
Техническая диагностика Лекции (заочно)
.pdf21
Наличие некоторого диагностического признака, не может быть однозначным диагнозом того, что диагностический параметр меньше или больше -допустимого значения
диагностического параметра SД .
Контролируемые диагностические параметры имеют:
-случайный разброс из-за ошибок измерения,
-случайное сочетание режимов работы разных элементов автомобиля и т. д.
Поэтому наличие или отсутствие диагностического признака при определенном диагнозе Di не является достоверным событием («1» или «0»), а наблюдается с некоторой
условной вероятностью PDi(Sj).
Наблюдая за большой группой автомобилей можно установить, как часто встречаются интересующие нас диагнозы D, и с какой вероятностью при этих диагнозах встречаются принятые для разрабатываемой системы диагностические параметры – S.
Для определения вероятностей наблюдения различных признаков, можно искусственно вносить в автомобиль интересующие нас неисправности (нарушать регулировки и т. п.).
Например, для инжекторного или дизельного ДВС последовательно отключать подачу топлива через форсунки и следить за перебоями в работе (если нет перебоя в работе ДВС, то форсунка неисправна)
Если допустить, что результаты статистических исследований, соответствуют диагностической матрице рассмотренной выше, то вместо однозначно поставленного диагноза «1» или «0» можно поставить вероятности их возникновения и добавить еще диагноз
D4 , который с определенной вероятностью на другие причины и образует полную группу
событий.
В этом случае диагностическая матрица может принять вид (табл.4):
|
Диагностическая матрица с учетом вероятностей проявления |
Таблица 4 |
|||||
|
|
||||||
|
|
диагностических параметров |
|
|
|
||
Диагноз |
|
Вероятности диагностических параметров |
|
|
Вероятность |
||
|
P(S1) |
P(S2) |
P(S3) |
P(S4) |
P(S5) |
|
диагноза |
|
|
|
|
|
|
|
P(Di) |
D1 |
1,0 |
0,8 |
0,9 |
1,0 |
0,2 |
|
0,05 |
D2 |
0,9 |
0,7 |
0,9 |
0,0 |
0,2 |
|
0,10 |
D3 |
0,6 |
0,1 |
0,9 |
0,1 |
0,9 |
|
0,30 |
D4 |
0,1 |
0,1 |
0,0 |
0,1 |
0,0 |
|
0,55 |
Применительно к диагностике, а в частности к диагностической матрице с учетом проявления вероятностей применяют формулу Бейеса для вероятности диагноза комплекса диагностических параметров:
|
|
n |
|
|
P(Di) P(Sj) |
|
|
PSj(Di) |
|
j 1 |
, |
m |
n |
||
|
P(Sj) |
|
|
|
i 1 |
j 1 |
|
где P(Di) - вероятность Di - го диагноза;
P(Sj)- вероятность наблюдения Sj- го параметра при диагнозе Di ;
Используем данные диагностической матрицы с учетом вероятностей и рассчитаем вероятности диагнозов для заданного ранее комплекса диагностических параметров по формуле Бейеса
22
PS1(D1) |
|
|
0,05 1 0,8 0,9 1,0 0,2 |
|
||||
0,05 1 0,8 0,9 1,0 0,2 0,1 0,9 0,7 0,9 0,0 0,8 0,3 0,6 0,55 |
||||||||
|
|
|
0,0072 |
|
0,0072 |
0,8316 |
. |
|
|
|
|
||||||
0,0072 0 0,001458 0 |
0,008658 |
|
||||||
|
|
|
|
|||||
PS2 |
(D2) 0. |
|
|
|
|
|||
P |
|
(D |
) 0,3 0,6 0,1 0,9 0,1 0,9 0,001458 0,1684. |
|
||||
S3 |
3 |
0,008658 |
|
0,008658 |
|
|||
|
|
|
|
|
PS4(D4) 0.
На основе проведенных расчетов можно сказать, что для автомобиля с набором признаков, соответствующих заданному комплексу диагностических параметров, наиболее вероятным является первый диагноз: негерметичен запорный клапан поплавковой камеры карбюратора.
