
Процессы формообразования_методичка по л-р
.pdf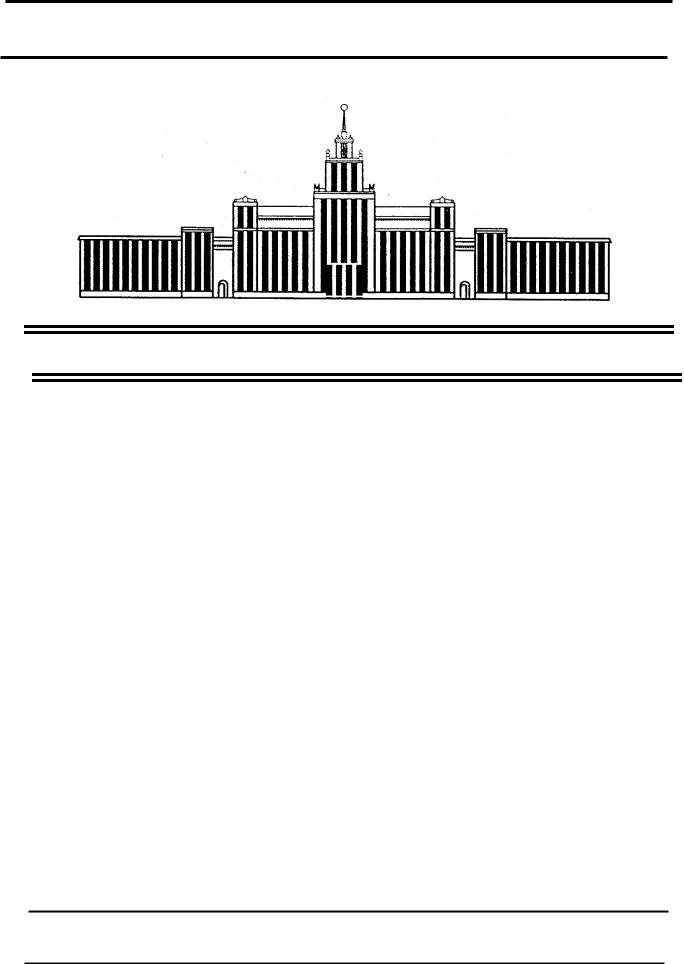
МИНИСТЕРСТВО ОБРАЗОВАНИЯ И НАУКИ РОССИЙСКОЙ ФЕДЕРАЦИИ
ЮЖНО-УРАЛЬСКИЙ ГОСУДАРСТВЕННЫЙ УНИВЕРСИТЕТ
621(07) А799
Д.В. Ардашев, С.Ф. Плаксин
ПРОЦЕССЫ И ОПЕРАЦИИ ФОРМООБРАЗОВАНИЯ. РЕЖУЩИЙ ИНСТРУМЕНТ
Учебное пособие по выполнению лабораторных работ
Челябинск
2013
Министерство образования и науки Российской Федерации Южно-Уральский государственный университет Кафедра «Технология обработки материалов»
621(07) А799
Д.В. Ардашев, С.Ф. Плаксин
ПРОЦЕССЫ И ОПЕРАЦИИ ФОРМООБРАЗОВАНИЯ. РЕЖУЩИЙ ИНСТРУМЕНТ
Учебное пособие по выполнению лабораторных работ
Челябинск Издательский центр ЮУрГУ
2013
1
УДК 621.9.02(07)
Одобрено учебно-методической комиссией филиала ЮУрГУ в г. Кыштыме
Рецензенты:
Н.А. Дружинин, Э.Р. Логунова
Ардашев, Д.В.
А799 процессы и операции формообразования. Режущий инструмент: учебное пособие по выполнению лабораторных работ / Д.В. Ардашев, С.Ф. Плаксин.
– Челябинск: Издательский центр ЮУрГУ, 2013. – 49 с.
Учебное пособие содержит сведения о физических явлениях, возникающих в процессе резания металлов и методики определения зависимости этих явлений от параметров режима резания. Также рассмотрены устройства, геометрия режущей части токарных резцов и способы её измерения.
Пособие предназначено для студентов направления 151900 «Конструкторскотехнологическое обеспечение машиностроительных производств» всех форм обучения.
УДК 621.9.02(07)
© Издательский центр ЮУрГУ, 2013.
