
Materialovedenie-uchebnik
.pdfСкорость охлаждения также влияет на результат закалки. Оптимальной охлаждающей является та среда, которая быстро охлаждает деталь в интервале температур минимальной устойчивости переохлажденного аустенита и замедленно в интервале температур мартенситного превращения для обеспечения равномерности этого превращения во всех зонах детали и снижения опасности образования трещин. Наиболее распространенными закалочными средами являются вода, водные растворы солей, щелочей, масло, расплавленные соли. При закалке в этих средах различают три периода:
∙пленочное охлаждение, когда на поверхности стали образуется «паровая рубашка», которая равномерно и сплошь окружает изделие, пар отнимает тепло не интенсивно, и скорость охлаждения в этот период сравнительно невелика;
∙пузырьковое кипение, наступающее при полном разрушении паровой пленки. В этот период происходит быстрый отвод тепла, так как на образование пузырьков пара расходуется большое количество тепла, и температура металла быстро снижается;
∙конвективный теплообмен, который отвечает температурам ниже температуры кипения охлаждающей жидкости. Теплоотвод в этот период происходит с наименьшей скоростью, которая определяется физическими свойствами жидкости (теплоемкостью, вязкостью и теплопроводностью), разностью температур и скоростью циркуляции.
Закалочная жидкость охлаждает тем интенсивнее, чем шире интервал стадии пузырчатого кипения, т. е. чем выше температура перехода от первой стадии охлаждения ко второй и чем ниже температура перехода от второй стадии к третьей.
Впрактике термической обработки сталей нашли широкое применение различные способы охлаждения в зависимости от размеров деталей, их химического состава и требуемой структуры (рис. 8.1).
Непрерывная закалка (1) – наиболее простой способ закалки. Деталь после нагрева помещают в закалочную среду и оставляют в ней до полного охлаждения. Способ применяют при закалке несложных изделий из углеродистых и легированных сталей. Закалочной средой для углеродистых сталей диаметром более 5 мм служит вода, менее 5 мм и легированных – масло.
Закалка в двух средах (2) осуществляется в разных температурных интервалах с разной скоростью охлаждения. Вначале деталь охлаждают в интервале температур 750–400 ° С в воде, затем переносят в другую охлаждающую среду – масло. Замедленное охлаждение в масле, где происходит мартенситное превращение, приводит к уменьшению возникающих при закалке внутренних напряжений и опасности появления трещин. Применяется этот способ при закалке инструмента из высокоуглеродистой стали.
91
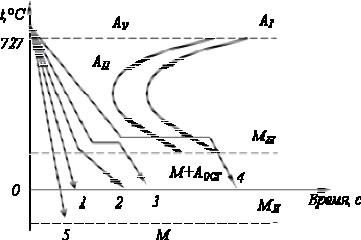
Рис. 8.1. Способы охлаждения при закалке сталей: 1 – непрерывная закалка; 2 – закалка в двух средах; 3 – ступенчатая закалка; 4 – изотермическая закалка; 5 – обработка холодом
При ступенчатой закалке (3) изделие охлаждают в закалочной среде, имеющей температуру более высокую, чем мартенситная точка данной стали. Охлаждение и выдержка в этой среде обеспечивает равномерное распределение температуры закалочной ванны по всему сечению детали. Затем следует окончательное, обычно медленное охлаждение, во время которого и происходит превращение аустенита в мартенсит. Этот способ дает закалку с минимальными внутренними напряжениями, однако его применение целесообразно для изделий небольшого размера из углеродистых и низколегированных сталей, закаливающихся в воде.
Изотермическая закалка (4) позволяет получать наиболее хорошее сочетание прочностных и пластических свойств. При изотермической закалке нагретую деталь переносят в ванну с расплавленными солями, имеющую температуру на 50–100 ° С выше мартенситной точки МH, выдерживают при этой температуре до завершения превращения аустенита в бейнит и затем охлаждают на воздухе. Во всех предыдущих случаях при закалке происходит образование мартенситной структуры.