Практически невероятен износ жиклеров, мало вероятно, что у карбюратора не отрегулирована система холостого хода.
Если первый диагноз не подтвердится при проверке карбюратора, то вторым по значимости будет третий диагноз.
Причина плохой работы двигателя не кроется в чем-то другом.
В реальных системах диагностирования подобные расчеты проводятся микропроцессорной техники автоматически (мотор-тестер).
Система диагностирования должна предусматривать процесс «обучения», т. е. корректирования матрицы вероятностей по мере накопления опытных данных.
С этой целью в памяти ЭВМ следует хранить не только вероятности диагноза P(Di ) и и вероятности диагноза для заданного комплекса PSj(Di), но и общее число объ-
ектов N, по которым определялись вероятности диагнозов P(Di ), а также Nij- число объектов с признаком Sj
Если поступает новый объект с диагнозом Dk , то проводят корректировку прежних априорных вероятностей следующим образом:
P(D |
) |
Ni |
|
|
Ni |
N |
|
|
P(D |
) |
N |
|
для |
i 1,2,3...m, i k ; |
||||||
N 1 |
|
|
|
N 1 |
||||||||||||||||
i |
|
|
|
N N 1 |
|
|
i |
|
|
|
||||||||||
P(D |
|
) |
Nk 1 |
P(D |
) |
|
|
N |
|
|
|
1 |
|
|
при |
i k . |
||||
|
N 1 |
|
N 1 |
|||||||||||||||||
k |
|
N 1 |
|
k |
|
|
|
|
|
После этого присваивается новое значение числу объектов N N 1.
Таким образом, после диагностирования очередного автомобиля и подтверждения фактического диагноза по результатам разборки узла или каким либо другим образом, диагност вносит коррективы в диагностическую матрицу. В результате такой процедуры диагностическая система «обучается», «набирается опыта», что имитирует рост профессионального мастерства человека, занимающегося диагностированием.
МЕТОДЫ И СРЕДСТВА ДИАГНОСТИРОВАНИЯ
Методы и средства диагностирования автомобилей служат для имитации режимов их работы, измерения диагностических параметров и постановки диагноза; они создаются соответственно диагностируемому механизму, видам диагностических параметров и технологическому назначению.
Методы диагностирования классифицируют на субъективные (органолептические)
и объективные.
23
Субъективную оценку дают с помощью органов чувств человека. Объективное диагностирование осуществляется с помощью приборов. Классификация методов и средств диагностирования автомобилей наавтотранс-
портных предприятиях и СТОА показана в табл. 5.
|
|
|
Таблица 5 |
Классификацияметодовдиагностированияавтомобилей,агрегатовисистем |
|||
|
|
|
|
Метод |
|
Диагностический параметр |
Объект диагностирования |
диагностирования |
|
||
|
|
|
|
|
|
|
|
|
|
Органолептические методы |
|
|
|
|
|
Визуальный |
1. утечки жидкостей и газов; |
Системы двигателя: |
|
|
2. |
дым, цвет и прозрачность жидкостей и |
а) питания топливом, |
|
газов; |
б) охлаждения, |
|
|
3. |
следы коррозии; |
в) тормозная и др. |
|
4. |
отслоение покрытия; |
Кузов, шины; световые приборы |
|
5. |
работоспособность; |
|
|
6. |
целостность; |
|
|
7. |
трещины и сколы |
|
Слуховой |
1. стуки; |
Двигатель; трансмиссия; тормозная, |
|
|
2. |
шумы; |
ходовая системы; подвеска; рулевое |
|
3. скрипы |
управление; кузов |
|
|
|
|
|
Обонятельный |
1. запах продуктов горения; |
Колодки тормозов колес, электрообо- |
|
|
2. |
утечки топлива |
рудование, топливная система |
|
|
|
|
Осязательный |
1. место и степень нагрева; |
Тормоза колес, ходовая система и |
|
|
2. источники и уровень вибрации; |
подвеска, рулевое управление, короб- |
|
|
3. |
люфты и зазоры; |
