
Литература / 106265
.pdf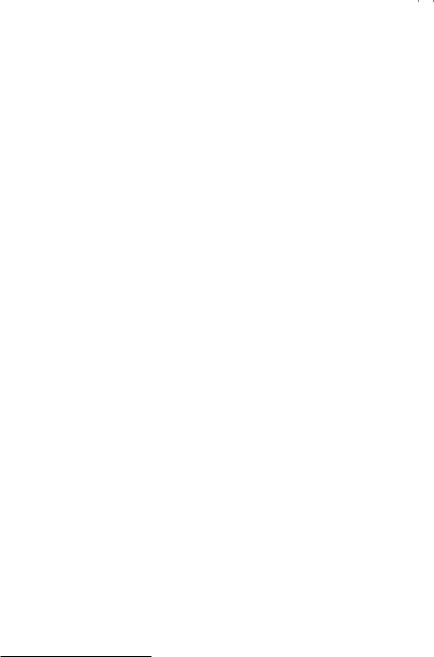
Глава 4. ПРИНЦИПЫ ПРОИЗВОДСТВЕННОЙ СИСТЕМЫ ТОЙОТЫ |
147 |
Сравнение производственных систем Форда и Тойоты
Когда г-на Оно попросили сравнить производственные системы Тойоты и Форда и сказать, какая компания имеет, по его мнению, доминирующее положение, он ответил:
«В обеих системах ежедневно возникают новые разработки и улучшения, поэтому трудно провести сравнение, но мне кажется, что система компании Toyota особенно подходит для производства в период слабого роста».
Как мы увидим, для такого заключения есть достаточно причин. Многие компании подобно компании Ford осуществляют массо-
вый выпуск деталей большими партиями, чтобы избежать эффекта возрастания затрат из-за частых замен инструментов и настройки оборудования. Производственная система Тойоты основывается на противоположной точке зрения. На стр. 147 в книге «Производственная система Тойоты» г-н Оно отмечает: «Наш производственный девиз — небольшие поставки и быстрая наладка». Он также говорит, что беззапасный подход — другая важная особенность системы компании Toyota:
«Даже если сегодня некоторые производители — к примеру, компания Volvo — практикуют сборку всего двигателя одним человеком, — это скорее исключение, а наиболее распространенной тенденцией является использование системы производственных потоков Форда или автоматизации. Хотя события, описанные Сорэнсеном, происходили еще в 1910 г., с тех пор суть процесса изменилась незначительно.
Производственная система Тойоты, так же, как и фордовская, основана на системе производственных потоков. Основное различие состоит в том, что если Сорэнсен думал над решением проблемы складирования запчастей, Toyota просто ликвидировала склады»*.
Три основных различия
Укомпании Toyota есть три основные особенности, отличающие
ееот компании Ford: небольшие размеры партий, производство смешанных моделей и постоянное выполнение операций по одному изделию, начиная от обработки и заканчивая окончательной сборкой.
Производство крупными или мелкими партиями. Можно утвер-
ждать, что различие между компаниями Ford и Toyota состоит в том, что компания Ford производит немногие модели автомобилей в
Оно, Т. Производственная система Тойоты: Уходя от массового производства, 2-е изд., с. 146-147.

148 |
Часть II |
|
|
|
|
большом объеме, а компания Toyota производит много моделей в небольших объемах. Это абсолютно верно, хотя и не дает полной картины. Как указывалось выше, выбор между этими возможностями делается не случайным образом, а является ответом на условия рынка и спрос потребителей.
Аналогично периоды быстрого или медленного роста происходят из-за изменения социальных обстоятельств практически без контроля компании. В период быстрого роста легко создать рынок продавца, но при медленном росте рынок определяют покупатели. Предприятия должны быть гибкими и готовыми удовлетворить новые запросы.
