
Литература / 106265
.pdf
Глава 5. МЕХАНИЗМ ПРОИЗВОДСТВЕННОЙ СИСТЕМЫ ТОЙОТЫ |
157 |
Для улучшения размещения необходимо предпринять несколько шагов. Первый — различные станки следует разместить в соответствии с технологическим маршрутом обработки продукции. Компоновка производственных участков по типам станков (например, участок прессов или токарный участок) только увеличивает транспортировку. Рассмотрим следующие варианты:
•линия одного процесса — для месячного производства одного изделия и одной модели в больших количествах;
•линия общих процессов — для случаев, когда производство од ного изделия в течение месяца нецелесообразно, но изделия А, В, С и D имеют общие процессы, которые можно выстроить в непрерывный поток;
•линия схожих процессов — изделия А, В, С, D, Е и F имеют некоторые, но не все, общие процессы, так что из них можно сформировать только отдельные линии общих процессов.
В компании Toyota чаще всего используются линии общего процесса. При этом у большинства заводов гораздо меньше общих процессов, поэтому на них должны использоваться линии схожих процессов*.
Улучшение размещения линии приносит следующие выгоды:
•устранение трудозатрат на транспортировку;
•более быстрое получение информации о качестве, что способствует снижению уровня дефектности;
•снижение трудозатрат за счет сокращения или устранения задержек процесса и задержек партий; •сокращение цикла производства.
Сокращение цикла производства способствует внедрению производства, основанного на заказах, и помогает снизить запасы готовой продукции. При устранении задержек двух типов между процессами беззапасное производство становится возможным.
Хотя формирование линии имеет много преимуществ, оно связано с определенными трудностями. Наибольшая потенциальная проблема обусловлена объединением станков с разной производительностью внутри одного процесса или между процессами. Как от-
Чтобы определить самое эффективное размещение станков для ваших конкретных требований, см. разд. «Улучшение размещения» (Improving Layout) в книге
Сигео Синго «Производство без запасов: система непрерывного улучшения Синго»
(«Non-Stock Production: The Shingo System for Continuous Improvement» Cambridge, MA: Productivity Press, 1988, с 326-328).

158 |
Часть II |
мечалось выше, производительность станка не считается в компании Toyota фактором управления производством. При беззапасной системе за каждый цикл производится не больше продукции, чем требуется. Поэтому вполне приемлемы станки низкой производительности, если они производят требуемое количество, и даже если производительность станка высока, перепроизводство не допускается. В идеале производительность станков должна соответствовать требованиям производства, но фактически высокопроизводительные станки применяются даже тогда, когда их нельзя использовать полностью.
В компании Toyota поиски путей решения этой проблемы привели к дальнейшим улучшениям. Между высоко- и низкопроизводительными станками создают небольшой запас. Когда он достигает 20 изделий, операция высокопроизводительного станка останавливается. Она возобновляется, когда запас падает до 5 изделий. Обычно высокопроизводительные станки чередуются с низкопроизводительными для синхронизации процессов и поддержания минимального уровня запасов.
Все это — полное управление работой, определяемое как метод управления, предусматривающий прекращение операций, когда запасы на максимуме. Таким образом, общий объем производства в конечном счете соответствует требуемому.
При данном методе управления высокая производительность станков не требуется, а часто и нежелательна. Чтобы выполнить заказ, необходимо придерживать работу станков, даже если это приводит к низкой производительности. Если данная идея не усвоена, полное управление работой не может применяться.
При объединении метода создания производственных линий, позволяющих осуществить выравнивание объема, синхронизацию и создать поток единичных изделий, с одной стороны, с системой SMED для производства малыми партиями, с другой, система полного управления работой позволяет сокращать цикл производства в геометрической прогрессии.
Синхронизация операций и уменьшение отклонений. Синхронизация или балансирование линии важны в любом потоке операций. Поэтому нужно прилагать все усилия, чтобы разделять задачи и стандартизировать операции для минимизации потерь, вызываемых дисбалансом.
