
- •Оглавление
- •ВВЕДЕНИЕ
- •РАЗДЕЛ II. МАТЕРИАЛОВЕДЕНИЕ СТАЛЕЙ И ЧУГУНОВ
- •РАЗДЕЛ III. МАТЕРИАЛОВЕДЕНИЕ ЦВЕТНЫХ МЕТАЛЛОВ И СПЛАВОВ
- •8.3. Композиционные материалы
- •8.4. Металлические стекла
- •9.1. Природные каменные материалы
- •9.2. Минеральные неорганические вяжущие вещества
- •9.4. Каменные плавленые материалы
- •11.1. Полупроводниковые материалы
- •БИБЛИОГРАФИЧЕСКИЙ СПИСОК

РАЗДЕЛ II. МАТЕРИАЛОВЕДЕНИЕ СТАЛЕЙ И ЧУГУНОВ
Глава4. Стали, сплавысистемыжелезо–углерод. Маркировка, структура, свойствасплавов
4.1. Строениеисвойствачистогожелеза
Железо – ферромагнитный переходный полиморфный металл, с поряд-
ковым номером 26 в таблице Д.И. Менделеева. Электронная структура: 1s2 2s2 2p6 3s2 3p6 3d6 4s2.
Температура плавления чистого железа 1539 °С. Плотность при комнатной температуре 7,684 г/см3, атомная масса 55,85. Структура железа представляет собой равноосные полиэдры, разделенные тонкими прожилками границ зерен. Чистое железо имеет сравнительно крупные зерна. Техническим железом называют сплавы железа с углеродом, если содержание углерода в них не превышает 0,02 % мас. Увеличение количества примесей, в том числе углерода, измельчает размер зерна и увеличивает толщину границ. В техническом железе возможно выделение прожилок третичного цементита вдоль границ зерен. Железо имеет ряд критических точек (А4 = 1 392 °С, А3 = = 911 °С), соответствующих полиморфным превращениям, а также точку магнитного превращения (точка Кюри – 770 °С).
При температурах ниже 911 оС железо имеет решетку объемноцентрированного куба (ОЦК), параметр решетки 2,8605 кХ при 20 °С. Эта модификация носит название альфа-железо (α-Fe). До 770 °С альфа-железо ферромагнитно, выше – парамагнитно. Ферромагнетизм исчезает при температуре точки Кюри, без какого-либо изменения в кристаллической структуре. Точка Кюри не обладает термическим гистерезисом, т.е. при охлаждении железа ниже 770 °С ферромагнетизм восстанавливается.
Температура 911 °С является критической точкой (А3), при которой осуществляется полиморфное превращение αFe γFe. Выше 911 °С происходит перестройка кристаллической структуры железа из решетки объемноцентрированного куба в решетку с более плотной упаковкой атомов – куб гранецентрированный (ГЦК) – гамма-железа (γ-Fe). Превращение αFe → γFe сопровождается уменьшением удельного объема примерно на 1%. Параметр ГЦК-решетки гамма-железа 3,6409 кХ при 950 °С.
В равновесных условиях при очень медленном нагреве перестройка решетки из альфа в гамма-железо начинается приблизительно на 10 °С выше, чем при образовании альфа из гамма-железа при очень медленном охлаждении. Поэтому для того, чтобы различить температуры, при которых начинаются превращения, используют дополнительные индексы c и r соответственно при нагреве и охлаждении. В этом случае критические точки обозначают,
Материаловедение. Учеб. пособие |
-159- |
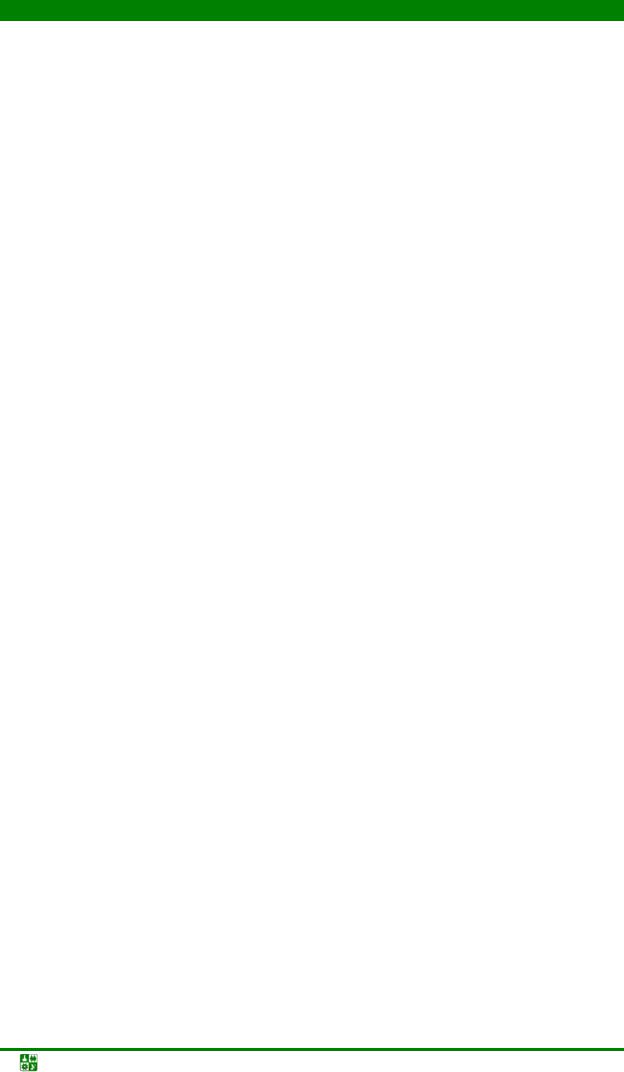
РАЗДЕЛ II. МАТЕРИАЛОВЕДЕНИЕ СТАЛЕЙ И ЧУГУНОВ
Глава 4. Стали, сплавы системы железо–углерод. Маркировка, структура, свойства сплавов
соответственно, Ас3 и Аr3 при нагреве и охлаждении. Разница в температурных значениях Ас3 и Аr3 называется температурным гистерезисом превращения.
Гамма-железо существует в температурном интервале 911–1 392 °С. Температура 1 392 °С (А4) является критической точкой, при которой происходит перестройка γFe δFe. Дельта-железо, существующее до температуры плавления, имеет решетку аналогичную альфа-железу, решетку объемноцентрированного куба, отличающуюся от альфа-железа параметром решетки (2,93 кХ при 1425 °С). Гамма и дельта-железо парамагнитны.
4.2. Диаграммасостоянияжелезо–углерод
Взаимодействие железа и углерода, природа фаз, характер фазовых равновесий в системе и сама диаграмма железо–углерод определяется электронным строением железа и углерода.
Железо в металлическом состоянии в реальных условиях, описываемых диаграммой железо–углерод, отдает два его внешних валентных электрона с оболочкой 4s2 в коллективизированное состояние. Открывающиеся при этом орбитали d6 электронной оболочкой перекрываются, образуя решетку объем- но-центрированного куба (ОЦК). Такое электронное строение свойственно альфа и дельта-железу.
В интервале температур от 911 до 1 392 оС d6-орбитали не перекрываются, в связи с чем сферическая симметричная электронная конфигурация электронной оболочки обеспечивает образование плотной упаковки гранецентрированного куба, отвечающей решетке гамма-железа.
Электронная конфигурация атомов углерода 1s2 2s2 2p2. Четыре электрона на внешней оболочке могут переходить либо в коллективизированное состояние при образовании растворов, либо принимать участие в валентных связях при образовании химических соединений. Кроме того, внешняя оболочка углерода может заполняться до уровня 2s2 2p6 при образовании металлических карбидов.
Углерод в системах с железом при нормальном давлении может находиться в свободном состоянии в виде графита, а также в растворенном состоянии в твердых и жидких растворах, кроме того, он образует карбиды, например, цементит Fe3C. Цементит – соединение с преимущественной ковалентной связью, усиленной небольшой долей ионной связи между ионами железа и углерода, а также металлической связью. Наличие некоторой части металлической связи в цементите обусловливает его проводимость в связи с появлением в связи с ней некоторой электронной концентрации.
При образовании цементита происходит обмен электронами между соседними атомами железа и углерода по одному d-электрону иона Fe2+ с конфигурацией d6 и электроном внешней оболочки атома углерода. У атома углерода принимают участие в образовании связей шесть валентных электронов, захваченных на уровень 2p. Шесть орбиталей 2p6-оболочки перекрываются с шестью d-орбиталями шести ближайших атомов железа (d6). При этом
Материаловедение. Учеб. пособие |
-160- |
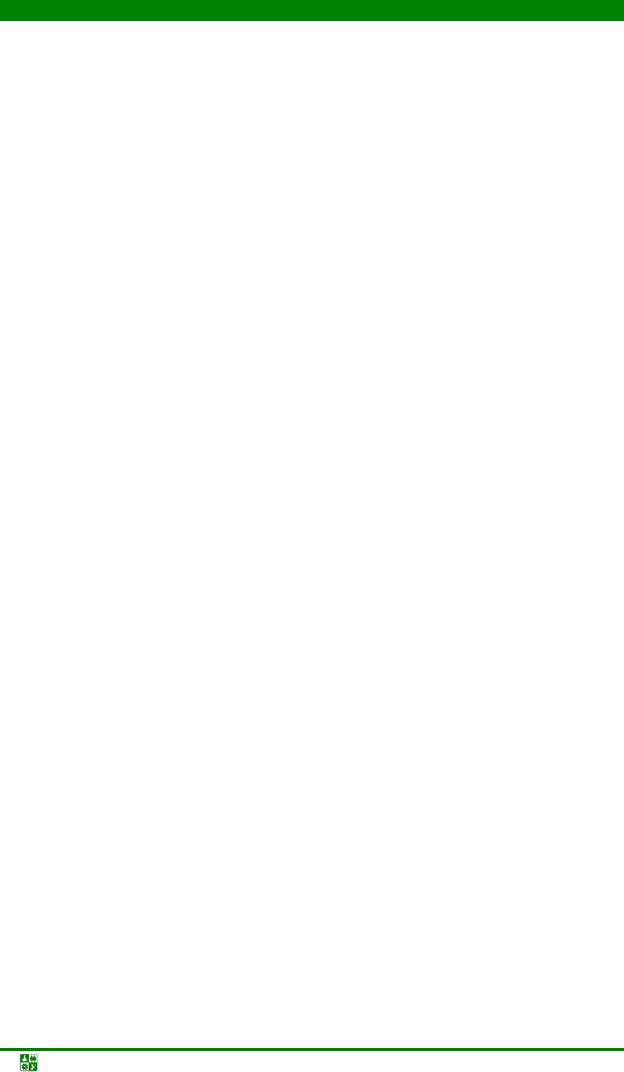
РАЗДЕЛ II. МАТЕРИАЛОВЕДЕНИЕ СТАЛЕЙ И ЧУГУНОВ
Глава 4. Стали, сплавы системы железо–углерод. Маркировка, структура, свойства сплавов
возникают шесть обменных двухэлектронных связей ковалентного типа, определяя преимущественную ковалентную связь в решетке цементита.
Графит имеет гексагональную слоистую структуру за счет полуторных связей между атомами углерода.
При растворении углерода в железе его атомы теряют валентные электроны, которые коллективизируются и переходят в электронный газ вместе с электронами железа. Оголяющаяся при этом 1s2-электронная конфигурация иона углерода приобретает сферическую конфигурацию и имеет очень малый размер (около 1,1 кХ). Это позволяет размещаться ионам углерода в октаэдрических пустотах ГЦК- и ОЦК-решеток железа, образуя твердые растворы внедрения: γ-твердый раствор (аустенит), α-феррит и δ-феррит.
Жидкие растворы углерода в железе выше температуры плавления сплавов в системе железо–углерод имеют то же электронное строение, что и твердые растворы: δ-феррит и γ-аустенит. При плавлении сохраняется тот же ближний порядок в кристаллическом строении сплавов, который наблюдался до плавления в данном сплаве в твердом состоянии. При плавлении нарушается лишь дальний порядок.
Фазовые состояния железоуглеродистых сплавов, в зависимости от состава и температуры, описываются диаграммами стабильного и метастабильного равновесия. Термодинамический анализ показывает, что наиболее стабильной системой, образованной двумя компонентами: железом и углеродом, является сис- темажелезо–графит. Метастабильнойявляетсясистемажелезо–цементит.
Диаграмма железо–графит построена в условиях очень медленного нагрева и охлаждения (доли градуса в минуту). Диаграмма железо–цементит строится в условиях более высоких скоростей нагрева и охлаждения (порядка нескольких градусов в минуту).
Диаграммы позволяют описать как фазовый состав, так и структуру сплава. В этом случае диаграммы называют, соответственно, фазовой или структурной. Часто обозначения фазового и структурного состава сплавов объединяют. В этом случае диаграмма носит название фазово-структурной. При изображении линий стабильной диаграммы железо–графит (рис. 4.1) чаще всего используют штриховые линии, при изображении линий метастабильной диаграммы – сплошные линии (рис. 4.2). Эти диаграммы также часто совмещают на одном координатном поле (рис. 4.3).
Материаловедение. Учеб. пособие |
-161- |

РАЗДЕЛ II. МАТЕРИАЛОВЕДЕНИЕ СТАЛЕЙ И ЧУГУНОВ
Глава 4. Стали, сплавы системы железо–углерод. Маркировка, структура, свойства сплавов
Рис. 4.1. Фазово-структурная стабильная диаграмма железо–графит
Все точки диаграммы железо–углерод имеют определенный физический смысл и общепризнанные в мировой практике буквенные обозначения. Знание основных свойств и характеристик этих точек облегчает понимание диаграммы и ее практическое использование. Ниже приведены краткие характеристики точек диаграммы.
А – точка, соответствующая плавлению или кристаллизации чистого железа. Температура, отвечающая этой точке, равна 1 539 °С. Число степеней свободы в этой точке равно нулю. На термических кривых для чистого железа температуре точки А соответствуют горизонтальные площадки, которые возникают за счет выделения скрытой теплоты кристаллизации. Переход из твердого в жидкое состояние, соответствующий точке А, сопровождается резким увеличением объема (около 6 %), связанным с нарушением дальнего порядка в кристаллическом строении δ-железа. При кристаллизации чистого железа в этой точке наблюдаются обратные явления.
Материаловедение. Учеб. пособие |
-162- |
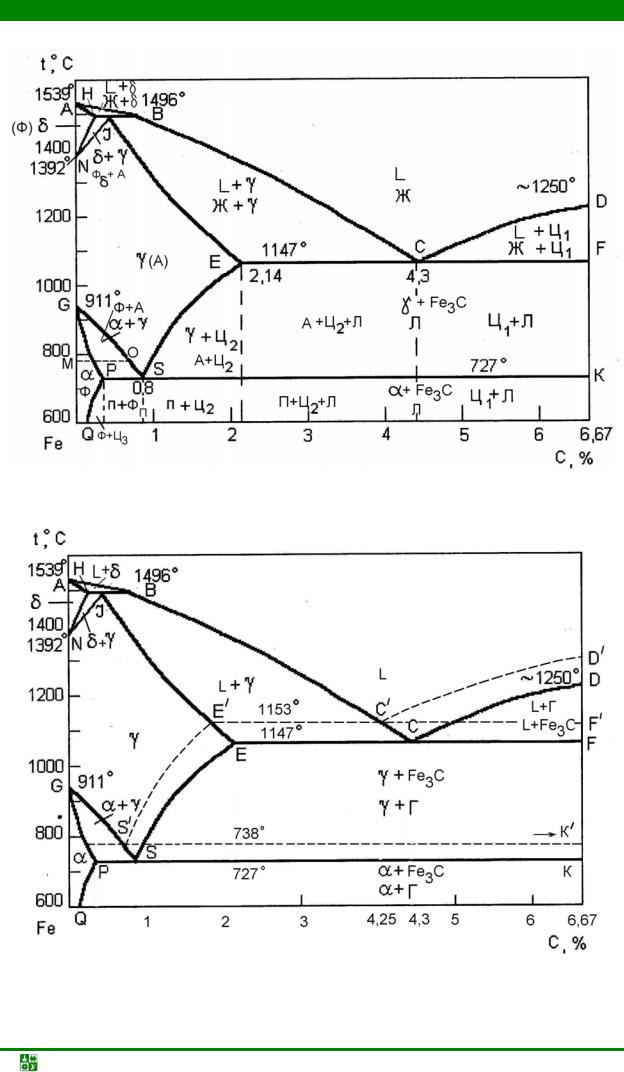
РАЗДЕЛ II. МАТЕРИАЛОВЕДЕНИЕ СТАЛЕЙ И ЧУГУНОВ
Глава 4. Стали, сплавы системы железо–углерод. Маркировка, структура, свойства сплавов
Рис. 4.2. Фазово-структурная метастабильная диаграмма железо–цементит
Рис. 4.3. Совмещенная фазовая диаграмма железо–углерод
Материаловедение. Учеб. пособие |
-163- |
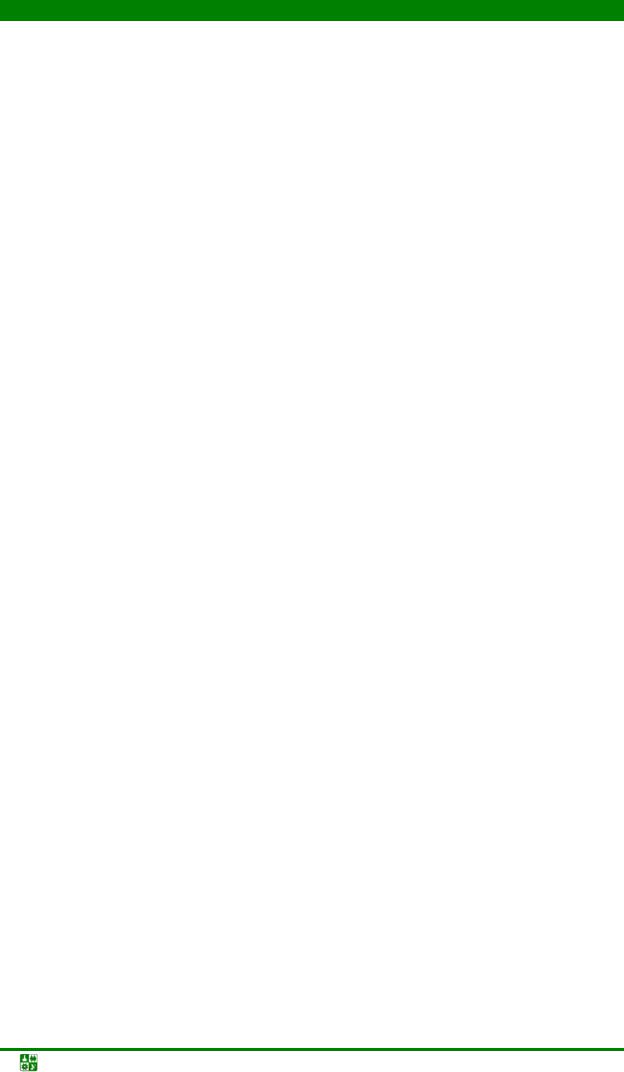
РАЗДЕЛ II. МАТЕРИАЛОВЕДЕНИЕ СТАЛЕЙ И ЧУГУНОВ
Глава 4. Стали, сплавы системы железо–углерод. Маркировка, структура, свойства сплавов
В – точка предельного насыщения железом жидкого раствора, находящегося в равновесии одновременно с кристаллами δ- и γ-твердых растворов при перитектической температуре. Точке В соответствует содержание углерода в жидкости 0,51 %, температура 1 496 °С.
С – эвтектическая точка в метастабильной системе Fe–Fe3C. Температура 1 147 °C, концентрация углерода, соответствующая точке С, равна 4,3 % – это содержание углерода в жидком растворе, находящемся в равновесии одновременно с аустенитом и цементитом при эвтектическом превращении. Число степеней свободы, соответствующее этой точке, равно нулю. На термических кривых охлаждения и нагрева точке С соответствуют горизонтальные площадки, аналогичные площадкам плавления-кристаллизации чистого железа.
С' – эвтектическая точка в стабильной системе железо–графит. Температура, соответствующая точке, равна 1 153 °С, концентрация углерода равна 4,25 % – это содержание углерода в жидкости, находящейся в равновесии с аустенитом и графитом при эвтектической кристаллизации. Как и в точке С, в данной точке система нонвариантна.
D – согласно принятым обозначениям, точку D относят к температуре плавления цементита. Однако известные данные свидетельствуют о том, что цементит представляет собой термодинамически неустойчивую фазу, в связи с чем перед плавлением он разлагается на железо и графит. При этом положение точки D на диаграмме оказывается неопределенным.
D' – точка, соответствующая температуре плавления графита (около 4
000°С).
Е– точка, отвечающая предельному содержанию углерода в аустените, находящемся в равновесии с цементитом и жидкостью при эвтектической температуре (1 147 °С) в метастабилъной системе. Значение содержания углерода 2,14 %. Точка Е на концентрационной оси диаграммы является своеобразной границей между сталями и чугунами. При содержании углерода в сплавах меньше 2,14 % в их структуре отсутствует ледебурит; при содержании углерода более 2,14 % ледебурит присутствует в структуре сплавов. Он является одной из важнейших структурных составляющих чугунов.
Е' – точка, отвечающая предельному содержанию углерода в аустените, находящемся в равновесии с графитом и жидким раствором при эвтектической температуре (1 153 °С) в стабильной системе. Значение содержания углерода, соответствующего этой точке, равно 2,03 %.
F – точка предельного насыщения цементита железом при эвтектической температуре (1 147 °С). Значение концентрации углерода, соответствующее точке F, практически близко к 6,67 %, хотя последние работы показывают наличие некоторой весьма малой растворимости железа в цементите.
F' – точка предельного насыщения графита железом при эвтектической температуре (1 153 °С).
G – точка полиморфного превращения в чистом железе α γ. Температура превращения 911°С. Число степеней свободы системы в этой точке
Материаловедение. Учеб. пособие |
-164- |
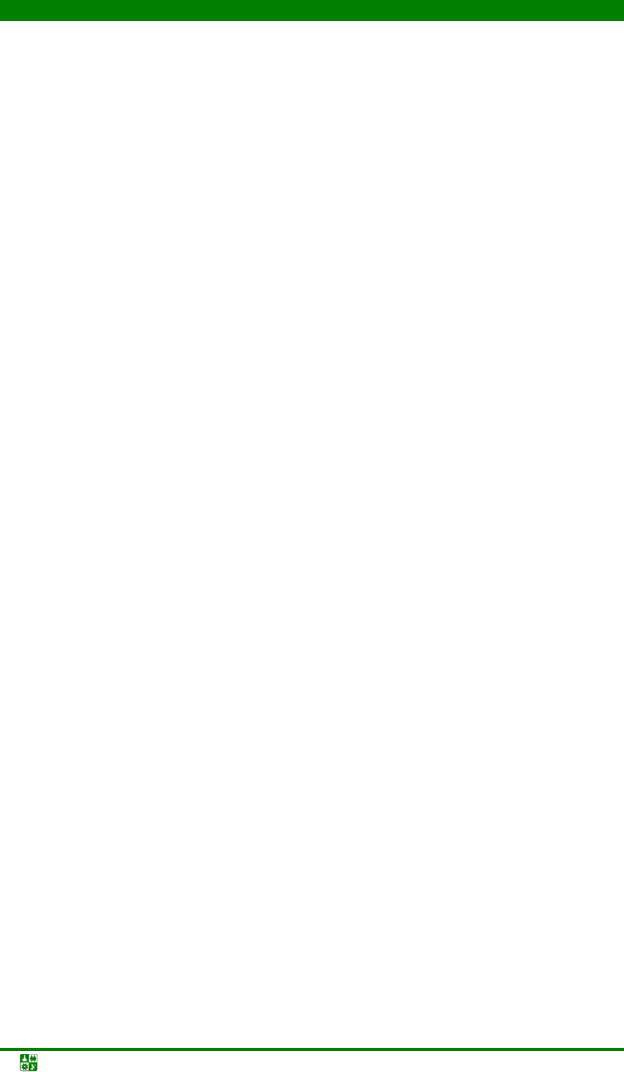
РАЗДЕЛ II. МАТЕРИАЛОВЕДЕНИЕ СТАЛЕЙ И ЧУГУНОВ
Глава 4. Стали, сплавы системы железо–углерод. Маркировка, структура, свойства сплавов
равно нулю. Перестройка кристаллической решетки α → γ сопровождается уменьшением объема, обратный переход γ → α увеличивает удельный объем образца, что связано с различной плотностью упаковки атомов в гранецентрированной решетке γ-железа и объемно-центрированной решетке α-железа. Точка G соответствует для чистого железа критической точке А3.
Н – точка предельного насыщения углеродом δ-феррита при температуре перитектического превращения. Температура, соответствующая этой точке, равна 1 496 °С, концентрация углерода 0,10 %. Это содержание углерода соответствует концентрации δ-феррита, находящегося в равновесии с аустенитом и жидкостью одновременно при температуре перитектического превращения.
I – перитектическая точка, точка трехфазного равновесия, соответствующая равновесной концентрации аустенита, образующегося по перитектичеокой реакции в изотермических условиях из жидкости состава точки В и δ-феррита состава точки Н. Температура, соответствующая точке I, равна 1 496 °С, концентрация углерода 0,16 %.
К – точка предельного насыщения железом цементита при эвтектоидной температуре 727 °С. Точке практически соответствует концентрация 6,67 % углерода.
К' – точка предельного насыщения железом графита при эвтектоидной температуре (738 °С).
М – точка Кюри чистого железа. Температура этой точки 770 °С. Точка соответствует потере ферромагнетизма α-железа при нагреве и восстановлению его ферромагнетизма при охлаждении.
N – точка полиморфного превращения δ γ в чистом железе. Температура превращения 1 392 °С. Точка N для чистого железа соответствует критической точке А4. В этойточке система нонвариантна.
О – точка наибольшей растворимости углерода в аустените, находящемся в контакте с немагнитным ферритом при температуре 770 °С. Содержание углерода в аустените в этой точке примерно равно 0,5 %.
Р – точка предельного содержания углерода в феррите, находящемся в равновесии с цементитом и аустенитом при эвтектоидной температуре (727 °С). Значение содержания углерода для этой точки 0,02 %. Точка Р на концентрационной оси диаграммы отделяет техническое железо от стали. В сталях (содержание углерода выше 0,02 %) в качестве структурной составляющей содержится перлит. В техническом железе (содержание углерода не более 0,02 %) перлит отсутствует.
S – эвтектоидная точка в метастабильной системе. Температура, соответствующая этой точке, равна 727 °С, содержание углерода 0,8 %. Это содержание углерода в аустените, находящемся в равновесии c ферритом и цементитом при эвтектоидной реакции. Число степеней свободы, как и для других трехфазных реакций в данной системе, равно нулю.
S' – эвтектоидная точка в стабильной системе железо–графит. Температура, отвечающая данной точке, равна 738 °С, содержание углерода в ау-
Материаловедение. Учеб. пособие |
-165- |
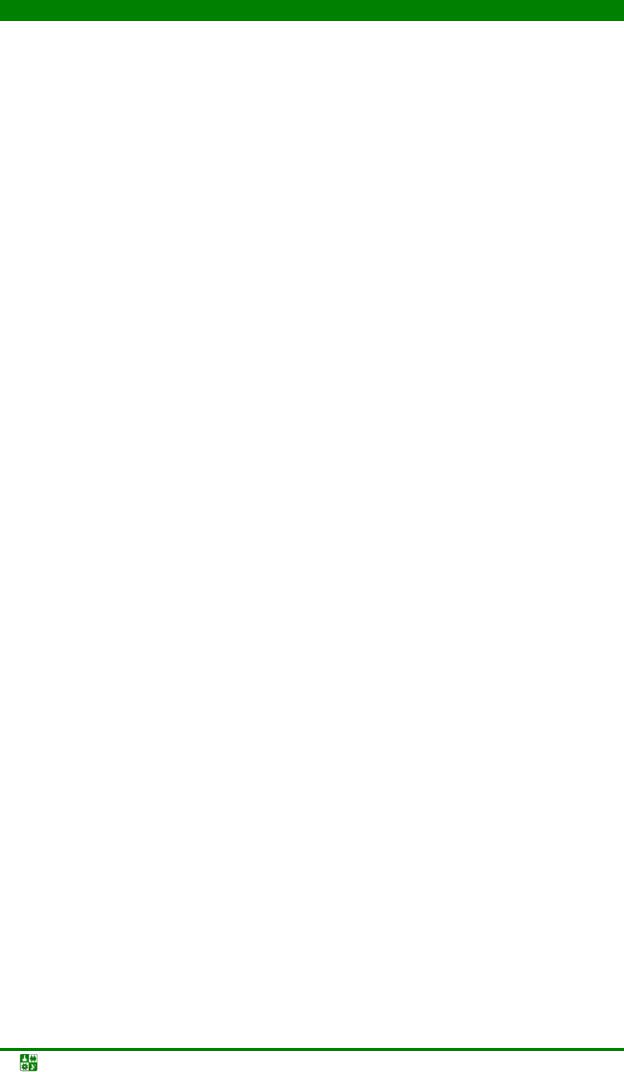
РАЗДЕЛ II. МАТЕРИАЛОВЕДЕНИЕ СТАЛЕЙ И ЧУГУНОВ
Глава 4. Стали, сплавы системы железо–углерод. Маркировка, структура, свойства сплавов
стените, соответствующее точке S', равно 0,69 %. Это содержание углерода в аустените, находящемся в состоянии равновесия с ферритом и графитом в момент развития прямого или обратного эвтектоидного превращения. Система в точке S' нонвариантна.
Q – точка предельной растворимости углерода в феррите (значение 0,006 % при комнатной температуре). Увеличение концентрации углерода в феррите до значений более 0,006 % приводит к изменению фазового состава и в первую очередь к появлению в структуре третичного феррита.
Каждая линия диаграммы железо–углерод является геометрическим местом точек того или иного фазового превращения, в том числе плавлениякристаллизации и фазовых превращений в твердом состоянии. Это значит, что переход через любую линию диаграммы, а также перемещение фигуративной точки внутри любой двухфазной области соответствует протеканию в сплаве того или иного фазового превращения. Тип этих превращений, их кинетика и полнота протекания определяются соответствующими линиями диаграммы. Ниже приведены характеристики практически всех известных к настоящему времени линий диаграммы, соответствующих стабильному и метастабильному равновесию.
АВСD – линия ликвидус в метастабильной системе, обозначающая начало процесса кристаллизации жидкости в метастабильной системе в равновесных условиях при охлаждении. Эта же линия означает окончание процесса плавления при нагреве сплавов в системе.
АВС'D' – то же, в стабильной системе.
AHIECF – линия солидус в метастабильной системе, обозначающая окончание процесса кристаллизация жидкости в равновесных условиях при охлаждении и начало плавления сплавов при нагреве.
AHIE'C'F' – то же в стабильной системе.
АВ – отрезок линии ликвидус – граница области L + δ.
ВС – отрезок линии ликвидус – граница области L + γ. СD – отрезок линии ликвидус – граница области L + Fe3C. С'D' – отрезок линии ликвидус – граница области L + Г. АН – отрезок лини солидус – граница области L + δ. HIB – линия перитектического превращения (1 496 °С).
HI – отрезок линии перитектического превращения и одновременно, отрезок линии солидус – граница между фазовыми областями L + δ и δ + γ.
IB – отрезок линии перитектического превращения – граница между базовыми областями L + δ и L + γ.
IE – отрезок линии солидус – граница области L + γ в метастабильной системе.
IE' – то же в стабильной системе.
ECF – линия эвтектического превращения – отрезок линии солидус в метастабильной системе (1 147 °С).
Е'С'F' – то же в стабильной системе (1 153 °C).
Материаловедение. Учеб. пособие |
-166- |
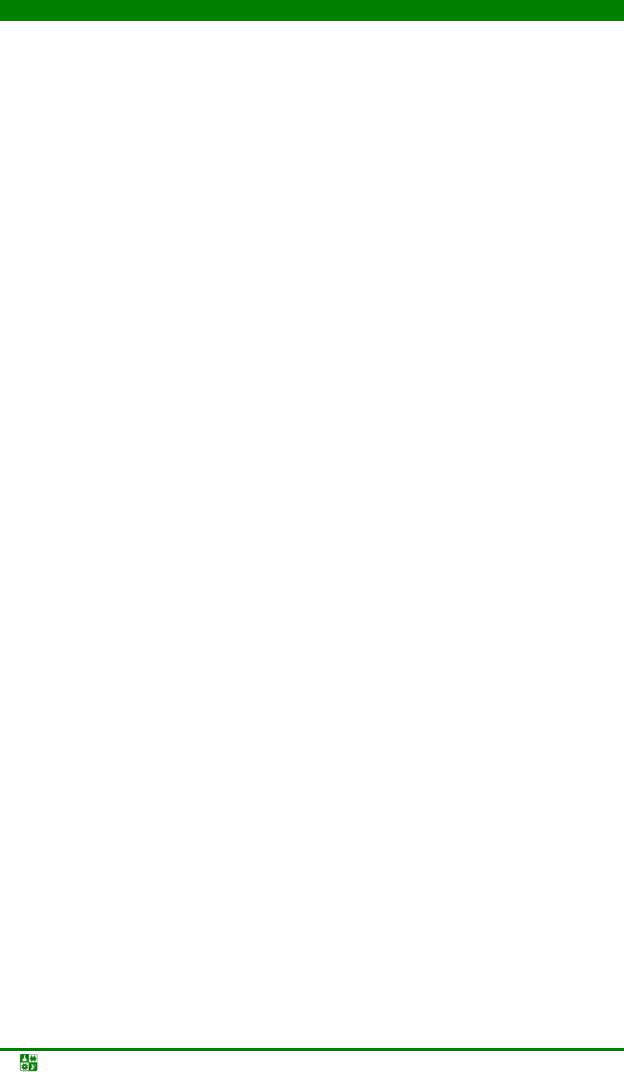
РАЗДЕЛ II. МАТЕРИАЛОВЕДЕНИЕ СТАЛЕЙ И ЧУГУНОВ
Глава 4. Стали, сплавы системы железо–углерод. Маркировка, структура, свойства сплавов
EC – отрезок линии эвтектического превращения и линии солидус в метастабильной системе – граница фазовых областей L + γ и γ + Fe3C.
E'C' – отрезок линии эвтектического превращения и линии солидус в стабильной системе – граница фазовых областей L + γ и γ + Г.
CF – отрезок линии эвтектического превращения и линии солидус в метастабильной системе – граница фазовых областей L + Fe3C и γ + Fe3C.
C'F' – отрезок линии эвтектического превращения и линии солидус в стабильной системе – граница фазовых областей L + Г и γ + Г.
NH – верхняя граница фазовых областей δ и γ + δ, верхняя температура полиморфного превращения твердых растворов δ → γ при охлаждении и γ → δ при нагреве.
NI – нижняя температура полиморфного превращения твердых растворов δ → γ при охлаждении и γ → δ при нагреве – граница фазовых областей γ и γ + δ. NI является критической точкой в сталях и техническом железе. Еe обозначение: А4 (Ac4, Аr4).
GS – верхняя температура полиморфного превращения твердых растворов γ → α при охлаждении и α → γ при нагреве – граница фазовых областей γ и γ + α. GS – критическая точка стали. Ее обозначение: А3(Ac3, Аr3).
GO – отрезок границы фазовых областей γ и γ + α, соответствующий выделению при охлаждении неферромагнитного феррита.
OS – отрезок границы фазовых областей γ и γ + α, соответствующий выделению при охлаждении ферромагнитного феррита.
GP – нижняя температура полиморфного превращения твердых растворов γ → α при охлаждении и α → γ при нагреве – граница фазовых областей α и α + γ.
МО – линия магнитного превращения феррита в стали (точка Кори). Температура – 770 °С. МО называют также второй критической точкой стали А2, однако при этом превращении не происходит фазовых переходов, связанных с перестройкой кристаллической решетки.
SE – линия переменной ограниченной растворимости углерода в аустените в метастабильной системе – граница фазовых областей γ и γ + Fe3С. SE – критическая точка стали Acm, характеризующая развитие частичной фазовой перекристаллизации в заэвтектоидных сталях и чугунах, заключающейся в выделении вторичного цементита из ауcтенита при охлаждении и растворении его в аустените при нагреве.
S'E' – линия переменной ограниченной растворимости углерода в аустените в стабильной системе – граница фазовых областей γ и γ + Γ. Как и в метастабильной системе, линия переменной ограниченной растворимости характеризует частичное фазовое превращение, заключающееся в выделе- нии-растворении вторичного графита в аустените.
PSK – линия эвтектоидного превращения в метастабильной системе (727 °С). PSK является критической точкой A1 (Aс1, Аr1) в сталях и чугунах, характеризующей развитие важнейших фазовых превращений в этих сплавах: аустенитного – при нагреве и перлитного – при охлаждении.
Материаловедение. Учеб. пособие |
-167- |
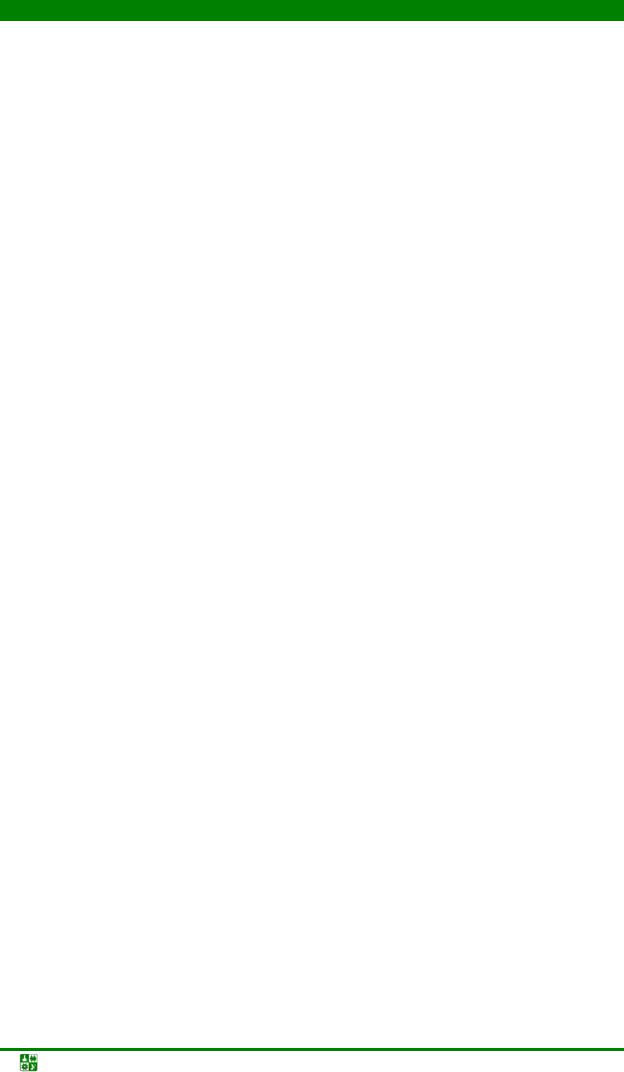
РАЗДЕЛ II. МАТЕРИАЛОВЕДЕНИЕ СТАЛЕЙ И ЧУГУНОВ
Глава 4. Стали, сплавы системы железо–углерод. Маркировка, структура, свойства сплавов
P'S'К' – то же в стабильной системе (738 °С).
PS – отрезок линии эвтектоидного превращения, характеризующий развитие этого превращения в доэвтектоидных сталях – граница фазовых областей γ + α и α + Fe3C.
SK – отрезок линии эвтектоидного превращения в метастабильной системе, характеризующий развитие этого превращения в заэвтэктоидных сталях и чугунах – граница фазовых областей γ + Fe3C и α + Fe3C.
S'К' – то же в стабильной системе – граница фазовых областей γ + Г и
α + Г.
PQ – линия переменной ограниченной растворимости углерода в феррите – граница фазовых областей α и α + Fe3C. Линия PQ характеризует частичную фазовую перекристаллизацию, заключающуюся в выделении третичного цементита из феррита при охлаждении и растворении его в феррите при нагреве. Это превращение имеет большое значение для технического железа и малоуглеродистых сталей (до 0,2 % С).
4.3. Фазы, структурныесоставляющие, ихстроениеисвойства
Фазовая составляющая, или фаза, – это гомогенная часть системы определенного состава и агрегатного состояния, отделенная от остальных частей системы поверхностями раздела.
В отличие от фазовой составляющей, структурная составляющая – это гомогенная или квазигомогенная часть системы, состоящая из одной или нескольких фаз, имеющая во всем объеме этой составляющей одинаковый средний химический состав и регулярное строение, обусловленное особенностями механизмов ее образования. К фазовым составляющим в системе железо–углерод относятся: жидкий раствор (L), твердые растворы: феррит (α), аустенит (γ) , высокотемпературный феррит (δ), а также цементит и графит
(Г).
Жидкий раствор в системе железо–углерод представляет собой раствор углерода в расплавленном железе. При температурах значительно выше линии ликвидус (преимущественно выше 1 700 °С) жидкость является статистически неупорядоченным раствором со статистически плотной упаковкой. При небольшом перегреве выше линии ликвидус жидкий раствор имеет сравнительно регулярное строение. Жидкий раствор, образовавшийся при плавлении δ-феррита (до 0,51 % С), сохраняет ближний порядок по ОЦК-решетке δ-железа. Жидкий раствор, образующийся при плавлении аустенита, имеет ближний порядок, соответствующий ГЦК-решетке γ-железа.
Феррит – это твердый раствор внедрения углерода в α-железе. Решетка феррита – объемно-центрированный куб с расположением атомов углерода в сравнительно небольших октаэдрических пустотах решетки (рис. 4.4), сильно искажая ее. Растворимость углерода в феррите невелика. При температуре 727 °С в феррите растворяется 0,02 % С; при понижении температуры рас-
Материаловедение. Учеб. пособие |
-168- |
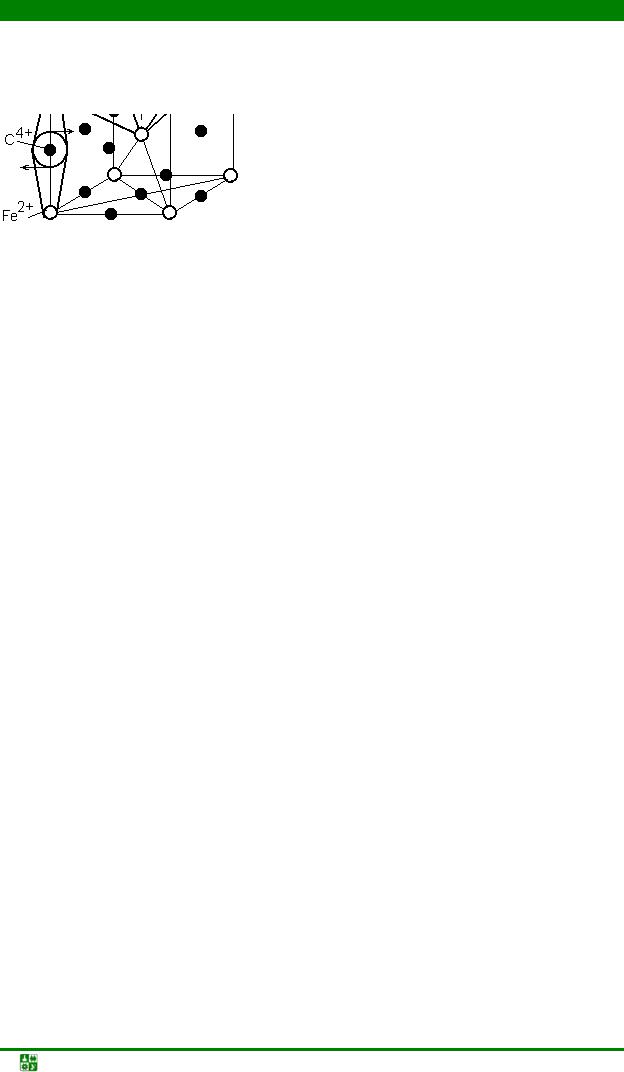
РАЗДЕЛ II. МАТЕРИАЛОВЕДЕНИЕ СТАЛЕЙ И ЧУГУНОВ
Глава 4. Стали, сплавы системы железо–углерод. Маркировка, структура, свойства сплавов
творимость уменьшается, достигая величины 0,006 % С при комнатной температуре.
Рис. 4.4. Позиции ионов углерода С4+ в ок- |
Рис. 4.5. Позиции ионов углерода С4+ в |
таэдрических пустотах ОЦК-решетки |
октаэдрических пустотах ГЦК-решетки |
|
γ-железа |
Структура феррита представляет собой сравнительно равноосные полиэдрические кристаллы, разделенные между собой тонкими высокоугловыми границами. Выявляется обычно структура феррита при травлении растворами азотной кислоты.
Феррит до температуры точки Кюри (770 °С) сильно ферромагнитен, хорошо проводит тепло и электрический ток. В равновесном состоянии феррит пластичен (относительное удлинение порядка 40 %), имеет небольшую прочность и твердость (HB = 65–130, в зависимости от величины зерна).
Феррит, в зависимости от характера протекающих фазовых превращений, в структуре железоуглеродистых сплавов может находиться в виде различных структурных состояний: феррит как основа структуры сплава (Ф); феррит как вторая (избыточная) фаза, располагающаяся по границам перлитных колоний, в виде отдельных включений равноосной или игольчатой формы; феррит, входящий в качестве фазы в состав другой структурной составляющей – перлита или феррито-графитного эвтектоида.
При температурах выше критической точки А4 стабильной становится модификация высокотемпературного δ-феррита, имеющего, как и низкотемпературный α-феррит, объемно-центрированную кубическую решетку, но с большими по сравнению с ним параметрами, δ-феррит парамагнитен.
Аустенит – твердый раствор внедрения углерода в γ-железе. Решетка аустенита – гранецентрированный куб (ГЦК). Атомы углерода располагаются в крупных октаэдрических пустотах решетки (рис. 4.5).
Растворимость углерода в аустените значительно больше, чем в феррите: 2,03 и 2,14 % при температурах эвтектического превращения, соответственно, в стабильной и метастабильной системе. При понижении температуры растворимость уменьшается до 0,69 и 0,80 % в упомянутых системах,
Материаловедение. Учеб. пособие |
-169- |
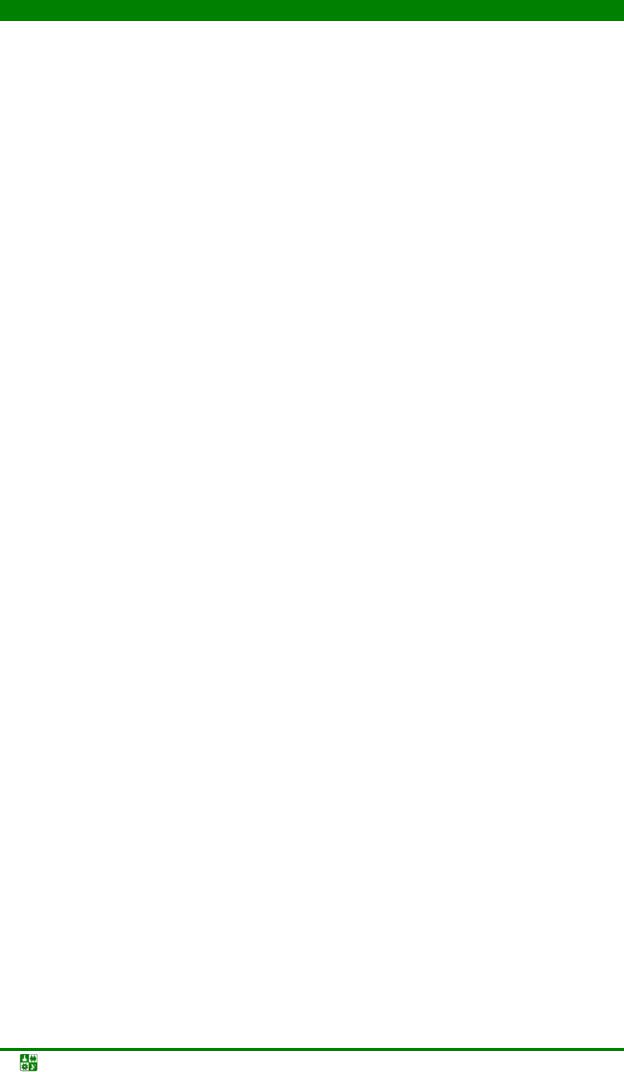
РАЗДЕЛ II. МАТЕРИАЛОВЕДЕНИЕ СТАЛЕЙ И ЧУГУНОВ
Глава 4. Стали, сплавы системы железо–углерод. Маркировка, структура, свойства сплавов
что соответствует температурам эвтектоидного превращения в той и другой системах.
Аустенит в структуре выявляется так же, как и феррит, в виде сравнительно равноосных полиэдров, но отличается от него значительным количеством двойников в теле зерна. Аустенит – парамагнитная составляющая во всем температурном интервале его существования. Аустенит мягок, хотя тверже феррита (HB = 200–250). Он пластичен (относительное удлинение 40–50 % и выше). Превращение феррита и феррито-цементитной смеси в аустенит сопровождается уменьшением объема.
Структурное состояние аустенита (А) в железоуглеродистых сплавах аналогично ферриту: он может быть единственной структурной составляющей в сплаве; составлять основу сплава; входить в него как остаточный аустенит; содержаться в виде фазовой составляющей в составе более сложной структурной составляющей – эвтектической аустенито-цементитной смеси (ледебурита), существующей при температурах выше эвтектоидной линии на диаграмме железо–углерод.
Цементит – метастабильное соединение железа с углеродом, соответствующее формуле Fe3C. Цементит имеет сложную орторомбическую решетку (рис. 4.6), основа которой представляет собой трехгранную, слегка искаженную призму, образованную шестью атомами железа.
Часть атомов железа имеет 11 соседних атомов железа, а часть – 12. Пустоты заполняются атомами углерода. В этом структура цементита близка по своему строению к структуре аустенита, а также к плотнейшей гексагональной модификации ε-железа.
Цементит – соединение практически постоянного состава. Растворимость железа в цементите имеет место, но ее величина очень мала и практически незначима. Цементит при повышении температуры сравнительно легко разлагается на железо (аустенит или феррит) и графит. Это свойство цементита лежит в основе явления графитизации и используется для получения серых и ковких чугунов. Цементит хрупок, очень тверд (НВ около 800), слабо магнитен до температуры 210 °С. Выше этой температуры цементит парамагнитен.
Рис. 4.6. Позиции ионов углерода и железа в структуре цементита
Материаловедение. Учеб. пособие |
-170- |
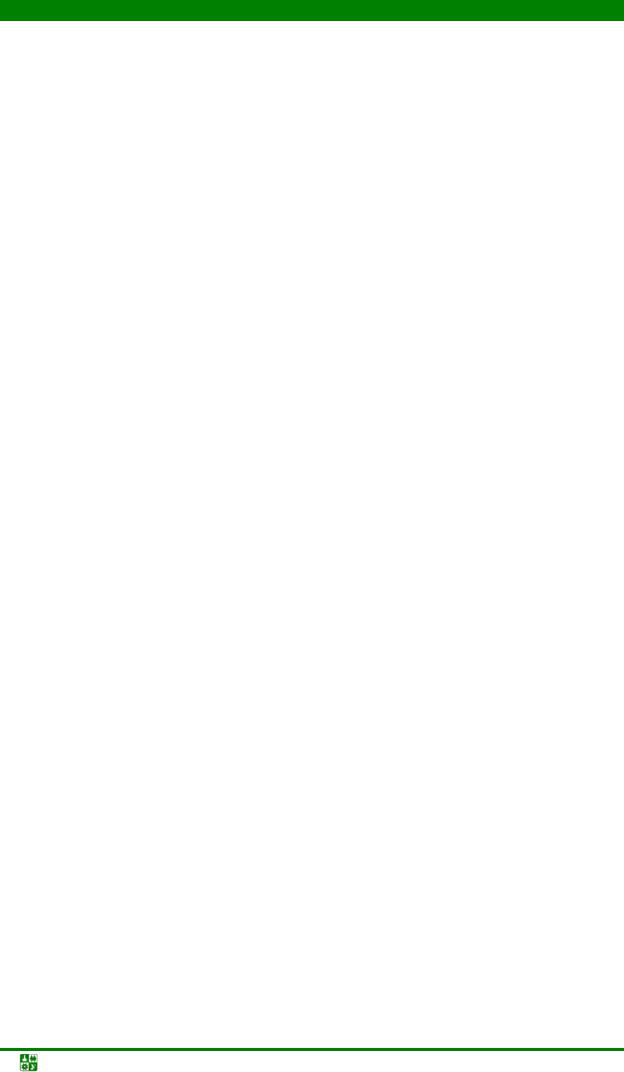
РАЗДЕЛ II. МАТЕРИАЛОВЕДЕНИЕ СТАЛЕЙ И ЧУГУНОВ
Глава 4. Стали, сплавы системы железо–углерод. Маркировка, структура, свойства сплавов
Структурное состояние цементита определяется в основном типом превращения, при котором он образуется. Различают первичный цементит (ЦI), который представляет собой крупные игольчатые кристаллы, образующиеся при кристаллизации непосредственно из жидкости в заэвтектическом белом чугуне. Вторичный цементит (ЦII) выделяется в заэвтектоидных сталях и доэвтектических чугунах в основном в виде сетки по границам зерен аустенита, а также в ряде случаев в виде равномерно распределенных по объему аустенитного зерна скогулированных частиц или игл. Вторичный цементит – это избыточная фаза в железоуглеродистых сплавах, выделяющаяся из аустенита при охлаждении в результате уменьшения растворимости углерода в аустените при понижении температуры.
Выделение третичного цементита (ЦIII) характерно для технического железа и малоуглеродистой стали. Выделяется третичный цементит из феррита в результате уменьшения растворимости углерода в феррите с понижением температуры от 727 °С до комнатной температуры. Третичный цементит в структуре железа и малоуглеродистой стали наблюдается в виде тонких прожилок по границам зерен феррита. Такие выделения третичного цементита охрупчивают железо и малоуглеродистые стали. Поэтому такие сплавы подвергают термической обработке с целью изменения структурного состояния третичного цементита. Желательное его положение в структуре сплава – равномерно рассредоточенные выделения в объеме ферритных зерен. Этого добиваются путем закалки и последующего старения.
Кроме того, цементит в качестве фазовой составляющей входит в состав сложных двухфазных структурных составляющих в железоуглеродистых сплавах – перлита и ледебурита. В этом случае такой цементит назы-
вают эвтектоидным или эвтектическим (Цэ) соответственно.
Графит – важнейшая фазовая и структурная составляющая (Г) серых и ковких чугунов, обусловливающая их малую усадку при кристаллизации, высокие антифрикционные свойства, малую изнашиваемость, большое внутреннее трение, обеспечивающее уменьшение вибраций, и ряд других полезных свойств. Графит – гексагональная модификация углерода. При нормальном давлении графит является стабильной составляющей до температур око-
ло 4 000 °С.
В решетке графита атомы расположены слоями с гексагональной симметрией (рис. 4.7). В первом и третьем слоях атомы расположены друг над другом. Во втором (среднем) слое атомы сдвинуты вдоль наибольшей диагонали шестигранника на величину параметра решетки (длину стороны шестигранника). Расстояние между слоями (3,35 кХ) значительно больше, чем расстояния между соседними атомами в гексагональном слое. Из-за легкой подвижности слабо связанных гексагональных слоев графит является наименее прочной фазой железоуглеродистых сплавов.
Материаловедение. Учеб. пособие |
-171- |
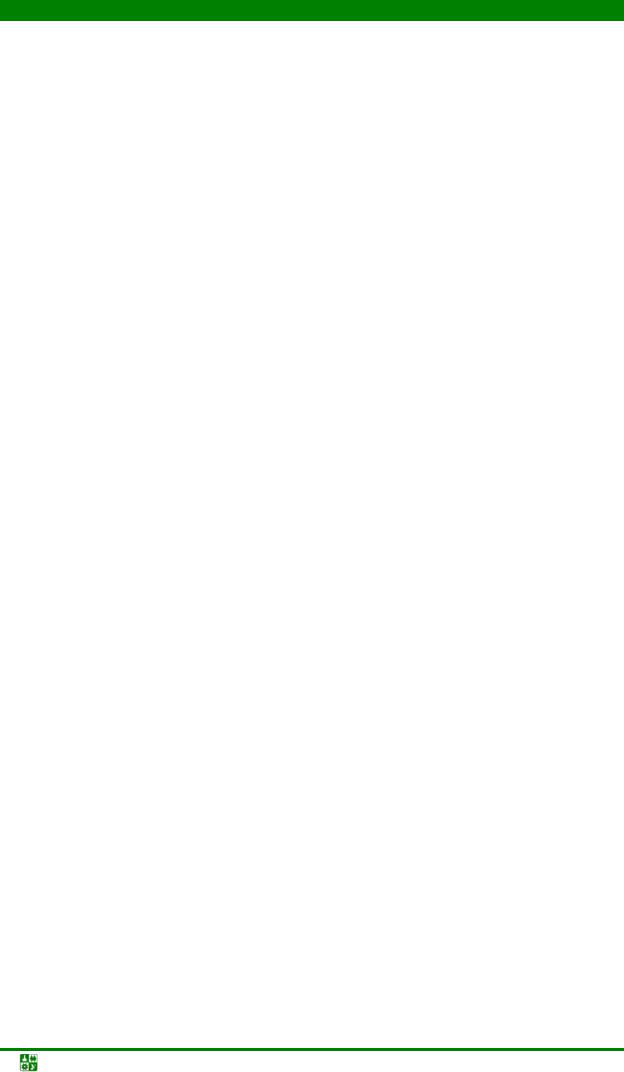
РАЗДЕЛ II. МАТЕРИАЛОВЕДЕНИЕ СТАЛЕЙ И ЧУГУНОВ
Глава 4. Стали, сплавы системы железо–углерод. Маркировка, структура, свойства сплавов
Рис. 4.7. Расположение атомов углерода в слоистой гексагональной решетке графита: сплошные линии – расположение атомов и связей в 1-м и 3-м гексагональных слоях, штриховые – в среднем, 2-м слое
Графит в структуре железоуглеродистых сплавов находится либо в виде избыточной фазы (в заэвтектическом сером чугуне), либо в качестве фазовой составляющей, входящей в состав аустенито-графитной эвтектики. Графит имеет форму разветвленных крабовидных включений. Эвтектический графит отличается от первичного меньшими размерами и большей разветвленностью.
После модифицирования жидкого чугуна магнием и некоторыми другими элементами, а также после отжига белого чугуна на ковкий в структуре можно наблюдать глобулярный графит. Эта форма графита обеспечивает получение повышенной прочности и пластичности чугуна.
Все описанные фазовые составляющие могут одновременно быть и структурными составляющими, если они в структуре сплава находятся в виде избыточных фаз или составляют основу структуры сплава.
Кроме однофазных структурных составляющих в железоуглеродистых сплавах имеют место и сложные двухфазные: перлит, ледебурит, графитоаустенитная эвтектика и феррито-графитный эвтектоид.
Перлит – это эвтектоидная физико-химическая смесь двух фаз: феррита и цементита, образовавшаяся в метастабильной системе железо–углерод за счет диффузионного расслоения аустенита по эвтектоидной реакции. Перлит образуется при переохлаждении аустенита ниже линии PSK диаграммы желе- зо–углерод. Строение перлита определяется величиной переохлаждения, при котором происходит распад.
При малом переохлаждении (на 20–30 °С ниже линии эвтектоидного превращения) образуется зернистый перлит. Зернистый перлит представляет собой феррито-цементитную структуру, в которой основой является феррит, а по его объему статистически равномерно распределены зернистые, близкие к сферическим, включения цементита.
При большем переохлаждении образуется структура пластинчатого перлита, состоящего из регулярно чередующихся пластин цементита и феррита, причем пластины феррита примерно в 7 раз толще пластин цементита.
