
КРАСОВСКИЙ_УП
.PDFсмесей должно быть увеличено примерно в 2 раза по сравнению со временем перемешивания подвижных смесей; для легкобетонных смесей время перемешивания уменьшается с увеличением объема бетономешалки, при использовании тонкомолотых добавок, вводимых непосредственно в смеситель, время перемешивания увеличивается в 1,5…2 раза.
9.2. Транспортировка бетонной смеси
Способ доставки бетонной смеси от смесительной установки к месту укладки и необходимое для этой цели оборудование выбирают в зависимости от принятой технологической схемы производства, а также от общего объема укладываемой смеси, суточной потребности в ней, высоты подъема и дальности перевозки.
К месту формования бетонную смесь доставляют различными способами, обеспечивающими сохранение ее связности, однородности и удобоукладываемости: ленточными конвейерами; бункерами и вагонетками по колейным путям; подвесными кюбелями и бадьями, которые электротельфер перемещает по кран-балкам или монорельсам; самоходными вибробункерами и бетононасосами; трансформируют смесь в автобетоносмесителях.
Автобетоновозы для обеспечения качества смеси, включают вращение барабана либо на подходах к месту укладки, либо сразу при загрузке бетоновоза смесью на заводе. При большой дальности возки используют загружаемые сухие смеси, в которые при подходе к объекту из емкостей автобетоновоза дозируется вода.
Для предотвращения загустевания смеси в нее могут вводиться поверхност- но-активные вещества, замедляющие структурообразование в первые 2…4 часа.
9.3. Укладка бетонной смеси
К числу наиболее трудоемких и энергоемких процессов относят укладку бетонной смеси и ее уплотнение в форме или опалубке. Эти операции выполняют при помощи бетоноукладчиков или более простых машин-бетонораздатчиков. Бетоноукладчики позволяют в большей степени механизировать процесс распределения бетонной смеси в форме. Она должна быть уложена в форму так, чтобы в ней не оставались свободные места; особенно тщательно нужно заполнять углы и суженные места формы. Современными, технологически вооруженными фирмами на крупных объектах используются целые комплексы по доставке бетона непосредственно к месту укладки, использующие бетононасосы, развитую сеть бетоноводов, направляемых с помощью кранов к месту укладки бетона.
9.4. Уплотнение бетонной смеси
После укладки бетонной смеси приступают к ее уплотнению.
Уплотнение оказывает на свойства будущего бетона еще большее влияние, чем перемешивание. Любое недоуплотнение приводит к уменьшению прочности бетона, ухудшению всех его свойств и снижению долговечности.
101
PDF created with pdfFactory Pro trial version www.pdffactory.com

Способ уплотнения смеси должен быть тесно связан с удобоукладываемостью смеси (со свойствами смеси, конфигурацией формы (опалубки), материалами для ее изготовления). Так, для жестких смесей требуется энергичное уплотнение и при формовании из них изделий следует применять интенсивную вибрацию с дополнительным пригрузом (рис. 9.9) разной конструкции, прессованием, штампованием, прокатом, вакуумированием, трамбованием. Для подвижных смесей лучше обычная вибрация, центрифугирование, вакуумирование.
Рис. 9.9. Виды пригрузов: а – инерционный; б – инерционный с автономным вибровозбудителем; в – безынерционный; г – безынерционный с автономным вибровозбудителем; д – безынерционный с пневматической подушкой; е – безынерционный с гидро- и пневмоцилиндрами
Из различных способов уплотнения бетонной смеси наибольшее распространение получило вибрирование. Уплотнение смеси при вибрировании происходит в результате передачи ей часто повторяющихся вынужденных колебаний (толчков), в совокупности выражающихся встряхиванием. В каждый момент встряхивания частицы бетонной смеси находятся как бы в подвешенном состоянии, при этом нарушается связь их с другими частицами, силы трения и сцепления уменьшаются. При последующих толчках частицы под действием собственной массы падают и занижают более выгодное положение, при котором на них в меньшей степени могут воздействовать толчки. Вторая причина уплотнения бетонной смеси при вибрировании – тиксотропность. То есть бетонная смесь приобретает свойства тяжелой жидкости и под влиянием сил тяжести расплывается, заполняя форму, что отвечает условию наиболее плотной
упаковки частиц и приводит к получению плотной бетонной смеси.