Однако на практике, независимо от тщательности планирования и выполнения операций, будут возникать некоторые отклонения от стандартного времени. Например, резьба винта может оказаться
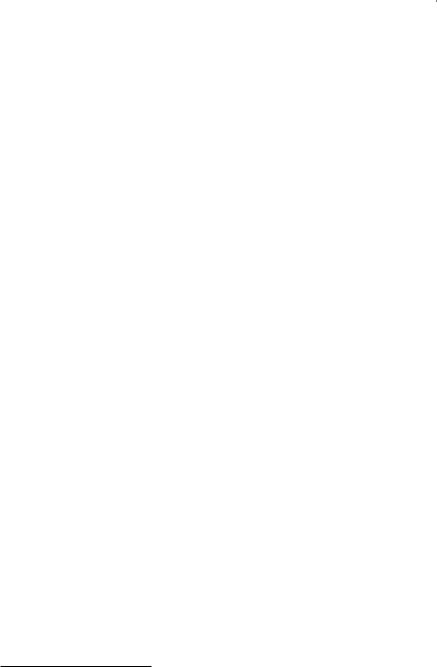
Глава 5. МЕХАНИЗМ ПРОИЗВОДСТВЕННОЙ СИСТЕМЫ ТОЙОТЫ |
159 |
слишком тугой, поэтому потребуется немного больше времени на завинчивание. Винт можно уронить и потерять время, пока берешь другой. Маленькие проблемы непременно возникают, поэтому нельзя избежать некоторого отклонения от стандартного времени.
Обычно для решения таких проблем мы используем буферный запас между рабочими участками. Если рабочие заканчивают работу быстрее предписанного графика, они производят обработку изделий в запас; когда же один рабочий задерживается, следующий берет детали из его буферного запаса, а запоздавший старается наверстать упущенное время, работая в следующем цикле быстрее. Вот так буферный запас между рабочими участками предупреждает задержки между процессами.
Если запасы служат лишь в качестве буфера, то для хранения между процессами вполне достаточно одного изделия, однако на практике их обычно несколько или даже очень много.
•Ящики для деталей. Ширина рабочей области, достаточная для комфортной работы, составляет около 75 см. Однако если не обходимо большое количество деталей, эти стандартные пара метры часто игнорируются: используется два или три ящика, следовательно, занимаемая площадь увеличивается. В таких ситуациях область хранения между рабочими можно сократить, применив ящики с несколькими отделениями.
Кроме этого, на операциях сборки фактически в любое время требуется только одна единица данной детали, что подсказывает несколько решений. Можно сконструировать вращающиеся ящики, позволяющие получать только одну необходимую в данное время деталь. Такие же функции могут выполнять и другие устройства, но выстроенные в трех измерениях, а не в двух, т. е. расположенные вертикально, а не по сторонам. Подобные решения предупреждают «размножение» ящиков для деталей и сдерживают увеличение необходимой рабочей площади.
•Исключение отклонений от стандартного времени. Применение описанных процедур помогает минимизировать запасы между процессами, но в компании Toyota такие запасы вообще не допускаются. Для поглощения отклонений от стандартного времени компания Toyota использует систему взаимной помощи*. При возникновении задержки рабочие помогают друг другу, а не накапливают запас. Для групповых операций работни-
Mutual assistance system.
160 |
Часть II |
ки компании Toyota применяют две эстафетные системы, используемые в спорте: эстафета в плавании и эстафета в легкой атлетике.
В плавании пловцу следующего этапа не позволяется прыгать в воду, пока пловец предыдущего этапа не коснется стенки бассейна, — таким образом, быстрый пловец (рабочий) работает со скоростью более медленного. А в беге, например, возможны варианты: а) если первым бежит более быстрый бегун, то эстафетная палочка может быть передана менее быстрому спортсмену в конце зоны передачи эстафетной палочки; б) если скорость бега выше у спортсмена на следующем этапе, то передача осуществляется в начале зоны, так что более быстрый помогает менее быстрому.
Такая система взаимной помощи позволяет снизить отклонения от стандартного времени между процессами без создания запасов.
