
Процессы формообразования и инструментальная техника - курсовая работа
.pdf
|
10 c |
p |
t x s y |
Bu z |
|
Pz |
|
z |
|
KMp ; [стм, с.282], где |
|
|
|
Dq nw |
|
||
|
|
|
|
|
КМр – поправочный коэффициент, учитывающий влияние качества обрабатываемого материала на силовые зависимости
|
|
|
|
в |
n |
|||
K |
|
|
|
; n = 0,3 [стм, с.264, табл.9] |
||||
Mp |
|
|
|
|||||
|
750 |
|
||||||
|
|
|||||||
|
|
410 |
|
0,3 |
||||
K Mp |
|
|
|
|
|
|
0,83; |
|
|
|
|
|
|||||
|
|
750 |
|
|
Cр = 68,2; x = 0,86; y = 0,72; u = 1,0; q = 0,86; w =0. [стм, с.291, табл.41]
Pz 10 68,2 20,86 0,050,72 41,0 5 0,83 445,9Н ; 140,86 10000
P |
445,9 44 |
0,32кВт; |
|
|
|||
рез |
1020 |
60 |
|
|
|
Pдв 2,2 0,8 1,76кВт;
0,32 кВт < 1,76 кВт => мощность привода обеспечивает мощность назначенного режима резания.
6. Расчет машинного времени:
Т 0 Lр.х. i; где
VS
Lр.х. – длина рабочего хода инструмента;
i – число рабочих ходов; i = 2; Lр.х. = l1 + lд + l2;
l1 + l2 = 10 мм; [обработка металлов резанием, с.623, табл.7]
Lр.х. = 15 + 10 = 20 мм;
Т |
|
|
25 |
3 0,3 мин. |
|
|
0 |
|
|
|
|||
|
250 |
|
|
|
||
|
|
|
|
|
||
|
|
|
|
|
|
Лист |
|
|
|
|
|
МСиИ.2012.ПФиИТ.КР.11.ПЗ |
21 |
Изм. Лист № докум. |
Подпись Дата |
|
||||
|
|
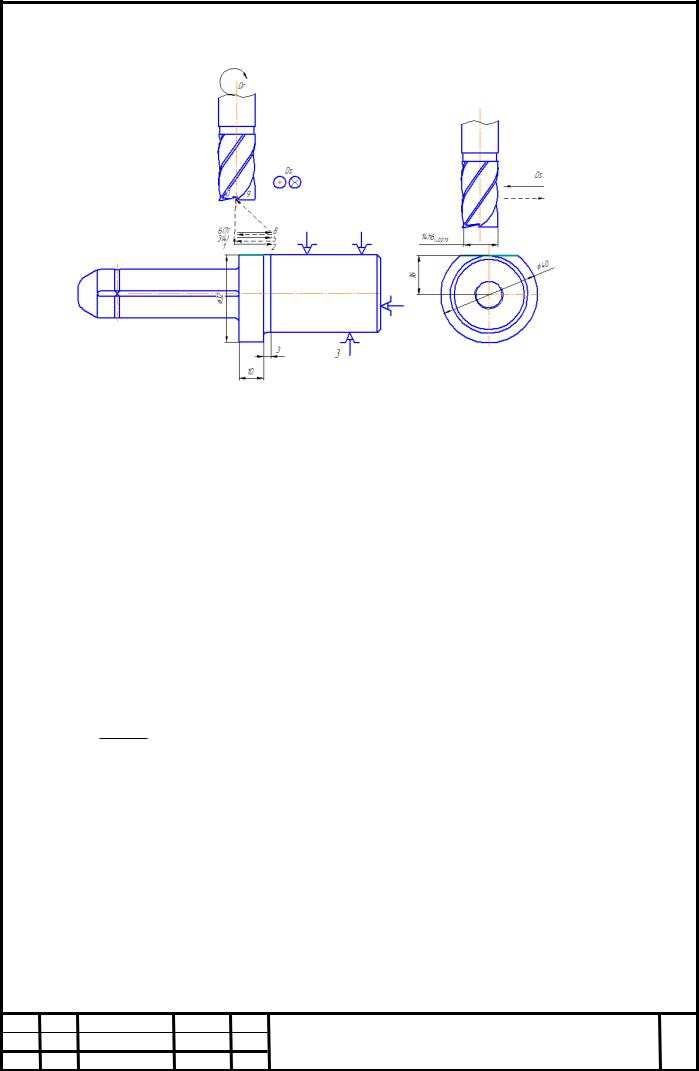
Рис. 4 Эскиз фрезерования лыски концевой фрезой
6.2 Назначение режимов резания на для нарезания внутренней резьбы
М12-6Н
Назначение параметров режима резания: 1. Подача
SР 1,75мм
2.Скорость резания :
C D q
v v Kv
T m S y
Cv=64,8; q=1,2; y=0,5; m=0,9. [1, с.296, табл.49]
Т=90 мин - среднее значение периода стойкости метчика. [1, с.296, табл.49]
Общий поправочный коэффициент на скорость резания, учитывающий
фактические условия резания:
Kv KMv Kиv Kсv ,
где Кмv – коэффициент, учитывающий качество обрабатываемого материала;
|
|
Лист |
|
МСиИ.2012.ПФиИТ.КР.11.ПЗ |
22 |
Изм. Лист № докум. Подпись Дата |
|
|
|
|

