
Свидунович_Материаловедение_для ХТОМ
.pdfКонтактные материалы
Электрические контакты подразделяют на разрывные, скользящие и неподвижные. Основное требование для всех контактов — малое переходное электросопротивление.
Разрывные контакты. Эти контакты предназначены для периодического замыкания и размыкания цепи и работают в наиболее трудных условиях. В процессе работы разрывных контактов возникает искра или электрическая дуга, что вызывает коррозию и электроэрозионный износ.
Обычно материалами для таких контактов служат серебро и сплавы на его основе.
Скользящие контакты. К материалам для скользящих контактов предъявляют те же требования, что и для разрывных, но основное требование к ним — высокое сопротивление свариванию. Кроме окисленного серебряномедного сплава для скользящих контактов применяют композиции из порошков меди или серебра с небольшой добавкой графита, препятствующего свариванию (МГЗ, МГ5, СГЗ, СГ5). Цифра в марках указывает на содержание графита в процентах.
Неподвижные контакты. Эти контакты должны иметь низкое значение переходного электросопротивления, которое, кроме того, должно быть стабильным при небольших контактных усилиях. Поэтому для зажимных контактов выбирают коррозионно-стойкий материал, не образующий оксидных пленок с высоким электросопротивлением на контактной поверхности. Всем этим требованиям удовлетворяют медь, латунь, цинк.
Сплавы с повышенным электросопротивлением
Эти сплавы используют для прецизионных элементов сопротивления (обмоток потенциометров, шунтов, катушек сопротивления, резисторов, термопар, тензометрических датчиков) и нагревательных элементов электрических приборов и печей.
Повышенным электросопротивлением обладают металлические сплавы со структурой твердых растворов. Значения р у таких сплавов (см. рис. 18.5) выше, чем у металлов, их составляющих. Сплавы с высоким электросопротивлением должны иметь малый температурный коэффициент электросопротивления, а также высокую жаростойкость, что особенно важно для нагревательных элементов.
При использовании сплавов в электроизмерительных приборах в паре с медью от них требуется малая термоэлектродвижущая сила (ТЭДС). В большинстве случаев сплавы используют в виде лент или проволоки, а поэтому они должны обладать хорошей пластичностью. Все сплавы с повышенным электросопротивлением в зависимости от рабочей температуры делят на три группы.
Сплавы, рабочая температура которых не выше 500° С, используют для изготовления прецизионных элементов сопротивления. К ним относятся медные сплавы, легированные никелем и марганцем.
Сплавы, рабочая температура которых менее 1200 ° С, используют
также для элементов сопротивления и нагревательных элементов. Это сплавы на основе железа и никеля. Легирование хромом обеспечивает им высокое электросопротивление и жаростойкость.
При температурах выше 1200 ° С (в вакуумных печах) используют сплавы на основе тугоплавких металлов (W, Мо, Та). Для изготовления нагревателей электрических печей (до 1500° С) применяют также керамические материалы, например, силитовые стержни, которые спекают из карбида кремния. Силит является полупроводниковым материалом и имеет высокое электросопротивление. Распространены также нагреватели из дисилицида молибдена (MоSi2).
МАТЕРИАЛЫ ДЛЯ РЕЖУЩИХ И ИЗМЕРИТЕЛЬНЫХ ИНСТРУМЕНТОВ
МАТЕРИАЛЫ ДЛЯ РЕЖУЩИХ ИНСТРУМЕНТОВ
Основные свойства, которыми должен обладать материал для режущих инструментов, — износостойкость и теплостойкость.
Условия работы инструментов зависят от режимов резания и свойств обрабатываемого материала. Чем больше скорость резания, сечение снимаемой стружки, а также прочность и вязкость обрабатываемого материала, тем выше температура нагрева режущей кромки инструментов. При этих условиях работоспособность инструментов определяется высокой «горячей» твердостью и способностью материала сохранять ее при длительном нагреве, т.е. теплостойкостью. От теплостойкости материала, таким образом, зависит производительность резания.
По теплостойкости применяемые материалы подразделяют на следующие группы: углеродистые и низколегированные стали (до 200° С), высоколегированные быстрорежущие стали (до 600 - 640 ° С), твердые сплавы (до 800 - 1000 ° С) и сверхтвердые материалы (до 1200 ° С).