ка передач, задний мост |
|
4. |
шероховатость; |
|
|
5. |
наличие механических включении в |
|
|
жидкостях |
|
|
|
|
|
|
|
|
Объективные мemoды |
|
|
|
|
|
По функциональным |
1. работоспособность; |
Двигатель, тормозная система, руле- |
|
параметрам |
2. мощность; |
вое управление, внешние осветитель- |
|
|
3. |
крутящий момент; |
ные приборы |
|
4. |
частота вращения коленчатого вала- |
|
|
двигателя; |
|
|
|
5. |
тормозные силы на колесах; |
|
|
6. |
тормозной путь; |
|
|
7. |
время торможения; |
|
|
8. |
освещенность и распределение осве- |
|
|
щенности контрольной поверхности |
|
|
|
|
|
|
По параметрам рабочих |
1. температура охлаждающей жидкости; |
Двигатель, внешние осветительные |
|
процессов |
2. состав отработавших газов; |
приборы, система охлаждения, элек- |
|
|
3. |
давление масла в смазочной системе |
трооборудование |
|
двигателя; |
|
|
|
4. |
удельный расход топлива; |
|
|
5. |
сила света ламп фар; |
|
|
6. |
плотность электролита; |
|
|
7. |
напряжение бортовой сети; |
|
|
8. |
зарядный ток |
|
По параметрам состояния |
1. температура и место нагреваподшип- |
Двигатель, коробка передач, редуктор |
|
и состава |
никовых узлов; |
главнойпередачи, подшипники колес, |
|
|
2. |
дымность газов; |
топливная система |
|
3. загрязненность масел; |
|
|
|
4. |
состав газов; |
|
|
5. |
концентрация примесей в масле |
|
24
|
|
|
Окончание табл. 5 |
Метод |
|
Диагностический параметр |
Объект диагностирования |
диагностирования |
|
||
|
|
|
|
По структурным геомет- |
1. |
зазоры; |
Двигатель, коробка передач, редуктор |
рическим параметрам |
2. |
люфты; |
главнойпередачи, ходовая часть, ру- |
|
3. |
форма поверхности; |
левое управление |
|
4. соосность отверстий; |
|
|
|
5. |
углы установки колес |
|
По герметичности рабо- |
1. компрессия в цилиндрах; |
Двигатель; шины; топливный бак; си- |
|
чих объемов |
2. |
количество прорывающихся в картер |
стемы питания, охлаждения, тормоз- |
|
двигателя отработавших газов; |
ная система |
|
|
3. |
давление в шинах, |
|
|
4. |
уровень охлаждающей жидкости в бач- |
|
|
ке |
|
|
По виброакустическим |
1. |
амплитудно-частотные; |
Двигатель, ходовая часть, коробка |
параметрам |
2. |
характеристики вибрации; |
передач, редуктор главной передачи, |
|
3. |
уровень шума |
рулевое управление |
По видам диагностических параметров методы диагностирования подразделяются на две группы:
•функциональные — соответствующие параметрам рабочих процессов или параметрам эффективности объекта диагностирования (мощность, тормозной путь, расход топлива);
•локальные — соответствующие параметрам процессов, сопутствующих функционированию объекта (нагрев, вибрация, состав отработавших газов), а также структурным или геометрическим параметрам (зазоры, люфты, смещения).
Первая группа методов предназначается главным образом для определения работоспособности объекта в целом, т. е. для общего (комплексного) диагностирования.
Если оказывается, что рабочие параметры объекта не соответствуют нормам, то диагностирование углубляют, определяя причины неисправностей его элементов при помощи локальных методов. Локальные методы и средства обеспечивают поэлементное диа-
гностирование.
Применение тех или иных методов и средств диагностирования существенно зависит от их технологического назначения.
Принципиально, важное значение приобретает классификация методов и средств диагностирования по схеме их применения — в стационарных условиях или в движении.