Очевидно, у массового производства есть преимущества, такие, как быстрая окупаемость специальных или уникальных станков, инструментов и штампов, но ключевой вопрос — применять мелкие или крупные партии? Традиционно американские автопроизводители считают, что большие партии и планируемое массовое производство позволяют получить существенную экономию затрат. Подобный подход приводит:
•к наличию больших запасов готовой продукции (что вызвано разрывом между прогнозируемым объемом выпуска продукции и действительным спросом);
•к накоплению объема незавершенного производства между процессами (создаваемому за счет производства крупными партиями).
Хотя эти явления часто усиливаются в периоды медленного роста, их терпят по ряду причин. Во-первых, крупные партии снижают задержки из-за замены инструментов и штампов; во-вторых, они облегчают разделение труда и снижают трудовые и другие затраты; в-третьих, разделение труда дает возможности найма низкоквалифицированных рабочих, что при условии снижения себестоимости продукции способствует увеличению потребления продукции.
Все эти доводы, однако, терпят крах, когда время замены инструментов и наладки снижается благодаря системе SMED. Добавим, что даже при производстве мелкими партиями многие функции становятся общими для нескольких продуктов или процессов. При условии, что небольшие партии в совокупности составляют большие объемы производства, разделение труда продолжает поддерживаться, что дает возможность привлекать неопытных рабочих.
Небольшие партии также способствуют сокращению цикла производства и снижению необходимости упреждающего производ-

Глава 4. ПРИНЦИПЫ ПРОИЗВОДСТВЕННОЙ СИСТЕМЫ ТОЙОТЫ |
149 |
ства. При этих условиях становится возможным производить продукцию на основе действительного спроса.
Использование производства смешанных моделей в сборочном процессе. Самые первые автомобили были произведены, вероятно, штучно небольшой группой рабочих. Конвейерное выполнение операций сборки в компании Ford по одному изделию сделало возможным разделение труда, но оно основывалось на производстве крупными партиями. Например, 200 тыс. автомобилей модели X изготовляются в начале месяца, затем 300 тыс. автомобилей модели Y — в середине месяца и 400 тыс. автомобилей модели Z — в конце. В компании Toyota, однако, выровненное производство смешанных моделей приводит к последовательности окончательной сборки в 2Х 3Y 4Z, которая повторяется в течение дня.
Смешанное производство устраняет накопление незавершенного производства за счет использования небольших партий. Оно быстро реагирует на изменение спроса и облегчает планирование, предоставляя информацию в начале процесса, какова будет средняя загрузка.
Устойчивая последовательность операций от обработки деталей до сборки. Сборка в компании Ford выстроена в поток единичных изделий, но детали и узлы, подаваемые на сборку, производятся исключительно крупными партиями. В компании Toyota и сборка, и обработка деталей осуществляются в потоке единичных изделий. Например, сварка рамы или механическая обработка деталей. Более того, компания Toyota применяет комплексную систему, в которой различные детали поступают прямо на окончательную сборку. Все детали, изготовляемые на заводе или поставляемые извне, производятся мелкими партиями и создают единый поток единичных изделий. Это — фундаментальный принцип системы Тойоты и ее существенное отличие от системы Форда.
В табл. 4.4 обобщаются различия в системах Тойоты и Форда.
•Компании Ford и Toyota используют поток единичных изделий на сборке.
•Однако компания Ford выпускает немного моделей автомобилей крупными партиями с простой последовательностью моделей на сборке. Компания Toyota производит много моделей малыми партиями, на сборке используется принцип смешанного производства.
•Сборка и производство деталей в компании Ford разделены, а в компании Toyota связаны.
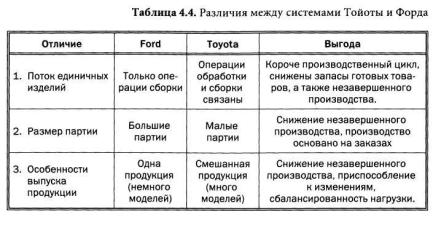
150 |
ЧАСТЬ II |
|
|
|
|
• В компании Ford поток единичных изделий используется только на сборке, а детали обрабатываются крупными партиями. В компании Toyota и сборка, и обработка производятся мелкими партиями.