Установление тактового времени. Такт — время производства одного изделия. Это время эквивалентно полному рабочему времени, деленному на количество произведенных изделий. Не следует думать, что снижение времени такта обязательно связано с повышением производительности. Например, 10 рабочих могут произвести 100 изделий. После улучшения условий работы они могут произвести 120 изделий. Но это не значит, что им следует делать 120 изделий в день. Если требуется всего 100 изделий, реальное улучшение достигается тогда, когда необходимый объем производит меньшее число рабочих —ь производство ненужной продукции не является повышением производительности.
В целом тактовое время можно вычислять исходя либо из требуемого объема производства, либо из реальной производительности рабочих и станков. Принятие того или иного метода расчета не вызывает затруднений, хотя следует проявлять осторожность. Например, было бы странно превышать ограничение скорости только потому, что автомобиль может ехать быстрее. Поскольку производственная система компании Toyota основана на том, что перепроизводство — это потери, тактовое время вычисляется исходя из требуемого объема производства.
Обеспечение производственного потока между процессами. Методология производства компании Toyota будет логически законченной, когда приведет производственную систему к идеальному состоянию, в котором все операции — от изготовления заготовок
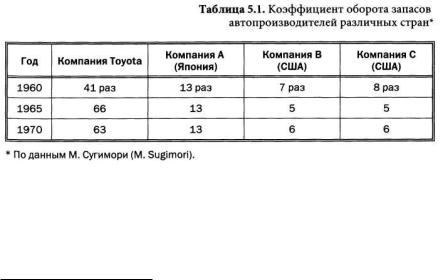
Глава 5. МЕХАНИЗМ ПРОИЗВОДСТВЕННОЙ СИСТЕМЫ ТОЙОТЫ |
161 |
(ковки, литья, штамповки) до их обработки, а затем предварительной, промежуточной и конечной сборки — связаны в гармоничный производственный поток единичных изделий. Хотя такая интеграция полностью еще не достигнута, Toyota разработала систему частых поставок малыми партиями с заводов изготовителей (например, рамного и окрасочного) на линию сборки.
Крайне частая поставка деталей и узлов от процессов, предшествующих окончательной сборке, создает поток продукции, приближающийся к состоянию всеобщей системы, описанной выше. На заводах компании Toyota часто встречаются погрузчики-трейлеры с надписью «Приоритетная поставка»*. Они доставляют небольшие смешанные партии деталей, которые требуются для конечной сборки и не могут быть задержаны. Когда они проезжают по цеху, даже президент компании уступает им дорогу. Аналогично погрузчики транспортируют детали с участков ковки, отливки и штамповки прямо на обработку.
Все эти действия согласованы с тактовым временем и управляются с помощью системы канбан. Работа столь упорядочена и происходит с такой скоростью, что ее иногда называют «вихревой системой». Успех отражается в показателях скорости оборота запасов компании Toyota. В табл. 5.1 приведены значения этого показателя у компании Toyota и других автопроизводителей.
Внедрение системы SMED
Можно сказать без преувеличения, что главным фактором успеха производственной системы Тойоты является впечатляющее со-
«Priority Vehicle». 6 – 3441

162 |
ЧАСТЬ II |
кращение времени замены штампов и инструментов. Производство, основанное на заказах, и беззапасное производство требуют максимального сокращения времени переналадки.
Первые дни SMED
Когда в 1970 году я в первый раз посетил компанию Toyota, время переналадки 1000-тонного пресса составляло 4 часа — вдвое больше, чем в компании Volkswagen. Примерно через шесть месяцев наши усилия позволили снизить это время до 1,5 часа. Все были в восторге, так как мы побили Volkswagen.
Однако когда через 2-3 месяца я вернулся в компанию Toyota, высшее руководство потребовало, чтобы время переналадки было снижено до 3 минут. Сначала я счел это нереальным требованием. Но после изучения производственной системы Тойоты я понял, что столь невероятно короткое время переналадки (которого нельзя, повидимому, добиться без SMED) было крайне необходимо для достижения основанного на заказах и беззапасного производства.
Вначале я не знал, как достичь такого резкого сокращения. Но вскоре пришло вдохновение: «А что если преобразовать внутренние действия во внешние!». Этот фундаментальный принцип SMED позволил снизить время переналадки до 3 минут уже через несколько месяцев.