Абсолютные значения толщины цементитных и ферритных пластин, величина расстояния между одноименными пластинами в составе эвтектоидной смеси, называемая межпластиночным расстоянием и характеризующая степень дисперсности структуры, определяются степенью переохлаждения
Материаловедение. Учеб. пособие |
-172- |
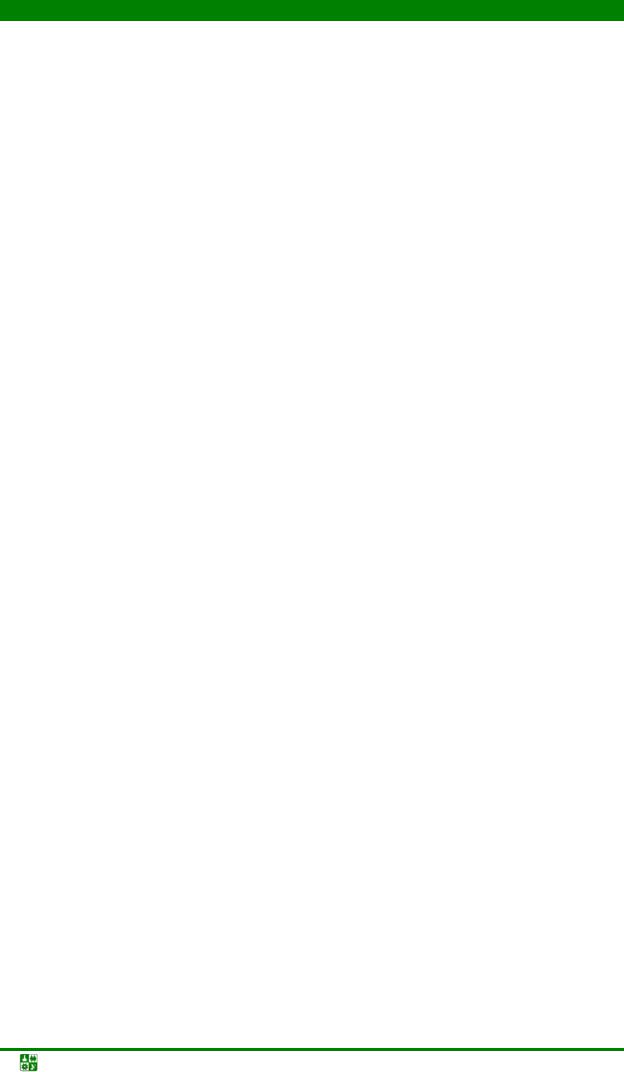
РАЗДЕЛ II. МАТЕРИАЛОВЕДЕНИЕ СТАЛЕЙ И ЧУГУНОВ
Глава 4. Стали, сплавы системы железо–углерод. Маркировка, структура, свойства сплавов
аустенита ниже равновесной температуры эвтектоидной реакции. Чем больше степень переохлаждения, тем выше дисперсность феррито-цементитной эвтектоидной смеси. Высокодисперсные феррито-цементитные смеси носят названия сорбит и троостит. Троостит – наиболее дисперсная ферритоцементитная смесь.
Перлит присутствует в структуре сталей и чугунов. Количество перлита растет в доэвтектоидных сталях с увеличением содержания углерода от 0,02 до 0,8 %. Эвтектоидная сталь имеет чисто перлитную структуру (100 % перлита). Дальнейшее увеличение содержания углерода в стали, соответствующее переходу к заэвтектоидным сталям, а далее – к чугунам, сопровождается уменьшением доли перлита в структуре за счет появления и увеличения количества вторичного, эвтектического и, наконец, первичного цементита.
Перлит в малоуглеродистых сталях появляется сначала в виде отдельных включений между зернами феррита, затем при увеличении его количества он постепенно занимает в структуре все большее поле зрения на поверхности шлифа. Пока перлита в структуре мало, строение его не выявляется при малых и средних увеличениях оптического микроскопа. В эвтектоидной и заэвтектоидной сталях пластинчатое строение его выявляется уже при небольших увеличениях (×100–200). В структуре чугуна перлит находится как в виде избыточных колонийных структурных составляющих – продуктов распада избыточного аустенита, так и в составе ледебурита. Механические свойства перлита определяются его структурным состоянием. Расчет твердости перлита по правилу аддитивности с учетом известных значений твердости феррита и цементита дает величину 150–180 НВ. Экспериментально определенные значения твердости пластинчатого перлита, сорбита и троостита, соответственно, равны 170–230, 230–330 и 330–400 НВ. Таким образом, можно видеть, что чем выше степень дисперсности феррито-цементитной смеси, тем выше его твердость.
Ледебурит – эвтектическая физико-химическая смесь аустенита и цементита, образующаяся в результате эвтектической кристаллизации из жидкости, содержащей 4,3 % С.
Ледебурит представляет собой колонийную структуру, основу которой составляют пластины цементита, проросшие разветвленными кристаллами аустенита. Ветви аустенита в составе ледебурита располагаются регулярно по всему объему эвтектической цементитной пластины и имеют форму стержней примерно цилиндрической конфигурации. На шлифе колония ледебурита, в зависимости от направления поверхности шлифа относительно аустенитных ветвей, может выглядеть либо в виде «зернистой» смеси при поперечном сечении колонии, либо «пластинчатой» – при продольном сечении. При сечении колонии под углом к плоскости базиса цементита, сечения аустенитных ветвей в составе ледебурита эллиптического характера.
Кроме колонийного (сотового) ледебурита, эвтектическая смесь аустенита и цементита может встречаться в виде пластинчатой эвтектики, представляющей собой пакет тонких цементитных пластинок, разделенных аустенитом. Такие пакеты образованы двумя переплетенными кристаллами це-
Материаловедение. Учеб. пособие |
-173- |
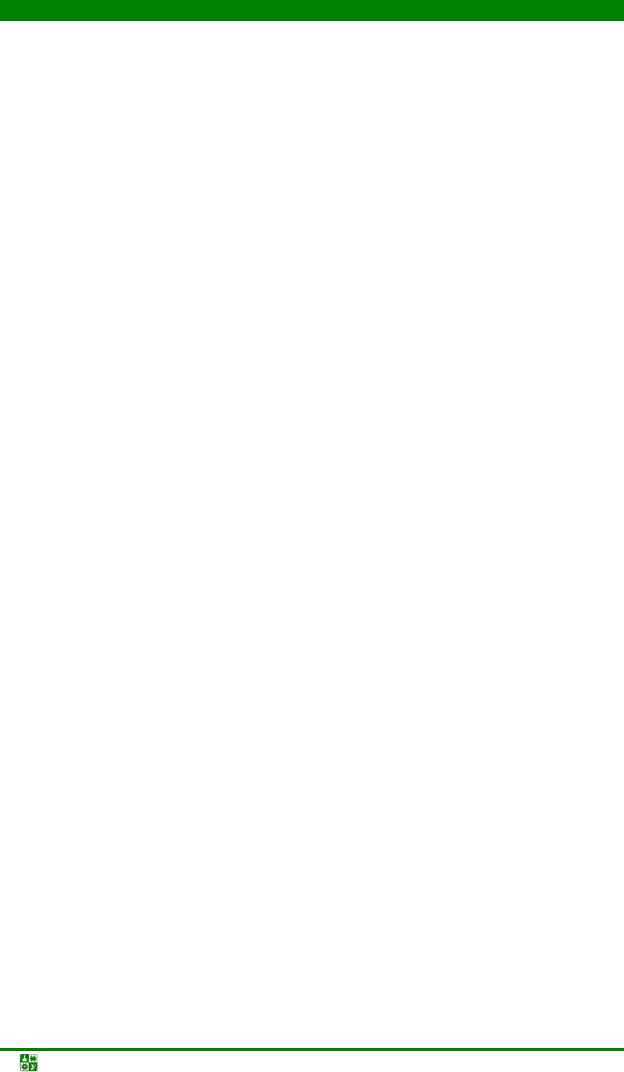
РАЗДЕЛ II. МАТЕРИАЛОВЕДЕНИЕ СТАЛЕЙ И ЧУГУНОВ
Глава 4. Стали, сплавы системы железо–углерод. Маркировка, структура, свойства сплавов
ментита и аустенита. Вероятность образования пластинчатого ледебурита увеличивается с ростом степени переохлаждения жидкости при кристаллизации. При этом увеличивается доля пластинчатого ледебурита в структуре белого чугуна. Чаще всего пакет пластинчатого ледебурита составляет основу, на которой зарождается и растет колония сотового ледебурита.
При очень больших скоростях охлаждения весь ледебурит может оказаться пластинчатым. В этом случае цементит разветвляется, приобретая вид веерообразных колоний. При еще больших скоростях охлаждения появляются сферолитные колонии.
Ледебурит, состоящий из эвтектической смеси аустенита и цементита, устойчив в температурном интервале от эвтектической до эвтектоидной линии на диаграмме железо–углерод. При понижении температуры ниже 727 °С аустенит в составе ледебурита претерпевает эвтектоидное превращение, в результате чего при комнатной температуре ледебурит представляет собой эвтектическую смесь перлита с цементитом.
Строение перлита в ледебурите такое же, как и в сплавах с меньшим содержанием углерода (сталях).
Ледебурит, как и цементит, образующий его основу, тверд, износостоек и обладает практически нулевой пластичностью. Эти свойства ледебурита лежат в основе использования такой структуры в белых чугунах, используемых в качестве одних из наиболее износостойких материалов.
Аустенито-графитная эвтектика образуется в стабильной системе железо–углерод и представляет собой смесь кристаллов графита, сформировавшуюся при одновременном выделении из жидкости состава 4,25 % углерода обеих фазовых составляющих. При малых степенях переохлаждения графит эвтектики имеет, как и первичный графит, разветвленную пластинчатую форму. Увеличение скорости охлаждения приводит к расщеплению графитных пластин и образованию сферических кристаллов. Эвтектическая ау- стенито-графитная структура мало отличается от выделения первичных кристаллов графита. Главное различие этих структур заключается в размере графитных включений. Они в эвтектике мельче первичных кристаллов.
Феррито-графитный эвтектоид – продукт эвтектоидного распада аустенита, содержащего 0,69 % углерода, который реализуется в условиях очень медленного охлаждения при температурах ниже 738 °С.
Феррито-графитный эвтектоид – дисперсная смесь феррита, составляющего основу структуры сплава, и дисперсных разветвленных или сферических графитных частиц, распределенных в феррите статистически равномерно. Однако в большинстве случаев эвтектоидный графит при распаде аустенита осаждается на ранее образовавшихся первичных и эвтектических графитных кристаллах. Эвтектоидное превращение с образованием ферритографитного эвтектоида используется при термической обработке чугунов и графитизированной стали для получения феррито-графитной структуры, обладающей хорошими антифрикционными свойствами при сохранении достаточно высокой пластичности сплавов.
Материаловедение. Учеб. пособие |
-174- |

РАЗДЕЛ II. МАТЕРИАЛОВЕДЕНИЕ СТАЛЕЙ И ЧУГУНОВ
Глава 4. Стали, сплавы системы железо–углерод. Маркировка, структура, свойства сплавов
4.4.Фазовыеиструктурныепревращения
вдиаграммежелезо−углерод
Фазовое и структурное состояния сплавов стабильной и метастабильной систем железо–углерод описывается диаграммами (см. рис. 4.1, рис. 4.2,
рис. 4.3).
При исследовании этих диаграмм необходимо иметь в виду, что в системах существует однофазные, двухфазные и трехфазные равновесия.
Коднофазным относятся: область жидкого раствора, расположенная выше линии ликвидус АВСD и АВС′D′, соответственно, в метастабильной и стабильной системах; три области твердых растворов – δ-феррита, аустенита
иα-феррита, примыкающих к ординате чистого железа, соответственно, в интервалах температур от 1 539 до 1 392, от 1 392 до 911°С и ниже 911°С; ордината цементита в метастабильной системе при содержании углерода 6,67 %
иобласть гомогенности графита при 100 % С.
Кдвухфазным областям относятся практически все остальные области диаграммы, соответствующие кристаллизации в интервале температур от линии ликвидус до линии солидус, области полной и частичной фазовой перекристаллизации в твердом состоянии. Фазовый состав двухфазных областей определяется как сумма составляющих, ограничивающих справа и слева данную фазовую область.
Участки трехфазного равновесия в диаграмме – это горизонтальные линии, соответствующие развитию перитектического превращения (линия HIB), эвтектического превращения в метастабильной и стабильной системах (соот-
ветственно, линии ECF и E′C′F), а также эвтектоидного превращения, соответственно, в метастабильной и стабильной системах (линии PSK и P′S′K′).
В трехфазных равновесиях участвуют те фазы либо однородные структурные составляющие, области которых выходят своими точками на соответствующую горизонталь диаграммы. При этом состав фаз, участвующих в трехфазных реакциях, определяется этими точками.
Например, перитектическому превращению в метастабильной системе соответствует трехфазное равновесие между фазами δ, γ и L; эвтектическому – между фазами γ, Fe3C, L; эвтектоидному – между α, Fe3C, γ.
При описании фазовых областей в системах приняты следующие обозначения: жидкий раствор – L, высокотемпературный феррит – δ, низкотемпературный феррит – α, аустенит – γ, цементит – Fe3C, графит – Г.
При описании структурного состава на диаграммах используются обозначения, отличные от обозначения фазового состава: жидкий раствор – Ж, высокотемпературный феррит – Фδ, низкотемпературный феррит – Ф, аустенит – А, цементит первичный – Ц1, вторичный – Ц2, третичный – Ц3, эвтектический и эвтектоидный Ц или Цэ, перлит – П, ледебурит – Л. Структурный состав ледебурита при температуре выше 727 °С – (А + Ц)э, а при температурах ниже 727 °С – (П + Ц)э.
Материаловедение. Учеб. пособие |
-175- |

РАЗДЕЛ II. МАТЕРИАЛОВЕДЕНИЕ СТАЛЕЙ И ЧУГУНОВ
Глава 4. Стали, сплавы системы железо–углерод. Маркировка, структура, свойства сплавов
Структурный состав в ряде областей диаграммы железо–углерод совпадает с фазовым составом. Такими областями являются однофазные области, а также двухфазные области, соответствующие твердо-жидкому состоянию и области δ + γ и α + γ.
Фазовые области γ + Fe3C и α + Fe3C характеризуются широким интервалом структур в зависимости от содержания углерода в сплавах. В двухфазной области γ + Fe3C можно выделить следующие структурные участки диаграммы: область аустенита с избыточным (вторичным) цементитом, соответствующую структурному состоянию заэвтектоидных сталей; область доэвтектического чугуна, описывающая его структуру тремя структурными составляющими: аустенитом, ледебуритом и цементитом вторичным; эвтектический чугун, содержащий одну структурную составляющую – ледебурит, и область заэвтектического чугуна со структурным составом: ледебурит плюс цементит первичный.
Сплаву, содержащему 6,67 % С, соответствует однофазная структура – цементит. Однако необходимо помнить, что кристаллизация сплава с содержанием углерода 6,67 % даже в условиях очень быстрого охлаждения с температуры плавления не обеспечивает получения 100 % цементита. Часть его распадается на железо (аустенит) и графит. В двухфазной области α + Fe3C еще большее количество структурных областей. Это области: технического железа, доэвтектоидной, эвтектоидной, заэвтектоидной стали, доэвтектического, эвтектического и заэвтектического чугуна.
Области технического железа соответствует структура феррита с избыточным (третичным) цементитом. Области доэвтектоидной стали – структура феррито-перлитная, эвтектоидной стали – 100 % перлита, заэвтектоидной стали – перлит с вторичным цементитом.
Структурным областям доэвтектического, эвтектического и заэвтектического чугунов отвечают последовательно следующие: доэвтектическому – перлит, вторичный цементит и ледебурит, количество которого увеличивается по мере приближения к эвтектической концентрации; в эвтектическом чугуне 100 % ледебурита; заэвтектическом – ледебурит с кристаллами первичного цементита.
Встабильной системе железо-углерод в двухфазных областях α + Г и
γ+ Г нет такого многообразия структурных областей. Практически все сплавы с содержанием углерода до 6 % при температуре выше 738 °С имеют близкие структуры, соответствующие структурному составу А + Г и при
температуре ниже 738 °С отличающиеся лишь количеством и дисперсностью графитных включений.
Структура чугунов усложняется в случае применения специальных видов термической обработки, а также в результате ускоренной кристаллизации серых чугунов, что приводит к формированию структуры частично по стабильной, а частично – по метастабильной системе. В этом случае могут быть сформированы структуры феррит + графит, феррит + перлит + графит, зернистый перлит + графит и др. Кроме того, неодинаковая скорость кристалли-
Материаловедение. Учеб. пособие |
-176- |
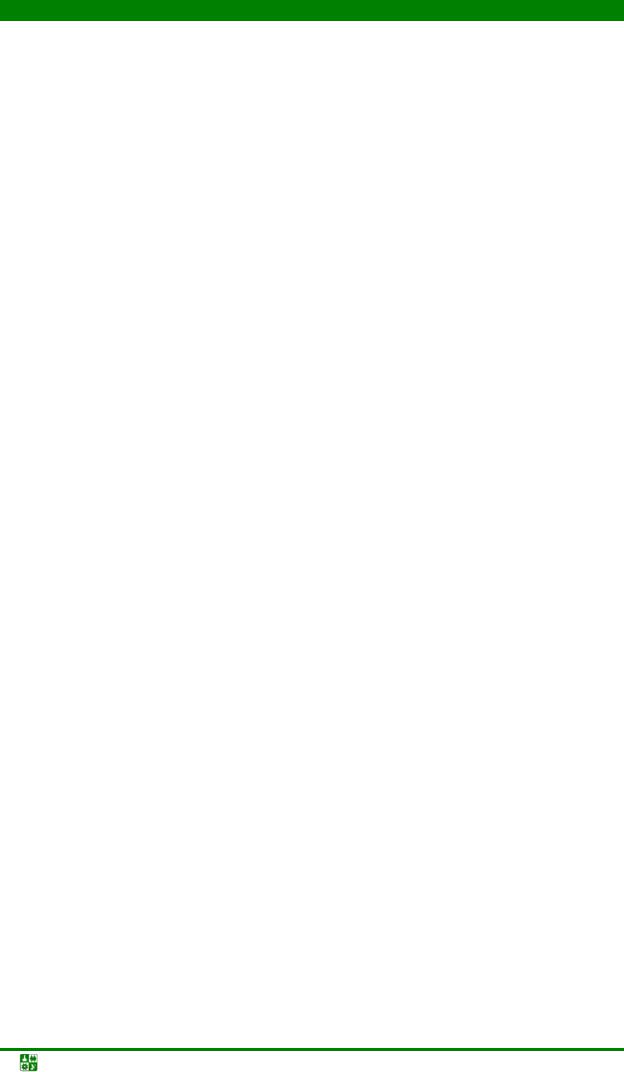
РАЗДЕЛ II. МАТЕРИАЛОВЕДЕНИЕ СТАЛЕЙ И ЧУГУНОВ
Глава 4. Стали, сплавы системы железо–углерод. Маркировка, структура, свойства сплавов
зации отливок на поверхности и внутри объема металла может привести к получению разных структур по сечению одной и той же отливки.
4.5. Условияпревращениявжелезоуглеродистыхсплавах
Структура железоуглеродистых сплавов формируется как при кристаллизации, так и в результате фазовых превращений в твердом состоянии. Конечная структура сплавов в большинстве случаев является результатом целой цепи превращений, протекающих в жидком, твердо-жидком и твердом состоянии.
Диаграмма состояния железо–углерод дает возможность проследить за изменениями структурного состояния сплавов как во всем интервале температур от жидкого состояния до комнатной температуры, так и в более узких температурных интервалах, характерных для той или иной горячей обработки сплава.
Фазовые превращения в сплавах и соответствующие им качественные или количественные структурные изменения происходят либо при постоянной температуре (t = const), либо в интервале температур (∆t). При постоянной температуре происходят кристаллизация и плавление чистого железа, перитектическая и эвтектическая кристаллизация, а также соответствующие им процессы плавления по обратному перитектическому и эвтектическому механизму, прямое и обратное эвтектоидное превращение. Во всех этих случаях в состоянии равновесия находится число фаз, на единицу больше числа компонентов, составляющих систему, что делает перечисленные превращения нонвариантными.
В интервале температур протекают такие структурные изменения, при которых в состоянии равновесия в конкретных условиях находится количество фаз, равное числу взаимодействующих компонентов. Для большинства превращений в системе железо–углерод таким условиям соответствуют две фазы (моновариантная система).
Важнейшими внешними графическими признаками, характеризующими на диаграмме состояния протекание фазовых и структурных изменений в сплавах, является либо пересечение линий диаграммы линиями фигуративных точек сплава, либо изменение положения фигуративной точки в двухфазной области диаграммы.
Фазовые и структурные изменения можно наблюдать в изучаемой системе и в изотермических условиях, если за счет каких-либо внешних воздействий на сплав в нем будут происходить изменения химического состава.
Как уже указывалось, изменения фазового и структурного состояния сплавов могут быть как качественными, так и количественными. Они могут протекать во всем объеме сплава либо только в части объема исходной фазы. Наконец, участвовать в превращении могут одновременно все фазы и структурные составляющие сплава или только некоторые из них.
Материаловедение. Учеб. пособие |
-177- |
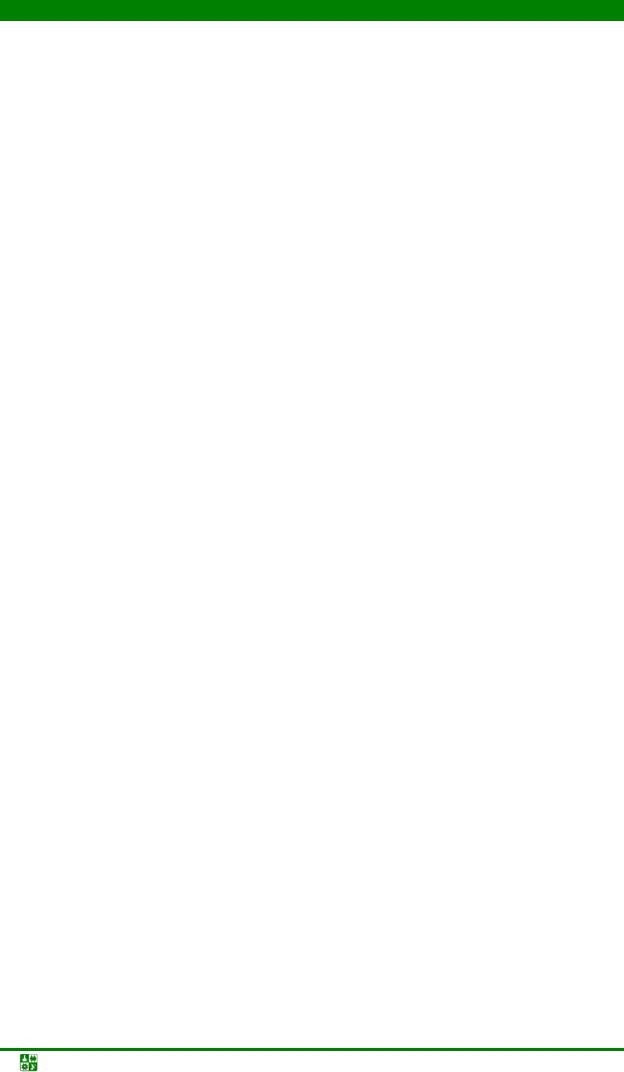
РАЗДЕЛ II. МАТЕРИАЛОВЕДЕНИЕ СТАЛЕЙ И ЧУГУНОВ
Глава 4. Стали, сплавы системы железо–углерод. Маркировка, структура, свойства сплавов
Внастоящем пособии принята табличная форма описания фазовых и структурных превращений, протекающих в сплавах при охлаждении, которая включает в себя сведения о протекающих процессах кристаллизации и фазовых превращениях в твердом состоянии в широком интервале температур: от температуры жидкого состояния до комнатной температуры. Такая форма записи цепочек фазовых и структурных превращений дает значительные преимущества перед традиционными формами записи. Она позволяет увидеть роль каждой фазовой составляющей в изменении структуры сплава при кристаллизации и фазовых превращениях, участие каждой из них в конкретных фазовых превращениях, а также в комплексе проследить за всем ходом процессов, формирующих конечную структуру сплава.
Вверхней строке таблицы указываются температурные условия развития превращения, которые записываются двумя обозначениями: t = const и ∆t, что соответственно обозначает, что превращение протекает в изотермических условиях или при понижении температуры. Здесь же указывается обозначение линии или характерной точки диаграммы железо–углерод, с которой связано рассматриваемое превращение.
Вследующей строке каждой таблицы записаны фазовые составляющие сплава в их структурном положении в сплаве при данных условиях, в такой последовательности, что каждая начальная графа таблицы описывает исходное состояние сплава, а каждая последующая – результат превращения. Стрелками показано схематическое изображение взаимосвязи взаимодействующих фазовых составляющих в процессе превращения, что указывает на превращение одной фазы в другую, на взаимодействие двух фаз, разделение одной фазы на две, выделение фазы или растворение одной фазы в другой и т.д.
Внижней строке таблицы указываются изменения структуры, которыми сопровождаются рассматриваемые фазовые превращения. Анализ фазовых и структурных изменений в любом сплаве системы железо–углерод по структурным цепочкам, приводимым в таблицах для каждого сплава, необходимо вести при наличии соответствующей фазовой диаграммы.
4.5.1. Фазовыеиструктурныепревращениявтехническомжелезе
Фазовое состояние и формирование структуры технического железа и сталей описывается метастабильной диаграммой Fe–Fe3C (см. рис. 4.3).
Чистое железо кристаллизуется при постоянной температуре (т. А на диаграмме железо–углерод). Кроме того, при понижении температуры, в нем развиваются 2 полиморфных превращения Fe-δ → Fe-γ и Fe-γ → Fe-α, соответственно, при температурах критических точек, соответствующих точкам N и G на диаграмме железо–углерод. Схема формирования структуры выглядит в виде линейной цепи процессов (табл. 4.1).
Материаловедение. Учеб. пособие |
-178- |
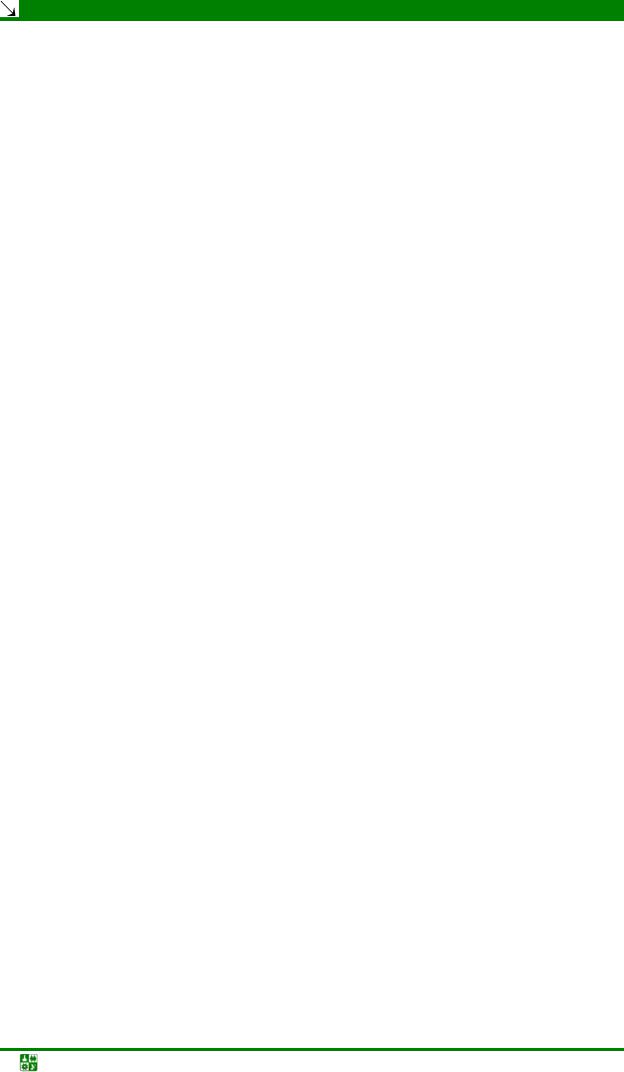
РАЗДЕЛ II. МАТЕРИАЛОВЕДЕНИЕ СТАЛЕЙ И ЧУГУНОВ
Глава 4. Стали, сплавы системы железо–углерод. Маркировка, структура, свойства сплавов
Таблица 4.1
Схема фазовых и структурных превращений в чистом железе
Условия развития превращения |
t = const в т. A |
t = const в т. N |
t = const в т. G |
||||
|
|
|
|
|
|
|
|
Фазовый состав |
L |
→ |
δ |
→ |
γ |
→ |
α |
Структура |
Ж |
→ |
Feδ |
→ |
Feγ |
→ |
Feα |
Техническое железо отличается от чистого железа тем, что кристаллизация и фазовые превращения развиваются по типу формирования структуры твердых растворов. Каждое из указанных превращений развивается в интервале температур (табл. 4.2). Конечная структура технического железа (сплава с содержанием углерода до 0,02 %): феррит и третичный цементит (рис. 4.8).
Таблица 4.2
Схема фазовых и структурных превращений в техническом железе
Условия развития |
|
t ниже |
|
t ниже |
|
t ниже |
|
t ниже |
|||||
превращения |
линии AВ |
линии NН |
линии GS |
линии PQ |
|||||||||
Фазовый |
L |
→ |
|
δ |
→ |
|
γ |
→ |
|
α |
→ |
|
α |
состав |
|
|
|
|
|
|
|
|
|
|
|
|
+ |
|
|
|
|
|
|
|
|
|
|
|
|
|
Fe3Cш |
Структура |
Ж |
→ |
|
Фδ |
→ |
|
А |
→ |
|
Ф |
→ |
|
Ф |
|
|
|
|
|
|
|
|
|
|
|
|
|
+ |
|
|
|
|
|
|
|
|
|
|
|
|
|
Цш |
Рис. 4.8. Микроструктура технического же- |
|
|
леза: а – чистое железо; б – технически чис- |
а |
б |
тое железо (феррит + третичный цементит) |
В техническом железе за счет полиморфных превращений при охлаждении ниже линии NH идет образование аустенита, а затем (ниже линии GS) феррита. При охлаждении до температур ниже линии PQ растворимость углерода в феррите уменьшается, и поэтому из феррита выделяется третичный цементит Fe3CIII в виде тонких светлых прожилок по границам светлых зерен феррита (рис. 4.8).
Материаловедение. Учеб. пособие |
-179- |
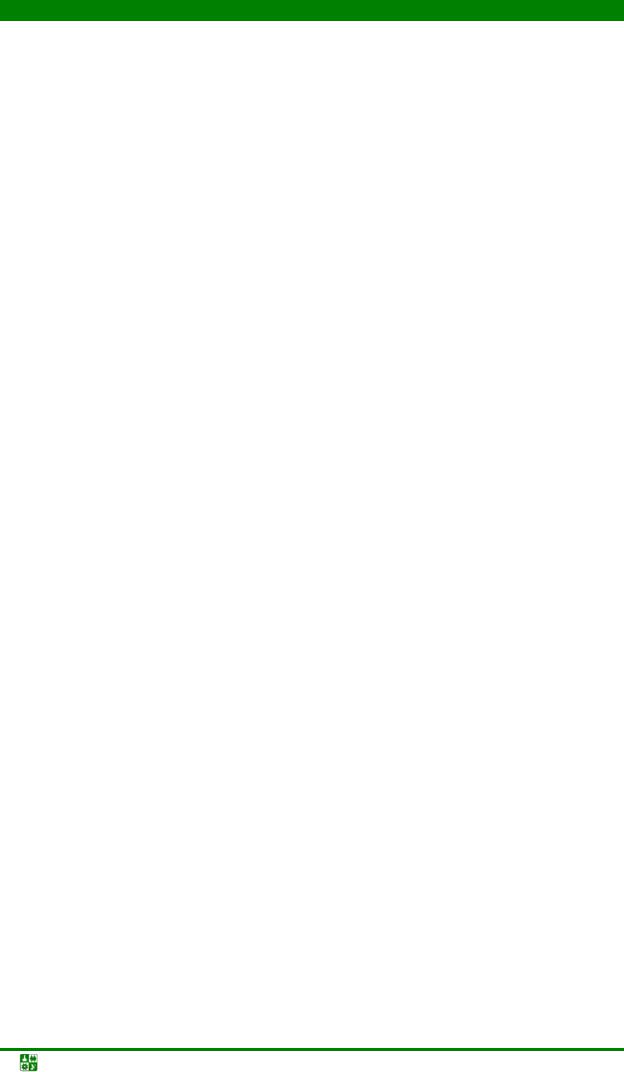
РАЗДЕЛ II. МАТЕРИАЛОВЕДЕНИЕ СТАЛЕЙ И ЧУГУНОВ
Глава 4. Стали, сплавы системы железо–углерод. Маркировка, структура, свойства сплавов
Если в техническом железе содержание углерода менее 0,006 %, то оно имеет структуру феррита. Выделения цементита по границам очень вредны, т.к. придают материалу хрупкость.
4.5.2. Фазовыеиструктурныепревращениявуглеродистыхсталях
Если в сталях содержание углерода находится в пределах: 0,02 < C < 0,8 %, то их называют доэвтектоидными. Типичной конечной структурой доэвтектоидной стали является смесь феррита и перлита (рис. 4.9).
Все стали, как и техническое железо, кристаллизуются по типу твердого раствора. При этом в зависимости от содержания углерода при кристаллизации образуется δ-феррит (до 0,1 % С) или аустенит (от 0,1 до 2,14 % С). В доэвтектоидных сталях при изменении содержания углерода от 0,1 до 0,51 % мас. идет перитектическое превращение (1 496 °С), завершающееся образованием аустенита (0,16 % С), аустенита с избыточным δ-ферритом (0,1 < C < 0,16), аустенита и избыточной жидкостью (0,16 < C < 0,51). Если содержание углерода в стали изменяется от 0,51 до 2,14 %, то первично кристаллизуется аустенит. После завершения всех этапов кристаллизации ниже линии солидус в техническом железе и стали формируется однофазная аустенитная структура.
а |
б |
в |
Рис. 4.9. Схема микроструктуры доэвтектоидной стали при содержании углерода, %: а – 0,15; б – 0,4; в – 0,65
В зависимости от содержания углерода в стали, формирование ее структуры при охлаждении происходит по цепочкам превращений, отраженным в табл. 4.3, табл. 4.4, табл. 4.5, табл. 4.6, табл. 4.7.
Материаловедение. Учеб. пособие |
-180- |
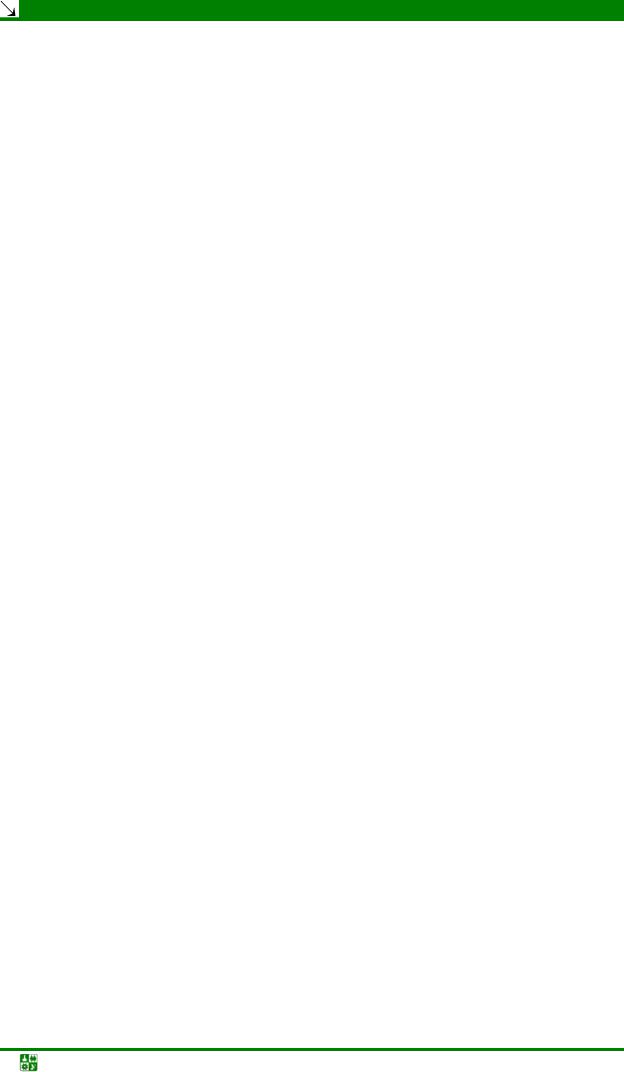
РАЗДЕЛ II. МАТЕРИАЛОВЕДЕНИЕ СТАЛЕЙ И ЧУГУНОВ
Глава 4. Стали, сплавы системы железо–углерод. Маркировка, структура, свойства сплавов
Таблица 4.3
Схема фазовых и структурных превращений в стали с содержанием 0,02–0,1 % С
Условия разви- |
t ниже |
t ниже |
t ниже |
|
t = const |
|
|
t ниже |
||||
тия превраще- |
|
|
|
|||||||||
линии AВ |
линии NН |
линии GS |
на линии PSK |
|
линии PQ |
|||||||
ния |
|
|
|
|
|
|
|
|
|
|
|
|
Фазовый |
L |
→ |
δ |
→ |
γ |
→ |
γ |
→ |
(α + Fe3C)э |
→ |
|
(α + Fe3C)э |
состав |
|
|
|
|
|
|
+ |
|
+ |
|
|
+ |
|
|
|
|
|
|
|
α |
→ |
α |
→ |
|
α |
|
|
|
|
|
|
|
|
|
|
|
|
+ |
|
|
|
|
|
|
|
|
|
|
|
|
Fe3Cш |
Структура |
Ж |
→ |
Фδ |
→ |
А |
→ |
А + Ф |
→ |
П + Ф |
→ |
П + Ф + Цш |
Таблица 4.4
Схема фазовых и структурных превращений в стали с содержанием 0,1–0,16 % С
Условия раз- |
|
|
t ниже |
t = const |
t ниже |
t ниже |
|
t = const |
|
|
t ниже |
|||||
вития превра- |
|
линии |
на линии |
линии |
линии |
на линии |
|
|
||||||||
|
|
линии PQ |
||||||||||||||
щения |
|
|
AВ |
|
HIB |
HIB |
|
GS |
|
|
PSK |
|
||||
|
|
|
|
|
|
|
|
|
||||||||
Фазовый |
L |
→ |
|
L |
→ |
γ |
→ |
γ |
→ |
γ |
→ |
(α + Fe3C)э |
→ |
|
(α + Fe3C)э |
|
состав |
|
|
|
+ |
|
+ |
|
|
|
+ |
|
|
+ |
|
|
+ |
|
|
|
|
δ |
→ |
δ |
|
|
|
α |
→ |
|
α |
→ |
|
α |
|
|
|
|
|
|
|
|
|
|
|
|
|
|
|
|
+ |
|
|
|
|
|
|
|
|
|
|
|
|
|
|
|
|
Fe3Cш |
Структура |
Ж |
→ |
Ж + Фδ |
→ |
Ж + А |
→ |
А |
→ |
А + Ф |
→ |
|
П + Ф |
→ |
П + Ф + Цш |
Таблица 4.5
Схема фазовых и структурных превращений в стали с содержанием 0,16 % С
Условия развития |
|
t ниже |
t = const |
t ниже |
|
t = const |
|
|
t ниже |
|||||
|
|
на линии |
|
|
||||||||||
превращения |
линии AВ |
в точке I |
линии GS |
|
|
линии PQ |
||||||||
|
|
PSK |
|
|||||||||||
|
|
|
|
|
|
|
|
|
|
|
|
|
|
|
Фазовый со- |
L |
→ |
|
L |
→ |
γ |
→ |
γ |
→ |
(α + Fe3C)э |
→ |
|
(α + Fe3C)э |
|
став |
|
|
|
+ |
|
|
|
+ |
|
|
+ |
|
|
+ |
|
|
|
|
δ |
|
|
|
α |
→ |
|
α |
→ |
|
α |
|
|
|
|
|
|
|
|
|
|
|
|
|
|
+ |
|
|
|
|
|
|
|
|
|
|
|
|
|
|
Fe3Cш |
Структура |
Ж |
→ |
Ж + Фδ |
→ |
А |
→ |
А + Ф |
→ |
|
П + Ф |
→ |
П + Ф + Цш |
Материаловедение. Учеб. пособие |
-181- |
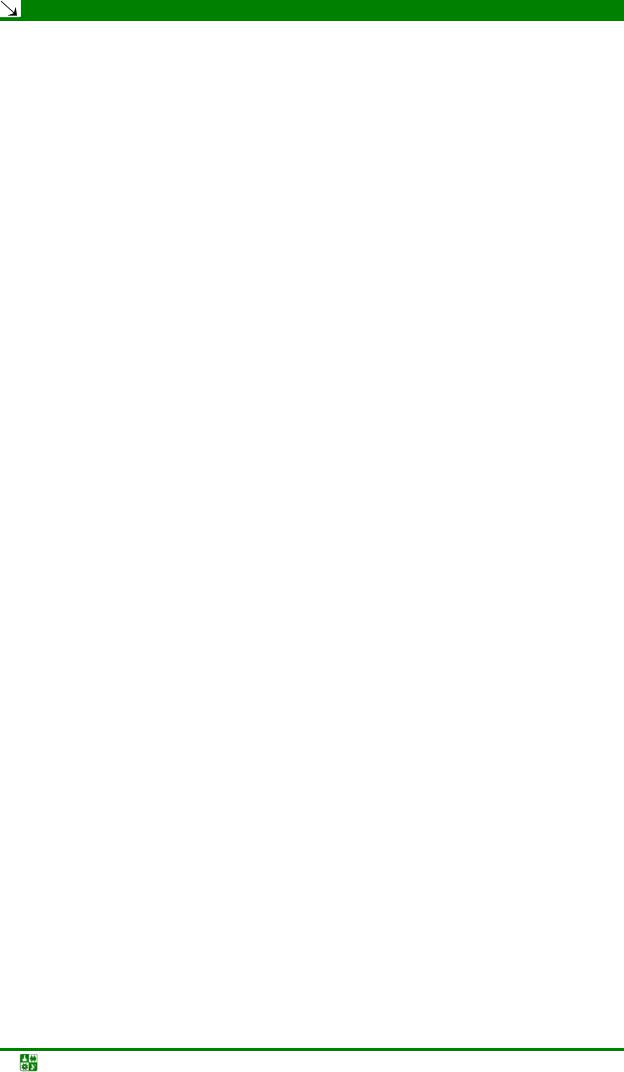
РАЗДЕЛ II. МАТЕРИАЛОВЕДЕНИЕ СТАЛЕЙ И ЧУГУНОВ
Глава 4. Стали, сплавы системы железо–углерод. Маркировка, структура, свойства сплавов
Таблица 4.6
Схема фазовых и структурных превращений в стали с содержанием 0,16–0,51 % С
Условия раз- |
t ниже |
t = const |
t ниже |
t ниже |
|
t = const |
|
|
t ниже |
||||||
вития пре- |
на линии |
|
на линии |
|
|
||||||||||
вращения |
линии AВ |
HIB |
линии HIB |
линии GS |
|
PSK |
|
линии PQ |
|||||||
Фазовый |
L |
→ |
L |
→ |
L |
|
|
|
|
|
|
|
|
|
|
состав |
|
|
+ |
|
+ |
|
|
|
|
|
|
|
|
|
|
|
|
|
δ |
→ |
γ |
→ |
γ |
→ |
γ |
→ |
(α + Fe3C)э |
→ |
(α + Fe3C)э |
||
|
|
|
|
|
|
|
|
|
|
+ |
|
+ |
|
|
+ |
|
|
|
|
|
|
|
|
|
|
α |
→ |
α |
→ |
|
α |
|
|
|
Структурно не выявляется |
|
|
|
+ |
||||||||
|
|
|
|
|
|
Fe3CIII |
|||||||||
|
|
|
|
|
|
|
|
|
|
|
|
|
|
|
|
Струк- |
Ж |
→ |
Ж + Фδ |
→ |
Ж+ А |
→ |
А |
→ |
А + Ф |
→ |
П + Ф |
→ |
П + Ф + ЦIII |
||
тура |
|
|
|
|
|
|
|
|
|
|
|
|
|
|
|
|
|
|
|
|
|
|
|
|
|
|
|
|
Таблица 4.7 |
Схема фазовых и структурных превращений в стали с содержанием 0,51–0,8 % С
Условия разви- |
|
t ниже |
t ниже ли- |
|
t = const |
t ниже линии PQ |
|||||
тия превращения |
линии BС |
нии GS |
на линии PSK |
||||||||
|
|
||||||||||
Фазовый |
L |
→ |
|
γ |
→ |
γ |
→ |
(α + Fe3C)э |
→ |
(α + Fe3C)э |
|
состав |
|
|
|
|
|
+ |
|
+ |
|
+ |
|
|
|
|
|
|
|
α |
→ |
α |
→ |
α |
|
|
|
|
|
|
|
|
|
|
|
|
|
|
|
Структурно не выявляется |
|
|
|
+ |
|||||
|
|
|
|
|
Fe3CIIII |
||||||
|
|
|
|
|
|
|
|
|
|
||
Структура |
Ж |
→ |
|
А |
→ |
А + Ф |
→ |
П + Ф |
→ |
П + Ф + ЦIII |
Как видно из приведенных схем формирования структуры сплавов, техническое железо и стали после завершения кристаллизации при охлаждении в широком интервале температур, получают структуру – аустенит. Снижение температуры ниже критических точек вызывает развитие превращений в твердом состоянии.
Фазовая перекристаллизация аустенита идет в две стадии: полиморфное превращение γ α (ниже линии GS) и эвтектоидное превращение γS (αр + Fe3C)э (на линии PSK). Перлит имеет пластинчатое строение. Конечная структура доэвтектоидных сталей при комнатной температуре – феррит и перлит. В зависимости от содержания углерода, соотношение количества феррита и перлита изменяется от 100 % феррита в техническом железе до 100 % перлита в эвтектоидной стали. При этом меняется тип структуры.
Материаловедение. Учеб. пособие |
-182- |
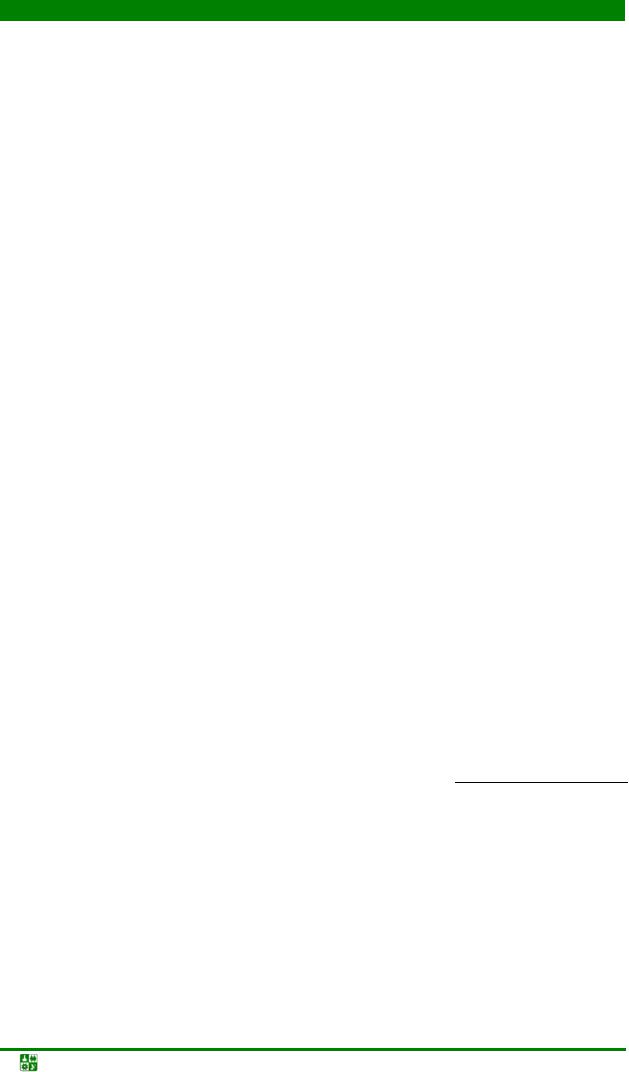
РАЗДЕЛ II. МАТЕРИАЛОВЕДЕНИЕ СТАЛЕЙ И ЧУГУНОВ
Глава 4. Стали, сплавы системы железо–углерод. Маркировка, структура, свойства сплавов
При содержании углерода до 0,1–0,3 % основу структуры составляет феррит с включениями перлита преимущественно на стыках зерен феррита
(рис. 4.9, а).
Увеличение содержания углерода в стали до 0,4–0,5 % приводит к тому, что количество феррита и перлита в структуре будет почти одинаково (рис. 4.9, б). При содержании углерода 0,5 % и выше основу стали составляет перлит с выделением феррита преимущественно по границам зерен. Если углерода в стали 0,6–0,8 %, феррита становится настолько мало, что он просматривается в виде тонкой ферритной сетки по границам перлитных колоний (рис. 4.9, в). При ускоренном охлаждении такой стали (неравновесные условия) уменьшается доля выделяющегося избыточного феррита, а структура становится подобной эвтектоидной. Такую структуру называют квазиэв-
тектоидом.
Таким образом, с повышением содержания углерода в стали увеличивается количество перлита, а значит, повышается ее прочность и уменьшается пластичность.
Стали с содержанием углерода 0,8 % называют эвтектоидными. Структура такой стали: пластинчатый или зернистый перлит (рис. 4.10).
Рис. 4.10. Микроструктура эвтектоидной |
|
|
|
|||
стали, × 500: а – пластинчатый перлит; |
б |
|
|
|
||
– |
|
|
|
а |
|
б |
зернистый перлит |
|
|
||||
Формирование структуры эвтектоидной стали происходит по схеме |
||||||
(табл. 4.8). |
|
|
|
|
|
|
|
|
|
|
|
|
Таблица 4.8 |
|
Схема фазовых и структурных превращений |
|
||||
|
в стали с содержанием 0,8 % С |
|
|
|||
|
|
|
|
|
|
|
Условия развития превращения |
t ниже линии BС |
t = const в точке S |
||||
|
|
|
|
|
|
|
Фазовый состав |
|
L |
→ |
γ |
→ |
(α + Fe3C)э |
Структура |
|
Ж |
→ |
А |
→ |
П |
Основное превращение в эвтектоидной стали – это распад аустенита при переохлаждении ниже 727 °С (точка S на диаграмме железо–углерод) на эвтектоид – перлит (феррито-цементитная смесь). Чаще перлит имеет пластинчатое строение – широкие пластины феррита и узкие цементита (рис. 4.10, а).
При наиболее медленном охлаждении сплава (десятые доли градуса в минуту) эвтектоид может получить зернистое строение. Форма цементита в
Материаловедение. Учеб. пособие |
-183- |
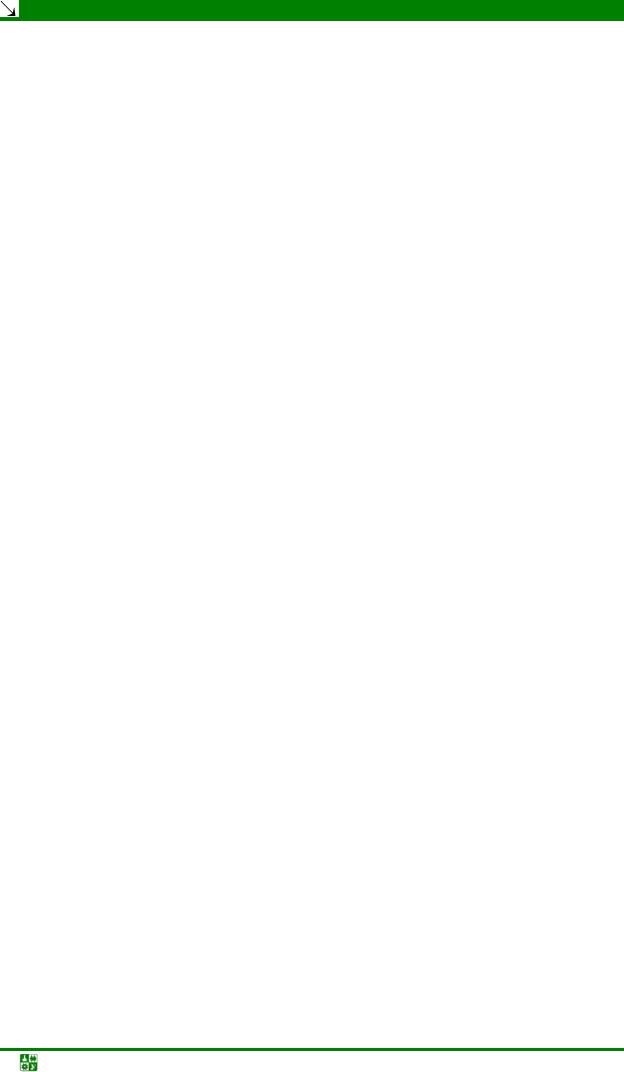
РАЗДЕЛ II. МАТЕРИАЛОВЕДЕНИЕ СТАЛЕЙ И ЧУГУНОВ
Глава 4. Стали, сплавы системы железо–углерод. Маркировка, структура, свойства сплавов
составе перлита определяется особенностями диффузионного перераспределения углерода в аустените в период его эвтектоидного распада (рис. 4.10, б).
Рис. 4.11. Микроструктура заэвтектоидной стали: отожженное состояние
Содержание углерода в заэвтектоидной стали 0,8 < C < 2,0 %. Ее типичная структура в равновесном состоянии (рис. 4.11) – перлит и вторичный цементит в виде сетки по границам зерен или (реже) в виде игл. Светлая сетка вторичного цементита выделяется из аустенита при переохлаждении от температур аустенитной области ниже линии SE.
Формирование структуры заэвтектоидной стали развивается по схеме (табл. 4.9).
Таблица 4.9
Схема фазовых и структурных превращений в заэвтектоидной стали с содержанием 0,8–2,14 % С
Условия развития превращения |
|
t ниже |
|
t ниже |
|
t = const |
|||||
линии BС |
линии SЕ |
на линии PSK |
|||||||||
|
|
||||||||||
Фазовый состав |
L |
→ |
|
γ |
→ |
|
γ |
→ |
|
(α + Fe3C)э |
|
|
|
|
|
|
|
|
+ |
|
|
+ |
|
|
|
|
|
|
|
|
Fe3CII |
→ |
|
Fe3CII |
|
Структура |
Ж |
→ |
|
А |
→ |
|
А + ЦII |
→ |
|
П + ЦII |
Цикл структурных и фазовых превращений, соответствующий кристаллизации, не отличается от эвтектоидной стали. Кристаллизация завершается образованием аустенита. Охлаждение в интервале температур ниже линии SЕ вызывает пересыщение аустенита углеродом и выделение из него избыточного вторичного цементита. При переохлаждении ниже 727 °С оставшийся аустенит распадается с образованием эвтектоида – перлита. Чем больше углерода в заэвтектоидной стали, тем больше в ней вторичного цементита, максимальное содержание которого достигает 20 % (в стали состава точки Е). Это приводит к увеличению толщины цементитной сетки. Такой характер структуры уменьшает пластичность стали. Ускоренное (неравновесное) охлаждение так же, как и в доэвтектоидных сталях, может приводить к образованию квазиэвтектоида, что уменьшает склонность стали к хрупкому разрушению.
Материаловедение. Учеб. пособие |
-184- |

РАЗДЕЛ II. МАТЕРИАЛОВЕДЕНИЕ СТАЛЕЙ И ЧУГУНОВ
Глава 4. Стали, сплавы системы железо–углерод. Маркировка, структура, свойства сплавов
В структуре сталей часто можно обнаружить структурные дефекты, та-
кие как видманштеттова структура и строчечность.
При ускоренном охлаждении доэвтектоидной стали из аустенитной области ниже линии GS полиморфное превращение γ → α идет в условиях частичной когерентности решеток исходного аустенита и образующегося феррита, при котором происходит ориентированный рост кристаллов феррита относительно подобных кристаллографических плоскостей в составе аустенита. В результате в структуре феррит выглядит в виде скопления игл (фактически – пластин), которые могут пересекаться (рис. 4.12). Такая структура (видманштеттов феррит) груба, крупнозерниста, с низкой пластичностью, невысокой твердостью, поэтому нежелательна. Видманшеттова структура может наблюдаться в перегретых поковках, перегретой околошовной зоне сварных швов, после перегрева при термообработке с ускоренным охлаждением. В доэвтектоидной стали в горячекатаном состоянии может образовываться строчечная структура в виде вытянутых полос перлита и феррита (рис. 4.13).
Рис. 4.12. Микроструктура доэвтектоидной стали в литом состоянии (видманштеттова структура)
Рис. 4.13. Микроструктура доэвтектоидной стали в горячекатаном состоянии (строчечная структура)
Такая структура образуется в том случае, если горячую пластическую деформацию доэвтектоидной стали заканчивают ниже линии GS диаграммы Fe– Fe3C, что соответствует температуре двухфазной аустенитно-ферритной области (преимущественно 730–800 °С). В такой стали зерна феррита и колонии перлита вытянуты вдоль направления прокатки. Это вызывает анизотропию свойств.
4.6. Классификациясталей
Стали и чугуны являются сплавами на основе железа. Технически чистое железо содержит углерода не более 0,04 %. Углеродистые стали относятся к сплавам системы Fe–Fe3C. По составу стали располагаются на диаграмме до точки Е, с концентрацией 2,14 % С. Промышленные углеродистые стали относятся к многокомпонентным системам, т.к. кроме углерода они содержат примеси других элементов. Содержание отдельных примесей может быть со-
Материаловедение. Учеб. пособие |
-185- |
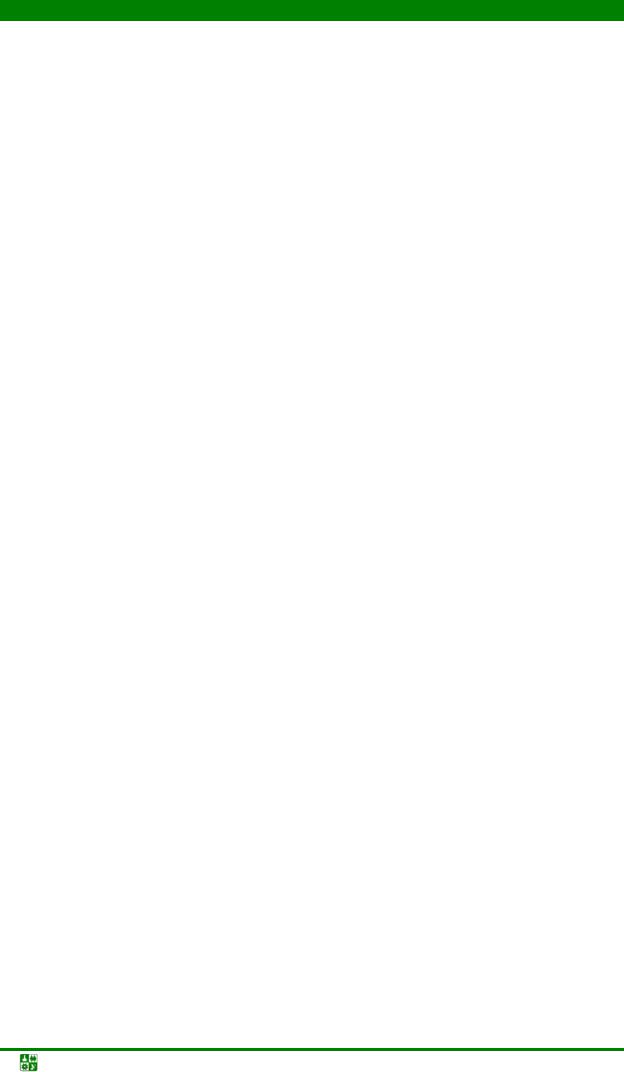
РАЗДЕЛ II. МАТЕРИАЛОВЕДЕНИЕ СТАЛЕЙ И ЧУГУНОВ
Глава 4. Стали, сплавы системы железо–углерод. Маркировка, структура, свойства сплавов
измеримо с содержанием углерода, однако углерод оказывает основное влияние на формирование структуры и на свойства сталей, поэтому анализ структуры промышленных углеродистых сталей можно проводить по диаграмме состояния Fe–Fe3C.
Промышленные нелегированные чугуны (серые, высокопрочные, ковкие, с вермикулярным графитом) относятся к высокоуглеродистым сплавам на основе системы Fe–C–Si, в которых углерода содержится более 2,14 %. Кристаллизация таких чугунов реализуется по стабильной Fe–C–Si или метастабильной Fe–Fe3C–Si диаграмме, в зависимости от состава и условий охлаждения. Белые чугуны кристаллизуются в условиях ускоренного охлаждения, для формирования их структуры можно использовать метастабильную диаграмму Fe–Fe3C, они являются исходным материалом для получения ковкого чугуна.
Стали относятся к сплавам на основе железа с углеродом (углеродистые стали). Стали, дополнительно содержащие хром, марганец, кремний, никель, молибден, и другие элементы, называют легированными сталями. Стали являются основными и наиболее распространенными сплавами для изготовления деталей конструкций, инструмента и изделий специального назначения. Сплавы на основе железа имеют хорошее сочетание высокой прочности, твердости, пластичности, вязкости и технологичности.
По химическому составу стали классифицируются на углеродистые и легированные.
По назначению стали подразделяются на конструкционные, инструментальные и стали специального назначения.
