
УТП / 53 234-241
.PDF234 |
Евдокимов В.Д., Клименко Л.П., Евдокимова А.Н. |
Метод термонапыления заключается в бомбардировании обрабатываемой поверхности (например, упорных центров, оправок к гидрокопировальным станкам, гибочных и раскатных роликов, направляющих оправок к насадному инструменту, борштанг, прессовых оправок и др.) частицами порошка, разогретыми до пластического состояния. Передача тепловой и кинетической энергий частицам порошка осуществляется плазменным (введением порошковых материалов в плазменную струю) игазопламенным (с введением порошков в газовую смесь) способами.
Для устойчивой работы плазмотрона электрическая дуга должна быть сформирована и стабилизирована вдоль продольной оси плазмотрона.
Используются порошки самофлюсующихся сплавов системы Ni-Сr-В-Si-С марок СНГН, ПГХН80СР и ВСНГН с температурой плавления 1050 °С, зернистостью 20-150 мкм, обеспечивающие твердость 35-62 HRCэ.
Недостатками плазменно-напыленных покрытий являются низкие прочность сцепления с основой, адгезионная прочность и термостойкость покрытия, что связано с различными коэффициентами температурного расширения покрытия и основы. Обладая значительной пористостью, плазменно-напыленные покрытия не защищают поверхность от окисления, что приводит к ускоренному разрушению (отслаиванию) покрытия.
Увеличить адгезионную прочность, термостойкость и стойкость покрытия в окислительных средах можно следующим способом [а. с. 676641 (СССР)]. На металлическую поверхность изделия наносят газотермическим напылением порошковое покрытие. Затем подвергают ее азотированию любым из известных способов до образования нитридной прослойки.
Так как порошковое покрытие пористое, то оно не препятствует диффузии атомов азота к поверхности защищаемого металла. Наоборот, благодаря усилению адсорбционных и абсорбционных процессов .ускоряется насыщение поверхности основного металла азотом и образование в поверхностном слое нитридов тех элементов, которые входят в состав защищаемого металла (железа, хрома, вольфрама, титана, алюминия и др.). Поскольку нитриды имеют плотность меньшую, чем металлы (плотность оксидов 3-5 г/см3, а плотность стали 7,8 г/см3), то при своем образовании они заполняют микропоры порошкового покрытия, увеличивая тем самым сцепляемость по типу механического зацепления. Одновременно повышается термостойкость покрытия, так как образовавшиеся нитриды играют роль прослойки, коэффициент термического расширения которой близок к значению порошковых материалов, созданных на основе оксидов. Нитридная прослойка обеспечивает также коррозионную стойкость защищаемого металла.
Повышение рабочих характеристик поверхностных слоев дейдвудных валов при их восстановлении
Дейдвудные валы являются важным конструктивным элементом силовой судовой установки. Они передают крутящий момент от главного дизеля к винту судна и имеют размеры до 900 мм диаметром и 10 м длиной. В процессе эксплуатации поверхности дейдвудных валов постепенно выходят из строя, приобретая ряд дефектов и разрушений.
При восстановлении дейдвудных валов в основном применяют следующую технологию восстановления. Сначала на прогретый до 350 °С вал наплавляют проволоку типа Св08А, Св08ГС или ленту 08кп, 10сп, после чего наплавляют
ТЕХНОЛОГИЯ УПРОЧНЕНИЯ МАШИНОСТРОИТЕЛЬНЫХ МАТЕРИАЛОВ |
235 |
слой, обладающий высокими коррозионными и износостойкими свойствами, используя проволоку Св04Х19НПМЗ, Св08Х20Н9Г7Т или ленту 08Х18Н10Т. Наплавленный вал обворачивают асбестовым полотном и при медленном вращении на токарном станке охлаждают до 50 °С. Затем осуществляют ряд операций механической обработки.