При изотермической закалке в детали возникают минимальные напряжения, исключается образование трещин и уменьшается деформация.
Обработка холодом (5) применяется для легированных сталей, у которых температура окончания мартенситного превращения МК значительно ниже 0 ° С. Если закаливать эти стали обычным способом, то, наряду с мартенситом, в структуре оказывается значительное количество остаточного аустенита. Остаточный аустенит понижает твердость закаленной стали и может вызвать нестабильность размеров готовых деталей, т. к. в процессе их работы может происходить превращение остаточного аустенита в мартенсит.
Для стабилизации размеров закаленных изделий и повышения их твердости проводится охлаждение до температуры МК, в процессе которо-
92
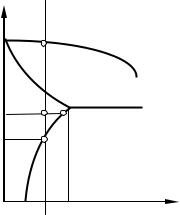
го аустенит превращается в мартенсит. Температура МК легированных сталей находится в широких пределах от – 40 до –196 ° С.
Обработке холодом подвергают быстрорежущие стали, цементованные детали, измерительные инструменты, подшипники и другие особо точные изделия.
Закалка без полиморфного превращения – это термическая обработка,
фиксирующая при более низкой температуре состояние сплава, свойственное ему при более высокой температуре. Такая термическая обработка применима к сплавам, у которых одна фаза полностью или частично растворяется в другой.
t,°C |
I |
|
Ж |
||
|
Ж + α
b
t2
α
t1 |
α+β |
|
α+βII
A a b' % B
Рис. 8.2. Диаграмма состояния сплава с переменной растворимостью компонента В в А
Например, в сплаве I (рис. 8.2) при нагреве до температуры t2 β-фаза растворяется в α-фазе. При обратном медленном охлаждении β-фаза выделяется из α-фазы, в которой концентрация компонента В уменьшается в соответствии с линией предельной растворимости аb. Т. к. составы α- и β- фаз различны, то выделение β-фазы связано с диффузионным перераспределением компонентов. При достаточном быстром охлаждении диффузионное перераспределение, необходимое для зарождения и роста кристаллов β-фазы, не успевает пройти и эта фаза не выделяется. После такой обработки (закалки) сплав состоит из одного пересыщенного α-твердого раствора.
Закалка без полиморфного превращения широко применяется к алюминиевым, магниевым, никелевым, медным и другим сплавам.
Закаливаемость – способность стали повышать твердость в результате закалки.
Необходимым условием закаливаемости стали является переохлаждение ее до температуры ниже точки МН. Минимальная скорость охлаждения аустенита, при которой отсутствует диффузия углерода и происходит пре-
вращение в мартенсит, называется критической скоростью охлаждения.
Эту скорость можно определить на С– образной диаграмме (рис. 8.3).
93
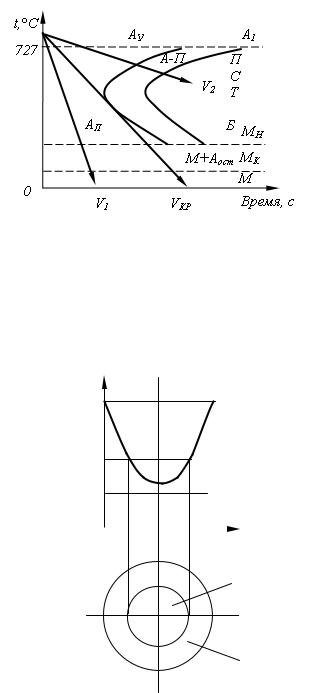
Рис.8.3. Определение скорости охлаждения при закалке
При закалке скорость охлаждения должна быть больше критической (V1). Для обычных углеродистых сталей значение критической скорости охлаждения составляет около 150 ° С/сек, поэтому на практике необходимо охлаждать сталь при закалке очень быстро, чтобы предупредить распад аустенита на феррито-цементитную смесь.
