
Kuzmichev
.pdfрегламентувала основні процедури здійснення окремих видів діяльності щодо метрологічного забезпечення виробництва. Результати діяльності метрологічної служби зображено на рис. 2.
Виражаючи метрологічне забезпечення виробництва як складову TQM, необхідно відзначити необхідність оцінювання та контролю його ефективності. Метою оцінювання відповідності метрологічного забезпечення встановленим вимогам є підтвердження можливості метрологічної служби підприємства забезпечити виробництво продукції з необхідними характеристиками та стабільністю якості виготовлення. Оцінюючи метрологічне забезпечення, перевіряють:
1.Обґрунтованість вибору номенклатури вимірюваних (контрольованих) параметрів та допустимих меж їхнього вимірювання.
2.Виконання вимог, правил та норм державної системи забезпечення єдності вимірювань, а також вимог до вірогідності контролю параметрів та точності встановлення режимів випробувань.
3.Легітимність діяльності метрологічної служби та компетентність її персоналу.
4.Забезпеченість організації засобами та приміщеннями, необхідними для вимірювань, перевірки (калібрування),ремонту, зберігання засобів вимірювання, контролю та випробувань та відповідність їх встановленим вимогам.
5.Систематичний аналіз стану вимірювань та робіт щодо здійснення метрологічної експертизи нормативної та технічної документації, процесів та продукції.
6.Забезпеченість усіх виробничих підрозділів підприємства необхідними
нормативними та технічними документами, в яких регламентовані вимоги з метрології, а також методиками та засобами контролю, вимірювань, випробувань та технічної діагностики з необхідними характеристиками.
7.Стан робіт щодо метрологічного підтвердження придатності еталонів та засобів вимірювань, їхньої ідентифікації.
8.Ведення записів про стан та умови застосування засобів метрологічного забезпечення. Для забезпечення ефективного оцінювання метрологічного забезпечення виробництва уповноважені працівники метрологічної служби здійснюють підготовчі
заходи, які полягають у складанні плану перевірки, визначенні підрозділів, які будуть перевірятися, відповідальних осіб, об’єктів перевірки та термінів її здійснення. Крім цього, необхідно перевірити готовність метрологічної та випробувальної баз до оцінювання, здійснити їхню самооцінку, визначити напрями покращання. Якщо оцінювання метрологічного забезпечення виробництва є складовою
сертифікації системи управління якістю (СУЯ), то оцінювання складається з таких етапів:
– попереднє оцінювання;
– остаточна перевірка та оцінювання;
– інспекційний контроль.
Під час попереднього оцінювання перевіряють наявність необхідних документів та їхню відповідність вимогам нормативно-правової документації. Остаточна перевірка
відповідності метрологічного забезпечення встановленим вимогам здійснюється згідно з програмою перевірки СУЯ, яка розроблена за результатами встановленого при попередньому оцінюванні обсягу контрольованих робіт щодо забезпечення якості. Інспекційний контроль відповідності метрологічного забезпечення встановленим вимогам здійснюється за результатами інспекційного контролю сертифікованої СУЯ.

33. Основи процесів очистки поверхні. Фізичні та хімічні забруднення, способи їх видалення.
Види забруднень.
Забруднення на поверхні пластин та підкладок класифікують, як правило, за їх фізикохімічними властивостями, тому що вони визначають вибір методів видалення забруднень. Найбільш поширеними є забруднення наступних видів:
*Фізичні забруднення - пилинки, ворсинки, абразивні матеріали, силікати, кремнієвий пил і інші сторонні частинки, хімічно не зв'язані з поверхнею пластин та підкладок.
*Забруднення, хімічно пов'язані з поверхнею пластин та підкладок - оксиди, нітриди та інші сполуки.
*Органічні забруднення - неполярні жири, масла, силікони та інші неіонні домішки.
*Розчинні у воді полярні забруднення - солі, кислоти, флюси та ін
*Гази, адсорбовані поверхнею пластин та підкладок.
Класифікація методів очищення пластин та підкладок.