По способу производства изделий стали классифицируются на дефор-
мируемые и литейные.
По металлургическому качеству в зависимости от содержания вредных примесей стали подразделяются на категории: стали обыкновенного качества, (ГОСТ 380-94), качественные (ГОСТ 1050-88 и др.), высококачественные, особовысококачественные.
К наиболее вредным примесям сталей (табл. 4.10) относятся сера и фосфор. Сера приводит к красноломкости стали, т.е. к хрупкости при горячей обработке давлением. Марганец, который вводят в сталь при раскислении, устраняет вредное влияние серы. Фосфор вызывает хладноломкость, т.е. охрупчивание при низких температурах.
По способу раскисления при выплавке стали классифицируются на кипящие, спокойные и полуспокойные.
Раскислением называется процесс восстановления железа из FeO, который протекает по следующим химическим реакциям:
FeO + Mn = Fe + MnO
2FeO + Si = 2Fe + SiO2
3FeO + 2Al = 3Fe + Al2O3
Кремний и марганец вводят в виде ферросплавов, алюминий – в чистом виде. Кипящие стали раскисляют только ферромарганцем. В таких сталях ос-
Материаловедение. Учеб. пособие |
-186- |
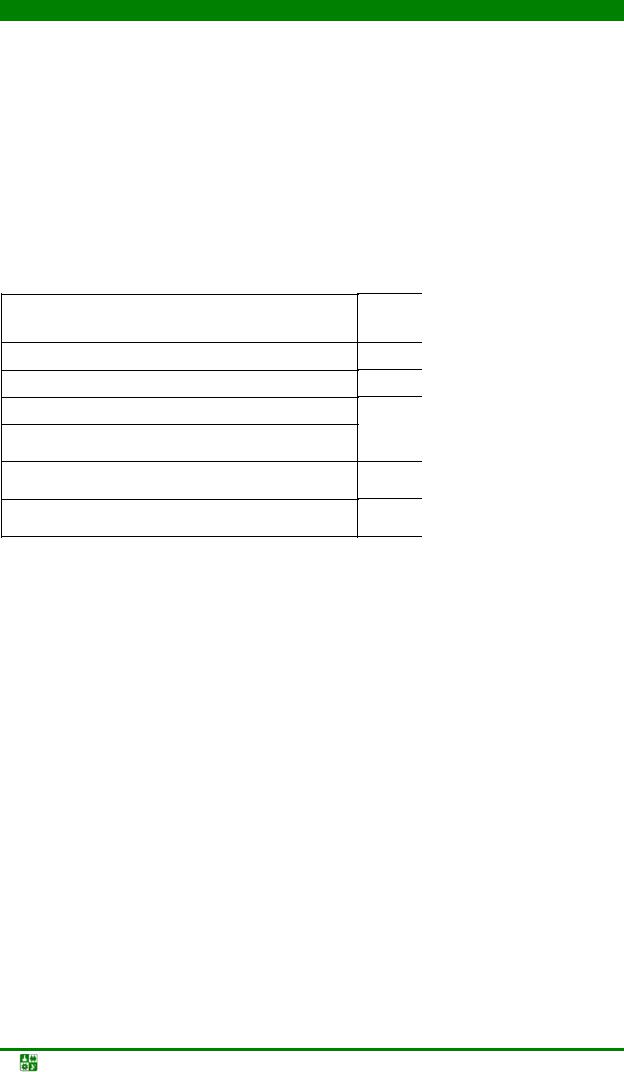
РАЗДЕЛ II. МАТЕРИАЛОВЕДЕНИЕ СТАЛЕЙ И ЧУГУНОВ
Глава 4. Стали, сплавы системы железо–углерод. Маркировка, структура, свойства сплавов
тается растворенный FeO, и при кристаллизации продолжается процесс кипения по реакции
FeO + C = Fe + CO
Газовые пузыри остаются в теле слитка и завариваются при последующей прокатке. Кипящая сталь дает наиболее высокий выход годного металла.
Таблица 4.10
Массовая доля серы и фосфора в углеродистых и легированных сталях
Категория качества стали
Обыкновенного качества конструкционная
Качественная конструкционная углеродистая
Качественная инструментальная углеродистая
Высококачественная инструментальная углеродистая
Высококачественная конструкционная легированная
Особовысококачественная конструкционная легированная
Фосфор |
Сера |
Признак качества |
|
%, не более |
|||
|
|||
|
|
|
|
0,04 |
0,05 |
В начале марки – Ст |
|
|
|
|
|
0,035 |
0,04 |
По умолчанию |
|
|
|
|
|
0,030 |
0,028 |
По умолчанию |
|
|
|
|
|
0,025 |
0,018 |
В конце марки – А |
|
|
|
|
|
0,025 |
0,025 |
В конце марки – А |
|
|
|
|
|
0,025 |
0,015 |
В конце марки – Ш |
|
|
|
|
Спокойную сталь раскисляют марганцем, кремнием, алюминием; при этом в металле достаточно полно удаляется растворенный кислород. При кристаллизации процесс кипения прекращается, сталь успокаивается.
Углеродистые стали относятся к железоуглеродистым сплавам с содержанием углерода от 0,05 до 1,35 % С. Углеродистые конструкционные стали содержат до 0,65 % С, инструментальные – более 0,65 % С.
Кроме вышеуказанной классификации, углеродистые стали подразделяются по содержанию углерода, по структуре, по назначению.
По содержанию углерода углеродистые стали делятся на низкоуглеродистые до 0,25 % С, среднеуглеродистые – 0,3–0,5 % С, высокоуглеродистые –
> 0,50 % С.
По структуре стали подразделяются на доэвтектоидные – до 0,8 % С, эвтектоидные – 0,8 % С, заэвтектоидные – более 0,8 % С.
Углеродистые стали, как наиболее дешевые, технологичные и имеющие достаточно высокий комплекс механических свойств, применяются для металлоконструкций общего назначения, используются в строительных конструкциях, для изготовления деталей в машиностроении и т.д.
Углеродистые стали по назначению подразделяются на стали общего и специального применения. К сталям специального назначения относятся автоматные, котельные, строительные, стали для глубокой вытяжки.
Материаловедение. Учеб. пособие |
-187- |
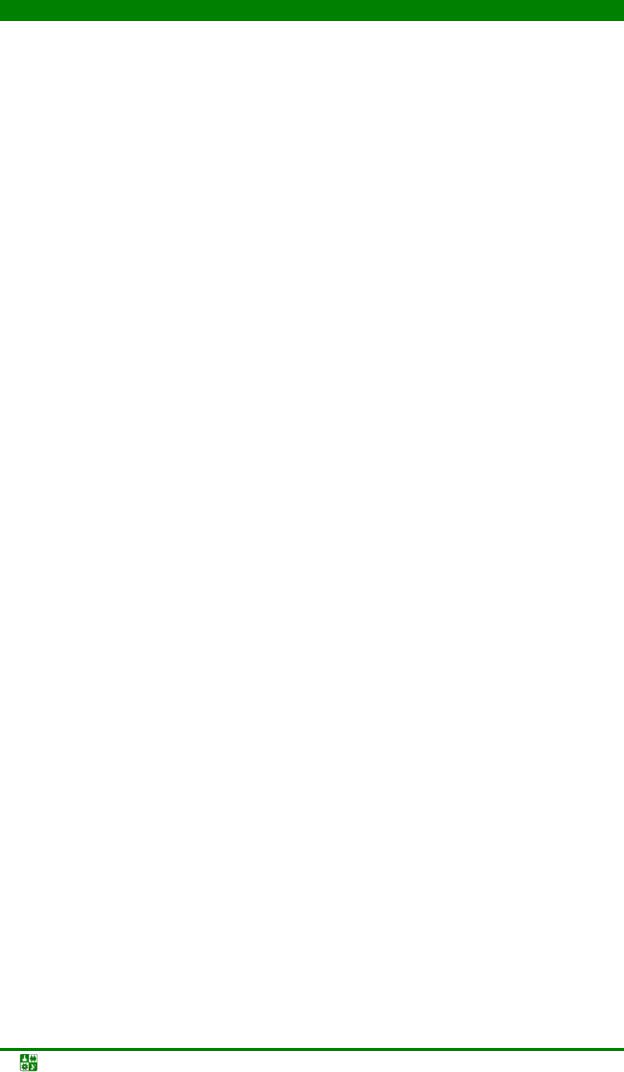
РАЗДЕЛ II. МАТЕРИАЛОВЕДЕНИЕ СТАЛЕЙ И ЧУГУНОВ
Глава 4. Стали, сплавы системы железо–углерод. Маркировка, структура, свойства сплавов
4.7. Влияниеуглерода, легирующихэлементов, примесейнасвойствасталей
Углерод является важнейшим элементом, определяющим структуру и свойства углеродистой стали. Даже при малом изменении содержания углерод оказывает заметное влияние на свойства стали. С увеличением содержания углерода в структуре стали увеличивается количество цементита. При содержании до 0,8 % С сталь состоит из феррита и перлита, при содержании более 0,8 % С в структуре стали кроме перлита появляется структурно свободный вторичный цементит. Феррит имеет низкую прочность, но сравнительно пластичен. Цементит характеризуется высокой твердостью, но хрупок. Поэтому с ростом содержания углерода увеличивается твердость и прочность, однако уменьшается вязкость и пластичность стали. Рост прочности происходит при содержании углерода в стали до 0,8–1,0 %. При увеличении содержании углерода в стали более 0,8 % уменьшается не только пластичность, но и прочность стали. Это связано с образованием сетки хрупкого цементита вокруг перлитных колоний, легко разрушающейся при нагружении. По этой причине заэвтектоидные стали подвергают специальному отжигу, в результате которого получают структуру зернистого перлита.
Углерод оказывает также существенное влияние на технологические свойства стали – свариваемость, обрабатываемость резанием и давлением. Низкоуглеродистые стали хорошо свариваются и имеют высокую обрабатываемость давлением.
Постоянными примесями в углеродистых сталях являются марганец, кремний, сера, фосфор, а также скрытые примеси – газы: кислород, азот, водород. Примесями могут считаться и такие элементы, как медь, никель, хром (если они не предусматриваются марочным составом стали и их содержание ограничивается по верхнему пределу с указанием «не более»). К полезным примесям (технологическим добавкам) в углеродистых сталях относятся марганец, кремний, хром; их содержание обычно не превышает одного процента. Марганец и кремний вводят в сталь при раскислении, они упрочняют железо. Марганец увеличивает прокаливаемость (возможную глубину закаленного слоя) сталей, а также уменьшает вредное влияние серы. Содержание вредных примесей – серы и фосфора регламентируется стандартами. Основным источником серы и фосфора в стали является исходное сырье – чугун. Сера снижает пластичность и вязкость стали, а также приводит к красноломкости стали при прокатке и ковке. Она образует с железом соединение FeS – сульфид железа. При нагреве стальных заготовок до температуры горячей деформации включения FeS вызывают в стали хрупкость, а в результате оплавления при деформации образуют надрывы и трещины. Фосфор, растворяясь в железе, уменьшает его пластичность. Кислород и азот мало растворимы в феррите. Они загрязняют сталь хрупкими неметаллическими включениями, снижают вязкость и пластичность стали. Повышенное содержание водорода охрупчивает сталь и приводит к образованию внутренних трещин – флокенов.
Материаловедение. Учеб. пособие |
-188- |
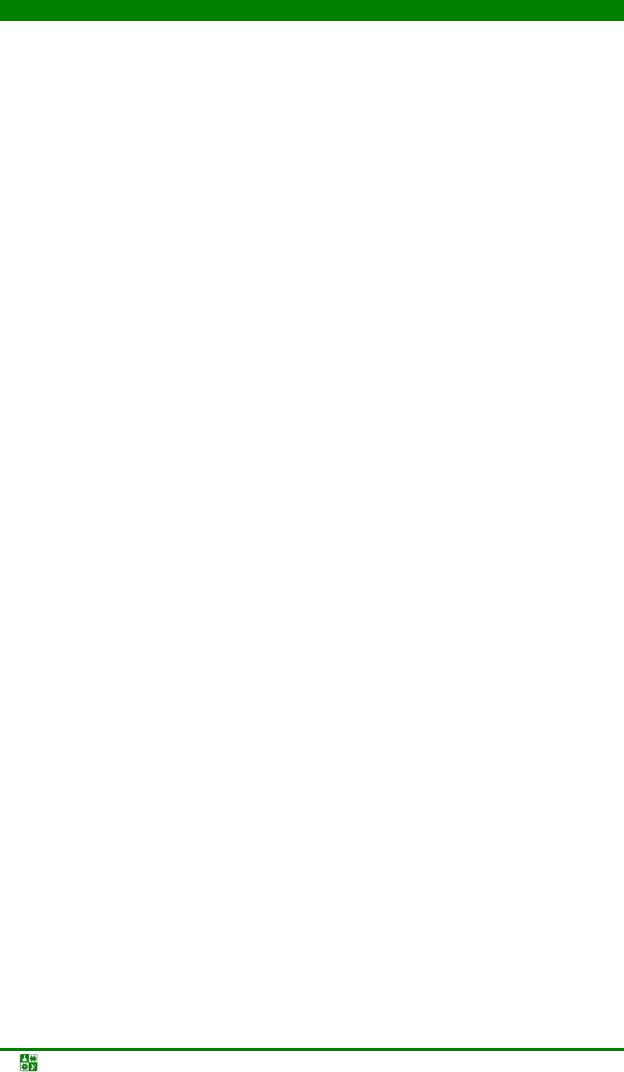
РАЗДЕЛ II. МАТЕРИАЛОВЕДЕНИЕ СТАЛЕЙ И ЧУГУНОВ
Глава 4. Стали, сплавы системы железо–углерод. Маркировка, структура, свойства сплавов
4.8. Термическаяихимико-термическаяобработкасплавов
4.8.1. Видытермическойобработкисталей
Термическая обработка – технологическая операция, состоящая из нагрева, выдержки при определенной температуре и охлаждения. Термическая обработка имеет важное значение именно для стали. Это обусловлено, с одной стороны, необыкновенно широким распространением стали в качестве конструкционных и инструментальных материалов, а с другой стороны, тем, что ни для одного сплава термическая обработка не дает такого эффекта по изменению свойств, как для стали.
Отжиг I рода – нагрев до различных температур с целью гомогенизации, снятия внутренних напряжений, рекристаллизации. Если в процессе нагрева и охлаждения в стали происходит полиморфное превращение, то оно является лишь процессом, сопутствующим гомогенизации, т.к. нет необходимости в фазовой перекристаллизации.
Отжиг II рода (или фазовая перекристаллизация) – нагрев выше Ас3 (или Ас1) с последующим медленным непрерывным или ступенчатым (изотермическим) охлаждением. Частный случай отжига II рода – нормализация (охлаждение на спокойном воздухе).
Закалка с полиморфным превращением – это термическая обработка,
при которой главным является мартенситное превращение высокотемпературной фазы. Поэтому такую термообработку обычно называют закалкой на мартенсит.
Отпуск – это термическая обработка закаленной на мартенсит стали, при которой главным процессом является распад мартенсита. Применяют нагрев закаленной стали до температур не выше Ас1.
Закалка без полиморфного превращения − это термическая обработка стали, при которой главным процессом является формирование неравновесной структуры во время ускоренного охлаждения. Она характерна для аустенитных сталей, не имеющих полиморфных превращений, и используется для растворения карбидов или интерметаллидов.
Старение – это термическая обработка, при которой в стали, подвергнутой закалке без полиморфного превращения, главным процессом является распад пересыщенного твердого раствора.
Закалка с плавлением поверхности − это термическая обработка, при которой главным процессом является быстрое затвердевание поверхностного слоя с образованием метастабильной структуры
4.8.2. Термическаяобработкасплавов, несвязанная сфазовымипревращениямивтвердомсостоянии
Нагрев для снятия остаточных напряжений. Многие технологиче-
ские воздействия на обрабатываемые детали сопровождаются возникновени-
Материаловедение. Учеб. пособие |
-189- |
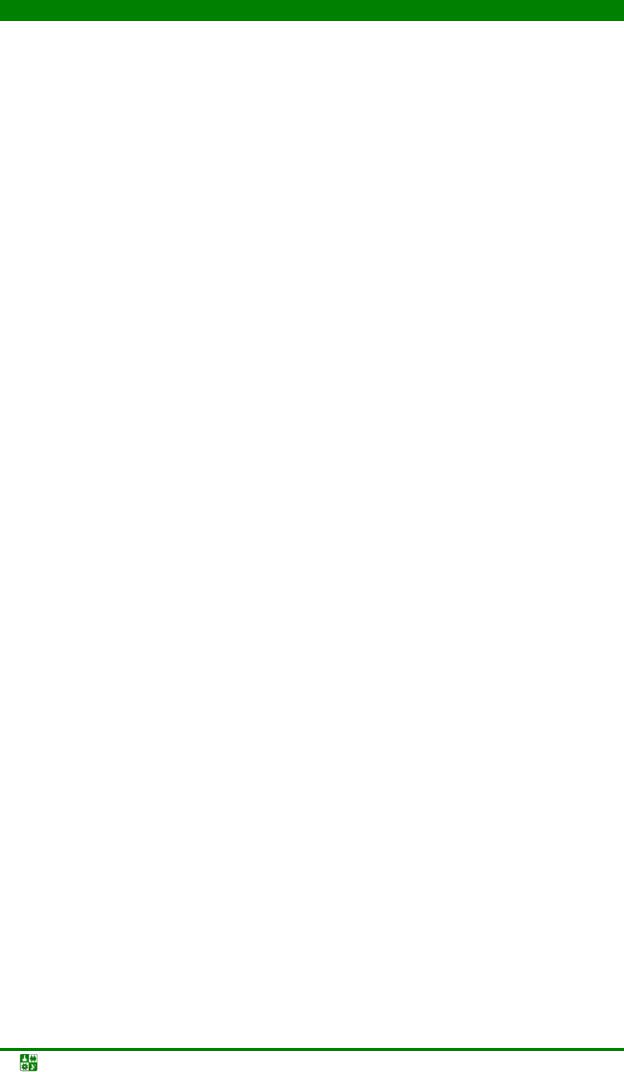
РАЗДЕЛ II. МАТЕРИАЛОВЕДЕНИЕ СТАЛЕЙ И ЧУГУНОВ
Глава 4. Стали, сплавы системы железо–углерод. Маркировка, структура, свойства сплавов
ем в них остаточных напряжений, которые уравновешиваются в объеме детали.
Значительные остаточные напряжения появляются в отливках и полуфабрикатах, неравномерно охлаждающихся после проката или ковки, в холоднодеформированных полуфабрикатах или заготовках, в прутках в процессе правки, в сварных соединениях, при закалке и т.п.
Чаще всего эти напряжения нежелательны. Они могут вызвать деформацию детали при обработке резанием или в процессе эксплуатации, а суммируясь с напряжениями от внешних нагрузок, привести к преждевременному разрушению или короблению конструкции.
Для уменьшения остаточных напряжений изделия нагревают. С повышением температуры предел текучести понижается, поэтому остаточные напряжения вызывают пластическую деформацию и снижаются до уровня предела текучести металла при температуре нагрева.
По окончании выдержки при заданной температуре изделия медленно охлаждают, чтобы предотвратить возникновение новых напряжений.
Рекристаллизационный отжиг. Нагрев деформированных полуфабрикатов или деталей выше температуры рекристаллизации называют рекристаллизационным отжигом. Цель отжига – понижение прочности и восстановление пластичности деформированного металла, получение определенной кристаллографической текстуры, создающей анизотропию свойств, и заданного размера зерна.
Рекристаллизационный отжиг часто используют в качестве межоперационной смягчающей обработки при холодной прокатке, волочении и других операциях холодного деформирования. Рекристаллизационный отжиг может быть использован в качестве окончательной обработки полуфабрикатов.
Диффузионный отжиг. В реальных условиях охлаждения расплава кристаллизация твердых растворов чаще всего протекает неравновесно: диффузионные процессы, необходимые для выравнивания концентрации растущих кристаллов по объему, отстают от процесса кристаллизации. В результате сохраняется неоднородность состава по объему кристалла – внутрикристаллическая ликвация.
Диффузионным отжигом называют длительную выдержку сплавов при высоких температурах, в результате которой уменьшается ликвационная неоднородность твердого раствора. При высокой температуре протекают диффузионные процессы, не успевшие завершиться при первичной кристаллизации.
Диффузионному отжигу подвергают слитки легированных сталей и многих алюминиевых сплавов, а в некоторых случаях и отливки. Для стальных слитков нагрев ведут при температуре 1 100–1 300 °С в течение 20–50 ч, для алюминиевых слитков – при температуре 420–520 °С с выдержкой 20–30 ч.
Термическая обработка сплавов с переменной растворимостью компонентов в твердом состоянии. Эта обработка значительно упрочняет сплавы, что привело к широкому использованию сплавов этого типа – стареющих сплавов – в качестве конструкционных материалов повышенной и
Материаловедение. Учеб. пособие |
-190- |
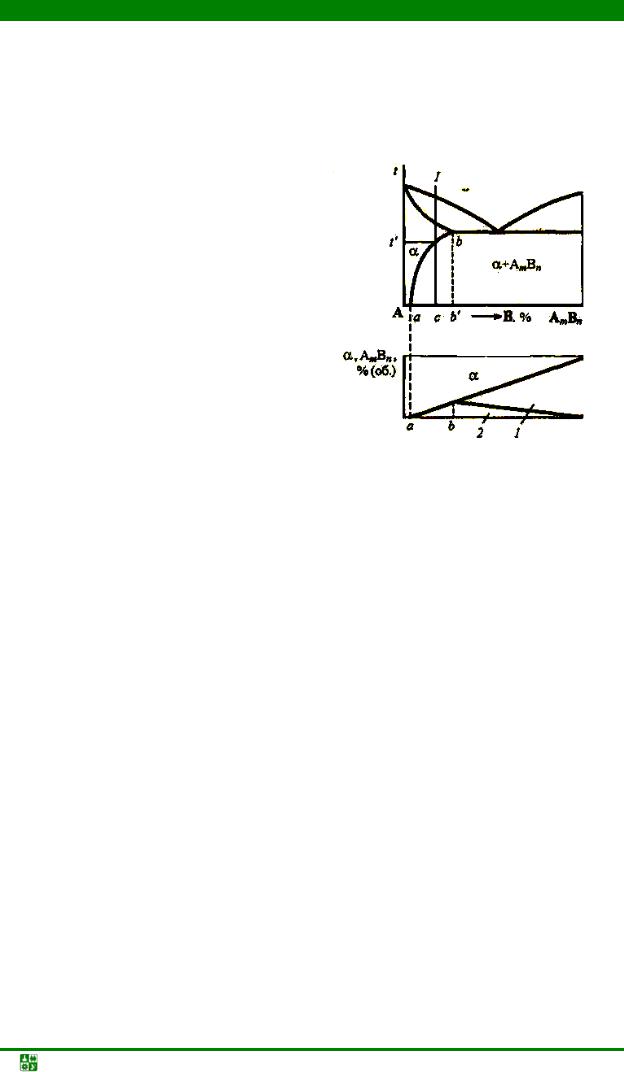
РАЗДЕЛ II. МАТЕРИАЛОВЕДЕНИЕ СТАЛЕЙ И ЧУГУНОВ
Глава 4. Стали, сплавы системы железо–углерод. Маркировка, структура, свойства сплавов
высокой прочности. Применяют стареющие сплавы на алюминиевой, медной, железной, никелевой, кобальтовой, титановой и других основах.
Рассмотрим принцип упрочняющей термической обработки стареющих сплавов на примере системы с промежуточным соединением (рис. 4.14).
Рис. 4.14. Диаграмма состояния компонентов с переменной растворимостью в твердом состоянии: а – диаграмма равновесия; б – количество первичных (1) и вторичных (2) кристаллов АmВn в сплавах разного состава при 20–25 °С (высота прямоугольника про-
порциональна массе всего сплава)
а
б
К термически упрочняемым относятся сплавы составов от точки а до промежуточного соединения АmВn, в которых при охлаждении из твердого раствора α выделяются кристаллы АmВn. При этом степень упрочнения тем выше, чем больше масса вторичных кристаллов в равновесном сплаве
(рис. 4.14, б).
Рассмотрим сплав I состава точки с, который в равновесном состоянии имеет двухфазную структуру, состоящую из кристаллов твердого раствора α концентрации точки а и относительно крупных вторичных кристаллов АmВn. Сопротивление движению дислокаций возрастает по мере уменьшения расстояния между частицами упрочняющей фазы, т.е. сплав I станет прочнее, когда вместо немногочисленных крупных включений образуется большое количество мелких. Наибольшее препятствие для движения дислокаций создают включения, отстоящие одно от другого на 25–50 межатомных расстояний. В большинстве стареющих сплавов желательная дисперсная структура образуется в результате термической обработки, состоящей из закалки и старения.
При закалке сплавы нагревают до температур, обеспечивающих распад вторичных кристаллов. Для рассматриваемого сплава I такой будет температура, несколько превышающая t1 (рис. 4.14, а). Быстрое охлаждение с температуры закалки полностью подавляет процесс выделения вторичных кристаллов, и в результате получают однофазный сплав – пересыщенный компонентом В твердый раствор. Пересыщение твердого раствора относительно мало сказывается на повышении твердости и прочности, незначительно изменяется и пластичность сплавов. Пересыщенный твердый раствор представ-
Материаловедение. Учеб. пособие |
-191- |
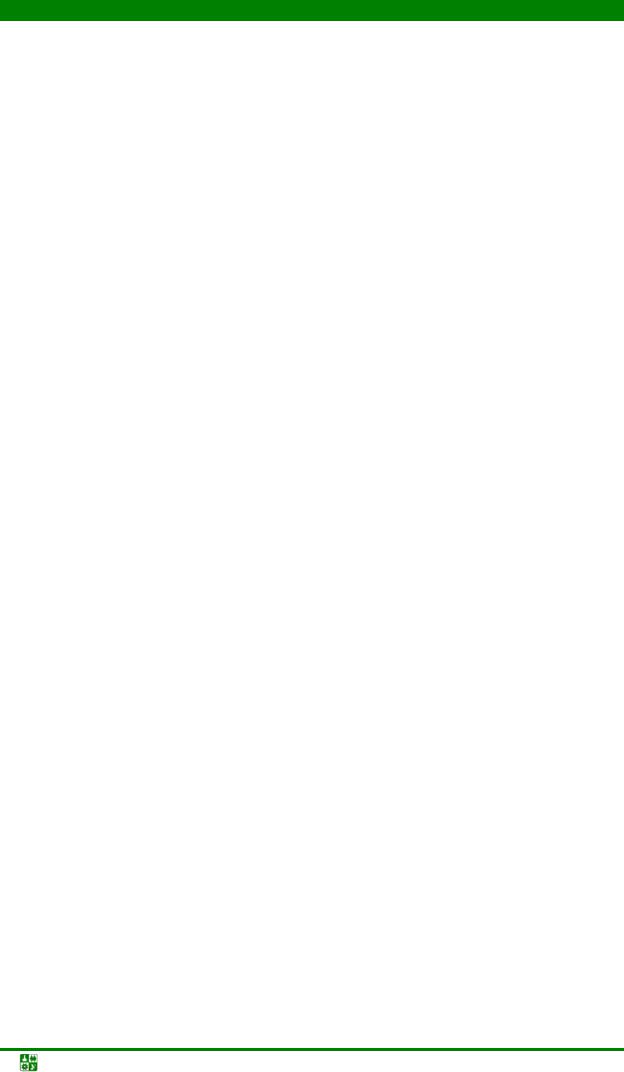
РАЗДЕЛ II. МАТЕРИАЛОВЕДЕНИЕ СТАЛЕЙ И ЧУГУНОВ
Глава 4. Стали, сплавы системы железо–углерод. Маркировка, структура, свойства сплавов
ляет собой неравновесную структуру с повышенным уровнем свободной энергии.
Поэтому как только подвижность атомов окажется достаточной, твердый раствор будет распадаться – начнется процесс старения.
При старении уменьшается концентрация пересыщающего компонента
втвердом растворе, этот компонент расходуется на образование выделений.
Вбольшинстве сплавов при старении получаются выделения нескольких типов.
При любой перегруппировке атомов в твердом растворе, в том числе и при зарождении выделений, необходимо преодолеть определенный энергетический барьер. Величину этого барьера называют энергией активации.
Энергия активации зарождения и роста выделений увеличивается с возрастанием отличий пространственной кристаллической решетки выделений от пространственной решетки основного твердого раствора. С увеличением температуры возрастает кинетическая энергия атомов и повышается вероятность преодоления более высокого энергетического барьера. Уменьшение свободной энергии при распаде пересыщенного твердого раствора бу-
дет наибольшим при выделении равновесных кристаллов АmBn, однако зарождение таких кристаллов, имеющих, как правило, сложную пространственную решетку, возможно только при достаточно высоких температурах. В общем случае при распаде пересыщенных твердых растворов могут возникать следующие образования (они перечисляются в порядке возрастания энергии активации зарождения): 1) зоны Гинье – Престона; 2) кристаллы метастабильной фазы; 3) кристаллы стабильной фазы.
Зоны Гинье–Престона (зоны Г–П) представляют субмикроскопические объемы твердого раствора с резко повышенной концентрацией растворенного компонента, сохраняющие решетку растворителя. При значительной разнице в размерах А и В, зоны Г–П имеют форму дисков. Диски закономерно ориентированы относительно пространственной решетки растворителя и затрудняют движение дислокаций.
Метастабильные фазы имеют иную пространственную решетку, чем твердый раствор, однако существует сходство в расположении атомов в определенных атомных плоскостях их решеток, что вызывает образование когерентной (или полукогерентной) границы раздела. Для метастабильных фаз характерна высокая дисперсность, что значительно повышает сопротивление движению дислокаций.
Стабильная фаза АmВn имеет сложную пространственную решетку с пониженным числом элементов симметрии и с большим числом атомов в элементарной ячейке.
Вторичные кристаллы со стабильной структурой в большинстве сплавов выделяются в виде достаточно крупных частиц. Значительное различие кристаллической структуры твердого раствора и стабильных кристаллов приводит к образованию некогерентной границы раздела и, следовательно, к минимальным искажениям решетки твердого раствора вблизи границы.
Материаловедение. Учеб. пособие |
-192- |
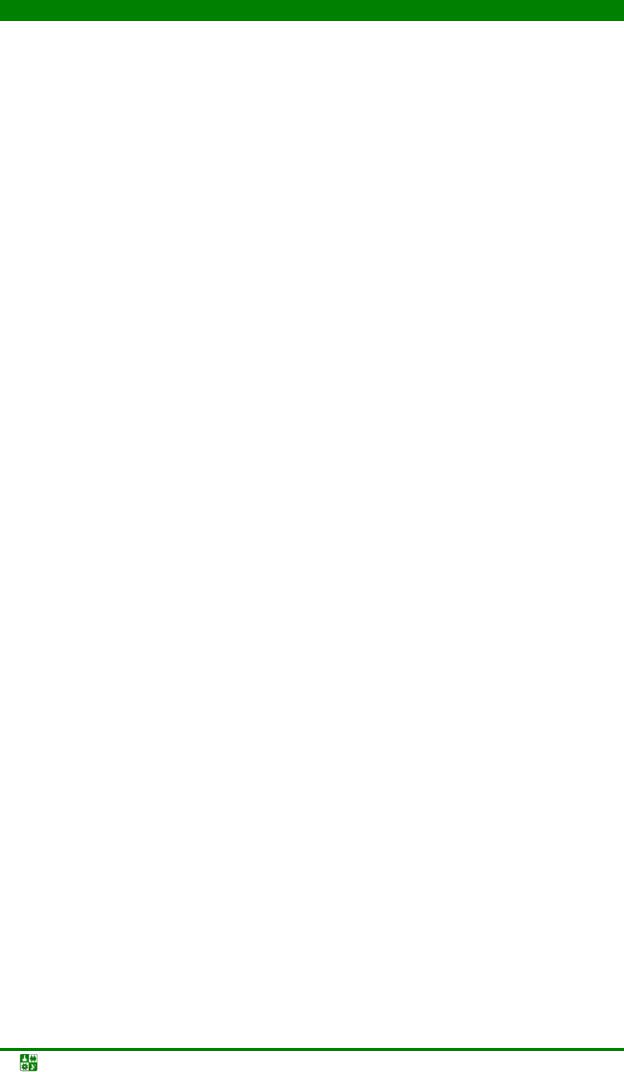
РАЗДЕЛ II. МАТЕРИАЛОВЕДЕНИЕ СТАЛЕЙ И ЧУГУНОВ
Глава 4. Стали, сплавы системы железо–углерод. Маркировка, структура, свойства сплавов
Если время выдержки достаточно велико, происходит коагуляция стабильных кристаллов. Коагуляцией называют рост кристаллов той фазы, которая распределена в виде включений в основе сплава. Рост кристаллов второй фазы происходит путем распада наиболее мелких и потому неустойчивых частиц и последующей диффузии растворенного компонента к более устойчивым частицам. Коагуляция приближает структуру сплава к равновесной.
Термическую обработку, приводящую к получению стабильной структуры (стабильные кристаллы АmВn после коагуляции), называют стабилизацией (термин подчеркивает получение более устойчивой структуры при возможном нагреве сплава в условиях эксплуатации).
4.8.3. Превращениявсталяхпринагреведоаустенитногосостояния
При многих видах термической обработки сталь нагревают до температур, соответствующих существованию аустенита (процесс аустенитизации). Образование аустенита при нагреве является диффузионным процессом и подчиняется основным положениям теории кристаллизации.
При нагреве эвтектоидной стали (0,8 % С) несколько выше критической точки А1 (727 °С) перлит (феррито-карбидная структура) превращается в аустенит:
ФP + Fе3С → АS.
Превращение состоит из двух одновременно протекающих процессов: полиморфного α → γ-перехода и растворения в аустените цементита.
При нагреве доэвтектоидной стали выше точки А1 после превращения перлита в аустенит образуется двухфазная структура – аустенит и феррит. При дальнейшем нагреве в интервале температур А1–А3 феррит постепенно растворяется в аустените. При температуре А3 феррит исчезает, а концентрация углерода в аустените соответствует содержанию его в стали. Аналогично протекает превращение и в заэвтектоидной стали. При температуре несколько выше А1 (727 °С) перлит превращается в аустенит, содержащий 0,8 % С. В интервале температур А1–Асm происходит растворение избыточного цементита. Выше температуры Асm будет только аустенит, содержание углерода в котором соответствует его содержанию в стали.
Материаловедение. Учеб. пособие |
-193- |
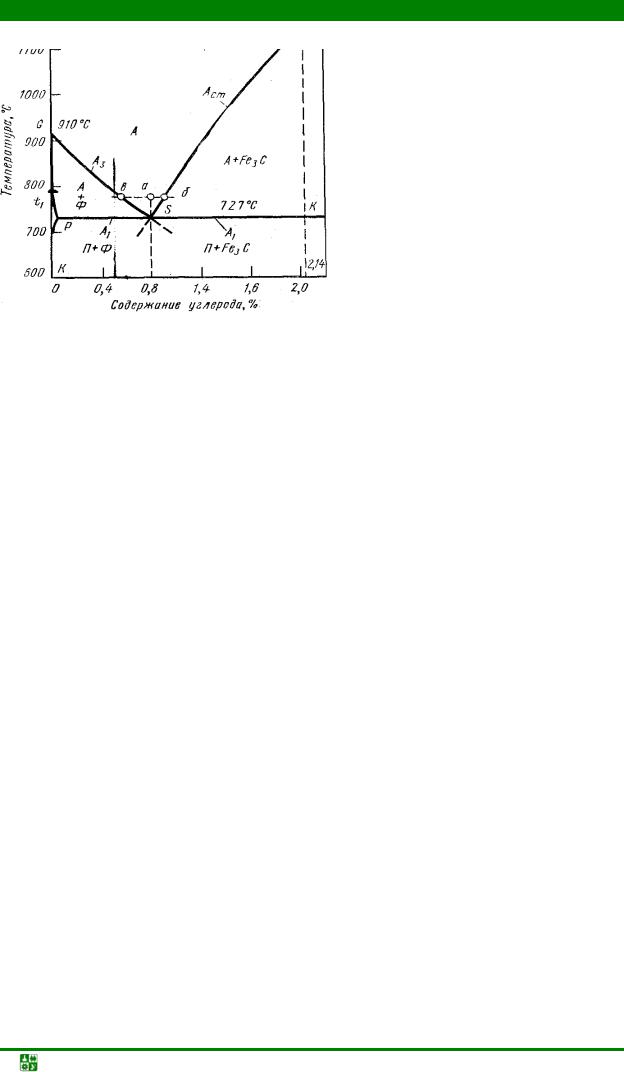
РАЗДЕЛ II. МАТЕРИАЛОВЕДЕНИЕ СТАЛЕЙ И ЧУГУНОВ
Глава 4. Стали, сплавы системы железо–углерод. Маркировка, структура, свойства сплавов
а |
б |
в
Рис. 4.15. Превращение стали с феррито-цементитной структурой при нагреве: а – схема изменений фазового состава при нагреве (диаграмма Fe–Fe3C); б – схема изотермического образования аустенита; в – последовательные стадии превращения перлита в аустенит (1 – начало превращения перлита в аустенит; 2 – конец превращения перлита в аустенит; 3 – полное растворение карбидов; 4 – гомогенизация аустенита)
Аустенит при температурах несколько выше Ас1 (727 °С) содержит ~ 0,8 % С. Зародыши аустенита образуются на границе раздела феррита и цементита (рис. 4.15, в), где наличие дефектов уменьшает работу образования зародыша аустенита. При росте зародыша когерентность α- и γ-решеток нарушается, сдвиговый механизм заменяется нормальным механизмом роста и зерна аустенита приобретают равноосную форму. Образовавшийся аустенит неоднороден по содержанию углерода. В участках, прилегающих к частицам цементита, концентрация углерода в аустените выше (точка б на рис. 4.15, а), чем в участках, прилегающих к ферриту (точка в на рис. 4.15, а).
Под влиянием этого градиента перепада концентрации происходит диффузия атомов углерода в аустените в направлении от границы с цементитом к участкам, граничащим с ферритом, что приводит к нарушению равновесия на межфазных поверхностях между аустенитом и указанными фазами. Восстановление равновесия достигается в результате дальнейшего растворения цементита в аустените и перехода атомов углерода в феррит, что облегчает превращение его в аустенит.
Материаловедение. Учеб. пособие |
-194- |
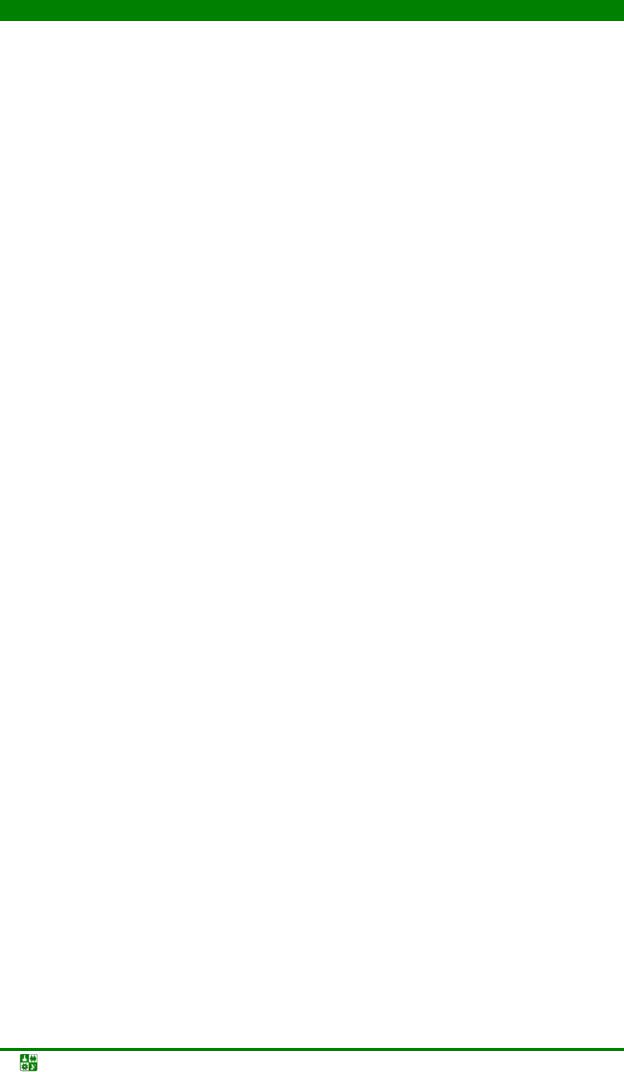
РАЗДЕЛ II. МАТЕРИАЛОВЕДЕНИЕ СТАЛЕЙ И ЧУГУНОВ
Глава 4. Стали, сплавы системы железо–углерод. Маркировка, структура, свойства сплавов
Образовавшийся в результате описанных превращений аустенит неоднороден по составу, и для его гомогенизации требуется дополнительное время.
Скорость превращения ферритоцементитной структуры в аустенитную, помимо температуры нагрева, зависит от ее исходного состояния. Чем тоньше ферритоцементитная структура, тем больше возникает зародышей аустенита и меньше пути диффузии, а значит, быстрее протекает процесс аустенитизации. Чем больше в стали углерода, тем быстрее протекает процесс аустенитизации, что объясняется увеличением количества цементита, а следовательно, и ростом суммарной поверхности раздела феррита и цементита. Введение в сталь хрома, молибдена, вольфрама, ванадия и других карбидообразующих элементов задерживает процесс аустенитизации вследствие образования легированного цементита или карбидов легирующих элементов, более трудно растворимых в аустените
Размер зерна аустенита при нагреве обуславливается несколькими факторами.
Зародыши аустенита при нагреве выше A1 образуются на границах раздела феррит–карбид. При таком нагреве число зародышей всегда достаточно велико и начальное зерно аустенита мелкое. Однако нередко при таких невысоких температурах нагрева наблюдается разнозернистость – на фоне мелкого зерна отмечаются и очень крупные зерна.
При дальнейшем повышении температуры или увеличении длительности выдержки при данной температуре происходит собирательная рекристаллизация, и зерно увеличивается. Рост зерна аустенита происходит самопроизвольно и вызывается стремлением системы к уменьшению свободной энергии вследствие сокращения поверхности зерен.
Способность зерна аустенита к росту неодинакова даже у сталей одного марочного состава вследствие влияния условий их выплавки.
По склонности к росту зерна различают два предельных типа сталей:
наследственно мелкозернистые и наследственно крупнозернистые.
В наследственно мелкозернистой стали при нагреве до высоких температур (1 000–l 050 °C) зерно увеличивается незначительно, однако при более высоком нагреве наступает бурный рост зерна. В наследственно крупнозернистой стали, наоборот, сильный рост зерна наблюдается даже при незначительном перегреве выше А1 (рис. 4.16).
Материаловедение. Учеб. пособие |
-195- |
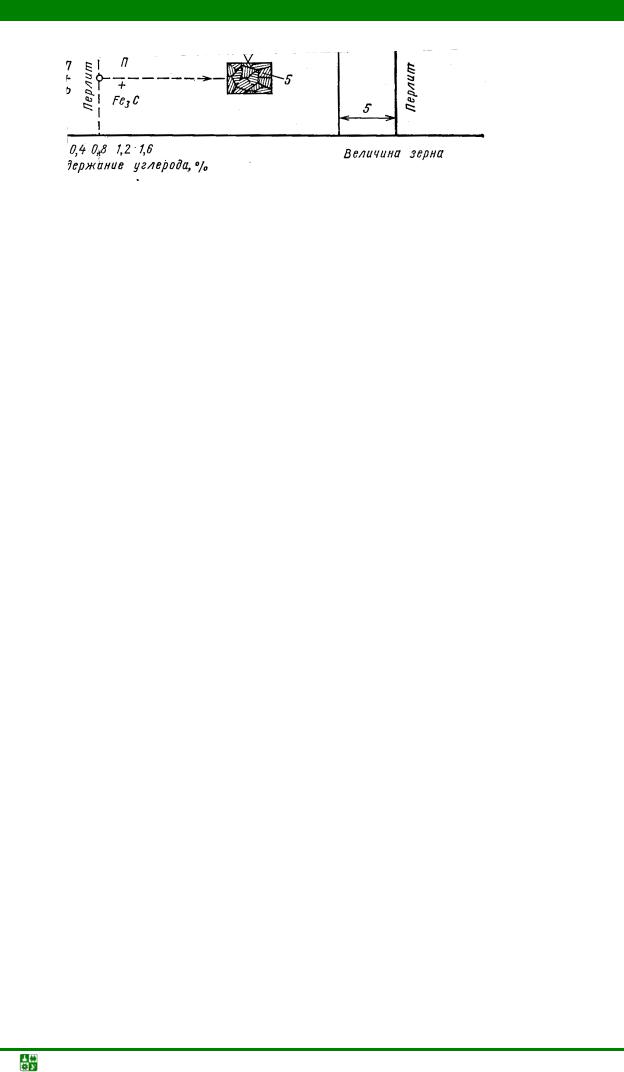
РАЗДЕЛ II. МАТЕРИАЛОВЕДЕНИЕ СТАЛЕЙ И ЧУГУНОВ
Глава 4. Стали, сплавы системы железо–углерод. Маркировка, структура, свойства сплавов
а |
б |
Рис. 4.16. Диаграмма состояния Fe–Fe3C (а) и схема роста зерна аустенита в стали, содержащей 0,8 % С (б): 1 – наследственно мелкозернистая сталь; 2 – наследственно крупнозернистая сталь; 3 – наследственное зерно; 4 – зерно при нагреве под термическую обработку; 5 – исходное зерно; 6 – начальное зерно аустенита
В двухфазных областях, например в заэвтектоидных сталях, в интервале температур Ас1–Асm (рис. 4.16, а) рост зерна аустенита сдерживается не растворившимися карбидными частицами. Такое же сдерживающее влияние на рост зерна в доэвтектоидных сталях в интервале температур Ас1–Асm (рис. 4.16, а) оказывают участки феррита.
Легирующие элементы, особенно карбидообразующие, замедляющие собирательную рекристаллизацию, задерживают рост зерна аустенита. Наиболее сильно действуют Ti, V, Zr, Nb, W и Мо, образующие труднорастворимые в аустените карбиды, которые служат барьером. Более слабое влияние оказывает такой карбидообразующий элемент, как хром. Марганец и фосфор способствуют росту зерна аустенита.
Наследственно мелкозернистая сталь при достаточно высокой температуре может даже иметь более крупное зерно аустенита, чем наследственно крупнозернистая сталь, поэтому введено понятие о действительном зерне, т.е. зерне, существующем в стали при данной температуре.
Размер действительного зерна аустенита обусловлен температурой нагрева, продолжительностью выдержки при ней и склонностью данной стали к росту зерна при нагреве.
Продолжительный нагрев доэвтектоидной (заэвтектоидной) стали при температурах, значительно превышающих А3 или Асm, приводит к образова-
Материаловедение. Учеб. пособие |
-196- |
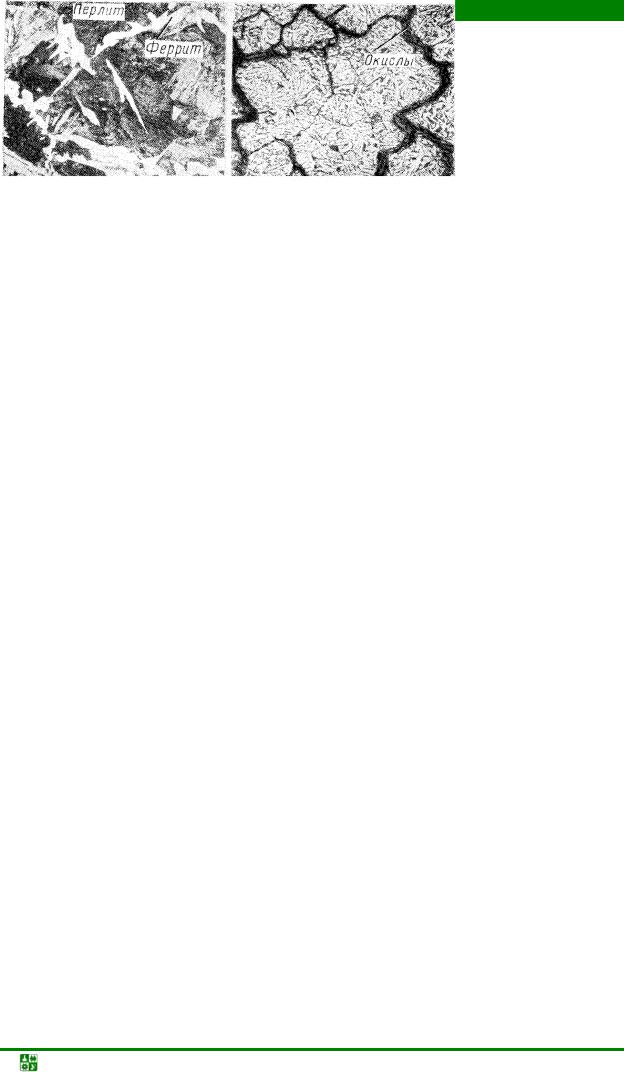
РАЗДЕЛ II. МАТЕРИАЛОВЕДЕНИЕ СТАЛЕЙ И ЧУГУНОВ
Глава 4. Стали, сплавы системы железо–углерод. Маркировка, структура, свойства сплавов
нию крупного действительного зерна как непосредственно при этой температуре, так и после охлаждения до 20 °С. Такой нагрев принято называть перегревом стали. Перегретая сталь характеризуется крупнокристаллическим изломом.
Рост видманштеттовых кристаллов феррита происходит при высоких температурах в условиях диффузии углерода (рис. 4.17, а).
а б
Рис. 4.17. Микроструктура стали, ×100: а – перегретой; б – пережженной
Перегрев может быть исправлен повторным нагревом стали доэвтектоидной до температуры выше точки А3, а эвтектоидной и заэвтектоидной –
выше А1.
Нагрев при еще более высокой температуре, чем нагрев, вызывающий перегрев, и к тому же в окислительной атмосфере, называют пережогом стали. Он сопровождается образованием по границам зерен окислов железа (рис. 4.17, б). При пережоге излом стали камневидный. Пережог – неисправимый дефект стали.
Величина зерна стали не оказывает существенного влияния на стандартный комплекс механических свойств, получаемых при испытании на статическое растяжение и твердость, но с ростом зерна резко снижается ударная вязкость, работа распространения трещины и повышается порог хладноломкости. Чем крупнее зерно, тем более сталь склонна к закалочным трещинам и деформациям. Все это следует учитывать при выборе режимов термической обработки.
4.8.4. Превращениеаустенитаприразличныхстепеняхпереохлаждения
Если сталь со структурой аустенита, полученной в результате нагрева до температуры выше Ас3 (для доэвтектоидной стали) или выше Асm (для заэвтектоидной стали), переохладить до температуры ниже А1, то аустенит оказывается в метастабильном состоянии и претерпевает превращение.
Для описания кинетики превращения переохлажденного аустенита пользуются экспериментально построенными диаграммами время–температура–
Материаловедение. Учеб. пособие |
-197- |
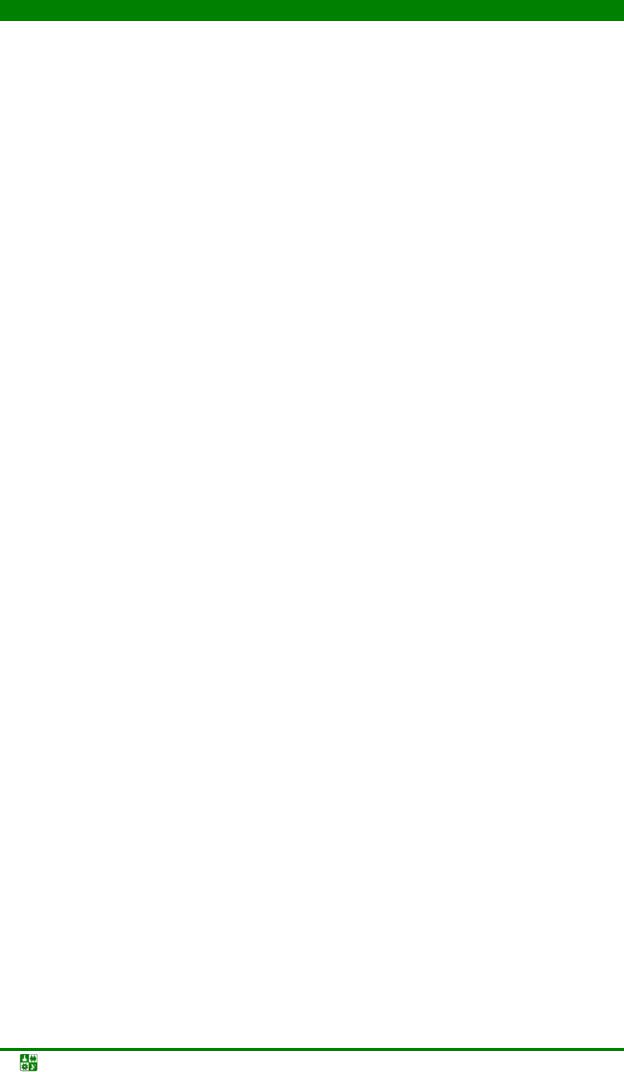
РАЗДЕЛ II. МАТЕРИАЛОВЕДЕНИЕ СТАЛЕЙ И ЧУГУНОВ
Глава 4. Стали, сплавы системы железо–углерод. Маркировка, структура, свойства сплавов
степень распада, или диаграммами изотермического превращения аустенита,
т.е. превращения, протекающего при постоянной температуре.
Для изучения изотермического превращения аустенита небольшие образцы стали нагревают до температур, соответствующих существованию стабильного аустенита (т.е. выше критической точки), а затем быстро охлаждают (переохлаждают) до температуры ниже А1 (например, до 700, 600, 500, 400, 300 °С и т.д.) и выдерживают при этих температурах различное время, в том числе и до полного распада аустенита. Степень его распада можно определять разными методами: микроскопическим, магнитным, дилатометрическим и др.
Результаты исследования описываются кинетической кривой, по которой можно оценить количество распавшегося аустенита в зависимости от времени, прошедшего с момента начала распада. Как видно из рис. 4.18, а, в течение некоторого промежутка времени (Н1, Н2, Н3) распад аустенита экспериментально не фиксируется. Этот период называют инкубационным.
По истечении этого периода аустенит начинает распадаться с образованием более стабильных структур. В области повышенных температур он протекает с образованием структуры, состоящей из феррита и цементита. Через различные промежутки времени (К1, К2, К3) процесс распада постепенно затухает и, наконец, полностью заканчивается или приостанавливается.
Построение таких кривых в изотермических условиях при разных температурах (t1, t2, t3) позволяет получить диаграмму изотермического превращения аустенита (рис. 4.18, б). Для этого нужно отрезки времени, соответствующие началу (Н1, Н2, Н3) и концу распада аустенита (К1, К2, К3) или какойто заранее принятой степени превращения для каждой из исследуемых температур (t1, t2, t3), перенести на график, на котором по оси абсцисс откладывают время, а по оси ординат – температуру, и одноименные точки соединить плавными кривыми. На диаграмме изотермического превращения аустенита (рис. 4.18, б) кривая 1 характеризует начало распада аустенита, а кривая 2 показывает время, необходимое для полного распада аустенита.
Область, лежащая левее кривой начала распада аустенита, относится к инкубационному периоду, в интервале температур и времени, определяемых этой областью, существует переохлажденный аустенит, практически не претерпевающий заметного распада. Длительность инкубационного периода характеризует устойчивость переохлажденного аустенита. С увеличением переохлаждения его устойчивость быстро уменьшается, достигая минимума, и далее вновь возрастает.
При температуре наименьшей устойчивости аустенита скорость превращения очень велика. Повышение устойчивости аустенита и уменьшение скорости его превращения при больших степенях переохлаждения определяется снижением скорости образования и роста новых фаз вследствие замедления процесса диффузии.
Материаловедение. Учеб. пособие |
-198- |
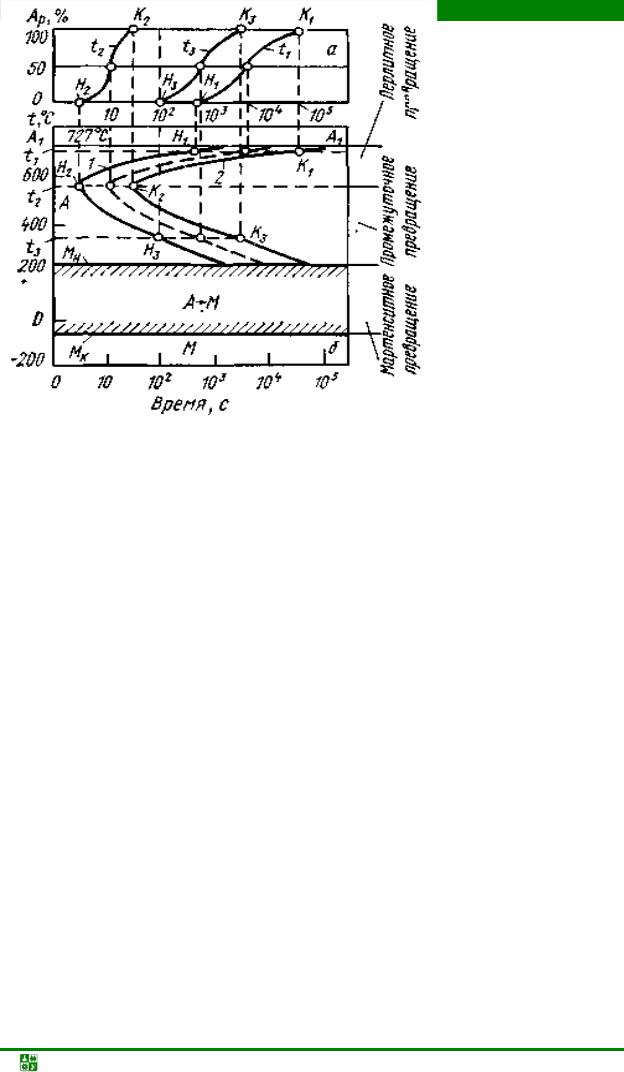
РАЗДЕЛ II. МАТЕРИАЛОВЕДЕНИЕ СТАЛЕЙ И ЧУГУНОВ
Глава 4. Стали, сплавы системы железо–углерод. Маркировка, структура, свойства сплавов
а
б
Рис. 4.18. Схема построения диаграммы изотермического превращения переохлажденного аустенита для эвтектоидной стали: а – кинетические кривые, б – диаграммы изотермического превращения аустенита
При переохлаждении аустенита до температуры, равной или ниже мартенситной точки (Мн), соответствующей температуре начала превращения переохлажденного аустенита в мартенсит, диффузионные процессы полностью подавляются и образование структуры, состоящей из феррита и цементита, становится невозможным. В этом случае протекает бездиффузионное превращение аустенита в структуру закаленной стали, называемую мартен-
ситом.
В зависимости от степени переохлаждения аустенита различают три температурные области или ступени превращения (рис. 4.18, б): перлитную, область промежуточного превращения (промежуточного между перлитным и мартенситным превращением) и мартенситную.
Перлитная область в углеродистых сталях распространяется на интервал температур от точки А1 до изгиба изотермической диаграммы (~ 550 °С). Промежуточное превращение протекает при температурах от изгиба кривой (~ 550 °С) до точки Мн. В результате превращения переохлажденного аустенита образуется структура, получившая название бейнита.
Ниже температуры, соответствующей точке Мн, переохлажденный аустенит бездиффузионно превращается в мартенсит.
