
Насосы С11АЭ,11МТ,11ТС / 11-МТ / 2.Ксерокопии книг / 03.Книга.ГЦН_АЭС
.pdfВ ГЦН с механическим уплотнением вала осевой подшипник работает на существенно более высоких удельных нагрузках (до 6 МПа), поэтому использовать рассмотренные конструкции невозможно. В этих ГЦН для осевых подшипников от внешнего источника подводятся специальные масла, а сама конструкция подпятника представляет собой набор не связанных между собой колодок, каждая из которых может поворачиваться вокруг оси или точки.
Известны две конструкционные схемы такого подпятника. В первой каждая колодка имеет жесткую точечную опору качания («подпятник Митчеля»), во второй колодки опираются на выравнивающие устройства гидравлического, рессорного или рычажного типа. Последний известен как подпятник с уравнительной системой Кингсбери. Принцип работы колодочных подпятников заключается в том, что при правильно установленном центре поворота колодки сами принимают наклон, соответствующий максимальному несущему усилию при любых условиях работы. Эти подшипники при эффективном теплоотводе могут работать с системой смазки «масляная ванна», т. е. не нуждаются в наружном источнике давления.
На рис. 3.13 изображен гидродинамический осевой подшипник Митчеля насосов реактора БН-350. Пята представляет собой диск, изготовленный из стали 40Х, нижний торец которого является рабочей поверхностью. Пята установлена на вал 6 на шпонке н крепится в осевом направлении двумя закладными полукольцами 5. Пята вместе с валом опирается на подпятник, состоящий из семи колодок 8, изготовленных из углеродистой стали с заливкой рабочей поверхности баббитом Б-83. Колодки, самоустанавливающиеся на опорных винтах 9, выверяются по высоте при помощи контрольной плиты.
Пята и подпятник заключены в масляную ванну с повышенным давлением, которое поддерживается за счет щелевого уплотнения В (зазор 0,5—1 мм) между верхним торцом пяты и кольцом 4. Масло поступает в каждую колодку через кольцевой коллектор 2 и три отверстия 1 в корпусе 11 радиального подшипника. Циркуляция масла осуществляется насосами системы смазки [6].
В подшипнике ГЦН АЭС «Obrigheim» (ФРГ) применена гидравлическая система выравнивания (рис. 3.14) [3, гл. 2]. Качающиеся колодки опираются на кольцо, которое установлено на подвижные поршни. Цилиндры всех поршней находятся под давлением масла и гидравлически связаны между собой. Это обеспечивает автоматическое поддержание одинакового зазора между поверхностями колодок и диском пяты.
61
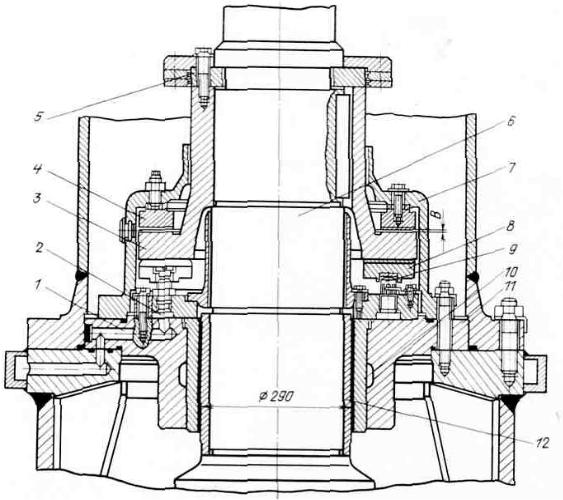
Рис. 3.13. Схема радиально-осевого подшипника насоса реактора БН-350:
1 – |
отверстие |
для |
подвода масла; |
2 |
– кольцевой коллектор; |
3 – диск |
пяты; 4 |
– |
упорное кольцо; |
5 – |
закладное полукольцо; 6 – вал; |
7 – |
корпус; 8 – колодка; 9 – |
винт опорный; 10 – |
втулка радиального |
||||
подшипника; 11 – корпус радиального подшипника; 12 – втулка вала |
|
|
|
||||||
|
На рис. |
3.15 |
показан гидродинамический двухсторонний |
осевой |
подшипник с |
выравнивающим устройством рессорного типа насосов реактора типа РБМК [7]. Диск пяты 3 вместе с валом 4 опирается на подпятник, состоящий из восьми колодок 7, воспринимающих осевую нагрузку, направленную вниз. Для лучшего теплоотвода колодки выполнены из оловянистой бронзы Бр 01ОФ1. Рабочие поверхности колодок наплавлены баббитом Б-83 толщиной 3 мм с шероховатостью поверхности Rа 0,32. Каждая колодка имеет опорное ребро, параллельное выходной кромке колодки, со смещением относительно оси симметрии на 9%. Колодка 7 устанавливается на пакет рессор 8 из стали 60С2А с твердостью поверхности НКСЭ 42—49 [8]. Напряжение изгиба под нагрузкой 196 кН составляет 50 МПа при прогибе пакета рессор 0,49 мм. Максимальный зазор между нижней пластиной рессоры и фундаментом 1подпятника равен 0,7 мм. При нагрузке более 295 кН рессоры ложатся на жесткий фундамент и подпятник работает как
62

Рис. 3.14. Схема подшипника ГЦН атомной электростанции KWO:
1 – радиальный подшипник; 2 – поршень; 3 – опорное кольцо; 4 – колодка; 5 – пята; 6 – опора
неподрессоренный подпятник Митчеля. Пята изготавливается из стали 40ХН с твердостью после закалки КТ60. Толщина диска пяты 100 мм, расчетный прогиб диска на ширине колодок 125 мм под нагрузкой 196 кН составляет 12,5 мкм. Диск пяты после шлифовки притирается по плите первого класса и после окончательной доводки имеет заданную шероховатость поверхности.
Поскольку на вал ГЦН могут действовать значительные выталкивающие силы, осевой подшипник выполнен двухсторонним с соответствующим набором колодок 2, фундамента 5 и комплекта рессор 6 для восприятия нагрузки, направленной вверх. Система смазки пяты — циркуляционная с фильтрацией и охлаждением масла.
Осевой подшипник насоса реактора РБМК выдерживает пуски и остановки при удельном давлении 2,94 МПа и номинальной частот« вращения и работает при удельном давлении до 4,9 МПа. При усилии 519,4 кН максимальная температура в слое баббита равна приблизительно 110° С при температуре масла на входе 50° С, колебания давления в масляном клине составляют 2—3% среднего давления, а неравномерность нагрузки отдельных колодок не превышает 15%, Конструкция радиального подшипника 9 аналогична конструкции подшипников ГЦН реактора БН-350. Радиально-осевая опора успешно эксплуатируется в серийных ГЦН на действующих АЭС.