УГЛЕРОДИСТЫЕ СТАЛИ
Из-за низкой прокаливаемости (10 - 12 мм) углеродистые стали пригодны для мелких инструментов или инструментов с поперечным сечением до 25 мм с незакаленной сердцевиной, в которой режущая часть приходится на поверхностный слой1 (метчики, развертки, напильники и т.п.). Несквозная закалка уменьшает деформацию инструментов и повышает благодаря вязкой сердцевине их устойчивость к ударам и вибрациям. Инструмент с поперечным сечением 15-25 мм после закалки охлаждают в воде или водных растворах солей и щелочей. Инструменты с незакаленной сердцевиной меньшего сечения для уменьшения деформаций и опасности растрескивания охлаждают в масле, водных растворах полимеров или расплавах солей.
Режущие инструменты (мелкие метчики, сверла, напильники, пилы, шаберы и др.) изготовляют из заэвтектоидных сталей У10, У11, У12 и У13. Их подвергают неполной закалке и низкому отпуску при 150 — 180 ° С на
структуру мартенсита с включениями цементита. Такие инструменты обладают повышенной износостойкостью и высокой твердостью (62 - 64 HRС) на рабочих гранях. Однако твердость сильно снижается при нагреве свыше 200 ° С. В связи с этим инструменты из этих сталей пригодны для обработки при небольших скоростях резания.
Заэвтектоидные стали используют также для изготовления измерительных инструментов (калибры простой формы и невысоких классов точности) и небольших штампов холодной высадки и вытяжки, работающих при невысоких нагрузках.
Стали У7, У8, У9, обеспечивающие более высокую вязкость, применяют для инструментов, подвергающихся ударам: деревообрабатывающих, слесарных, кузнечных, а также пуансонов, матриц и др. После полной закалки их отпускают на структуру троостита при 275 — 325 ° С (48 - 55 HRС) или при 400 - 450 ° С (38 - 45 HRС).
НИЗКОЛЕГИРОВАННЫЕ СТАЛИ
Эти стали содержат до 5 % легирующих элементов (табл. 19.1), которые вводят для увеличения закаливаемости, прокаливаемости, уменьшения деформаций и опасности растрескивания инструментов^ Хром -постоянный элемент низколегированных сталей. Для улучшения свой:т; в них дополнительно вводят марганец, кремний, вольфрам. Марганец(1 - 2%) обеспечивает минимальное изменение размеров инструментов при закалке. Интенсивно снижая интервал температур мартенситного превращения, он способствует сохранению в структуре повышенного количества остаточного аустенита (15 - 20 %), который частично или полностью компенсирует увеличение объема в результате образования мартенсита. Кремний (1 — 1,5 %) несколько повышает сопротивление отпуску и способствует образованию легко отделяющейся окалины. Вольфрам (1 -5 %) повышает износостойкость.
По структуре низколегированные стали относятся к заэвтектоидным сталям перлитного класса. Их подвергают неполной закалке от температуры несколько выше точки А1 и низкому отпуску. Структура мартенсита и избыточных карбидов (легированный цементит) обеспечивает им твердость (62 - 69 HRС) и высокую износостойкость. Однако из-за низкой теплостойкости низколегированные стали имеют практически одинаковые с углеродистыми сталями эксплуатационные свойства. Их применяют для инструментов, работающих при небольших скоростях резания, не вызывающих нагрева свыше 200 - 260 ° С. В отличие от углеродистых эти стали меньше склонны к перегреву и позволяют изготовлять инструменты больших размеров и более сложной формы.
Сталь ХВ4 отличается особо высокой твердостью и износостойкостью благодаря тому, что в ней кроме легированного цементита присутствует карбид вольфрама типа Ме6С, который практически не растворяется при температуре закалки. Из-за высокой твердости (67 - 69 HRС) эту сталь называют алмазной и применяют для чистовой обработки твердых материалов.