Это определяет высокие технические свойства вибрированного бетона и экономическую эффективность способа виброуплотнения.
Для качественного уплотнения смеси при принятых параметрах колебаний необходима оптимальная продолжительность вибрирования (рис. 9.10). Длительное вибрирование может привести к расслоению смеси уже в форме или опалубке, недостаточное – к недоуплотнению и ухудшению всех свойств бетона. Обычно дли-
102
PDF created with pdfFactory Pro trial version www.pdffactory.com
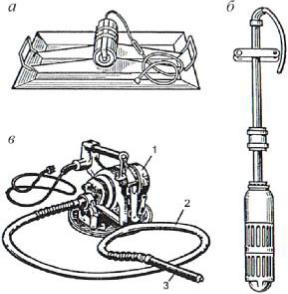
тельность вибрирования, с, принимают в 8…10 раз больше показателя жесткости смеси [30], хотя известны и другие подходы, когда длительность вибрации рекомендуется
tв = жст + 30 с.
При уплотнении бетонной смеси необходимо, чтобы даже на удаленных от вибратора участках амплитуда вибраций и ее интенсивность были достаточны для уплотнения смеси с учетом ее реологических характеристик. Отсюда и появились различные способы уплотнения бетонной смеси. Виброуплотняют бетонную смесь переносными и стационарными вибромеханизмами. Переносные в технологии сборного железобетона применяют ограниченно (в основном на стендах). Основное применение в технологии сборного железобетона находят виброплощадки, представляющие плоские столы, опирающиеся через пружинные опоры на раму (станину). В нижней части к столу жестко прикреплен вибровал с мощным электродвигателем, позволяющим уплотнять бетонную смесь в форме общей массой до 24 т. Зато на строительных площадках преобладают переносные (и как следствие маломощные) вибромеханизмы.
По роду двигателя вибраторы могут быть электромеханическими, электро-
магнитными и пневматическими. |
|
|
|||
В зависимости от вида, формы и |
|
||||
размеров |
бетонируемой конструкции |
|
|||
используют поверхностные с глуби- |
|
||||
ной распространения |
колебаний |
до |
|
||
20…30 см, и глубинные (вибробулавы |
|
||||
или высокочастотные – виброиглы, |
|
||||
рис. 9.11). |
|
|
|
|
|
Главной |
целью виброуплотнения |
|
|||
является удаление воздуха, попадаю- |
|
||||
щего в смесь при перемешивании сме- |
|
||||
си в бетономешалке или укладке смеси |
|
||||
в форму или опалубку. |
|
|
|
||
При станковом или поверхност- |
|
||||
ном вибрировании наибольшее коли- |
|
||||
чество воздушных пор образуется у |
|
||||
поверхности изделия, что существен- |
Рис. 9.11. Переносные вибраторы: а – по- |
||||
но ухудшает ее качество. |
|
верхностный; б, в – глубинные (б – вибробу- |
|||
При |
глубинном |
вибрировании |
лава, в – виброигла) |
||
наибольшее |
воздухововлечение |
на- |
|
блюдается в глубине бетона, а поверхность изделия получается более гладкой. Воздухововлечение увеличивается с уменьшением крупности заполнителя
особенно в мелкозернистых смесях и при несоответствии реологических свойств бетонной смеси характеристикам применяемого режима уплотнения (мы не рассматриваем сейчас воздухововлечение за счет добавок).
103
PDF created with pdfFactory Pro trial version www.pdffactory.com
Низкочастотное вибрирование, в том числе с асинхронным видом колебаний, и ударные способы уплотнения бетонной смеси обеспечивают экономию энергии, уменьшают опасность вибрационного воздействия на рабочих и понижают воздухововлечение в бетонную смесь, способствуя получению изделий с гладкой лицевой поверхностью.
Ударный способ вибрирования предусматривает подъем и падение формы с бетонной смесью с небольшой высоты (как при испытании цементного раствора на встряхивающем столике). При этом происходит постепенное уплотнение бетонной смеси в изделиях значительной высоты и сложной конфигурации, однако смесь должна быть пластичной или хотя бы малоподвижной.