Для видалення забруднень використовують різні методи. За механізмом протікання процесів всі методи очищення класифікують на фізичні та хімічні, а по застосовуваних засобах - на рідинні і сухі.
В основу кожного способу очищення покладений один з трьох методів видалення забруднень з поверхні:
*Механічне видалення часток забруднювача потоком рідини або газу;
*Розчинення у воді;
*Хімічна реакція.
.
До фізичних методів видалення забруднень відносять розчинення, отжиг, обробку поверхні прискореними до великих енергій іонами інертних газів. Ці методи використовують в основному для видалення забруднень, розташованих на поверхні. Для видалення забруднень на поверхні і в приповерхневому шарі, у тому числі тих, які знаходяться в хімічній зв'язку з матеріалом пластини або підкладки, використовують хімічні методи видалення. Вони засновані на переведенні шляхом хімічної реакції забруднень в нові сполуки, які потім легко видаляються (травлення, знежирення).
Рідинне очищення передбачає використання водних та інших розчинів різних реактивів. Цілий ряд органічних жирових забруднень не розчиняється у воді і перешкоджає змочування водою і більшістю розчинів оброблюваної поверхні (поверхня гідрофобна). Процес видалення жирових забруднень, що супроводжується зміною поверхні з гідрофобного стану в гідрофільний, називається знежиренням.
Суха очистка заснована на використанні відпалу, газового, іонного та плазмохімічного травлення. Ці способи виключають застосування дорогих і небезпечних в роботі рідких хімічних реактивів; вони більш керовані і легше піддаються автоматизації. Процеси сухого очищення є найбільш ефективними також при обробці локальних ділянок та рельєфної поверхні.
34К.Очистка в рідких середовищах. Видалення органічних та жирових забруднень. Використання ультразвуку для очистки.
Жидкостная счистка (далее ЖО) выполняется органическими растворителями; разнообразными составами, содержащими щелочи, кислоты, пероксид и другие реактивы, водой. Подобрать жидкое средство, одновременно удаляющее все возможные поверхностные загрязнения, практически невозможно, поэтому ЖО включает ряд последовательных операций. Нерастворимые в воде органические жировые загрязнения делают поверхность гидрофобной, тс есть плохо смачиваемой водой и большинством растворов. Для равномерной счистки поверхность подложек (пластин) необходимо перевести в гидрофильное, тс есть хорошо смачиваемое водой, состояние. Операция удаления жировых загрязнений, сопровождаемая переводом поверхности из гидрофобного в гидрофильное состояние, называется обезжириванием (обезжиривание — первая операция при ЖО).
Обезжиривание
Обезжиривание (отмывка) в органических растворителях применяется для удаления с поверхности пластин (подложек) жиров животного и растительного происхождения, минеральных масел, смазок, воска, парафина и других органических и механических загрязнений. (Б качестве растворителей наиболее часто применяют четыреххлсристый углерод, бензол, толуол, изопропиловый спирт, фреон и др., в которых эффективно растворяется большинство жировых загрязнений.)
Десорбция молекул жира с обрабатываемой поверхности происходит в результате их собственных колебательных движений и притяжения со стороны молекул растворителя. Если силы связи с поверхностью меньше сил притяжения молекулами растворителя, частицы жира отрываются от поверхности и благодаря диффузии распространяются по объему обрабатывающей жидкости. На счищаемую поверхность адсорбируются молекулы растворителя и могут также вновь попасть молекулы жира и загрязнения самого растворителя. Именно поэтому применяют счищенные растворители, вс время обезжиривания создают условия для максимальной растворимости и минимальной обратной адсорбции на обрабатываемую поверхность загрязнений из растворителя, а после обезжиривания удаляют с поверхности его остатки.
При выборе обезжиривающего состава необходимо учитывать, что большинство органических растворителей неполярны, они растворяют только неполярные органические загрязнения. Поэтому вначале неполярными или слабсполярными растворителями (бензолом, толуолом, четырехлсристым углеродом) удаляют неполярные загрязнения (парафины, еазелины, минеральные масла). Затем ацетоном, спиртами, трихлорэтиленом и другими полярными растворителями удаляют полярные загрязнения (жиры, белки, следы поверхностно активных веществ — ПАВ). Для интенсивного одновременного удаления полярных и неполярных органических загрязнений в промышленном производстве широко применяют смеси различных растворителей.