Проф. А.Н. Евдокимовой и проф. В.П. Сторожевым предлагается опреде-
ленное совершенствование технологии. Сначала поверхностную корку наплавленного слоя протачивают резцом, затем осуществляют операцию упрочнения поверхности деформирующими роликами или другими методами. Конечной операцией является шлифование на чистовых режимах. В этой принятой заводами технологии имеется определенный резерв, использование которого должно привести не только к упрощению процедуры обработки дейдвудного вала, но и к увеличению его коррозионной стойкости и износостойкости. Как известно, наплавочные и сварочные операции приводят к образованию значительных по величине растягивающих напряжений в поверхностных и подповерхностных слоях. Эти напряжения способствуют развитию усталостных процессов, повышают коррозионную способность рабочих поверхностей и снижают их износостойкость. Применение операции медленного охлаждения дейдвудного вала с наплавленной поверхностью в большинстве случаев уменьшают, но не снимают полностью растягивающие напряжения. Снятие же резцом после этого части наплавленного поверхностного слоя в виде корки снова образует растягивающие напряжения первого рода с текстурой, вытянутой в направлении выхода обработанной поверхности из-под резца. Последующая обработка роликами приводит к пластическому деформированию слоев и возникновению напряжений сжатия с движением металла по обе стороны от оси ролика и в значительно меньшей степени – в плоскости его вращения. В результате в материале сохраняется предыстория предшествующих видов механической обработки, в изменение которой вносит определенный вклад последующее чистовое шлифование вала, применяемое для получения требуемых размеров и шероховатости поверхности.
Установлено, что после наплавки с естественным охлаждением в поверхностных слоях возникают напряжения растяжения порядка 400 МПа. Если охлаждение после наплавки электродной проволоки осуществлять с использованием термоизолированной асбестовой шубы, замедляя тем самым процесс охлаждения, то внутренние напряжения растяжения в поверхностных слоях значительно уменьшаются. Обработка проходным резцом на токарном станке снимает корку и часть наплавленного поверхностного слоя, но вносит свои растягивающие напряжения. Получается, что уменьшенные или даже сведенные практически к нулю растягивающие напряжения после медленного охлаждения образцов в термоизоляции снова возникают, но уже за счет механической обработки. Так как по принятой на судоремонтных заводах технологии после обработки резцом проводят выглаживание цилиндрической поверхности дейдвудного вала упрочняющими роликами, то это формирует напряжения сжатия порядка 200-250 МПа.
Однако практика применения упрочняющих роликов показала, что эта технологическая операция образует волнистую поверхность по длине образующей дейдвудного вала. Для снятия этой волнистости применяют последующее шлифование, что снимает часть упрочненного слоя с высокими напряжениями сжатия и вносит свои напряжения растяжения, хотя и незначительные. Таким образом, получается вновь сформированная поверхность с ухудшенными свойствами.
236 |
Евдокимов В.Д., Клименко Л.П., Евдокимова А.Н. |
Повышение качества наплавленных поверхностных слоев проводили в два этапа. На первом этапе было осуществлено шлифование абразивным кругом по наплавленной поверхности с одновременным снятием припуска и упрочнением поверхностных слоев, образовавшихся после снятия этого припуска. Были использованы обычные абразивные круги типа ЗЗА16НСТ2К6 при скорости круга 30 м/с, глубиной резания 0,15-0,20 мм при скорости вращения детали 0,01 м/с. Смазка осуществлялась не сульфофрезолом, а с использованием индустриального масла.
При шлифовании учитывалось, что упрочняющий эффект зависит от величины удельной поверхностной энергии Е (Дж/мм2). Так, по нашим расчетам для получения максимальной твердости упрочненного слоя порядка 10·103 МПа следует ввести в обрабатываемый шлифованием наплавленный слой удельную энергию порядка 60 Дж/мм2. Этой энергии, по данным работы, вполне достаточно для создания белого слоя толщиной 0,5 мм и даже более, в зависимости от условий охлаждения. Однако в действительности получается меньшая толщина белого слоя.