Стационарное диагностирование обеспечивает ТО и ремонт автомобилей в производственных помещениях АТП, СТОА и т. д.
Ходовое диагностирование осуществляется во время движения автомобиля при помощи встроенных датчиков и измерительных приборов непрерывного контроля или же при помощи таких переносных приборов, как расходомер топлива, деселерометр.
Основные требования к методам и средствам диагностирования — достоверность измерений, надежность, технологичность и экономичность.
Достоверность измерений характеризуется: точностью, воспроизводимостью и чувствительностью.
Надежность — безотказностью, долговечностью и ремонтопригодностью средств диагностирования.
Технологичность — сложностью, трудоемкостью и универсальностью процессов диагностирования.
Экономичность — стоимостью технических средств, затратами на их эксплуатацию и эффектом от применения.
Перечисленные требования связаны между собой и зависят от целей и объекта диагностирования. Поэтому методы и средства диагностирования следует оценивать прежде всего комплексно, по экономическому критерию, а затем в целях сравнения и выбора по
25
техническим свойствам — метрологическим, технологическим, надежностным, эргономическим.
Применяемые методы и средства поэлементного и общего диагностирования тормозов автомобиля представлены в табл. 6.
Таблица 6 Методы и средства измерения или оценки диагностических параметров
тормозной системыавтомобиля (выборочно)
Диагностический |
Метод диагностирования |
Техническое средство |
параметр |
(измерения) |
диагностики |
|
|
|
Свободный ход |
Прямое измерение хода педали до момента резкого воз- |
Специальная линейка или |
педали |
растания сопротивления перемещению |
телескопический прибор |
Утечка тормозной |
Визуальный осмотр. Замер уровня тормозной жидкости |
— |
жидкости |
в бачке после нескольких нажатий на педаль тормоза |
|
|
|
|
Эффективность |
При дорожных испытаниях — прямое измерение тор- |
Рулетка, деселерометр, се- |
торможения |
мозного пути, установившегося замедления и времени |
кундомер, тормозной стенд |
|
торможения. |
|
|
При стендовых испытаниях — измерение общей удель- |
|
|
ной тормозной силы и времени срабатывания тормозной |
|
|
системы |
|
|
|
|
Устойчивость |
При дорожных испытаниях — прямое измерение ли- |
Рулетка, тормозной стенд |
торможения |
нейного отклонения автомобиля от оси прямолинейного |
|
|
движения. При стендовых испытаниях — измерение |
|
|
разности тормозных сил колес одной оси |
|
|
|
|
Кчислу основных требований, предъявляемых к современным средствам технического диагностирования (СТД) автомобилей, относятся:
•заданная точность измерений и необходимая достоверность диагностирования;
•удобство и простота считывания показателей;
•возможность запоминания результата измерения;
•возможность выдачи результата измерения в текстовом или графическом виде.
Кчислу перечисленных требований, влияющих на выбор типа индикации, относится малая погрешность измерения тех или иных параметров.
Для большинства технических измерений, связанных с диагностированием автомобиля, достаточно класса точности 2,0 или 3,0, а в некоторых случаях даже 10,0.
Например для измерения расхода топлива необходимо иметь прибор класса 2,5, неплотности цилиндропоршневой группы — класса 4,0, а для высокого напряжения в цепи зажигания — класса точности 10,0.
В средствах технического диагностирования используется как аналоговая, так и цифровая индикация.
В качестве аналоговых индикаторов в СТД применяются чаще микроамперметры магнитоэлектрической системы, обеспечивающие заданную точность, хорошую чувствительность и линейность; реже — светолучевые гальванометры и линейные газоразрядные индикаторы.
Аналоговые индикаторы позволяют получить не только количественную, но и качественную информацию о контролируемом процессе, например о нахождении параметра в заданных пределах, динамике протекания процесса. В аналоговых индикаторах можно
26
нанести на шкалы вспомогательные метки, обозначить и выделить цветом определенные зоны, чтобы облегчить работу оператора-диагноста.
