
ГОСЫ / shpory_gos (1) / ОПП
.pdf
Многопредметная (многономенклатурная) поточная линия ¾ это такая линия, на которой одновременно или последовательно изготавливаются предметы различных типоразмеров (наименований), сходных по конструкции или технологии обработки и сборки. Применяются многопредметные линии в серийном производстве, когда количество выпускаемых предметов одного типоразмера за соответствующий период времени недостаточно для полной загрузки оборудования и рабочих.
С точки зрения вида чередования предметов различают линии с партионно-последовательным
(переменно-поточные линии), партионно-групповым (партионно-групповые линии), и комплектногрупповым (комплектно-групповые линии) чередованием.
Переменно-поточной линией называется такая многопредметная линия, на которой предметы производства (поковки, детали, изделия) обрабатываются последовательно партиями по своему стандарт-плану.
Групповые линии основываются на групповых методах обработки деталей. Каждый станок выполняет определенные закрепленные за ним деталеоперации. Групповые линии могут работать с переналадками и без переналадок оборудования.
Групповая линия, на которой на разных операциях одновременно обрабатывается набор различных партий предметов, т.е. партии различных предметов чередуются параллельно, называется
партионно-групповой линией.
Групповая линия, на которой на разных операциях одновременно обрабатывается комплект различных предметов, является комплектно-групповой.
С точки зрения степени непрерывности производственного процесса различают непрерывно- и
прерывно-поточные линии.
Непрерывной называется такая поточная линия, на которой каждый предмет или транспортная партия предметов одного наименования проходит обработку или сборку по всем операциям непрерывно, независимо от других. Движение предметов осуществляется по параллельному виду.
Для прерывно-поточной линии характерным является то, что движение предметов по некоторым операциям происходит прерывно.
По характеру движения и транспортировки предмета различают поточные линии с принудительным (механизированным), полусвободным (немеханизированным), свободным движением.
К поточным линиям с принудительным движением относятся линии, на которых передача предметов с операции на операцию осуществляется при помощи конвейера. Принудительное движение применяется только на непрерывно-поточных линиях.
Для поточных линий со свободным движением характерным является то, что передача отдельных предметов может производиться с незначительными отклонениями от установленного ритма работы линии.
Расчет основных параметров поточных линий
Выбор организационных форм поточных линий определяется тактом работы линии, степенью синхронизации операций технологического процесса, уровней загрузки рабочих мест на линии.
Под тактом поточной линии понимается календарный период времени между запуском (выпуском) на линию данного объекта (деталь, сборочная единица, изделие) и следующего за ним. Такт является функцией заданной программы выпуска, существенно влияет на выбор технологического процесса, оборудования, оснастки, транспортных средств. В общем виде величина такта определяется:
r = Fд / Nз
где Fд – действительный фонд времени за плановый период (смена, сутки, месяц);
Nз – количество запускаемых на поточную линию объектов производства за тот же период.
В тех случаях, когда передача с операции на операцию осуществляется транспортными партиями (небольшие детали, малая величина такта, измеряемая секундами), рассчитывается ритм поточной
линии:
rр = r nтр,
где nтр – величина транспортной (передаточной) партии.
Чтобы обеспечить единый такт или ритм поточной линии, при организации поточного производства осуществляется синхронизация, т. е. производительность выравнивается по всем операциям технологического процесса.
Полная синхронизация операций обеспечивается при достижении равенства

t1 / c1 = t2 / c2 = t3 / c3 = … = t m/ cm = rпл
где t1, t2, t3, tm – норма времени по операциям, мин.; с1, с2, с3, сm – число рабочих мест на операции, шт.; rпл – такт поточной линии, мин.
На следующем этапе определяем необходимое число рабочих мест (единиц оборудования) для каждой операции:
сi расч = ti / rпл
где ti – норма времени на i-ю операцию.