После упрочняющего шлифования с одновременным снятием части наплавленного слоя вместе с поверхностной коркой на втором этапе проводилось чистовое шлифование на тонком режиме для получения требуемой геометрии и шероховатости поверхности вала, а затем определение ряда показателей, характеризующих свойства упрочненного слоя. Так, упрочняющее шлифование с образованием сплошного белого слоя вызывает в поверхностных слоях в два раза большие напряжения сжатия, чем обработка поверхности роликами. Снятие тонкого поверхностного слоя последующим финишным шлифованием несколько уменьшает сжимающие напряжения в поверхностных слоях, однако оставляет их достаточно высокими – до 450...500 МПа на глубине порядка 20-40 мкм.
Измерение микротвердости наплавленной поверхности после упрочняющей обработки абразивным кругом и последующего тонкого шлифования показывает ее увеличение до 9,5·103 МПа, что более чем в два раза выше, чем достигаемое упрочнение с применением холодного пластического деформирования роликами (4,2·103 МПа). Полученные белые слои обеспечили повышение коррозионной стойкости упрочненных шлифованием поверхностных слоев.
Упрочненные шлифованием образцы, а также образцы, обработанные по заводской технологии, подвергались испытаниям на износ, которые проводились в морской воде с добавлением пяти процентов корундового порошка с фракцией 5-8 мкм. Оказалось, что применение упрочнения абразивным шлифованием на 40% повышает износостойкость наплавленных поверхностных слоев по сравнению с принятой заводской технологией, включающей после наплавки проволоки обработку резцом, роликами и тонким шлифованием.
Таким образом, применение технологии упрочнения рабочих поверхностей с помощью шлифовального абразивного круга может представлять практический интерес при восстановлении наплавкой дейдвудных валов с одновременным улучшением рабочих характеристик и поверхностных слоев.
Применение методов наплавки и напыления износостойких и прочных слоев металла на рабочие поверхности деталей машин и технологической оснастки позволяют не только обеспечить их упрочнение, но и решить комплекс взаимосвязанных технических и экономических задач, направленных на сбережение ресурсов. К таким задачам относятся: снижение удельной металлоемкости изделия и его элементов на единицу основной характеристики повыше-
ТЕХНОЛОГИЯ УПРОЧНЕНИЯ МАШИНОСТРОИТЕЛЬНЫХ МАТЕРИАЛОВ |
237 |
нием их прочности и уменьшением массы благодаря применению объемно- и поверхностно-упрочненных материалов. Восстановление изношенных поверхностей (например, шеек коленчатых валов, элементов гравюр штампов для горячей штамповки и др.) методами наплавки и напыления позволяет совместить процессы создания новых слоев металла взамен изношенных с процессами их упрочняющей обработки.
Методы напыления широко используют для восстановления и упрочнения деталей автомобилей, тракторов, сельскохозяйственной техники, подвижного железнодорожного состава, инструментов и др.
Отличительной особенностью покрытий, нанесенных способами газотермического напыления, является их пористость. Она зависит от способа напыления, типа и марки напыляемого материала, режима его нанесения и др. При прочих равных условиях пористость покрытий, нанесенных электродуговой металлизацией, составляет 15-20%; плазменным напылением – 2-20%; детонационным напылением – 0,2-1,5%. Пористость покрытий может оказывать положительное влияние на их износостойкость и ресурс, так как поры хорошо удерживают смазку. Пористое покрытие имеет пониженную механическую твердость. При нарушении работы фильтров системы смазки поры могут накапливать продукты износа, что приводит к выходу из строя сопряженной детали.