КМv 0,7 ; [1,с.261, табл.1-4]
КСv=0,8 - коэффициент, учитывающий способ нарезания резьбы;
Киv=1,0 - коэффициент, учитывающий материал инструмента. [1, с.263,
табл.6] |
|
|
|
Kv |
0,7 0,8 1,0 0,56 ; |
||
v |
64,8 121,2 |
0,56 9,43м / мин. |
|
900,9 1,750,5 |
|||
|
|
Частота вращения шпинделя:
n |
1000 v |
|
1000 9,43 |
250,1мин 1 |
250мин 1. |
||
D |
3,14 16 |
|
|||||
|
|
|
|
Фактическая скорость резания:
v |
|
D n |
|
3,14 12 250 |
9,42м / мин. |
ф |
|
||||
|
1000 |
1000 |
|
||
|
|
|
3. Крутящий момент
M кр 10 См Dq P y K p
Cм=0,027;y=1,5; q=1,4; кр=кмр=1,3 [1, с.296, табл.49]
. M кр 10 0,027 121,4 1,751,5 1,3 26,35Нм
4. Мощность резания (эффективная), кВт
Pe М кр n 26,35 250 0,68кВт 9750 9750
Pe |
Pдв 8,8кВт .- мощность привода обеспечивает |
||
назначенного режима резания. |
|||
5. |
Расчет машинного времени: |
||
Т 0 |
|
Lз.х. |
i; где |
|
|||
|
|
VS |
Lр.х. – длина рабочего хода инструмента;
i – число рабочих ходов; i = 1;
МСиИ.2012.ПФиИТ.КР.11.ПЗ
Изм. Лист № докум. Подпись Дата
мощность
Лист
23

Lр.х. = l1 + lд + l2;
l1 + l2 = 5 мм; [обработка металлов резанием, с.623, табл.7]
Lр.х. = 18 + 5 =23 мм;
Т 0 |
23 |
1 |
0,1 |
мин. |
|
|
|||||
437,5 |
|||||
|
|
|
|
Рис.5 Эскиз нарезания внутренней резьбы М12-6Н
6.3 Назначение режимов резания для шлифования поверхности Ø32
1. Скорость вращения шлифовального круга – скорость резания
м
кр кр
2. Скорость вращения заготовки – окружная скорость заг определяем по справочнику технолога машиностроителя и корректируем согласно паспорта станка
заг |
|
м мин |
|
|
|
|
3. Частота вращения заготовки |
|
заг |
||
|
заг заг |
|
|||
заг |
|
|
мин |
|
|
|
|
|
|
(полученное значение корректируем по паспорту выбранного станка ), принимаем 250мин
|
|
Лист |
|
МСиИ.2012.ПФиИТ.КР.11.ПЗ |
24 |
Изм. Лист № докум. Подпись Дата |
|
|
|
|

