установки пылеулавливающих устройств при смешении тонкодисперс- ных материалов.
14.6. Ленточные смесители
Ленточные смесители предназначены для смешения сыпучих мате- риалов насыпной плотностью не более 1 500 кг/м3, а также сыпучих мате- риалов с небольшим количеством жидких компонентов, вводимых в рас- пыленном состоянии, с получением готового продукта в виде сыпучей
смеси. |
|
|
|
|
|
|
Лопастным |
рабочим |
|
||
органом (рис. 14.6) ленточ- |
|
||||
ного |
смесителя |
является |
|
||
вращающийся |
в |
цилиндри- |
|
||
ческом или корытообразном |
|
||||
корпусе вал, на котором |
|
||||
смонтированы |
стержни 1 |
с |
Лопастной вал ленточного смесителя: |
||
|
|
|
|
Рис. 14.6. |
|
укрепленными на их верши- |
1 – стержень; 2 – лента |
||||
|
|
|
|
2, |
|
нах |
плоскими |
лентами |
|
изогнутыми по винтовым линиям. В ряде случаев корпус ленточного сме- сителя снабжают рубашкой для обогрева или охлаждения перемешиваемой массы. Смешение в таких аппаратах нередко совмещают с другими техно- логическими операциями (например, с подсушкой материала), присоеди- няя корпус смесителя к источнику вакуума.
Тема 15 СМЕСИТЕЛИ ДЛЯ ПАСТООБРАЗНЫХ МАТЕРИАЛОВ
Пастообразные материалы характеризуются очень высокой вязко- стью, в связи с чем основным требованием к таким смесителям является обеспечение рационального движения перемешиваемой массы. Этому тре- бованию в значительной мере отвечают двухроторные смесители с рабо- чими органами Z-образной формы, размещенными в горизонтальной сме- сительной камере. Отечественной промышленностью и иностранными
171

фирмами выпускается много типоразмеров таких смесителей, наиболее универсальных для паст различной вязкости. Фактически они могут ре- шить практически любую технологическую задачу.
15.1. Смесители с Z-образными лопастями
Такие смесители предназначены для приготовления пастообразных смесей с динамической вязкостью 200·105 Па·с.
Смеситель (рис. 15.1) представляет собой смесительную камеру 1 корытообразной формы с рубашкой 4 для нагрева или охлаждения смеси. Внутри смесительной камеры размещены два ротора 3 с Z-образными ло- пастями, у которых различные частота и направление вращения. Быстро- ходный ротор получает вращение от мотор-редуктора 9 через цепную пе- редачу 10 либо от электродвигателя через редуктор и муфту. Частота вра- щения быстроходного ротора колеблется от 32 до 60 об/мин.
Рис. 15.1. Смеситель периодического действия с Z-образными лопастями
Исходный материал загружают в смесительную камеру через шар- нирно прикрепленную к корпусу крышку 2 либо через штуцер в крышке. Степень заполнения смесительной камеры достигает 60 – 70 % ее номи- нального объема. Выгрузка продукта осуществляется через те же устрой- ства при опрокидывании смесительной камеры. Угол опрокидывания со- ставляет 110°. Для смесителей объемом 0,01 и 0,025 м3 опрокидывание производится с помощью червячного механизма 11 посредством рукоятки
172

12. В смесителях большего объема для опрокидывания используется гид- равлический механизм. Все узлы смонтированы на станине 8, устанавли- ваемой на фундаменте. Подвод и отвод теплоносителя происходит по гиб- ким шлангам через штуцеры 6 и 7.
В результате усовершенствования смесителей были созданы новые конструкции, в частности, снабженные дополнительным рабочим органом
– шнеком, выполняющим после завершения смешения роль разгрузочного механизма.
15.2. Планетарно-лопастные смесители
Планетарно-лопастные смесители используются для приготовления легкоподвижных пастообразных смесей с вязкостью не более 50 – 200 Па·с.
Рис. 15.2. Планетарно-лопастной смеситель
Смеситель (рис. 15.2) состоит из смесительной камеры 1 с затвором 10 для выгрузки готовой смеси, мешалок 9, планетарной зубчатой передачи 4, а также штуцеров 2 и 3 для загрузки сыпучих и жидких компонентов. Мешалки вращаются вокруг собственной оси с частотой 104 – 84 об/мин и вокруг оси смесительной камеры с частотой 55 – 36 об/мин. Привод меша- лок закреплен на верхней плите 6, которая может подниматься и опускаться.