Упрочнение и восстановление деталей, работающих в условиях абразивного изнашивания при нормальных и повышенных температурах (до 500 °С), проводят газотермическим (плазменным) напылением порошков из высоколегированных чугунов марок ПГ-С27, ПР-С1, ПГ-ФБХ6, ПГ-УС25. Для восстановления и упрочнения деталей, работающих в условиях газовой коррозии и абразивного изнашивания при высоких температурах, выполняют газотермическое напыление порошком из высоколегированного чугуна марки ПР-ЧЮ22СГ.
При плазменном напылении деталей из алюминиевых сплавов используют смесь из порошков АКЛ (95%) и ПМС-2 (5%).
Для газопорошковой наплавки чаще всего применяются металлопорошковые самофлюсующиеся материалы. Детали из чугуна упрочняют и восстанавливают, применяя порошковые сплавы (табл. 36). Стальные детали наращиваются сплавами типа ПГ-ХН80СР на никель-хромистой основе. Химический состав и твердость наплавленного слоя приведены в табл. 37.
Характеристики порошковых материалов для детонационного напыления покрытий приведены в табл. 38; физико-механические характеристики некоторых детонационных покрытий – в табл. 39.
36. Порошки для нанесения покрытий из сплавов на основе железа
Марка |
|
|
Содержание компонентов, % (мас. доля) |
|
|
||||
|
|
|
|
|
|
|
|
|
|
порошка |
C |
Mn |
Cr |
Ni |
V |
Ti |
Al |
B |
Cu |
|
|||||||||
|
|
|
|
|
|
|
|
|
|
ПР-180Х16Н8ФТ3Р |
1,8 |
- |
16 |
8 |
8 |
3 |
- |
1,5 |
- |
ПР-СХ20Н8106Т2Р2 |
- |
- |
20 |
8 |
- |
2 |
5,5 |
2,5 |
- |
ПР-150Г10Т11Р5 |
1,0 |
10 |
- |
- |
- |
11 |
- |
5 |
- |
ПР-150Х12Ф6Д |
1,5 |
- |
12 |
- |
6,5 |
- |
- |
- |
0,4 |
ПР-290Х14Ф12Д |
2,9 |
- |
14,5 |
- |
12 |
- |
1,0 |
- |
- |
ПР-0Х18Н9Т |
- |
- |
18 |
9 |
- |
0,7 |
- |
- |
- |
ПР-Х23Н28М3Д3Т |
- |
- |
23 |
28 |
- |
1,0 |
- |
- |
3,0 |

238 Евдокимов В.Д., Клименко Л.П., Евдокимова А.Н.
37. Химический состав порошковых сплавов и характеристики твердости слоя, наплавленного газопорошковой наплавкой
Марка |
|
Содержание компонентов, % (мас. доля) |
|
||
порошкового |
|
|
|
|
|
Si |
B |
Fe |
Cu |
||
сплава |
|||||
|
|
|
|
|
|
НПЧ-1 |
1,3-1,5 |
1,2-1,5 |
0,1-0,7 |
4-5 |
|
НПЧ-2 |
2,4-2,7 |
2,2-2,7 |
0,3-1,0 |
||
|
|||||
НПЧ-3 |
0,2-0,95 |
0,7-1,1 |
0,1-0,7 |
Остальное |
|
|
|
|
|
|
|
ПГ-ХН80СР2 |
1,5-3,0 |
1,5-2,5 |
5,0 |
- |
|
ПГ-ХН80СР3 |
2,5-4,5 |
2,0-3,0 |
|||
|
|
||||
ПГ-ХН80СР4 |
3,0-5,0 |
2,5-4,0 |
|
|
|
|
|
|
|
|
|
Марка |
Содержание компонентов, % (мас. доля) |