Материаловедение. Учеб. пособие |
-199- |
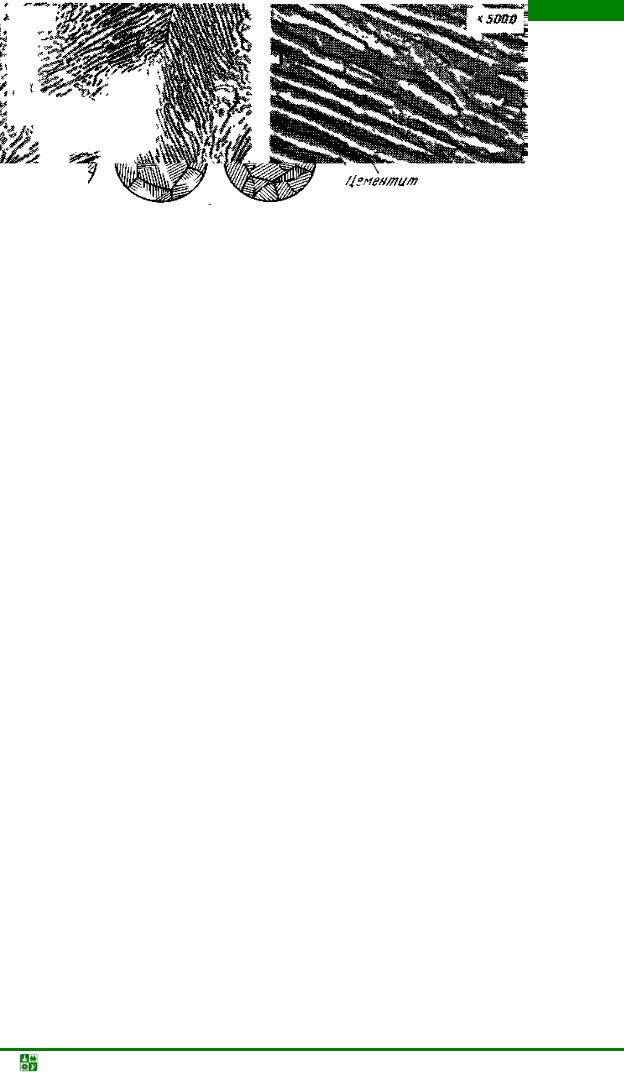
РАЗДЕЛ II. МАТЕРИАЛОВЕДЕНИЕ СТАЛЕЙ И ЧУГУНОВ
Глава 4. Стали, сплавы системы железо–углерод. Маркировка, структура, свойства сплавов
а
б
Рис. 4.19. Продукты распада аустенита: а – схемы образования (I – аустенит; II – образование зародыша цементита на границе зерна аустенита; III – образование пластины феррита; IV–VI – рост и образование новых пластин цементита и феррита (перлита); VII – перераспределение углерода при образовании перлита; 1 – высокая концентрация углерода – цементит (6,67 % С); 2 – низкая кон-
центрация углерода – феррит (0,02 % С); |
0 – межпластиночное расстояния); |
б – микроструктуры пластинчатого перлита |
при разном увеличении |
Перлитное превращение переохлажденного аустенита носит кристаллизационный характер и начинается по диффузионному механизму. Это следует из того, что аустенит, например, углеродистой стали (рис. 4.19), практически однородный по концентрации углерода, распадается с образованием феррита (почти чистое железо) и цементита, содержащего 6,67 % С. Ведущей, в первую очередь возникающей фазой при этом является карбид (цементит). Как правило, его зародыши образуются на границах зерен аустенита.
В результате роста частиц этого карбида прилегающий к нему объем аустенита обедняется углеродом, снижает свою устойчивость и испытывает полиморфное γ → α-превращение. При этом кристаллы феррита зарождаются на межфазных границах с цементитом, где этот процесс облегчен.
Дальнейший рост ферритных пластин ведет к обогащению окружающего аустенита углеродом, что затрудняет дальнейшее развитие γ → α-превращение. В обогащенном таким образом углеродом аустените зарождаются новые и растут ранее возникшие пластинки цементита. В результате происходит колониальный (совместный) рост кристаллов феррита и цементита, образующих перлитную колонию (рис. 4.19). Размер перлитных колоний («перлитное
Материаловедение. Учеб. пособие |
-200- |
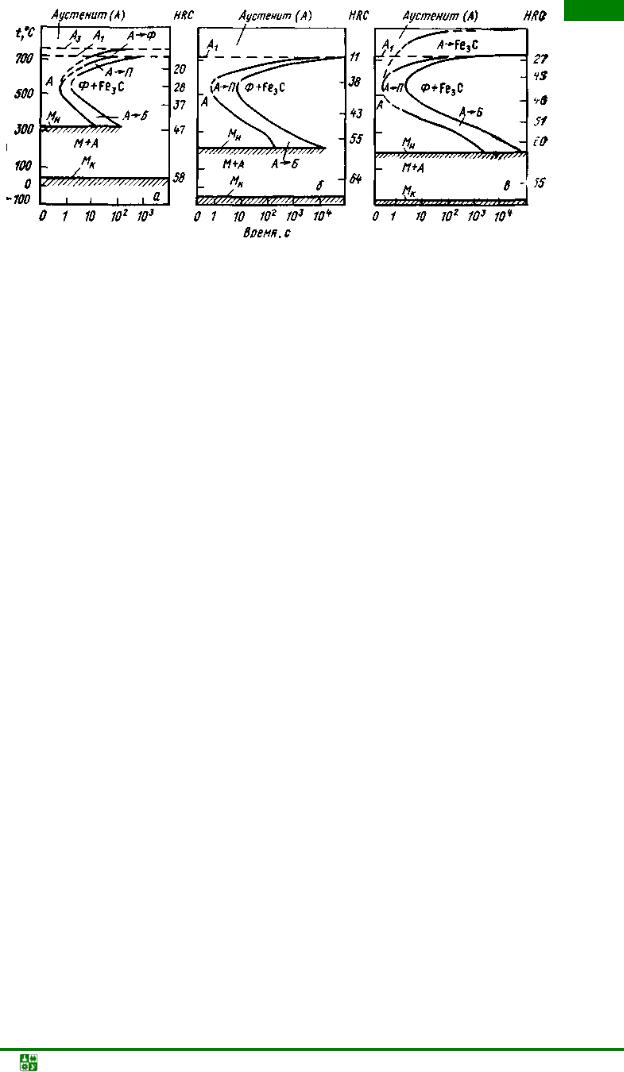
РАЗДЕЛ II. МАТЕРИАЛОВЕДЕНИЕ СТАЛЕЙ И ЧУГУНОВ
Глава 4. Стали, сплавы системы железо–углерод. Маркировка, структура, свойства сплавов
зерно») тем меньше, чем мельче зерно исходного аустенита и больше степень его переохлаждения.
Продукты перлитного превращения имеют пластинчатое строение. Чем больше переохлаждение, тем тоньше получающаяся феррито-цементитная структура, т.е. меньше величина межпластинчатого расстояния ( 0), равного усредненной сумме толщин двух пластинок феррита и цементита, и выше твердость. Пластинчатые структуры эвтектоидного типа часто определяют как перлит, сорбит и троостит (табл. 4.11).
|
|
|
|
Таблица 4.11 |
|
Характеристика продуктов распада аустенита |
|||
|
|
|
|
|
Структура |
|
Перлит |
Сорбит |
Троостит |
0, мкм |
|
0,6–1,0 |
0,25–0,3 |
0,1–0,15 |
НВ, МПа |
|
1800–2500 |
2500–3500 |
3500–4500 |
а б в
Рис. 4.20. Диаграммы изотермического распада переохлажденного аустенита а – доэвтектоидная сталь (0,45 % С); б – эвтектоидная сталь (0,8 % С); в – заэвтектоидная сталь (1,2 % С)
С увеличением степени дисперсности феррито-цементитной структуры (уменьшением 0), т.е. с понижением температуры его распада, твердость, временное сопротивление, пределы текучести и выносливости возрастают.
Изотермическое превращение аустенита в доэвтектоидных и заэвтектоидных сталях отличается от превращения в эвтектоидной стали тем, что в верхнем интервале температур сначала выделяются избыточные фазы: феррит (в доэвтектоидной стали) или цементит (в заэвтектоидной стали).
Начало выделения избыточного феррита (цементита) на диаграмме изотермического распада отмечается дополнительной кривой (рис. 4.20).
Увеличение содержания углерода в аустените доэвтектоидной концентрации повышает его устойчивость (кривые изотермической диаграммы сдвигаются вправо).
Материаловедение. Учеб. пособие |
-201- |
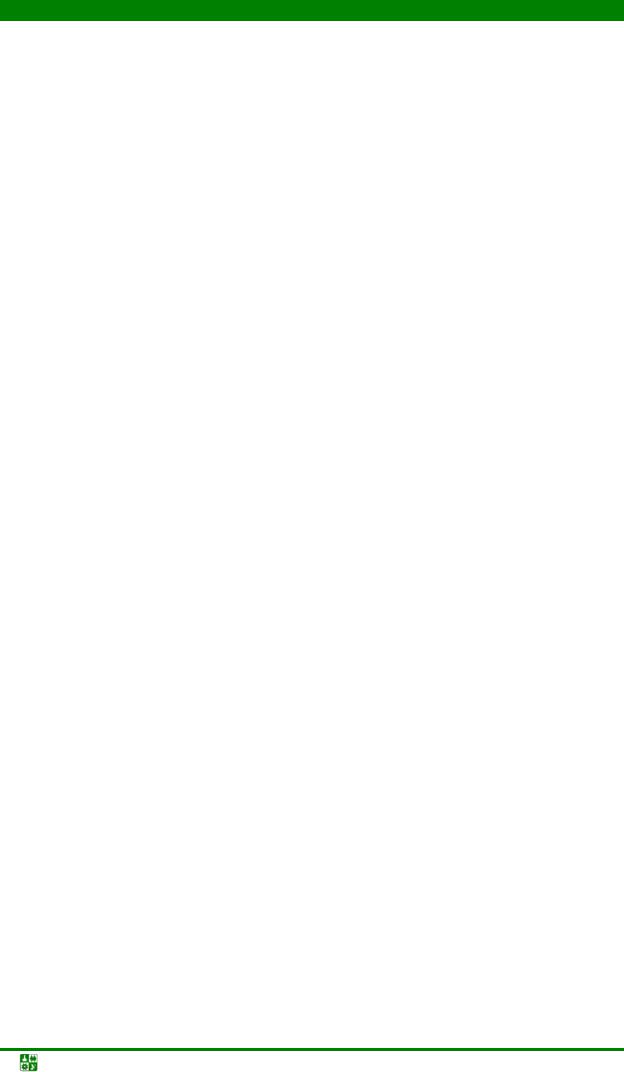
РАЗДЕЛ II. МАТЕРИАЛОВЕДЕНИЕ СТАЛЕЙ И ЧУГУНОВ
Глава 4. Стали, сплавы системы железо–углерод. Маркировка, структура, свойства сплавов
4.8.5. Мартенситноепревращение
Природа мартенсита. Мартенсит является упорядоченным пересыщенным твердым раствором внедрения углерода в α-железе. Если в равновесном состоянии растворимость углерода в α-железе при 20 °С не превышает 0,002 %, то его содержание в мартенсите может быть таким же, как в исходном аустените, т.е. может достигать 2,14 %.
Атомы углерода занимают октаэдрические поры в решетке α-железа (мартенсите) и сильно ее искажают. Мартенсит имеет тетрагональную решетку, в которой один период с больше другого – а. При увеличении содержания углерода высота тетрагональной призмы увеличивается, а размеры ее основания уменьшаются.
Отношение с/а = 1 + 0,046 С, где С – концентрация углерода в аустените (по массе).
Превращение носит бездиффузионный характер, т.е. оно не сопровождается диффузионным перераспределением атомов углерода и железа в решетке аустенита. Мартенситное превращение осуществляется путем сдвига и не сопровождается изменением состава твердого раствора.
Сдвиговый механизм превращения отличается закономерным кооперативным направленным смещением атомов в процессе перестройки решетки. Отдельные атомы смещаются относительно друг друга на расстояния, не превышающие межатомные, сохраняя взаимное соседство. Это приводит к макроскопическому сдвигу, внешним проявлением которого является игольчатый микрорельеф на поверхности металлического шлифа (рис. 4.21, а). В процессе превращения кристаллы мартенсита сопряжены с аустенитом по определенным кристаллографическим плоскостям и межфазная граница не образуется. При мартенситном превращении происходит одновременный и направленный групповой сдвиг атомов в решетке аустенита.
Пока на границе мартенсита и аустенита существует сопряженность решеток (когерентность), скорость образования и роста кристаллов мартенсита очень велика ~ 103 м/с.
Диффузионный переход атомов из кристаллов аустенита в мартенсит при низких температурах невозможен. Дальнейшее превращение протекает в результате образования новых кристаллов мартенсита.
Материаловедение. Учеб. пособие |
-202- |
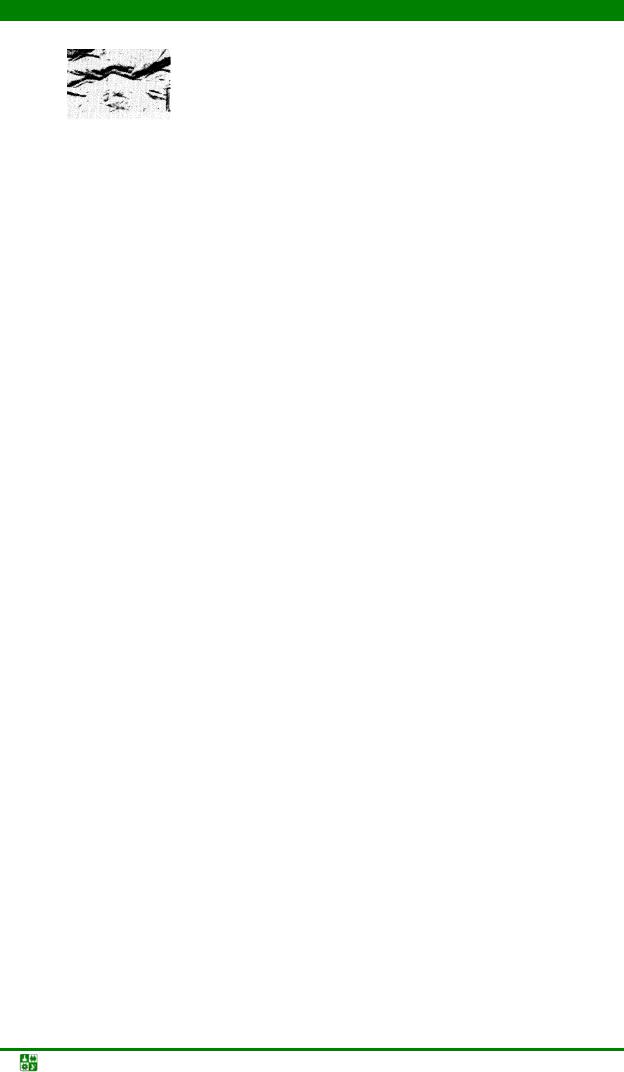
РАЗДЕЛ II. МАТЕРИАЛОВЕДЕНИЕ СТАЛЕЙ И ЧУГУНОВ
Глава 4. Стали, сплавы системы железо–углерод. Маркировка, структура, свойства сплавов
а |
б |
в |
г |
Рис. 4.21. Микроструктура мартенсита: а – мартенситныйрельеф; б – высокоуглеродистый пластинчатый мартенсит и остаточный аустенит, ×500; в – низкоуглеродистый реечный мартенсит, ×2 700; г – мартенсит (реечный) стали, содержащей 0,45 % С, ×1 000
Кинетика мартенситного превращения. Мартенситное превращение в общем случае не удается подавить быстрым охлаждением, как это может быть при диффузионных превращениях, протекающих по обычной кристаллизационной кинетике. Превращение начинается сразу при температуре Мн и происходит не в изотермических условиях, а в интервале температур. При переохлаждении до температуры, соответствующей точке Мн, аустенит начинает превращаться в мартенсит.
Чтобы мартенситное превращение развивалось, необходимо непрерывно охлаждать сталь ниже температуры Мн. Чем ниже температура, тем больше образуется мартенсита. Количество мартенсита при этом возрастает в результате образования все новых и новых кристаллов, а не вследствие роста уже возникших кристаллов, имеющих некогерентную границу. Температуру окончания мартенситного превращения обозначают Мк. Положение точек Мн и Мк не зависит от скорости охлаждения и обусловлено химическим составом аустенита. Чем больше в аустените углерода, тем ниже температура точек Мн и Мк (рис. 4.22). Все легирующие элементы, за исключением кобальта и алюминия, понижают точки Мн и Мк.
Мартенситное превращение очень чувствительно к напряжениям, а деформация аустенита может вызывать превращение даже при температурах
выше Мн.
Кристаллы мартенсита в зависимости от состава стали, а следовательно, и от температуры своего образования могут иметь различные морфологию и субструктуру. Различают два типа мартенсита – пластинчатый и реечный.
Материаловедение. Учеб. пособие |
-203- |
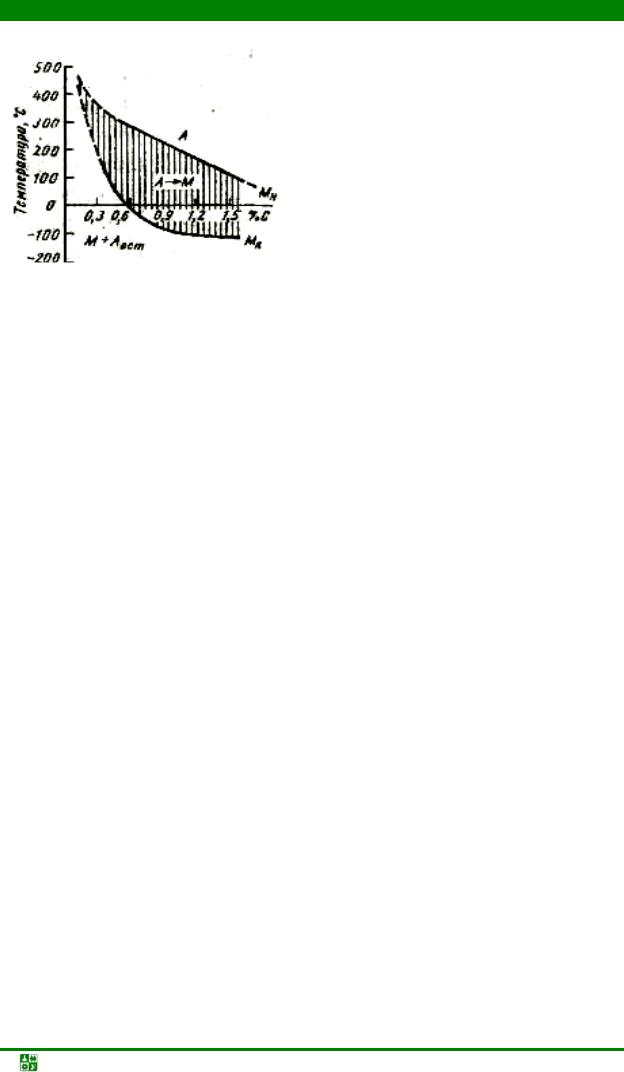
РАЗДЕЛ II. МАТЕРИАЛОВЕДЕНИЕ СТАЛЕЙ И ЧУГУНОВ
Глава 4. Стали, сплавы системы железо–углерод. Маркировка, структура, свойства сплавов
Рис. 4.22. Температура мартенситных точек Мн и Мк при различном содержании углерода в сталях
Пластинчатый мартенсит образуется в высокоуглеродистых сталях, характеризующихся низкой температурой мартенситной точки.
На рис. 4.21, б приведена микроструктура такого мартенсита. Его кристаллы представляют собой широкие пластины. В плоскости шлифа они имеют вид игл. Наиболее часто (конструкционные углеродистые и легированные стали) кристаллы мартенсита имеют форму тонких реек (реечный мартенсит), вытянутых в одном направлении (рис. 4.21, в, г). Чаще образуется и наблюдается пакет из реек.
Размеры кристаллов любой морфологии мартенсита определяются величиной исходного зерна аустенита. Они тем крупнее, чем больше зерно аустенита. Первая пластина мартенсита имеет протяженность, соответствующую поперечному размеру зерна аустенита. Кристаллы, образующиеся при более низких температурах, стеснены в своем развитии и имеют меньшие размеры.
Остаточный аустенит. Мартенситное превращение не протекает до конца при комнатной температуре, поэтому в закаленных сталях, имеющих точку Мк ниже 20 °С, а именно в углеродистых сталях, содержащих свыше 0,4–0,5 % С, присутствует остаточный аустенит. Его количество тем больше, чем ниже температура точек Мн и Мк, т.е. чем выше содержание в аустените углерода и легирующих элементов (за исключением Со и А1).
Стабилизация аустенита. Если задержать на некоторое время охлаждение при температуре, лежащей ниже температуры, соответствующей точке Мн, например 20 °С, то аустенит, сохранившийся не превращенным при охлаждении до этой температуры, становится более устойчивым. Количество образующегося в итоге мартенсита оказывается меньше, чем при непрерывном охлаждении.
Характерной особенностью мартенсита является его высокая твердость и прочность. Твердость мартенсита возрастает с увеличением в нем содержания углерода (рис. 4.23); в стали с 0,6–0,7 % С твердость мартенсита 65 НRС, что во много раз больше твердости феррита.
Материаловедение. Учеб. пособие |
-204- |
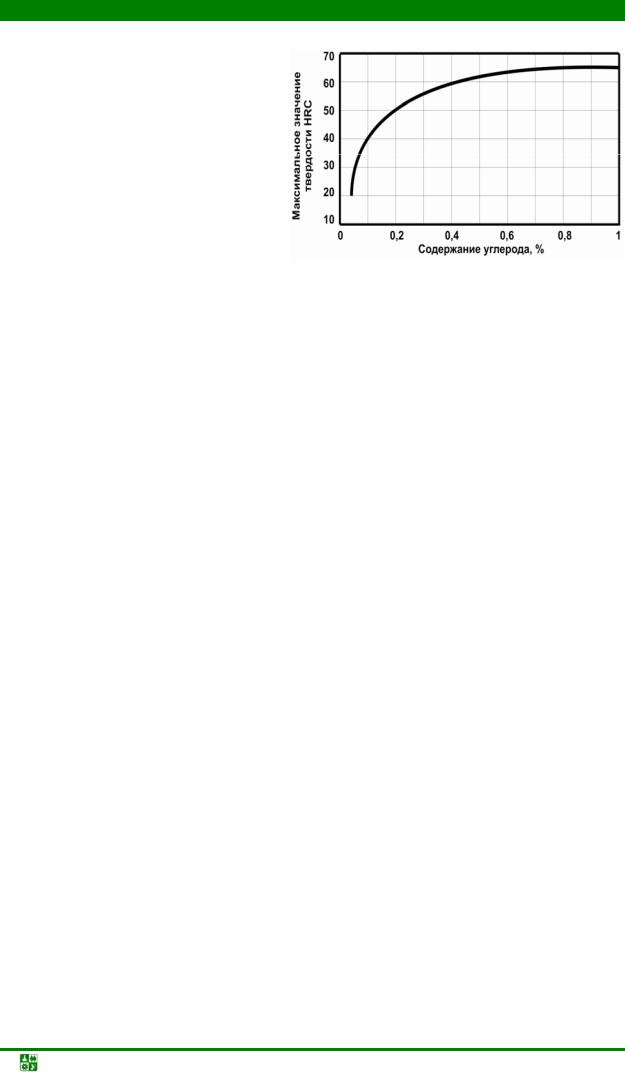
РАЗДЕЛ II. МАТЕРИАЛОВЕДЕНИЕ СТАЛЕЙ И ЧУГУНОВ
Глава 4. Стали, сплавы системы железо–углерод. Маркировка, структура, свойства сплавов
Рис. 4.23. Твердость мартенсита в зависимости от содержания в нем углерода
Временное сопротивление низкоуглеродистого мартенсита (0,025 % С) составляет ~ 1 000 МПа, а при 0,6–0,8 % С достигает 2 600–2 7 00 МПа.. Однако с повышением в мартенсите содержания углерода возрастает склонность его к хрупкому разрушению. Мартенсит, содержащий свыше 0,35–0,4
%С, обладает пониженным сопротивлением зарождению развитию трещины
иразрушается хрупко.
Мартенсит, по сравнению с другими структурными составляющими стали, и особенно с аустенитом, имеет наибольший удельный объем. Увеличение удельного объема при образовании мартенсита является одной из основных причин возникновения при закалке больших внутренних напряжений, вызывающих деформацию изделий или даже появление трещин.
4.8.6. Отжигсталей
Существует несколько разновидностей отжига, из них для конструкционных сталей наибольшее применение находит перекристаллизационный отжиг, а для инструментальных сталей – сфероидизирующий отжиг.
Конструкционные стали чаще всего содержат углерод в количестве до 0,7 %, т.е. являются доэвтектоидными сталями.
Перекристаллизационный отжиг проводят для снижения твердости, повышения пластичности и получения однородной мелкозернистой структуры. Одновременно при отжиге полностью снимаются остаточные напряжения.
Полуфабрикаты из конструкционных сталей после литья или горячего деформирования из-за ускоренного охлаждения с высоких температур могут иметь повышенную твердость, что затруднит их обработку резанием и приведет к понижению пластичности.
Характерный структурный дефект стальных отливок – крупнозернистость.
При ускоренном охлаждении крупнозернистого аустенита создаются условия для образования видманштеттовой структуры. Типичная структура литой стали и видманштеттовая структура горячедеформированной стали показана на рис. 4.17, а.
Материаловедение. Учеб. пособие |
-205- |
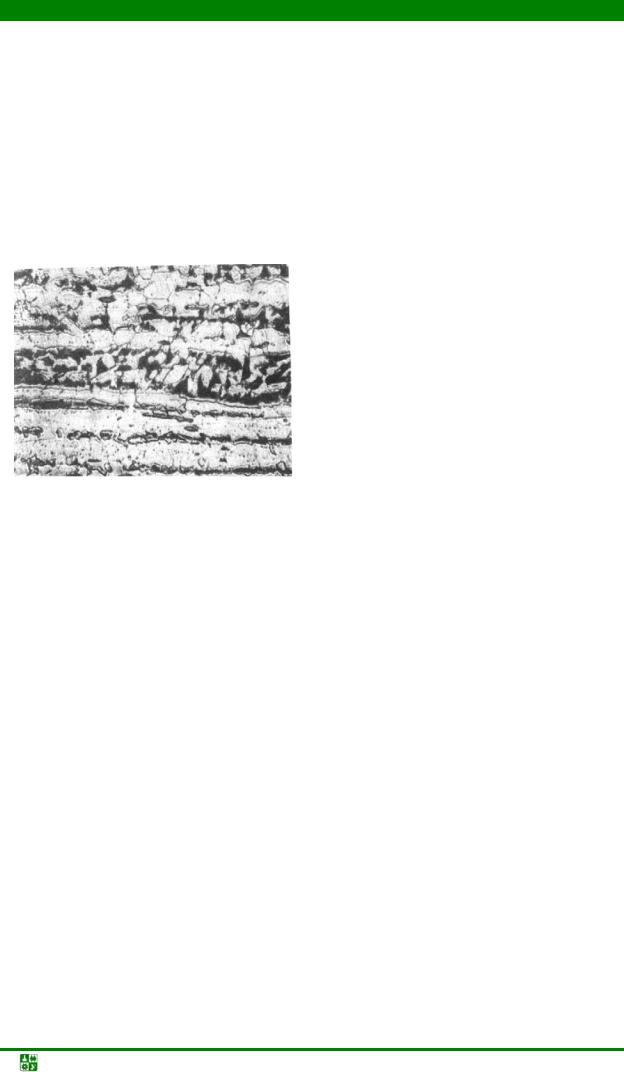
РАЗДЕЛ II. МАТЕРИАЛОВЕДЕНИЕ СТАЛЕЙ И ЧУГУНОВ
Глава 4. Стали, сплавы системы железо–углерод. Маркировка, структура, свойства сплавов
Строчечная структура стали значительно чаще возникает из-за загрязнения стали неметаллическими включениями, обычно сульфидами, а также в результате ликвации фосфора. При обработке давлением включения вытягиваются. Феррит, зарождаясь на вытянутых включениях, образует вытянутые скопления. Строчечность структуры, вызванная неметаллическими включениями, не исправляется отжигом. Горячекатаная сталь со строчечной структурой (рис. 4.24) имеет худшие механические свойства (прочность, пластичность и вязкость) в поперечном и высотном направлениях по сравнению с основным направлением деформации.
Рис. 4.24. Строчечная структура конструкционной углеродистой стали (сернистые включения – центры кристаллизации
доэвтектоидного феррита). ×250
Для полной перекристаллизации структуры конструкционные стали нагревают до температуры, превышающей температуру Аст на 30–50 °С. После сквозного прогрева изделия следует медленно охлаждать, чтобы обеспечить в результате распада аустенита равновесную феррито-перлитную структуру и, соответственно, низкую твердость и высокую пластичность.
Скорость охлаждения при отжиге выбирают в зависимости от степени легированности стали.
Углеродистые стали получаются достаточно мягкими при скорости охлаждения 100–200 °С/ч. Легированные стали с более высокой устойчивостью переохлаждённого аустенита нужно охлаждать медленнее, со скоростью 20– 70 °С/ч. Высоколегированные стали экономичнее подвергать изотермическому отжигу, т.е. дать выдержку при температуре немного меньшей Аr1, чтобы получить продукты распада аустенита с низкой твёрдостью.
Для заэвтектоидных сталей перекристаллизационный отжиг с нагревом выше Асm (линия ES) вообще не используют, т.к. при медленном охлаждении после такого нагрева образуется грубая сетка вторичного цементита, ухудшающего механические свойства. К заэвтектоидным углеродистым сталям широко применяют отжиг с нагревом до 740–780 °С и последующим медленным охлаждением. После такого нагрева в аустените остается большое число нерастворившихся включений цементита, которые служат центрами кристаллизации во время распада аустенита при охлаждении.
В результате образуется структура зернистого перлита (сферодита), почему этот отжиг и называют сфероидизирующим.
Материаловедение. Учеб. пособие |
-206- |
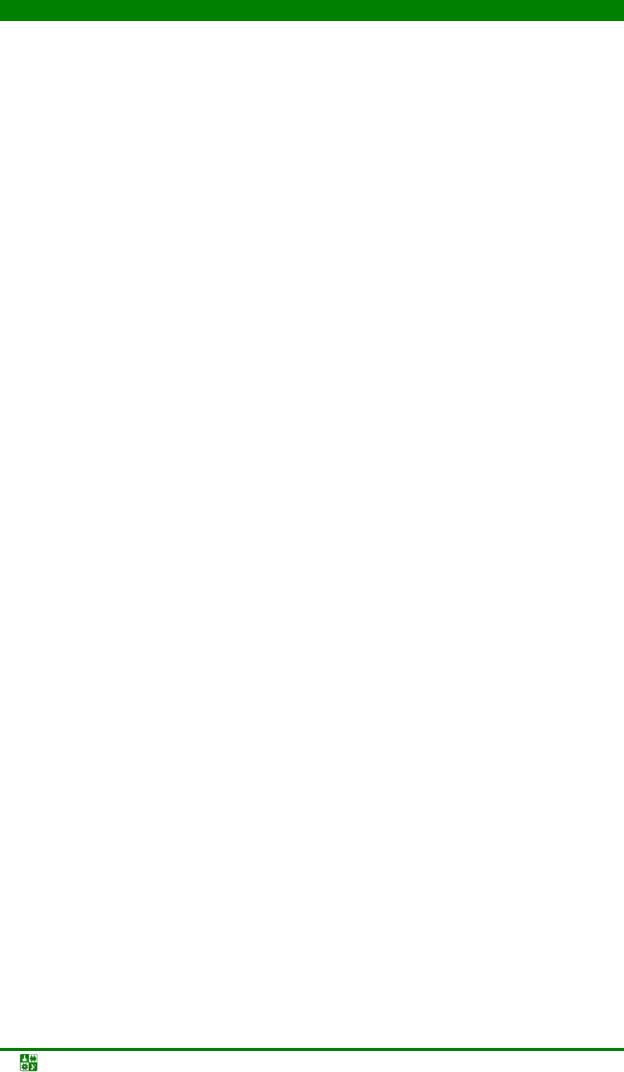
РАЗДЕЛ II. МАТЕРИАЛОВЕДЕНИЕ СТАЛЕЙ И ЧУГУНОВ
Глава 4. Стали, сплавы системы железо–углерод. Маркировка, структура, свойства сплавов
Для режима сфероидизирующего отжига заэвтектоидных сталей характерен узкий температурный «интервал отжигаемости». Нижняя его граница должна находиться выше точки А1, а верхняя граница не должна быть слишком высокой, т.к. иначе из-за растворения в аустените центров карбидного выделения при охлаждении образуется пластинчатый перлит. Так, если точки Асm и Ас1 сходятся при эвтектоидной концентрации, то у сталей, близких к эвтектоидному составу, «интервал отжигаемости» особенно узок. Например, для сталей У9А и У10А граница этого интервала 740–750 °С, в то время как для сталей У11А, У12А и У13А они находятся в пределах 750–780 °С.
Конечная структура зависит от скорости охлаждения и температуры сфероидизирующего отжига. Чем меньше скорость охлаждения, тем до больших размеров вырастают глобули карбида при распаде аустенита. Регулируя скорость охлаждения, можно получить структуры глобулярного перлита от точечного до крупнозернистого. Более мелкозернистый перлит обладает повышенной твердостью.
Сфероидизирующему отжигу подвергают углеродистые и легированные инструментальные и шарикоподшипниковые стали. Сталь со структурой зернистого перлита обладает наименьшей твердостью, легче обрабатывается резанием, что особенно важно, например, для работы автоматических линий в условиях массового подшипникового производства. Кроме того, зернистый перлит является оптимальной исходной структурой перед закалкой. Сталь со структурой зернистого перлита имеет меньшую склонность к росту аустенитного зерна, более широкий допустимый интервал закалочных температур, меньшую склонность к растрескиванию при закалке, более высокие прочность и вязкость после закалки (мелкие глобули равномерно распределены в мартенсите закаленной заэвтектоидной стали).
Если при однократном отжиге не произошло полной сфероидизации цементита, то можно применять циклический, или маятниковый, отжиг, являющийся разновидностью сфероидизирующего.
Изотермический отжиг. Малая степень переохлажденного аустенита, необходимая при отжиге, может быть получена не только при непрерывном охлаждении стали с печью. Другой путь – ступенчатое охлаждение с изотермической выдержкой в интервале перлитного превращения. Такая термообработка называется изотермическим отжигом. После нагрева до температуры выше А3 сталь ускоренно охлаждают до температуры изотермической выдержки, которая находится ниже точки А1. Затем проводят ускоренное охлаждение на воздухе; мелкие изделия простой конфигурации можно охладить в подогретой воде.
Чем ближе температура изотермической выдержки к точке А1, тем больше межпластинчатое расстояние в перлите и мягче сталь, но больше и время превращения. Так как основное назначение изотермического отжига – смягчение стали, то выбирают такую температуру изотермической выдержки (на 30–100 °С ниже температуры А1), при которой получается достаточное смягчение стали за сравнительно небольшой промежуток времени.
Материаловедение. Учеб. пособие |
-207- |
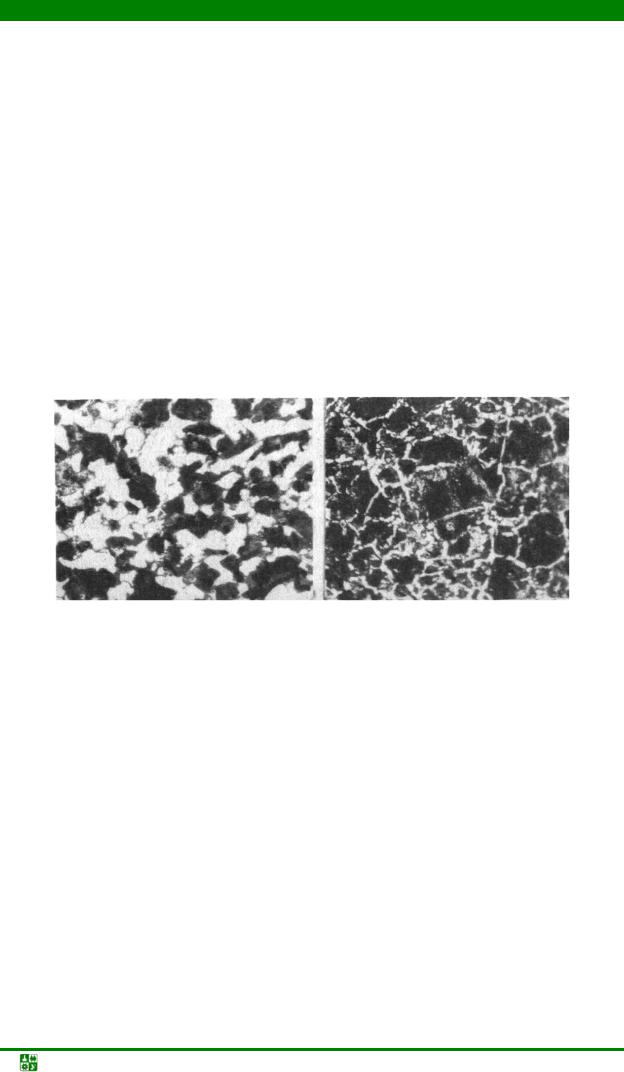
РАЗДЕЛ II. МАТЕРИАЛОВЕДЕНИЕ СТАЛЕЙ И ЧУГУНОВ
Глава 4. Стали, сплавы системы железо–углерод. Маркировка, структура, свойства сплавов
Изотермический отжиг по сравнению с обычным отжигом имеет два преимущества. Прежде всего он может дать выигрыш во времени, если суммарное время ускоренного охлаждения, изотермической выдержки и последующего ускоренного охлаждения меньше времени медленного непрерывного охлаждения изделия вместе с печью.
Нормализация сталей. Нормализации, так же как и перекристализационному отжигу, чаще всего подвергают конструкционные стали после горячей обработки давлением и фасонного литья. Нормализация отличается от отжига в основном условиями охлаждения после нагрева до температуры на 50–70 °С выше температуры Ас3, сталь охлаждают на спокойном воздухе.
Нормализация – более экономичная термическая операция, чем отжиг, т.к. меньше времени затрачивается на охлаждение стали. Кроме того, нормализация, обеспечивая полную перекристализацию структуры, приводит к получению более высокой прочности стали, поскольку при ускорении охлаждения распад аустенита происходит при более низких температурах.
а |
б |
Рис. 4.25. Микроструктура стали (0,4 % С), ×300: а – после отжига; б – после нормализации
После нормализации углеродистых и низколегированных сталей так же, как и после отжига, образуется феррито-перлитная структура, однако имеются и существенные структурные отличия (рис. 4.25).
При ускоренном охлаждении, характерном для нормализации, доэвтектоидный феррит при прохождении температурного интервала Ar3–Ar1 выделяется на границах зёрен аустенита, поэтому кристаллы феррита образуют сплошные или разорванные оболочки вокруг зёрен аустенита – ферритную сетку.
Нормализация позволяет несколько уменьшить анизотропию свойств, вызванную наличием в горячедеформированной стали вытянутых неметаллических включений. При ускоренном охлаждении (по сравнению с отжигом) возникает больше самопроизвольно образующихся центров кристаллизации, поэтому строчечность структуры менее резко выражена. Это дополнительное преимущество данного вида обработки.
Материаловедение. Учеб. пособие |
-208- |
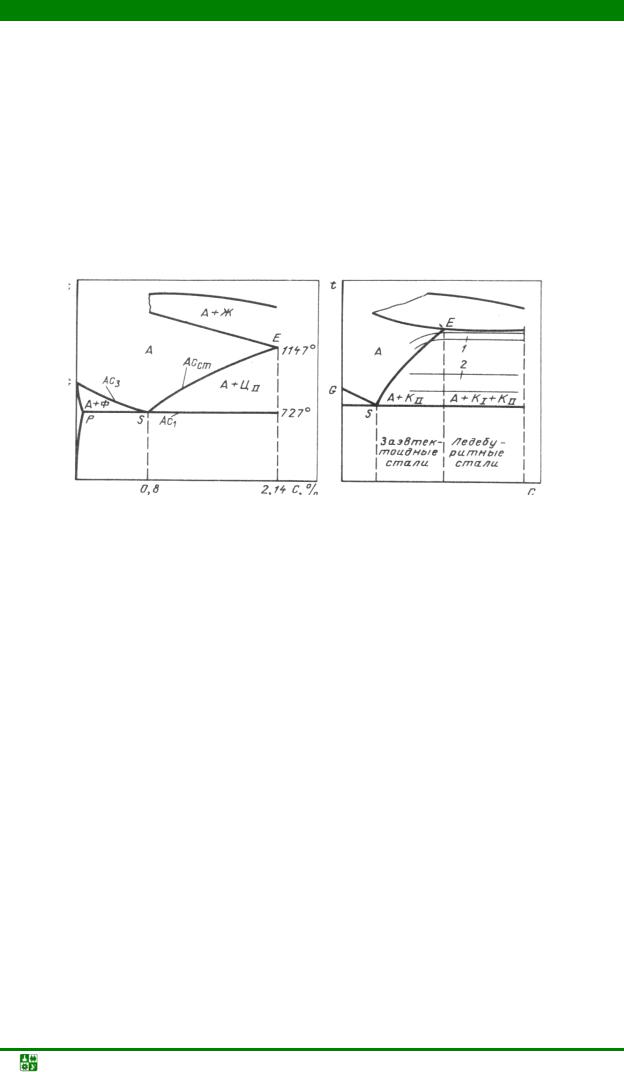
РАЗДЕЛ II. МАТЕРИАЛОВЕДЕНИЕ СТАЛЕЙ И ЧУГУНОВ
Глава 4. Стали, сплавы системы железо–углерод. Маркировка, структура, свойства сплавов
Свойства нормализованных горячекатаных полуфабрикатов существенно зависят от сечения: чем меньше сечение, тем быстрее произойдёт охлаждение на спокойном воздухе и тем выше прочность стали.
4.8.7.Особенностизакалкисталей
Вбольшинстве случаев при закалке желательно получить структуру наивысшей твёрдости, т.е. мартенсит, при последующем отпуске которого можно понизить твёрдость и повысить пластичность стали.
а |
б |
Рис. 4.26. Оптимальные температуры нагрева под закалку для сталей: а – доэвтектоидных, заэвтектоидных; б – высоколегированных ледебуритных
Доэвтектоидные стали, как правило, подвергают полной закалке, при этом оптимальной температурой нагрева является температура Ас3 + (30–50 °С). Такая температура обеспечивает получение при нагреве мелкозернистого аустенита и соответственно после охлаждения – мелкокристаллического мартенсита. Недогрев до температуры Ас3 приводит к сохранению в структуре кристаллов доэвтектоидного феррита, что при некотором уменьшении прочности обеспечивает повышенную пластичность закаленной стали (рис. 4.26).
Заэвтектоидные стали подвергают неполной закалке. Оптимальная температура нагрева углеродистых и низколегированных сталей – темпера-
тура Ас1 + (30–50 °С).
После закалки заэвтектоидная сталь приобретает структуру, состоящую из мартенсита и цементита. Кристаллы цементита твёрже кристаллов мартенсита, поэтому при неполной закалке заэвтектоидные стали имеют более высокую твёрдость, чем при полной закалке. Высоколегированные инструментальные стали ледебуритного класса (рис. 4.26) для повышения теплостойкости нагревают при закалке до очень высоких температур (область 1), близких к эвтектической. При этом происходит распад всех вторичных карбидов, аустенит обогащается не только углеродом, но и легирующими элементами,
Материаловедение. Учеб. пособие |
-209- |
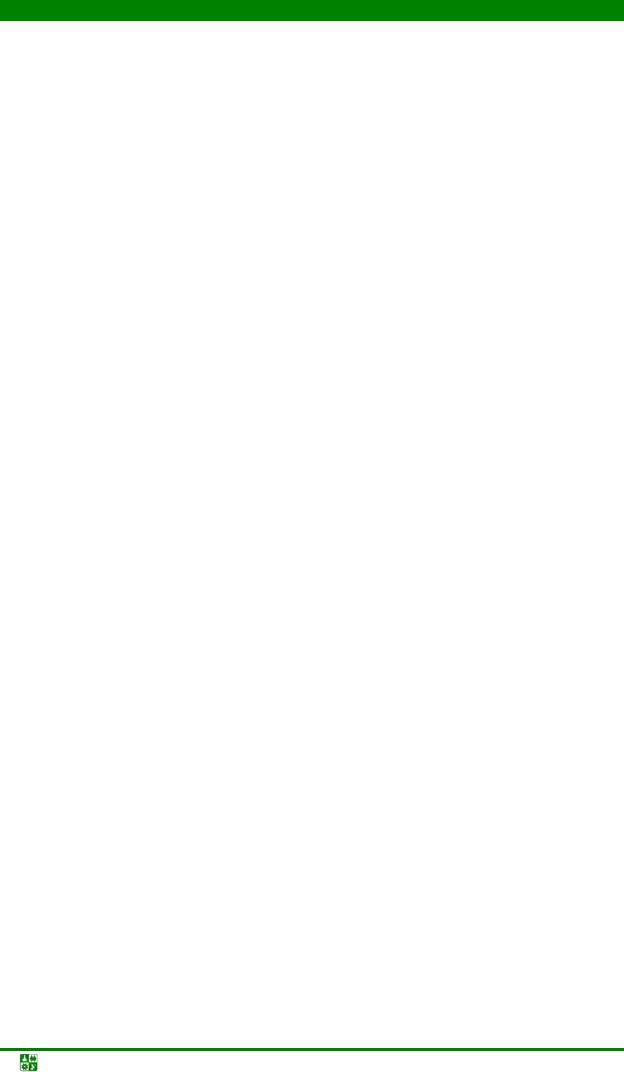
РАЗДЕЛ II. МАТЕРИАЛОВЕДЕНИЕ СТАЛЕЙ И ЧУГУНОВ
Глава 4. Стали, сплавы системы железо–углерод. Маркировка, структура, свойства сплавов
содержащимися в карбидах. В результате получается высоколегированный, а следовательно, и теплостойкий мартенсит.
Для получения мартенситной структуры необходимо переохладить аустенит до температуры мартенситного превращения, следовательно, скорость охлаждения должна превышать критическую скорость υкр.
Продолжительность нагрева. Скорость нагрева и время выдержки при температуре нагрева для закалки зависят от химического состава стали и размеров обрабатываемых деталей. Чем больше размеры и сложнее конфигурация закаливаемых деталей или инструмента, тем медленнее происходит нагрев. Чем больше в стали углерода, легирующих элементов, тем менее она теплопроводна. Нагревают детали из высокоуглеродистых и легированных сталей медленно, равномерно и с повышенной выдержкой нагрева. Величина напряжений должна быть всегда ниже допустимой величины, в противном случае в изделии при нагреве могут образоваться трещины. Выдержка при термической обработке необходима для того, чтобы изделия полностью прогрелись после достижения заданной температуры и произошли структурные превращения в металле. Время выдержки зависит в основном от структуры металла и примерно равно 1 мин для углеродистых сталей и 1,5–2,0 мин для сталей легированных на 1 мм диаметра.
Время нагрева определяют для каждого вида деталей или инструмента
(табл. 4.12).
Таблица 4.12
Среднее время нагрева деталей из углеродистых сталей под закалку в различных средах
Нагревательные |
Температура |
Время нагрева, с, 1 мм диаметра |
|||
или толщины деталей с сечением |
|||||
устройства |
нагрева, °С |
||||
круглым |
квадратным |
прямоугольным |
|||
|
|
||||
Электрическая печь |
800 |
40–50 |
50–60 |
60–75 |
|
Пламенная печь |
800 |
35–40 |
45–50 |
55–60 |
|
Соляная ванна |
800 |
12–15 |
15–18 |
18–22 |
Для охлаждения стальных деталей при закалке в качестве закалочных сред применяют воду, водные растворы солей, расплавленные соли и минеральные масла.
Закалочные среды с разной интенсивностью отводят тепло от нагретых под закалку деталей. При выборе закалочной среды учитывают химический состав стали и степень допустимой деформации. Единой универсальной среды для закалки стали не имеется, поэтому пользуются различными средами
(табл. 4.13).
Материаловедение. Учеб. пособие |
-210- |
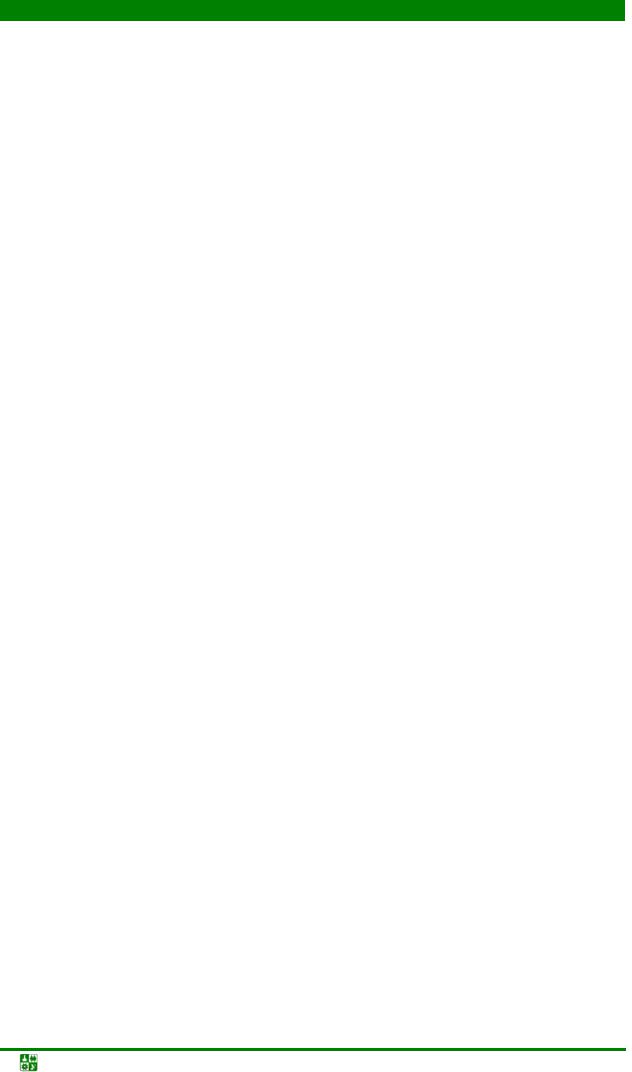
РАЗДЕЛ II. МАТЕРИАЛОВЕДЕНИЕ СТАЛЕЙ И ЧУГУНОВ
Глава 4. Стали, сплавы системы железо–углерод. Маркировка, структура, свойства сплавов
Таблица 4.13
Скорость охлаждения стали в зависимости от закалочных сред
|
Скорость охлаждения, град/с, |
|
Закалочная среда |
в интервале температур, °С |
|
|
600–500 |
300–200 |
|
|
|
Вода: |
|
|
при 20 °С (спокойная) |
600 |
270 |
при 20 °С (циркулирующая) |
350 |
700 |
Дистиллированная вода при 20 °С |
250 |
200 |
10 %-е водные растворы: |
|
|
поваренной соли |
1 100 |
300 |
едкого натра |
1 200 |
300 |
соды (Na2CO3) |
800 |
270 |
Минеральное масло при 20 °С |
120 |
25 |
Эмульсия (смесь масла и воды) |
70 |
200 |
Закаливаемость и прокаливаемость. Это важнейшие характеристики сталей. Закаливаемость определяется твёрдостью поверхности закаленной детали и зависит главным образом от содержания углерода в стали. При закалке различных деталей поверхность их, как правило, охлаждается со скоростью, большей υкр, следовательно, на поверхности образуется мартенсит, обладающий высокой твёрдостью.
Если скорость охлаждения сердцевины при закалке будет меньше υкр, то деталь не прокалится насквозь, т.е. там не образуется мартенсит. Прокаливаемостью называют способность стали закаливаться на определённую глубину. При оценке прокаливаемости закаленным считается слой, в котором содержится не менее 50 % мартенсита (полумартенситная зона). Установлено, что легирование стали любыми элементами, кроме кобальта, увеличивает прокаливаемость, т.к. при этом повышается устойчивость переохлаждённого аустенита.
4.8.8. Способызакалкисталей. Дефекты, возникающиепризакалке
Способы закалки сталей. Основные способы закалки стали – закалка в одном охладителе, в двух средах, струйчатая, с самоотпуском, ступенчатая и изотермическая.
Закалка в одном охладителе. Деталь, нагретую до температуры закалки, погружают в закалочную жидкость, где она находится до полного охлаждения. Детали из углеродистых сталей охлаждают в воде, а детали из легированных сталей – в масле. Высокоуглеродистые стали закаливают с подстуживанием, это уменьшает внутренние напряжения в деталях и исключает образование трещин.
Материаловедение. Учеб. пособие |
-211- |
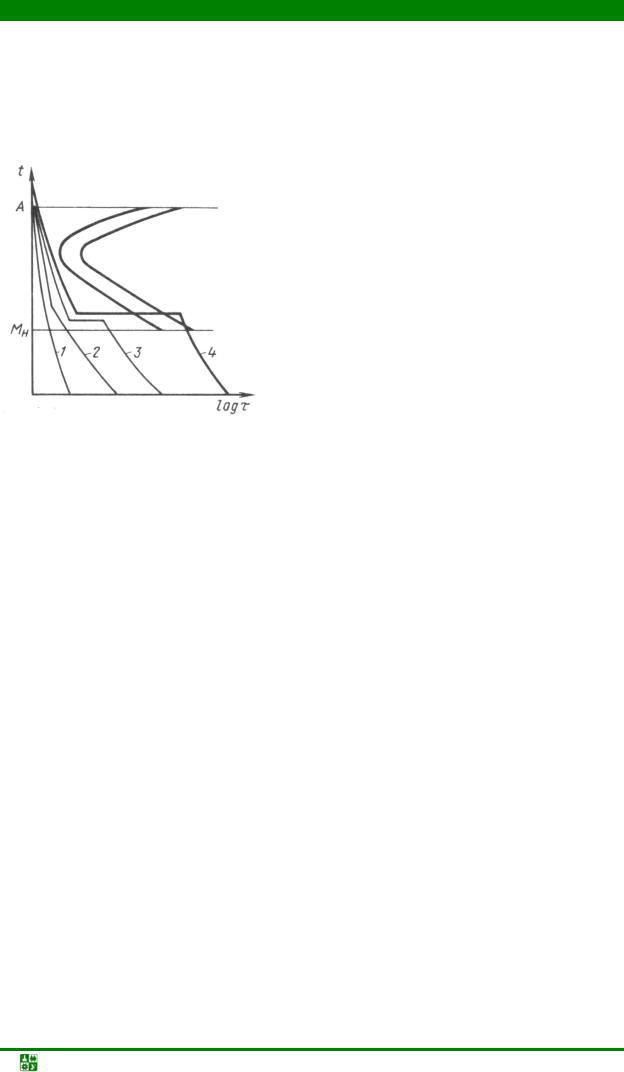
РАЗДЕЛ II. МАТЕРИАЛОВЕДЕНИЕ СТАЛЕЙ И ЧУГУНОВ
Глава 4. Стали, сплавы системы железо–углерод. Маркировка, структура, свойства сплавов
Закалка в двух средах, или прерывистая закалка (рис. 4.27). Деталь сначала охлаждают в быстро охлаждающей среде – воде, а затем переносят её в медленно охлаждающую среду – масло. Такой способ применяется при закалке инструмента, изготовленного из высокоуглеродистой стали.
Рис. 4.27. Способы охлаждения при закалки сталей: 1 – непрерывное охлаждение; 2 – закалка в двух средах; 3 – ступенчатая закалка; 4 – изотермическая закалка
Струйчатая закалка. Детали, нагретые до температуры закалки, охлаждают струёй воды. Такой способ применяют для закалки внутренних поверхностей, высадочных штампов, матриц и другого инструмента, у которого рабочая поверхность должна иметь структуру мартенсита. При струйчатой закалке не образуется паровая рубашка, что обеспечивает более глубокую прокаливаемость, чем при простой закалке в воде.
Закалка с самоотпуском. Детали выдерживают в охлаждающей среде не до полного охлаждения, а до определённой стадии, чтобы сохранить в сердцевине детали тепло, необходимое для самоотпуска.
Ступенчатая закалка. При этом способе закалки нагретые детали охлаждают сначала до температуры несколько выше точки Мн (в горячем масле или расплавленной соли), затем после короткой выдержки при этой температуре (до начала промежуточных превращений) охлаждают на воздухе.
Изотермическая закалка. Детали нагревают до заданной температуры и охлаждают в изотермической среде до 220–350 °С, что несколько превышает температуру начала мартенситного превращения. Выдержка деталей в закалочной среде должна быть достаточной для полного превращения аустенита в игольчатый троостит. После этого производится охлаждение на воздухе. При изотермической закалке выдержка значительно больше, чем при ступенчатой.
Изотермическая закалка позволяет устранить большое различие в скоростях охлаждения поверхности и сердцевины деталей, которое является основной причиной образования термических напряжений и закалочных трещин. Изотермическая закалка в ряде случаев исключает операцию отпуска, что сокращает на 35–40 % цикл термической обработки.
Материаловедение. Учеб. пособие |
-212- |
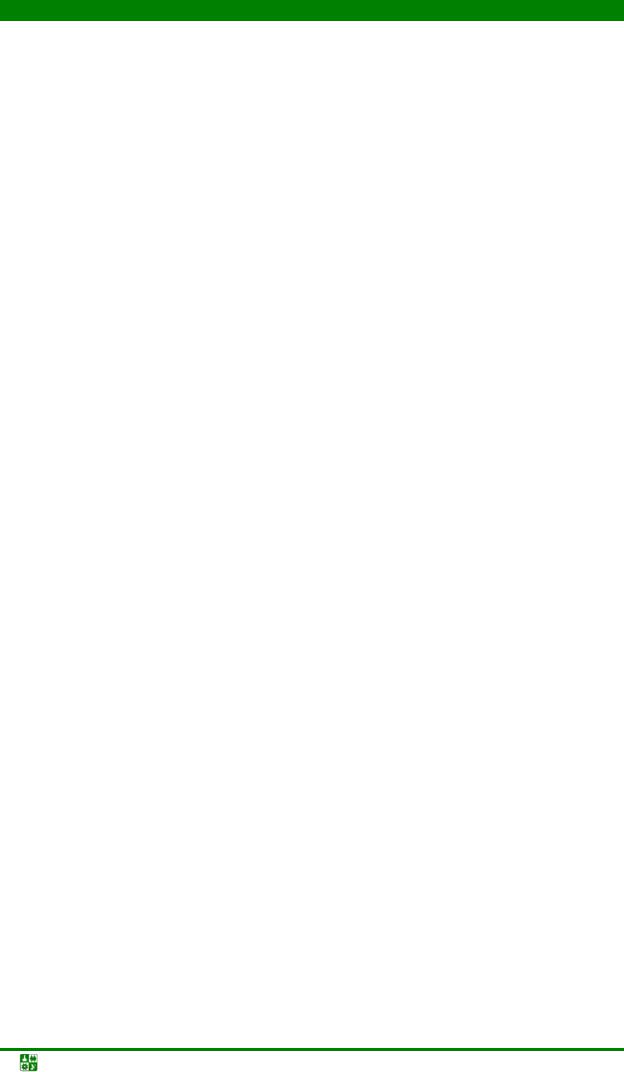
РАЗДЕЛ II. МАТЕРИАЛОВЕДЕНИЕ СТАЛЕЙ И ЧУГУНОВ
Глава 4. Стали, сплавы системы железо–углерод. Маркировка, структура, свойства сплавов
Светлая закалка. При этом способе закалки детали нагревают в нейтральной безокислительной атмосфере или в расплавленных нейтральных солях. При светлой закалке нагрев деталей или инструмента осуществляют в жидких солях, не вызывающих окисление металла, с последующим охлаждением их в расплавленных едких щелочах.
Дефекты, возникающие при закалке. Основными видами брака яв-
ляются: образование трещин, деформация и коробление, обезуглероживание и окисление, изменение размеров, появление мягких пятен, низкая твёрдость, перегрев.
Закалочные трещины. В крупных деталях, например в матрицах и ковочных штампах, закалочные трещины могут появляться даже при закалке в масле. Поэтому такие детали целесообразно охлаждать до 150–200 °С с быстрым последующим отпуском.
Чтобы уменьшить скорость охлаждения при закалке легированных сталей и снизить напряжение, эти стали подвергают медленному охлаждению в масле или струе воздуха.
Деформация и коробление. Этот вид брака деталей образуется в результате неравномерных структурных и связанных с ними объёмных превращений и возникновения внутренних напряжений при охлаждении.
Обезуглероживание инструмента при нагреве в электрических печах и жидких средах (соляных ваннах) – серьёзный дефект при закалке, т.к. он в несколько раз снижает стойкость инструмента.
Мягкие пятна. При закалке на поверхности детали или инструмента образуются участки с пониженной твёрдостью. Причинами такого дефекта могут быть наличие на поверхности деталей окалины и загрязнении, участки с обезуглероженной поверхностью или недостаточно быстрое движение деталей в закалочной среде (паровая рубашка). Мягкие пятна полностью устраняются при струйчатой закалке и в подсоленной воде.
Причинами низкой твёрдости являются недостаточно быстрое охлаждение в закалочной среде, низкая температура закалки, а также малая выдержка при нагреве под закалку. Чтобы исправить этот дефект, детали или инструмент сначала подвергают высокому отпуску при температуре 600–625 °С, а затем – закалке.
Перегрев приводит к образованию крупнозернистой структуры, что ухудшает механические свойства стали. Для измельчения зерна и подготовки структуры для повторной закалки перегретую сталь необходимо подвергать отжигу.
Недогрев. Если температура закалки была ниже критических точек Ас3 (для доэвтектоидных сталей) и Ас1 (для заэвтектоидных сталей), то структура закаленной стали будет состоять из мартенсита и зерен феррита, который имеет низкую твёрдость. Недогрев можно исправить отжигом с последующей закалкой.