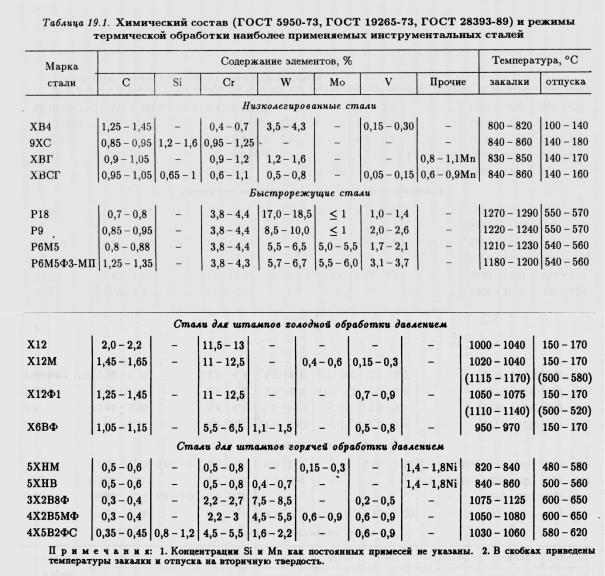
Стали X, 9ХС, ХВГ, ХВСГ относят к сталям с глубокой прокаливаемостью. Сталь 9ХС в отличие от X (1,5% Сг) имеет более высокую устойчивость к разупрочнению при отпуске (до 260° С), повышенные эксплуатационные свойства; ее применяют для изготовления фрез, сверл, резьбонарезных и других инструментов с поперечным сечением до 35 мм. Недостаток стали 9ХС — склонность к обезуглероживанию. Сталь ХВГ характеризуется малой деформацией при закалке. Применяют ее в основном для длинных стержневых инструментов (сверла, развертки, протяжки и т.п.) с поперечным сечением до 45 мм. Сложнолегированная сталь ХВСГ сочетает в себе лучшие свойства сталей 9ХС и ХВГ; из нее изготовляют инструменты большого поперечного сечения (до 100 мм).
БЫСТРОРЕЖУЩИЕ СТАЛИ
К этой группе относятся высоколегированные стали, предназначенные для изготовления инструментов высокой производительности. Основное свойство этих сталей — высокая теплостойкость, которая обеспечивается введением большого количества вольфрама совместно с другими карбидообразующими элементами — молибденом, хромом, ванадием.
Вольфрам и молибден в присутствии хрома связывают углерод в специальный труднокоагулируемый при отпуске карбид типа Ме6С и задерживают распад мартенсита. Выделение дисперсных карбидов, которое происходит при повышенных температурах отпуска (500 — 600 ° С), вызывает дисперсионное твердение мартенсита — явление вторичной твердости. Особенно эффективно вторичная твердость и теплостойкость повышаются при введении нескольких сильных карбидообразователей, например вольфрама (одного или совместно с молибденом) и ванадия. При отпуске ванадий, выделяясь в виде карбидов, усиливает дисперсионное твердение, а вольфрам (молибден), сохраняясь в мартенсите, задерживает его распад.
Увеличению теплостойкости способствует также кобальт. Он не образует карбидов, но, повышая энергию межатомных сил связи, затрудняет коагуляцию карбидов и увеличивает их дисперсность.
В результате комплексного легирования инструменты из быстрорежущих сталей сохраняют высокую твердость до 560 — 640 ° С и допускают в 2 - 4 раза более производительные режимы резания, чем инструменты из углеродистых и низколегированных сталей.
Быстрорежущие стали (см. табл. 19.1) обозначают буквой Р, после которой стоит число, указывающее содержание (в процентах) вольфрама — основного легирующего элемента (ГОСТ 19265-73). Содержание ванадия (до 2 %) и хрома (~ 4 % во всех сталях) в марке не указывается. Стали, легированные дополнительно молибденом, кобальтом или имеющие повышенное количество ванадия, содержат в марке соответственно буквы М, К, Ф и числа, показывающие их содержание в процентах (например, Р6М5, Р10К5Ф5). ГОСТ 19265-73 предусматривает 14 марок быстрорежущих сталей, которые по эксплуатационным свойствам делятся на две группы: нормальной и повышенной производительности.
Группу сталей нормальной производительности образуют вольфрамовые (Р18, Р12, Р9, Р9Ф5) и вольфрамомолибденовые (Р6МЗ, Р6М5) стали, сохраняющие твердость не ниже 58 HRС до 620 ° С. При одинаковой теплостойкости эти стали отличаются главным образом механическими и технологическими свойствами. Лучшей обрабатываемостью давлением и
шлифуемостью, а также прочностью и вязкостью обладают стали Р6МЗ и Р6М5. Стали Р9, Р9Ф5 плохо шлифуются из-за присутствия твердых карбидов ванадия.