Твердость |
|||
порошкового |
|
|
|
напыленного |
|
C |
Ni |
Cr |
|||
сплава |
слоя |
||||
|
|
|
|
|
|
НПЧ-1 |
0,1-0,3 |
Остальное |
|
НВ: |
|
|
190-235 |
||||
НПЧ-2 |
- |
||||
|
|
300-400 |
|||
|
|
|
|
|
|
НПЧ-3 |
0,2 |
41-60 |
|
180-200 |
|
|
|
|
|
|
|
ПГ-ХН80СР2 |
0,3-0,6 |
Остальное |
12,0-15,0 |
NRC: |
|
35 |
|||||
ПГ-ХН80СР3 |
0,4-0,8 |
13,5-16,5 |
|||
|
45 |
||||
|
|
|
|
||
|
|
|
|
|
|
ПГ-ХН80СР4 |
0,6-1,0 |
|
15,0-18,0 |
55 |
|
|
|
|
|
|
38. Порошковые материалы для детонационного напыления
Материал |
Марка |
Содержание компонентов, |
|
материала |
% (мас. доля) |
||
|
|||
|
|
|
|
Глинозем (оксид алюминия) |
Г-00, ГО |
Al2O3 ≥ 99,5% |
|
Алюмомагнезиальная шпинель |
ГШП |
Cr2O3 ≥ 99% |
|
Карбид: |
- |
MgO, Al2O3 ≥ 95% |
|
хрома |
- |
||
вольфрама |
- |
- |
|
титана |
- |
- |
|
Для детонационного напыления |
ВК-6 |
WC 94; Co 6 |
|
износостойких покрытий |
ВК-10 |
WC 90; Co 10 |
|
|
ВК-15 |
WC 85; Co 15 |
|
|
ВК-20 |
WC 80; Co 20 |
|
|
ВК-30 |
WC 70; Co 30 |
|
|
ВН-6 |
WC 94; Ni 6 |
|
|
ВН-10 |
WC 90; Ni 10 |
|
|
ВН-15 |
WC 85; Ni 15 |
|
|
ВН-20 |
WC 80; Ni 20 |
|
|
ВН-30 |
WC 70; Ni 30 |
|
Порошок: |
ЖЛ-1 |
Fe – основа, легирующие добавки Al и B |
|
ЖЛ |
|||
НХЛ |
НХЛ-1 |
Ni – Cr – основа, легирующие добавки Al и B |
|
НЛ |
НЛ-1 |
Ni – основа, легирующие добавки Al и B |
|
НЖЛ |
НЖЛ-1 |
Коррозионно-стойкая сталь – основа, легирующие |
|
|
|
добавки Al и B |
|
НХ16С3Р4 |
ПГАН60 |
Ni 70-77; Cr 14-18; B 2,8- 3,8; Fe 3; Si 2,5-3,5; C 0,9-1,8 |
ТЕХНОЛОГИЯ УПРОЧНЕНИЯ МАШИНОСТРОИТЕЛЬНЫХ МАТЕРИАЛОВ |
239 |
39. Физико-механические характеристики детонационных покрытий
|
Материал |
Микротвердость, |
Пористость, |
Прочность |
Максимальная |
|
|
сцепления |
температура |
||||
|
покрытия |
МПа |
% |
|||
|
с основой, МПа |
эксплуатации, ºС |
||||
|
|
|
|
|||
|
|
|
|
|
|
|
92% |
WC + 8% Co |
12 000-15 000 |
0,4-0,5 |
180-210 |
560 |
|
|
|
|
|
|
|
|
85% |
WC + 15% Co |
12 500-14 500 |
0,2-0,5 |
220-250 |
560 |
|
|
|
|
|
|
||
25% WC + 7% Co Ni |
10 000-12 000 |
0,5 |
180 |
780 |
||
+ карбиды Ti и Сr |
||||||
|
|
|
|
|||
85% |
Cr3C2 |
10 000-12 000 |
0,5 |
180-210 |
1000 |
|
+ 15% нихрома Ni |
3 500-3 800 |
0,1-0,15 |
250-300 |
1000 |
||
80% |
Al2O3 + 20% Ni |
6 000-10 000 |
0,5-1,0 |
70-100 |
1000 |
|
|
|
|
|
|
|
|
60% |
Al2O3 + 40% Ni |
5 000-6 000 |
0,5-1,0 |
80-130 |
1000 |
|
|
|
|
|
|
||
Порошок НЖЛ-1, |
10 800-11 000 |
До 1,0 |
80-90 |
– |
||
легированный Al и B |