Материаловедение. Учеб. пособие |
-213- |
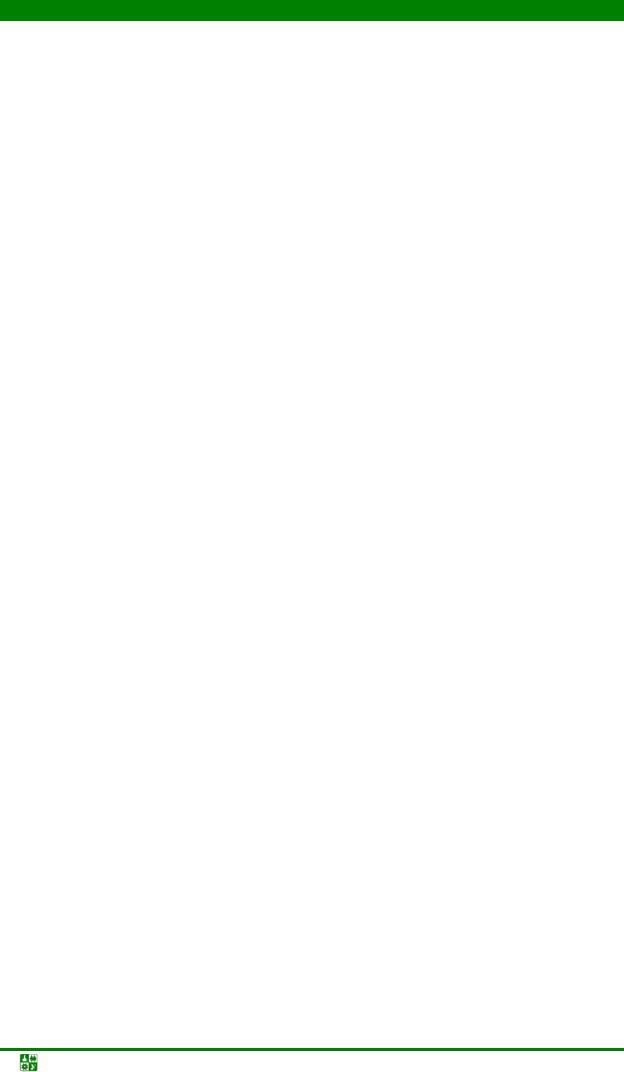
РАЗДЕЛ II. МАТЕРИАЛОВЕДЕНИЕ СТАЛЕЙ И ЧУГУНОВ
Глава 4. Стали, сплавы системы железо–углерод. Маркировка, структура, свойства сплавов
4.8.9. Превращения, происходящиепринагревезакаленныхсталей
Отпуск – это термическая обработка закаленного на мартенсит сплава (или металла), при которой главными процессами являются распад мартенсита.
При нагреве после закалки вследствие увеличивающейся подвижности атомов создаются условия для процессов, изменяющих структуру стали в направлении к более равновесному состоянию. Характер этих процессов определяется тремя важнейшими особенностями строения закаленной стали: сильной пересыщенностью твердого раствора – мартенсита, повышенной плотностью в нем дефектов кристаллической решетки – дислокаций, малоугловых и высокоугловых границ, двойниковых прослоек и присутствием во многих сталях значительных количеств остаточного аустенита.
Распад мартенсита с выделением карбидов – главный процесс при отпуске сталей. Распад мартенсита в зависимости от температуры и продолжительности отпуска проходит через стадии предвыделения, выделения промежуточных метастабильных карбидов, выделения цементита и коагуляции.
В свежезакаленном мартенсите перераспределение углерода заметно уже при 40 °С. Вначале на каждый кластер приходится лишь несколько атомов углерода. Кластеры постепенно укрупняются, а содержание углерода в них становится соответствующим составу, который можно описать формулой Fe4C. Этот процесс контролируется диффузией углерода.
Выделение промежуточных карбидов из мартенсита – следующая после сегрегации углерода стадия структурных изменений при отпуске. Начиная примерно с температуры 100 °С экспериментально обнаруживается метастабильный e-карбид, отличающийся от цементита типом решётки (гексагональная у ε-карбида, ромбическая у цементита).
При низких температурах ε-карбид выделяется в виде очень дисперсных пластин или стержней. С повышением температуры или увеличением продолжительности отпуска частицы ε-карбида укрупняются.
Образование цементита Fе3С со структурой, одинаковой или близкой к структуре цементита отожженной стали, происходит при температурах выше 250 °С, причем наиболее активно в интервале 300–400 °С.
Цементит Fе3С – более стабильная фаза, обладающая меньшей объемной («химической») свободной энергией, чем промежуточный карбид. Кроме того, при повышении температуры отпуска снижение концентрации углерода в распадающемся α-растворе так изменяет межплоскостные расстояния, что решетка α-фазы лучше сопрягается уже не с решеткой ε-карбида, а с решеткой цементита. Таким образом, при более высоких температурах отпуска выигрыш в объемной и поверхностной свободной энергии делает предпочтительными зарождение и рост цементита, а не промежуточного карбида.
Коагуляция и сфероидизация цементита − завершающая стадия процессов карбидообразования при отпуске. Размер цементитных пластин различен. Концентрация углерода в α-растворе около относительно мелких частиц выше, чем около более крупных. Эта разность концентраций обеспечива-
Материаловедение. Учеб. пособие |
-214- |
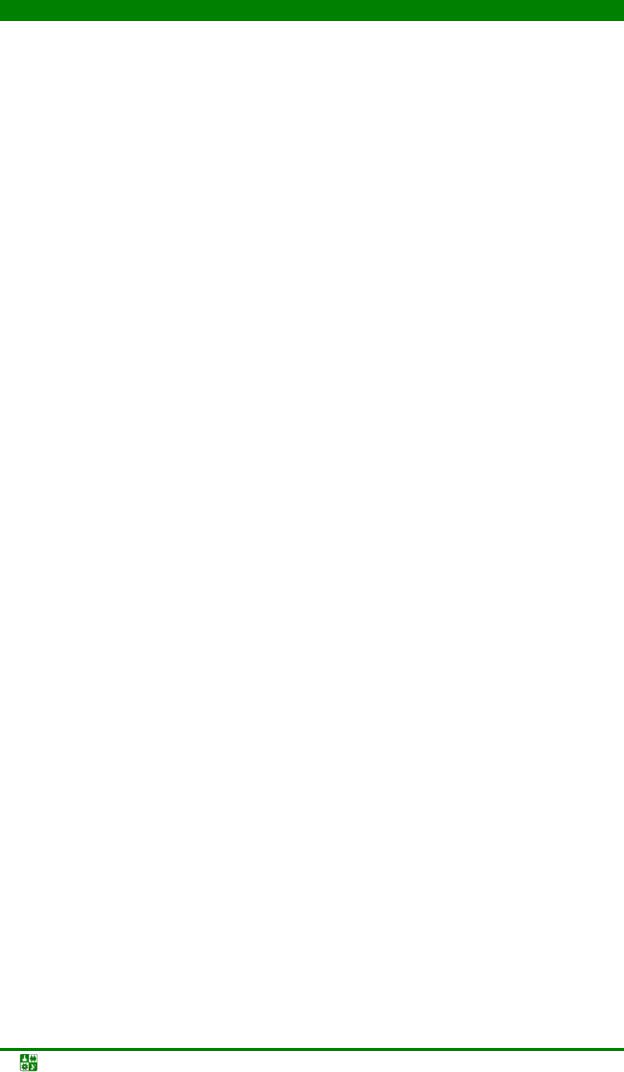
РАЗДЕЛ II. МАТЕРИАЛОВЕДЕНИЕ СТАЛЕЙ И ЧУГУНОВ
Глава 4. Стали, сплавы системы железо–углерод. Маркировка, структура, свойства сплавов
ет диффузию углерода в α-растворе от более мелких цементитных частиц к более крупным. В результате выравнивающей диффузии α-раствор становится ненасыщенным около мелких частиц и пересыщенным около крупных. Более мелкие цементитные частицы растворяются, а более крупные подрастают. По-настоящему интенсивные коагуляция и сфероидизация начинаются с 35–400 °С. Выше 600 °С все частицы цементита сферические и идет только их коагуляция. При изотермической выдержке коагуляция цементита интенсивно развивается в течение короткого времени (первого часа) и затем затухает. Средний размер цементитных частиц растет с повышением температуры отпуска.
Распад остаточного аустенита играет существенную роль в процессах отпуска высокоуглеродистых сталей, где он находится в значительном количестве. Распад аустенита активно протекает в интервале температур примерно 200–300 °С. Остаточный аустенит при отпуске превращается в нижний бейнит.
Уменьшение концентрации углерода в α-растворе идет во всем температурном интервале выделения из него карбидной фазы.
Традиционно принято выделять три температурных интервала и соответствующие им три «превращения» при отпуске углеродистых сталей.
Первое «превращение» при отпуске относят к интервалу температур 100–200 °С. При этих температурах закаленный образец укорачивается. Так как из всех структурных составляющих стали наибольший удельный объем у мартенсита, то первое «превращение» связывают с его распадом.
Второе «превращение» при отпуске относят к интервалу температур 200–300 °С. При выдержке в этом интервале длина закаленных образцов средне- и высокоуглеродистых сталей увеличивается и тем больше, чем выше содержание углерода в стали. Так как удельный объем аустенита наименьший и количество остаточного аустенита растет с увеличением содержания углерода в стали, то второе «превращение» связывают с его распадом. При этом, конечно, следует иметь в виду, что в температурном интервале второго «превращения» продолжается распад мартенсита.
Третье «превращение» при отпуске относят к интервалу температур 300–600 °С. В этом температурном интервале длина образцов сокращается. Одно из объяснений − окончание выделения Fe3С из мартенсита.
Структуру, получающуюся после отпуска стали при температурах ниже 300 °С, называют отпущенным мартенситом. После отпуска при температурах 300–450 °С обнаруживается особенно сильно травящаяся игольчатая структура, которую называют трооститом отпуска. В интервале температур 450–650 °С получается сорбит отпуска.
4.8.10. Изменениесвойствприотпускесталей. Видыотпуска
Углеродистые стали. Закаленная углеродистая сталь характеризуется не только высокой твердостью, но и очень большой склонностью к хрупкому разрушению. Кроме того, при закалке возникают значительные остаточные
Материаловедение. Учеб. пособие |
-215- |

РАЗДЕЛ II. МАТЕРИАЛОВЕДЕНИЕ СТАЛЕЙ И ЧУГУНОВ
Глава 4. Стали, сплавы системы железо–углерод. Маркировка, структура, свойства сплавов
напряжения. Поэтому закалку углеродистых сталей обычно не применяют как окончательную операцию. Для увеличения вязкости и уменьшения закалочных напряжений после закалки применяют отпуск.
На рис. 4.28 видно, что до температуры отпуска около 100 °С твердость закаленной стали или практически не меняется, или слабо (на 1–2 HRC) возрастает. С дальнейшим повышением температуры отпуска твердость плавно снижается.
С ростом температуры отпуска разупрочнение усиливается из-за следующих причин: 1) уменьшения концентрации углерода в α-растворе; 2) нарушения когерентности на границе карбид−матрица и снятия упругих микронапряжений; 3) коагуляции карбидов и увеличения межчастичного расстояния; 4) развития возврата и рекристаллизации. В разных температурных интервалах преобладает действие разных факторов разупрочнения в соответствии с интенсивностью развития тех или иных структурных изменений.
В высокоуглеродистых сталях, содержащих значительное количество остаточного аустенита, распад его с выделением карбида задерживает падение твёрдости, а в интервале температур 200–250 °С даже несколько увеличивает ее.
Прочностные характеристики углеродистой стали (временное сопротивление, предел текучести и твердость) непрерывно уменьшаются с ростом температуры отпуска выше 300 °С, а показатели пластичности (относительное удлинение и сужение) непрерывно повышаются (рис. 4.29). Ударная вязкость начинает интенсивно возрастать при отпуске выше 300 °С. Максимальной ударной вязкостью обладает сталь с сорбитной структурой, отпущенная при 600 °С. Некоторое снижение ударной вязкости при температурах отпуска выше 600 °С можно объяснить тем, что частицы цементита по границам ферритных зерен, растущие вследствие растворения частиц внутри α-фазы, становятся слишком грубыми.
Рис. 4.28. Зависимость твердости углеро- |
Рис. 4.29. Влияние температуры отпуска |
дистых сталей разного состава от темпе- |
на механические свойства стали |
ратуры отпуска |
|
Материаловедение. Учеб. пособие |
-216- |
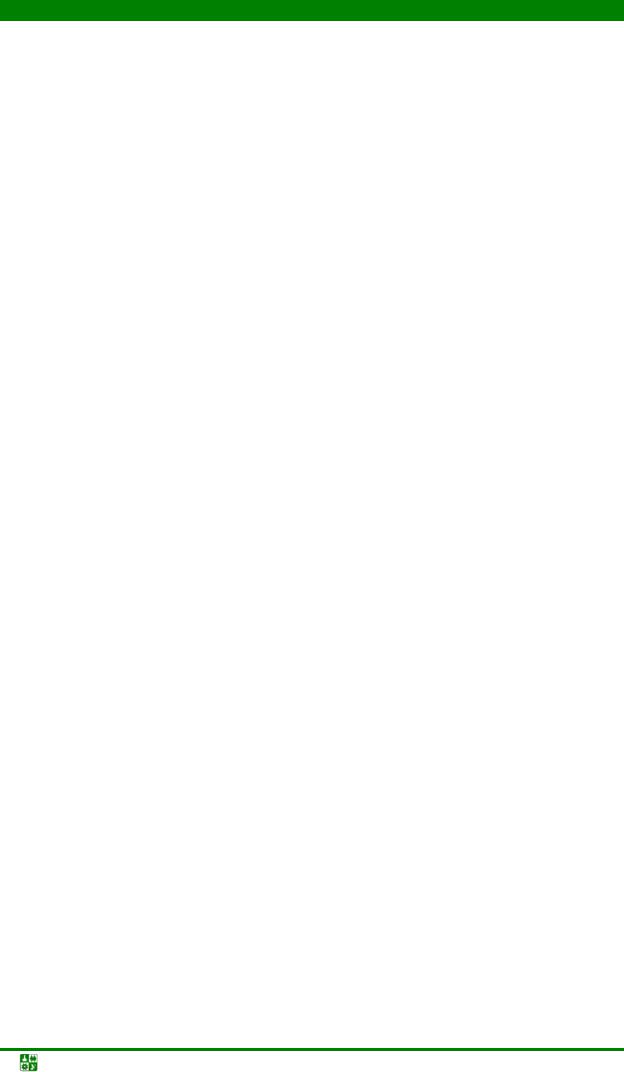
РАЗДЕЛ II. МАТЕРИАЛОВЕДЕНИЕ СТАЛЕЙ И ЧУГУНОВ
Глава 4. Стали, сплавы системы железо–углерод. Маркировка, структура, свойства сплавов
По температуре нагрева различают низкий, средний и высокий отпуск. Низкий отпуск на отпущенный мартенсит (120–250 °С) широко применяют после закалки инструментов, цементованных и цианированных изделий и после поверхностной закалки. Цель низкого отпуска − уменьшение остаточных закалочных напряжений. Температуру низкого отпуска выбирают такой, чтобы твердость и износостойкость не снизились или слабо снизились. Выдержка при температуре низкого отпуска обычно не превышает 1−3 ч; с дальнейшим увеличением выдержки остаточные напряжения очень слабо
уменьшаются.
Разновидность низкого отпуска − стабилизирующий отпуск. В закаленной стали даже при комнатной температуре, а тем более в результате климатических колебаний температуры происходят медленные (в течение многих лет) процессы распада мартенсита, перехода остаточного аустенита в мартенсит и снятия напряжений. Все эти явления ведут к постепенному изменению размеров изделия. Для таких изделий, как мерительный инструмент высокого класса точности и прецизионные подшипники, недопустимы изменения размеров даже на насколько микронов. Стабилизации мартенсита и напряженного состояния достигают низким (стабилизирующим) отпуском при 100–180 °С с выдержкой до 30, а иногда и до 150 ч.
Средний отпуск на троостит (350–450 °С) используют тогда, когда необходимо получить в стали сочетание высокой прочности, упругости и вместе с тем достаточной вязкости. Среднему отпуску подвергают пружины и рессоры.
Высокий отпуск на сорбит (450–650 °С) широко применяют в машиностроении к изделиям из конструкционной стали, которые должны характеризоваться не только достаточной прочностью, но и хорошей сопротивляемостью ударным нагрузкам. Выдержку при высоком отпуске (обычно несколько часов) подбирают опытным путем для получения заданного комплекса свойств.
Двойная операция получения сорбита − закалка с высоким отпуском − называется улучшением. Эту операцию применяют к среднеуглеродистым сталям, содержащим от 0,35 до 0,6 % С. Такие стали называют улучшаемыми в отличие от малоуглеродистых цементуемых.
Скорость охлаждения с температуры отпуска не влияет на механические свойства углеродистых сталей, и если не опасны термические напряжения, то можно проводить ускоренное охлаждение.
Легированные стали. Легирующие элементы, затрудняющие распад мартенсита и коагуляцию карбидов, смещают температурную границу начала интенсивного разупрочнения при отпуске с 200−300 до 450–550 °С. Повышение красностойкости закаленной стали, т.е. способности ее сопротивляться смягчению при нагреве, − одна из основных целей легирования в производстве инструмента.
Материаловедение. Учеб. пособие |
-217- |
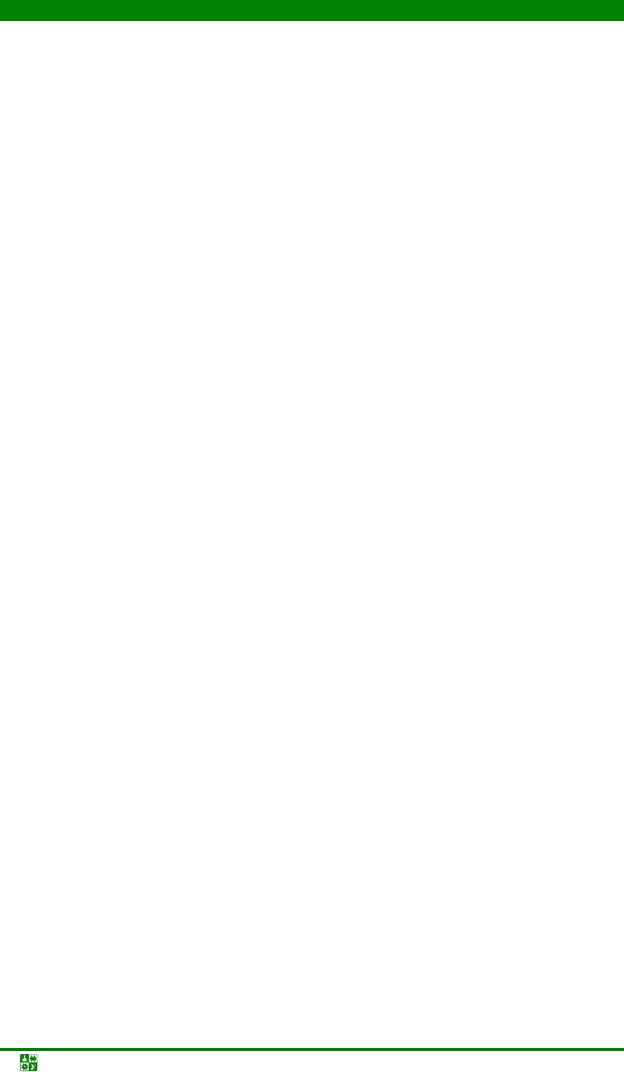
РАЗДЕЛ II. МАТЕРИАЛОВЕДЕНИЕ СТАЛЕЙ И ЧУГУНОВ
Глава 4. Стали, сплавы системы железо–углерод. Маркировка, структура, свойства сплавов
Для конструкционных легированных сталей весьма важно, что специальные карбиды выделяются при высоком отпуске в более дисперсной форме, чем цементит. Это обеспечивает повышенную вязкость, т.к. микропустоты (очаги разрушения) зарождаются около мелких частиц специального карбида труднее, чем около более крупных частиц цементита.
Отпускная хрупкость присуща многим сталям. В результате медленного охлаждения с температуры высокого отпуска ударная вязкость легированной стали может оказаться в несколько раз (и даже на порядок) меньше, чем после охлаждения в воде с той же температуры. Есть два температурных интервала, при которых у конструкционных сталей ударная вязкость заметно снижается: 250–350 и 500–600 °С. Понижение вязкости называют отпускной хрупкостью, соответственно, I и II рода.
Понижение ударной вязкости после отпуска при 250–350 °С наблюдается у всех конструкционных сталей независимо от степени легирования. Заметное падение ударной вязкости после отпуска 500–600 °С наблюдается только у легированных конструкционных сталей – хромистых, марганцевых, хромоникелевых, хромомарганцевых и т.д. Снижение вязкости почти не происходит в случае быстрого охлаждения от температуры отпуска (в воде или масле). Отпускная хрупкость II рода заметно подавляется даже при медленном охлаждении от температуры отпуска дополнительным легированием сталей молибденом или вольфрамом в количестве 0,3 и 1 % соответственно.
4.8.11. Общиезакономерностихимико-термическойобработкисплавов
Химико-термической обработкой называют технологические процессы, приводящие к диффузионному насыщению поверхностного слоя деталей различными элементами.
Химико-термическую обработку применяют для повышения твердости, износостойкости, сопротивления усталости и контактной выносливости, а также для защиты от электро-химической и газовой коррозии.
Фазовые и структурные изменения, происходящие на диффузионной стадии процесса, можно предсказать с помощью двойных диаграмм состояния, если в диффузионном взаимодействии участвуют всего два элемента. При этом предполагается, что диффузионный процесс не интенсифицируется и образующаяся диффузионная зона находится в равновесном состоянии.
Материаловедение. Учеб. пособие |
-218- |
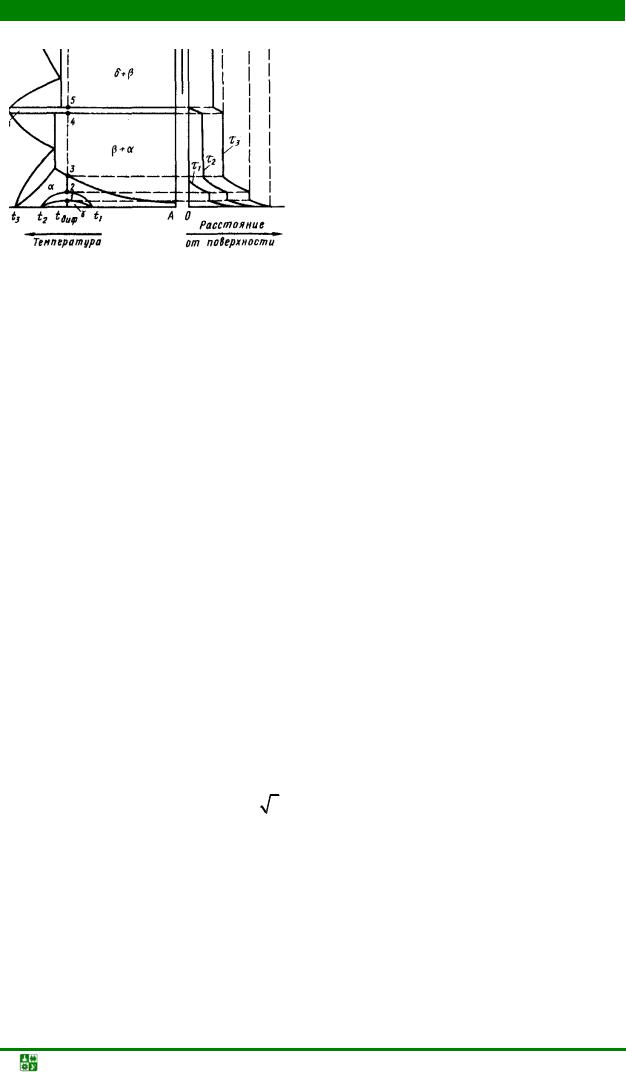
РАЗДЕЛ II. МАТЕРИАЛОВЕДЕНИЕ СТАЛЕЙ И ЧУГУНОВ
Глава 4. Стали, сплавы системы железо–углерод. Маркировка, структура, свойства сплавов
Рис. 4.30. Схема образования фаз в диффузион- |
Рис. 4.31. Равновеснаядиаграммасэвтекто- |
ных слоях в соответствии с равновесной диа- |
идным превращением γ-твердого раствора |
граммойсостояния(времявыдержкиτ1 < τ2 < τ3) |
|
Так, при длительном диффузионном насыщении τз элемента А элементом В можно добиться соответствия фазового состава диффузионной зоны равновесной диаграмме состояния (рис. 4.30). Последовательность образования фаз при температуре диффузионного насыщения соответствует последовательности их расположения на диаграмме (γ, α, β, δ на рис. 4.31). Однако фазы с очень узкими областями гомогенности на диаграмме состояния могут расти так медленно, что их слои в диффузионной зоне не обнаруживаются.
Двухфазные области в диффузионной зоне не образуются, т.к. через фазу постоянного состава диффузионный перенос невозможен из-за отсутствия градиента концентрации.
Двухфазный слой в диффузионной зоне может образоваться при медленном охлаждении от температуры диффузионного насыщения вследствие переменной растворимости и вторичных выделений α- и β-фазы. Кроме того, двухфазная смесь может образоваться в диффузионной зоне в результате фазовой перекристаллизации в процессе охлаждения от температуры диффузионного насыщения (рис. 4.35), в то время как при диффузионном насыщении образуется γ-твердый раствор переменной концентрации.
Для однофазных областей диффузионной зоны зависимость роста толщины слоя от продолжительности насыщения при τдиф = соnst подчиняется
параболическому закону: ∆ = k1 τ , а зависимость толщины слоя от температуры при τ = соnst – экспоненциальному:
∆ = k2е–Q/RT,
где k1, k2 – константы; Q – энергия активации диффузионных процес-
сов. Толщина диффузионного cлоя τдиф = соnst и τ = соnst тем больше, чем выше концентрация диффундирующего элемента на насыщаемой поверхно-
сти.
Материаловедение. Учеб. пособие |
-219- |
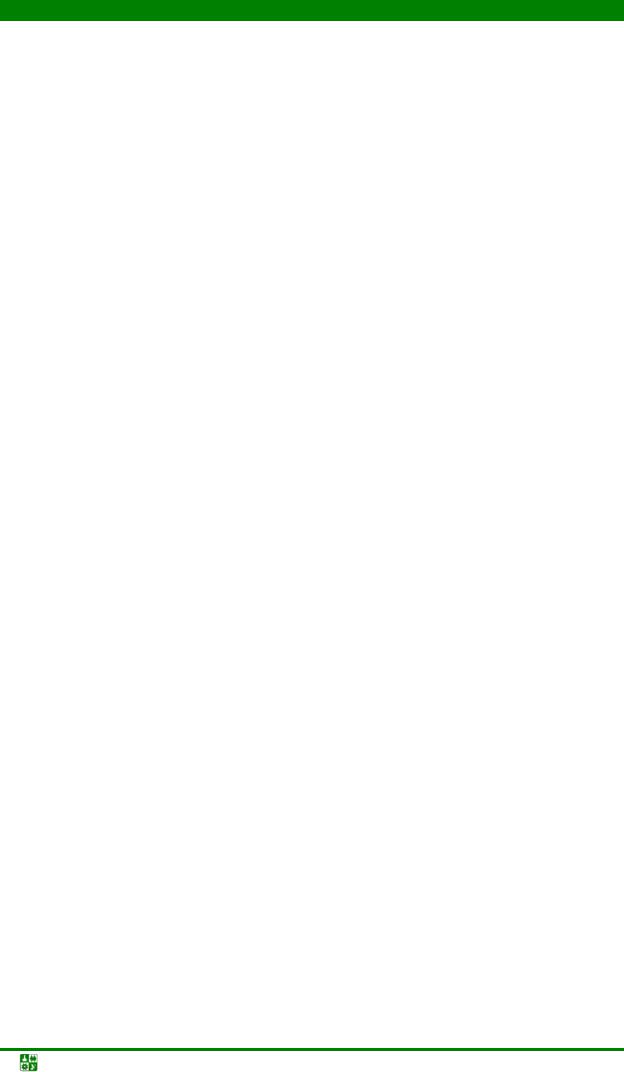
РАЗДЕЛ II. МАТЕРИАЛОВЕДЕНИЕ СТАЛЕЙ И ЧУГУНОВ
Глава 4. Стали, сплавы системы железо–углерод. Маркировка, структура, свойства сплавов
Существует множество способов химико-термической обработки, однако наибольшее распространение в промышленности получили процессы диффузионного насыщения из активных жидких и газовых сред. Более рациональной исходной средой является активизированная газовая среда, т.е. среда, лишенная нейтральных (балластных) примесей.
Диффузионное насыщение стали углеродом, азотом и совместно этими элементами – наиболее распространенные в промышленности процессы хи- мико-термической обработки.
4.8.12. Цементациясталей
Технологический процесс диффузионного насыщения углеродом называется цементацией. Обычно после цементации сталь подвергают закалке и низкому отпуску. После такого комплексного процесса концентрация углерода на поверхности стальной детали доводится до 0,8–1 %, структура низкоотпущенного мартенсита с мелкими сфероидальными карбидами хорошо сопротивляется износу. Твердость на поверхности 7500–9500 НV. Сердцевина детали, содержащая 0,08–0,25 % С, остается вязкой, а поверхности, не подлежащие цементации, защищаются гальваническим омеднением. Толщина медного слоя составляет 0,02–0,05 мм.
Цементации обычно подвергают такие детали машин, которые должны иметь износостойкую рабочую поверхность и вязкую сердцевину: зубчатые колеса, валы и пальцы, распределительные валики, кулачки, червяки и др.
Карбюризаторы. Исходную среду для цементации (науглероживания) принято называть карбюризатором. В основном применяют два способа цементации: в твердом и в газовом карбюризаторе. Несмотря на различные названия, процесс цементации в твердом и газовом карбюризаторе идет через газовую фазу. Наиболее распространенный твердый карбюризатор состоит в основном из древесного угля с добавкой 20–25 % углекислого бария для интенсификации процесса и 3–5 % СаСО3 для предотвращения спекания частиц карбюризатора. Детали, подлежащие цементации, и карбюризатор упаковывают в контейнер (стальной ящик) и нагреваются в печи до 910–930 °С. При нагреве уголь взаимодействует с кислородом остаточного воздуха по реакции
2С + О2 → 2СО Кроме того, оксид углерода образуется в результате реакции
ВаСО3 + С→ ВаО + 2СО
На поверхности деталей протекает ведущая процесс цементации реакция диспропорционирования
2СО ↔ СО2 + С,
в результате которой активный углерод адсорбируется насыщаемой поверхностью, находящейся в аустенитном состоянии, а СО2 взаимодействует с углем, образуя новые порции СО.
Материаловедение. Учеб. пособие |
-220- |

РАЗДЕЛ II. МАТЕРИАЛОВЕДЕНИЕ СТАЛЕЙ И ЧУГУНОВ
Глава 4. Стали, сплавы системы железо–углерод. Маркировка, структура, свойства сплавов
При газовой цементации в качестве карбюризатора используют разбавленный природный газ (состоящий почти полностью из метана), контролируемые атмосферы, получаемые в специальных генераторах, а также жидкие углеводороды (керосин, бензол и др.), каплями подаваемые в герметичное рабочее пространство печи, где они образуют активную газовую среду. Основная ведущая реакция при наличии метана
СН4 → 2Н2 + С
В ряде случаев (эндотермическая контролируемая атмосфера) при наличии в газе СО возможна также реакция
2СО → СО2 + С
В зависимости от состава газовой смеси и содержания углерода в стали атмосфера в рабочем пространстве печи может быть науглероживающей, обезуглероживающей и нейтральной. Нейтральному составу газовой смеси соответствует определенная равновесная концентрация углерода на поверхности стальной детали. Эту концентрацию углерода принято называть углеродным потенциалом контролируемой атмосферы. Следовательно, науглероживание будет происходить в том случае, если концентрация углерода на поверхности стали будет меньше углеродного потенциала газовой смеси при данной температуре.
Структура цементованного слоя. Типичная структура цементованного слоя на поверхности низкоуглеродистой стали после медленного охлаждения от температуры цементации показана на рис. 4.32. Обычно ее сопоставляют со схемами, приведенными выше. Наружная часть слоя, содержащая больше 0,8 % С, имеет структуру заэвтектоидных сталей – перлит и вторичный цементит, который при медленном охлаждении выделяется на границах аустенитных зерен в виде оболочек (на шлифе сетка). Средняя часть слоя, имеющая эвтектоидную концентрацию, состоит из перлита. Далее по направлению к сердцевине концентрация углерода уменьшается, структура соответствует доэвтектоидной стали, причем количество перлита уменьшается при приближении к сердцевине.
Материаловедение. Учеб. пособие |
-221- |
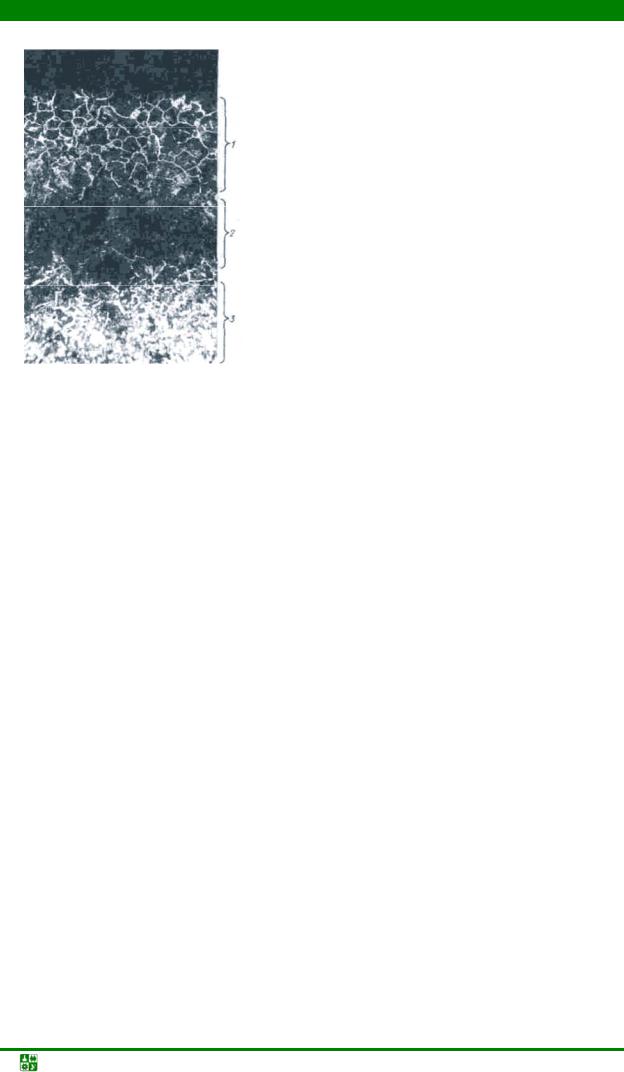
РАЗДЕЛ II. МАТЕРИАЛОВЕДЕНИЕ СТАЛЕЙ И ЧУГУНОВ
Глава 4. Стали, сплавы системы железо–углерод. Маркировка, структура, свойства сплавов
Рис. 4.32. Микроструктура диффузионного слоя после цементации низкоуглеродистой стали, х200: 1 – заэвтектоидная зона; 2 – эвтектоидная зона; 3 – доэвтектоидная зона
За эффективную толщину принимают сумму заэвтектоидной, эвтектоидной и половины доэвтектоидной зоны слоя. Эффективная толщина цементованного слоя обычно составляет 0,5–1,8 мм и в исключительных случаях достигает 6 мм при больших контактных нагрузках на цементованную поверхность.
Структура после цементации получается крупнозернистой в связи с длительной выдержкой деталей при температуре науглероживания. Длительность изотермической выдержки при цементации зависит от заданной толщины слоя и марки цементируемой стали.
Процесс газовой цементации идет быстрее, т.к. не приходится нагревать ящик с карбюризатором.
Кроме того, процесс газовой цементации легко регулируется и автоматизируется.
На заводах работают автоматизированные агрегаты для цементации, которые регулируют процесс по углеродному потенциалу.
Термическая обработка после цементации. Для получения заданного комплекса механических свойств после цементации необходима дополнительная термическая обработка деталей.
В зависимости от условий работы, а также от выбранной для изготовления детали стали режим упрочняющей термической обработки может быть различен. Для тяжелонагруженных трущихся деталей машин, испытывающих в условиях работы динамическое нагружение, в результате термической обработки нужно получить не только высокую поверхностную твердость, но и высокую прочность (например, для зубчатых колес – высокую прочность на изгиб), и высокую ударную вязкость. Для обеспечения указанных свойств требуется сформулировать мелкое зерно как на поверхности детали, так и в сердцевине. В таких ответственных случаях цементованные детали подвергают сложной термической обработке, состоящей из двух последовательно проводимых закалок и низкого отпуска.
Материаловедение. Учеб. пособие |
-222- |
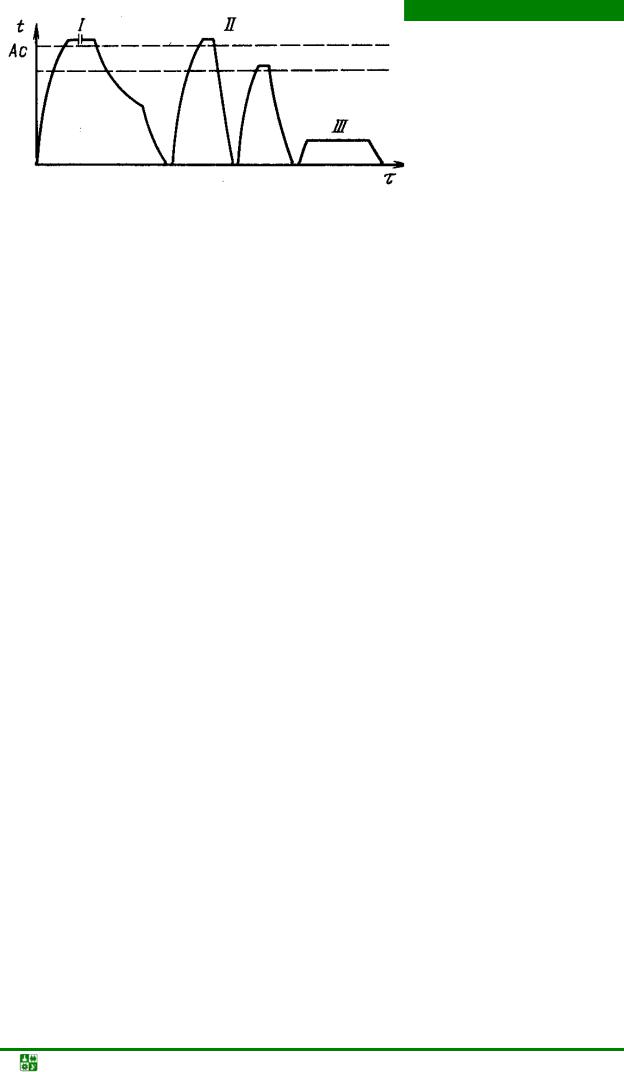
РАЗДЕЛ II. МАТЕРИАЛОВЕДЕНИЕ СТАЛЕЙ И ЧУГУНОВ
Глава 4. Стали, сплавы системы железо–углерод. Маркировка, структура, свойства сплавов
При первой закалке деталь нагревают до температуры на 30–50 °С выше температуры Ас3 цементируемой стали. При таком нагреве во всем объеме детали установится аустенитное состояние. Нагрев до температур, лишь немного превышающих Ас3, вызывает перекристаллизацию сердцевины детали с образованием мелкого аустенитного зерна, что обеспечит мелкозернистость продуктов распада. При температуре tЗI, как видно на рис. 4.33, весь диффузионный слой переходит в аустенитное состояние, поэтому для предотвращения выделения цементита проводят закалку.
Рис. 4.33. Режим термической обработки ответственных деталей машин после цементации (схема): I – цементация; II – двойная закалка; III – низкий отпуск
При второй закалке деталь нагревают до температуры tЗII с превышением на 30–50 °С температуры Ас1. В процессе нагрева мартенсит, полученный
врезультате первой закалки, отпускается, что сопровождается образованием глобулярных карбидов, которые в определенном количестве сохраняются после неполной закалки в поверхностной заэвтектоидной части слоя, увеличивая его твердость. Вторая закалка обеспечивает также мелкое зерно в науглероженном слое.
Окончательной операцией термической обработки является низкий от-
пуск при 160–200 °С.
После двойной закалки и низкого отпуска поверхностный слой приобретает структуру отпущенного мартенсита с включениями глобулярных карбидов. Структура сердцевины детали зависит от легированности стали. Если для цементации выбрана углеродистая сталь, то из-за малой прокаливаемости
всердцевине получится сорбитная структура; если же цементировалась легированная сталь, то в зависимости от количества легирующих элементов сердцевина может приобрести структуру бейнита или низкоуглеродистого мартенсита
Если для цементации выбирают природно-мелкозернистые стали и содержание углерода на поверхности близко к эвтектоидному, то и при одной закалке получают удовлетворительные свойства как в сердцевине, так и в цементованном слое. Однократная закалка широко используется на заводах массового производства, где цементацию ведут в газовом карбюризаторе.
Материаловедение. Учеб. пособие |
-223- |
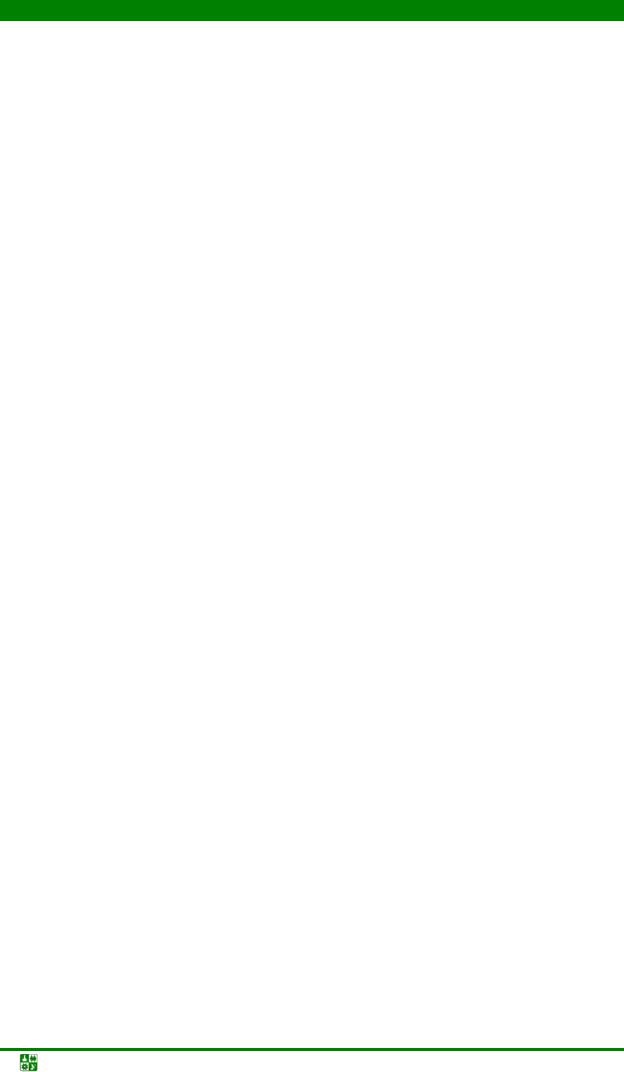
РАЗДЕЛ II. МАТЕРИАЛОВЕДЕНИЕ СТАЛЕЙ И ЧУГУНОВ
Глава 4. Стали, сплавы системы железо–углерод. Маркировка, структура, свойства сплавов
Выгодно и удобно в этом случае закалку проводить после цементационного нагрева. Цементованные детали подвергают шлифованию.
4.8.13. Азотированиесталей
Азотированием называют процесс диффузионного насыщения азотом поверхностной зоны деталей. Азотирование применяют для повышения износостойкости и предела выносливости деталей машин (коленчатые валы, гильзы цилиндров, червяки, валики и др.).
До азотирования детали подвергают закалке и высокому отпуску (улучшению), чистовой обработке. После азотирования детали шлифуют или полируют.
Обычное азотирование проводят при температуре 500–600 °С в муфелях или контейнерах, через которые пропускается диссоциирующий аммиак.
Вероятно, что на стальной поверхности происходит реакция диссоциации аммиака с выделением ионов азота, которые адсорбируются поверхностью детали, а затем диффундируют вглубь.
При нагреве аммиака в изолированном объеме возможна лишь реакция с образованием молекулярного азота
2NН3 → N2 + 3Н2,
который не может диффундировать в сталь без ионизации. Формирование структуры азотированной зоны в углеродистых сталях
происходит примерно так же, как при азотировании железа. Поэтому, пользуясь диаграммой Fe–N (рис. 4.34), можно предсказать структуру азотированной зоны низкоуглеродистых сталей.
По мере насыщения железа азотом при температуре ниже 590 °С сначала образуется α-твердый раствор внедрения азота в железо, затем слой γ'- фазы с ГЦК-решеткой и упорядоченным расположением атомов азота в центрах элементарных ячеек. Обычно процесс азотирования завершается образованием на поверхности слоя ε-фазы с ГП-решеткой и упорядоченным расположением атомов в широком интервале концентраций азота.
Материаловедение. Учеб. пособие |
-224- |
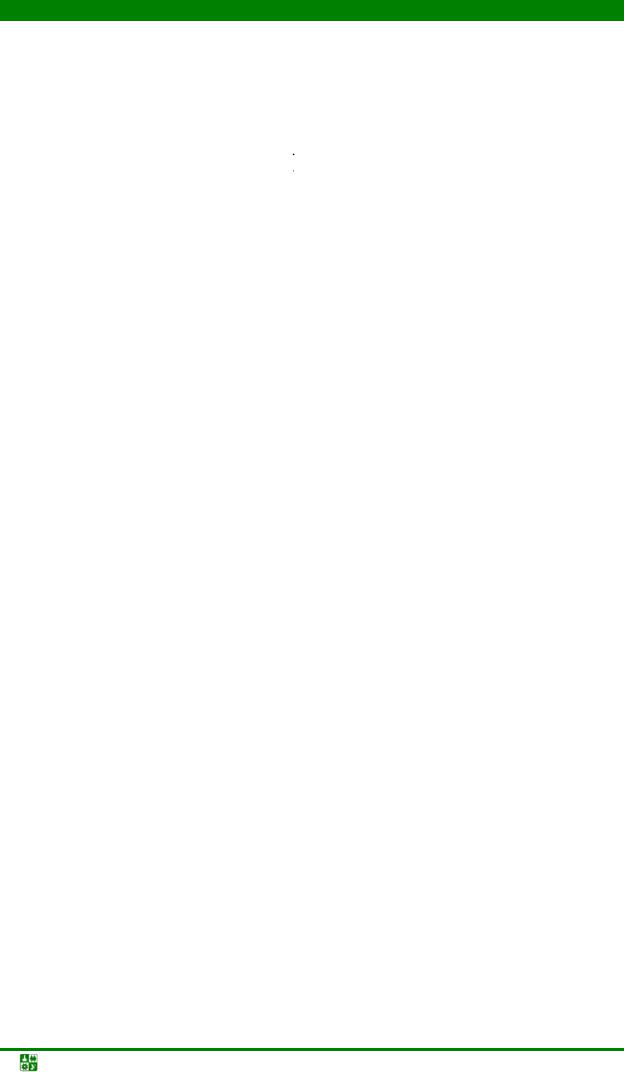
РАЗДЕЛ II. МАТЕРИАЛОВЕДЕНИЕ СТАЛЕЙ И ЧУГУНОВ
Глава 4. Стали, сплавы системы железо–углерод. Маркировка, структура, свойства сплавов
Рис. 4.34. Участок диаграммы Fe–N. Изменение содержания азота и фазового состава по толщине слоя при tазот
При медленном охлаждении после азотирования вследствие переменной растворимости азота в α- и ε-фазах происходит выделение избыточной γ'вт-фазы, и структура азотированной зоны от поверхности к сердцевине ста-
новится следующей: (ε + γ'вт) → γ' → (α + γ'вт) → α.
При азотировании углеродистых сталей с увеличением содержания углерода уменьшается скорость диффузии азота и возможно образование карбонитридных фаз.
Азотированная сталь, имеющая на поверхности слой ε-фазы, коррози- онно-стойка в воде и в атмосферных условиях. В системе Fе–N ε- и γ'-фазы имеют сравнительно невысокую твердость, соответственно, 4 500 НV и 5 500 НV. Значительно большая твердость достигается при азотировании специально легированных сталей – нитраллоев, которые содержат более активные нитридообразующие элементы: Сr, Мо, А1, V, Ti.
При азотировании структуры диффузионной зоны легированных и углеродистых сталей аналогичны. Однако легирование изменяет состав фаз и температурные границы их образования. При изотермической выдержке в процессе азотирования могут образовываться двухфазные слои в диффузионной зоне.
Установлено, что при азотировании упрочнение α-фазы в легированных сталях происходит по механизму старения пересыщенных твердых растворов. При образовании полностью когерентных зародышей нитридной фазы в α-фазе легированных сталей наблюдается максимальная твердость.
Высокие твердость и износостойкость получаются после азотирования легированной стали 38Х2МЮА. Комплексное легирование хромом, алюминием и молибденом позволяет повысить твердость азотированного слоя до
12 000 НV.
Молибден также устраняет отпускную хрупкость, которая может возникнуть при медленном охлаждении от температуры азотирования. При обычном азотировании стали 38Х2МЮА диффузионную зону толщиной около 0,5 мм получают при 500–520 °С за 55 ч выдержки. Такую же толщину
Материаловедение. Учеб. пособие |
-225- |
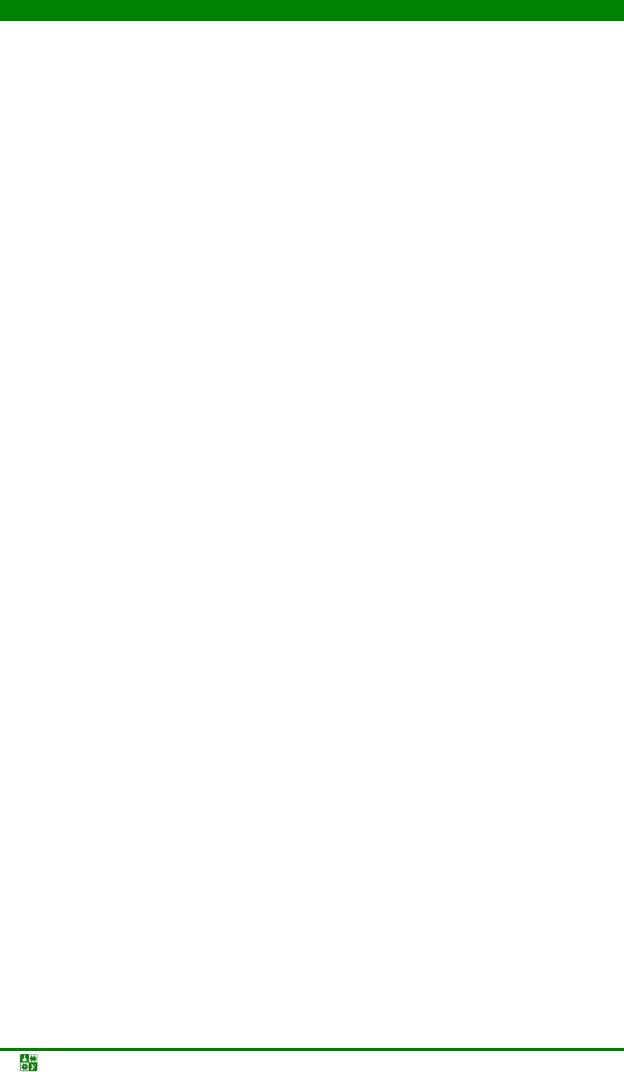
РАЗДЕЛ II. МАТЕРИАЛОВЕДЕНИЕ СТАЛЕЙ И ЧУГУНОВ
Глава 4. Стали, сплавы системы железо–углерод. Маркировка, структура, свойства сплавов
зоны можно получить за 40 ч, если применить двухступенчатый режим азо-
тирования: 510 °С – 15 ч и 550 °С – 25 ч.
По сравнению с цементованными, азотированные слои легированных сталей имеют более высокие твердость и износостойкость. Однако азотирование используют реже, чем цементацию, из-за большей длительности процесса и меньшей толщины упрочненного слоя, что ограничивает величину контактных нагрузок на поверхность детали.
4.8.14.Насыщениеповерхностисталейуглеродомиазотом
Вряде случаев совместное диффузионное насыщение стали азотом и углеродом позволяет получать определенные преимущества. Например, азот способствует диффузии углерода, поэтому можно понизить температуру диффузионного насыщения до 850 °С и получить примерно такое же науглероживание, как при цементации. В этом случае уменьшится рост зерна аустенита и последующую закалку можно проводить сразу же после некоторого подстуживания. Такой процесс называют нитроцементацией, т.к. исходной средой является смесь цементирующего газа с 3–5 % аммиака, а в диффузионной зоне образуются карбонитриды. Нитроцементованный слой хорошо сопротивляется износу и коррозии.
Нитроцементацию широко применяют на автомобильных и тракторных заводах для упрочнения поверхностей нешлифуемых деталей.
Одновременное насыщение стали углеродом и азотом можно также проводить при температуре 820–860 °С в расплавленных солях, содержащих цианистый натрий. В ванне, имеющей состав 20–25 % NаСN, 25–50 % NаС1
и25–50 % Nа2СО3, за 1 ч выдержки при указанной температуре можно получить диффузионный слой толщиной примерно 0,3 мм, который после закалки от 820–860 °С из ванны и отпуска при 180 °С содержит 0,7 % С и 1 % N. Цианированный слой по сравнению с цементованным обладает более высокой износостойкостью.
Существенный недостаток цианирования – ядовитость цианистых солей, что требует принятия специальных мер по охране труда.
Для повышения стойкости быстрорежущего инструмента после закалки
ивысокого отпуска проводят карбонитрацию.
Взависимости от вида инструмента режим процесса устанавливают в следующих пределах: температура расплава 530–570 °С, время выдержки 5– 30 мин.
Ионное азотирование и цементация сталей. Для активизации про-
цессов в газовой среде и на насыщаемой поверхности применяют ионное азотирование (азотирование в плазме тлеющего разряда).
При этом достигается значительное сокращение общего времени процесса (в 2–3 раза) и повышение качества азотированной зоны.
Процесс ионного азотирования ведут в стальном контейнере, который является анодом. Катодом служат азотируемые детали. Через контейнер при низкомдавлениипропускается азотсодержащаягазоваясреда(аммиак, азотидр.).
Материаловедение. Учеб. пособие |
-226- |

РАЗДЕЛ II. МАТЕРИАЛОВЕДЕНИЕ СТАЛЕЙ И ЧУГУНОВ
Глава 4. Стали, сплавы системы железо–углерод. Маркировка, структура, свойства сплавов
Вначале азотируемая поверхность очищается катодным распылением в разреженном азотсодержащем газе или водороде. При напряжении около 1 000 В и давлении 13,33–26,66 Па (1–2 мм рт. ст.) ионы газа бомбардируют и очищают поверхность катода (деталей). Поверхность при этом нагревается до температуры не более 200 °С. Затем устанавливается рабочий режим в диапазоне основных параметров: напряжение 300–800 В, давление 133,3–1333 Па (1–10 мм рт. ст.), удельная мощность 0,7–1 Вт/см2. Поверхность детали нагревается до требуемой температуры (450–550 °С) в результате бомбардировки положительными ионами газа. Ионы азота поглощаются поверхностью катода (детали), а затем идет диффузия вглубь. Параллельно с этим протекает процесс катодного распыления поверхности, что позволяет проводить азотирование трудноазотируемых сплавов, самопроизвольно покрывающихся защитной оксидной пленкой, которая препятствует проникновению азота при обычном азотировании. Ионное азотирование инструментов из быстрорежущей стали повышает стойкость в 2–5 раз в зависимости от условий резания.
Наряду с ионным азотированием начинают применять ионную цементацию деталей. В отличие от ионного азотирования при ионной цементации требуется более высокая температура нагрева поверхности (900–1050 °С), что достигается либо увеличением удельной мощности, либо применением дополнительного внешнего нагрева цементуемых деталей. Исходной газовой средой являются углеводороды, которые разбавляются аргоном или азотом для предотвращения выделений сажи на насыщаемой поверхности. Сажа препятствует науглероживанию.
При ионной цементации, как и при ионном азотировании, наблюдается ускорение диффузионного насыщения, особенно в начальной стадии, и сокращение общей длительности технологического процесса по сравнению с традиционными способами цементации и азотирования.
4.8.15. Диффузионноенасыщениесплавовметалламиинеметаллами
Для многих деталей теплоэнергетического машиностроения требуются жаростойкие покрытия. Их поверхность должна хорошо сопротивляться окислительному действию рабочей или окружающей среды. Традиционными способами получени таких покрытий являются алитирование (алюминирование), хромирование и силицирование из порошковых смесей, содержащих диффундирующий элемент, активизатор (NН4С1, NН4J и др.) и нейтральный порошок (шамот, глинозем и др.) для предотвращения спекания смеси.
Насыщаемые детали вместе с порошком упаковывают в металлические контейнеры с плавкими затворами, нагревают в печи до 1 000–1 200 °С и выдерживают несколько часов для получения диффузионных слоев заданных толщины и структуры.
Наряду с основными или ведущими реакциями протекают побочные, иногда нежелательные превращения. Так, во время нагрева в алитирующей смеси протекают следующие реакции:
Материаловедение. Учеб. пособие |
-227- |
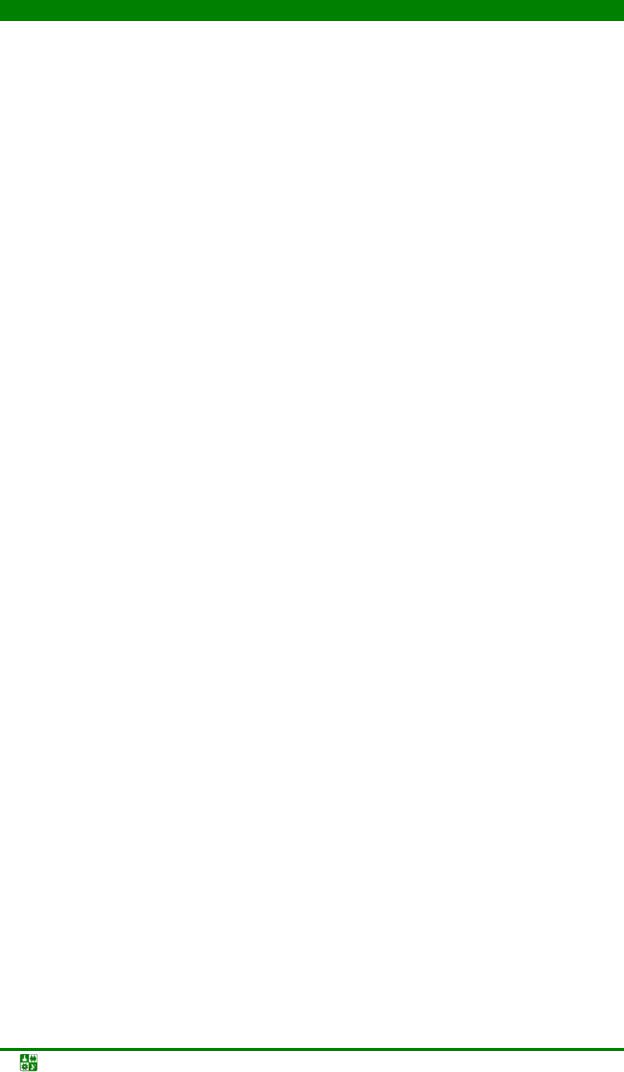
РАЗДЕЛ II. МАТЕРИАЛОВЕДЕНИЕ СТАЛЕЙ И ЧУГУНОВ
Глава 4. Стали, сплавы системы железо–углерод. Маркировка, структура, свойства сплавов
NH4Cl → NH3 + HCl
NH3 →1/2N2 + 3/2H2
HCl + 2/3Al → 2/3AlCl3 + H2
Процесс алитирования различных сплавов происходит либо в результате выделения на насыщаемой поверхности алюминия по реакциям диспропорционирования, либо в результате взаимодействия субхлоридов AlCl2 и А1С1 с элементами насыщаемых сплавов по реакциям типа
А1С12 + Fе → 2/3А1С13 + 1/3Fе3А1 А1С14 + Ni → 2/3А1С13 + 1/3Ni3А1
В соответствии с приведенными реакциями в контейнере в ходе диффузионного насыщения алюминием восстанавливается А1С13, который вновь вступает в обратимые реакции.