Однако в приборах с аналоговой индикацией считывание показаний затруднено тем, что они перегружены шкалами, а оператору приходится не только выбирать нужную шкалу, но зачастую проводить в уме арифметические операции, что приводит к увеличению времени считывания и появлению дополнительных ошибок. Кроме того, вывод на печать аналоговой информации возможен только в виде графиков с помощью громоздких самописцев.
В этом отношении цифровые индикаторы имеют по сравнению с аналоговыми приборами решающее преимущество, поскольку выдают информацию непосредственно в готовом виде, не требующем дополнительной обработки оператором.
При измерении медленно меняющихся параметров динамических процессов преимущества цифровой индикации при считывания явно выражены. При измерении параметров динамических процессов цифровая индикация оказывается весьма эффективной, если за 8 —10 последовательных циклов измерений значение параметра меняется не более чем на ±2 единицы младшего разряда индикатора.
Развитие радиоэлектроники привело к резкому снижению стоимости приборов с цифровой индикацией, причем в ряде случаев их стоимость намного ниже, чем у приборов с аналоговой индикацией.
Сегодня, благодаря развитию ЭВМ, современные СТД основаны на применении компьютерной техники, которая, хорошо сопрягаясь с любыми датчиками, позволяет выдавать с высокой точностью информацию о любых процессах и параметрах в виде цифровой индикации, графиков, диаграмм или таблиц. При необходимости диагностические параметры могут быть распечатаны в диагностической карте.
ДИАГНОСТИРОВАНИЕ ДВИГАТЕЛЯ ВНУТРЕННЕГО СГОРАНИЯ
Общее диагностирование ДВС проводят в целях контроля работоспособности двигателя путем количественной оценки его основных параметров. В качестве диагностических параметров при этом используют эффективную мощность, расход топлива, состав отработавших газов, уровни шума и вибраций, давление масла в смазочной системе.
Например, для определения эффективной мощности двигателя разработаны тормозные и бестормозные методы.
Тормозные методы диагностирования предполагают нагружение двигателя со стороны колес автомобиля с использованием тяговых стендов с беговыми барабанами. Тормозной момент создается гидравлическими, электрическими или инерционными нагружающими устройствами.
Бестормозные методы диагностирования более просты и не требуют для реализа-
ции специальных тормозных устройств. К ним относятся метод измерения частоты вращения коленчатого вала двигателя под нагрузкой, создаваемой поочередным выключением из работы его цилиндров; метод анализа разгонной характеристики двигателя на холостом ходупри полной подаче топлива.
Локальное (поэлементное) диагностирование двигателя проводят, чтобы найти те-
ряющий работоспособность механизм или систему, определить конкретную причину отказа либо предотказное состояние детали или сопряжения, влияющие на эксплуатационные показатели двигателя.
Поэлементное диагностирование проводят в двух случаях:
•когда по завершении общего диагностирования были получены отклонения от нормы его выходных параметров;
•если имеется конкретный симптом неисправности (двигатель плохо пускается, неустойчиво работает на холостом ходу, прослушиваются стуки, не работает один из цилиндров).
27
Для оценки технического состояния основных механизмов и систем автомобильного двигателя используются следующие методы поэлементного диагностирования:
1.определение угара масла;
2.герметичности камеры сгорания;
3.спектральный анализ картерного масла;
4.химический анализ отработавших газов.
Методы диагностирования по герметичности камеры сгорания.
Метод 1. Метод используется для оценки износа деталей цилиндропоршневой группы и плотности посадки клапанов; он основан на определении количества прорвавшихся газов или сжатого воздуха в картер, утечки сжатого воздуха из цилиндра при закрытых клапанах, а также давления газовой смеси или воздуха в цилиндре в конце такта сжатия.
Измерение прорыва газов в картер производят с помощью газового расходомера, который подсоединяют к маслоналивной горловине. При этом требуется герметизировать все другие возможные пути выхода картерных газов при работе двигателя на полной нагрузке и номинальной частоте вращения коленчатого вала.