63
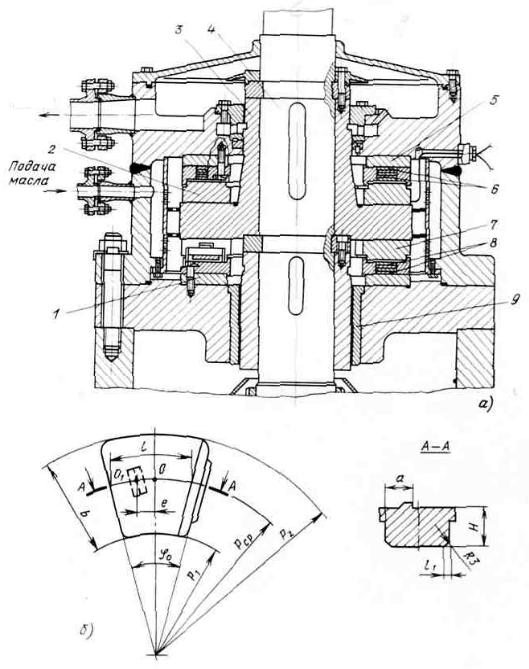
Рис. 3.15. Схема радиально-осевого подшипника насоса реактора РБМК:
а – общий вид; б – основные обозначения колодки; 1,5 – фундамент; 2,7 – колодка верхняя нижняя соответственно; 3 – пята; 4 – вал; 6,8 – пакет рессор верхних и нижних колодок соответственно; 9 – радиальный подшипник
Осевые и радиальные усилия, действующие на вал насоса ГЦН-317, воспринимаются радиально-осевым подшипником, выполненным отдельным узлом (рис. 3.16, а) . Подшипник состоит из корпуса 1 упорного гребня 3, верхнего 4 и нижнего 2 упорных колодок, радиального подшипника 5 и поддона. Упорный гребень, выполненный совместно с шейкой радиального подшипника, установлен на валу на двух цилиндрических поясках и прижимается гай кой в осевом направлении через прокладки 12. Крутящий момент от упорного гребня на вал насоса передается через шлицевое
64
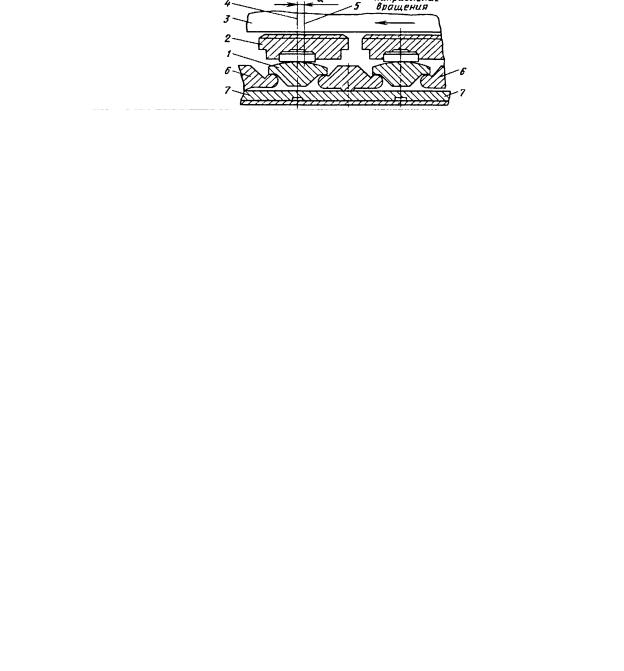
соединение втулки 9 с валом насоса. Осевые усилия, действующие на вал насоса, через упорный гребень передаются на упорные колодки 2,4, которые опираются на рычажную балансирную систему типа Кингсбери, обеспечивающую равномерное распределение нагрузки между колодками (рис. 3.16, 6). Упорные колодки выполнены составными и имеют рабочий слон из баббита Б-83 толщиной 3 мм. Для улучшения образования масляного клина точка опоры колодок имеет смещение от центра колодки в сторону выходной кромки.
Рис. 3.16. ГЦН реактора типа ВВЭР: радиально-осевой подшипник насоса ГЦН-317 (а):
1 – корпус; 2,4 – колодки; 3 – упорный гребень; 5 – радиальный подшипник; 6 – корпус электромагнитного разгрузочного устройства; 7– электрокатушка; 8 – разгрузочный диск; 9 – втулка; 10 – кольцо; 11 – муфта; 12 – прокладка; 13 – кулачок; 14 – храповое кольцо
схема рычажной системы осевого подшипника ГЦН-195 реактора ВВЭР-1000 (б):
1,6 |
– верхний |
и нижний уравновешивающий рычаг соответственно; 2 – колодка; 3 – диск пяты; |
5 – |
радиальный |
подшипник; 4,5– ось симметрии рычага и колодки соответственно; 7– обойма |
65
Рычажная система с колодками и обоймой собрана в упорное кольцо. В корпусе радиально-осевого подшипника установлены два упорных кольца: верхнее, воспринимающее осевые силы, действующее вверх, и нижнее при обратном направлении осевых сил. Радиальное усилие воспринимается радиальным подшипником, представляющим собой упорную цилиндрическую втулку с заливкой баббитом Б-83.