||||||
|
|
|
|
|||
Порошок НХ16С3Р4 |
5 500 |
0,3 |
80-50 |
– |
||
|
|
|
|
|
||
Порошок ПН70Ю30 |
5 000-6 000 |
1,0 |
Не менее 60 |
– |
||
|
|
|
|
|
||
Порошковая смесь Ti; Cr; B |
10 000-12 000 |
1,0-1,5 |
50-60 |
– |
||
|
|
|
|
|
|
Используют порошки с размером частиц, мкм: 40-100 для газопламенного и плазменного напыления; до 200 для газопорошковой наплавки; 20-60 для детонационного напыления. Гранулированные порошки марок ПГ-10Н-01, ПГ-10Н- 04 и ПГ-10К-01 применяют для порошковой наплавки; высоколегированную порошковую смесь ПС-12НВК-01, гранулированные порошки ПГ-12Н-01 и ПН- 12Н-02 – для газотермического напыления с последующим оплавлением; ПГ- 19М-01 и термореагирующие композиционные порошки ПТ-НА-01 и ПТ-19Н-01
– для газотермического напыления без последующего оплавления, изготовляют методом конгломерирования. Характеристики порошков приведены в табл. 40.
40. Химический состав напыляемых детонационным способом порошков и твердость покрытий
Марка |
|
Содержание компонентов, % (мас. доля) |
|
Твердость |
||||
|
|
|
|
|
|
покрытий |
||
порошка |
Cr |
B |
Si |
Fe |
C |
Ni |
||
HRC |
||||||||
|
||||||||
|
|
|
|
|
|
|
|
|
ПГ-10Н-01 |
14-20 |
2,8-4,2 |
4,0-4,5 |
3-7 |
0,6-1,0 |
Остальное |
55-62 |
|
ПГ-10Н-04 |
- |
1,2-1,8 |
2,3-2,8 |
До 2 |
До 0,2 |
То же |
230 НВ |
|
ПГ-10К-01 |
21-25 |
1,2-1,8 |
0,8-1,3 |
До 2 |
1,3-1,7 |
28-32 |
45-50 |
|
ПН-12Н-01 |
8-14 |
1,7-2,8 |
1,2-3,2 |
2-5 |
0,3-0,6 |
Остальное |
35-44 |
|
ПГ-12Н-02 |
10-16 |
2-4 |
3-5 |
3-6 |
0,4-0,8 |
То же |
45-54 |
|
ПГ-19М-01 |
- |
- |
- |
До 4 |
- |
- |
65-72 |
|
ПТ-НА-01 |
- |
- |
- |
- |
- |
Остальное |
- |
|
ПТ-19Н-01 |
8-14 |
1,7-2,8 |
1,2-3,2 |
2-5 |
0,3-0,6 |
То же |
28-40 |
Примечания: 1. В состав порошков входят также следующие компоненты, % (мас. доля): ПГ-19М-01: вольфрам
8,5-10,5; остальное– медь; ПГ-10К-01: вольфрам3,5-4,5; ПТ-НА-01: алюминий4,5-5,5; ПТ-19Н-01: алюминий 0,8-1,3%.
2.Обозначения в марках: ПГ – порошок гранулированный, ПН – порошок напыляемый (для газотермического напыления с последующим оплавлением), ПТ – порошок терморегулирующий композиционный.
240 |
Евдокимов В.Д., Клименко Л.П., Евдокимова А.Н. |
Сплавы и порошки металлидов для нанесения покрытий газотермическим напылением изготовляют способом совместного восстановления оксидов металлов гидридом кальция или распылением расплава. Характеристики этих сплавов и порошков приведены в табл. 41 и 42.