2
Оглавление |
|
Лабораторная работа №1........................................................................................... |
5 |
Геометрические параметры режущей части резцов................................................. |
5 |
Цель работы................................................................................................................ |
5 |
1.1. Общие положення. Основные типы резцов....................................................... |
5 |
1.2. Конструктивные и геометрические параметры резцов..................................... |
7 |
1.2.1. Конструктивные элементы резца .................................................................... |
7 |
1.2.2. Геометрические параметры резца ................................................................... |
7 |
1.2.3. Углы резца в процессе резания...................................................................... |
11 |
1.2.4. Контроль геометрических параметров резца................................................ |
12 |
1.3. План работы....................................................................................................... |
15 |
Лабораторная работа №2......................................................................................... |
16 |
Процесс деформации срезаемого слоя при резании металлов .............................. |
16 |
Цель работы.............................................................................................................. |
16 |
2.1. Общие положения............................................................................................. |
16 |
2.1.1. Пластическая деформация металла в процессе резания и усадка |
|
стружки..................................................................................................................... |
16 |
2.1.2. Виды стружки образующейся в процессе резания....................................... |
19 |
2.1.3. Методы определения коэффициента усадки стружки.................................. |
20 |
2.2. Проведение работы ........................................................................................... |
21 |
2.2.1. Условия проведения опытов.......................................................................... |
21 |
2.2.2. Подготовка к опытам ..................................................................................... |
22 |
2.2.3. Методика проведения опытов ....................................................................... |
22 |
2.2.4. Графическая обработка опытных данных..................................................... |
23 |
Библиографический список..................................................................................... |
23 |
Лабораторная работа №3......................................................................................... |
24 |
Силы резания при точении...................................................................................... |
24 |
Цель работы.............................................................................................................. |
24 |
3.1. Общие положения............................................................................................. |
24 |
3.2. План работы....................................................................................................... |
25 |
3.2.1. Графоаналитический способ.......................................................................... |
27 |
3.2.2. Аналитический способ................................................................................... |
29 |
3.2.3. Механический динамометр ДК-1. Назначение, конструкция и |
|
работа........................................................................................................................ |
29 |
3.2.4. Тарирование динамометра............................................................................. |
30 |
3.3. Порядок проведения опытов............................................................................. |
32 |
Лабораторная работа №4......................................................................................... |
33 |
Исследование температурных зависимостей при точении.................................... |
33 |
Цель работы.............................................................................................................. |
33 |
4.1. Общие сведения................................................................................................. |
33 |
4.1.1. Метод естественной термопары.................................................................... |
34 |
3 |
|
4.2. Методика проведения работы........................................................................... |
36 |
4.2.1. Графоаналитическая обработка результатов эксперимента ........................ |
36 |
4.3. План проведения работы .................................................................................. |
39 |
Библиографический список..................................................................................... |
39 |
Лабораторная работа №5......................................................................................... |
40 |
Определение оптимального износа резца............................................................... |
40 |
Цель работы.............................................................................................................. |
40 |
5.1. Общие сведения................................................................................................. |
40 |
5.1.1. Геометрические характеристики изношенных............................................. |
42 |
поверхностей режущих инструментов.................................................................... |
42 |
5.1.2. Критерии износа резцов................................................................................. |
43 |
5.1.3. Средства измерения величины износа по задней грани резца..................... |
46 |
5.2. Методические указания по проведению лабораторной работы ..................... |
47 |
5.2.1. Объекты работы, оборудование, приборы.................................................... |
47 |
и инструменты для проведения работы.................................................................. |
47 |
5.2.2. Порядок выполнения работы......................................................................... |
48 |
5.2.3. Порядок заполнения отчета........................................................................... |
48 |
Библиографический список..................................................................................... |
49 |
4
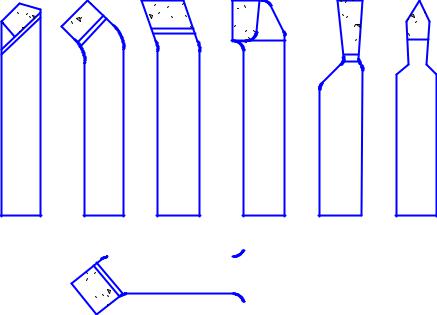
Лабораторная работа №1
Геометрические параметры режущей части резцов
Цель работы
1.Ознакомление с основными типами токарных резцов.
2.Изучение методов контроля геометрических параметров резцов.
3.Изучение конструктивных и геометрических параметров заданного токарного резца.