Центровка радиального подшипника осуществляется по узкому кольцевому пояску, который обеспечивает его самоустановку по шейке осевого подшипника. Для предотвращения от перемещения радиальный подшипник закрепляется двумя штифтами. Питание его производится под давлением турбинным маслом, которое дросселируется до атмосферного давления при сливе из полости подшипника. Все масло отводится через единый сливной патрубок. Давление в полости подшипника регулируется дросселем. Конструкция сливного бачка обеспечивает аварийную подпитку маслом упорных колодок при обесточивании.
Для обеспечения запуска электродвигателя насоса при полном давлении в первом контуре, а также для обеспечения работы осевого подшипника на номинальной нагрузке в верхней части радиально-осевого подшипника установлено электромагнитное разгрузочное устройство, создающее на роторе усилие (15—20) · 10 4 Н, направленное вниз. Электромагнитное разгрузочное устройство состоит из разгрузочного диска 8 и корпуса 6 с электрокатушкой 7. Разгрузочный диск установлен на гребне осевого подшипника на двух шпонках и прижимается к гребню через зубчатую втулку муфты 11 кольцом 10. Корпус электромагнита — цельнокованый, изготовлен из магнитной углеродистой стали, установлен на корпус радиально-осевого подшипника и одновременно служит для него крышкой. Имеются подвод и отвод охлаждающей воды холодильника, установленного в корпусе электромагнита. В корпус холодильника укладываются две электрокатушки, последовательно соединенные между собой. Катушки изолированы микалентной и стеклотканью. Электромагнит питается постоянным током. Питание подводится к коробке зажимов, установленной на корпусе электромагнита.
С целью предотвращения обратного вращения вала при остановке (реверсировании) установлено стопорное устройство, представляющее собой храповой механизм.
Оно состоит из храпового кольца 14, установленного на корпусе электромагнита, и двух кулачков 13, свободно вращающихся на осях, закрепленных в цапфах, диаметрально расположенных на разгрузочном диске 8. При прямом вращении вала насоса центробежная сила выводит кулачки из зацепления с храповым кольцом, и происходит свободное вращение вала. При остановке вала кулачки под действием собственной массы входят в зацепление с храповым кольцом и стопорят вал при обратном вращении.
66

В ГЦН реактора ВВЭР-1000 также применен маслосмазываемый осевой подшипник с рычажной уравнительной системой Кингсбери (рис. 3.16, б) . Диск 3 пяты опирается на восемь колодок 2, установленных на верхние уравновешивающие рычаги 1, которые, в свою очередь, двумя заплечиками держатся на заплечиках нижних уравновешивающих рычагов 6. Последние цилиндрическими выступами, расположенными радиально по середине, опираются на плоскость обоймы 7. Таким образом, упорные колодки в комплекте с верхними и нижними рычагами представляют собой замкнутую по кругу рычажную систему. Для образования масляного клина между диском пяты и колодками ось симметрии 5 упоров колодок смещена от оси симметрии 4 рычагов 1 на величину а в сторону вращения. Если некоторые из упорных колодок по каким-либо причинам выйдут из контакта с пятой, то остальные колодки через рычажную систему будут перемещать их до тех пор, пока осевые усилия, действующие на все колодки, не станут одинаковыми. Данная система распределения нагрузки между колодками хотя сложна и трудоемка при изготовлении, но обеспечивает равномерность осевой нагрузки по всем колодкам. Осевой подшипник в насосе реактора ВВЭР-1000 выполнен в одном блоке с двумя радиальными гидродинамическими подшипниками. Рассмотренные конструкционные решения по осевым подшипникам характерны и для зарубежных ГЦН с уплотнением вала.
Порядок расчета осевых ГДП . Подшипники с плоскопараллельными поверхностями скольжения. Опоры с идеально плоскопараллельными поверхностями скольжения не могут работать в режиме жидкостной смазки. Для опор такого типа наиболее характерен режим граничной смазки и реже полужидкостной. Смазка обычно подводится к поверхностям трения подшипника с помощью радиальных канавок, выполняемых на поверхности пяты или подпятника (см. рис. 3.8).