Коэффициент загрузки рабочих мест на каждой операции, %,
Средний коэффициент загрузки рабочих мест на поточной линии, %,
Планировка поточных линий должна обеспечивать прямоточность и наиболее короткий путь движения изделия, рациональное использование производственных площадей, удобство транспортировки заготовок и деталей к рабочим местам, к местам обслуживания и выполнения ремонтов.
Длина деления, или шаг конвейера, выбирается из соотношения
lшmin< lш<lшmin. lшmin определяется габаритами объекта и средним расстоянием между двумя рядом находящимися на конвейере объектами (lср= 200 – 300 мм), а 1ш max определяется допустимой скоростью движения конвейера.
Скорость движения конвейера должна соответствовать такту потока. Это соответствие достигается, если путь, равный шагу, конвейер проходит за такт:
vk = lш / r .
Чаще всего применяют распределительные конвейеры со скоростями в пределах 0,5 + 2 м/мин. Период распределительного конвейера П – это комплект знаков, предназначенных для его разметки.
Длина рабочей части конвейера:
wpi и wki – количество рабочих мест, где выполняются производственные и контрольные операции; и – число всех операций в технологическом процессе.
Длина рабочей линии конвейера lр к согласовывается с его периодом.
Организация инструментального хозяйства
Основные задачи инструментального хозяйства ¾ определить потребности предприятия в технологической оснастке, запланировать ее приобретение или изготовление и обеспечить ею производство, организовать рациональную эксплуатацию оснастки, обеспечить оснасткой рабочие места, организовать ее учет и хранение.
К общезаводским органам инструментального хозяйства относятся инструментальные цехи, мастерские восстановления оснастки, центральный склад инструментального хозяйства (ЦИС), инструментальный отдел. ЦИС осуществляет приемку всей оснастки, организует хранение, учет запаса и движения оснастки, выдает ее цеховым инструментально-раздаточным кладовым (ИРК). Инструментальный отдел выполняет планово-диспетчерские функции по обеспечению предприятия оснасткой, производству ее в инструментальных цехах, а так же осуществляет технический надзор за эксплуатацией оснастки и контроль ее состояния. На крупном машиностроительном предприятии организационная структура инструментального хозяйства может состоять из следующих элементов (в составе инструментального отдела):
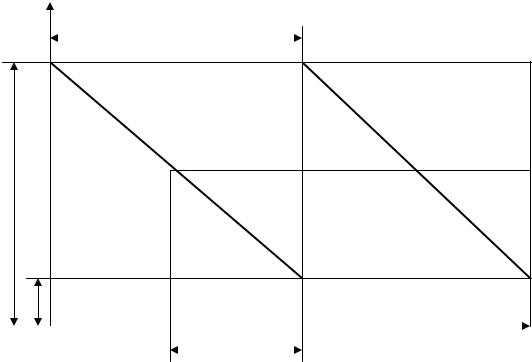
-заместитель начальника отдела по производству оснастки;
-заместитель начальника отдела по эксплуатации оснастки;
-технический сектор;
-планово-экономический сектор;
-инструментальные цехи;
-бухгалтерия отдела.
Кцеховым органам инструментального хозяйства относятся инструментально-раздаточные кладовые и мастерские по заточке и текущему ремонту оснастки.
Наиболее точен расчет расхода оснастки по нормам расхода. Под нормой расхода оснастки понимается ее количество, изнашиваемое при выполнении определенного объема работ.