Механизм подъема размещен в стойке 5. Привод механизма подъема осуществляется от электродвигателя через редуктор, которые установлены на станине 8 и заключены в кожух 7.
173

15.3. Смесители непрерывного действия для пастообразных материалов
В химических производствах и в других отраслях промышленности они составляют небольшую часть общего объема выпуска всех типов сме- сителей. На рис. 15.3 представлен смеситель непрерывного действия типа СНД-1500 (производительностью 1 500 кг/ч), предназначенный для приго- товления пастообразных смесей вязкостью 200·105 Па·с.
Рис. 15.3. Смеситель непрерывного действия
Смеситель состоит из смесительной камеры 6 корытообразной фор- мы с рубашкой. Внутри смесительной камеры размещены два ротора 5, представляющих собой валы с закрепленными на них лопастями 4. Все уз- лы смонтированы на раме 8. Частота вращения роторов составляет 21 об/мин. Их привод осуществляется от электродвигателя 1 через редук- тор 2 и муфту. На плоской крышке 7 расположены технологические шту- церы, в том числе штуцер 3 для загрузки материала. Выгрузка материала осуществляется через окно в торцовой стенке корпуса.
174
МЕТОДИЧЕСКИЕ УКАЗАНИЯ К ЛАБОРАТОРНЫМ РАБОТАМ
Лабораторная работа № 1 ОБОРУДОВАНИЕ ДЛЯ ПЕРЕРАБОТКИ ПОЛИМЕРОВ
ПРЕССОВАНИЕМ
Цель работы: изучение конструкции колонного пресса и техноло- гии переработки полимеров методом прессования.
Общие сведения
Прессование – способ получения изделий из полимеров в замкну- той форме с фиксацией геометрических размеров охлаждением (термо- пласты) или отверждением (термореактопласты). Обычно готовое изде- лие получается в одну стадию прессования (прямое или компрессион- ное). Однако существуют способы прессования, когда требуются и до- полнительные стадии (спекание или вспенивание).
Исторически прессование было одним из первых способов перера- ботки полимеров, но в настоящее время оно практически вытеснено из технологии полимеров более производительными методами и сохрани- лось лишь там, где его пока заменить не удалось. Значительный удель- ный вес прессования можно отметить в технологии резиновых техниче- ских изделий, в технологии термореактопластов (древесных пластиков) и в технологии фторопластов. Политетрафторэтилен – практически единст- венный термопласт, переработка которого вследствие его особенностей ведется методом прессования.
Для реализации процесса прессования необходимо соответствую- щее оборудование: пресс и инструментальная оснастка – пресс-формы. Прессы могут иметь конструктивные различия. По типу станины прессы делятся на колонные, рамные и челюстные. По виду привода – на меха- нические, гидромеханические и гидравлические.
Наибольшее распространение в технологии полимеров получили колонные и рамные гидравлические прессы. Их достоинством является возможность определять и в широких пределах регулировать усилие прессования, величину и скорость рабочего хода. В гидравлических прес- сах обеспечивается независимость величины усилия прессования от хода пресса, отсутствует жесткая связь пресса с приводом.
175
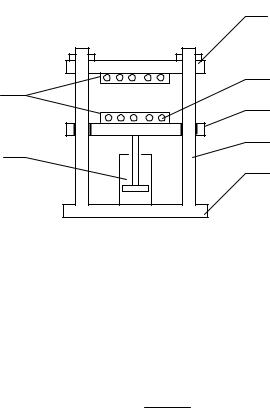
Основными частями гидравлического пресса являются: станина; ра- бочие, возвратные и выталкивающие цилиндры и плунжеры; подвижные и неподвижные плиты. Гидравлические прессы делятся на прессы с верхним и нижним расположением рабочего цилиндра. Прессы с верхним распо- ложением рабочего цилиндра преимущественно применяются для перера- ботки термореактивных пластмасс. Прессы с нижним расположением ра- бочего цилиндра в основном применяются для прессования слоистых пла- стиков (этажные прессы) и резиновых изделий в съемных пресс-формах.
Для обеспечения работы гидравлического пресса необходимо нали- чие гидродвигателя, распределителей жидкости и трубопроводов.