К группе сталей повышенной производительности относятся стали, содержащие кобальт и повышенное количество ванадия (Р6М5К5, Р9М4К8, Р9К5, Р9К10, Р10К5Ф5, Р18К5Ф2). Они превосходят стали первой группы по теплостойкости (630 — 640 ° С), твердости (≥ 64 HRС) и износостойкости, но уступают им по прочности и пластичности. Стали повышенной производительности предназначены для обработки высокопрочных сталей, коррозионно-стойких и жаропрочных сталей с аустенит-ной структурой и других труднообрабатываемых материалов.
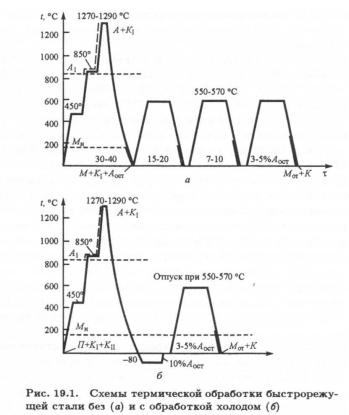
Быстрорежущие стали, особенно второй группы, отличаются высокой стоимостью. Для уменьшения расхода дорогих и дефицитных элементов, особенно вольфрама, преимущественно используют экономно-легированные стали. Из них наиболее широкое применение имеет сталь Р6М5. Разрабатываются безвольфрамовые быстрорежущие стали.
Особенности термической обработки, структуры и свойств быстрорежущих сталей представлены на примере сталей Р18 и Р6М5.
По структуре после отжига быстрорежущие стали относятся к ледебуритному классу. В литом виде они имеют ледебуритную эвтектику, которую устраняют горячей деформацией путем измельчения первичных карбидов.
Ковка стали — ответственная операция. При недостаточной проковке возникает карбидная ликвация — местное скопление карбидов в виде участков неразрушенной эвтектики. Карбидная ликвация снижает стойкость инструмента и увеличивает его хрупкость. Деформированную сталь для снижения твердости (до 207 - 255 НВ) подвергают изотермическому отжигу. Структура отожженных сталей состоит из сорбито-образного перлита, вторичных и более крупных первичных карбидов. Общее количество карбидов в стали Р18 составляет примерно 28 %, в стали Р6М5 — 22 %.
Основным карбидом стали Р18 является сложный карбид вольфрама переменного состава FезWзС (Ме6С), который растворяет в себе часть ванадия и хрома. В остальных сталях кроме Ме6С и небольшого количества карбида (Fе, Сг)2зС6, присутствует карбид VС (МеС).
В карбидах содержится 80 - 95 % (W + V) и 50 % Сг. Остальная часть легирующих элементов растворена в феррите.
Высокие эксплуатационные свойства инструменты из быстрорежущих
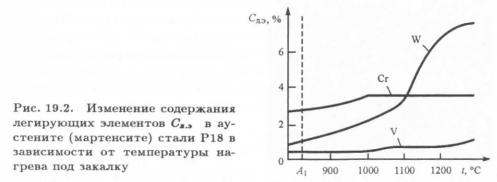
сталей приобретают после закалки и трехкратного отпуска (рис. 19.1). Из-за низкой теплопроводности быстрорежущие стали при закалке нагревают медленно с прогревами при 450 и 850 ° С, применяя соляные ванны для уменьшения окисления и обезуглероживания. Особенность
закалки быстрорежущих сталей — высокая температура нагрева (см. табл. 19.1). Она необходима для обеспечения теплостойкости — получения после закалки высоколегированного мартенсита в результате перехода в раствор максимального количества специальных карбидов.
Степень легирования аустенита (мартенсита) увеличивается с повышением температуры нагрева (рис. 19.2). При 1300 ° С достигается предельное насыщение аустенита — в нем растворяются весь хром, ~ 8 % W, 1
% V и 0,4 - 0,5 % С.
Легирование аустенита происходит при растворении вторичных карбидов. Первичные карбиды не растворяются и тормозят рост зерна аустенита, поэтому при нагреве, близком к температуре плавления, в быстрорежущих сталях сохраняется мелкое зерно.
Быстрорежущие стали по структуре после нормализации относятся к мартенситному классу. От температуры закалки мелкие инструменты охлаждают на воздухе, крупные — в масле1. Сложные по форме инструменты для уменьшения деформаций подвергают ступенчатой закалке с выдержкой в горячих средах при 500 - 550 ° С.