На этом принципе основан циркуляционный метод диффузионного насыщения металлов различными элементами. Так, для алитирования в хлоридной среде достаточно в рабочую камеру установки, где находятся обрабатываемые детали и алюминий, ввести пары хлористого алюминия после удаления воздуха.
Циркуляционным методом можно проводить диффузионное насыщение не только алюминием, кремнием, хромом, но и рядом других элементов как в отдельности, так и совместно в специальной установке.
Движущая сила циркуляционного процесса – перепад парциального давления газа-переносчика диффундирующего элемента между зонами расположения исходного материала и насыщаемого сплава. Для получения равномерных покрытий на деталях в муфеле циркуляционной установки поддерживается реверсируемое движение газовой среды.
Для получения многокомпонентных покрытий в рабочую камеру установки загружают одновременно несколько диффундирующих элементов, проведя предварительно термодинамический расчет состава образующейся газовой смеси.
Наиболее широко используется борирование сталей в расплавах буры с добавками восстановителей-карбидов бора и кремния. Насыщение бором проводят при температуре 850–1 050 °С в течение 2–10 ч. Электролизное борирование в расплавленной буре значительно ускоряет процесс диффузионного насыщения. Катодом являются борируемые детали, анодом – графитовые электроды либо тигель из коррозионно-стойкого сплава.
Алитированию, хромированию и силицированию подвергают сплавы на железной, никелевой и других основах. Эти диффузионные покрытия способны защищать детали от окисления при высоких температурах, т.к. на их
Материаловедение. Учеб. пособие |
-228- |
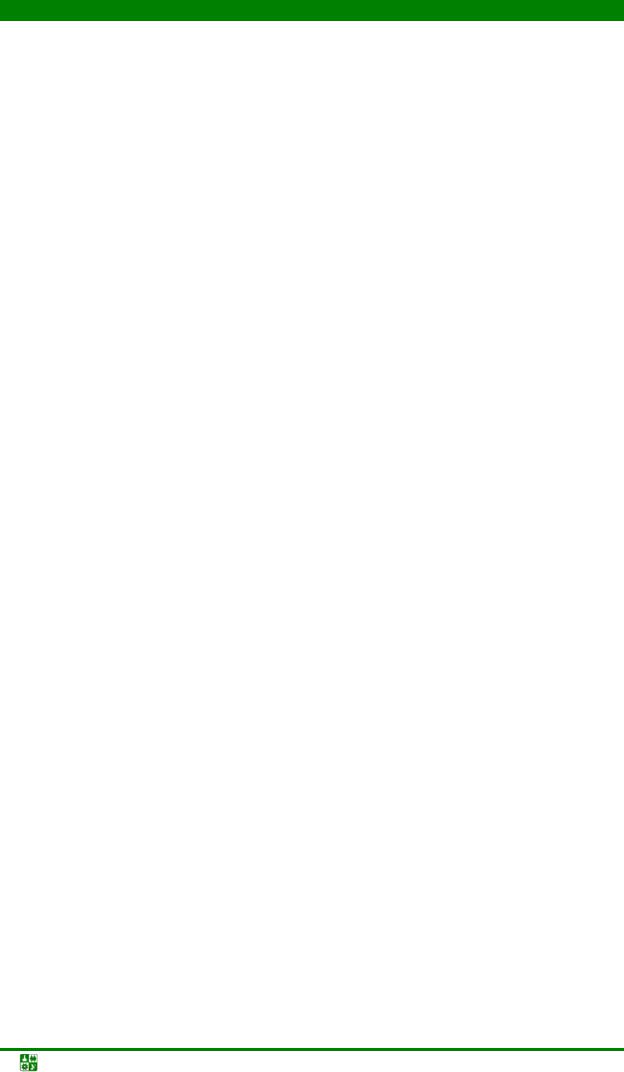
РАЗДЕЛ II. МАТЕРИАЛОВЕДЕНИЕ СТАЛЕЙ И ЧУГУНОВ
Глава 4. Стали, сплавы системы железо–углерод. Маркировка, структура, свойства сплавов
поверхности в окислительной среде образуются плотные пленки из А12О3, Сr2О3 и SiO2, препятствующие диффузии кислорода.
Хромирование среднеуглеродистых сталей (0,3–0,4 % С) приводит к повышению поверхностной твердости и износостойкости, т.к. на поверхности образуется тонкий слой (0,025–0,030 мм) карбида (Сr, Fе)23С6 с твердостью 12 000–13 000 НV. Несмотря на низкую твердость (2 000–3 000 НV), силицированный слой хорошо сопротивляется износу после предварительной пропитки маслом при 170–200 °С.
Наибольшей стойкостью к действию 10 %-го водного раствора азотной кислоты обладают хромотитанированные и хромоалитированные стали. Несколько уступают им хромированные и хромотитаноалитированные стали.
4.9.Конструкционныесталиисплавы
4.9.1.Методыповышенияконструкционнойпрочностисталейисплавов
Технология производства чистой стали. Качество стали зависит от содержания газов, вредных примесей (сера, фосфор, цветные металлы), количества, размеров и формы неметаллических включений.
Для массового производства стали используют мартеновские печи, кислородные конвертеры и дуговые электропечи. Самой чистой по сере и фосфору является электросталь, но по суммарному содержанию примесей цветных металлов и газов она не лучше сталей других способов производства.
Раскисление жидкой стали является основным процессом, снижающим содержание кислорода. Образующиеся оксиды, благодаря меньшей растворимости, переходят из жидкого металла в шлак, однако часть их остается в металле в виде неметаллических включений. Неметаллические включения существенно снижают конструкционную прочность, нарушая сплошность металлической основы. Для улучшения качества жидкой стали в условиях массового производства применяют внепечные методы ее обработки: обработка металла в ковше синтетическими шлаками, продувка аргоном, внепечное вакуумирование в ковше и изложнице при разливке.
Развитие новых отраслей техники обусловило необходимость производства сталей с особыми свойствами – высокой прочностью в сочетании с пластичностью, жаропрочностью, контактной выносливостью. Производство таких материалов стало возможным благодаря применению электрошлакового (ЭШП), вакуумно-дугового (ВДП), электронно-лучевого (ЭЛП) переплавов.
Управление природой неметаллических включений. Зарождение трещин у неметаллических включений обычно происходит либо в результате разрушения включения и переходе трещины из него в металл, либо при отделении включения от металлической матрицы с последующим ростом образовавшейся полости.
Согласно классификации Симса–Даля различают три вида неметаллических включений: глобулярные, пленочные по границам зерен и остроугольные. Наиболее опасны включения второго типа – пленочные, встре-
Материаловедение. Учеб. пособие |
-229- |
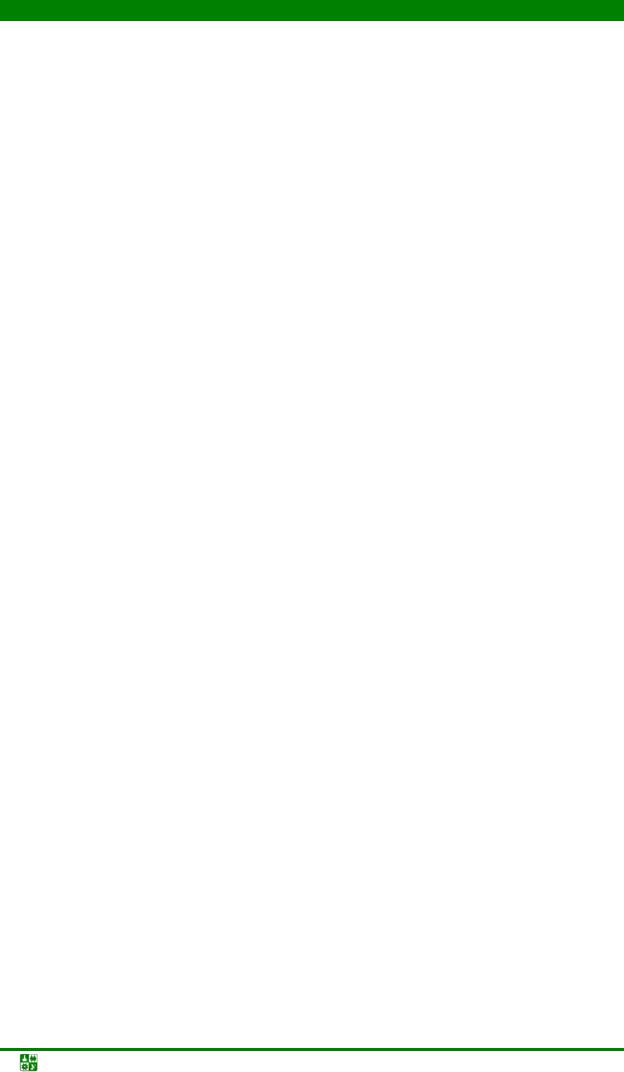
РАЗДЕЛ II. МАТЕРИАЛОВЕДЕНИЕ СТАЛЕЙ И ЧУГУНОВ
Глава 4. Стали, сплавы системы железо–углерод. Маркировка, структура, свойства сплавов
чающиеся сравнительно редко. Поэтому важной задачей современного материаловедения является управление природой включений с целью получения необходимого комплекса механических свойств и повышения конструкционной прочности материалов. Это достигается применением модификаторов, в качестве которых применяют небольшие добавки сплавов на основе редкоземельных (РЗМ) и щелочноземельных (ЩЗМ) металлов. Их важным свойством является высокое химическое сродство к растворенным в сталях примесям серы, кислорода, азота и водорода. При этом сульфиды (оксисульфиды) располагаются преимущественно в осях дендритов в центральных областях литого зерна. ЩЗМ и РЗМ, вводимые в жидкую сталь, не входят в состав твердого раствора, не обогащают границы зерен, а полностью находятся в неметаллических включениях глобулярной формы.
Формирование структуры дисперсными выделениями. Дисперсион-
ное упрочнение происходит при старении многих сплавов, предварительно прошедших закалку на твердый раствор. Этому виду упрочнения подвергаются сплавы на основе алюминия, меди, никеля, кобальта, мартенситостареющие, микролегированные конструкционные стали и др. Прочность повышается в результате распада пересыщенного твердого раствора с образованием дисперсных упрочняющих фаз.
Достоинством дисперсионно-твердеющих сплавов является то, что они могут подвергаться формоизменению с целью изготовления деталей, пока легирующие элементы находятся в растворе, после чего их можно упрочнять за счет старения.
Комбинированное термомеханическое воздействие. Термомеханиче-
ское обработка (ТМО) относится к числу наиболее эффективных способов повышения сопротивления высокопрочных сталей хрупкому разрушению. Комбинированное воздействие пластической деформации и термообработки позволяет наиболее существенно изменить структуру металла и его тонкое строение. ТМО состоит в пластическом деформировании аустенита с последующим быстрым охлаждением и низким отпуском. В зависимости от температуры, при которой производится деформация, различают высокотемпературную (ВТМО) и низкотемпературную (НТМО) термомеханическую обработку.
Регулирование размеров зерна термоциклированием. Размер конеч-
ного зерна стали зависит от различных факторов: химического состава стали, исходной микроструктуры, скорости нагрева в интервале превращения, максимальной температуры нагрева, времени выдержки выше точки Ас3 и числа циклов быстрый нагрев-охлаждение.
Многократные циклы фазового перехода при нагреве и охлаждении позволяют измельчить первичное аустенитное зерно до 14-го балла по шкале АSТМ (средним диаметром зерен 3–5 мкм).
После термоциклирования стали, по сравнению со сталями, прошедшими обычную термическую обработку, имеют значительно более высокие прочностные свойства при одновременном снижении порога хладноломкости в области более низких температур.
Материаловедение. Учеб. пособие |
-230- |
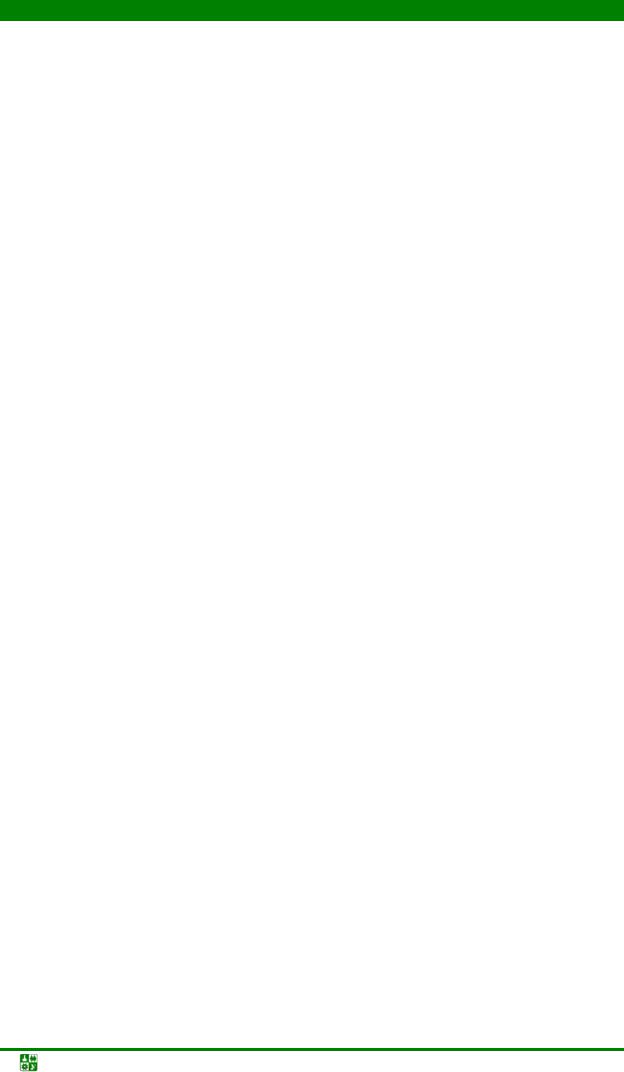
РАЗДЕЛ II. МАТЕРИАЛОВЕДЕНИЕ СТАЛЕЙ И ЧУГУНОВ
Глава 4. Стали, сплавы системы железо–углерод. Маркировка, структура, свойства сплавов
Перспективы космического материаловедения. В наземных лабора-
ториях невоспроизводима длительная невесомость, а для получения ничтожного магнитного поля, глубокого вакуума, температур, близких к абсолютному нулю, требуются большие затраты материальных средств и энергии. Кроме того, в отличие от земных, в космических условиях действие перечисленных факторов проявляется одновременно.
Невесомость позволяет осуществлять в космосе смешивание металлов, расслаивающихся в земных условиях. Благодаря невесомости и силам поверхностного натяжения в условиях космоса возможно получать для шарикоподшипников шары идеальной сферической формы. Такие шары работают без заеданий и биения, являющихся основной причиной выхода из строя шарикоподшипников. Кроме того, при впрыскивании порции инертного газа внутрь капли, свободно парящей в невесомости, можно получить полые шары, которые долговечнее сплошных в несколько раз. Для дополнительного повышения износоустойчивости и стойкости против коррозии можно изготавливать многослойные шары.
Невесомость позволяет реализовать процесс получения прецизионночистых стекол, основанный на методе бестигельной плавки с удержанием расплава силами радиационного давления звукового поля.
4.9.2. Критериивыбораматериалов
Свойство – это количественная или качественная характеристика материала, определяющая его общность или различие с другими материалами.
Выделяют три основные группы свойств: эксплуатационные, технологические и стоимостные, которые лежат в основе выбора материала. Первостепенное значение имеют эксплуатационные свойства.
Эксплуатационными называют свойства материала, которые определяют работоспособность деталей машин, приборов или инструментов, их силовые, стойкостные и другие технико-эксплуатационные показатели.
Работоспособность отдельной группы деталей машин зависит не только от механических свойств, но и от сопротивления воздействию химически активной рабочей среды.
Жаростойкость характеризует способность материала противостоять химической коррозии, развивающейся в атмосфере сухих газов при повышенной температуре.
Коррозионная стойкость – это способность металла противостоять электрохимической коррозии, которая развивается при наличии жидкой среды на поверхности металла и ее электрохимической неоднородности.
Среди технологических свойств главное место занимает технологичность материала – его пригодность для изготовления деталей машин, приборов, инструментов, требуемого качества при минимальных трудовых затратах. Она оценивается обрабатыванием резанием, давлением, свариваемостью,
Материаловедение. Учеб. пособие |
-231- |
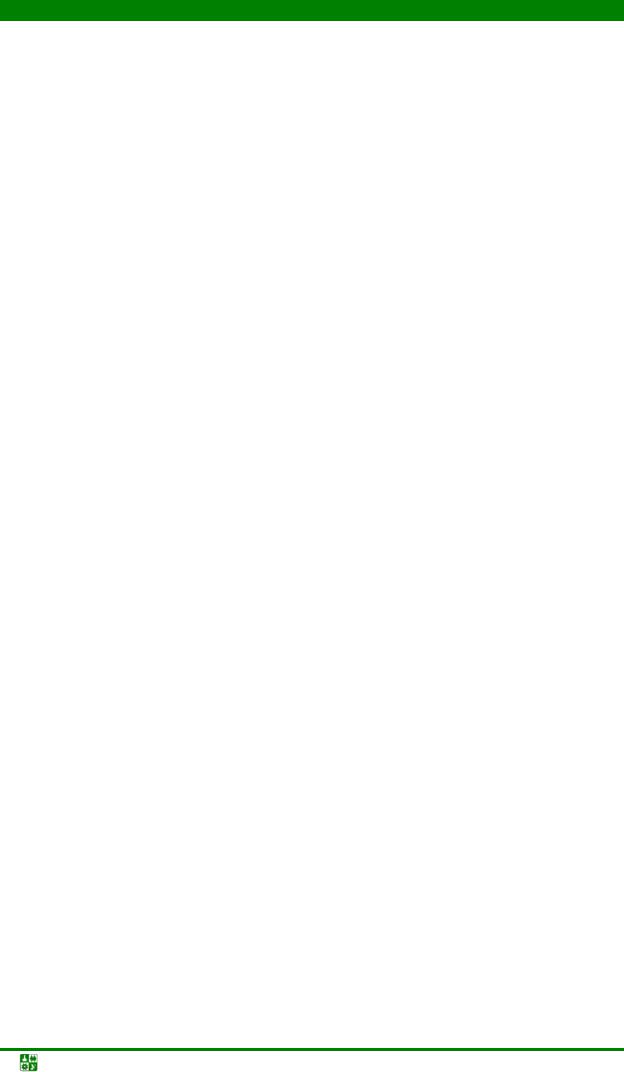
РАЗДЕЛ II. МАТЕРИАЛОВЕДЕНИЕ СТАЛЕЙ И ЧУГУНОВ
Глава 4. Стали, сплавы системы железо–углерод. Маркировка, структура, свойства сплавов
способностью к литью, а также прокаливаемостью, склонностью к деформации и короблению при термической обработке.
К последней группе относится стоимость материала, которая оценивает экономичность его использования. Ее количественным показателем является оптовая цена – стоимость единицы массы материала в виде заготовок, проката, слитков, порошка.
Эксплуатационные требования имеют первостепенное значение. Для того чтобы обеспечить работоспособность конкретных машин и приборов, конструкционный материал должен иметь высокую конструкционную прочность.
Конструкционной прочностью называется комплекс механических свойств, обеспечивающих надежную и длительную работу материала в условиях эксплуатации. Конструкционная прочность – комплексная характеристика, включающая сочетание критериев прочности, надежности и долговечности.
Критерии прочности материала выбирают в зависимости от условий его работы. Критерием прочности при статических нагрузках является временное сопротивление σв или предел текучести σ02 (σт), характеризующие сопротивление материала пластической деформации. Поскольку при работе большинства деталей пластическая деформация недопустима, то их несущую способность, как правило, определяют по пределу текучести. Для приближенной оценки статической прочности используют твердость НВ (для стали справедливо эмпирическое соотношение σв = НВ/3).
Большинство деталей машин испытывает длительные циклические нагрузки. Критерием их прочности является предел выносливости σR (при симметричном круговом изгибе σ–1).
По величине выбранных критериев прочности рассчитывают допустимые рабочие напряжения.
Повышение уровня прочности материала и, как следствие, рабочих напряжений сопровождается увеличением упругих деформаций:
εупр = σ/Е,
где Е – модуль нормальной упругости.
Для ограничения упругой деформации материал должен обладать высоким модулем упругости (или сдвига), являющимся критерием его жесткости. Для пружин, мембран и других чувствительных упругих элементов приборов, наоборот, важно обеспечить большие упругие перемещения. Поскольку εупр = σупр/Е, то от материала требуются высокий предел упругости и низкий модуль упругости.
Для материалов, используемых в авиационной и ракетной технике, важное значение имеет эффективность материала по массе. Она оценивается удельными характеристиками: удельной прочностью σ/(pg) [р – плотность, g – ускорение свободного падения], удельной жесткостью E/(pg).
Материаловедение. Учеб. пособие |
-232- |
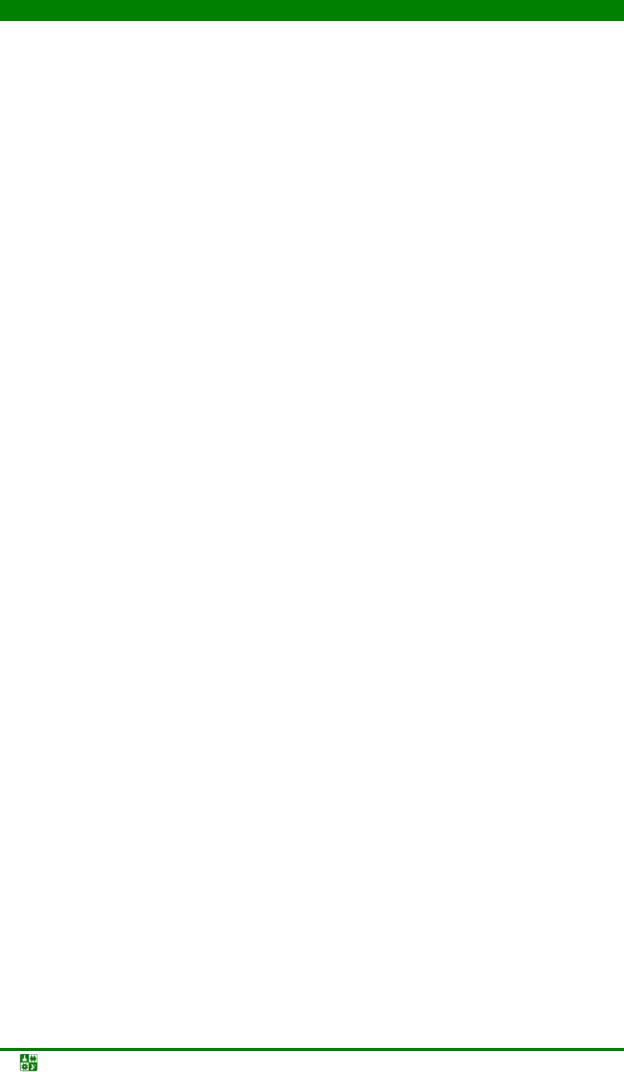
РАЗДЕЛ II. МАТЕРИАЛОВЕДЕНИЕ СТАЛЕЙ И ЧУГУНОВ
Глава 4. Стали, сплавы системы железо–углерод. Маркировка, структура, свойства сплавов
Таким образом, в качестве критериев конструкционной прочности выбирают те характеристики, которые наиболее полно отражают прочность в условиях эксплуатации.
Надежность– свойствоматериалапротивостоятьхрупкомуразрушению. Для предупреждения хрупкого разрушения конструкционные материалы должны обладать достаточной, пластичностью (δ, φ) и ударной вязкостью
(KCU). Необходимо также учитывать то, что в условиях эксплуатации действуют факторы, дополнительно снижающие их пластичность, вязкость и увеличивающие опасность хрупкого разрушения. К таким факторам относятся концентраторы напряжений (надрезы), понижение температуры, динамические нагрузки, увеличение размеров деталей (масштабный фактор).
Для того чтобы избежать внезапных поломок в условиях эксплуатации, необходимо учитывать трещиностойкость материала. Трещиностойкость – группа параметров надежности, характеризующих способность материала тормозить развитие трещины.
Хрупкие материалы, наоборот, чрезвычайно чувствительны к надрезам. Рост трещины не тормозится, как в пластичных материалах, а, наоборот, ускоряется. После достижения некоторой критической величины наступает самопроизвольный лавинообразный рост трещины, вызывающей хрупкое разрушение.
Так как высокопрочные материалы обладают определенной пластичностью, то для них реальную опасность представляют трещины не любых размеров, а только критической длины lкр. Подрастание трещины до lкр тормозится в них местной пластической деформацией. Но при определенном сочетании рабочего напряжения и длины дефекта равновесное положение трещины нарушается и происходит самопроизвольное разрушение. Оценку надежности высокопрочных материалов по размеру допустимого дефекта (меньше критического) проводят по критериям Ж. Ирвина. Им предложено два критерия, из которых наибольшее применение имеет критерий K. Критерий K называют коэффициентом интенсивности напряжений в вершине трещины.
Критерий K для наиболее жесткого нагружения (плоская деформация растяжением) обозначают K–1, при достижении критического значения, когда стабильная трещина переходит в нестабильную – K–1с. Критерий K–1с показывает, какого значения (интенсивности) достигает напряжение вблизи вершины трещины в момент разрушения. Он связывает приложенное среднее напряжение с критической длиной трещины.
Материаловедение. Учеб. пособие |
-233- |
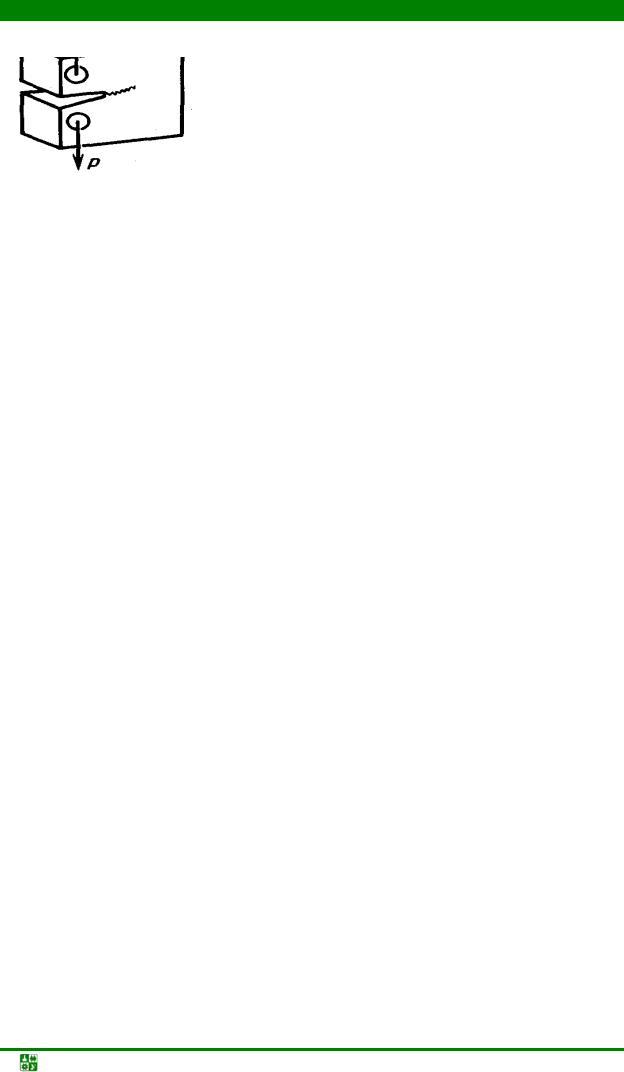
РАЗДЕЛ II. МАТЕРИАЛОВЕДЕНИЕ СТАЛЕЙ И ЧУГУНОВ
Глава 4. Стали, сплавы системы железо–углерод. Маркировка, структура, свойства сплавов
Рис. 4.35. Образец тля определения K–1с
Значение K–1с определяют экспериментально на образцах с надрезом и с заранее созданной на дне этого надреза усталостной трещиной
(рис. 4.35).
Величина K–1с зависит от степени пластической деформации у вершины трещины (ее затуплении) и характеризует сопротивление развитию вязкой трещины. По этой причине критерии K–1с называют вязкостью
разрушения.
Чем он больше, тем выше сопротивление материала вязкому разрушению и его надежность. Кроме качественной характеристики надежности, K–1с дополняет параметры σ02 и Е при расчетах на прочность деталей из высокопрочных материалов (сталей с σв > 1200 МПа, титановых сплавов с σв > 800 МПа и алюминиевых сплавов с σв > 450 МПа). Он позволяет определить безопасный размер трещины при известном рабочем напряжении.
Для оценки надежности материала используют также ударную вязкость KCV и КСТ и температурный порог хладноломкости t50.
Параметром KCV оценивают пригодность материала для сосудов давления, трубопроводов и других конструкций повышенной надежности.
Параметр КСТ, определяемый на образцах с трещиной усталости у основания надреза, более показателен. Он характеризует работу развития трещины при ударном изгибе и оценивает способность материала тормозить начавшееся разрушение.
Порог хладноломкости характеризует влияние снижения температуры на склонность материала к хрупкому разрушению. Его определяют по результатам ударных испытаний образцов с надрезом при понижающейся температуре. Порог хладноломкости обозначают интервалом температур (tн–tк) либо одной температурой t50, при которой в изломе образца имеется 50 % волокнистой составляющей и величина КСТ снижается наполовину.
Долговечность – свойство материала сопротивляться развитию постепенного разрушения (постепенного отказа), обеспечивая работоспособность деталей в течение заданного времени (ресурса). Причины потери работоспособности (постепенного отказа) разнообразны: развитие процессов усталости, изнашивания, ползучести, коррозии, радиационного разбухания и пр. Для большинства деталей машин (более 80 %) долговечность определяется сопротивлением материала усталостным разрушениям (циклической долговечностью) или сопротивлением изнашиванию (износостойкостью).
Циклическая долговечность характеризует работоспособность материала в условиях многократно повторяющихся циклов напряжений. Цикл напряжения – совокупность изменения напряжения между двумя его предельными значениями σmax и σmin в течение периода Т.
Материаловедение. Учеб. пособие |
-234- |
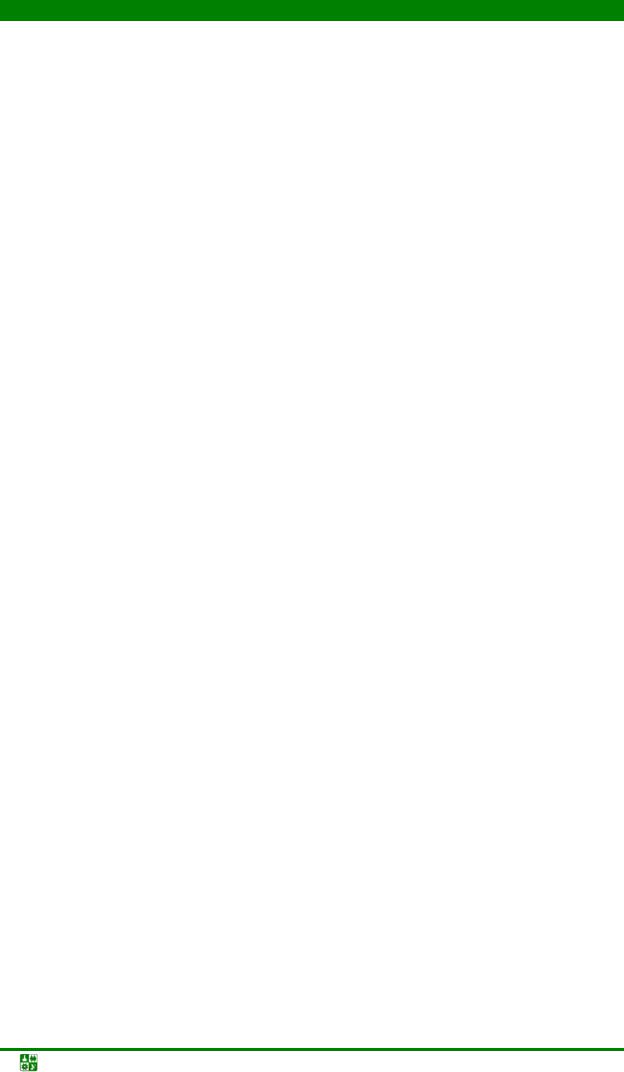
РАЗДЕЛ II. МАТЕРИАЛОВЕДЕНИЕ СТАЛЕЙ И ЧУГУНОВ
Глава 4. Стали, сплавы системы железо–углерод. Маркировка, структура, свойства сплавов
Процессы постепенного накопления повреждений в материале под действием циклических нагрузок, приводящие к изменению его свойств, образованию трещин, их развитию и разрушению, называют усталостью, а свойство противостоять усталости – выносливостью (ГОСТ 23207–78).
Разрушение от усталости по сравнению с разрушением от статической нагрузки имеет ряд особенностей.
1.Разрушение происходит при напряжениях, меньших, чем при статической нагрузке, и меньшем пределе текучести или временном сопротивлении.
2.Разрушение начинается на поверхности , в местах концентрации напряжений (деформации). Локальную концентрацию напряжений создают повреждения поверхности в результате циклического нагружения либо надрезы
ввиде следов обработки, воздействия среды.
3.Разрушение протекает в несколько стадий, характеризующих процессы накопления повреждений в материале, образования трещин усталости.
4.Разрушение имеет характерное строение излома, отражающее последовательность процессов усталости. Излом состоит из очага разрушения (места образования микротрещин) и двух зон – усталости и долома (рис. 4.36).
Рис. 4.36. Излом усталостного разрушения: 1 – очаг зарождения трещины; 2 – зона усталости; 3 – зона долома (схема)
Износостойкость – свойство материала оказывать в определенных условиях трения сопротивление изнашиванию.
Изнашивание – процесс постепенного разрушения поверхностных слоев материала путем отделения его частиц под влиянием сил трения. Результат изнашивания называют износом. Его определяют по изменению размеров (линейный износ), уменьшению объема или массы (объемный или массовый износ). Износостойкость материала оценивают величиной, обратной скорости υ или интенсивности Jh изнашивания.
Скорость и интенсивность изнашивания представляют собой отношение износа, соответственно, к времени или пути трения. Чем меньше значение скорости изнашивания при заданном износе h, тем выше ресурс работы t узла трения:
t = h/υh.
Работоспособность материала детали в условиях эксплуатации характеризуют следующие критерии конструкционной прочности:
Материаловедение. Учеб. пособие |
-235- |
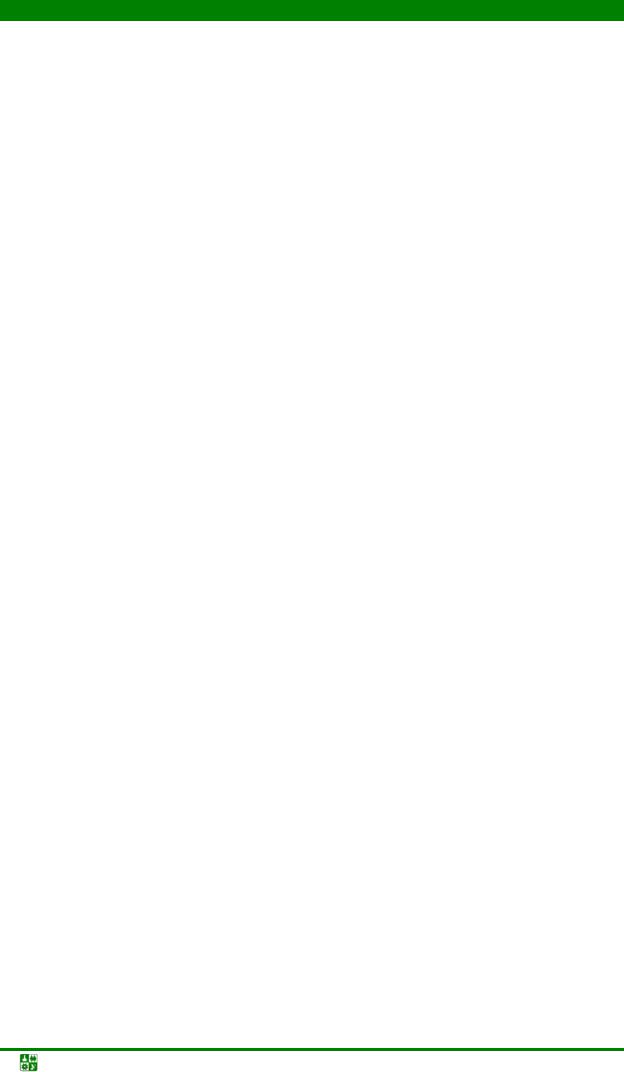
РАЗДЕЛ II. МАТЕРИАЛОВЕДЕНИЕ СТАЛЕЙ И ЧУГУНОВ
Глава 4. Стали, сплавы системы железо–углерод. Маркировка, структура, свойства сплавов
1)критерии прочности σd, σ0,2, σ–1, которые при заданном запасе прочности определяют допустимые рабочие напряжения, массу и размеры деталей;
2)модуль упругости Е, который при заданной геометрии детали определяет величину упругих деформаций, т.е. ее жесткость;
3)пластичность δ, φ, ударная вязкость KСТ, KCV, KCU, вязкость раз-
рушения K1с, температурный порог хладноломкости t50, которые оценивают надежность материала в эксплуатации;
4)циклическая долговечность, скорости изнашивания, ползучести, коррозии, определяющие долговечность материала.
4.9.3.Углеродистыестали
Классификация углеродистых сталей. Углеродистыми сталями называ-
ют железоуглеродистые сплавы с содержанием углерода от 0,05 до 1,35 % углерода. Углеродистые стали подразделяются на конструкционные и инструментальные. Конструкционные стали содержат до 0,65 % С, инструментальные – более 0,65 % С.
Кроме вышеуказанной классификации, углеродистые стали подразделяются по содержанию углерода, по структуре, по назначению, качеству, способу производства.
По содержанию углерода углеродистые стали делятся на низкоуглеродистые (до 0,25 % С), среднеуглеродистые (от 0,3 до 0,5 % С), высокоуглеродистые (более 0,50 % С).
По структуре стали подразделяются на доэвтектоидные при содержании углерода до 0,8 % С, эвтектоидные – 0,8 % С и заэвтектоидные – бо-
лее 0,8 % С.
Углеродистые стали, как наиболее дешевые, технологичные и имеющие достаточно высокий комплекс механических свойств, применяются для металлоконструкций общего назначения, используются в строительных конструкциях, для изготовления деталей в машиностроении и т.д. Стали углеродистые поставляются по ГОСТ 380-94 (стали обыкновенного качества), ГОСТ 1050-88 (прокат из углеродистой качественной конструкционной стали).
По назначению стали подразделяются на стали общего и специального применения. К сталям специального назначения относятся автоматные, котельные, строительные, стали для глубокой вытяжки.
По качеству стали подразделяют на стали обыкновенного качества, качественные и высококачественные.
По способу производства стали подразделяют на деформируемые стали и на литейные.
Согласно диаграмме железо–углерод, к сталям относят сплавы железа с содержанием углерода, менее 2,14 % (все сплавы левее точки Е). Углерод является важнейшим элементом, определяющим структуру и свойства углеродистой стали. Даже при малом изменении содержания углерод оказывает заметное влияние на свойства стали. С ростом содержания углерода увеличивает-
Материаловедение. Учеб. пособие |
-236- |
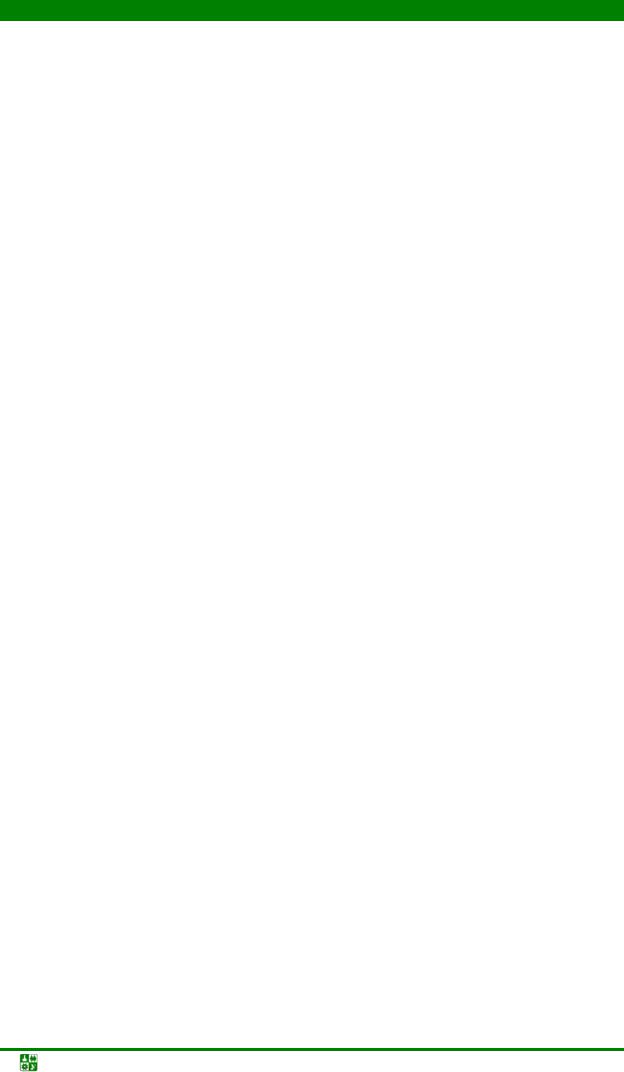
РАЗДЕЛ II. МАТЕРИАЛОВЕДЕНИЕ СТАЛЕЙ И ЧУГУНОВ
Глава 4. Стали, сплавы системы железо–углерод. Маркировка, структура, свойства сплавов
ся твердость и прочность, однако уменьшается вязкость и пластичность стали. Рост прочности происходит при содержании углерода в стали до 0,8 –1,0 %. При увеличении содержании углерода в стали более 0,8 % уменьшается не только пластичность, но и прочность стали. Это связано с образованием сетки хрупкого цементита вокруг перлитных колоний, легко разрушающейся при нагружении.
Углерод оказывает также существенное влияние на технологические свойства стали – свариваемость, обрабатываемость резанием и давлением. Низкоуглеродистые стали хорошо свариваются и имеют высокую обрабатываемость давлением.
Кроме железа и углерода (основных компонентов), в сталях содержатся технологические добавки (марганец, кремний) и примеси, главными из которых, наиболее вредными, являются сера и фосфор.
Сера и фосфор – основные вредные примеси в сталях. Массовая доля серы в стали всех марок по ГОСТ 380-94, кроме Ст0, должна быть не более 0,050 %, фосфора – не более 0,040 %, в стали марки Ст0: серы – не более 0,060 %, фосфора – не более 0,070 %. Кроме того, вредными примесями в сталях являются кислород, водород и азот. Их присутствие вызывает понижение пластичности.
Кислород и азот мало растворимы в феррите. Они загрязняют сталь хрупкими неметаллическими включениями, снижают вязкость и пластичность стали. Повышенное содержание водорода охрупчивает сталь и приводит к образованию внутренних трещин – флокенов.
Деформируемые углеродистые стали. Деформируемые углеродистые стали поставляются металлургическими заводами в горячекатаном состоянии без дополнительной термической обработки, или после термического упрочнения. Из таких сталей производят листы, полосы, прутки, швеллерные и двутавровые прокатанные профили, то есть деформируемые полуфабрикаты. Маркировка и технические условия деформируемых углеродистых конструкционных и инструментальных сталей обыкновенного качества, а также качественных и высококачественных определены, соответственно, в ГОСТ 380-94,
ГОСТ 1050-88, ГОСТ 1435-90.
Углеродистые стали обыкновенного качества. Конструкционные стали обыкновенного качества, благодаря их технологическим свойствам, доступности и возможности получения необходимого комплекса свойств, используются при изготовлении металлоконструкций массового производства, а также слабонагруженных деталей машин и приборов.
Углеродистые стали по ГОСТ 380-94 применяют для изготовления проката горячекатаного: сортового, фасонного, толстолистового, тонколистового, широкополосного и холоднокатаного тонколистового, а также слитков, блюмсов, слябов, сутунки, заготовок катаной и непрерывнолитой, труб, поковок и штамповок, ленты, проволоки, метизов и др.
Материаловедение. Учеб. пособие |
-237- |
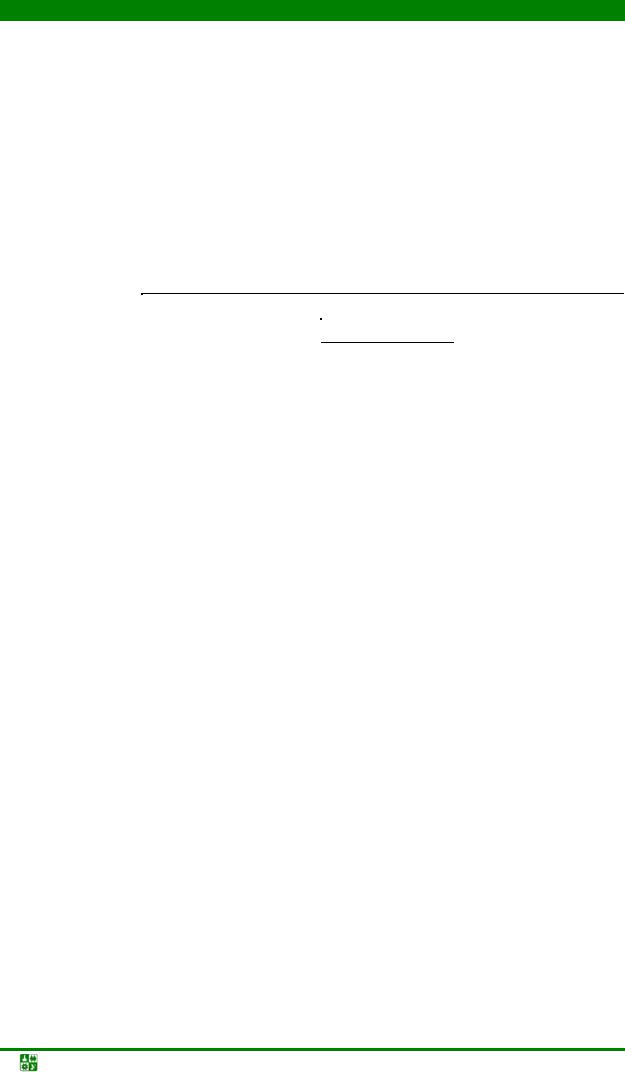
РАЗДЕЛ II. МАТЕРИАЛОВЕДЕНИЕ СТАЛЕЙ И ЧУГУНОВ
Глава 4. Стали, сплавы системы железо–углерод. Маркировка, структура, свойства сплавов
Углеродистые горячекатаные стали, обыкновенного качества по ГОСТ 380-94 «Сталь углеродистая обыкновенного качества» изготовляют следующих марок: Ст0, Ст1кп, Ст1пс, Ст2кп, Ст2пс, Ст3кп, Ст3пс, Ст3сп, Ст3Гпс, Ст3Гсп, Ст4кп, Ст4пс, Ст4сп, Ст5пс, Ст5сп, Ст5Гпс, Ст6пс, Ст6сп
(табл. 4.14).
Таблица 4.14
Марки и химический состав сталей углеродистых обыкновенного качества по ГОСТ 380-94
Марка стали |
|
Массовая доля элементов, % |
|
||
углерода |
|
марганца |
|
кремния |
|
|
|
|
|||
|
|
|
– |
|
|
Ст0 |
Не более 0,23 |
|
|
– |
|
Ст1кп |
0,06–0,12 |
|
0,25–0,50 |
|
Не более 0,05 |
Ст1пс |
0,06–0,12 |
|
0,25–0,50 |
|
0,05–0,15 |
Ст1сп |
0,06–0,12 |
|
0,25–0,50 |
|
0,15–0,30 |
Ст2кп |
0,09–0,15 |
|
0,25–0,50 |
|
Не более 0,05 |
Ст2пс |
0,09–0,15 |
|
0,25–0,50 |
|
0,05–0,15 |
Ст2сп |
0,09–0,15 |
|
0,25–0,50 |
|
0,15–0,30 |
Ст3кп |
0,14–0,22 |
|
0,30–0,60 |
|
Не более 0,05 |
Ст3пс |
0,14–0,22 |
|
0,40–0,65 |
|
0,05–0,15 |
Ст3сп |
0,14–0,22 |
|
0,40–0,65 |
|
0,15–0,30 |
Ст3Гпс |
0,14–0,22 |
|
0,80–1,10 |
|
Не более 0,15 |
Ст3Гсп |
0,14–0,20 |
|
0,80–1,10 |
|
0,15–0,30 |
Ст4кп |
0,18–0,27 |
|
0,40–0,70 |
|
Не более 0,05 |
Ст4пс |
0,18–0,27 |
|
0,40–0,70 |
|
0,05–0,15 |
Ст4сп |
0,18–0,27 |
|
0,40–0,70 |
|
0,15–0,30 |
Ст5пс |
0,28–0,37 |
|
0,50–0,80 |
|
0,05–0,15 |
Буквы Ст обозначают «Сталь», цифры – условный номер марки в зависимости от химического состав стали, буквы «кп» – кипящая, «пс» – полуспокойная, «сп» – спокойная – способ раскисления стали. Массовая доля вредных примесей в стали всех марок, кроме Ст0, должна быть не более 0,050 %, фосфора – не более 0,040 %, в стали марки Ст0 серы – не более 0,060 %, фосфора – не более 0,070 %. Массовая доля углерода в сталях колеблется от 0,06 до 0,49 %, массовая доля марганца – от 0,25 до 0,80 %. Полуспокойные и спокойные стали могут содержать повышенное количество марганца (до 1,20 %), тогда в обозначении марок добавляют букву «Г», например, Ст5Гпс. В кипящих сталях массовая доля кремния составляет не более 0,05 %, в полуспокойных – от 0,05 до 0,15 %, в спокойных – от 0,15 до 0,3 %.
В сталях допускается повышенное содержание вредных примесей, газонасыщенность и загрязненность неметаллическими включениями, поэтому они относятся к наиболее дешевым сталям.
Материаловедение. Учеб. пособие |
-238- |
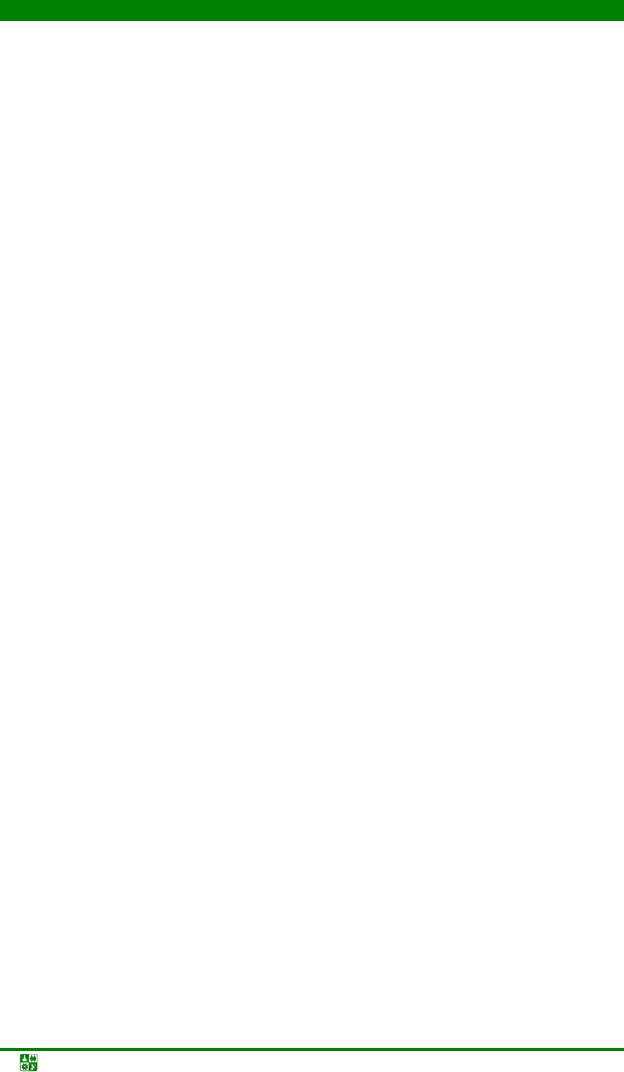
РАЗДЕЛ II. МАТЕРИАЛОВЕДЕНИЕ СТАЛЕЙ И ЧУГУНОВ
Глава 4. Стали, сплавы системы железо–углерод. Маркировка, структура, свойства сплавов
Кипящие стали отличаются от спокойных и полуспокойных более низкой ударной вязкостью. Порог хладноломкости (температура перехода стали из вязкого состояния в хрупкое) у кипящей стали на 30–40 градусов выше, чем у спокойной. Для ответственных конструкций лучше всего использовать спокойные стали. Однако кипящие стали вследствие низкого содержания кремния имеют невысокий уровень предела текучести и упругости. Этим объясняется высокая способность кипящей стали к вытяжке при деформации. Недостатком при использовании сталей обыкновенного качества является малая прочность и малая хладностойкость.
Стали обыкновенного качества Ст2пс, Ст2кп, Ст3кп применяются для неответственных, малонагруженных элементов сварных конструкций. Стали Ст4пс, Ст5сп используются для изготовления деталей клепаных конструкций, болтов, гаек, звездочек, рычагов и других изделий.
Углеродистые качественные конструкционные стали. Стандарт ГОСТ 1050-88 «Прокат сортовой, калиброванный, со специальной отделкой поверхности из углеродистой качественной конструкционной стали» устанавливает технические условия для горячекатаного и кованого сортового проката из сталей марок 05кп, 08кп, 08пс, 08, 10кп, 10пс, 10, 11кп, 15кп, 15пс, 15, 18кп, 20кп, 20пс, 20, 25, 30, 35, 40, 45, 50, 55, 58 (55пп), 60 диамет-
ром или толщиной до 250 мм. Качественные углеродистые стали, по ГОСТ 1050-88 маркируются буквами и цифрами. Двузначные числа показывают содержание углерода в сотых долях процента. Последующее буквенное обозначение указывает на степень раскисления: с – спокойная сталь, пс – полуспокойная сталь, кп – кипящая сталь. При отсутствии буквенного обозначения сталь относят к спокойной стали. Содержание углерода в конструкционных углеродистых сталях составляет от 0,05 до 0,65 %, марганца – от 0,25 до 0,80 %, кремния – от 0,03 до 0,37 % в зависимости от степени раскисления и содержания углерода. По содержанию углерода стали 05кп, 08, 08кп, 10, 15, 20, 25 относятся к низкоуглеродистым сталям, 30, 35, 40, 45, 50 – к среднеуглеродистым, 55, 60 – к высокоуглеродистым.
Главное преимущество сталей качественных по ГОСТ 1050-88 – более низкое содержание серы (не более 0,035 %) и фосфора (не более 0,040 %). Содержание примесей в этих сталях меньше, чем в сталях обыкновенного качества. Массовая доля серы в сталях должна быть не более 0,040 %, фосфора – не более 0,035 %, исключая марки 11кп и 18кп.
Механические свойства проката из углеродистой качественной конструкционной стали по ГОСТ 1050-88 приведены в табл. 4.15. В соответствии с маркой стали увеличение содержания углерода приводит к росту прочности (σв и σт) и уменьшению пластичности (δ и Ψ).
Материаловедение. Учеб. пособие |
-239- |
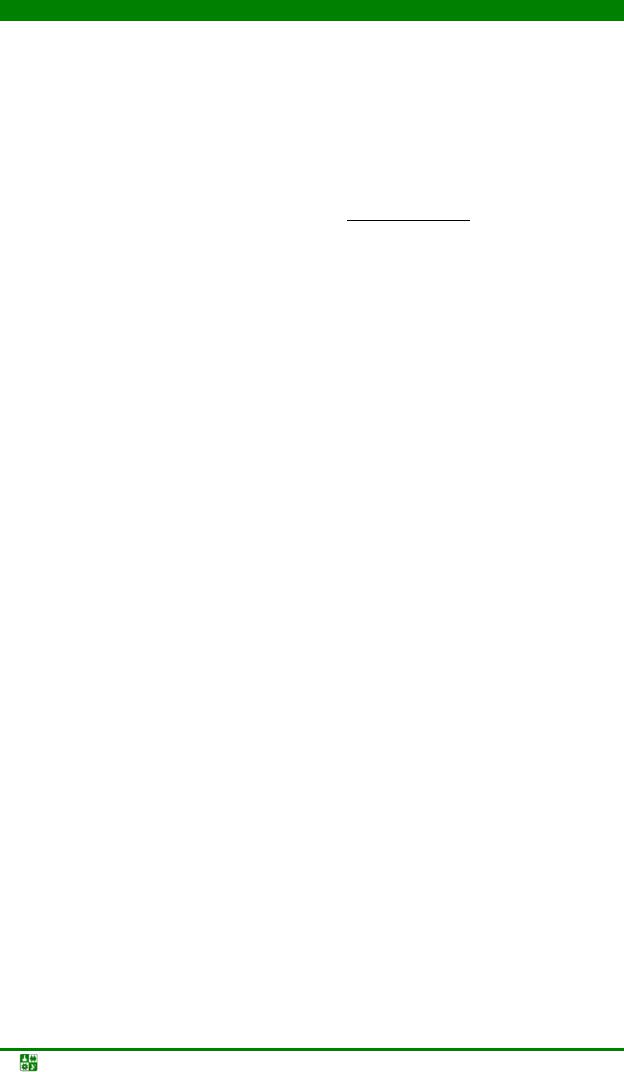
РАЗДЕЛ II. МАТЕРИАЛОВЕДЕНИЕ СТАЛЕЙ И ЧУГУНОВ
Глава 4. Стали, сплавы системы железо–углерод. Маркировка, структура, свойства сплавов
Таблица 4.15
Механические свойства проката из сталей по ГОСТ 1050-88
|
Механические свойства, не менее |
НВ, не более, для горячекатаного |
|||||
Марка |
и кованого проката |
||||||
|
|
|
|
||||
стали |
σт, |
σв, |
δ |
ψ |
Без термиче- |
После отжига или |
|
|
Н/мм2 |
Н/мм2 |
|
% |
ской обработки |
высокого отпуска |
|
08 |
196 |
320 |
33 |
60 |
131 |
– |
|
10 |
205 |
330 |
31 |
55 |
143 |
– |
|
15 |
225 |
370 |
27 |
55 |
149 |
– |
|
20 |
245 |
410 |
25 |
55 |
163 |
– |
|
25 |
275 |
450 |
23 |
50 |
170 |
– |
|
30 |
295 |
490 |
21 |
50 |
179 |
– |
|
35 |
315 |
530 |
20 |
45 |
207 |
– |
|
40 |
335 |
570 |
19 |
45 |
217 |
187 |
|
45 |
355 |
600 |
16 |
40 |
229 |
197 |
|
50 |
375 |
630 |
14 |
40 |
241 |
207 |
|
55 |
380 |
650 |
13 |
35 |
255 |
217 |
|
58 |
315 |
600 |
12 |
28 |
255 |
217 |
|
60 |
400 |
680 |
12 |
35 |
255 |
229 |
Кроме содержания углерода, на уровень механических свойств оказывает большое влияние термическая обработка. Прокат поставляется в отожженном, высокоотпущенном, нормализованном, улучшенном состояниях.
Низкоуглеродистые кипящие стали характеризуются низким пределом текучести, т.к. практически не содержат кремния. Низкоуглеродистые стали типа 05кп, 08, 08кп, 10кп, 10 используются без термической обработки, они хорошо штампуются в отожженном состоянии и применяются в автомобилестроении для изготовления изделий сложной формы: крылья, двери, капот, не несущих деталей кузова.
Стали качественные по ГОСТ 1050-88 предназначены для изготовления широкой номенклатуры изделий, полуфабрикатов, металлоконструкций в строительстве, машиностроении и других отраслях промышленности.
Стали 15, 20, 25 – цементуемые. Данные стали применяют для изделий, работающих в условиях повышенного износа и динамических нагрузок, но не испытывающих значительных напряжений. Из цементуемых сталей 15кп, 20, 25, 20кп изготавливают болты, винты, фланцы, рычаги, шпиндели, клапаны холодильных аппаратов, змеевики и другие детали, работающие при температурах от –40 до +125 °С.