Vохл, °/сек
Vк
V'к
D, мм
феррит + цементит
мартенсит
Рис. 8.4. Распределение структуры по глубине цилиндрического образца
Скорость охлаждения на поверхности изделия может быть больше критической, а в центре меньше. В этом случае аустенит в поверхностных слоях превратится в мартенсит, а в центре изделия испытывает перлитное превращение, т. е. деталь не прокалится насквозь. Прокаливаемость – одна из важнейших характеристик стали.
Прокаливаемостью называют способность стали получать закаленный слой на ту или иную глубину с мартенситной или троосто-мартенситной структурой.
Для характеристики прокаливаемости стали часто используют в качестве параметра критический диаметр. Критический диаметр – это макси-
94
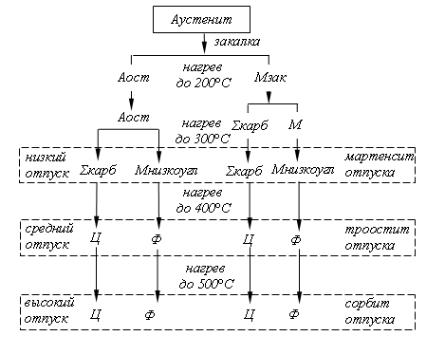
мальный диаметр цилиндрического образца, который прокаливается насквозь в данной охлаждающей среде.
Критический диаметр увеличивается и, соответственно, повышается прокаливаемость стали при увеличении охлаждающей способности закалочной среды и при введении в сталь легирующих элементов. Например, углеродистая сталь имеет критический диаметр 8–10 мм. Это значит, что при закалке более крупных изделий из данной стали сердцевина не будет закаленной (рис. 8.4).
8.2. Отпуск закаленных углеродистых сплавов
Нагрев закаленных сталей до температур, не превышающих А1, называют отпуском. В результате закалки чаще всего получают структуру мартенсита с некоторым количеством остаточного аустенита. Процесс нагрева и выдержки закаленной стали сопровождается превращением мартенсита и остаточного аустенита. В результате этого превращения уменьшаются внутренние напряжения и хрупкость, повышаются вязкость и пластичность.
Фазовые превращения при отпуске закаленной стали можно показать в виде схемы (рис. 8.5).
Рис. 8.5. Схема фазовых превращений при отпуске закаленной стали
При низкотемпературном отпуске (150–300 ° С) из мартенсита выде-
ляется часть избыточного углерода с образованием мельчайших карбидных частиц. Дисперсные кристаллы Σ -карбида когерентны с решеткой мартенсита. В мартенсите остается около 0,2 % растворенного углерода. Распад остаточного аустенита происходит по механизму бейнитного превращения: образуется смесь кристаллов низкоуглеродистого мартенсита и
95
дисперсных карбидов. При температуре около 250 ° С начинается превращение Σ -карбида в цементит; при этом когерентность решеток α-твердого раствора и карбида нарушается.
При среднем отпуске (350–400 ° С) из мартенсита выделяется весь избыточный углерод с образованием цементитных частиц. При этом тетрагональность решетки железа уменьшается, она становится кубической. В результате вместо мартенсита остается феррит. Такая ферритоцементитная смесь называется трооститом отпуска, а процесс, приводящий к таким изменениям, среднетемпературным отпуском. При таком нагреве значительно уменьшаются внутренние напряжения и снижается плотность дислокаций.
При более высоких нагревах (500 ° С и выше) в углеродистых сталях происходят изменения структуры, не связанные с фазовыми превращениями: изменяются форма, размер карбидов и структура феррита. С повышением температуры происходит коагуляция – укрупнение частиц цементита. Форма кристаллов постепенно становится сферической – этот процесс назвали сфероидизацией.