При асинхронном низкочастотном вибрировании форма колеблется с частотой 600…1000 кол./мин. Специальные резиновые ограничители тормозят движение площадки сверху вниз и способствуют возникновению ударного воздействия на бетонную смесь. Сочетание вибрационного и ударного воздействия обеспечивает высокую эффективность уплотнения, в том числе и жестких смесей.
В технологии бетона применяются и безвибрационные методы уплотнения бетонной смеси. Среди них наиболее распространены литьевой, набивной, центрифугирование.
Для литьевой технологии используют высокоподвижные или литые бетонные смеси, которые транспортируют по трубопроводам и заливают в опалубку. Также необходимы меры, предотвращающие возможное расслоение.
Литьевой способ получил признание благодаря внедрению суперпластификаторов, способствующих получению более подвижных смесей при ограниченном водосодержании, и успешно применяется в монолитном строительстве.
Набивной способ позволяет эффективно уплотнять бетонные смеси с низким водосодержанием и В/Ц отношением. Он предусматривает передачу составляющим бетонной смеси кинетической энергии, под действием которой бетонная смесь забрасывается в форму и уплотняется.
Известные разновидности этой технологии можно объединить в три группы.
1.Шприц-бетон – частицы цемента и заполнителя подаются в сопло установки, где смешиваются с водой и под действием энергии сжатого воздуха забрасываются в форму или на поверхность сооружения.
2.Набрызг-бетон – бетонная смесь перемешивается заранее и через специальное сопло забрасывается в форму, причем смеси используются более подвижные, чем в первом случае. Уменьшается эффективность уплотнения, поскольку трудно обеспечить смеси большое количество кинетической энергии.
3.Заранее приготовленной смеси механическим способом сообщается кинетическая энергия, необходимая для набрызга смеси и ее уплотнения. Для этого используется набрызгивающее устройство в виде быстровращающихся валов, в щель между которыми подается бетонная смесь из бункера.
Обеспечивая достаточно высокое уплотнение бетонной смеси, набивные способы не позволяют получать гладкую поверхность бетона и требуют специальных дополнительных операций по ее отделке.
104
PDF created with pdfFactory Pro trial version www.pdffactory.com

При центрифугировании бетонная смесь помещается в цилиндрическую форму, при вращении которой она уплотняется за счет действия центробежных сил, а излишняя вода отжимается на внутреннюю поверхность формуемого слоя бетона и удаляется самотеком из формы, установленной под небольшим углом к горизонту. Этим способом формуются трубы, опоры линий передач и другие цилиндрические изделия.
Для вакуумирования на поверхности бетона помещают вакуум-щит и создают разряжение. Под действием разряжения часть воды отсасывается из поверхностных слоев бетона, который доуплотняется под действием щита, прижимаемого к поверхности атмосферным давлением. Для повышения эффекта воздействие применяют сочетание вакуумирования с вибрированием.
Прессование – способ (редко применяется) для уплотнения бетонной смеси в технологии сборного железобетона, хотя по технологическим показателям он отличается большой эффективностью – позволяет получать бетон особо высокой плотности и прочности при минимальном расходе цемента (100…150 кг/м3 бетона). Однако для эффективного уплотнения необходимо давление 10…15 МПа, которое можно создать только с помощью дорогостоящих мощных прессов. Поэтому в технологии сборного железобетона прессование применяют как дополнение к вибрации. Разновидностью вибропрессования является вибро-
штампование (рис. 9.12).
Рис. 9.12. Схемы виброштампования бетонной смеси: а – одномассным виброштампом; б – двухмассным штампом; 1 – виброштамп; 2 – прижимная ограничительная рама; 3 – бортовая оснастка; 4 – безынерционный пригруз; 5 – эластичная рессора
В последнее время получает распространение уплотнение жестких бетонных смесей с помощью быстро катящихся по ее поверхности цилиндров – роликовое уплотнение. Этот способ чаще применяют при формовании бетонных труб.
Для уплотнения малоцементных смесей в плотинах гидростанций используют катковые уплотнители и др.
105
PDF created with pdfFactory Pro trial version www.pdffactory.com

9.5. Твердение бетона и уход за ним
Бетон набирает прочность постепенно, по мере твердения цементного камня. В значительной степени скорость нарастания прочности зависит от температуры и влажности среды. Как уже отмечалось, нормальными условиями при-
нято считать t = (20 ± 3) оС и W = 95÷100 %.