Число канавок выбирают в зависимости от размеров подпятника с учетом равномерного распределения смазки по всей поверхности трения. Для улучшения подачи жидкости к трущимся поверхностям маслоподводящим канавкам придают профиль, который при относительном движении поверхностей трения обеспечивает попадание смазки в зазор между поверхностями.
Для этой цели смазочная канавка должна иметь прямолинейный наклонный участок. В случае движения трущейся поверхности в разных направлениях (при реверсировании) смазочная канавка должна иметь два наклонных участка. Глубина канавки S = 0,5 - 1 мм, угол наклона прямоугольного участка αе = 5 - 15° ( на рисунке не показан).
См. сноску на с . 54
67
В условиях полужидкостной смазки наличие указанных наклонных участков при достаточном количестве жидкой смазки может способствовать образованию гидродинамического клина. В этом случае уклон наклонных участков целесообразно принимать равным 0,007 – 0,01 мм. Осевые подшипники с плоскопараллельными поверхностными скольжения рассчитывают, как правило, по критерию [рmυ], где рm - удельная нагрузка; υ — скорость скольжения.
Удельная нагрузка на кольцевую пяту
|
= |
|
4W |
|
pm |
|
|
, |
|
π (d 2 |
|
|||
|
|
− d02 )χ1 |
где χ1 — коэффициент, учитывающий уменьшение площади опорной поверхности за счет смазочных канавок; в зависимости от числа канавок и их ширины принимают χ1 = 0,8 ÷ 0,9.
Внутренний диаметр d0= (0,6-0,8)d, где d — наружный диаметр. Значение υ определяют по зависимости
|
υ = |
ω(d 3 − d 3 ) |
|
|
||||||
|
3(d 2 − d020 ). |
|
|
|||||||
Необходимо выполнение соотношения |
|
|
|
|
|
|
|
|||
|
4Wω(d 3 − d03 ) |
|
≤ [pmυ]. |
|||||||
|
3π (d 2 − d02 )2 |
χ1 |
|
|||||||
|
|
|
|
|
||||||
Момент трения: |
|
|
|
|
|
|
|
|
|
|
для неприработавшейся пяты |
|
|
|
|
|
|
|
|
|
|
|
M ' = |
W |
|
f |
|
d 3 − d03 |
; |
|
||
|
3χ1 |
1 d 2 − d02 |
|
|||||||
|
тр |
|
|
|
||||||
для приработавшейся пяты |
|
|
|
|
|
|
|
|
|
|
M ' = 0,25 f |
|
W |
(d − d |
|
). |
|||||
|
|
|
||||||||
|
тр |
|
|
1 |
χ1 |
|
|
0 |
|
где f1 – коэффициент трения.
Подшипники с наклонными несущими поверхностями. Обычно рабочие поверхности подпятника состоят из двух участков, из которых одни являются плоскими (без скосов) и служат для восприятия нагрузки в процессе пуска и остановки машины, когда скорость относительного перемещения подвижного элемента (пяты) мала для образования в клиновом зазоре достаточного гидродинамического давления; другие — собственно клиновые участки (см. рис. 3.9).
68

Ширину канавки принимают равной 2—4 мм. Размер d плоского участка выбирают так, чтобы среднее давление неподвижной пяты на плоскопараллельную поверхность подпятника не превышало допускаемого. Тогда
|
d = |
W |
|
|
, |
|
|
(r − r )n[p |
m |
] |
|
||
|
2 1 |
|
|
|
||
где W – |
нагрузка на подпятник; n – число наклонных поверхностей; |
[pm] - допустимая |
||||
нагрузка; r2 – r1 = b ширина наклонного участка. |
|
|
|
|
||
При |
проектировании подпятника обычно задаются следующими |
соотношениями: |
r2/r1 = 1,5 ÷ 2; l/b = 0,5 ÷ 1,6, где l - длина клинового наклонного участка.
Число наклонных поверхностей определяют в зависимости от характера вращения пяты. Для постоянного направления вращения п = пD c / (l +c+a ); для переменного направления вращения п = пD c / (2 l +c+a ), где D c = r 1 +r 2 - средний диаметр подпятника.