4. Возвратно-поступательное движение стола – продольная подача , (мм/об), (зависит от и характера шлифования – предварительного или окончательного. В нашем случае шлифование окончательное)
0,2…0,4)B
ммоб
5.Рассчитываем необходимую мощность N
Где |
|
, r=0.5 x=0.5 y=0.55 q=0 |
|
|
N=1,37 кВт |
|
|
|
|
ст |
кВт |
|
||
Проверяем режим резания по мощности расч |
станка, условие выполняется. |
|||
6. |
Машинное время (основное технологическое время работы инструмента): |
|||
|
маш |
|
, |
|
|
|
|
||
|
|
заг |
|
|
|
где |
– длина рабочего хода,: |
|
|
|
|
|
мм. |
|
– длина шлифуемой поверхности,
; B – высота круга
– коэффициент, учитывающий время на выхаживание (при окончательном
)
маш |
|
мин |
|
|
|
Лист |
|
МСиИ.2012.ПФиИТ.КР.11.ПЗ |
25 |
Изм. Лист № докум. Подпись Дата |
|
|
|
|

Рис.6 Эскиз шлифования поверхности Ø 32мм
|
|
Лист |
|
МСиИ.2012.ПФиИТ.КР.11.ПЗ |
26 |
Изм. Лист № докум. Подпись Дата |
|
|
|
|
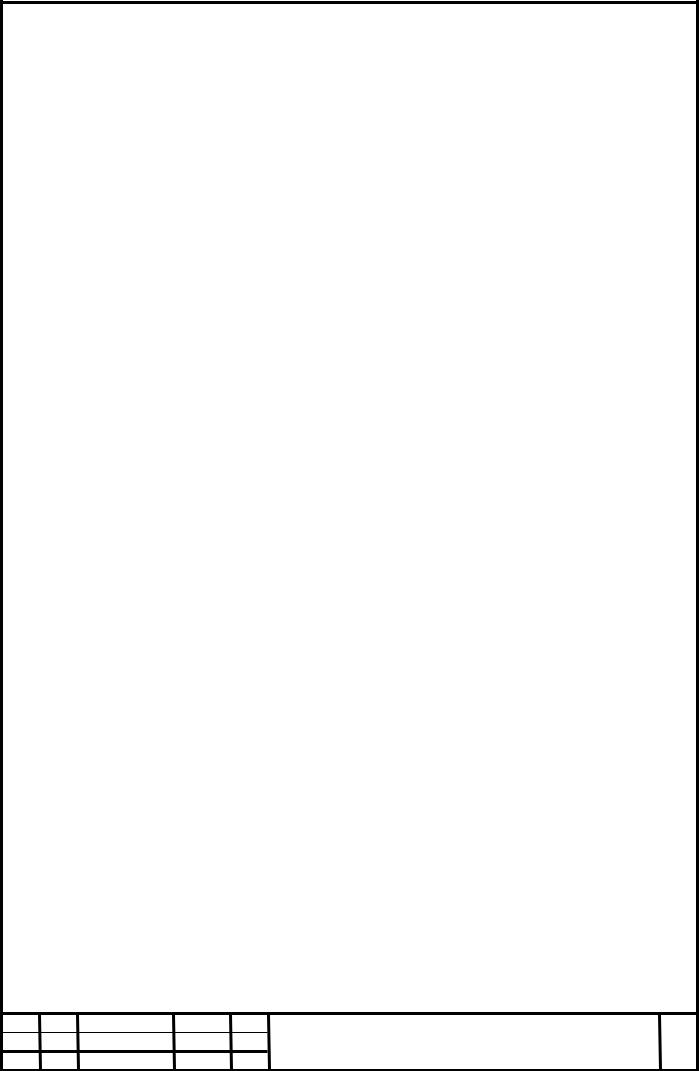
7. Проектирование и расчет специального инструмента для обработки
отверстия
7.1 Проектирование инструмента для нарезании внутренней резьбы М12 – 6Н
Для нарезания внутренней метрической резьбы М12 – 6Н на многоцелевом токарно – винторезном станке с ЧПУ мод. 16К20ФС32 целесообразно использовать метчик
Метчик – широко распространенный инструмент для нарезания внутренней резьбы. При проектировании метчиков специальной конструкции он должен иметь ряд стандартных конструктивных элементов, выбранным по ГОСТ3266 - 81
1.Материал рабочей части определяется условиями эксплуатации, при нарезании резьбы в стали 20 потребуется материал Р6М5 ГОСТ 19265 – 73
2.Число зубьев метчика выбирается в зависимости от обрабатываемого материала и диаметра резьбы. При нарезании резьбы диаметром 3…16мм,
принимаем z=3
3.Форма канавки должна обеспечивать свободное перемещение стружки, содействовать ее легкому отводу, не допускать налипания и спрессовывания в канавке. Наиболее распространена двухрадиусная форма канавки. Ее размеры назначаем из ГОСТ 3266 – 81
4.Длина заборной части зависит от сбега резьбы и допустимой толщине среза. При обработке стали 20 толщина среза а=0,02…0,05 мм, принимаем а
=0,04мм
5.Рекомендуется применять метчики со следующей унифицированной
длиной заборной части: - для глухих отверстий; -
для сквозных отверстий. Так как обработке подвергается сквозное отверстие, то
мм |
|
|
6. Длина калибрующей части |
, где – длина рабочей части |
|
принимается из ГОСТ , |
29 мм, тогда |
|
|
|
Лист |
|
МСиИ.2012.ПФиИТ.КР.11.ПЗ |
27 |
Изм. Лист № докум. Подпись Дата |
|
|
|
|