Основу приведенных в табл. 41 порошков и самофлюсующихся сплавов составляют никель и титан. К примесям относятся сера, фосфор и кислород; их содержание должно быть соответственно не более 0,04; 0,04 и 0,05% (маc. доля). Порошки наносят на детали машин для упрочнения и восстановления поверхностей всеми способами напыления. Оплавление нанесенных покрытий, а также свободно насыпанных порошков может производиться газопламенным способом, ТВЧ, лазерным лучом и другими источниками тепла. Покрытия отличаются высокой стойкостью к износу и коррозии. Детали с покрытиями используют в условиях ударных нагрузок, в агрессивных средах, с абразивным износом при температуре до 600 °С. Целесообразно применять порошки при восстановлении и упрочнении клапанов, распределительных валов двигателей внутреннего сгорания, лопаток и роторов, вентиляторов, валов и втулок гидронасосов, деталей сельскохозяйственных и других машин.
В условиях ударно-абразивного изнашивания никелевые сплавы, нанесенные газотермическим напылением, по износостойкости не могут конкурировать со сплавами на основе железа, и поэтому в подобных условиях наносят покры-
41. Химический состав напыляемых газотермическим способом титаноникелевых сплавов
Марка |
Основные компоненты |
|
Примеси (не более) |
|
Твердость |
|||||
|
|
|
|
|
|
|
|
|
HRC |
|
Ni |
Ti |
Al |
Fe |
C |
Ca |
|
N2 |
|||
стали |
|
напыленного |
||||||||
|
|
|
|
|
|
|
|
|
||
|
|
|
% (мас. доля) |
|
|
|
слоя |
|||
|
|
|
|
|
|
|
|
|
|
|
ПН-70Ю30 |
|
- |
28-33 |
|
|
|
0,15 |
|
0,08 |
40 |
|
|
|
|
|
|
|
|
|||
ПН-85Ю15 |
Основа |
12-15 |
|
|
|
|
- |
|||
|
|
|
|
|
|
|
||||
|
|
|
|
|
|
|
|
|
|
|
ПН-55Т45 |
|
43-47 |
- |
0,2 |
|
|
0,3 |
|
0,1 |
55-60 |
|
|
|
|
|
|
|
|
|
||
ПТ-88Н12 |
10-12,5 |
Основа |
|
0,07 |
|
0,15 |
|
|
||
|
|
|
|
|
|
|||||
|
|
|
|
|
|
|
|
|
||
ПТ-65Ю35 |
- |
35,5-40 |
|
|
|
|
|
- |
||
|
|
|
|
|
|
|
||||
|
|
|
|
|
|
|
|
|
|
|
ПР-Н70Ю30 |
Основа |
- |
28-33 |
2,0 |
|
|
0,1 |
|
0,08 |
|
|
|
|
|
|||||||
|
|
|
|
|
|
|
|
|||
ПР-П85Ю15 |
12-15 |
1,0 |
|
|
|
|
|
|||
|
|
|
|
|
|
|
|
|||
|
|
|
|
|
|
|
|
|
|
|
42. Химический состав порошков для газотермического напыления
Марка |
|
Содержание основных компонентов, % (мас. доля) |
|
||||
порошка |
C |
|
Cr |
Si |
B |
Mn |
Fe |
|
|
||||||
|
|
|
|
|
|
|
|
ПР-Н80Х13С2Р |
0,2-0,4 |
|
12-14 |
2,0-2,8 |
1,2-1,8 |
- |
|
ПР-Н77Х15С3Р2 |
0,35-0,6 |
|
14-16 |
2,8-3,5 |
1,8-2,3 |
- |
До 5 |
ПР-Н73Х16С3Р3 |
0,6-0,9 |
|
15-17 |
2,7-3,7 |
2,3-3,0 |
- |
|
ПР-Н70Х17С4Р4 |
0,8-1,2 |
|
16-18 |
3,8-4,5 |
3,1-4,0 |
- |
|
ПР-Н67Х18С5Р4 |
0,9-1,5 |
|
16-19 |
4,0-5,0 |
40-4,7 |
До 1 |
|
ПР-Н65Х25С3Р3 |
0,9-1,5 |
|
23,5-26,5 |
2,1-3,3 |
2,0-3,0 |
0,05-0,35 |
4-7 |
ПР-Н68Х21С5Р |
0,35-0,5 |
|
20-22 |
4-5 |
1,0-1,3 |
- |
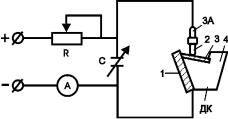
ТЕХНОЛОГИЯ УПРОЧНЕНИЯ МАШИНОСТРОИТЕЛЬНЫХ МАТЕРИАЛОВ |
241 |