Установлено, что при износе деталей цилиндропоршневой группы, близком к предельному, утечки газов в картер увеличиваются в 7—12 раз.
Недостатками данного метода при измерении расхода картерных газов являются затрудненность определения непосредственной причины повышенной утечки газов в картер, а также зависимость утечки от скоростного и нагрузочного режимов работы двигателя.
Метод 2. Для более точной оценки герметичности камеры сгорания и соответственно состояние деталей цилиндропоршневой группы, клапанных уплотнений и прокладки головки цилиндров можно путем подачи в цилиндр сжатого воздуха через отверстия для свечей зажигания.
Утечки воздуха (падение давления сжатого воздуха в надпоршневом пространстве), составляющие более 15% при положении поршня вблизи ВМТ на такте сжатия, когда клапаны закрыты, свидетельствуют об износе цилиндров. Если после внесения масла в камеру сгорания утечка воздуха кратковременно резко снизилась, это говорит об износе или поломке колец.
Утечки воздуха через клапаны впуска газовой смеси или выпуска продуктов сгорания определяют на слух в соответствующей системе.
О неудовлетворительном состоянии прокладки головки цилиндров судят по появлению пузырьков воздуха в горловине радиатора.
Герметичность камеры сгорания можно оценить также по падению давления сжатого воздуха в цилиндре в конце такта сжатия либо по величине компрессии при проворачивании коленчатого вала стартером. На достоверность результатов такого диагностирования оказывает влияние непостоянство частоты вращения коленчатого вала стартером. Кроме того, только по падению давления (компрессии) невозможно определить конкретное сопряжение, ответственное за недостаточную герметичность камеры
Проверка компрессии ДВС
Компрессию двигателя (максимальное давление в камере сгорания) определяют на прогретом до нормальной температуры двигателе.
Для проверки компрессии необходимо:
•очистить грязь, собравшуюся в углублениях для свечей;
•отсоединить электрические провода от свечей и вывернуть все свечи;
•отсоединить от катушки зажигания центральный провод распределителя;
•открыть полностью воздушную и дроссельную заслонки карбюратора;
28
•вставить наконечник компрессометра в отверстие для свечи зажигания и плотно его прижать;
•провернуть на несколько оборотов коленчатый вал стартером с частотой 180...200 мин-1, чтобы компрессометр зафиксировал максимальное давление в цилиндре;
•вынуть из отверстия свечи наконечник компрессометра, записать показания, открыть выпускной клапан компрессометра и выпустить воздух;
•повторить проведенную операцию для остальных цилиндров.
Проверку повторяют 2 — 3 раза для каждого цилиндра. Полученное значение усредняют. Минимально допустимая компрессия для бензиновых двигателей зависит от степени сжатия и находится в пределах от 0,7 до 10 МПа. Разность показаний манометра при измерении на различных цилиндрах для исправного двигателя не должна превышать
0,1 МПа.
ОБОРУДОВАНИЕ ДЛЯ ДИАГНОСТИРОВАНИЯ АВТОМОБИЛЕЙ
Классификация средств диагностики автомобилей
Техническое диагностирование автомобилей — комплекс увязанных между собой методов технологических процессов, нормативов и средств диагностики. Средства технического диагностирования могут быть классифицированы по ряду признаков представленных в табл.7.