Коагуляция и сфероидизация карбидов происходят с заметной скоростью, начиная с температуры 400 ° С. Зерна феррита становятся крупными и их форма приближается к равноосной. Феррито-карбидная смесь, которая образуется после отпуска при температуре 400–600 ° С, называется сорбитом отпуска. При температуре, близкой к точке А1, образуется грубая феррито-цементитная смесь – зернистый перлит.
Влияние температуры отпуска на механические свойства стали с 0,4 % углерода показано в таблице 8.1.
Таблица 8.1
Температура |
|
|
|
отпуска, |
τ , МПа |
НRС |
δ , % |
° С |
|
|
|
Без отпуска |
1400 |
60 |
3 |
200 |
1400 |
52 |
4 |
400 |
1080 |
35 |
11 |
600 |
700 |
12 |
22 |
При отпуске некоторых сталей возможны негативные явления – отпускная хрупкость. Это снижение ударной вязкости сталей, отпущенных при температуре 250–400 и 500–550 º С (рис. 8.6).
Первый вид отпуска называется необратимой хрупкостью (Ι рода); присущ практически всем сталям и обусловлен неоднородным выделением карбидов из мартенсита. Повторный отпуск при более высокой температуре (400–500 ° С) снимает хрупкость и сталь становится к ней не склонной
96
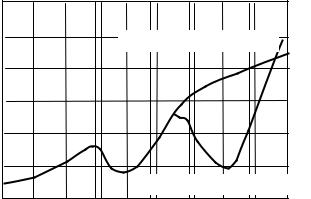
даже при повторном нагреве при 250–400 ° С. В связи с этим эта хрупкость получила название необратимой. Отпуск сталей, склонных к этому виду хрупкости при температурах 250–400 ° С, не назначается. Этот род хрупкости не зависит от скорости охлаждения после отпуска.
Ударная вязкость, Дж/м2
0,016
I |
II |
Быстрое охлаждение
0,012
0,006
Медленное охлаждение
0 |
150 |
300 |
450 |
600 |
Температура отпуска, ° С
Рис. 8.6. Влияние температуры отпуска на ударную вязкость стали:
Ι – зона необратимой отпускной хрупкости; ΙΙ – зона обратимой отпускной хрупкости
Второй вид отпускной хрупкости (ΙΙ рода) является обратимым. Проявляется он при медленном охлаждении легированной стали при температуре 500–550 ° С. Данная хрупкость может быть устранена повторным отпуском с большой скоростью охлаждения. В этом случае устраняется причина этой хрупкости – выделение карбидов по границам бывших аустенитных зерен. Устранение отпускной хрупкости легированных сталей возможно введением в них малых добавок молибдена (0,2–0,3%) или вольф-
рама (0,5–0,7%).
Тесты для контроля текущих знаний.
1.Твердый раствор внедрения углерода в Feα называется:
1) цементитом;
2) ферритом;
3) аустенитом;
4) ледебуритом.
2.Твердый раствор внедрения углерода в Feγ называется:
1) цементитом;
2) ферритом;
3) аустенитом;
4) ледебуритом.
3.Химическое соединение Fe3C называется:
97
1)цементитом;
2)ферритом;
3)аустенитом;
4)ледебуритом.
4. Упорядоченный перенасыщенный твердый раствор углерода в Feα
называется:
1) цементитом;
2) ферритом;
3) аустенитом;
4) мартенситом.
5. Сталями называют:
1) сплавы железа с углеродом, содержащие до 0,02% С; 2) сплавы железа с углеродом, содержащие от 0,02 до 2,14% С;
3) сплавы железа с углеродом, содержащие от 2,14 до 6,67% С; 4) сплавы железа с углеродом, содержащие 0,8% С.
6. Чугунами называют:
1) сплавы железа с углеродом, содержащие до 0,02% С; 2) сплавы железа с углеродом, содержащие от 0,02 до 2,14% С;
3) сплавы железа с углеродом, содержащие от 2,14 до 6,67% С; 4) сплавы железа с углеродом, содержащие 0,8% С.