Определяющими параметрами процесса являются температура и время. Растворимость жиров увеличивается с повышением температуры. Поэтому обезжиривание осуществляют в горячих или кипящих растворителях. Обезжиривание в органических растворителях наиболее часто выполняют погружением в парах, с помощью ультразвука, струйной обработкой.
Ультразвуковая отмывка
Для проведения ультразвуковой отмывки используется ультразвуковая ванна. При использовании ультразвуковой ванны с частотами 20–50 кГц устранение загрязнений происходит за счет кавитационного эффекта. Явление кавитации заключается в «схлопывании» газовых пузырьков, образующихся при сжатии и расширении жидкости. При использовании ультразвуковой ванны, в растворе, омывающем пластину, создаются переменные сжимающие и растягивающие напряжения, под действием которых образуются кавитационные пузырьки.
35 Термічна очистка, вибір робочого середовища.
очистка отливок от пригара кварц, песка или от остатков оболочки (в литье по выплавляемым моделям) в растворах щелочей КОН или NaOH при температурах до 150°С или в расплавленных щелочах и солях при температурах.
Процесс очистки загрязненных деталей оборудования от полимеров осуществляется в печи особого типа при температуре от 300 до 500°C. В камере происходит пиролиз — расщепление полимеров на составные части, — переводящий пластмассу из твердого состояния в газообразное.
К 36. Дифузійнітехнологіябіполярного транзистора.
Диффузионнуютехнологиюнаиболееприменяют при изготовлениикремниевыхдиодов. Исходнымматериаломздесьтакжеслужиткремнийи-типа. Для созданияр-слояиспользуютдиффузию акцепторного элемента ( бора илиалюминия) через поверхностьисходногоматериала. Диффузияможетосуществляться в любомизтрехсостояний акцепторного вещества: твердом, жидкомилигазообразном. При диффузионномметодедостигаютсядостаточнаяточностьвыполненияглубины / - слоя и концентрацияпримеси в нем на большойплощадир-я-перехода, что важно для получениятребуемыхпараметровдиодов.
При диффузионнойтехнологии, технологиивытягиванияизрасплава и некоторых других видах технологии на поверхностиполупроводника не образуетсяслояметалла. В этомслучаеприходитсяпроизводитьдополнительнуюоперацию по созданиюомического ( невыпрямляющего) контакта.
37.Дифузійнатехнологіявиготовленнябіполярнихтранзисторів
Основным методом изготовления современных транзисторов является планарнаятехнология, а транзисторы, выполненные по этой технологии,
называютпланарными. У таких транзисторов p-n переходы эмиттер-база и коллекторбаза находятся в одной плоскости. Суть метода заключается в диффузии (вплавлении) в пластину исходного кремния примеси, которая может находиться в газообразной, жидкой или твердой фазе.
Как правило, коллектором транзистора, изготовленного по такой технологии, служит пластина исходного кремния, на поверхность которой вплавляют близко друг от друга два шарика примесных элементов. В процессе нагрева до строго определенной температуры происходит диффузия примесных элементов в пластину кремния.
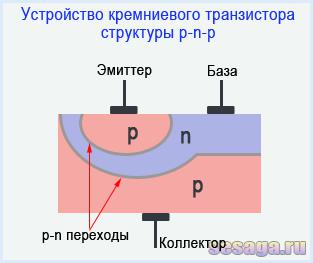
При этом один шарик образует в пластине тонкую базовую область, а другойэмиттерную. В результате в пластине исходного кремния образуются два p-n перехода, образующие транзистор структуры p-n-p. По такой технологии изготавливают наиболее распространенные кремниевые транзисторы.
Также для изготовления транзисторных структур широко используются комбинированные методы: сплавление и диффузия или сочетание различных вариантов диффузии (двусторонняя, двойная односторонняя). Возможный пример такого транзистора: базовая область может быть диффузионная, а коллектор и эмиттер – сплавные.