|
|
Таблица 7 |
|
Классификациясредствдиагностированияавтомобилей |
|||
|
|
|
|
Признак |
|
Средства диагностики |
|
|
|
|
|
Функционально-технологическое |
1 |
- для автомобиля в целом; 2 - для поэлементного анализа си- |
|
назначение |
стем, агрегатов, сборочных единиц, деталей |
|
|
Конструктивная связь с автомобилем |
1 |
- внешние — датчик на автомобиле, указатель за пределами |
|
|
автомобиля; 2 - бортовые — датчик и указатель как оборудование |
|
|
|
автомобиля |
|
|
Степень подвижности |
1 |
- стационарные;2 - передвижные; 3 - переносные |
|
Степень автоматизации |
1 |
– автоматические; 2 - частично автоматизированные; 3 - неав- |
|
|
томатизированные |
|
|
Вид энергии носителя сигналов в ли- |
1 |
– механические; 2 – электрические; 3 – магнитные; 4 – электро- |
|
нии связи |
магнитные; 5 – оптические; 6 – пневматические; 7 - гидравличе- |
|
|
|
ские; 8 – комбинированные; 9 - используемые иные виды энергии |
|
|
Вид источника энергии привода или |
От источника: 1 - электроэнергии; 2 - сжатого воздуха; 3 – ваку- |
|
|
функционирования СТД |
ума; 4 - механической энергии (вращающих масс); 5 - комбини- |
|
|
|
рованной энергии; 6 - звуковых колебаний; 7 - вибрации |
|
|
|
|
|
|
Функционально-технологическая классификация контрольно-диагностического и регулировочного оборудования приведена на рис.17.
Диагностическое и регулировочное оборудование подразделяется на две группы. К первой группе относятся оборудование и приборы для общей диагностики и кон-
троля тормозной системы автомобиля — тормозные стенды; ко второй — станки для балансировки колес стенды развал-схождения и др.
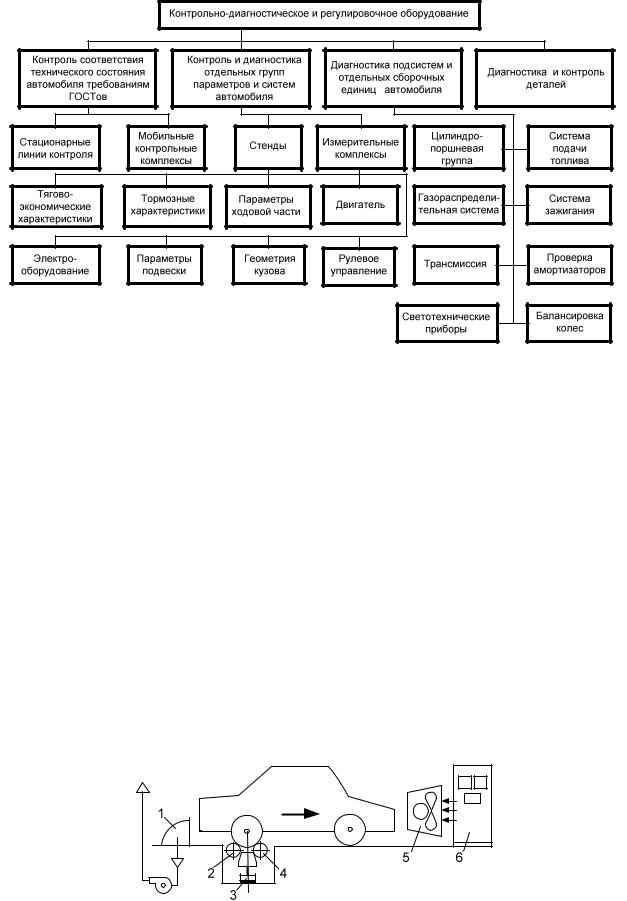
29
Рис.17. Функционально-технологическая классификация контрольно-диагностического и регулировочного оборудования
ТЯГОВЫЕ СТЕНДЫ ДЛЯ ОБЩЕЙ ДИАГНОСТИКИ АВТОМОБИЛЯ И КОНТРОЛЯ ЕГО ТЯГОВО-ЭКОНОМИЧЕСКИХ ПОКАЗАТЕЛЕЙ
Тяговые стенды (или иначе стенды контроля тяговых качеств автомобиля — СТК) роликового (барабанного) типа имитируют движение автомобиля с различными скоростными режимами и режимами нагружения двигателя. На стендах тестируются:
1.Комплексные параметры: мощность на ведущих колесах, тяговое усилие на ведущих колесах, линейная скорость на окружности колеса (скорость автомобиля), расход топлива, время (путь) разгона, выбега.