7. Эвтектоидной сталью называют:
1)сплавы железа с углеродом, содержащие до 0,02% С;
2)сплавы железа с углеродом, содержащие от 0,02 до 2,14% С;
3)сплавы железа с углеродом, содержащие от 2,14 до 6,67% С;
4)сплавы железа с углеродом, содержащие 0,8% С.
8.Завтектоидной сталью называют:
1)сплав железа с углеродом, содержащий до 0,02% С;
2)сплав железа с углеродом, содержащий от 0,02 до 0,8% С;
3)сплав железа с углеродом, содержащий от 0,8 до 2,14% углерода;
4)сплав железа с углеродом, содержащий 0,8% углерода.
9.Доэвтектоидной сталью называют:
1)сплав железа с углеродом, содержащий до 0,02% С;
2)сплав железа с углеродом, содержащий от 0,02 до 0,8% С;
3)сплав железа с углеродом, содержащий от 0,8 до 2,14% С;
4)сплав железа с углеродом, содержащий 0,8% С.
10. Доэвтектическими чугунами называют:
98
1)сплавы железа с углеродом, содержащие до 2,14% С;
2)сплавы железа с углеродом, содержащие от 2,14 до 4,3% С;
3)сплавы железа с углеродом, содержащие от 4,3 до 6,67% С;
4)сплавы железа с углеродом, содержащие 4,3% С.
11. Эвтектическим чугуном называют:
1) сплав железа с углеродом, содержащий до 2,14% С; 2) сплав железа с углеродом, содержащий от 2,14 до 4,3% С;
3) сплав железа с углеродом, содержащий от 4,3 до 6,67% С; 4) сплав железа с углеродом, содержащий 4,3% С.
12. Заэвтектическими чугунами называют:
1) сплавы железа с углеродом, содержащие до 2,14% С; 2) сплавы железа с углеродом, содержащие от 2,14 до 4,3% С;
3) сплавы железа с углеродом, содержащие от 4,3 до 6,67% С; 4) сплавы железа с углеродом, содержащие 4,3% С.
13. Какие примеси в железоуглеродистых сталях относятся к вредным:
1)кремний;
2)марганец;
3)сера;
4)фосфор.
14. Какие примеси в железоуглеродистых сталях относятся к полезным:
1)кремний;
2)марганец;
3)сера;
4)фосфор.
15. В каких сталях в наибольшей степени удален кислород:
1)в кипящих «кп»;
2)в спокойных «сп»;
3)в полуспокойных «пс»;
4)в низкоуглеродистых.
16.Стали, характеризующиеся низким содержанием вредных при-
месей и неметаллических включений, называются:
1)малопрочными и высокопластичными;
2)углеродистыми качественными;
3)углеродистыми сталями обыкновенного качества;
4)автоматными сталями.
99
17. Чугун, в котором весь углерод находится в виде химического соединения Fe3С, называется:
1)серым;
2)ковким;
3)белым;
4)высокопрочным.
18.Чугуны с пластинчатой формой графита, называются:
1) серыми;
2) ковкими;
3) белыми;
4) высокопрочными.
19.Чугуны, в которых графит имеет шаровидную форму, называют-
ся:
1)серыми;
2)ковкими;
3)белыми;
4)высокопрочными.
20. Чугуны, в которых графит имеет хлопьевидную форму называется:
1)серыми;
2)ковкими;
3)белыми;
4)высокопрочными.
21.Среднее значение предела прочности чугуна СЧ25 в МПа равно:
1) 25;
2) 150;
3) 250;
4) 2500.
22.Среднее значение предела прочности чугуна ВЧ60 в МПа равно:
1) 60;
2) 150;
3) 600;
4) 2500.
23.Среднее значение предела прочности чугуна КЧ37–12 в МПа рав-
но:
1) 37;
100