На рис. 1 показана схема гидравлического пресса. Жидкость под давлением поступает от насоса или насосно-аккумуляторной станции в рабочий цилиндр. Давление жидкости распространяется во все стороны равномерно. Давление, действующее на стенку цилиндра, должно учиты- ваться при его прочностном расчете. На плунжер и на дно цилиндра дей- ствуют силы, равные по величине и противоположные по направлению.
Рис.1. Гидравлический пресс:
1 – станина; 2 – неподвижная плита; 3 – подвижная плита; 4 – гидроцилиндр; 5 – прессформа; 6 – обогрев; 7 – колонны
Основным параметром, используемым для характеристики пресса, является номинальное усилие прессования Fн
Fн = pн × π× D2 , 4
где pн – номинальное давление рабочей жидкости;
D – диаметр поршня гидроцилиндра.
Расчетное усилие для колонн Fк , Н:
176

Fк = K × Fн , n
где K – коэффициент, учитывающий предварительную затяжку гаек колонны; K = 1,15 ÷1,25 . Меньшее значение следует принимать для тихо- ходных прессов большого усилия, большие значения – для быстроходных прессов небольшого усилия;
n – количество колонн.
Расчетным сечением колонны является сечение по резьбе. Внут- ренний диаметр резьбы колонны d0
d0 = |
|
4 × Fк |
|
, |
|
||||
|
|
π ×[σP ] |
где [σP ] – допускаемое напряжение, МПа; для стали марки Ст5 реко-
мендуется принимать [σP ] =100 МПа.
Расчет производится по следующей методике: устанавливаются ис- ходные данные для расчета; рассчитывается давление в цилиндре; опре- деляется усилие пресса Р, Н, при максимальной мощности.
Технология прессования зависит от типа перерабатываемого поли- мера. Так, для термопластов необходимо осуществлять формообразова- ние при температуре выше температуры плавления, а фиксацию формы – охлаждением. Для реактопластов охлаждение не требуется. Некоторые полимеры перерабатывают холодным прессованием с последующим спе- канием. При этом формование изделий из порошкообразных полимерных материалов осуществляется путем прессования при температуре ниже температуры текучести полимеров с последующим нагревом до сплавле- ния в монолит.
Этот способ пригоден для переработки любых термопластов, но в промышленности применяется только для изготовления изделий из поли- тетрафторэтилена. Переработка в вязко-текучем состоянии политетрафто- рэтилена невозможна из-за очень узкого температурного интервала между температурой плавления и температурой деструкции. Для других полиме- ров, не имеющих ограничений на более дешевую переработку в вязко- текучем состоянии, способ прессования применяется в случаях, когда тре- буется получить уникальное по свойствам (например, открыто-пористое) изделие. Для изготовления изделий сложной формы из порошкообразных полимеров возможно использование механической обработки заготовок.
Технология прямого прессования термореактивных материалов включает стадии подготовки и дозировки сырья, формования с отвержде- нием, механической обработки и контроля деталей.
177
Оборудование и материалы: лабораторный пресс; пресс-формы; набор полимеров.
Порядок выполнения работы
1.Выбрать материал для изготовления предложенного изделия.
2.Подготовить пресс-форму и установить ее на прессе.
3.Сделать навески кондиционированного полимера.
4.Выбрать режим прессования и отпрессовать изделие.
5.Выполнить прочностные расчеты деталей пресса.
6.Сделать вывод о правильности выбранного технологического режима прессования и возможности использования лаборатор- ного пресса для выполнения задания.
Содержание отчета
Название и цель работы. Краткие сведения об оборудовании для прессования полимеров. Расчеты производительности пресса. Выбран- ный технологический режим прессования. Выводы.
Контрольные вопросы
1.Какие способы прессования полимеров Вам известны? Оха- рактеризуйте их.
2.Дайте определение метода прямого прессования.
3.Назовите конструктивные элементы колонного пресса.
4.Перечислите основные параметры процесса прессования.
5.Опишите известные вам способы обогрева пресс-форм.
Литература
1.Практикум по технологии переработки пластических масс / под ред. В.М. Ви- ноградова, Г.С. Головкина. – М.: Химия, 1980.
2.Калинчев, Э.Л. Выбор пластмасс для изготовления и эксплуатации изделий: справ. пособие / Э.Л. Калинчев, М.Б. Саковцева. – Л.: Химия, 1987. – 416 с.