2.Элементные параметры (с добавлением дополнительных приборов): частота вращения коленчатого вала, пробуксовка сцепления, исправность спидометра, неисправности трансмиссии и др.
3.Диагностирование и контроль ведутся в режимах максимальной тяговой силы (крутящего момента), максимальной скорости.
Стенды выпускаются для легковых и грузовых автомобилей, для легковых с одной ведущей осью и полноприводных автомобилей.
Принципиальная схема стенда для контроля заднеприводных легковых автомобилей дана на рис.18.
Рис. 18. Принципиальная схема тягового стенда для легковых заднеприводных автомобилей:
1 — местный отсос; 2 — опорный ролик; 3 — подъемная площадка с тормозными колодками; 4 — тормозной ролик; 5 — вентилятор; 6 — пульт управления и индикации
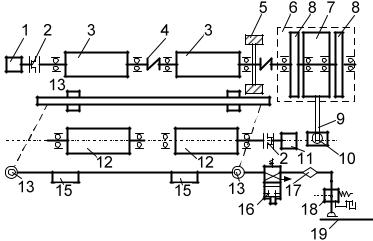
30
Принцип действия тяговых стендов заключается в том, что движущие силы и мощность, развиваемые двигателем автомобиля и приведенные к его колесам, уравновешиваются силами тормозных устройств стенда и фиксируются с помощью специальных силоизмерительных устройств.
Нагружение ведущих колес автомобиля в силовых стендах осуществляется за счет применения тормозного устройства. В качестве тоомоза используются устройства, позволяющие менять в широких пределах тормозное усилие. Чаще всего для этой цели применяются вихревые электродинамические и гидродинамические тормозные устройства, реже электродвигатели, работающие в генераторном режиме.
Винерционных стендах для нагружения ведущих колес использованы в качестве маховых масс массы роликов (барабанов) и специальные тяжелые маховики, соединенные
сроликами стенда через редуктор.
Встендах с комбинированным нагружением применяются как тормозные устройства, так и маховики.
Всоответствии со способом нагружения автомобиля, диагностирование на стендах ведется либо в скоростном, либо в нагрузочном режимах.
Скоростной режим реализуется с помощью инерционных маховых масс в процессе
разгона системы автомобиль — стенд.
Нагрузочный режим осуществляется в силовых стендах. Для этого режима характерно постоянство скорости движения автомобиля и тормозных сил, развиваемых стендом.
Комбинированная пневмо-кинематическая схема опорного блока стенда представлена на рис. 19.
Рис. 19. Пневмо-кинематическая схема опорного блока стенда для проверки тягового-экономических показателей с инерционным и силовым нагружением роликов: 7 — тахогенератор; 2 — муфта (2 шт.); 3 — опор- но-тормозной ролик (2 шт.); 4 — упругая муфта (2 шт.); 5— маховик; 6 — тормозной электродвигатель в сборе с балансир-ным статором 7 и ротором 8; 9— рычаг; 10 — силоизмерительный тензодатчик; 11 — реле скорости; 12— опорный ролик (2 шт.); 13— подъемная площадка; 14 — тормозная колодка роликов (2 шт.); 15— пневмоподъемник сильфонный; 16— распределитель; 17—фильтр; 18— редукционный клапан; 19 — магистраль сжатого воздуха
Все элементы опорного блока стенда размещены в раме. Каждое ведущее колесо одной оси автомобиля опираются на два ролика 3 и 10. Ролики 10 являются опорными; правый ролик через реле скорости 9 включает электросекундомер.
Тормозные ролики 3 соединены между собой муфтой 4. На валу правого ролика закреплен маховик 5, маховые массы которого имитируют инерционные массы автомобиля с нагрузкой на ось 500 кг.
Тормозной электродвигатель 7 подключается к роликам 3 при выборе режима комбинированного нагружения. Тормозной электродвигатель выполнен в виде ротора с выходным валом и посаженного на этот же вал на подшипниках статора, который имеет ба-