Стали от 30 до 60 – улучшаемые. Детали из них подвергаются закалке с высоким отпуском, что обеспечивает им высокий комплекс механических свойств. Они не склонны к отпускной хрупкости, дешевы, однако обладают низкой прокаливаемостью. Критический диаметр, при котором обеспечива-
Материаловедение. Учеб. пособие |
-240- |
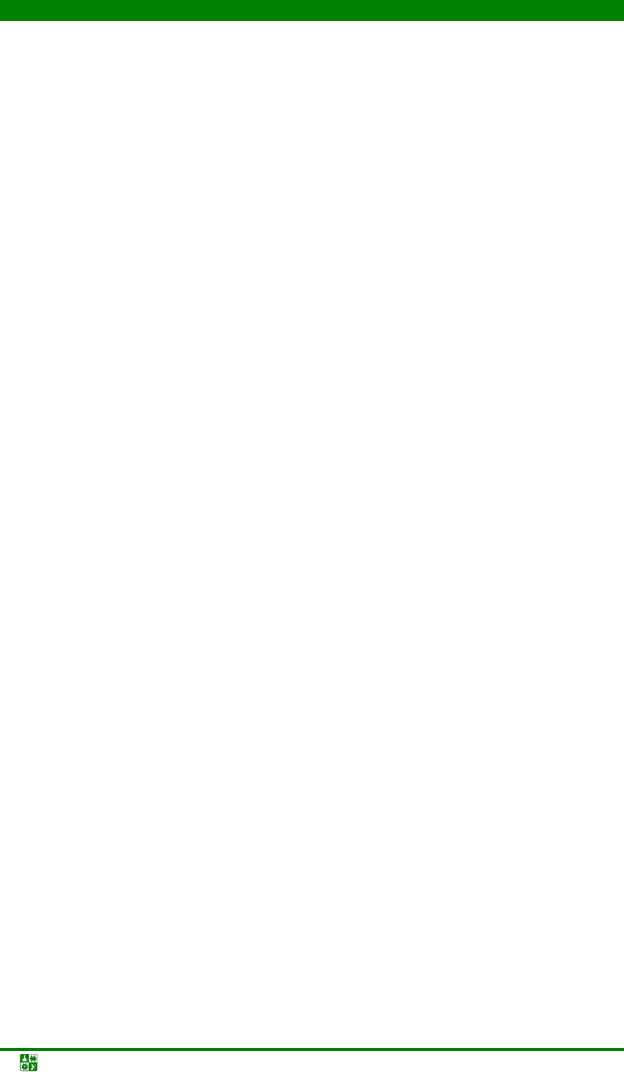
РАЗДЕЛ II. МАТЕРИАЛОВЕДЕНИЕ СТАЛЕЙ И ЧУГУНОВ
Глава 4. Стали, сплавы системы железо–углерод. Маркировка, структура, свойства сплавов
ется сквозная прокаливаемость, не более 12 мм. Улучшаемые стали 30, 35, 40, 45 используются для изготовления деталей средних размеров несложной конфигурации, к которым предъявляются требования повышенной прочности: ролики, валики, втулки, коленчатые валы, звездочки, оси, шайбы, шатуны, зубчатые колеса, болты и др.
Стали с содержанием углерода более 0,6 % (60, 65, 70, 75, 80), а также стали такого же класса, но дополнительно содержащие повышенное количество кремния или марганца (65Г, 60С2, 70С3), применяются для изготовления рессор и пружин. При этом такие стали подвергаются термической обработке, заключающейся в закалке и среднетемпературном отпуске, после которой пружины и рессоры приобретают высокие упругие характеристики механических свойств и большой предел выносливости. Высокоуглеродистые стали применяют после нормализации, закалки, отпуска или поверхностного упрочнения. Они обладают высокой прочностью и износостойкостью, а также высоким пределом упругости.
4.9.4. Влияниелегирующихэлементов наравновеснуюструктуруисвойствасталей
Влияние легирующих элементов на свойства феррита и аустенита. В
конструкционных сталях феррит – основная структурная составляющая (не менее 90 % по объему), во многом определяющая их свойства.
Легирующие элементы, растворенные в феррите, повышают значения временного сопротивления, не изменяя существенно относительного удлинения, за исключением марганца и кремния при содержании их больше 2,5–3,0 % (рис. 4.37). Наиболее сильно упрочняют феррит, кремний, марганец и никель. Остальные элементы сравнительно мало изменяют прочность феррита.
Легирующие элементы при введении их в сталь в количестве 1–2 % снижают ударную вязкость (рис. 4.37, в) и повышают порог хладноломкости. Исключение составляет никель, который упрочняет феррит при одновременном увеличении его ударной вязкости с понижением порога хладноломкости.
Материаловедение. Учеб. пособие |
-241- |
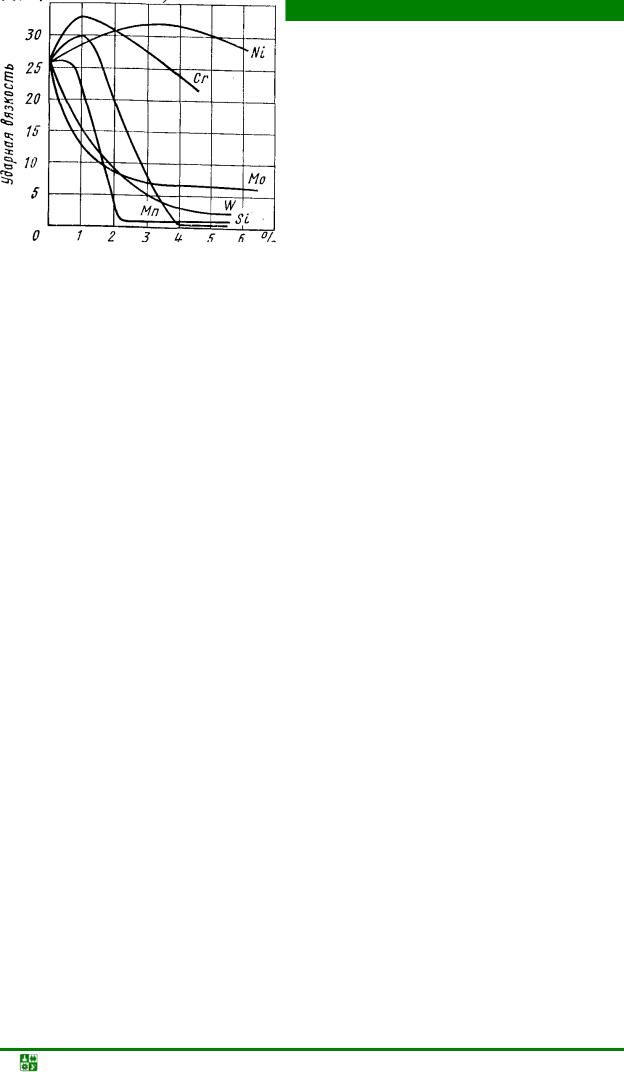
РАЗДЕЛ II. МАТЕРИАЛОВЕДЕНИЕ СТАЛЕЙ И ЧУГУНОВ
Глава 4. Стали, сплавы системы железо–углерод. Маркировка, структура, свойства сплавов
кгс·м/см2
|
легирующего элемента |
Содержание легирующего элемента |
Содержание |
||
|
а |
б |
кгс·м/см2
|
|
Рис. 4.37. Влияние легирующих элементов |
Содержание легирующего элемента |
||
|
в |
на механические свойства феррита |
Феррит, легированный хромом, марганцем и никелем, при быстром охлаждении из области температур γ-раствора претерпевает мартенситное возрастает до 200–250 НВ. Повышение твердости происходит вследствие наклепа феррита в процессе γ → α-превращения, протекающего с увеличением объема. Наклеп, вызываемый фазовыми превращениями, называют фазовым наклепом.
Легирующие элементы, растворяясь в γ-железе, повышают прочность аустенита при нормальной и высоких температурах. Для легированного аустенита характерны низкий предел текучести при сравнительно высоком пределе прочности. Аустенит легко наклепывается, т.е. быстро и сильно упрочняется под действием деформации. Аустенит парамагнитен, обладает большим коэффициентом теплового расширения.
Карбидная фаза в легированных сталях. По отношению к углероду легирующие элементы подразделяют на две группы:
1)графитизирующие элементы: Si, Ni, Сu, А1 (находятся в твердом растворе);
2)карбидообразующие элементы:
Материаловедение. Учеб. пособие |
-242- |
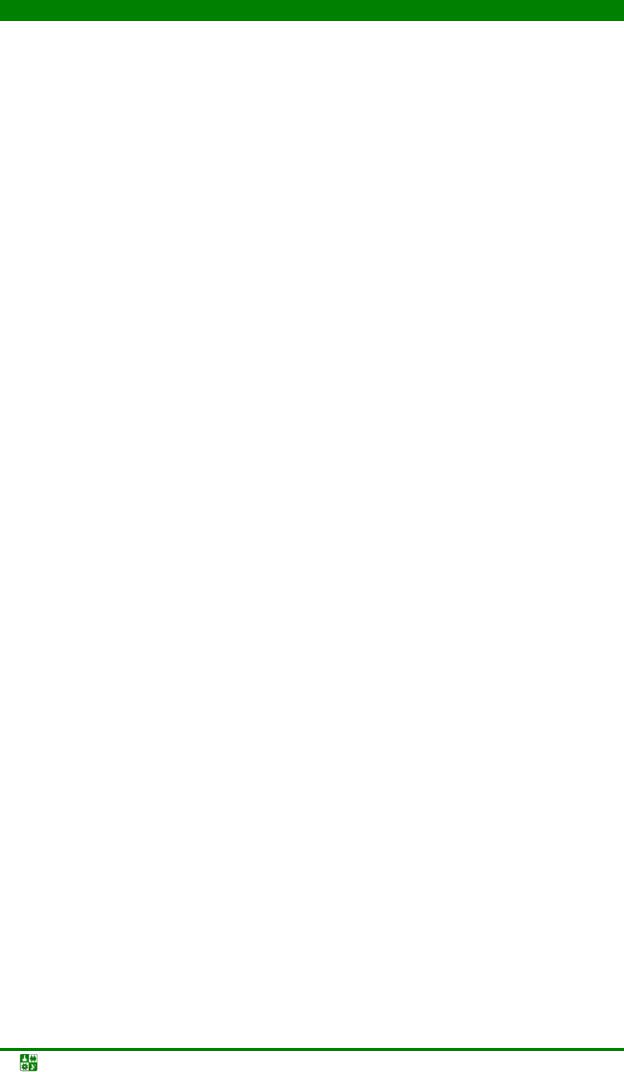
РАЗДЕЛ II. МАТЕРИАЛОВЕДЕНИЕ СТАЛЕЙ И ЧУГУНОВ
Глава 4. Стали, сплавы системы железо–углерод. Маркировка, структура, свойства сплавов
Fe → Мn → Сr → Мо → W → Nb → V → Zr → Ti
(расположены по возрастающей степени сродства к углероду и устойчивости карбидных фаз).
При малом содержании в стали таких карбидообразующих элементов, как Мn, Сr, W и Мо, последние растворяются в цементите, замещая в нем атомы железа. Состав цементита в этом случае может быть выражен формулой (Fe, М)3С, где М – легирующий элемент.
Более сильные карбидообразующне элементы (Ti, Nb, V, Zr) практически не растворяются в цементите и образуют самостоятельные специальные карбиды.
При повышенном содержании хрома, вольфрама, молибдена в зависимости от содержания углерода в стали могут образовываться специальные карбиды. Если содержание хрома не превышает 2 %, то образуется легированный цементит (Fe, Сr)3С. При повышенном содержании хрома образуется специальный карбид (Сr, Fе)7С3. При еще больших содержаниях хрома (более 10–12 %) образуется карбид (Сr, Fe)23C6.
При введении вольфрама и молибдена в сталь в количестве, превышающем предел насыщения цементита этими элементами, образуются слож-
ные карбиды FезМо3С(Fе2Мо2С) и FезW3С(Fе2W2С).
Специальные карбиды, образуемые легирующими элементами, способны растворить железо и другие металлические элементы. Так, например, карбид Сr7С3 при 20 °С растворяет до 55 % Fe, образуя сложный карбид (Сr
, Fе)7С3, а карбид Cr23C6 – до 35 % Fe, образуя карбид (Сr, Fe)23C6.
Приняты следующие обозначения карбидов: М3С (карбиды цементитного типа), М23С6 и М7С3 (карбиды, имеющие кристаллическую решетку карбидов хрома), М6С и М4С (карбиды с решеткой, в которой атомы металла расположены по типу карбидов вольфрама или молибдена) и, наконец, МС (карбиды по типу кубической гранецентрированной решетки). Под символом М подразумевается сумма металлических элементов, входящих в состав карбида.
При высоком содержании легирующие элементы образуют с железом или друг с другом интерметаллические соединения. Примером таких соединений могут служить Fe7Mo6, Fe7W6, Fе3Nb2, Fe3Ti и др. В сплавах Fe–Сr и Fe– V образуются твердая и хрупкая σ-фазы, отвечающие соединению FeCr и FeV.
В сплавах Fe–Сr–Мо (8–27 % Сr и более 5 % Мо), Fе–Сr–Ni–Мо (2–3 % Мо)
может образовываться хрупкая χ-фаза состава Fe3CrMo.
Влияние легирующих элементов на механические свойства сталей.
Легированными называют стали, в которые для получения требуемых свойств специально вводят легирующие элементы. При наличии элементов в количестве примерно 0,1 % легирование называют микролегированием.
Часто легирование сопровождается повышением сопротивления твердого раствора пластической деформации. Так, легирование железа марганцем способствует образованию мартенситной структуры марганцевого феррита, повышению плотности дислокаций и, как следствие, значительному возрастанию прочности твердого раствора. Но есть и исключения: например, ле-
Материаловедение. Учеб. пособие |
-243- |
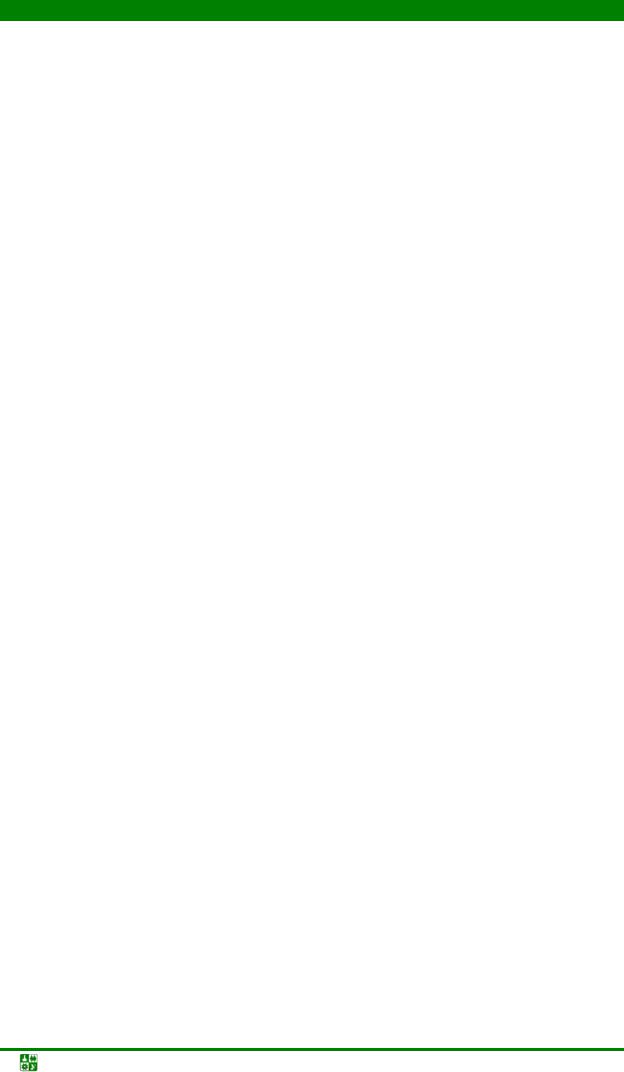
РАЗДЕЛ II. МАТЕРИАЛОВЕДЕНИЕ СТАЛЕЙ И ЧУГУНОВ
Глава 4. Стали, сплавы системы железо–углерод. Маркировка, структура, свойства сплавов
гирование железа хромом в определенных пределах уменьшает прочность твердого раствора. Эффект упрочнения при легировании железа элементами внедрения (азот, углерод) значительно сильнее, чем элементами замещения (никель, марганец). Так, добавление в железо каждой очередной сотой доли процента углерода или азота (0,01 %) повышает предел текучести сплава на 40–50 МПа, в то время как введение аналогичного количества никеля – всего на 0,3 МПа, т.е. эффект упрочнения в последнем случае на два порядка меньше.
Механические свойства сталей зависят от размера зерна. Границы зерен могут являться барьерами для дислокаций, источниками вакансий и дислокаций, а также стоками вакансий. Как показали исследования железа и малоуглеродистой стали, прочность феррита существенно зависит от диаметра.
Так, предел текучести феррита (в отожженной стали) может возрастать при уменьшении размера зерна в три раза.
Легированные стали характеризуются лучшим комплексом физикохимических (в том числе и механических) свойств по сравнению с углеродистыми: они отличаются повышенной жаростойкостью, сопротивлением коррозии, значительной ударной вязкостью, высокими значениями предела текучести и относительного сужения, большим электросопротивлением и др. Оптимальные механические свойства обеспечиваются формированием в результате термической обработки дисперсных структур и более мелкого зерна. Легированные стали могут закаливаться в масле или на воздухе (ибо обладают лучшей прокаливаемостью, чем углеродистые), что способствует уменьшению деформации изделий и вероятности образования трещин.
4.9.5. Влияниелегирующихэлементов наположениекритическихточекипрокаливаемостьсталей
Все элементы, за исключением углерода, азота, водорода и отчасти бора образуют с железом твердые растворы замещения. Они растворяются в железе и влияют на положение точек А3 и А4, определяющих температурную область существования α- и γ-железа.
К элементам первой группы относятся никель и марганец, которые понижают точку А3 и повышают точку А4. В результате этого на диаграмме состояния железо–легирующий элемент наблюдается расширение области γ-фазы и сужение области существования α-фазы (рис. 4.38, а). Как видно на рисунке, под влиянием легирующих элементов точка А4 повышается до линии солидус, а точка А3 при повышенной концентрации легирующего элемента снижается до нормальной температуры. Следовательно, сплавы, имеющие концентрацию легирующего элемента больше указанной на рисунке (точка х), не испытывают фазовых превращений α ↔ γ, при всех температурах представляют твердый раствор легирующего элемента в γ-железе. Такие сплавы называют аустенитными.
Материаловедение. Учеб. пособие |
-244- |
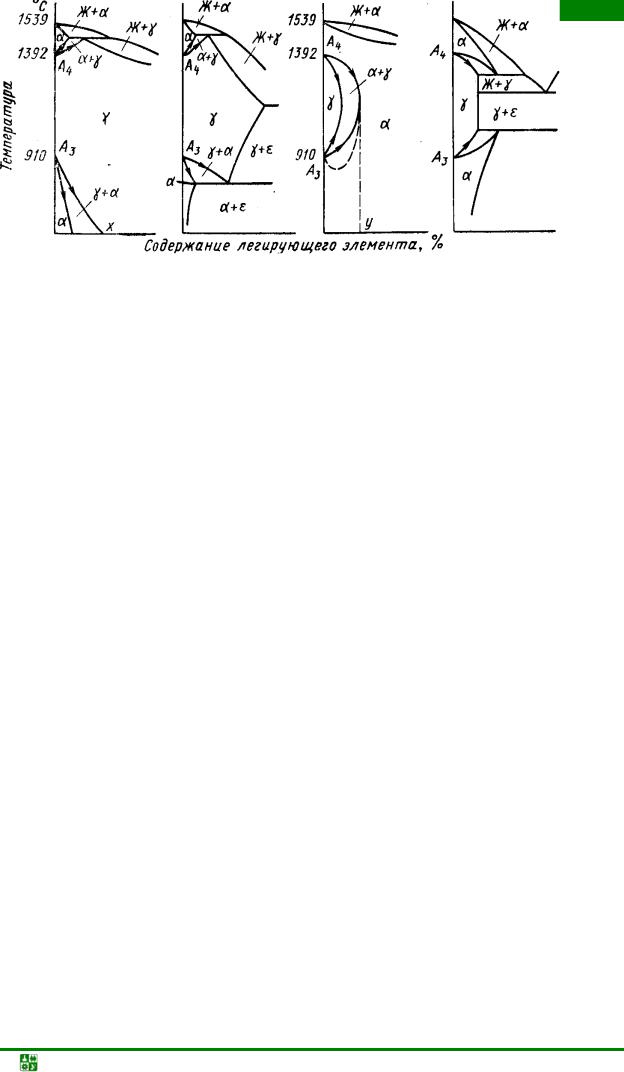
РАЗДЕЛ II. МАТЕРИАЛОВЕДЕНИЕ СТАЛЕЙ И ЧУГУНОВ
Глава 4. Стали, сплавы системы железо–углерод. Маркировка, структура, свойства сплавов
γ
а |
б |
в |
г |
Рис. 4.38. Схема влияния легирующих элементов на полиморфизм железа
Сплавы, частично претерпевающие превращение α ↔ γ, называют по-
луаустенитными.
К элементам первой группы относятся также медь, углерод и азот, но они при небольшом содержании в сплаве расширяют область существования гомогенной γ-фазы (рис. 4.38, б), а при большем содержании вследствие их ограниченной растворимости в железе сначала сужают однофазную область γ-фазы и затем ее полностью выключают.
Элементы второй группы (Cr, W, Мо, V, Si, A1 и др.) понижают точку А4 и повышают точку А3. Это приводит к тому, что при определенной концентрации легирующих элементов (точка y на рис. 4.38, в) критические точки А3 и А4, а точнее их интервалы, сливаются, и область γ-фазы полностью замыкается. При содержании легирующего элемента большем, чем указано на рис. 4.38, в, сплавы при всех температурах состоят из твердого раствора легирующего элемента в α-железе. Такие сплавы называют ферритными, а сплавы, имеющие лишь частичное превращение, – полуферритными.
Такие легирующие элементы, как бор, цирконий, ниобий, даже при сравнительно небольшом содержании способствуют сужению области γ-фазы. Однако вследствие их малой растворимости в железе, прежде чем наступает полное замыкание однофазной области γ-фазы, образуются двухфазные сплавы (рис. 4.38, г).
Основой современных сложнолегированных сталей являются не двойные, а тройные, четвертные и более сложные твердые растворы. При введении в сплав нескольких легирующих элементов их влияние на α- и γ-области диаграммы состояния не всегда суммируется.
Углерод чаще повышает растворимость легирующих элементов в γ-растворе (аустените), сдвигая точку y вправо. Такие элементы, как Ni, Co, Si, W, Мо, Сr, Mn, точки S и Е сдвигают влево в сторону меньшего содержания углерода, а V, Ti, Nb, наоборот, повышают концентрацию углерода в эв-
Материаловедение. Учеб. пособие |
-245- |
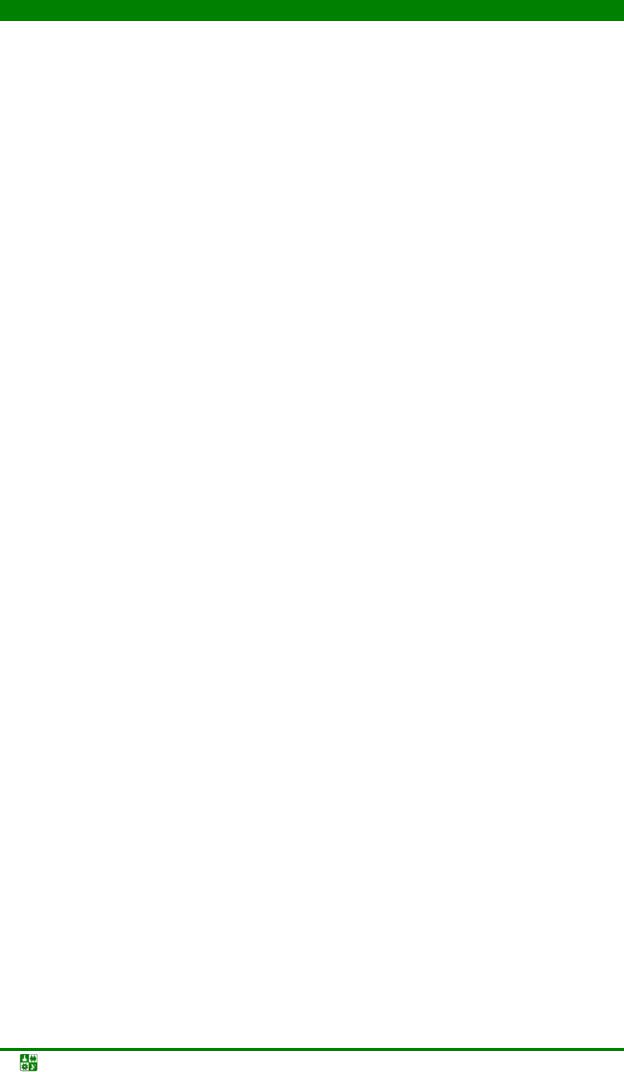
РАЗДЕЛ II. МАТЕРИАЛОВЕДЕНИЕ СТАЛЕЙ И ЧУГУНОВ
Глава 4. Стали, сплавы системы железо–углерод. Маркировка, структура, свойства сплавов
тектоиде. Это объясняется тем, что составы феррита и карбидов в эвтектоиде (перлите) иные, чем в двойных железоуглеродистых сплавах. Соответственно, из-за изменения состава аустенита меняется и растворимость в нем углерода.
Нагрев легированных сталей приводит при соответствующей температуре (выше А1) к образованию аустенита. Но в легированных сталях, содержащих карбидообразующие элементы, при достаточном количестве углерода имеется карбидная фаза, которая в зависимости от её природы полностью или частично переходит в γ-твердый раствор при более высоких температурах. Наличие, наряду с аустенитом, нерастворившейся карбидной фазы (а также нитридной, карбонитридной, оксидной и др.) задерживает рост аустенитного зерна.
При высоком содержании легирующих элементов и углерода бейнитное превращение на диаграмме изотермического превращения переохлажденного аустенита может отсутствовать. При высоком содержании некарбидообразующих элементов и низком содержании углерода, напротив, перлитное превращение полностью отсутствует, и тогда говорят о том, что сталь не отжигается.
В подавляющем большинстве случаев легирующие элементы сдвигают область минимальной устойчивости в области перлитного превращения вправо, и поэтому уменьшают критическую скорость закалки и увеличивают прокаливаемость. Во многих легированных сталях, как уже указывалось выше, области бейнитного и перлитного превращений разделены. Это является характерным признаком легированных сталей.
Введение легирующих элементов в сталь (за исключением кобальта) снижает температуру начала и конца мартенситного превращения (Мн и Мк), что сказывается на кинетике мартенситного превращения и количестве остаточного аустенита.
При снижении мартенситной точки до 0 °С и ниже сталь не претерпевает превращения А → М, и закалка фиксирует аустенитную структуру. Сталь относится к аустенитному классу.
Для развития превращений при отпуске необходимы диффузионные перемещения атомов легирующих элементов. В связи с этим легирующие элементы замедляют или, соответственно, повышают температурные границы указанных выше превращений, но не оказывают существенного влияния на первое превращение, для развития которого требуется только диффузия атомов углерода.
При высоком содержании карбидообразующих легирующих элементов, например в быстрорежущих сталях, при отпуске образуются специальные карбиды (при температурах выше 500−550 °С).
При низком отпуске, отвечающем превращению мартенсита, тетрагональность его решетки убывает за счет выделения ε-карбида, содержащего легирующие элементы в том же количестве, что и в исходном мартенсите. Второе превращение, связанное с образованием бейнита, из остаточного аустенита отсутствует, а третье − выражено слабо. Начиная с температуры
Материаловедение. Учеб. пособие |
-246- |
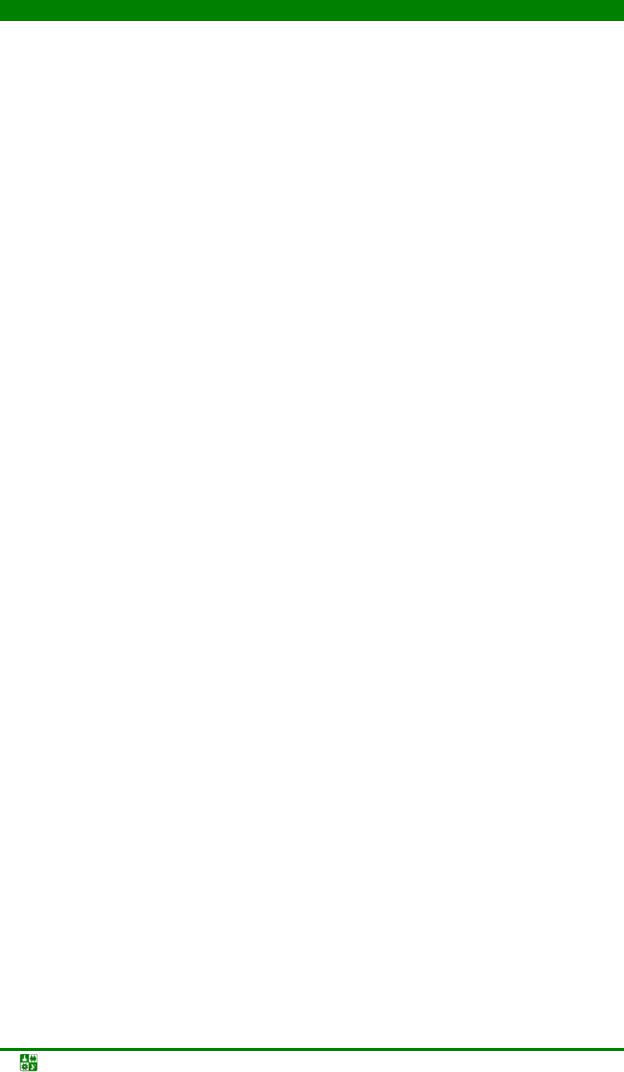
РАЗДЕЛ II. МАТЕРИАЛОВЕДЕНИЕ СТАЛЕЙ И ЧУГУНОВ
Глава 4. Стали, сплавы системы железо–углерод. Маркировка, структура, свойства сплавов
примерно 500 °С ранее образовавшийся карбид цементитного типа растворяется, и из α-твердого раствора выпадает легированый или специальный карбид.
Никель увеличивает пластичность и вязкость стали, снижает температуру порога хладноломкости и уменьшает чувствительность стали к концентраторам напряжений, перечисленные факторы способствуют повышению сопротивления стали хрупкому разрушению.
Хром повышает жаростойкость и коррозионную стойкость стали, увеличивает ее электрическое сопротивление и уменьшает коэффициент линейного расширения. Легирование стали хромом приводит к уменьшению склонности аустенитного зерна к росту при нагреве, существенному увеличению ее прокаливаемости, а также к замедлению процесса распада мартенсита.
Кремний широко используется при выплавке стали как раскислитель. Легирование кремнием углеродистых и хромистых сталей увеличивает их жаростойкость. Уменьшая подвижность углерода в феррите, кремний тем самым затрудняет формирование и рост цементитных частиц, что проявляется в повышении устойчивости структуры стали при отпуске. Содержание кремния в стали ограничивают, поскольку он повышает склонность стали к тепловой хрупкости.
Марганец подобно никелю, снижает критическую скорость охлаждения, но в отличие от последнего уменьшает и вязкость феррита.
Вольфрам, молибден, ванадий, титан, бор и другие вводят в сталь со-
вместно с хромом, никелем и марганцем для дополнительного улучшения ее свойств.
Молибден и вольфрам повышают прокаливаемость стали (особенно в присутствии никеля), способствуют измельчению зерна и подавлению отпускной хрупкости. Легирование стали молибденом приводит к значительному улучшению ее механических свойств после цементации и нитроцементации.
При введении в сталь ванадия, титана, ниобия и циркония образуются труднорастворимые в аустените карбиды. Эффективность воздействия этих элементов (измельчение зерна, снижение порога хладноломкости, уменьшение чувствительности стали к концентраторам напряжений) проявляется лишь при их малом содержании в стали (до 0,15 %).
Положительное влияние бора на повышение прокаливаемости и прочности стали проявляется лишь при микролегировании им (0,001–0,005 %), когда атомы бора располагаются в приграничных слоях зерна аустенита, заполняют вакансии, делая структуру границ более совершенной, и таким образом уменьшают скорость зарождения центров кристализации перлита. При повышенном содержании бора он выделяется по границам зерен в виде боридов, сильно охрупчивая сталь.
Материаловедение. Учеб. пособие |
-247- |
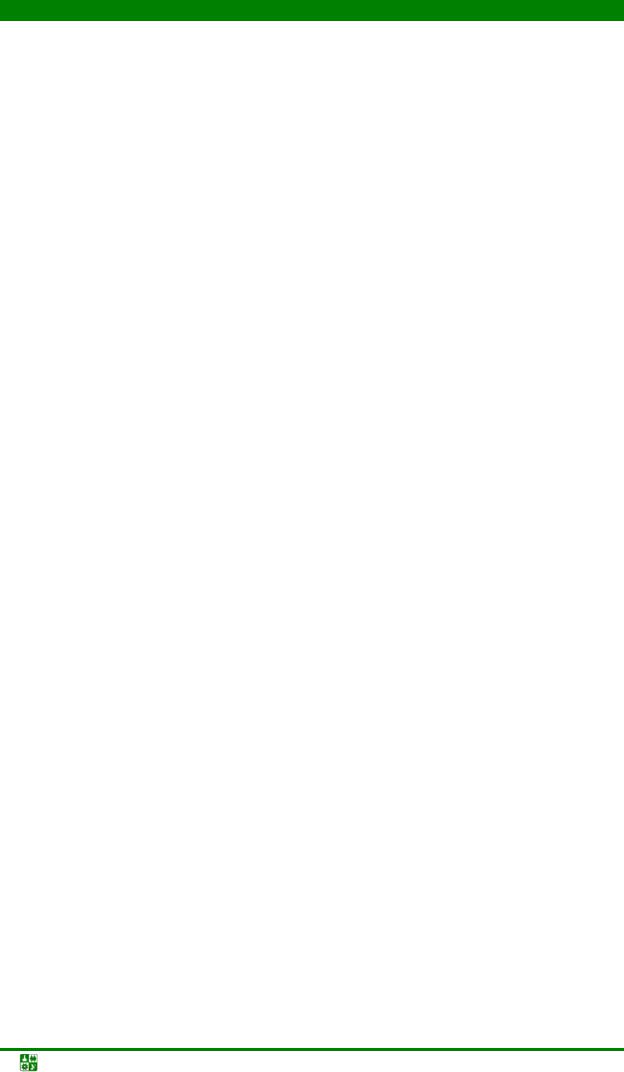
РАЗДЕЛ II. МАТЕРИАЛОВЕДЕНИЕ СТАЛЕЙ И ЧУГУНОВ
Глава 4. Стали, сплавы системы железо–углерод. Маркировка, структура, свойства сплавов
4.9.6. Классификацияимаркировкалегированныхсталей
По типу равновесной структуры стали подразделяются на доэвтектоидные, эвтектоидные, заэвтектоидные и ледебуритные. Эвтектоидные ста-
ли имеют перлитную структуру, а доэвтектоидные и заэвтектоидные наряду с перлитом содержат соответственно избыточный феррит или вторичные карбиды типа М3С. В структуре литых ледебуритных (карбидных) сталей присутствует эвтектика (ледебурит), образованная первичными карбидами вместе с аустенитом, поэтому по структуре они могут быть отнесены к белым чугунам, но их причисляют к сталям с учетом меньшего, чем у чугунов, содержания углерода (менее 2 %) и возможности подвергать пластической деформации. Влияние легирующих элементов на положение точек S и Е диаграммы Fe–С проявляется чаще всего в их смещении в направлении меньшего содержания углерода. В сталях с высоким содержанием элементов, сужающих γ-область, при определенной концентрации исчезает γ ↔ α- превращение. Такие стали относят к ферритному классу. При высокой концентрации в стали элементов, расширяющих γ-область, происходит стабилизация аустенита с сохранением его при охлаждении до комнатной температуры. Эти стали причисляют к аустенитному классу. Таким образом, с учетом фазового равновесия легированные стали относят к перлитному, карбидному,
ферритному или аустенитному классам.
Классификация по структуре после нормализации предполагает разделение сталей на три основных класса: перлитный, мартенситныи и аустенитный. Такое подразделение обусловлено тем, что с увеличением содержания легирующих элементов в стали возрастает устойчивость аустенита в перлитной области (это проявляется в смещении вправо С-образных кривых), одновременно снижается температурная область мартенситного превращения. Все это приводит к изменению получаемых при нормализации структур от перлита (сорбита, троостита и бейнита) в относительно малолегированных сталях до мартенсита (в легированных) и аустенита (в высоколегированных).
Классификация по химическому составу предполагает разделение легированных сталей (в зависимости от вводимых элементов) на хромистые, марганцовистые, хромоникелевые, хромоникельмолибденовые и т.д. Согласно той же классификации, стали подразделяют по общему количеству легирующих элементов в них на низколегированные (до 2,5 % легирующих эле-
ментов), легированные (от 2,5 до 10 %) и высоколегированные (более 10 %).
Разновидностью классификации по химическому составу является классификация по качеству. Качество стали – это комплекс свойств, обеспечиваемых металлургическим процессом, таких как однородность химического состава, строения и свойств стали, ее технологичность. Эти свойства зависят от содержания газов (кислород, азот, водород) и вредных примесей – серы и фосфора.
Материаловедение. Учеб. пособие |
-248- |
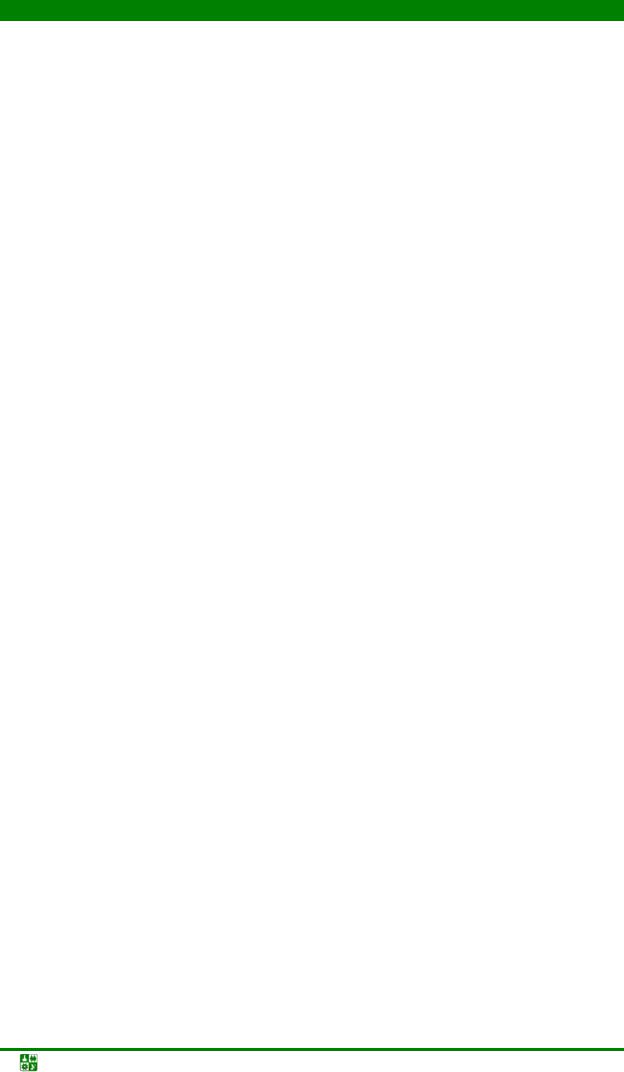
РАЗДЕЛ II. МАТЕРИАЛОВЕДЕНИЕ СТАЛЕЙ И ЧУГУНОВ
Глава 4. Стали, сплавы системы железо–углерод. Маркировка, структура, свойства сплавов
По качеству легированные стали подразделяют на качественные
(до 0,04 % S и до 0,035 % Р), высококачественные (до 0,025 % S и до 0,025 % Р)
и особовысококачественные (до 0,015 % S и до 0,025 % Р).
По назначению стали подразделяют на конструкционные (например, цементуемые, улучшаемые), инструментальные и с особыми свойствами. К последним относят «автоматные», пружинные, шарикоподшипниковые, износостойкие, коррозионностойкие, теплоустойчивые, жаропрочные, электротехнические и другие стали.
Маркировка легированных сталей. Обозначение марки включает в се-
бя цифры и буквы, указывающие на примерный состав стали. В начале марки приводятся двузначные цифры (например, 12ХНЗА), указывающие среднее содержание углерода в сотых долях процента. Буквы справа от цифры обозначают легирующие элементы: А – азот, Б – ниобий, В – вольфрам, Г – марганец, Д – медь, Е – селен, К – кобальт, Н – никель, М – молибден, П – фосфор, Р – бор, С – кремний, Т – титан, Ф – ванадий, Х – хром, Ц – цирконий, Ч – редкоземельные элементы, Ю – алюминий. Следующие после буквы цифры указывают примерное содержание (в целых процентах) соответствующего легирующего элемента (при содержании 1–1,5 % и менее цифра отсутствует, например 30ХГС).
Высококачественные стали обозначаются буквой А, а особовысококачественные – буквой Ш, помещенными в конце марки (30ХГСА, 30ХГС-Ш). Если буква А расположена в середине марки (14Г2АФ), то это свидетельствует о том, что сталь легирована азотом. При обозначении автоматных сталей с повышенной обрабатываемостью резанием буква А ставится в начале марки (А20, А40Г). Если автоматная сталь легирована свинцом, то обозначение марки начинается с сочетания букв АС (АС35Г2, где цифра 35 обозначает среднее содержание углерода в сотых долях процента). Маркировка шарикоподшипниковой стали начинается с буквы Ш (ШХ15, где 15 – среднее содержание хрома в десятых долях процента). В начале обозначения марки быстрорежущих сталей стоит буква Р, за которой следует цифра, отражающая концентрацию вольфрама (Р18, Р6М5). Опытные стали, выплавленные на заводе «Электросталь», первоначально обозначают буквами ЭИ (электросталь исследовательская) или ЭП (электросталь пробная) с порядковым номером разработки (освоения), например, ЭИ962 (11Х11Н2В2МФ), ЭП33 (10Х11Н23Т3МР). Такое упрощенное обозначение сталей, особенно высоколегированных, в дальнейшем широко используется и в заводских условиях.
4.9.7. Автоматныестали
Автоматные стали хорошо обрабатываются при больших скоростях резания, и при этом получается высокое качество. При их применении снижается расход режущего инструмента. Эти свойства достигаются повышением в автоматных сталях содержания серы и фосфора.
Материаловедение. Учеб. пособие |
-249- |
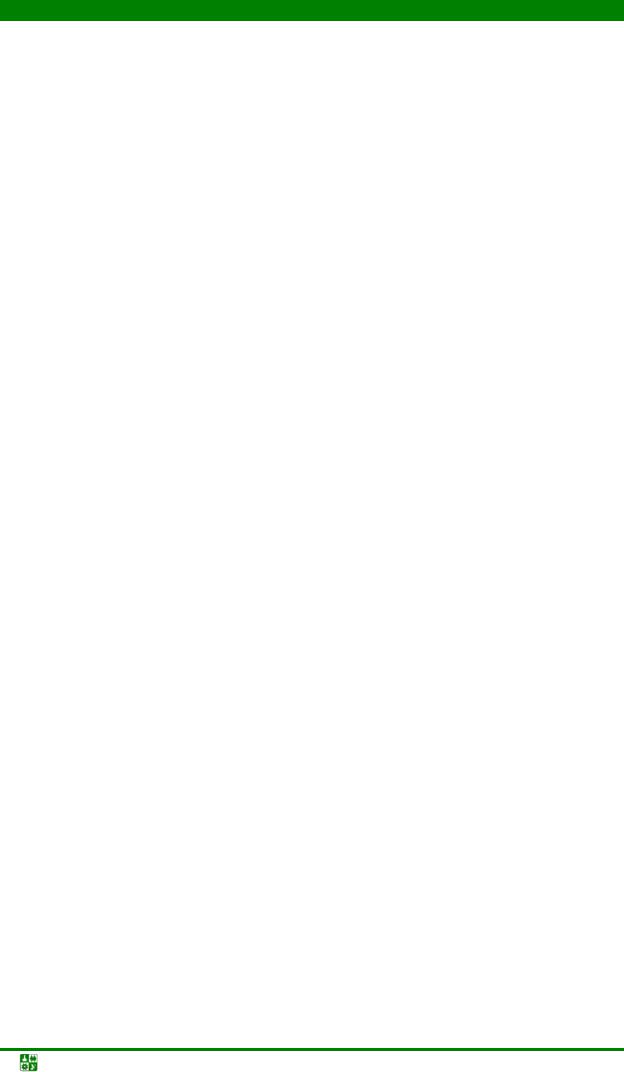
РАЗДЕЛ II. МАТЕРИАЛОВЕДЕНИЕ СТАЛЕЙ И ЧУГУНОВ
Глава 4. Стали, сплавы системы железо–углерод. Маркировка, структура, свойства сплавов
Сера в автоматной стали находится в виде сульфидов марганца MnS, т.е. вытянутых вдоль прокатки включений, которые способствуют образованию короткой и ломкой стружки. При повышенном содержании серы уменьшается трение между стружкой и инструментом из-за смазывающего действия сульфидов марганца.
Фосфор, повышая твердость, прочность и порог хладноломкости, способствует образованию ломкой стружки и получению гладкой блестящей поверхности при резании.
Состав автоматных сталей приведен в табл. 4.16.
Таблица 4.16
Химический состав автоматных сталей
Марка стали |
C |
Mn |
Si |
S |
P |
|
|
|
|
|
|
А12 |
0,08–0,16 |
0,7–1,0 |
0,15–0,35 |
0,08–0,20 |
0,08–0,15 |
А20 |
0,17–0,24 |
0,7–1,0 |
0,15–0,35 |
0,08–0,15 |
Менее 0,06 |
А30 |
0,27–0,35 |
0,7–1,0 |
0,15–0,35 |
0,08–0,15 |
Менее 0,06 |
А40Г |
0,37–0,45 |
1,20–1,55 |
0,15–0,35 |
0,18–0,30 |
Менее 0,06 |
Стали маркируют буквой А (автоматная), после которой следует цифра, указывающая среднее содержание углерода в сотых долях процента; при повышенном содержании в стали марганца в конце марки добавляется буква Г, например А40Г. Сталь А12 используют для изготовления на быстроходных автоматах винтов, болтов, гаек и различных мелких деталей сложной конфигурации. Стали А20, АЗО, А40Г применяют для изготовления на автоматах деталей, работающих в условиях повышенных напряжений.
Для увеличения производительности станков автоматов Волжский автомобильный завод применяет стали с добавкой 0,15–0,3 % Pb (AC11, АС14). Свинец, находящийся в стали в виде мельчайших округлых включений, связанных с сульфидами, действует как разрушитель стружки сильнее, чем MnS. Пленка свинца, образующаяся при резании, уменьшает трение между инструментом и обрабатываемым изделием.
Стали с повышенным содержанием серы и со свинцом обладают большой анизотропией механических свойств, склонны к хрупкому разрушению и имеют пониженный предел выносливости. Они не могут быть рекомендованы для тяжелонагруженных ответственных деталей.
Улучшение обрабатываемости резанием может быть достигнуто и путем легирования стали селеном (~ 0,1 %). Скорость резания повышается в 1,2–1,8 раза, а стойкость инструмента – более чем в 2 раза.
Стали с селеном менее склонны к хрупкому разрушению, однако механические свойства их ниже, чем у обычных конструкционных сталей.
Материаловедение. Учеб. пособие |
-250- |
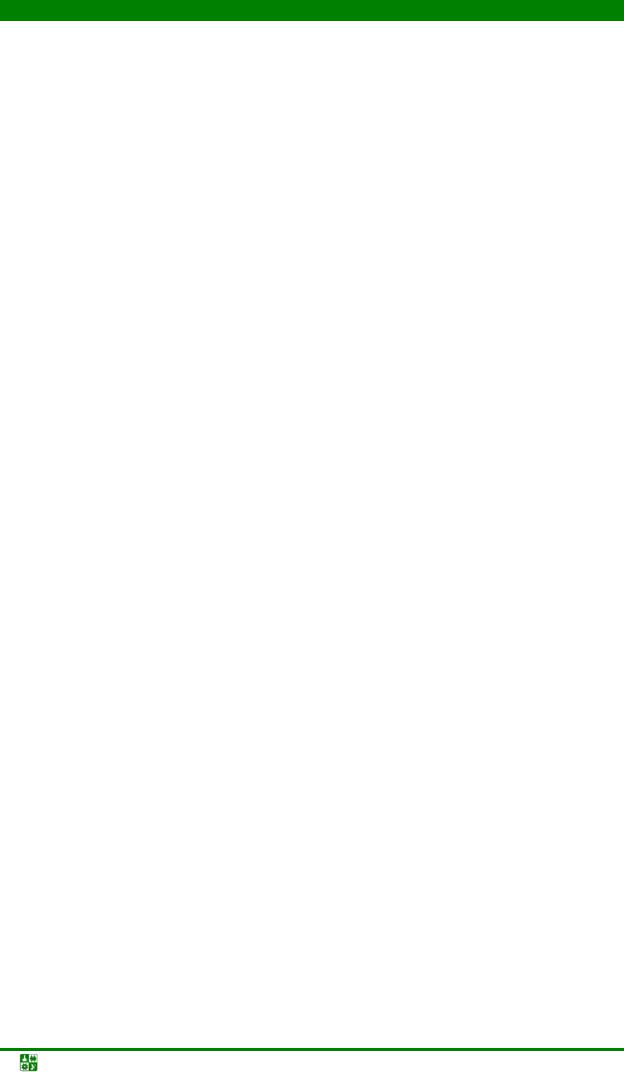
РАЗДЕЛ II. МАТЕРИАЛОВЕДЕНИЕ СТАЛЕЙ И ЧУГУНОВ
Глава 4. Стали, сплавы системы железо–углерод. Маркировка, структура, свойства сплавов
4.9.8. Цементуемыестали
Конструкционные легированные стали общего назначения преимущественно поставляются по ГОСТ 4543-71.
Для цементуемыx изделий применяют низкоуглеродистые (0,1–0,25 % С) стали. После цементации, закалки и низкого отпуска этих сталей цементованный слой должен иметь твердость 58–62 HRC, а сердцевина 20–40 HRC. Сердцевина цементуемых сталей должна иметь высокие механические свойства, особенно повышенный предел текучести, кроме того, она должна быть наследственно мелкозернистой.
Для изделий небольших размеров, работающих на износ и не требующих высокой прочности сердцевины, применяют углеродистые стали марок 10, 15, 20. Легированные стали используют для более сильно нагруженных и особенно крупных изделий, сердцевина которых должна иметь высокий предел текучести, а цементованный слой – высокую твердость и износостойкость.
Хромистые стали. Для изделий несложной формы (втулки, пальцы, валики, некоторые зубчатые колеса), цементуемых на глубину 1,0–1,5 мм, применяют хромистые стали марок 15Х, 15ХА и 20Х, содержащие 0,7–1,0 % Сr. В хромистых сталях в большей степени развивается промежуточное превращение, и при закалке с охлаждением в масле, выполняемой после цементации, сердцевина изделия имеет бейнитное строение. Вследствие этого хромистые стали, по сравнению с углеродистыми, обладают более высокими прочностными свойствами при несколько меньшей пластичности в сердцевинеи лучшей прочностью в цементованном слое. Хромистая сталь чувствительна к перегреву (но меньше, чем углеродистая) и при цементации может получать повышенное содержание углерода в поверхностном слое. Прокаливаемость хромистых сталей невелика. Критический диаметр для 95 % мартенсита при закалке в воде 12–20 мм и при закалке в масле 5–12 мм.
Хромованадиевые стали. Легирование хромистой стали ванадием (0,1–0,2 %) улучшает механические свойства. Кроме того, хромованадиевые стали менее склонны к перегреву. Из-за малой прокаливаемости их используют только для сравнительно небольших изделий (поршневые пальцы, распределительные валики и т.д.).
Хромоникелевые стали. Для деталей ответственного назначения, испытывающих в эксплуатации значительные динамические нагрузки, применяют хромоникелевые и более сложнолегированные стали. Одновременное легирование хромом и никелем повышает прочность, пластичность и вязкость сердцевины. Никель, кроме того, повышает прочность и вязкость цементованного слоя. Хромоникелевые стали малочувствительны к перегреву при длительной цементации и не склонны к пересыщению поверхностных слоев углеродом. Большая устойчивость переохлажденного аустенита в области перлитного и промежуточного превращений обеспечивает высокую прокаливаемость хромоникелевой стали. Критический диаметр при закалке в
Материаловедение. Учеб. пособие |
-251- |
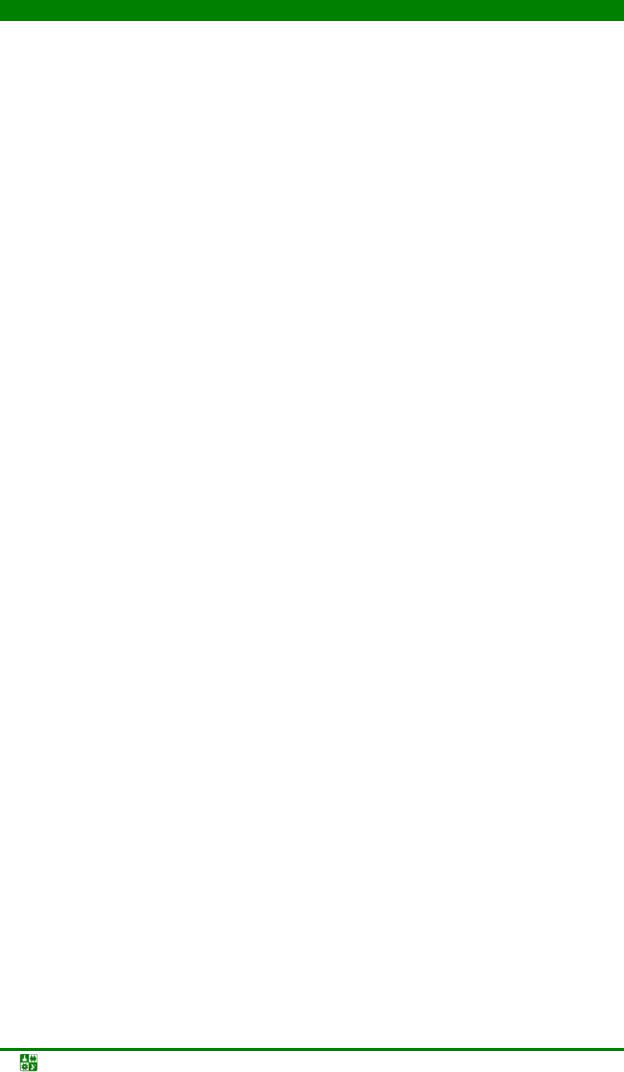
РАЗДЕЛ II. МАТЕРИАЛОВЕДЕНИЕ СТАЛЕЙ И ЧУГУНОВ
Глава 4. Стали, сплавы системы железо–углерод. Маркировка, структура, свойства сплавов
масле (для 95 % мартенсита) 25–70 мм. Это же позволяет закалить крупные детали с охлаждением в масле, а в некоторых случаях и на воздухе.
Легирование хромоникелевых сталей вольфрамом (или молибденом) дополнительно повышает устойчивость переохлажденного аустенита, а следовательно, и прокаливаемость. Сталь 18Х2Н4ВА или соответствующую ей сталь с молибденом 18Х2Н4МА применяют для крупных тяжелонагруженных деталей, например зубчатых колёс, коленчатых валов, осей и т.д. Вследствие высокой устойчивости переохлажденного аустенита детали сечением до 150–200 мм из стали 18Х2Н4ВА (18Х2Н4МА) закаливаются при охлаждении на воздухе, что еще больше уменьшает коробление. Критический диаметр прокаливаемости 100 мм, а порог хладноломкости – 80 °С.
Стали 12ХНЗ, 20ХНЗ, 20Х2Н4, 12Х2Н4, 18Х2Н4ВА и др. при закалке в масле приобретают в сердцевине структуру нижнего бейнита или низкоуглеродистого мартенсита, что приводит к значительному упрочнению стали. В результате цементации повышается устойчивость переохлажденного аустенита в поверхностном слое, особенно в зоне промежуточного превращения.
Поэтому при закалке в масле на поверхности образуется высокоуглеродистый мартенсит, обладающий твердостью 58–63 HRC. Однако следует иметь в виду, что при насыщении стали углеродом понижается температура мартенситного превращения в поверхностном слое и возрастает количество остаточного аустенита, особенно в сталях 18Х2Н4ВА и 20Х2Н4. При несоблюдении установленного режима обработки повышенное количество остаточного аустенита в цементованном слое может быть и в менее легированной стали 12ХНЗА. Количество остаточного аустенита в цементованном слое увеличивается с повышением температуры закалки и концентрации углерода. Остаточный аустенит понижает твердость, сопротивление износу, предел прочности при изгибе и предел выносливости. Снижение количества остаточного аустенита достигается обработкой холодом (от –100 до –120 °С) после закалки или применением промежуточного высокого отпуска (600– 640 °С) с последующей закалкой при возможно более низкой температуре. При высоком отпуске из аустенита выделяются легированные карбиды. При последующем нагреве под закалку значительная часть карбидов остается вне твердого раствора, а менее легированный аустенит при охлаждении превращается в мартенсит, и поэтому количество остаточного аустенита уменьшается, а твердость повышается. Сталь после такого высокого отпуска характеризуется меньшей прокаливаемостью при последующей закалке. При обработке холодом уменьшается количество остаточного аустенита и повышается твердость, однако происходит некоторое снижение предела выносливости и вязкости по сравнению с высоким отпуском.
Для изготовления ответственных зубчатых колес, валов и других деталей, в том числе работающих в условиях Севера, предложены экономнолегированные стали 18ХНМФА (18ХН1МФА) следующего химического со-
става: 0,16–0,21 % С; 0,8–1,2 % Cr; 0,6–0,9 % Ni (1,2–1,6 % Ni); 0,45–0,65 % Мо и 0,08–0,14 % V. Стали имеют повышенную прочность, прокаливаемость и сопротивление хрупкому разрушению.
Материаловедение. Учеб. пособие |
-252- |
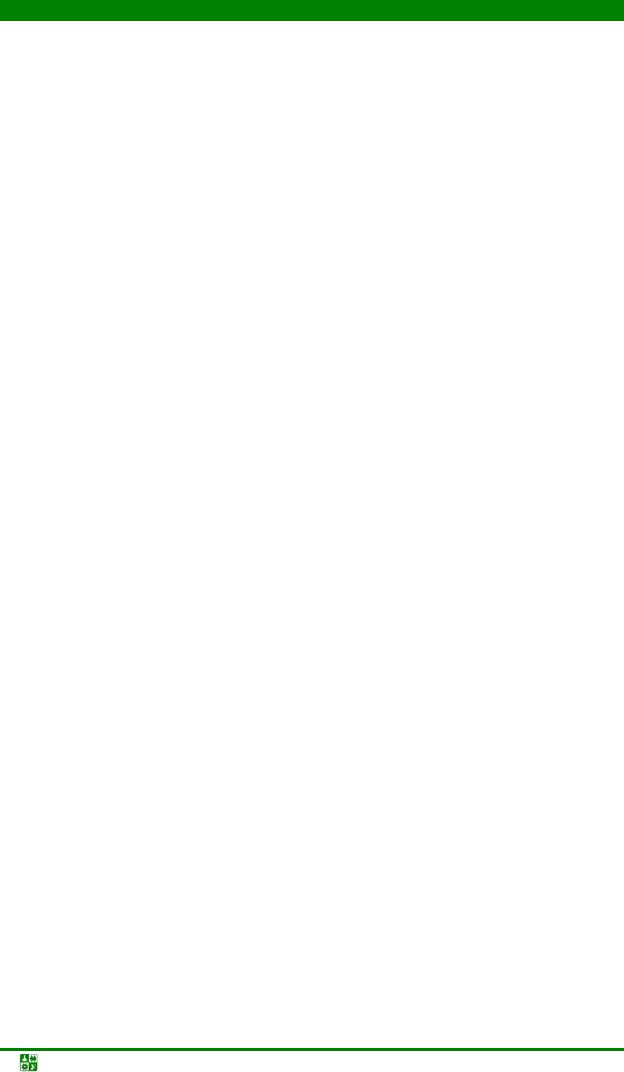
РАЗДЕЛ II. МАТЕРИАЛОВЕДЕНИЕ СТАЛЕЙ И ЧУГУНОВ
Глава 4. Стали, сплавы системы железо–углерод. Маркировка, структура, свойства сплавов
Хромомарганцевые стали применяют во многих случаях вместо более дорогих хромоникелевых сталей для зубчатых колес, валов и других деталей. Эти стали менее устойчивы против перегрева и имеют меньшую вязкость по сравнению с хромоникелевыми. Введение небольших количеств титана (0,03–0,09 %) уменьшает склонность хромомарганцевых сталей к перегреву. В связи с этим более широкое применение получила хромомарганцевая сталь
ститаном марки 18ХГТ. Сталь 18ХГТ цементуют при 910–930 °С, закаливают с 870 °С с охлаждением в масле и подвергают отпуску при 180–200 °С. Сталь 18ХГТ сохраняет мало остаточного аустенита и получает после закалки высокую твердость в цементованном слое (58–61 HRС).