Сумма мероприятий, обеспечивающих благоприятные условия твердения уплотненной бетонной смеси, а также способы, предохраняющие бетон от повреждения его структуры в раннем возрасте, составляет уход за бетоном. Уход должен быть организован сразу после укладки и уплотнения бетонной смеси и прежде всего нужно защищать поверхность от высыхания.
Одним из эффективных методов ухода за свежеуложенным бетоном, например в дорожном строительстве, является покрытие его поверхности пленкообразующими веществами, в качестве которых применяют битумные или латексные эмульсии, синтетический каучук и т. д. (рис. 9.13).
Наряду с этим горизонтальные поверхности после схватывания бетона покрывают песком или опилками и периодически их увлажняют. Длительность сроков увлажнения зависит от атмосферных условий: в жаркие дни – до двух недель, а в прохладную погоду – несколько дней. В холодные дни бетон следует предохранять от
охлаждения, чтобы не замедлилось твердение, и тем более от замерзания. Конструкции отгружать потребителю или на склад можно только после то-
го, когда бетон достигает прочности, установленной проектом, как правило, не менее 70 %. Это определяется испытаниями контрольных образцов бетона.
Контрольные вопросы
1.Как приготавливается бетонная смесь?
2.Какие типы дозаторов вы знаете и с какой точностью дозируются компоненты бетонной смеси?
3.Назовите типы смесителей для бетона.
4.Как транспортируют бетонную смесь?
5.С какой целью уплотняют бетонную смесь?
6.Назовите средства уплотнения бетонной смеси.
7.Каковы правила ухода за бетоном?
106
PDF created with pdfFactory Pro trial version www.pdffactory.com

10.ТВЕРДЕНИЕ БЕТОНА ПРИ ПОНИЖЕННЫХ
ИОТРИЦАТЕЛЬНЫХ ТЕМПЕРАТУРАХ
10.1. Твердение бетона при пониженных температурах
Для уточнения термина «пониженные температуры» следует напомнить, что стандартными условиями твердения при испытаниях принято считать температуру (20±3) оС и влажность 95÷100 %. Любые отклонения от этих условий приводят к изменениям в процессе твердения. В этих условиях понятие «пониженные» включает температуры от 17 до 0 °С, температуры ниже 0 °С относятся к группе «отрицательных».
При производстве бетонных работ в осенне-весенний период, а в условиях севера Дальневосточного региона в начале и конце летнего периода (а при бетонировании по методу термоса и в зимний), вопросы продолжительности выдерживания бетона при пониженных положительных температурах становятся вполне актуальными.
Исследованиями влияния температурного фактора на процесс твердения было установлено положительное влияние предварительной гидратации цемента [31], выдерживания готовой бетонной смеси при пониженных температурах перед укладкой в гидротехнические и другие массивные конструкции, а также прогрева.
Дело в том, что для формирования структуры бетона понижение температуры сказывается, наоборот, положительно: вследствие температурного сжатия составляющих бетона, более полного прохождения процесса седиментации при замедленном схватывании цемента формируется более плотная структура цементного камня.
Однако с понижением температуры и ее приближением к 0 °С твердение бетона резко замедляется, особенно в раннем возрасте. Объясняется это замедле-
нием процесса растворения, скорости |
|
|
химических |
реакций взаимодействия |
|
воды с минералами клинкера и резким |
|
|
ослаблением |
диффузионного переме- |
|
щения вновь образовавшихся частиц от |
|
|
поверхности цементной частицы в по- |
|
|
ровое пространство, заполненное водой. |
|
|
Снижение температуры в пределах |
|
|
от 20 до 0 оС приводит к снижению |
|
|
прочности бетона до 50 % (рис. 10.1) |
|
|
[35]. |
|
|
Наиболее это заметно в бетонах на |
|
|
пуццолановых и шлаковых портланд- |
|
|
цементах. Поэтому при решении вопро- |
Рис. 10.1. Изменение прочности бетона на |
|
сов о распалубке конструкций, частич- |
Спасском портландцементе 400 при тем- |
|
ной или полной их загрузке очень важ- |
пературах: 1 – 20 оС; 2 – 10 оС; 3 – 5 оС; 4 – |
|
но иметь данные не только о темпера- |
0 оС |
|
|
107 |
|
PDF created with pdfFactory Pro trial version www.pdffactory.com

турном режиме твердения бетона (это позволяет пользоваться температурными коэффициентами скорости твердения), но и результаты испытания контрольных образцов, хранившихся в аналогичных условиях.