Целью расчета при проектировании осевого подшипника с наклонными поверхностями является определение основных характеристик - несущей способности, потерь мощности на трение, количество смазки, необходимой для создания гидродинамического трения. При этом необходимо, чтобы были удовлетворены основные критерии работоспособности, т. е. hmin ≥ hкр и максимальная температура смазки в зазоре нс превышала допустимую. Толщина смазочного слом в клиновом зазоре между наклонной поверхностью и пятой в окружном направлении изменяется линейно.
Получено следующее выражение:
h = h2 – (h 2 - hmin)(χ/l) ,
где h2 – толщина смазочного слоя на входе в клин; h1 – толщина смазочного слоя на выходе из клина; χ – текущая координата; l – ширина клинового наклонного участка.
Введем отношение h2/hmin = βn, которое является важной характеристикой смазочного слоя и называется коэффициентом уклона наклонной поверхности. Обозначим β = D1/D2, тогда средний радиус rc = 0,25D1(1+β), длина b = 0,5D1(β - 1), число наклонных поверхностей
|
0,5πD1 (1 + β ) − |
2W |
|||||||
n = |
D1 (β − 1)[ pm ] |
, |
|||||||
|
|
|
|||||||
|
|
|
|
|
|||||
(0,25 |
÷ 0,8)D1 (β − 1) + l |
||||||||
угловой размер плоскопараллельного участка |
|
|
|
|
|||||
|
Qn = |
|
8W |
|
|
, |
|
||
|
|
|
|
|
|
|
|||
|
nD 2 (β 2 |
− 1)[ p |
|
|
|
||||
|
|
m |
] |
|
|||||
|
|
|
1 |
|
|
|
|
угловой размер канавки
69
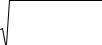
|
= |
4C |
||
Qc |
|
|
, |
|
D1 (1 |
|
|||
|
|
+ β ) |
угловой размер клинового участка для постоянного направления вращения
Qк = 2π / n − Qn − Qc .
Подшипники с самоустанавливающимися колодками. Надежность работы осевого подшипника (подпятника) зависит от воспринимающего осевого усилия, а также от конструкционных особенностей и организации маслосжнабжения. Среди конструктивных факторов, определяющих несущую способность осевого подшипника, важнейшим является устройство колодок (целые, составные, слоеные), вид опоры и ее положение по длине колодки, распределение нагрузки по колодкам, размеры и материал колодки, профилирование ее входной кромки и т. д. Кроме того, конструкция осевого подшипника должна обеспечивать распределение нагрузки на все колодки с учетом возможных отклонений гребня (пяты) во время работы от положения его в состоянии покоя.
Толщина смазочного слоя в месте наибольшего сближения колодки подпятника с плоскостью упорного гребня является одним из основных критериев работоспособности осевых подшипников (подпятников) с самоустанавливающимися колодками. Устойчивая работа осевого подшипника в
режиме жидкостной смазки обеспечивается при условии hmin |
≥ hкр, |
где hкр |
|
рекомендуют выбирать исходя из следующего условия: hкр ≥ fmax |
+ 0,01 мм. где fmax |
||
– наибольший прогиб упорного кольца. |
|
|
|
Вторым критерием, определяющим |
работоспособность |
опоры, |
является |
температура смазки в зазоре, измеренная вблизи рабочей упорной колодки.
На тепловой режим подшипника большое влияние оказывает система входа масла в смазочный зазор, направленная на исключение завихрений масла на входе в клин, местных понижений давления и застойных зон перед колодкой, на улучшение температурного режима всей колодки.
Зависимость между минимальной толщиной смазочной пленки и ее температурой и следовательно, температурой рабочей поверхности колодки учитывают с помощью характеристического числа подпятника
A = hmin |
2W |
|
|
, |
|
|
||
|
μср Dсрω ln SЭ |
которое является аналогом коэффициента несущей способности (Sэ — эффективная площадь опорной поверхности; μср — вязкость смазки при усредненном значении температуры в смазочной пленке).
70