Запас оснастки в ИРК Zк является суммой двух слагаемых: переходящего Z пер и страхового, или |
||
резервного, запаса |
Z ст.з . |
Страховой запас представляет собой резерв, создаваемый на случай |
нарушения сроков и объемов поставок оснастки. Его величина может быть определена в виде |
||
произведения среднедневного потребления оснастки на число дней возможного запоздания очередной |
||
поставки. |
|
|
Основная часть запасов хранится в ЦИСе. Устанавливается три уровня запасов: максимальный |
||
Z max , минимальный Z min и точки заказа Z т.з , т.е. предельного значения запаса, при котором необходимо |
||
осуществить заказ на его пополнение. Максимальный уровень запаса в ЦИСе устанавливается |
||
первоначально при фиксированной периодичности пополнения запаса. |
||
Например, страховой запас режущего инструмента на центральном складе установлен в размере |
||
двухдневного расхода инструмента за период выполнения заказа. Периодичность поставки инструмента |
||
из ЦИС (период между моментом выдачи заказа и поступлением инструмента на склад) Tо = 10 дней. |
||
Среднедневной расход инструмента за период исполнения заказа Q р = 35 штук. Цикл выполнения |
||
заказа цеха инструментальным складом (время между двумя поступлениями партий инструмента) |
||
Tц = 20 дней. |
|
|
Тогда минимальная норма запаса режущего инструмента на ЦИС составит: |
||
Z min = Z стр = 2 × Q р = 2 × 35 = 70 шт. |
||
Норму запаса режущего инструмента на ЦИС, соответствующую точке заказа, определим по |
||
формуле: |
|
|
Z т.з = Z min + Tо × Q р = 70 + 10 × 35 = 420 шт. |
||
Максимальная норма запаса определяется по формуле: |
||
Z max = Z min + Tц × Q р = 70 + 20 × 35 = 770 шт. |
||
График изменения запаса режущего инструмента на ЦИС по системе «максимум-минимум». |
||
|
Z ц |
= 20 |
Z |
|
|
|
|
Z max = 770 |
|
|
Z т.з = 420 |
|
Z min |
= 70 |
|
|
То = 10 |

Организация ремонтного хозяйства
Для бесперебойной работы оборудования с заданными точностными характеристиками требуется систематическое техническое обслуживание его и выполнение ремонтных работ и мероприятий по технической диагностике.
Организационная и производственная структура ремонтных служб зависит от ряда факторов ¾ типа и объемов производства, его технологических характеристик, развития кооперирования при выполнении ремонтных работ и др. В состав ремонтного хозяйства крупного машиностроительного предприятия входят ремонтно-строительный цех, выполняющий ремонт зданий и сооружений, подчиненный отделу или управлению капитального строительства; электроремонтный цех (или мастерская), выполняющий ремонт электрооборудования и подчиненный главному энергетику; ремонтно-механический цех, выполняющий ремонт технологического и других видов оборудования, изготовление сменных частей и находящийся в подчинении главного механика.
На ремонтную службу предприятия возложены: паспортизация и аттестация оборудования, разработка технологических процессов ремонта и их оснащения, планирование и выполнение работ по техническому обслуживанию и ремонту оборудования, модернизация оборудования, совершенствование организации труда работающих, занятых в этой службе.
Системой ППР оборудования называется совокупность запланированных организационных и технических мероприятий по уходу, надзору за оборудованием, его обслуживанию и ремонту. Основная цель этих мероприятий ¾ предотвращать прогрессивно нарастающий износ, предупреждать аварии и поддерживать оборудование в состоянии постоянной готовности к работе. Система ППР включает техническое обслуживание и плановые ремонты ¾ текущий и капитальный.
Техническое обслуживание ¾ это комплекс операций по поддержанию работоспособности оборудования при использовании его по назначению, при хранении и транспортировании. В процессе технического обслуживания периодически повторяющиеся операции ¾ осмотры, промывки, проверки на точность и др. ¾ регламентированы, выполняются по заранее разработанному графику.
Текущий ремонт производится в процессе эксплуатации оборудования. При этом виде ремонта заменяются и восстанавливаются отдельные части (детали, узлы) оборудования и выполняется регулировка его механизмов.
Капитальный ремонт осуществляют для восстановления полного или близкого к полному ресурса. Обычно он сопровождается модернизацией оборудования.
Ремонты, вызываемые отказами и авариями оборудования, называются неплановыми (аварийными).
Под ремонтным циклом понимается период времени от момента ввода оборудования в эксплуатацию до первого капитального ремонта или между двумя последовательно выполняемыми капитальными ремонтами К.