10.2. Гидратация цемента при отрицательных температурах
Говорить о гидратации цемента при отрицательных температурах, казалось бы, не имеет смысла, поскольку вода замерзает при 0 оС. Однако частицы клинкера имеют различного рода микротрещины, проникая в которые, а также, адсорбируясь на их поверхности, часть воды изменяет свои физические свойства. Такая вода замерзает при отрицательных температурах, но, находясь еще в жидком состоянии, может реагировать с минералами цемента. Вследствие этого, постепенно замедляясь, процесс гидратации C3S, C3A и C4AF наблюдается при температурах до –15 °С, с C2S до –10 °С.
Исследования показали, что при действии низких температур на сформированный цементный камень фазовый состав гидратных образований изменяется незначительно. Основные изменения обусловлены сублимацией льда и превращениями сильнообводненных гидратных соединений, например, (3CaO·Al2O3·3CaSO4·31H2O) – эттрингита.
Действительно, наиболее существенное влияние на свойства портландцемента оказывают силикаты кальция C3S и β-C2S. Электронно-стереомикроско- пические исследования микроструктуры камня C3S, твердевшего при –15 °С и +20 °С, совершенно различны. В микроструктуре камня С3S, твердевшего на морозе, полностью отсутствуют кристаллические блоки сросшихся шестигран-
ных призматических или гексагональных пластинчатых кристал-
лов Ca(ОН)2 (рис. 10.2) [32].
До месяца твердения структура C3S рыхлая, состоит из отдельных зерен, слабо соединенных между собой. Поверхность их покрыта мельчайшими гидросиликатами кальция. Основу микроструктуры камня составляют чешуйчатые и округлые ломаные частички, а также участки мелких кристаллов кальцита, что можно объяснить более стесненными ус-
ловиями роста кристаллов, так как все свободное пространство заполнено льдом, препятствующим росту кристаллов.
Как и в случае с C3S, в результате гидратации β-C2S при –15 °С образуются чешуйчатые гидросиликаты кальция, которые меньше аналогичных чешуек,
108
PDF created with pdfFactory Pro trial version www.pdffactory.com
возникающих при нормальных условиях твердения. Количество их с возрастом гидратации увеличивается, а после шести месяцев твердения отмечается их собирательная рекристаллизация. Как и сформировавшиеся при нормальной температуре, гидросиликаты чешуйчатой формы представляют собой зародыши кристаллов гидросиликатов кальция, выпавших из сильно перенасыщенных растворов. Их рост может происходить, в частности, при повышении температуры окружающей среды.
Сильно замедленный процесс гидратации β-C2S при –15 °С резко снижает увеличение его прочности (табл. 10.1).
Таблица 10.1
Влияние условий твердения на прочность камня C3S и β-C2S
|
Температура |
|
Предел прочности в различном возрасте |
|
||||||
Минерал |
|
|
|
твердения, МПа |
|
|
|
|||
твердения, °С |
|
|
|
|
|
|
||||
|
1 сут |
|
7 сут |
|
28 сут |
|
6 мес |
|
2 года |
|
|
|
|
|
|
|
|||||
|
+20 |
10 |
|
55 |
|
56 |
|
59 |
|
79 |
С3S |
0 |
0 |
|
14 |
|
26 |
|
44 |
|
– |
|
–15 |
0 |
|
5 |
|
17 |
|
42 |
|
72 |
|
+20 |
0 |
|
2 |
|
4 |
|
3 |
|
56 |
β-C2S |
0 |
0 |
|
0 |
|
0 |
|
12 |
|
– |
|
–15 |
0 |
|
0 |
|
0 |
|
9 |
|
19 |
Электронно-стереомикроскопические исследования камня C3А, твердевшего при отрицательных температурах, показали наличие достаточно плотной структуры уже в первые сутки твердения [33, 34]. Особенность гидратации C3А при этом проявляется в образовании сильнообводненных гексагональных гидратов типа С4AH19, перекристаллизовывающихся с возрастом твердения по схеме
С4AH19 → С4AH13 → С3AH6 [Ш].