Система компании Toyota не противопоставляется системе компании Ford. Скорее это постепенное улучшение — система приспособлена к японскому рынку за счет массового производства небольшими партиями с минимальными запасами.
Это принципиальные особенности производственной системы компании Toyota. Основа их достижения — внедрение системы SMED, позволяющей снизить время переналадки и обеспечить производство небольшими партиями.
Выводы
Главная цель производственной системы Тойоты — выявлять и устранять потери и снижать затраты. Запасы ликвидируются обнаружением и исправлением скрытых причин, которые их порождают. Производство на основе заказов, или ориентация на спрос, а не прогнозное или упреждающее производство, помогает управлять этими условиями. Другая важная с точки зрения операций стратегия — отделение рабочего от станка, предавтоматизация для обеспечения многостаночной работы.
Глава 5
МЕХАНИЗМ ПРОИЗВОДСТВЕННОЙ СИСТЕМЫ ТОЙОТЫ
УЛУЧШЕНИЕ ПРОЦЕССА: УПРАВЛЕНИЕ ПРОИЗВОДСТВЕННЫМ ГРАФИКОМ И ПРИНЦИП «ТОЧНО ВОВРЕМЯ»
Производственный процесс состоит из операций обработки, контроля, транспортировки и хранения, но только обработка добавляет ценность. Это очень хорошо усвоено в компании Toyota, где снижение затрат за счет устранения потерь, особенно потерь от перепроизводства, является главной целью. Контроль, транспортировка и особенно хранение, или практика накопления запасов, считаются потерями и устраняются где только возможно.
Многие считают самой важной особенностью производственной системы Тойоты принцип «точно вовремя» (just-in-time), но в действительности это не более чем стратегия достижения беззапасного производства.
Важными концепциями в производственной системе Тойоты являются управление графиком работ и управление нагрузкой. Управление графиком обеспечивает своевременность изготовления продукции. Управление нагрузкой обеспечивает саму возможность выпуска продукции за счет поддержания баланса между производственными возможностями и нагрузкой. Вот иллюстрация этому: если вы не явитесь на вокзал вовремя, то опоздаете на поезд (управление графиком), но даже если вы придете вовремя, все равно не сможете сесть на поезд, если он уже полон (управление нагрузкой).

152 |
Часть II |
|
|
Управление производственным графиком и принцип |
|
«точно вовремя» |
|
Планирование производства
Обычно планирование производства проходит три стадии:
•основной график — долгосрочный (двухлетний, ежегодный или квартальный); •промежуточный график — ежемесячный;
•детализированный график — реальная последовательность производства на неделю, три дня или один день.
Основной график компании Toyota базируется на глубоком исследовании рынка (см. главу 4, с. 142) и устанавливает примерные объемы производства. Общие ежемесячные объемы производства предоставляются заводам и поставщикам комплектующих за два месяца до начала производства и затем подтверждаются через месяц. Эти окончательные объемы используют для составления детальных недельных и ежедневных производственных графиков и выравнивания производства. Примерно за две недели до начала производства каждой линии предоставляются проектные дневные объемы производства по каждой модели автомобиля. Детальный производственный график с имеющимися дневными изменениями направляется на выход линии окончательной сборки для согласования графика с действительными заказами. Изменения сообщаются по линии через систему канбан. Гибкость детального графика — это особенность, отличающая систему производственных графиков компании Toyota от других. Изо дня в день в график могут быстро и легко вноситься точные изменения.
Управление производственным графиком и беззапасное производство
В главе 4 описаны две отличительные особенности производственной системы Тойоты: производство, основанное на заказах, и беззапасное производство.