Использование той или иной технологии при создании полупроводниковых приборов диктуется различными соображениями, связанными с техническими и экономическими показателями, а также их надежностью.
38. Технологія алмазного скрайбування.
З перерахованих способів найбільше поширення знайшли: різання алмазним ріжучим диском, Скрайбування алмазним різцем і ла зерно Скрайбування з подальшою ламкою.
Різка алмазним ріжучим диском (ДАР) найбільш простий і легко здійсненний у Виробничих умовах спосіб різання напівпровідникових матеріалів. Алмазна кромка диска "володіє високою ріжучою здатністю.
Механізм різання напівпровідникового матеріалу ДАР наступний: кожне алмазне зерно являє собою мікрорезец, який знімає дрібні стружки з оброблюваної поверхні напівпровідникового матеріалу. Різка виробляється на високих швидкостях (близько 5000 об / хв), з одночасною участю у різанні великої кількості алмазних зерен, і внаслідок чого досягається висока продуктивність обробки. При різанні виділяється велика кількість тепла, тому ДАР необхідно охолоджувати водою або спеціальною рідиною, що охолоджує.
На малюнку 1 показана схема різання напівпровідникової пластини диском з зовнішньої алмазної ріжучої крайкою. Диск 1 встановлюється на шпинделі верстата і затискається з двох сторін фланцями 2. У процесі різання алмазний ріжучий диск обертається з великою швидкістю і охолоджується рідиною 3. Розрізаємо напівпровідникову пластину 4 закріплюють клеїть мастикою 5 на підставу 6.

Малюнок 1. Схема різання напівпровідникової пластини диском з зовнішньої алмазної ріжучої крайкою.
Для збільшення продуктивності на шпинделі верстата через прокладку розміщують декілька ДАР (у середньому до 200). Товщину прокладок вибирають в залежності від необхідних розмірів обробки.
Основним недоліком різання диском з зовнішньої ріжучої крайкою була "невисока жорсткість Інструменту (ДАР), що залежить в основному від співвідношення його розмірів (товщини і зовнішнього діаметра). Один із шляхів підвищення жорсткості інструмента (ДАР) - збільшення швидкості його обертання. Виникаючі 'при цьому відцентрові сили спрямовують по радіусу ДАР, надають йому додаткову жорсткість, однак при великій кількості оборотів (понад 10 000 об / хв) виникають вібрації верстата і ріжучого інструменту.
Інший шлях збільшення жорсткості - це застосування більш товсто основи ДАР, однак при цьому виходить велика ширина пропилу, також збільшуються втрати напівпровідникового матеріалу.
Жорсткість інструмента може бути збільшена також за рахунок зменшення різниці зовнішнього діаметра ДАР і притискних фланців або прокладок. Встановлено, що ДАР буде володіти більшою жорсткістю, якщо ріжуча кромка виступає за краї прокладок не більше ніж на 1,5 товщини розрізається матеріалу.
Сучасний ДАР (малюнок 2) являє собою алюмінієвий корпус, на якому електрохімічним методом обложений нікель (в якості сполучного матеріалу) з різними абразивними включеннями (для розділення напівпровідникових пластин, наприклад, використовують дрібні зерна алмазу розміром 3-5 мкм), а потім з частини корпусу нікель вилучений хім1 ческйм травленням для розтину ріжучої Кромки.

Малюнок 2. Сучасний ДАР:
1 - притискна прокладка; 2 - адгезійний матеріал; 3 - абразивний шар; 4 - алюмінієвий корпус; b - товщина леза; h - висота леза; d - посадковий діаметр ДАР; p - зовнішній (робочий) діаметр ДАР
При різанні пластин ДАР на швидкостях обертання інструменту вище 6700 про / с внаслідок інтенсифікації гідромеханічних процесів віку величина відколів в зоні різу. Проблема усунення цих явищ була вирішена в конструкції диска, де за рахунок введення тонкого шару алмазно-адгезійного матеріалу між абразивним шаром ріжучої кромки опорним кільцем диска забезпечується поглинання енергії коливань стоячих хвиль в ріжучій кромці і забезпечується більш висока якість юза.