1.1. Общие положення. Основные типы резцов
Резец является наиболее распространенным инструментом в металлообрабатывающей промышленности. Он применяется при работе на токарных, револьверных, карусельных, расточных, строгальных, долбежных станках, токарных автоматах, полуавтоматах и на многих станках специального назначения. Многообразие использования резцов породило множество форм конструкций и геометрических параметров их, которые меняются в зависимости от вида станка и рода выполняемой работы.
Резцы разделяются на следующие виды:
По виду станка: токарные (рис. 1.); строгальные (рис. 2 а); долбежные (рис. 2 б); резцы для автоматов и полуавтоматов; фасонные (рис. 2 в) и т.д.
По виду обработки: проходные (рис. 1 а, б); подрезные (рис. 1 в); отрезные (см. рис. 1 д); прорезные; расточные (рис. 1 ж); фасонные (рис. 2 в); резьбонарезные (рис. 1 е).
По установке относительно детали: радиальные (рис. 1); тангенциальные.
а) |
б) |
в) |
г) |
д) |
е) |
|||
|
|
|
|
|
|
|
|
|
|
|
|
|
|
|
|
|
|
|
|
|
|
|
|
|
|
|
ж)
Рис. 1. Классификация резцов по виду обработки
5
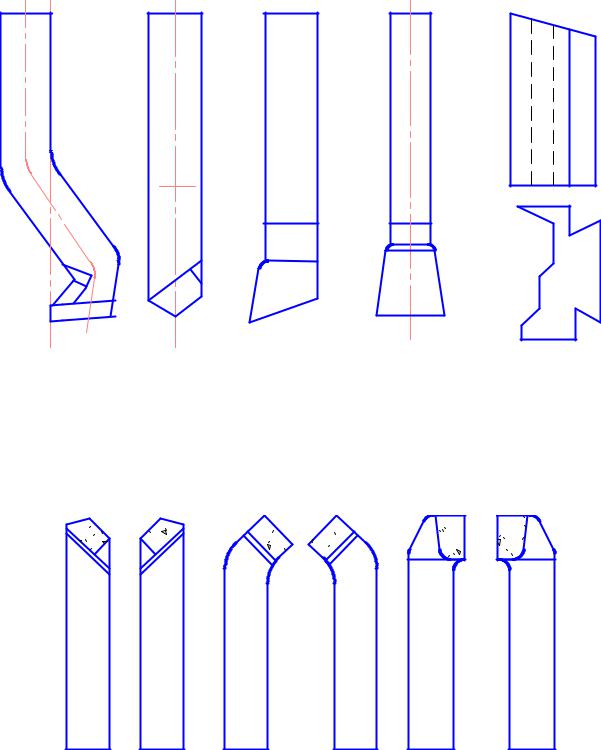
Рис. 2. Классификация резцов по виду станков
По характеру обработки: обдирочные (черновые); чистовые; для тонкого точения.
По сечению стержня: прямоугольные; квадратные; круглые.
По конструкции головки: прямые (см. рис. 1 а); отогнутые (см. рис. 1 б, в); изогнутые (см. рис. 2 а); оттянутые (см. рис. д, е).
По направлению подачи: правые (см. рис. 1 а, б, в, г; рис. 3); левые (рис. 3).
левый правый левый |
правый левый |
правый |
Рис. 3. Классификация резцов по направлению подачи
По способу изготовления: с головкой, сделанной заодно целое со стержнем; с приваренной или припаянной пластинкой (см. рис. 1); с механическим креплением пластинки и т.д.
По роду материала: с пластинками из твердого сплава; из быстрорежущей стали; с пластинками из минералокерамики.
6

1.2. Конструктивные и геометрические параметры резцов
1.2.1. Конструктивные элементы резца
Резец состоит из головки А, т.е. рабочей части и тела, или стержня Т (рис. 4.), служащего для закрепления резца в резцедержателе.
4 6 5
А 1
5
3
B |
А |
Т |
|
H |
|
1 |
|
|
Т |
4 |
|
B•H
6 2
Рис. 4. Конструктивные элементы резца
Рабочая часть (головка) А принимает непосредственное участие в процессе резания. Она образуется специальной заточкой и состоит из следующих элементов (см. рис. 4.): передней поверхности 1, по которой в процессе резания сходит стружка; главной задней поверхности 2, обращенной к поверхности резания; вспомогательной задней поверхности 3, обращенной к обработанной поверхности; главной режущей кромки 4, образованной пересечением передней и главной задней поверхностей; вспомогательной режущей кромки 5, образованной пересечением передней и вспомогательной задней поверхностей; вершины резца 6, являющейся местом сопряжения главной и вспомогательной режущих кромок.