В одном экономическом журнале было написано, что значительного сокращения времени переналадки в компании Toyota удалось добиться потому, что были ликвидированы частые простои рабочих. Это — чрезвычайно поверхностное объяснение, показывающее, что автор плохо понимает сущность производственной системы Тойоты. Сокращение времени переналадки никогда не было вопросом интенсивности труда, прежде всего это — результат изменения мышления и применения научных методов, основанных на особом подходе к решению проблемы.
Другие авторы, пытаясь объяснить успехи SMED в компании Toyota инженерными навыками, вычислили, что потребовалось 340 тыс. практических нововведений, что равносильно 30 человеко-го- дам, чтобы сократить замену с 3 часов до 3 минут. С их точки зрения достижение было в основном результатом обучения, хотя признавалась роль усовершенствованных приспособлений, оснастки и методов переналадки, а также проворность и энтузиазм рабочих компании Toyota.
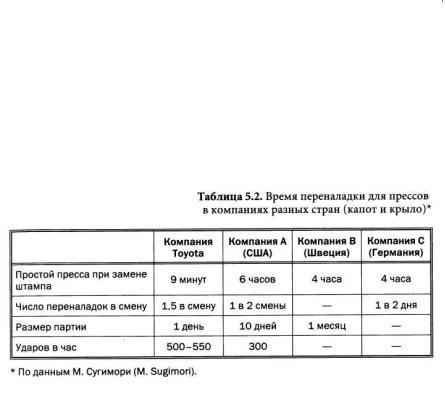
Глава 5. МЕХАНИЗМ ПРОИЗВОДСТВЕННОЙ СИСТЕМЫ ТОЙОТЫ |
163 |
Однако на то, чтобы снизить время переналадки с 3 часов до 3 минут, фактически ушло лишь 3 месяца. И это решение было найдено скорее с помощью научных принципов SMED, нежели инженерных навыков. Я мог бы привести тысячи примеров других японских предприятий, показывающих, что время установки инструментов и переналадки штампов можно снизить приблизительно на 95 % за несколько месяцев. Как только мы сравним показатели времени переналадки в компании Toyota и компаниях других стран, мы сможем оценить впечатляющие достижения компании Toyota в снижении времени переналадки (табл. 5.2).
Важные аспекты системы SMED
Как уже говорилось, за 10 лет практического применения сформировалось 8 основных способов или принципов замены инструментов и штампов. Важнейшие из них:
1.Четко различайте внутренние и внешние действия. 2.Преобразуйте внутренние действия во внешние. 3.Усовершенствуйте функциональные зажимы (рассмотрите «безрезьбовой» крепеж).
4.Устраните регулировки.
Последние два принципа требуют более детального рассмотрения.
6*

164 |
ЧАСТЬ II |
Функциональные зажимы
При креплении болтов и гаек должны выполняться следующие 3 действия:
1)поместите гайку на верхнюю часть болта и проверните ее один раз, чтобы закрепить; 2)продолжайте вращать гайку;
3)на последнем витке затяните ее с требуемым моментом.
Из трех перечисленных действий труднее всего первое. Если гайка не сцентрирована и не помещена на болт точно под нужным углом, она не войдет в резьбу болта. Почему бы не рассмотреть возможность затяжки и ослабление болта без снятия с него гайки? И как можно вообще работать, осознавая факт, что болты и гайки ослабляются на первом обороте, а разъединяются на последнем витке резьбы?
Удивительно, но эти простые в общем-то вещи понимают не все. Однажды я поставил рабочим задачу сменить штамп без проворачивания либо гайки, либо болта более чем на один оборот. Они должны были платить мне 500 долл. за каждый лишний оборот! Чтобы избежать этих штрафов, они внесли следующие усовершенствования:
1.12 болтов закрепляли крышку вулканизационной камеры. Отверстия для болтов в крышке вырезали в форме старомодных отверстий для ключей, а болты закрепили U-образными шайбами (рис. 29, а). После одного оборота гаек шайбы можно вынуть, и при вращении крышки против часовой стрелки к большей стороне ключевого отверстия крышка снимается без удаления или даже касания гаек. Это значительно сократило время замены штампа.