Отсутствие запасов и «точно вовремя»
Как мы видели в предыдущей главе, использование принципа «точно вовремя» только для обеспечения поставки готовой продук-

Глава 5. МЕХАНИЗМ ПРОИЗВОДСТВЕННОЙ СИСТЕМЫ ТОЙОТЫ |
153 |
ции в предписанный период часто приводит к перепроизводству и преждевременному производству. Однако в компании Toyota принцип «точно вовремя» применяется также к производству деталей и узлов в точно требуемом количестве, точно ко времени, когда они нужны, и не раньше.
В компании Toyota беззапасное производство означает, что запасы готовых автомобилей должны быть нулевыми, т.е. объем производства не должен превышать объем заказов. Для достижения такого баланса компания Toyota ввела производство, основанное на заказах. Поскольку не всегда удается добиться, чтобы цикл производства Рбыл меньше периода между заказом и поставкой Д т.е. P<D, в планировании и производстве был использован принцип «супермаркета» (супермаркет работает на предположении, что купленное сегодня будет, вероятно, требоваться и завтра). Итак, планирование предварительных процессов основано на ожидаемых заказах, однако создание излишних запасов предупреждается привязкой последующих процессов и окончательной сборки к действительным заказам потребителей. Поэтому гибкость и управление достигаются системой канбан. Наконец, поскольку главное абсолютное правило — производить не больше, чем требуется, возможности оборудования и степень его загрузки не считаются факторами управления производством.
Семь принципов сокращения цикла производства
В компании Toyota говорят: «Блок цилиндров, отлитый на заводе Kamigo утром, работает в готовом автомобиле вечером». Каким же образом это достигается?
Снижение задержек процесса. Задержки процесса возникают, когда вся партия ожидает обработки. Для сокращения цикла производства намного эффективнее ликвидировать задержки процесса, чем стремиться к уменьшению времени обработки. Как правило, соотношение времени обработки и времени хранения находится в пределах от 2:3 до 1:4. Во многих случаях сокращение задержек процесса наполовину приведет к сокращению времени производства на 60 %, а полное устранение задержек может сократить производственный цикл на 80 %.
Для достижения таких результатов нужно выровнять объемы производства и возможности обработки на всех процессах и синхронизовать поток работы по всему предприятию. При любом раз-

154 |
Часть II |
мере партии — будь то 3000, 300, 3 изделия или только одно — если время обработки на каждом процессе одинаково, процессы можно синхронизовать для устранения задержек. Когда последовательно расположены станки с разной производительностью, время обработки на каждом из них будет отличаться. В этом случае нужно намеренно замедлять работу более быстрых станков, чтобы выровнять номинальное время обработки. Однако при больших размерах партий производственный цикл будет увеличиваться за счет задержек партий.
Снижение задержек партий. Устранение задержек процесса выравниванием объема производства и синхронизацией может сократить цикл производства максимум на 80 %. Для дальнейшего его сокращения требуется снижение или устранение задержек партий.
В целом эти задержки являются частью времени обработки, и их нелегко обнаружить.
На рис. 28 показано различие во времени обработки при производстве партиями и при потоке единичных изделий. Для того чтобы вся партия из 3000 изделий прошла три этапа обработки, необходимо 15 часов (три 5-часовых процесса). Однако если 3 процесса соединены так, что каждое изделие, обработанное на одном процессе, тут же передается на следующий, производственный цикл существенно сокращается. Так, в приведенном примере, если время обработки одного изделия на каждом процессе равно 6 секунд, цикл производства можно снизить до 5 часов 12 секунд. Это сокращение производственного цикла на2/3. Если в производственный поток по одному изделию включить 5 процессов, цикл производства будет сокращен до X; если 10 — до Хо и т.д.
Разбивка производства на небольшие партии может резко сократить циклы производства. Однако многие автопроизводители сопротивляются этой идее, так как производство большими партиями снижает время, затрачиваемое на замену инструментов и штампов, тем самым уменьшая общие затраты (в человеко-часах) на обработку. Производство мелкими партиями, однако, компенсирует это преимущество сокращением производственного цикла за счет увеличения количества транспортируемых партий.