После закалки не достигается максимальная твердость сталей (60 -65 HRС), так как в структуре кроме мартенсита и первичных карбидов содержится 30 - 40 % остаточного аустенита, присутствие которого вызвано снижением температуры точки Мk ниже 0° С. Остаточный аустенит превращают в мартенсит при отпуске или обработке холодом. Отпуск проводят при 550 — 570 ° С. В процессе выдержки при отпуске из мартенсита и остаточного аустенита выделяются дисперсные карбиды Ме6С. Аустенит, обедняясь углеродом и легирующими элементами, становится менее устойчивым и при охлаждении ниже точки МH испытывает мартенситное превращение (на рис. 19.1 температурный интервал превращения показан жирной линией). Однократного отпуска недостаточно для превращения всего остаточного аустенита. Применяют двух-, трехкратный отпуск с выдержкой по 1 ч и охлаждением на воздухе. При этом количество аустенита снижается до 3 - 5 %. Применение обработки холодом после закалки сокращает цикл термической обработки (см. рис. 19.1, б). В термически обработанном
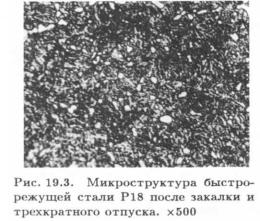
состоянии быстрорежущие стали имеют структуру, состоящую из мартенсита отпуска и карбидов (рис. 19.3), и твердость 63 - 65 HRС.
Режущие свойства некоторых видов инструментов (фасонные резцы, сверла, фрезы, протяжки и др.) дополнительно улучшают созданием
на неперетачиваемых поверхностях тонкого слоя (10 - 50 мкм) нитридов или карбонитридов. Такой слой характеризуется высокой твердостьо (≥ 1000 НV) и износостойкостью. Его получают газовым или ионным азотированием, которое проводят непродолжительное время (20 -30 мин) при температуре, не превышающей температуру отпуска (470 - 550 ° С). Используют также и другие способы: низкотемпературное цианирование, карбонитрацию, напыление нитридов титана.
Для структуры деформированных быстрорежущих сталей характерна, карбидная неоднородность. Скопление карбидов и их полосчатость отрицательно влияют на эксплуатационную стойкость инструментов, способствуют выкрашиванию рабочих кромок. Эффективный способ устранения такого структурного дефекта — изготовление быстрорежущих сталей порошковой технологией.
Порошковые быстрорежущие стали (ГОСТ 28393-89) получают распылением жидкой быстрорежущей стали в азоте и последующим горячим компактированием. Металл приобретает высокую плотность и отличается равномерным распределением дисперсных (1 мкм и менее) частиц карбидов. Эффект измельчения карбидов настолько значителен, что перекрывает нежелательную загрязненность порошковых сталей кислородными включениями.
Повышение структурной однородности сопровождается улучшением шлифуемости, ударной вязкости, прочности при изгибе. Порошковые быстрорежущие стали (Р6М5ФЗ-МП, Р7М2Ф6-МП, Р12МФ5-МП, Р12МЗК5Ф2-МП и др.) имеют повышенное количество углерода (1,20 - 1,75%) и ванадия (2,3 - 3,7%). Благодаря этому они содержат больше высокотвердых дисперсных карбидов типа МеС и, как следствие, имеют высокую вторичную твердость (65 - 67 HRС) и износостойкость (стойкость инструментов возрастает не менее чем в 1,5 раза).
Высокованадиевую сталь Р7М2Ф6-МП изготавливают только порошковой технологией. По стойкости она превосходит кобальтсодержащие стали
(Р9М4К8, Р13Ф4К5 и др.), полученные традиционной технологией. Инструмент из порошковых быстрорежущих сталей также подвергают
закалке и трехкратному отпуску. Отличие состоит в том, что его закаливают с температуры, которая на 20 — 30 ° С ниже температуры закалки инструмента из соответствующих сталей, полученных традиционным способом производства. Обусловлено это тем, что процессы растворения дисперсных карбидов идут интенсивнее и насыщение аустенита углеродом и легирующими элементами наступает при более низкой температуре.
ПОРОШКОВЫЕ ТВЕРДЫЕ СПЛАВЫ
К порошковым твердым сплавам относятся материалы, состоящие из высокотвердых и тугоплавких карбидов вольфрама, титана, тантала, соединенных металлической связкой.