2.В операции намотки проволоки в компании S Industry для снятия изделия необходимо было сначала снять гайку, а затем шайбу. Этот процесс был улучшен использованием гайки с внешним диаметром, меньшим, чем внутренний диаметр в сердечнике намотки, закрепляющей его U-образной шайбой (рис. 29,6). Теперь для вынимания сердечника гайка ослабляется на 1 оборот и шайба вытаскивается. Затем без касания гайки вынимается сердечник. Это сократило время между операциями до Хо от прежнего.
В результате внедрения подобных устройств в американской компании F.M. двухчасовое время замены было сокращено до 2 минут.
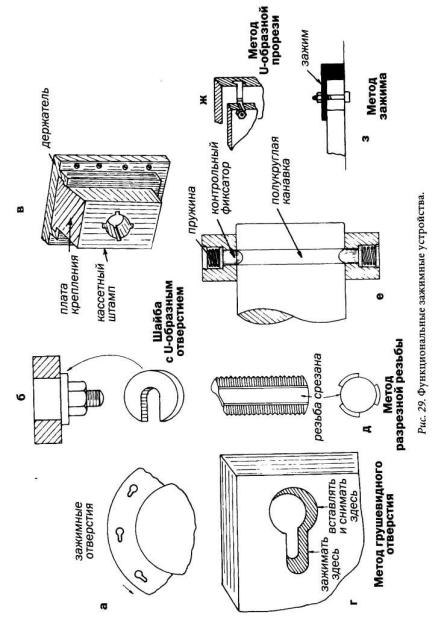
Глава 5. МЕХАНИЗМ ПРОИЗВОДСТВЕННОЙ СИСТЕМЫ ТОЙОТЫ |
165 |

166 |
ЧАСТЬ II |
Предложенное решение показано на рис. 29, д. Оно работает так: резьба срезается на трех участках окружности болта и трех соответствующих участках гайки (которая немного толще обычной). Это делает возможным насадить гайку на болт до требуемой глубины и повернуть один раз, чтобы затянуть ее и закрепить в одно касание.
Функциональные зажимы без резьбы. Рассмотрим теперь другой подход — зажим без резьбы, снижающий время переналадки еще более эффективно.
Цель затяжки резьбовых винтов — закрепление объекта, но винт — лишь один путь для этого. Однако многие инженеры считают винты универсальным методом закрепления и не думают применять нерезьбовые устройства, такие, как кулачки и клинья. Различные схемы зажима и «кассетный» метод — это другие возможные методы (рис. 29, ву г, з).
Во всех таких случаях важно учесть направление, в котором будет прилагаться сила. Их существует три: из стороны в сторону — X, вперед и назад — Y и вверх и вниз — Z.
Зажимы прессов. От штампов, используемых в прессах, обычно не требуется выдерживать сильные нагрузки вперед и назад (Y) и из стороны в сторону (X): они просто должны удерживаться от перемещения. Однако вертикально нижний штамп поддерживается станиной пресса, а верхний должен быть подвешен, чтобы он не падал под собственным весом. Поэтому максимальная нагрузка — сила сжатия верхнего и нижнего штампов.
Решение относительно зажима — стандартизировать обе стороны верхнего и нижнего штампов и составить их вместе с допуском ±0,15 мм с направляющим L-образным стержнем. Кроме того, движения вперед и назад исключаются при помощи клиньев. При таком методе штампы для прессов менее 50 тонн можно просто вставлять или вытаскивать, что делает возможным производить замену приблизительно за 15 секунд. При этом, конечно, необходимо стан-
дартизировать высоту штампов.
Стопоры расточных станков. На 8-шпиндельном расточном станке стопоры каждого шпинделя закреплялись винтами, расположенными в труднодоступном для регулировки и затяжки месте. Для нормального функционирования стопоры, безусловно, должны иметь контакт со шпинделем. Главное усовершенствование состояло в следующем (рис. 29, е):
•резьба на концах болтов была сточена, в результате чего получились цилиндрические фиксаторы;