Структура ремонтного цикла устанавливает перечень ремонтов, расположенных в последовательности их выполнения. Например, К ¾ Т ¾ Т ¾ С ¾ Т ¾ Т ¾ К.
Структура цикла технического обслуживания может включать , например, сменный осмотр, четыре пополнения смазки, одну замену смазки, один частичный осмотр и две профилактические регулировки.
Ремонтный цикл измеряется оперативным временем работы оборудования (время простоя в ремонте в цикл не включается). Определяется он расчетным способом, по эмпирическим зависимостям от ряда факторов. Например, ремонтный цикл для металлорежущих станков
Tц. р =16800 × βо.м × βп.и × βт.о × βв × βд × βк.м ,
где 16800 ¾ нормативный ремонтный цикл, ч; βо. м , βп.и , βт.о , βв , βд , βк.м ¾ коэффициенты, учитывающие вид обрабатываемого материала,
применяемого инструмента, класс точности оборудования, возраст, долговечность, категорию массы. Оборудование категорируется по массе: до 10 т, свыше 10 т до 100 т и свыше 100 т.
Межремонтный период Tм. р и периодичность технического обслуживания Тт.о рассчитываются по формуле:
Тм. р = Тм.ц /(d т +1) ,
Тт.о = Т м.ц /(d т + d т.о +1) ,
где d т , d т.о ¾ число текущих ремонтов и технических обслуживаний.

Трудоемкость и материалоемкость ремонта и технического обслуживания оборудования зависят от его конструкционных особенностей. По этому признаку все оборудование распределено на категории сложности. Трудоемкость ремонтных работ определяется через трудоемкость единицы сложности ремонта.
Суммарная трудоемкость ремонтных работ в плановом периоде может быть определена по формуле:
d к |
d т |
d т.о |
tр. р = ∑Ri ´tр.к |
+ ∑Ri |
´ tр.т + ∑Ri ´tт.о , |
i =1 |
i =1 |
i =1 |
где d к , d т , d т.о |
¾ число капитальных, текущих ремонтов и технических обслуживаний в |
|
плановом периоде; Ri |
¾ категория сложности ремонта I-го оборудования; t р.к , t р.т , tт.о ¾ нормы |
трудоемкости капитального и теку щих ремонтов, технического обслуживания на одну ремонтную единицу, нормо-ч.
Организация материально-технического снабжения предприятия
Службу материально-техниче ского снабжения возглавляет отдел МТС (ОМТС). Задача ОМТС - бесперебойное материальное обесп ечение производства в соответствии с планом выпуска продукции. Структура ОМТС показана на рис.
Основные функции ОМТС:
-разработка нормативов запасов мат ериальных ресурсов;
-планирование потребности в мате риальных ресурсах и в увязка ее с планом производства и нормативами запасов;
-поиск поставщиков, оценка вариан тов поставок и выбор поставщиков по критериям качества поставляемых материалов, надежно сти поставщиков, цен, условий платежей и поставок, транспортнозаготовительных расходов и т.д.;
-заключение договоров на поставки ;
-организация работ по доставке мат ериальных ресурсов, контроль и операти вное регулирование выполнения договоров поставок;
-организация приемки, обработки и хранения материальных ресурсов;
-оперативное планирование и регул ирование обеспечения производства материальными ресурсами;
-учет, контроль и анализ расходова ния материальных ресурсов;
-надзор за рациональным использованием материалов в производстве.