7.Для уменьшения трения калибрующая часть должна иметь обратную конусность по всему профилю резьбы. Для стали 20 обратная конусность на 100
ммдлины 0,05…0,08 мм
8.Размеры хвостовика следует назначить по ГОСТ 3266 - 81
9. |
Передний угол стали 20 |
принимаем |
10. |
Задний угол для сквозных отверстий |
, принимаем |
11.У метчиков с нешлифованным профилем затылование производиться
только по заборной части |
, к=3,14∙12∙tg4 /3=0,88 мм |
12.Степень точности метчика зависит от точности нарезаемой резьбы и свойств обрабатываемого материала. Так как точности резьбы 6Н, то степень точности метчика Н2
13.Исполнительные размеры метчика указаны в ГОСТ 17039 - 71
Рис. 7. Элементы конструкции и геометрические параметры метчика
|
|
Лист |
|
МСиИ.2012.ПФиИТ.КР.11.ПЗ |
28 |
Изм. Лист № докум. Подпись Дата |
|
|
|
|

8.Прочностные расчеты инструментов
8.1Расчет на прочность концевой фрезы
Проверка условия равномерного фрезерования
Окружной торцовый шаг зубьев:
Sокр D 8 6.28 мм z 4
Осевой шаг зубьев:
S |
ос |
D ctg 8 |
ctg 30 10,5 мм |
|
|
z |
4 |
|
|
|
|
|
С |
B |
|
21 |
2 - так как эта величина – целое число, то условие равномерного |
|
|
|
|
|||
|
Sос |
10,5 |
|
фрезерования выполнено.
8.2 Расчет на прочность метчика
Толщина срезаемого слоя должна удовлетворять двум условиям: она не должна быть меньше радиуса скругления режущих кромок, чтобы осуществить процесс резания и исключить подминание удаляемого слоя задней поверхностью зубьев. С другой стороны, наибольшая толщина срезаемого слоя должна быть такая, чтобы получить шероховатость обработанной поверхности и нужное качество поверхностного слоя. Исследование показывают, что этим условиям удовлетворяет толщина а1=0,02…0,15 мкм.
а1=Р
где P – шаг резьбы;
z – число режущих перьев;
а1= |
|
мкм – условие выполняется. |
|
|
|
Лист |
|
МСиИ.2012.ПФиИТ.КР.11.ПЗ |
29 |
Изм. Лист № докум. Подпись Дата |
|
|
|
|

9. Подбор вспомогательного инструмента.
Специализированные станки с ЧПУ (сверлильные, горизонтально-
расточные, фрезерные, координатно-расточные) и многооперационные станки в том числе встраиваемые в автоматизированные комплексы, комплектуются соответствующим вспомогательным инструментом.
Станки с ЧПУ работают в автоматическом режиме, поэтому их инструментальная оснастка должна удовлетворять требования автоматизированного производства и кроме того, обладать гибкостью,
позволяющей без переналадки выполнять разнообразные технологические операции при изготовлении различных деталей. Для уменьшения отклонения от сносности можно применять оправки с небольшой конусностью. Высокая точность обработки по диаметру и допуску концентричности достигается с использованием мембранных патронов.
.
|
|
Лист |
|
МСиИ.2012.ПФиИТ.КР.11.ПЗ |
30 |
Изм. Лист № докум. Подпись Дата |
|
|
|
|