Твердые сплавы изготовляют порошковой технологией. Порошки карбидов смешивают с порошком кобальта, выполняющего роль связки, прессуют и спекают при 14001550 ° С. При спекании кобальт растворяет часть карбидов и плавится. В результате получается плотный материал1, структура которого на 80 - 95 % состоит из карбидных частиц, соединенных связкой. Увеличение содержания связки вызывает снижение твердости, но повышение прочности и вязкости. Твердые сплавы производят в виде пластин, которыми оснащают резцы, сверла, фрезы и другие режущие инструменты. Такие инструменты сочетают высокую твердость 85 - 92 НRА (74-76 HRС) и износостойкость с высокой теплостойкостью (800 - 1000 ° С). По своим эксплуатационным свойствам они превосходят инструменты из быстрорежущих сталей и применяются для резания с высокими скоростями.
Твердые сплавы характеризуются также высоким модулем упругости (до 6,8 • 10 5 МПа) и пределом прочности на сжатие (до 6000 МПа), их недостатки — сложность изготовления фасонных изделий и высокая хрупкость.
В зависимости от состава карбидной основы порошковые твердые сплавы выпускают трех групп.
Первую (вольфрамовую) группу составляют сплавы системы WС-Со. Их маркируют буквами ВК и числом, показывающим содержание кобальта в процентах (табл. 19.2). Карбидная фаза сплавов этой группы состоит из зерен WС. При одинаковом содержании кобальта они в отличие от сплавов двух других групп характеризуются наибольшей прочностью, но более низкой твердостью. Сплавы вольфрамовой группы теплостойки до 800 ° С.
Сплавы ВКЗ-ВК8 применяют для режущих инструментов при обработке материалов, дающих прерывистую стружку (чугуны, цветные металлы, фарфор, керамика и т.п.).
Сплавы ВК10 и ВК15, обладающие из-за повышенного содержания кобальта более высокой вязкостью, используют для волочильных и буровых инструментов, стойкость которых в десятки раз превышает стойкость стальных инструментов. Сплавы с высоким содержанием кобальта (ВК20 и ВК25) применяют для изготовления штамповых инструментов, а также в
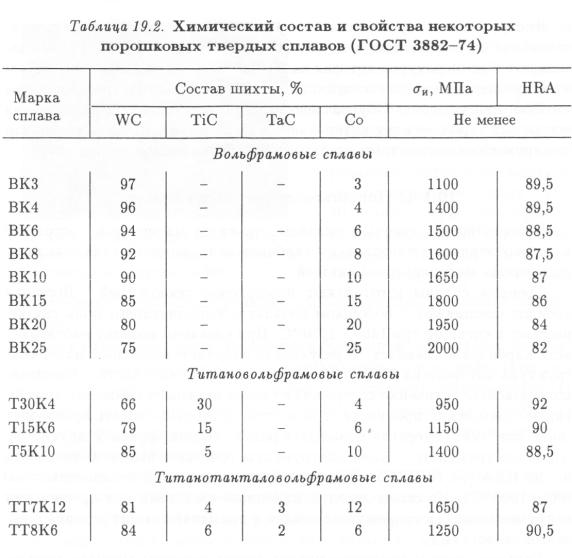
качестве конструкционного материала для деталей машин и приборов, от которых требуется высокое сопротивление пластической деформации или изнашиванию.
Вторую (титановольфрамовую) группу образуют сплавы системы ТiС- WС-Со. Их маркируют буквами Т и К, а также числами, показывающими процентное содержание карбидов титана и кобальта. При температуре спекания карбид титана растворяет до 70 % WС и образует твердый раствор (Тi,W) С, обладающий более высокой твердостью, чем WС. Структура карбидной основы зависит от соотношения карбидов в шихте. В сплаве Т30К4 образуется одна карбидная фаза — твердый раствор (Тi,W) С, который придает ему наиболее высокие режущие свойства, но понижает прочность. В остальных сплавах этой группы количество WС превышает его предельную растворимость в ТiC, поэтому карбиды вольфрама присутствуют в виде избыточных кристаллов.
Сплавы второй группы характеризуются более высокой, чем у сплавов первой группы, теплостойкостью (900 — 1000° С), которая повышается по мере увеличения количества 11 С. Их наиболее широко применяют для