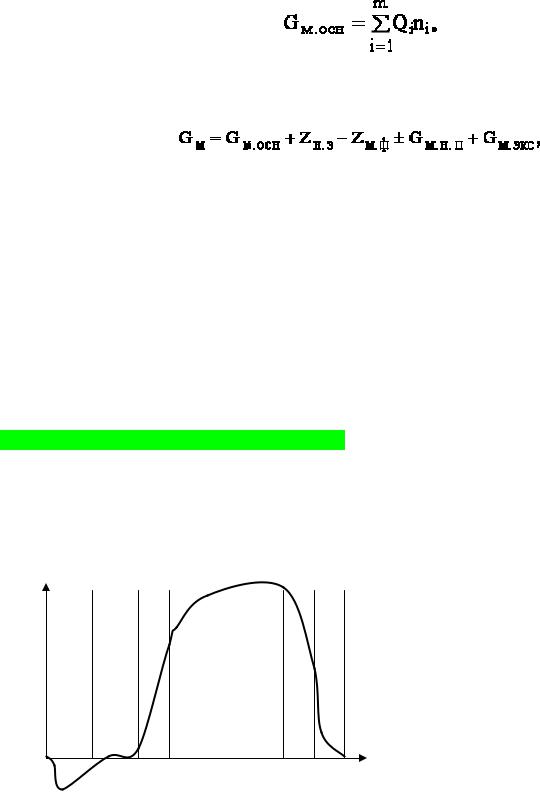
Планирование МТС. План материально-технического снабжения - это совокупность расчетных документов, в которых обоснована п отребность предприятия в материальных ресурсах и определены источники их покрытия. Он сопоставляется в форме баланса МТС.
План МТС разрабатывается с учетомм:
-производственной программы;
-нормативов запасов материальных ресурсов;
-норм расходов сырья, материалов, полуфабрикатов, топлива, комплектующиих изделий;
-планов капитального строительства, реконструкции, подготовки производствва новых изделий, работ по ремонту и эксплуатации оборудования, зданий, сооружений, бытовых объектов и т.д.;
-остатков материальных ресурсов на начало и конец планируемого периода;
-установленных и вновь налаживаемых связей с поставщиками;
-цен на все виды материально-технических ресурсов.
Потребность в материалах на основнное производство (Gм.осн) определяется по формуле
где Qi - объем выпуска продукции по каждому наименованию (шт.);
ni - норма расхода материала на одно изделие с учетом технологических потерь (натур. ед.); m - количество наименований изделий.
Общая потребность в конкретных материалах (Gм) определяется по формуле
где Zн.з - норма запаса материала;
Zм.ф - фактическое наличие материалов на предприятии;
Gм.н.п - необходимое количество материалов для изменения незавершенного производства; Gм.экс - потребность в материалах для ремонтно-эксплуатационных и других нужд. Потребность в материальных ресурсах определяется расходами на:
-основное производство, включая производство комплектующих изделий и запасных частей;
-изготовление технологической осннастки и инструмента;
-изготовление нестандартного обор удования и модернизация оборудования;
-проведение НИР и ОКР (с учетом изготовления опытных образцов и экспериментальных работ);
-реконструкцию цехов, участков;
-ремонтно-эксплуатационные нужды;
-капитальное строительство;
-работы социально-культурной и бытовой сфер;
-создание запасов.
Организация освоения выпуска новой продукции
Главный признак большинства видов продукции состоит в том, что они имеют ограниченный период спроса. Любой продукт проходит в своем развитии различные стадии. Период времени между моментом возникновения и прекращения использования продукта принято называть его жизненным циклом. Фазы жизненного цикла являются общими и включают: создание, освоение, рост, зрелость старение.
1 |
2 |
3 |
4 |
5 |
6 |
Объем производства и сбыта
Время

Рисунок 7.1 – Характерные зоны промышленного выпуска изделия: 1¾ Создание;2 ¾ Освоение и начало промышленного производства; 3 ¾ Рост сбыта, расширение выпуска; 4 ¾ Устойчивый сбыт и выпуск; 5 ¾ Падение сбыта и выпуска; 6 ¾ Снятие с производства.
Для большинства продуктов характерна циклическая повторяемость этих фаз, связанная каждый раз, как правило, с освоением новой модификации нововведения. Для отдельных фаз жизненного цикла свойственны определенные организационно-экономические условия, выражающиеся в типичных формах финансирования, характере выбираемой ценовой политики, поведении на рынках, масштабе производства и сбыта продукта и пр.