При криволинейном сопряжении режущих кромок вершина имеет скругленную форму радиуса r (рис. 6, 7 и 9). Радиус r называется радиусом при вершине.
1.2.2. Геометрические параметры резца
Для облегчения процесса резания режущая часть резца имеет форму клина, заточенного с определенными углами. На рис. 5. представлены поверхности на заготовке и координатные плоскости при точении, необходимые для определения геометрических параметров резца.
7
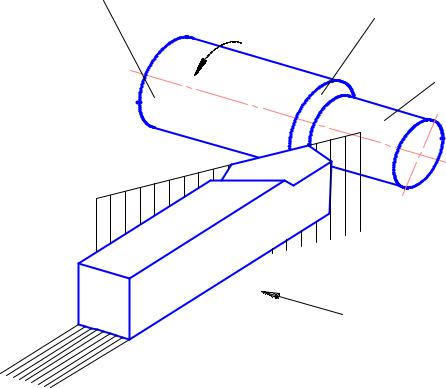
Обрабатываемая
поверхность
Поверхность резания
Обработаныя
v
поверхность
Плоскость резания
S
Основная плоскость
Рис. 5. Схема расположения поверхностей заготовки и резца
На обрабатываемой заготовке (см. рис. 5) различают следующие поверхности: обрабатываемую, обработанную, и поверхность резания.
Обрабатываемой называется поверхность заготовки, которая будет удалена в результате обработки.
Обработанной называется поверхность, полученная после снятия стружки. Поверхностью резания называется поверхность, образуемая на обрабатываемой заготовке непосредственно главной режущей кромкой. Поверхность резания является переходной между обрабатываемой и обработанной поверхностями.
Ккоординатным плоскостям относят плоскость резания и основную плоскость (см. рис. 5).
Плоскость резания – это плоскость, проходящая через главную режущую кромку резца касательно к поверхности резания.
Основной плоскостью называют плоскость, параллельную векторам продольной и поперечной подач резца.
Кглавным углам резца относят передний угол γ, главный задний угол α, угол резания δ и угол заострения β резца.
Эти углы измеряются в главной секущей плоскости, проходящей перпендикулярно к проекции главной режущей кромки на основную плоскость. След главной секущей плоскости А – А представлен на рис. 6.
8

|
|
|
|
А-А |
|
|||
|
|
|
|
|
|
|
|
|
Б |
А |
|
|
|
|
|
|
|
|
|
|
|
|
|
|
|
|
r |
Б |
|
|
|
|
|
|
|
|
|
|
|
|
|
|||
|
А |
|
|
Б-Б |
|
|
|
|
|
|
|
|
|
|
|
|
|
|
|
|
|
|
|
|
||
|
|
|
|
1 |
|
|||
|
|
|
|
|
||||
|
|
|
|
|
|
|
||
|
|
|
|
|
|
|
|
|
|
|
1 |
|
|
|
|
|
|
|
|
|
|
|
|
|
||
|
|
|
|
|
|
|
|
|
Рис. 6. Углы резца в главной и вспомогательной секущих плоскостях
Передним углом γ называется угол между передней поверхностью резца и плоскостью, проходящей через главную режущую кромку перпендикулярно к плоскости резания (см. рис. 6).
При неплоской передней поверхности передний угол γ образован плоскостями, проходящими через главную режущую кромку резца, из которых одна – касательна к передней поверхности резца, а другая – перпендикулярна к плоскости резания.
Главный задний угол α – это угол между главной задней поверхностью резца и плоскостью резания.
Углом резания δ называется угол между передней поверхностью резца и плоскостью резания.
Угол заострения β – угол ме5жду передней и главной задней поверхностями резца.
При положительном переднем угле γ между углами существуют следующие зависимости:
α+β+γ=90°; |
α + β = δ; |
δ = 90° – γ; |
δ + γ=90°. |
При отрицательном переднем угле γ угол резания δ>90°.
Кроме рассмотренных главных углов, резец характеризуется вспомогательным задним α1 и передним γ1 углами. Эти углы рассматриваются во вспомогательной секущей плоскости Б – Б (см. рис. 6). Обычно на чертеже оговаривается лишь угол α1.
Вспомогательным задним углом α1 (см. рис. 6) называется угол между вспомогательной задней поверхность и поверхностью, проходящей через вспомогательную режущую кромку перпендикулярно основной плоскости.
9