Выделяющаяся при этом вода участвует в процессе дальнейшей гидратации вяжущего и ее количества вполне достаточно для осуществления процесса гидратации. В период с 1 по 28 сут твердения C3А в нормальных условиях дополнительно гидратирует на 10 %, а при –15 оС – на 15 %, что значительно уплотняет структуру камня. Повышение плотности камня C3А при твердении на морозе, а также уменьшение деструктивного фактора – теплоты гидратации за счет ее отвода на разогрев массы и в окружающую среду обеспечивает повышение прочности камня C3А на целый порядок.
Алюмоферриты кальция, представляющие собой серию твердых растворов, которые мы отождествляем с C4AF, составляют в клинкере портландцемента около 10–15 % и оказывают существенное влияние на процессы твердения портландцемента, обеспечивая высокую начальную прочность цементного камня.
Данные термического и микроскопического анализов свидетельствуют о том, что основными продуктами гидратации алюмоферритов кальция на морозе являются гексагональные гидроалюмоферриты с более мелкодисперсной струк-
109
PDF created with pdfFactory Pro trial version www.pdffactory.com
турой и малым количеством пор, что обеспечивает высокую прочность камня уже в первые сутки твердения. Установлено, что прочность алюмоферритов кальция, твердевших при –15 °С, определяется величиной выделяемого тепла гидратации. Уменьшение скорости тепловыделения минерала C6A2F по сравнению с C3А способствует увеличению его прочности в 4…5 раз при –15 °С.
Итак, исследования фазового состава и микроструктуры отдельных клинкерных минералов, твердеющих при отрицательных температурах, показали, что по кинетике нарастания прочности их можно разделить на 2 группы. К первой относятся силикаты кальция, медленно твердеющие при отрицательных температурах, а ко второй – С3А и алюмоферриты кальция, прочность которых и с понижением температуры нарастает достаточно быстро.
Аналогично кинетике нарастания прочности изменяется степень гидратации минералов при низких температурах. Для С3S отмечается уменьшение скорости гидратации в начальный период при –15 °С в пять раз по сравнению с нормальными условиями, в то время как для С3А и алюмоферритов кальция этот показатель практически не меняется. Максимальная степень гидратации на морозе
присуща С3А.
Таким образом, для интенсификации процессов твердения цемента в условиях отрицательных температур необходимо, прежде всего, предотвратить образование льда в цементном камне за счет связывания большого количества воды в метастабильные гидратные новообразования, а также обеспечить длительное, но умеренное, тепловыделение в цементном камне. Этим условиям наиболее полно удовлетворяют алюмоферриты кальция, обладающие плотной структурой и обеспечивающие высокую начальную прочность камня. При длительном возрасте твердения резервом нарастания прочности является алитовая фаза
(табл. 10.2)
Таблица 10.2
Влияние условий твердения мономинералов на прочность камня
|
Температу- |
Предел прочности в различном возрасте твердения, МПа |
||||||
Минерал |
ра тверде- |
|
|
|
|
|
|
|
1 сут |
2 сут |
7 сут |
28 сут |
6 мес |
2 года |
|||
|
ния, оС |
|||||||
|
+20 |
10 |
52 |
55 |
56 |
59 |
79 |
|
С3S |
0 |
0 |
2 |
14 |
26 |
44 |
– |
|
|
–15 |
0 |
0 |
5 |
17 |
42 |
72 |
|
|
+20 |
0 |
1 |
2 |
4 |
– |
56 |
|
β-C2S |
0 |
0 |
0 |
0 |
0 |
12 |
– |
|
|
–15 |
0 |
0 |
0 |
0 |
9 |
19 |
|
C3A |
+20 |
0,6 |
– |
0,6 |
1,3 |
6,4 |
– |
|
–15 |
4,2 |
– |
5,5 |
13,5 |
17,0 |
29,0 |
||
|
||||||||
|
+20 |
32,5 |
60,0 |
61,1 |
67,5 |
69,2 |
73,0 |
|
С4AF |
0 |
42,5 |
54,0 |
55,3 |
57,2 |
59,2 |
– |
|
|
–15 |
27,0 |
53,0 |
54,6 |
55,8 |
58,3 |
59,1 |
|
|
|
|
110 |
|
|
|
|
PDF created with pdfFactory Pro trial version www.pdffactory.com