В потоке единичных изделий каждая транспортируемая партия эквивалентна одному изделию. Это значительно сокращает производственный цикл. Например, партию в 3000 изделий можно обработать за очень короткое время, если каждое изделие передается на следующий процесс по мере его обработки. Но чтобы добиться такого снижения, размещение оборудования должно способствовать
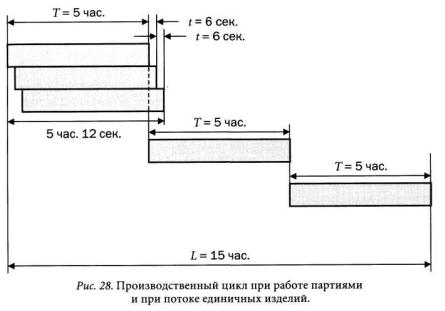
Глава 5. МЕХАНИЗМ ПРОИЗВОДСТВЕННОЙ СИСТЕМЫ ТОЙОТЫ |
155 |
удобной и быстрой транспортировке продукции от одного процесса к другому.
Снижение времени производства. С помощью выравнивания объема производства и синхронизации можно устранить задержки процесса, снизив цикл производства до X от первоначального. А, используя, например, поток единичных изделий для 10 последовательных процессов, можно снизить цикл производства до ХоПе- ремножением эффекта от устранения задержек процесса и партии можно снизить цикл производства для десяти процессов до Хо от первоначального (ХхХо)-
Этот эффект перемножения еще более возрастает, когда определяют оптимальный размер партии. Предельное ограничение на цикл производства — время обработки одной партии. Размер обрабатываемой партии, в свою очередь, принципиально определяется временем, необходимым для переналадки и установки инструментов. Это время можно сократить на 90 %, если часовая замена может быть сокращена до 6 минут. В этом случае производственный цикл не увеличится, даже если обрабатываемая партия уменьшится с 3000 до 300 изделий.
Если время обработки теперь равно 0,5 часа и размер партии сокращен до 0,1 от имевшегося, эти улучшения, объединяясь с устра-

156 |
Часть II |
нением задержек процесса и партии, делают возможным поразительное снижение цикла производства:
Производство партиями по 3000 изделий включает не только задержки процесса, но и задержки партии, и потребует для выполнения 10 дней. Переходя к партиям по 300 изделий, выравнивая и синхронизируя 10 процессов и выстраивая поток единичных изделий, получим время обработки всего 0,5 часа (Хоо от 240 часов).
Существует четыре основных принципа, которых нужно придерживаться при создании потока единичных изделий, который, в свою очередь, позволит существенно сократить производственный цикл (см. пример выше):
•выравнивание объемов производства между процессами и синхронизация всех процессов (для устранения задержек процессов); •уменьшение размера транспортируемой партии до одного из-
делия (для устранения задержек партий); •улучшение расположения рабочих участков, чтобы компенси-
ровать необходимость гораздо более частой транспортировки; •уменьшение размера партии.
Вот так, следуя этим принципам, компания Toyota добивается, чтобы блок цилиндров двигателя, отлитый утром, работал в готовом автомобиле вечером.
Используйте размещение, формирование линий и систему полного управления работой. Как отмечалось выше, создание потока единичных изделий требует выравнивания объема производства, использования мелких партий и синхронизации процессов. Поскольку это сильно увеличивает число операций транспортировки, были разработаны 2 стратегии для снижения общего времени транспортировки:
•изменение размещения производственных мощностей таким образом, чтобы требовалось немного или вообще не требовалось транспортных средств;
•применение более удобного метода соединения процессов, та кого, например, как конвейер.
Поскольку второй метод может оказаться дорогим и сложным, в общем случае предпочтительно совершенствование размещения.