Потребность общества в появлении нового продукта |
||
1.Научно-исследовательские работы |
||
Фундаментал |
Поисковые |
Прикладн |
ьные |
|
ые |
Открытия |
Изобретения |
|
2. Техническое задание |
|
3. Проектно-конструкторские работы |
|||
Эскизны |
Технич |
Опытные образцы |
|
Технич |
еский |
и рабочая |
|
й проект |
|||
.предл |
проект |
документация |
|
ожени |
|||
|
|
||
4. Технологическая подготовка и освоение |
|||
|
производства |
|
Технолог |
Проектиров |
Отладка |
Организац |
ич.маршр |
ание и |
процессов |
ия |
уты и |
изготовлен |
и сдача |
освоения |
|
|||
|
|
|
|
5.Производство
6.Реализация, хранение, транспортирование, монтаж
иотладка изделия
7.Эксплуатация
8.Утилизация
Рис. Примерная схема стадий и этапов жизненного цикла изделия.
Исследовательская стадия проектирования продукта
Развитие современного производства конкурентоспособной продукции немыслимо без масштабных, ориентированных на долгосрочный период научных исследований.
Научно-исследовательские работы (НИР) ─ это целенаправленная деятельность, имеющая своей задачей создание новой информации об объектах, явлениях или процессах, происходящих в природе, обществе или технике.
В зависимости от целей, содержания и характера результатов различают:
-фундаментальные исследования;
-поисковые исследования;
-прикладные исследования.

Фундаментальные исследования, как правило, имеют наиболее общий и абстрактный характер. Они направлены на расширение знаний и понимание наиболее общих закономерностей, действующих в природе, технике, обществе, без проникновения в области их конкретного применения.
Поисковые исследования. Главные задачи поисковых исследований заключаются в следующем:
-изучение возможности применения известных или вновь открытых явлений и закономерностей для создания новой техники, технологии или материалов;
-оценка и прогнозирование развития отдельных направлений науки, техники и технологии;
-поиск сфер, областей и изучение условий применения новых решений и открытий (так называемые аппликационные исследования).
Прикладные исследования направлены на решение конкретных научно-технических и организационно-экономических проблем, связанных с выполнением последующих проектных разработок.
Прикладные исследования включают:
-поиск путей улучшения существующих конструкций, технологий или материалов в целях повышения конкурентоспособности продуктов;
-определение способов использования новейших достижений науки и техники для создания новой конкурентоспособной продукции;
-проведение аналитических работ по обобщению опыта конкурентов и исследованию рыночной конъюнктуры;
-выполнение модельных разработок, проведение экспериментальных и испытательных работ. Этот вид исследования более строго ориентирован на потребности рынка, обычно
регламентирован по времени и исполнителям. Затраты при проведении прикладных исследований резко возрастают по сравнению с другими видами исследовательских работ. Планирование основывается на укрупненных нормативных расчетах и предусматривает наличие опытно-экспериментальной базы.
Опытно-конструкторские разработки
Опытно-конструкторские разработки ─ это комплекс работ, осуществляемых с целью создания новых видов техники с заданными технико-экономическими параметрами в виде опытного образца, опытной установки и рабочей документации для их промышленного изготовления и использования.
Главная задача ОКР состоит в создании конкурентоспособного продукта, отличающегося высоким научно-техническим уровнем инженерных решений, способного удовлетворять потребительский спрос рынка.
ОКР, в отличии от научно-исследовательских работ характеризуются достаточно устойчивым составом стадий, этапов и работ. Технология их проведения, приемы инженерных разработок и расчетов регламентируются, как правило, специальными отраслевыми или внутрифирменными нормативными документами, основанными на разработанной в стране системе государственных стандартов, определяющих состав этапов ОКР, порядок их проведения и требования к оформлению документации.
Комплекс работ по конструированию нового продукта обычно включает три относительно самостоятельные стадии ОКР:
-подготовительную;
-разработку проектной документации;
-разработку рабочей документации.