тия из порошков на основе железа. Первые пять видов порошков (см. табл. 42) по свойствам соответствуют сталям типа Х18Н9, Х17, Х13. Они обеспечивают твердость покрытий до 55 HRC. Их применяют для напыления износо- и корро- зионно-стойких покрытий взамен самофлюсующихся хромоникелевых сплавов. Порошок марки ПР-0Х18Н9Т используют для нанесения коррозионно-стойких покрытий. Порошок марки ПР-Х23Н28М3Д3Т целесообразен взамен самофлюсующихся хромоникелевых сплавов для нанесения износостойких покрытий.
Упрочнение методами электроискровой обработки
Электроискровую обработку применяют для повышения износостойкости
итвердости поверхности деталей машин, работающих в условиях повышенных температур в инертных газах; жаростойкости и коррозионной стойкости поверхности; долговечности (режущей способности) металлорежущего, деревообрабатывающего, слесарного и другого инструмента; создания шероховатости (на поверхности) под последующее гальваническое покрытие; облегчения условий проведения процесса пайки обычным припоем труднопаяемых материалов (нанесение промежуточного слоя, например, меди); увеличения размеров изношенных деталей машин при ремонте; изменения свойств поверхностей изделий из цветных металлов. Благодаря такой обработке создается возможность значительно изменять исходные физические и химические свойства поверхностного слоя (твердость, износостойкость, жаростойкость и др.) как быстрорежущей, так
идругих инструментальных сталей. Электроискровая обработка заключается в легировании поверхностного слоя металла изделия (катода) материалом электрода (анода) при искровом разряде в воздушной среде (рис. 39).
Врезультате химических реакций легирующего металла с диссоциированным атомарным азотом и углеродом воздуха, а также с материалом детали в поверхностных слоях образуются закалочные структуры и сложные химические соединения (высокодисперсные нитриды, карбонитриды и карбиды), возникает диффузионный износостойкий упрочненный слой.
Упрочненный слой имеет высокие износостойкость и твердость (измеренная методом Виккерса на приборе ПМТ-3 твердость составляет 1000-1400 HV и зависит от материала электрода). Общий слой упрочненного металла после электроискровой обработки состоит из верхнего белого нетравящегося и нижнего переходного диффузионного слоев с переменной концентрацией в нем легирующих примесей и карбида, с сильно измененной исходной структурой, постепенно переходящей в структуру основного металла. В большинстве случаев нижний слой по глубине несколько больше верхнего. Благодаря наличию диффузионного слоя в структуре упрочненного металла возможно многослойное упрочнение, в том чис-
Рис. 39. Принципиальная электрическая схема устройства для электроискровой обработки: ЭА — электрод — анод; ДК — деталь — катод на контактной пластине;
1 — графитовая пластинка;
2 — упрочняющий электрод;
3 — упрочняемая поверхность;
4 — корпус инструмента