Вдосконаленим варіантом ДАР є конструкція, що представляє собою найтонше лезо у формі кола, основою якого є еластичний компаунд з рівномірно розподіленими в ньому за обсягом алмазними зернами. Гонці лезо затискається між двома обкладинками, що надають йому жорсткість. Такий диск забезпечує отримання ширини різу, що дорівнює його товщині.
Алмазний ріжучий диск - своєрідний абразивний інструмент, і тому бічні площини кристала мають вигляд шліфованої поверхні. Завдяки використанню високих швидкостей руху ДАР можна різати тендітні, тверді та інші матеріми. Якість поділу пластин і зносостійкість дисків визначається, в першу чергу, точністю обладнання і правильним вибором технологічних режимів різання. Вибір оптимального технологічного режиму обробки визначається властивостями оброблюваних матеріалів, глибиною різання і допустимим рівнем сколів.
При поділі напівпровідникових пластин на кристали зі збереженням орієнтації дискову різання проводять на еластичних адгезійних носіях, що представляють собою полімерні стрічки з адгезійним шаром на поверхні, або на жорстких підкладках, у якості яких можуть використовуватися браковані кремнієві пластини, графіт, кераміка та інші матеріали. Для закріплення пластини найчастіше використовують "електронний" віск.
При використанні гнучкого носія пластини надрізаються до мінімальної перемички (~ 10мкм). Операція розламування на кристали, характерна при скрайбуванні,
відсутній, а здійснюється безпосередньо на операції монтажу, де кожен з кристалів знімається з адгезійного носія з подколи. Якість цього процесу в значній мірі визначається властивостями адгезійного носія, що забезпечує орієнтацію кристалів при обробці та межоперационной транспортуванні. Адгезійний носій за фізико-хімічними властивостями повинен бути сумісний з кремнієвим, а також мати виняткову рівномірністю клейового покриття, стабільністю адгезійних властивостей у воді (відмивання у воді після різання), високою пластичністю (розтягуватися в 1,5-2 рази) і здатністю зберігати напружене стан при розтягуючих зусиллях.
При виборі типу адгезійного носія необхідно враховувати розміри кристалів: чим більше кристал тим меншою адгезією повинен область носій. Ця вимога визначається необхідністю безперешкодного знімання при монтажі.
Напівпровідникова пластина, наклеєна на адгезійний носій - стрічку для збереження орієнтації розділених кристалів, закріплюється в касеті, що забезпечує натяг стрічки. Такі касети випускаються двох типів в різному конструкторському виконанні кільцеподібні і прямокутні.
Скрайбування є одним з методів розділення пластин на кристали, що полягає в тому, що на поверхню Напівпровідникової пластини різцем, лазерним променем або іншими способами наносять неглибоку ризику (англ. scribe), навколо якої концентруються механічні напруги, що послаблюють матеріали. Основною перевагою методу скрайбування поряд з високою продуктивністю та культурою виробництва є: мала ширина прорізу, а, отже, і відсутність втрат напівпровідникового, матеріалу, яких неможливо уникнути при використанні інших методів розділення пластини на кристали. Найбільш широко Скрайбування використовують в планарної технології виготовлення ІС, коли на пластині вже сформовані напівпровідникові структури.
Поділ здійснюється у дві стадії: спочатку пластини скрайбіруют, для чого ризики наносять між готовими структурами по вільному полю в двох взаємно перпендикулярних напрямках, а потім розламують по ризиках на прямокутні або квадратні кристали.
Операція розламування. Виробляється на спеціальному технологічному обладнанні. Якість скрайбування при механічному створення ризики різцем і подальшої ломки
в значній мірі залежить від стану робочої частини алмазного різця. Робота різців із зношеним ріжучим ребром або вершиною призводить до відколів при скрайбуванні та неякісної ломки. Зазвичай Скрайбування виконують різцями, виготовленими з натурального алмазу, які в порівнянні з більш дешевими різцями з синтетичних алмазів мають велику стійкість. Найбільшого поширення набули різці, мають ріжучу частину у формі тригранної або усіченої чотиригранної піраміди, ріжучими елементами якої є ребра піраміди.