На подготовительной стадии конструирования нового продукта обосновывается необходимость его создания и согласовывается состав основных технико-экономических параметров. На этой стадии изучается рыночная ситуация, проводятся маркетинговые исследования, анализируется и прогнозируется спрос на новый продукт, устанавливаются технологические ограничения на условия производства нового продукта. Результаты расчетов и согласований отражаются в утверждаемом техническом задании на разработку. На подготовительной стадии осуществляется регламентация процесса выполнения проекта: определение состава этапов и работ, последовательности и календарных сроков их выполнения, установление состава исполнителей и распределение заданий между ними, выявление контрагентов и планирование кооперации.
Разработка проектной документации предусматривает выполнение комплекса работ, определяющих концептуальные решения по новому продукту: выбор принципа действия, общую

компоновку продукта, требования к составу узлов и функциональных блоков, инженерный и стоимостной анализ функциональной структуры продукта, проведение экспериментальных работ и испытаний отдельных узлов и компоновочных решений. Эта стадия проектирования продукта включает выполнение этапов разработки технического предложения, эскизного проекта и технического проекта.
Разработка рабочей документации завершает проектирование нового продукта. На этой стадии осуществляется подготовка комплекса конструкторской документации, необходимой для материального воплощения проектируемого изделия. Рабочий проект предусматривает наиболее полную детализацию разрабатываемой конструкции, обеспечивающую возможность изготовления, контроля и приемки отдельных деталей и узлов, а также сборки, испытания и эксплуатации продукта у потребителя. Рабочая документация включает подготовку рабочих чертежей деталей, сборочных единиц и узлов изделия, производственной и эксплуатационной документации (паспорт изделия, описание для пользователя, инструкция по эксплуатации, документы сервисного обслуживания, гарантийная документация и пр.)
Конструкторская подготовка производства
Конструкторская подготовка производства ─ это совокупность взаимосвязанных процессов, обеспечивающих техническую готовность предприятия к выпуску нового продукта в установленные сроки с заданными параметрами качества, объемом производства и уровнем затрат.
Главная задача конструкторской подготовки производства заключается в целесообразном и эффективном приспособлении отработанной конструкции продукта к условиям его будущего производства при обязательном сохранении заложенных в конструкцию параметров качества.
В процессе конструкторской подготовки последовательно отрабатываются качественные параметры продукта и решаются две главные задачи:
-повышение уровня унификации и стандартизации конструкции;
-обеспечение технологичности продукта.
Конструкторская унификация ─ это сокращение разнообразия элементов без ущерба разнообразию систем или ситуаций, в которых они применяются. Это комплекс мероприятий, устраняющих необоснованное многообразие типов и конструкций изделий, форм и размеров деталей и заготовок, профилей и марок материалов. В качестве основных направлений унификации выступают:
-сокращение номенклатуры изделий, сборочных единиц и узлов, имеющих одинаковое или сходное эксплуатационное назначение и параметры;
-заимствование отдельных деталей, узлов для нового продукта из числа ранее освоенных в производстве на основе конструктивной преемственности;
-создание параметрических рядов (гамм) продуктов, аналогичных по конструктивному решению, но различных по габаритам, мощности и другим эксплуатационным параметрам;
-типизация форм и размеров деталей и заготовок, профилей и марок используемых материалов. Стандартизация представляет собой высшую форму унификации. Международная организация
по стандартизации (ИСО) приняла следующее определение стандартизации. «Стандартизация ─ это процесс установления и применения правил с целью упорядочения деятельности в данной области на пользу и при участии всех заинтересованных сторон, в частности, для достижения всеобщей максимальной экономии, с соблюдением функциональных условий и требований безопасности». Стандарты устанавливают обязательные для выполнения нормы, образцы, типы решений и распространяются не только на конструкцию продукта, но на все другие факторы производства.