Лабораторная работа № 2 ПЕРЕРАБОТКА ТЕРМОПЛАСТОВ ЛИТЬЕМ ПОД ДАВЛЕНИЕМ
Цель работы: изучение оборудования и технологии литья под дав- лением термопластов. Определение влияния технологических параметров литья на качество изделий из термопластов.
178

Общие сведения
Литье под давлением – один из прогрессивных современных спо- собов переработки пластических масс в изделия. В настоящее время наи- большее распространение получили литьевые машины с червячной пла- стикацией. Однако в мелкосерийном производстве для изготовления не- больших изделий в отдельных случаях применяют механические и гид- равлические плунжерные литьевые машины.
Литьевая машина должна обеспечить нагрев материала до перехода его в вязко-текучее состояние, подачу определенной дозы расплава под давлением в охлаждаемую форму, смыкание и размыкание формы. Все основные технологические параметры процесса литья должны иметь возможность плавного и точного регулирования. Для достижения наи- высшей производительности процесс получения изделий на литьевой машине должен быть полностью автоматизирован, машина – снабжена блокирующими устройствами, предохраняющими ее от поломки и обес- печивающими безопасность обслуживания.
Современная литьевая машина состоит из двух основных частей: инжекционного узла, предназначенного для разогрева и последующего впрыска расплавленного материала через мундштук в литьевую форму, и узла смыкания (или прессовой части), предназначенного для закрытия и открытия формы, противодействия усилиям, возникающим в ней при формовании изделий, и извлечения изделий из формы.
На рис. 2 представлена схема термопластавтомата с червячной пла- стикацией.
Рис. 2. Схема термопластавтомата с червячной пластикацией:
1 – гидравлический цилиндр узла смыкания; 2 – рычажное устройство; 3 – ма- териальный цилиндр; 4 – шнек; 5 – привод вращения; 6 – цилиндр гидропровода узла впрыска; 7 – загрузочное устройство; 8 – мундштук; 9 – литьевая форма; 10 – деталь
179
Инжекционный узел машины состоит из цилиндра 3 с обогревом и червяка 4. Червяк совершает вращательное и поступательное движение. Во вращение червяк приводится гидромотором 5. Поступательное дви- жение червяку сообщается от цилиндра 6 узла впрыска.
Узел смыкания с гидромеханическим приводом состоит из гид- равлического цилиндра 1 с поршнем и передаточного рычажного уст- ройства 2. При движении поршня вправо рычаги выпрямляются, и промежуточная плита вместе с соединенной с ней подвижной плитой быстро перемещаются вправо.
По компоновке основных частей литьевые машины бывают гори- зонтальные, вертикальные, угловые. Большинство современных машин выполняют по горизонтальной схеме, так как она обеспечивает наилуч- шие условия для автоматизации процесса литья.
При работе термопластавтомата материал загружают в бункер. Для повышения качества изделий и производительности машины перераба- тываемый материал предварительно просушивают в специальных су- шильных шкафах или непосредственно в бункере машины горячим воз- духом или с помощью электронагревателей. Это особенно необходимо для материалов, обладающих повышенной гигроскопичностью, таких как полиамиды и поликарбонаты. Материал из загрузочного бункера забира- ется вращающимся червяком при одновременном отводе его назад. Не- обходимая для впрыска доза расплавленного материала накапливается между мундштуком 8 и наконечником червяка. Регулируя величину от- вода червяка, устанавливают необходимую объемную дозу впрыска. Ма- териальный цилиндр во всех схемах термопластавтоматов обогревается электронагревательными элементами сопротивления и имеет, как прави- ло, несколько регулируемых зон нагрева. В каждой зоне вмонтирован термодатчик, соединенный с термореле и показывающим прибором, с помощью которых устанавливают и поддерживают заданную температу- ру в цилиндре.
В резьбовом гнезде материального цилиндра закрепляется мунд- штук, через который расплавленный материал под давлением подается в формующую полость формы 9. Впрыск расплава в форму осуществляется червяком, который работает в момент впрыска как поршень и приводится в поступательное движение на гидравлических машинах от гидроцилин- дра. В литьевую форму расплав впрыскивается под большим давлением, величина которого зависит от свойств материала, степени его предвари- тельной пластикации, температуры, а также от конструкции изделия. Это давление может находиться в пределах 60 – 200 МПа. Впрыснутый под высоким давлением расплав стремится разомкнуть литьевую форму, за-
180