Середня стійкість різця (одного різального ребра) при скрайбуванні кремнію становить 25-40 пластин діаметром 100 мм (3500 різів). Після скрайбування 25 - 40 пластин або при появ відколів на пластині різець необхідно проконтролювати під мікроскопом. Як показує досвід, застосовувати різці з зносом різального ребра більше 1015 мкм недоцільно, так як вони не забезпечують якісного скрайбування. Крім того, при надмірному зносі вершин різального ребра їх відновлення при переточуванні різця утруднено, до швидкого зносу різця призводить Скрайбування пластин з покриттям з оксиду кремнію або іонного діелектрика. На таких пластинах необхідно передбачати спеціальну (без покриття) доріжку напівпровідникового матеріалу шириною 50 - 75 мкм.
Широке застосування націю також лазерне Скрайбування напівпровідникових пластин, при якому надріз (ризику) утворюється не механічним, а електрофізичних способом - шляхом випаровування вузької смуги напівпровідникового матеріалу з поверхні пластини за допомогою сфокусованого лазерного пучка, що має велику потужність випромінювання.
Скрайбування променем лазера має велику перевагу перед скрайбування алмазним різцем: на робочій поверхні пластини не відбувається утворення мікротріщин і відколів
внаслідок відсутності механічного контакту "ріжучого інструменту" (лазерного променя) з напівпровідниковим матеріалом; швидкість скрайбування може бути збільшена в декілька разів (до 100 - 200 мм / с) завдяки тому, що промінь лазера завжди контактує з поверхнею пластини; можливо Скрайбування пластин з будь-яким, в тому числі з діелектричним покриттям; можливо не тільки Скрайбування на різну глибину, але і наскрізне поділ пластини (без наступного розламування їх на кристали) .
Розміри ризики - ширина і глибина, зона термічного впливу лазерного променя, а також швидкість скрайбування і рівномірність видалення матеріалу по всій довжині ризики визначається швидкістю переміщення пластин щодо лазерного променя, потужністю, частотою і тривалістю імпульсів лазерного випромінювання, а також розміром сфокусованого плями.
Сучасні установки лазерного скрайбування дозволяють отримувати ризики шириною близько 30 мкм і глибиною не менш 50 мкм при швидкості скрайбування понад 50 - 100 мм / с. Зона термічного впливу лазерного випромінювання становить при цьому не більше 50 - 75 мкм, включаючи ширину ризики. Скрайбування на велику глибину, в тому числі наскрізне поділ (на глибину до 200 мкм), виконують з меншою швидкістю (5-
10 мм / с).
До недоліків лазерного скрайбування слід віднести велику складність і вартість обладнання, а також необхідність спеціальних заходів захисту робочої поверхні від продуктів лазерної обробки, що утворюються в процесі випаровування матеріалу під впливом лазерного випромінювання.
39.Контроль та випробування виробів у електронній промисловості. Роль операцій контролю та випробувань. Види контролю та випробувань. Автоматизація контролю та випробувань
Вхідний контроль — перевірка якості сировини та допоміжних матеріалів які надходять у виробництво. Постійний аналіз якості сировини та матеріалів, які постачаються дозволяє впливати на виробництво підприємства –
постачальників,добиваючись підвищення якості. Цей контроль регулюється положеннями ГОСТ24297-87 "Входной контроль продукции.Основныеположения".
Вхідний контроль проводить підрозділ вхідного контролю, який входить до складу служби технічного контролю підприємства. Задачами контролю є перевірканаявності супроводжуючої документації на продукцію, відповідність
продукціїнормам конструкторської та нормативно-технічної документації, накопичення данихпо фактичному рівню якості продукції, що отримується, і розробці пропозицій попідвищенню якості та перегляду вимог НТД на продукцію, періодичний контроль заправилами та строками зберігання продукції постачальників.