Степень унификации и стандартизации может быть охарактеризована следующими коэффициентами:
Показатель |
Расчетная формула |
Принятые обозначения |
||||||||||
Коэффициент унификации |
k |
|
= |
тун |
|
|
тун |
─ количество типоразмеров |
||||
|
ун |
|
т |
деталей, |
унифицированных с |
|||||||
|
|
|
|
|||||||||
|
|
|
|
|
||||||||
|
|
|
|
|
|
|
|
деталями других изделий; |
||||
|
|
|
|
|
|
|
|
т |
─ |
общее |
количество |
|
|
|
|
|
|
|
|
|
типоразмеров деталей в изделии |
||||
Коэффициент |
k |
|
= |
тст |
|
тст |
─ количество типоразмеров |
|||||
стандартизации |
|
|
||||||||||
ст |
т |
стандартных деталей в изделий; |
||||||||||
|
|
|
||||||||||
|
|
|
|
|||||||||
|
|
|
|
|
|
|
|
т |
─ |
общее |
количество |
|
|
|
|
|
|
|
|
|
типоразмеров деталей в изделии |

Коэффициент |
k |
|
= |
т - то |
|
то |
─ количество |
типоразмеров |
|
преемственности |
пр |
т |
|
оригинальных деталей в изделий; |
|||||
|
|
|
|
||||||
|
|
|
|
|
|
т |
─ |
общее |
количество |
|
|
|
|
|
|
типоразмеров деталей в изделии |
Производственной технологичностью ─ называется степень соответствия конструкции оптимальным производственно-технологическим условиям его изготовления при заданном объеме выпуска; технологичной можно считать только ту удовлетворяющую эксплуатационным требованиям конструкцию, освоение и выпуск которой при заданном объеме производства будет протекать с минимальными производственными издержками (наименьшая трудоемкость, материалоемкость, кратчайший производственный цикл).
Эксплуатационная технологичность ─ конструкции изделия проявляется в сокращении затрат времени и средств на техническое обслуживание и ремонт изделий, зависящих от так называемой ремонтопригодности конструкции ─ ее приспособленности предупреждать, обнаруживать и устранять отказы и неисправности. Таким образом, это характеристика соответствия изделий рациональным условиям его эксплуатации.
Технологическая подготовка производства Технологическая подготовка производства (ТПП) ¾ это совокупность взаимосвязанных
процессов, обеспечивающих технологическую готовность предприятия к выпуску нового продукта в установленные сроки, с заданными параметрами качества, объемом производства и уровнем затрат. В рамках ТПП решаются следующие основные задачи проектирования производства нового продукта на предприятии:
-обеспечение технологической конструкции изделия;
-выбор и расстановка технологических процессов по всем стадиям производства и составным элементам нового продукта;
-проектирование и изготовление средств технологического оснащения производственных
процессов;
-управление процессами технологической подготовки производства.
На российских предприятиях при осуществлении технологической подготовки производства пользуются рекомендациями стандартов системы ЕСТПП (Единая система технологической подготовки производства): ГОСТ 14.301 – 73 « Общие правила разработки технологических процессов и выбора средств технологического оснащения», ГОСТ 14.301 – 72 « Виды технологических процессов» и др.
Технологические процессы делятся на единичные (предназначены для изготовления продукта одного наименования, назначения или типоразмера), типовые (применяется для совокупности однородных по технологическим и конструктивным признакам деталей) и групповые (применяется для изготовления предметов с различными конструктивными, но общими технологическими признаками).
Технологический маршрут (межцеховой и внутрицеховой) ¾ это последовательность прохождения заготовки, детали или сборочной единицы по цехам и производственным участкам предприятия.
Состав работ по технологической подготовке производства
Общий порядок работ по технологической подготовке производства нового продукта представлен на рисунке 1.
По формам организации различают внутризаводскую и внезаводскую технологическую подготовку производства. На предприятии технологическое обеспечение производства осуществляют службы главного технолога. К ним относятся отдел главного технолога, конструкторские бюро по оснастке, инструментальные производства, нормативно-плановые службы. Планирование и координация всех работ по подготовке производства новых продуктов осуществляет, как правило, специальная служба ¾ бюро планирования подготовки производства, находящаяся в подчинении главного инженера предприятия.