Вхідний контроль проводять в спеціальному приміщенні, обладнаному необхіднимобладнанням для контролю, випробування та оргтехнікою, які відповідають вимогамохорони праці.
Класифікація показників якості На стадії експлуатації конструкції розробляються програми якості по таких напрямках:
-проектні (оцінка проектної документації); -виробничо-технологічні (підготовка виробництва, а саме обладнання, робітників, робочих місць); -експлуатаційні (по умовах експлуатації данного виробу);
-прогнозуючі (з урахуванням умов експлуатації конструкції).При виготовленні зварних конструкцій деякі властивості матеріалів,такі, як розміри, а також металургійні та температурні показникиможуть змінюватись, що призведе до зміни показників якості. Ці
та інші важливі показники якості для конкретногонапрямупродукції впливають нанайголовніший показник якості – експлуатаційну надійність. Експлуатаційною надійністю називають здатність виробу виконувати задані функції, при збереженні своїх експлуатаційних показників, в заданих межах і на протязі певного проміжку часу. Точно цей показник визначити неможливо, адже для його визначення треба відстежувати весь цикл роботи конструкції, або проводити статичні випробування, що є великою
тратою часу та коштів. Тому замість експлуатаційної надійностівикористовують показник виробничої або виробничо-технологічної надійності – величини, які не можуть бути виміряні кількісно.
Заготівкам до зварювання, показник якості яких Ні, присвоємо умовне значення
1,0. При виконанні зварювання з’єднання зазнає технологічних rт –технологічнихвтрат, за рахунок зміни властивостей основного матеріалу при зварюванні тавиробничих rв – виробничих втрат, за рахунок зварювальних дефектів. Виробничі татехнологічні втрати об’єднуть і називають однією назвою виробничо-технологічнівтрати rВТ.
На стадії експлуатації конструкція «зношується» і це приводить до втрати якості,яка позначається Dе – експлуатаціїні втрати. Нтв – це потенційна якість конструкції. ЇЇможна спрогнозувати, визначивши DТ та DВ за допомогою руйнівних тестів, якіімітують умови експлуатіції конструкції.
Всі випробування класифікують:
-за методами проведення
-за призначенням
-за етапами проектування, виготовлення та випуску
-за видами готової продукції
-за тривалістю
-за рівнем проведення
-за видами впливу, що визначаютьсяхарактеристикам об'єкту.
К.40 Етапи розробки виробів та технології, технічна документація.Технічне завдання, технічні умови на виріб. Основні види конструкторської та технологічної документації. Системи стандартів ЕСКД, ЕСТД, ЕСТПВ.
Техні чнадокумента ція— система графічних і текстових документів, необхідних і достатніх для безпосереднього використання на усіх стадіях життєвого циклу продукції[1] (конструюванні, виготовленні та експлуатації промислових виробів; при проектуванні, зведенні і експлуатації будівель і споруд; при розробці технологічних процесів виробництва; при розробці та використанні програмного забезпечення).
Констру кторськадокумента ція (КД—) частина технічної документації у вигляді графічних і текстових документів, котрі в сукупності або окремо, визначають склад і будову виробу та містять необхідні дані для його розробки, виготовлення, контролю, експлуатації, ремонту і утилізації.
Система конструкторської документації (СКД) — комплекс національних стандартів, які встановлюють взаємопов'язані правила розробляння, оформлювання та обігу конструкторської документації[1]. В Україні СКД базується на Єдиній системі конструкторської документації — комплексі державних та міждержавних стандартів, що бере свій початок від СКД, створеної у колишньому СРСР.
ЕСКД - Єди насисте маконструкторськоїдокумента ції (ЄСКД—) комплекс державних стандартів, що встановлюють взаємопов'язані правила, вимоги і норми по розробці, оформленню і обігу конструкторської документації, що розробляється і застосовується на усіх стадіях життєвого циклу виробу (при проектуванні, розробці, виготовленні, контролі, прийманні, експлуатації, ремонті, утилізації).