Кнедостатку можно отнести сравнительно небольшую устойчивость переохлажденного аустенита в стали 18ХГТ, а следовательно, и прокаливаемость. Ее критический диаметр для 95 % мартенсита при закалке в воде составляет 25–40 и при закалке в масле 10–25 мм. Сталь 18ХГТ используют для зубчатых колес автомобилей (коробка передач). Порог хладноломкости для полностью вязкого излома +20 °С. Для изготовления зубчатых колес и валов коробки передач грузовых автомобилей применяют стали 25ХГТ и 25ХГМ
(0,23–0,29 % С; 0,9–1,2 % Мn; 0,9–1,2 % Сr; 0,15–0,25 % Мо), упрочняемые цементацией или нитроцементацией. Стали подвергают непосредственной закалке с цементационного нагрева. Для деталей с максимальной твердостью более 60 HRC (зубчатые колеса модуля 3–4 мм) рекомендуется сталь 25ХГМ
сразмером зерна № 5–8.
Молибден повышает прокаливаемость цементованного слоя и обеспечивает максимальную твердость на поверхности.
Повышение прокаливаемости и прочности хромомарганцевых сталей достигается также дополнительным легированием их никелем. Такие менее легированные хромомарганцевоникелевые стали, например 18ХГН и 15ХГН2Т, приближаются по своим механическим и технологическим свойствам к хромоникелевым сталям.
Стали, легированные бором. Для цементации используют также стали, содержащие бор (в количестве 0,001–0,005 %). Бор повышает устойчивость переохлажденного аустенита в области перлитного превращения и поэтому увеличивает прокаливаемость стали.
Повышение устойчивости аустенита связано с тем, что бор, присутствуя преимущественно по границам зерен, тормозит образование зародышей перлита. Однако при повышенном содержании бора образуются бориды железа, уменьшающие устойчивость аустенита.
Бор повышает прокаливаемость лишь доэвтектоидных сталей, содержащих 0,5–0,6 % С, но не улучшает пракаливаемость цементованного слоя.
Легирование бором повышает прочностные свойства после закалки и низкого отпуска, не изменяя или несколько снижая вязкость и пластичность. Бор делает сталь чувствительной к перегреву. Поэтому такая сталь, как правило, должна быть наследственно мелкозернистой (зерно № 7–10). Легирование бористой стали титаном (цирконием) повышает ее устойчивость против перегрева. В промышленности для деталей небольших сечений, работающих
Материаловедение. Учеб. пособие |
-253- |
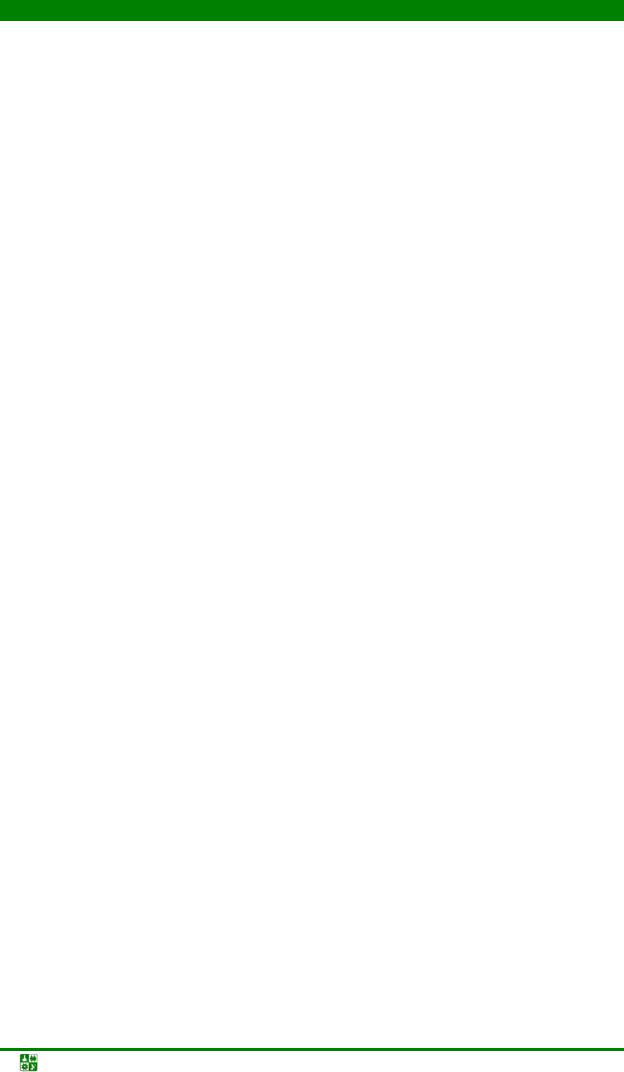
РАЗДЕЛ II. МАТЕРИАЛОВЕДЕНИЕ СТАЛЕЙ И ЧУГУНОВ
Глава 4. Стали, сплавы системы железо–углерод. Маркировка, структура, свойства сплавов
в условиях износа при трении (втулки, пальцы, толкатели и т.д.), применяют сталь 15ХР состава: 0,12–0,17 % С; 0,7–1,0 % Сr 0,002–0,005 % В, а для на-
груженных шестерен сталь 20ХГР, содержащую 0,18–0,24 % С; 0,7–1,0 %
Мn; 0,8–1,1 % Сr; 0,002–0,005 % В.
Дополнительное легирование стали 20ХГР никелем в количестве 0,8–1,1 % (20ХГНР) повышает прокаливаемость, пластичность и вязкость, поэтому сталь 20ХГНР применяют для некоторых деталей вместо хромоникелевых сталей типа 12ХНЗА.
4.9.9. Улучшаемыестали
Улучшаемыми называют такие стали, которые используются после закалки с высоким отпуском (улучшения). Эти стали (40Х, 40ХФА, 30ХГСА, 38ХН3МФА и др.) содержат 0,3–0,5 % углерода и 1–6 % легирующих элементов (ГОСТ 4543-71). Стали закаливают с 820–880 °С в масле (крупные детали – в воде), высокий отпуск производят при 500–650 °С с последующим охлаждением в воде, масле или на воздухе (в зависимости от состава стали). Структура стали после улучшения – сорбит. Данные стали применяют для изготовления валов, шатунов, штоков и других деталей, подверженных воздействию циклических или ударных нагрузок. В связи с этим улучшаемые стали должны обладать высоким пределом текучести, пластичностью, вязкостью, малой чувствительностью к надрезу.
Хромистые улучшаемые стали (30Х, 40Х, 50Х) содержат 1 % Cr, 0,65 % Мn и 0,3–0,5 % С. Повышенное содержание углерода в них с 0,3 до 0,5 % вызывает увеличение прочности (с 900 до 1080 МПа), но приводит к снижению пластичности (с 12 до 9 %) и вязкости разрушения (с 0,7 до 0,4 МДж/м2). Стали обладают небольшой прокаливаемостью, увеличение которой достигается микролегированием (0,001–0,005 %) их бором (35ХР. 40ХР), однако при этом повышается порог хладноломкости. Введение в сталь 0,15 % V (40ХФА) способствует увеличению ее вязкости с 0,6 (у стали 40Х) до 0,9 МДж/м2 (у стали 40ХФА). Стали склонны к отпускной хрупкости.
Хромокремниймарганцевые стали типа 35ХГСА, называемые хромансилами, содержат по 1 % хрома, марганца и кремния и характеризуются хорошими механическими и технологическими (свариваются, штампуются) свойствами. Среди их недостатков можно отметить чувствительность к концентраторам напряжений, к коррозии под напряжением и водородному охрупчиванию, а также склонность к обратимой отпускной хрупкости. Эти стали широко применяют в автомобилестроении и авиации для изготовления силовых сварных конструкций валов, деталей рулевого управления и т.д.
Хромоникелевые стали (40ХН, 45ХН, 30ХН3А и др.) содержат 0,5–0,8 % Сr и 1–3 % Ni. Они отличаются хорошей прокаливаемостью, проч-
ностью и вязкостью (σв = 1 000 МПа; σ0,2 = 800 МПа; KCU = 0,7–0,8 МДж/м2). Хромоникелевые стали так же, как хромансил и хромистые, склонны к обра-
Материаловедение. Учеб. пособие |
-254- |
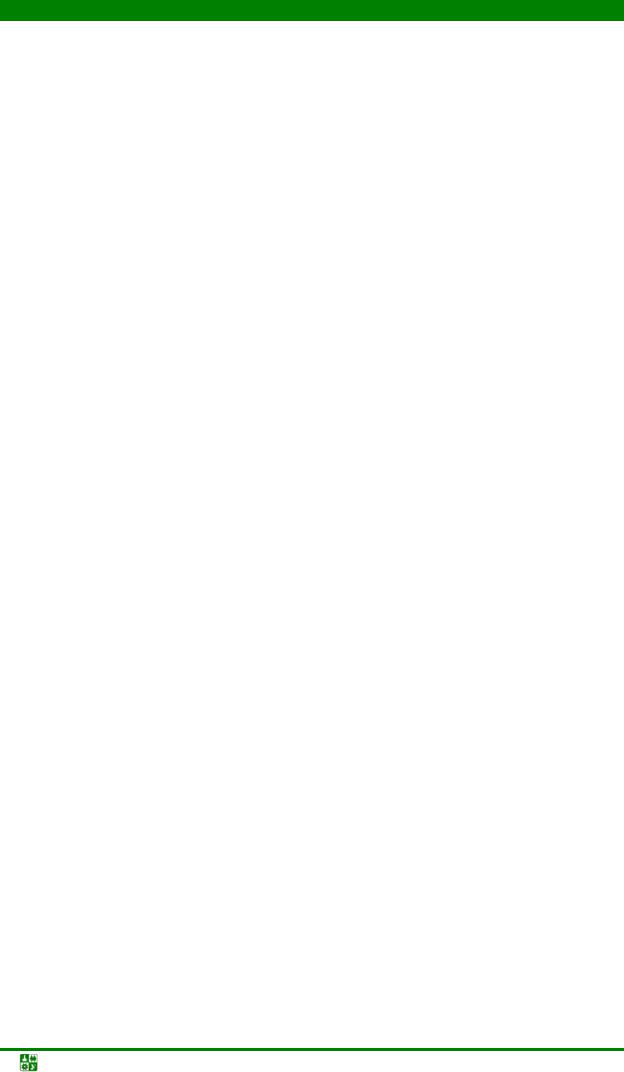
РАЗДЕЛ II. МАТЕРИАЛОВЕДЕНИЕ СТАЛЕЙ И ЧУГУНОВ
Глава 4. Стали, сплавы системы железо–углерод. Маркировка, структура, свойства сплавов
тимой отпускной хрупкости и должны охлаждаться после высокого отпуска с большой скоростью.
Присутствие же 0,2–0,5 % молибдена (или 0,5–0,8 % вольфрама) в стали затормаживает диффузионные процессы, уменьшает разницу в диффузионной подвижности атомов в объеме и по границам зерна и тем самым существенно препятствует возникновению неоднородности. Ванадий (0,15 %) способствует измельчению зерна. Поэтому хромоникелевые стали, легированные молибденом (вольфрамом) и ванадием, 36Х2Н2МФА, 38ХНЗМА, 38ХНЗВА, 38ХНЗМФА и др., обладают лучшими свойствами (σв = 1100–
1200 МПа; σ0,2 = 950–1 100 МПа; δ = 12 %, ψ = 50 %; KCU = 0,8 МДж/м2).
Повышение в них содержания никеля до 3–4 % еще более улучшает прокаливаемость и снижает порог хладноломкости с –40 до –60 °С.
Стали относятся к мартенситному классу, слабо разупрочняются при нагреве до 300–400 °С. Из них изготавливают валы и роторы турбин, тяжелонагруженные детали редукторов и компрессоров.
4.9.10. Рессорно-пружинныестали
Рессорно-пружинные легированные стали имеют высокий модуль упругости, ограничивающий упругую деформацию. В связи с этим они применяются для изготовления жестких (силовых) упругих элементов. Недорогие и достаточно технологичные рессорно-пружинные стали широко используют в авто- и тракторостроении, железнодорожном транспорте.
Кроме того, они находят применение и для силовых упругих элементов приборов. Часто эти материалы называют пружинными сталями общего назначения.
Для обеспечения работоспособности упругих элементов рессорнопружинные стали должны иметь высокие пределы упругости, выносливости, релаксационную стойкость. Этим требованиям удовлетворяют стали с повышенным содержанием углерода (0,5–0,7 %), которые подвергают закалке и отпуску при температуре 420–520 °С.
Закаленная на мартенсит сталь имеет невысокий предел упругости. Он заметно повышается при отпуске, когда образуется структура троостита. В этой структуре феррит из-за сильного фазового наклепа имеет высокую плотность малоподвижных дислокаций, которые, кроме того, эффективно блокируются дисперсными карбидными частицами. Поэтому троостит отличается стабильной дислокационной структурой.
Кроме высоких упругих свойств отпуск на троостит обеспечивает некоторое повышение пластичности и вязкости (особенно в сталях, не склонных к отпускной хрупкости), что важно для снижения чувствительности к концентраторам напряжений и увеличения предела выносливости.
Хорошие результаты дает также изотермическая закалка на структуру нижнего бейнита. Она позволяет получить высокие механические свойства при малой деформации изделий.
Материаловедение. Учеб. пособие |
-255- |
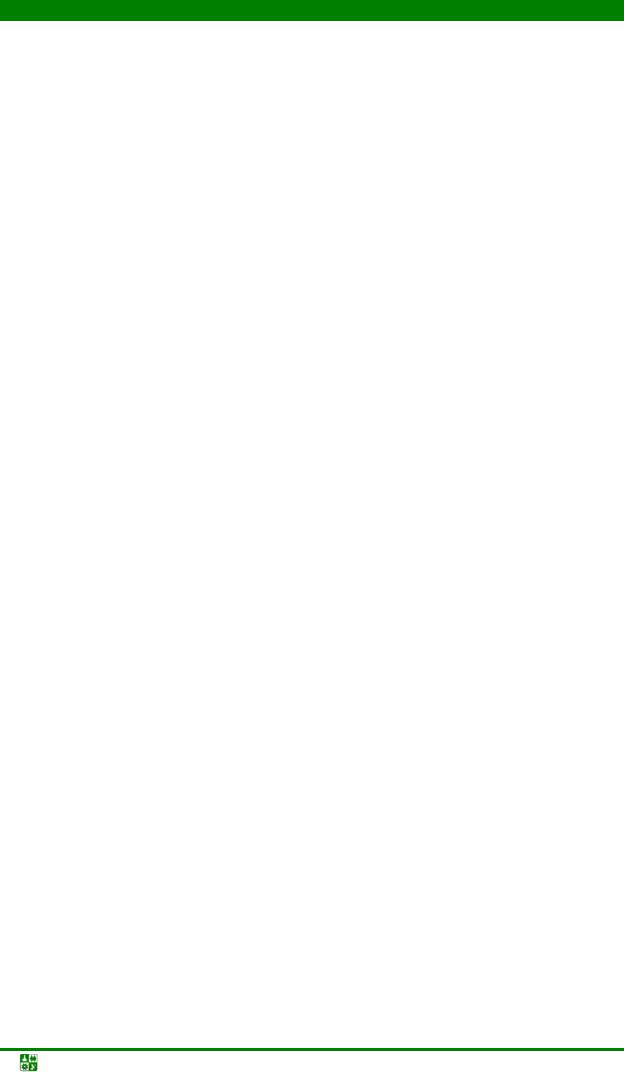
РАЗДЕЛ II. МАТЕРИАЛОВЕДЕНИЕ СТАЛЕЙ И ЧУГУНОВ
Глава 4. Стали, сплавы системы железо–углерод. Маркировка, структура, свойства сплавов
Небольшие пружины простой формы изготовляют из стали, поставляемой в термически обработанном состоянии. Для крупных пружин, требующих больших усилий при навивке, сталь используют в отожженном состоянии. Термической обработке подвергают готовые изделия, полученные горячей навивкой или штамповкой.
Сталь для рессор поставляют в виде полосы. Нарезанные из нее заготовки закаливают в специальных штампах с определенной стрелой прогиба, затем отпускают и собирают в виде пакета.
Углеродистые стали (65, 70, 75, 80, 85, 60Г, 65Г, 70Г по ГОСТ 1050-87),
характеризуются невысокой релаксационной стойкостью, особенно при нагреве. Они не пригодны для работы при температуре выше 100 °С. Из-за низкой прокаливаемости из них изготовляют пружины небольшого сечения.
Легированные рессорно-пружинные стали относятся к перлитному классу. Основными легирующими элементами в них являются кремний (1–3 %), марганец (~ 1 %), а в сталях более ответственного назначения – хром (~ 1 %), ванадий (~ 0,15 %) и никель (1,7 %). Легирование (за исключением кремния и марганца) мало влияет на предел упругости – главное свойство этих сталей. Более существенно оно проявляется в повышении прокаливаемости, релаксационной стойкости, предела выносливости. В связи с этим легированные стали предназначены для больших по размеру упругих элементов и обеспечивают их более длительную и надежную работу.
Дешевые кремнистые стали 55С2, 60С2, 70СЗА применяют для пружин и рессор толщиной до 18 мм. Стали стойки к росту зерна при нагреве под закалку, но склонны к обезуглероживанию – опасному поверхностному дефекту, снижающему предел выносливости. В кремнемарганцевой стали 60СГА этот недостаток выражен менее сильно. Ее преимущественно применяют для рессор толщиной до 14 мм.
Стали 50ХФА, 50ХГФА, которые, в отличие от кремнистых и кремнемарганцевой сталей, подвергают более высокому нагреву при отпуске (520 °С), обладают теплостойкостью, повышенной вязкостью, меньшей чувствительностью к надрезу. Они предназначены для рессор легковых автомобилей, клапанных и других пружин ответственного назначения, которые могут работать при температурах до 300 °С.
Стали 60С2ХА и 60С2Н2А прокаливаются в сечениях, соответственно, до 50 и 80 мм и применяются для крупных тяжелонагруженных и особо ответственных пружин и рессор. Механические свойства сталей определяются содержанием углерода и температурой отпуска. Отпуск проводят при температуре несколько более высокой, чем та, которая отвечает максимальному пределу упругости, что необходимо для повышения пластичности и вязкости.
Наиболее высокие механические свойства имеют стали 70СЗА, 60С2ХА и 60С2Н2А. Предел упругости составляет 880–1 150 МПа, а твердость 38–48 HRC. При такой прочности и твердости стали чувствительны к концентраторам напряжений, поэтому на сопротивление усталости большое влияние оказывает состояние поверхности. При отсутствии поверхностных дефектов (обезуглероживания, окалины, грубых рисок и др.) предел вынос-
Материаловедение. Учеб. пособие |
-256- |
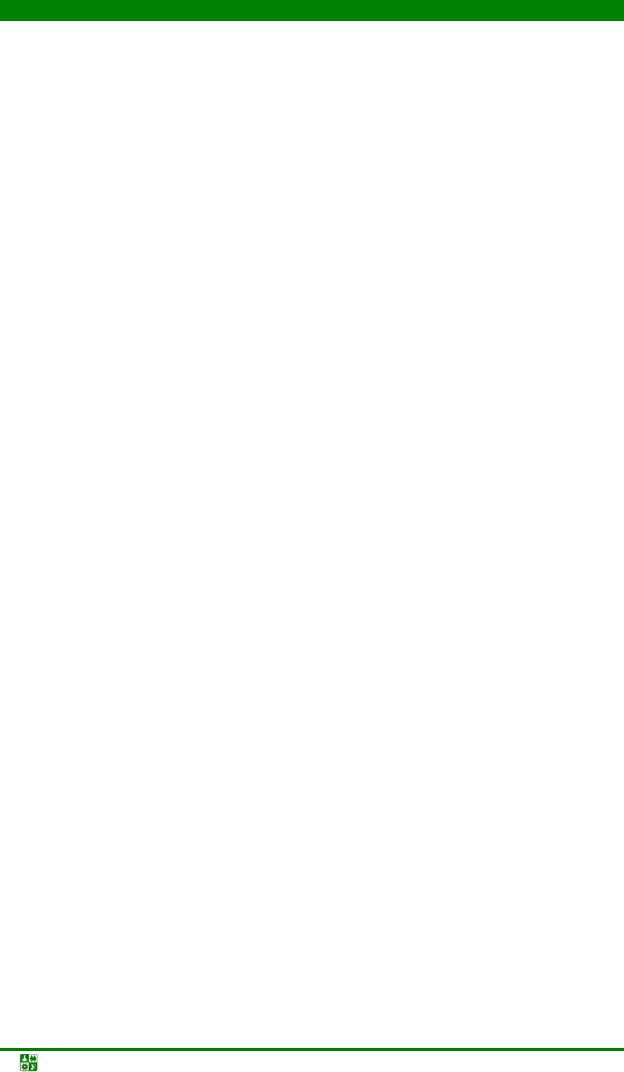
РАЗДЕЛ II. МАТЕРИАЛОВЕДЕНИЕ СТАЛЕЙ И ЧУГУНОВ
Глава 4. Стали, сплавы системы железо–углерод. Маркировка, структура, свойства сплавов
ливости сталей при изгибе не ниже 500 МПа. Для уменьшения чувствительности к концентраторам напряжений готовые пружины и листы рессор подвергают поверхностному наклепу обдувкой дробью. После упрочнения дробью предел выносливости увеличивается в 1,5–2 раза.
4.9.11. Износостойкиеконструкционныестали
Характеристики износа и виды изнашивания. Износостойкость –
свойство материала оказывать в определенных условиях трения сопротивление изнашиванию. Изнашивание – процесс постепенного разрушения поверхностных слоев материала путем отделения его частиц под влиянием сил трения. Результат изнашивания называют износом. Его определяют по изменению размеров (линейный износ), уменьшению объема или массы (объемный или массовый износ).
Существует три периода износа:
I – начальный, или период приработки, когда изнашивание протекает с постоянно замедляющейся скоростью;
II – период установившегося (нормального) износа, для которого характерна небольшая и постоянная скорость изнашивания;
III – период катастрофического износа.
Обеспечение износостойкости связано с предупреждением катастрофического износа, уменьшением скорости начального и установившегося изнашивания. Износостойкость материала при заданных условиях трения, как правило, определяют экспериментальным путем.
Работоспособность материалов в условиях трения зависит от трех параметров: внутренних, определяемых свойствами материалов; внешних, характеризующих вид трения (скольжение, качение) и режим работы (скорость относительного перемещения, нагрузка, характер ее приложения, температу-
ра); от рабочей среды и смазочного материала.
Совокупность этих факторов обусловливает различные виды изнаши-
вания (ГОСТ 23.002-78):
•абразивное, адгезионное, гидро- и газоабразивное, эрозионное, гидро- и газоэрозионное, кавитационное, усталостное, фреттинг-процесс при механическом способе воздействия;
•окислительное, фреттинг-коррозия при коррозионно-механическом воздействии.
Детали, подвергающиеся изнашиванию, подразделяют на две группы: детали, образующие пары трения (подшипники скольжения и качения, зубчатые передачи и т.п.), и детали, изнашивание, которых вызывает рабочая среда (жидкость, газ и т.п.).
Характерные виды изнашивания деталей первой группы – абразивное (твердыми частицами, попадающими в зону контакта), адгезионное, окисли-
тельное, усталостное, фреттинг-процесс (фреттинг-коррозия). Для деталей второй группы типично абразивное изнашивание (наприме, истирание поч-
Материаловедение. Учеб. пособие |
-257- |
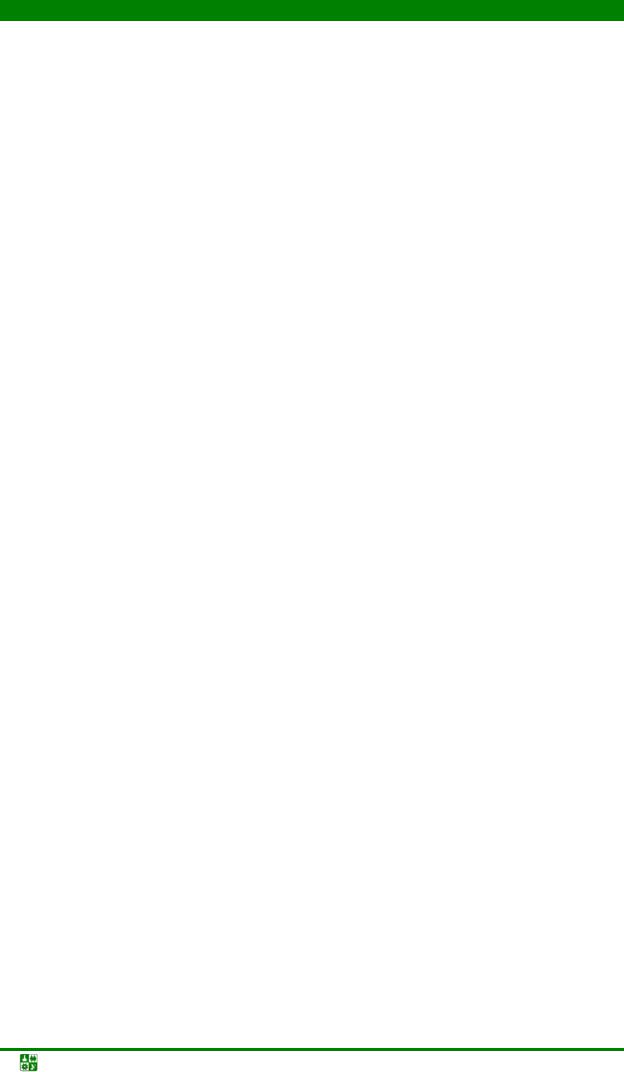
РАЗДЕЛ II. МАТЕРИАЛОВЕДЕНИЕ СТАЛЕЙ И ЧУГУНОВ
Глава 4. Стали, сплавы системы железо–углерод. Маркировка, структура, свойства сплавов
вой), гидро- и газоабразивное (твердыми частицами, перемешиваемыми жидкостью или газом), эрозионное, гидро- и газоэрозионное (потоком жидкостью или газа), кавитационное (от гидравлических ударов жидкости).
Материалы, устойчивые к абразивному изнашиванию. Износостой-
кость при абразивном изнашивании чистых металлов пропорциональна их твердости. В сплавах эта зависимость может не соблюдаться.
При абразивном изнашивании ведущими являются процессы многократного деформирования поверхности скользящими по ней частицами и микрорезание. Степень развития этих процессов зависит от давления и соотношения твердости материала и абразивных частиц. Т.к. твердость последних велика, то наибольшей износостойкостью обладают материалы, структура которых состоит из частиц твердой карбидной фазы и удерживающей их высокопрочной матрицы.
Карбидные сплавы применяют при наиболее тяжелых условиях работы в виде литых и наплавочных материалов, которых в промышленности более ста наименований. Они представляют собой сплавы с высоким содержанием углерода (до 4 %) и карбидообразующих элементов (хром, вольфрам, титан). В их структуре может быть до 50 % специальных карбидов. Структура матричной фазы регулируется введением марганца или никеля. Она может быть мартенситной, аустенитно-мартенситной и аустенитной.
Для деталей, работающих без ударных нагрузок, применяют сплавы с мартенситной структурой: 250Х38, 320Х23Г2С2Т; при значительных ударных нагрузках (зубья ковшей экскаваторов, пики отбойных молотков): сплавы 370Х7Г7С, 110Г13, 300Г34; при средних условиях изнашивания применяют твердые сплавы, структура которых состоит из специальных карбидов (WC, TiC, TaC), связанных кобальтом, а также высокоуглеродистые стали типа Х12, Х12М, Р18, Р6М5. Эти материалы относятся к инструментальным.
Основные методы защиты от этого вида изнашивания – повышение твердости контактирующих поверхностей (цементацией, азотированием), применение смазочных материалов, лаков, пленочных покрытий из полимеров, затрудняющих металлический контакт поверхностей трения и доступ к нему кислорода.
Материалы, устойчивые к усталостному изнашиванию. Эти мате-
риалы предназначены для таких изделий массового производства, как подшипники качения и зубчатые колеса. Усталостное выкрашивание на их рабочих поверхностях вызывает циклические контактные напряжения сжатия. Они создают в поверхностном слое мягкое напряженное состояние, которое облегчает пластическое деформирование поверхностного слоя деталей и, как следствие, развитие в нем процессов усталости. В связи с этим высокая контактная выносливость может быть обеспечена лишь при высокой твердости поверхности, необходимой также для затруднения истирания контактных поверхностей при их проскальзывании.
Материалы, устойчивые к изнашиванию в условиях больших давле-
ний и ударных нагрузок. Трение при высоком давлении и ударном нагруже-
Материаловедение. Учеб. пособие |
-258- |
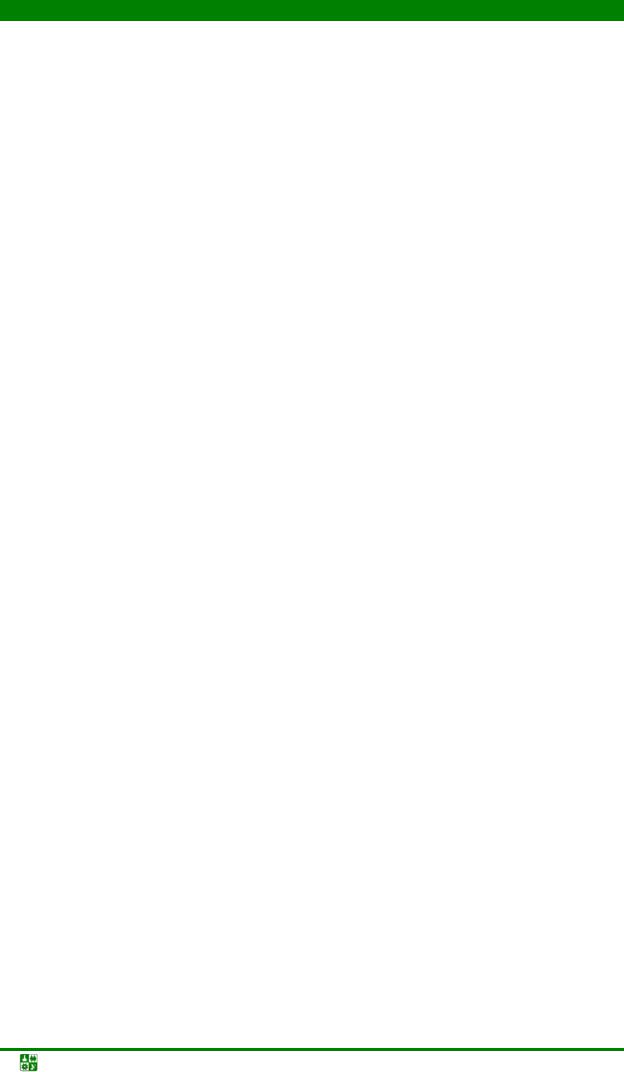
РАЗДЕЛ II. МАТЕРИАЛОВЕДЕНИЕ СТАЛЕЙ И ЧУГУНОВ
Глава 4. Стали, сплавы системы железо–углерод. Маркировка, структура, свойства сплавов
нии характерно для работы тракторов гусеничных машин, крестовин железнодорожных рельсов, ковшей экскаваторов и других деталей.
Износостойкость деталей обычно обеспечивается повышенной твердостью поверхности. Особое место занимает высокомарганцевая сталь для литья, аустенитного класса, с высокой стойкостью к ударно-абразивному изно-
су 110Г13Л – сталь Гадфильда (1,25 % С, 13 % Мn, 1 % Сr, 1 % Ni).Сталь по-
ставляется по ГОСТ 977-88. При низкой начальной твердости (180–220 НВ) она успешно работает на износ в условиях абразивного трения, сопровождаемого воздействием высокого давления и больших динамических (ударных) нагрузок (такие условия работы характерны для траков гусеничных машин, щек дробилок и др.). Это объясняется повышенной способностью стали упрочняться в процессе холодной пластической деформации. Так, при пластической деформации, равной 70 %, твердость стали возрастает с 210 до 530 НВ. Высокая износостойкость стали достигается не только деформационным упрочнением аустенита, но и образованием мартенсита с гексагональной (ε) или ромбоэдрической (ε') решеткой. При содержании фосфора более 0,025 % сталь становится хладноломкой. Структура литой стали представляет собой аустенит с выделившимися по границам зерен избыточными карбидами марганца (Мn3С), снижающими прочность и вязкость материала. Для получения однофазной аустенитной структуры отливки закаливают в воде с температуры 1 050–1 100 °С, без отпуска. В таком состоянии сталь имеет высокую пластичность δ = 34–53 %, ψ = 34–43 %, низкую твердость 180–220 НВ и невысокую прочность σв = 830–654 МПа.
Фрикционные материалы. Фрикционные материалы применяют в тормозных устройствах и механизмах, передающих крутящий момент. Они работают в тяжелых условиях изнашивания – при высоких давлениях (до 6 МПа), скоростях скольжения (до 40 м/с) и температуре, мгновенно возрастающей до 1 000 °С. Эти материалы должны иметь высокий и стабильный в широком интервале температур коэффициент трения, минимальный износ, высокие теплопроводность и теплостойкость, хорошую прирабатываемость и достаточную прочность. Этим требованиям удовлетворяют многокомпонентные неметаллические и металлические материалы. Их производят в виде пластин или накладок, которые прикрепляют к стальным деталям, например дискам трения.
Из асбофрикционных материалов наибольшей работоспособностью обладает ретинакс (ФК-34А и ФК_16Л), который содержит 25 % фенолформальдегидной смолы, 40 % асбеста, 35 % барита, кусочки латуни и пластификатор. В паре со сталью ретинакс обеспечивает коэффициент трения 0,37–0,40. Его используют в тормозных механизмах самолетов, автомобилей и других машин.
Металлические спеченные материалы применяют при тяжелых режимах трения. Их производят на основе железа (ФМК-8 и ФМК-11) и меди (МК- 5). Кроме основы и металлических компонентов (Sn, Pb, Ni), обеспечивающих прочность, хорошую теплопроводность и износостойкость, эти материалы содержат неметаллические добавки – асбест, графит, оксид кремния, барит.
Материаловедение. Учеб. пособие |
-259- |
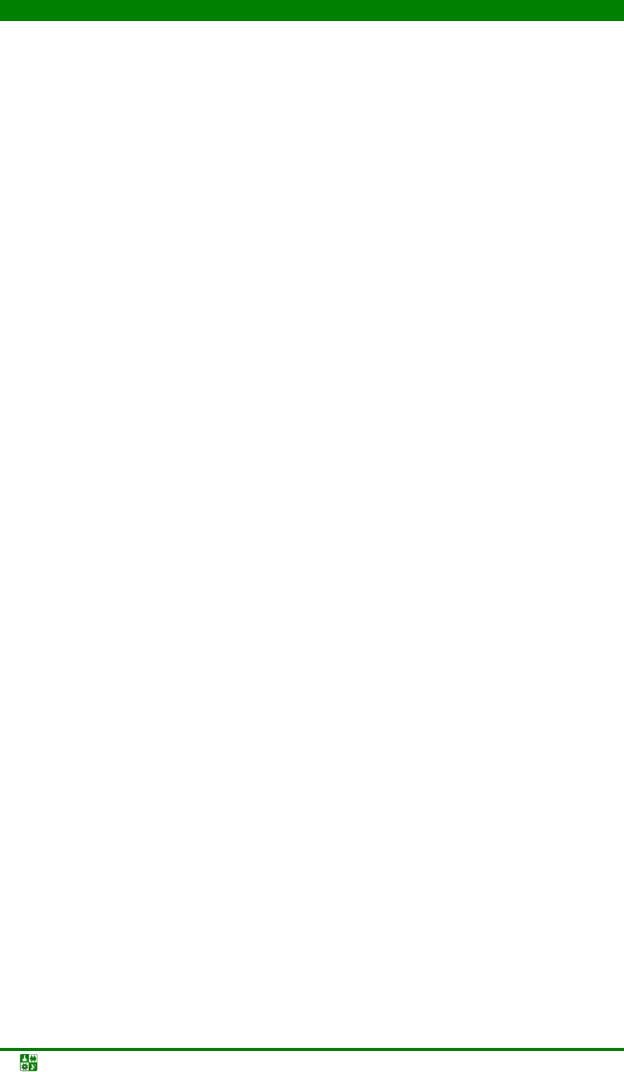
РАЗДЕЛ II. МАТЕРИАЛОВЕДЕНИЕ СТАЛЕЙ И ЧУГУНОВ
Глава 4. Стали, сплавы системы железо–углерод. Маркировка, структура, свойства сплавов
Вмногодисковой тормозной системе самолетов применяют бериллий из-за его высокой теплоемкости, теплопроводности и малой плотности.
Стали для изготовления шарико- и роликоподшипников поставляют по ГОСТ 801-78. Подшипники качения работают в условиях качения шариков (или роликов) по наружному и внутреннему кольцам. Наиболее часто причиной отказа подшипников является излом, разрушение тел качения и рабочих поверхностей колец, а также усталостное выкрашивание рабочих поверхностей элементов подшипников.
Кольца, ролики и шарики работают в условиях, которые требуют от стали высокой твердости, износостойкости и сопротивляемости контактной усталости.
Вкачестве шарикоподшипниковой стали используют высокоуглеродистые (заэвтектоидные) хромистые стали, а для больших сечений – хромомарганцевокремнистую сталь, прокаливающуюся на большую глубину.
К сталям этого класса предъявляют высокие требования по содержанию неметаллических включений, т.к., попадая в поверхностный рабочий слой, они становятся концентраторами напряжений, вызывая преждевременное усталостное разрушение. Недопустима также карбидная неоднородность. Стали после отжига должны иметь однородную структуру мелкозернистого перлита с мелкими включениями вторичных карбидов. Твердость в этом состоянии 187–207 НВ, что обеспечивает достаточно хорошую обрабатываемость резанием. Кольца, шарики и ролики после закалки в масле при 830–860 °С (для стали ШХ15) и 810–850 °С (для стали ШХ15ГС) и низкого отпуска при 150–200 °С должны иметь твердость 61–66 HRC. Для более полного снятия напряжений выдержка при отпуске 2,5–6 ч.
Обозначение марки надо расшифровывать так: шарикоподшипниковая хромистая, цифра показывает примерное содержание хрома в десятых долях. Хром вводят для обеспечения необходимой прокаливаемости. Следовательно, чем меньше диаметр закаливаемой детали подшипника, тем меньше может быть содержание хрома в стали. По своей природе перечисленные стали близки к углеродистым сталям с содержанием углерода около 1 %.
Крупногабаритные кольца и ролики изготовляют из цементуемой хромоникелевой стали 20Х2Н4А. После цементации при 940–970 °С на глубину 5–10 мм указанные детали подшипников подвергают высокому отпуску при 550 °С в течение 8 ч и затем при 630 °С в течение 8 ч для устранения остаточного аустенита. Закалку проводят при 800 °С в масле, а затем низкотемпературный отпуск при 160 °С.
Для подшипников, работающих в агрессивных средах, применяют нержавеющую сталь 95Х18 (0,9–1,0 % С и 17–18,5 % Сr, остальное марганец, кремний, сера, фосфор и т.д. в обычных пределах).
Высокое содержание хрома необходимо для придания стали большего сопротивления коррозии. Сталь обладает высокой коррозионной стойкостью
впресной и морской воде, в растворах азотной и уксусной кислот, в различных органических средах, но имеет плохую стойкость в смеси азотной и серной кислот.
Материаловедение. Учеб. пособие |
-260- |
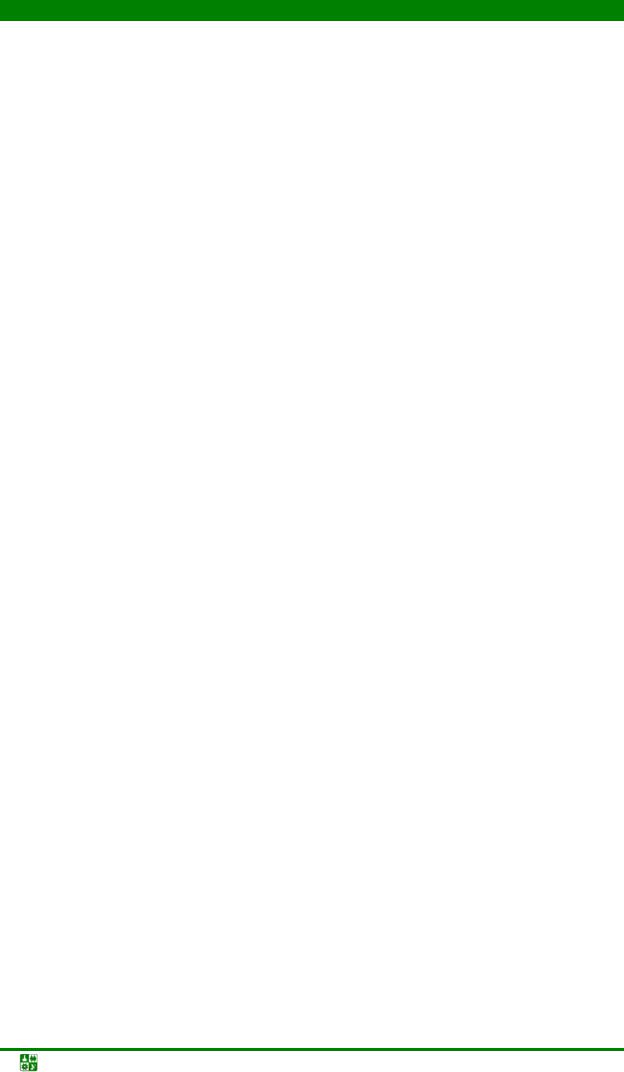
РАЗДЕЛ II. МАТЕРИАЛОВЕДЕНИЕ СТАЛЕЙ И ЧУГУНОВ
Глава 4. Стали, сплавы системы железо–углерод. Маркировка, структура, свойства сплавов
Термическая обработка для придания наивысшей в данной стали твердости и достаточной стабильности в размерах заключается в закалке с 1 050 °С в масле, обработке холодом при минус 70 °С и отпуске при 150–160 °С. Твердость после такой обработки 60–61 HRC.
Подшипники, подвергаемые в процессе эксплуатации значительным нагревам (до 400–500 °С), изготавливают из стали типа быстрорежущих. Обычно применяют сталь Р9, но с пониженным содержанием углерода и ванадия. Снижение углерода необходимо для уменьшения карбидной ликвации, снижающей долговечность подшипника. Обработку такой стали проводят по режимам термической обработки инструментов из быстрорежущих сталей.
4.9.12. Коррозионнаястойкость. Коррозионно-стойкиесталиипокрытия
Коррозией называют разрушение металлов под действием окружающей среды. При этом часто металлы покрываются продуктами коррозии (ржавеют). В результате воздействия внешней среды механические свойства металлов резко ухудшаются иногда даже при отсутствии видимого изменения внешнего вида поверхности.
Различают химическую коррозию, протекающую при воздействии на металл газов (газовая коррозия) и не электролитов (нефть и ее производные), и электрохимическую коррозию, вызываемую действием электролитов: кислот, щелочей и солей. К электрохимической коррозии относятся также атмосферная и почвенная коррозия.
Введение в сталь более 12 % Сr делает ее коррозионно-стойкой в атмосфере и во многих других промышленных средах. Сплавы, содержащие меньше 12 % Сr, практически в столь же большой степени подвержены коррозии, как и железо. Сплавы, содержащие более 12–14 % Cr, ведут себя как благородные металлы: обладая положительным потенциалом, они не ржавеют и не окисляются на воздухе, в воде, ряде кислот, солей и щелочей.
Существует несколько видов электрохимической коррозии. Если металл однороден (например, однородный твердый раствор), то наблюдается равномерная коррозия, протекающая примерно с одинаковой скоростью по всей поверхности металла. В неоднородном металле, что является наиболее частым случаем, коррозия носит локальный характер и охватывает только некоторые участки поверхности. Это местная, или локальная, коррозия, которая в свою очередь делится на точечную, пятнистую и с язвами. Очаги пятнистой и точечной коррозии являются концентраторами напряжений. Наиболее опасна так называемая интеркристаллитная коррозия, распространяющаяся по границам зерен, вследствие более низкого их электрохимического потенциала. Коррозия без заметных внешних признаков быстро развивается по границам зерен, в глубь металла, резко снижая при этом механические свойства. Сталь, пораженная интеркристаллитной коррозией, теряет металлический звук и при изгибе дает надрывы по границам зерен в местах коррозионного разрушения металла. Кроме того, различают коррозию под
Материаловедение. Учеб. пособие |
-261- |
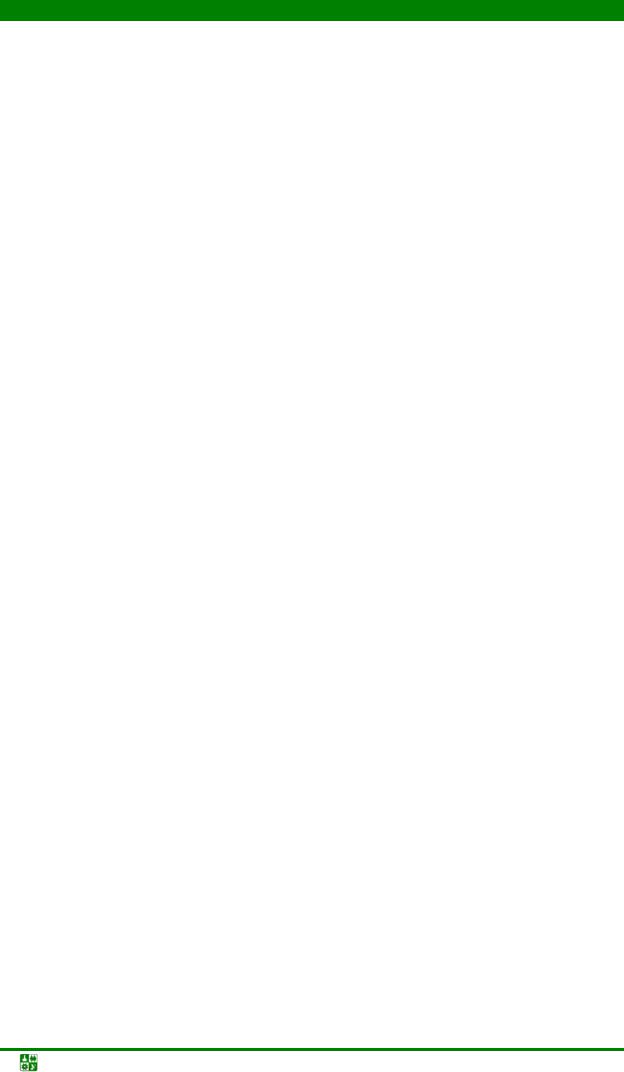
РАЗДЕЛ II. МАТЕРИАЛОВЕДЕНИЕ СТАЛЕЙ И ЧУГУНОВ
Глава 4. Стали, сплавы системы железо–углерод. Маркировка, структура, свойства сплавов
напряжением, которая возникает при одновременном действии коррозионной среды и напряжений растяжения. Разновидностью этой коррозии является коррозионное растрескивание, т.е. образование в металле тонкой сетки трещин, проходящих по объему зерна при воздействии коррозионной среды и напряжений.
Сталь, устойчивую против газовой коррозии при высоких температурах (более 550 °С), называют жаростойкой (окалиностойкой). Стали, устойчивые против электрохимической коррозии, называют коррозионно-стойкими, или нержавеющими. Повышение устойчивости стали против коррозии достигается введением в нее элементов, образующих на поверхности защитные пленки, прочно связанные с основным металлом и предупреждающие контакт между сталью и агрессивной наружной средой, а также повышающих электрохимический потенциал стали в разных агрессивных средах.
Коррозионно-стойкие стали. Такие стали являются высоколегированными и содержат не менее 13 % Cr, что обеспечивает образование на поверхности металла пассивирующей защитной пленки.
Их разделяют на классы в зависимости от структуры, которая образуется после высокотемпературного нагрева и охлаждения на воздухе: мартенситный, мартенситно-ферритный (при содержании феррита не менее 10 %), ферритный, аустенито-ферритный (при содержании феррита не менее 10 %), аустенитный и аустенито-мартенситный (ГОСТ 5632–72).
В настоящее время разработано несколько групп высокоазотистых кор- розионно-стойких сталей с низким содержанием углерода.
Азот – доступный практически в неограниченных количествах легирующий элемент – отличается повышенной аустенитообразующей и упрочняющей особенностью.
Аустенитные стали – это наиболее важный класс коррозионностойких сталей по масштабам использования и универсальности применения.
Преимуществами этих сталей кроме коррозионной стойкости являются высокая пластичность и вязкость. Изделия из них, включая тонкую ленту и фольгу, легко получают всеми способами пластического деформирования. Стали имеют хороший комплекс литейных свойств и свариваемость. Исключением является обработка резанием – стали обрабатываются хуже углеродистых и низколегированных из-за высокой пластичности и упрочнения при резании. Сталь 12Х18Н10Е с добавкой Sе является автоматной.
Аустенитные стали, обычно легированные хромом и никелем (или марганцем), после охлаждения до комнатной температуры имеют аустенитную структуру, низкий предел текучести, умеренную прочность, высокую пластичность и хорошую коррозионную стойкость в окислительных средах. Эти стали парамагнитны.
Представителями аустенитных нержавеющих сталей являются 12Х18Н9, 17Х18Н9, содержащие 17–18 % Cr, 8–10 % Ni. После медленного охлаждения стали имеют структуру, состоящую из аустенита, феррита и карбидов M23C6. Для получения чисто аустенитной структуры, обладающей высокой коррозионной стойкостью стали нагревают выше линии SE чаще
Материаловедение. Учеб. пособие |
-262- |
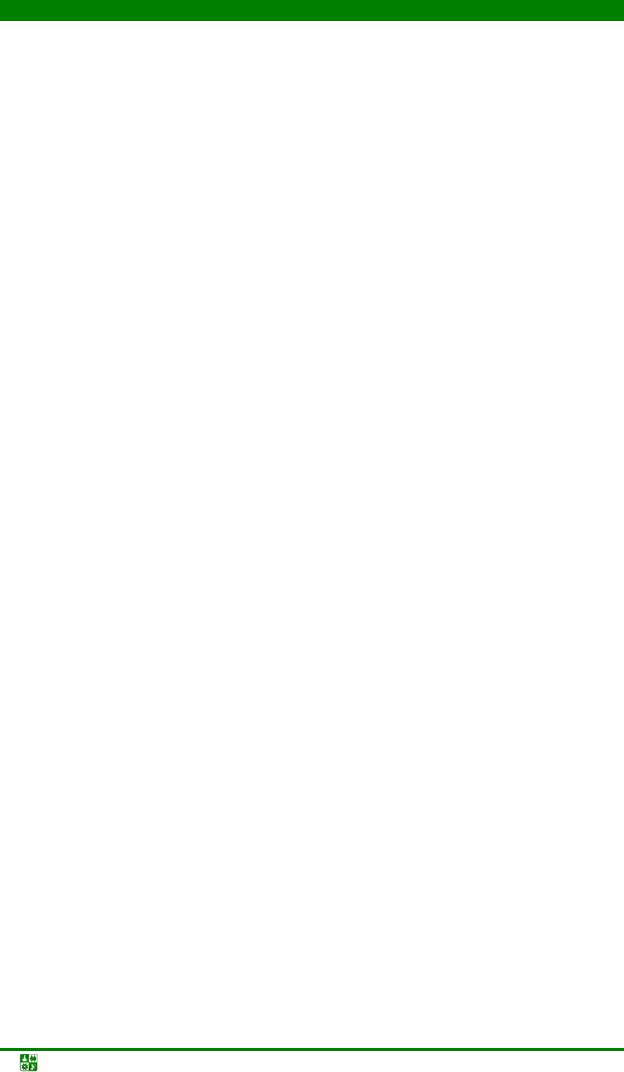
РАЗДЕЛ II. МАТЕРИАЛОВЕДЕНИЕ СТАЛЕЙ И ЧУГУНОВ
Глава 4. Стали, сплавы системы железо–углерод. Маркировка, структура, свойства сплавов
до 1 100–1 150 °С (для растворения карбидов) и закаливают в воде (на воздухе). Сталь 12Х18Н9 обычно применяют в виде холоднокатаного листа или ленты.
В процессе холодной пластической деформации сталь легко наклепывается. Значения временного сопротивления после холодной деформации (60–70 %) могут быть повышены до 1 200–1 300 МПа, при этом относительное удлинение снижается до 4–5 %. Упрочнение в процессе холодной деформации связано с наклепом и протеканием мартенситного превращения. Чем менее стабилен аустенит, тем интенсивнее при холодной деформации происходит превращение аустенита в мартенсит.
Стали хорошо свариваются и штампуются. При нагреве закаленной до 550–750 °С стали, например при сварке, они охрупчиваются и приобретают склонность к межкристаллитной коррозии (МКК). Это связано с тем, что в пограничных зонах выделяются карбиды хрома M23C6 и происходит обеднение этих зон аустенита хромом ниже того предела, т.е. 12 %, который обеспечивает коррозионную стойкость. Межкристаллитная коррозия возникает лишь в тех случаях, когда карбиды М23С6 образуют сплошную или слаборазобщенную сетку по границам зерен. Разрыв сетки в результате коагуляции карбидов снижает склонность стали к межкристаллитной коррозии. Пониженное содержание хрома вокруг аустенитного зерна распространяется на толщину, не превышающую 0,8 мкм. Двухфазная структура и внутренние напряжения, возникающие при образовании карбидов, затрудняющие пассивацию границ зерен, способствуют развитию коррозии. Для уменьшения склонности к интеркристаллитной коррозии в состав стали вводят титан (реже ниобий) в количестве (0,5–0,7) (08Х18Н10Т, 12Х18Н12Т). В этом случае образуется карбид МС (TiC, NbC), связывающий весь углерод, а хром остается в растворе. Для повышения стабильности аустенита количество никеля в этих сталях увеличивают до 10–12 %. Эти стали обладают пониженной технологической пластичностью.
Высокое сопротивление межкристаллитной коррозии, хорошую пластичность и свариваемость имеют низкоуглеродистые аустенитные стали
04Х18Н10 и ОЗХ18Н12Т.
Стали с пониженным содержанием углерода устойчивы в азотной кислоте и используются для изготовления химической аппаратуры.
Хромоникелевые нержавеющие стали дороги. В связи с этим в некоторых случаях применяют более дешевые стали, в которых часть никеля заменена марганцем.
Аустенито-ферритные стали (078Х22Р6Т, 08Х21Н6М5Т, 08Х18Г8Н2Т) имеют оптимальный комплекс свойств при практически равном содержании аустенита и феррита, которое обеспечивается закалкой с 1 000─1 100 °С. Эти стали дешевле аустенитных, т.к. содержат меньше никеля, прочнее из в 1,5–2 раза и имеют почти такое же сопротивление коррозии, как сталь 12Х18Н10Т. Во избежание МКК эти стали стабилизируют титаном. Изделия из этих сталей рекомендуют эксплуатировать при температурах не выше 350 °С во избежания охрупчивания из-за структурных изменений.
Материаловедение. Учеб. пособие |
-263- |
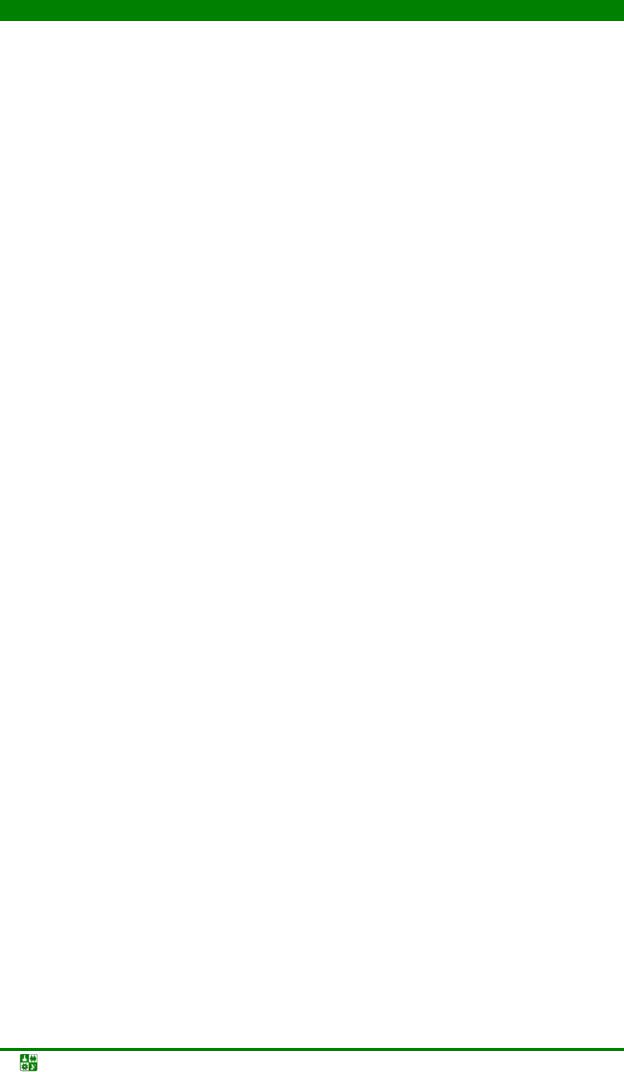
РАЗДЕЛ II. МАТЕРИАЛОВЕДЕНИЕ СТАЛЕЙ И ЧУГУНОВ
Глава 4. Стали, сплавы системы железо–углерод. Маркировка, структура, свойства сплавов
Аустенито-мартенситные стали (07Х16Н6, 09Х15Н9Ю, 08Х17Н5М3)
имеют высокую прочность, которая достигается сложной термической обработкой, включающей закалку для получения аустенита, обработку холодом при –70 °С для превращения аустенита в мартенсит и старения мартенсита при 350–500 °С. Обработка холодом может быть заменена пластическим деформированием, во время которого значительная часть аустенита превращается в мартенсит. Химический состав сталей отличается малым содержанием углерода, пониженным количеством никеля и добавками Al, Ti, Cu, Mo для упрочнения мартенсита при старении. При 70–90 % мартенсита стали имеют σв = 1 100–1 400 МПа. При таком уровне прочности эти стали особенно склонны к коррозионному растрескиванию. Для защиты от этого вида коррозии старение рекомендуется прервать на стадии образования зон Г–П, не допуская максимума прочности.
Ферритные стали 08Х13, 12Х17, 08Х17Т, 15Х25Т, 15Х28 используют чаще без термической обработки для изготовления деталей, работающих в более агрессивных средах (кипящая азотная кислота). Эти стали обладают крупнозернистостью в литом виде и склонны к сильному росту зерна при нагреве до температур более 850 °С (например, при сварке), что сопровождается охрупчиванием стали.
После высокотемпературного нагрева они подвержены МКК. Проверка стойкости против МКК предусмотрена только для сталей 08Х17Т, 15Х25Т. Склонность к охрупчиванию ферритных сталей ограничивает их применение несмотря на меньшую стоимость по сравнению с аустенитными сталями.
Мартенситные стали (20Х13, 30Х13, 40Х13, 20Х17Н, 95Х18) исполь-
зуют для деталей и инструментов, подвергающихся воздействию слабоагрессивных сред: воды, атмосферы, разбавленных расстворов кислот и солей. Структура отожженных сталей представляет собой легированный феррит с частицами карбида хрома. Отожженные стали имеют удовлетворительную стойкость против коррозии, но их прочность невысока. Прочность увеличивается после закалки и отпуска. Закалку проводят с 1 050–1 100 °С для растворения карбидов хрома с последующим низким или высоким отпуском. Максимальное сопротивление коррозии стали имеют после низкого отпуска, пониженное, но тем не менее достаточно высокое, – после высокого отпуска. Шлифование и полирование поверхности дополнительно повышают стойкость изделий.
Сталь 20Х13 применяют для клапанов гидравических насосов, лопаток гидротурбин, арматуры крекинг-установок, предметов домашнего обихода, пищевой промышленности и т.д. Их подвергают закалке в масле с 1 000–1 100 °С и высокому отпуску при 700–775 °С, после которого карбиды присутствуют в виде более крупных частиц. Применение более низкого отпуска, создающего более мелкие карбидные частицы, усиливает коррозию.
Стали 30Х13 и 40Х13 используют для карбюраторных игл, пружин, хирургических инструментов и т.д. Эти стали закаливают с 1 000─1 050 °С в масле и отпускают при 180–200 °С. После такого отпуска они сохраняют
Материаловедение. Учеб. пособие |
-264- |
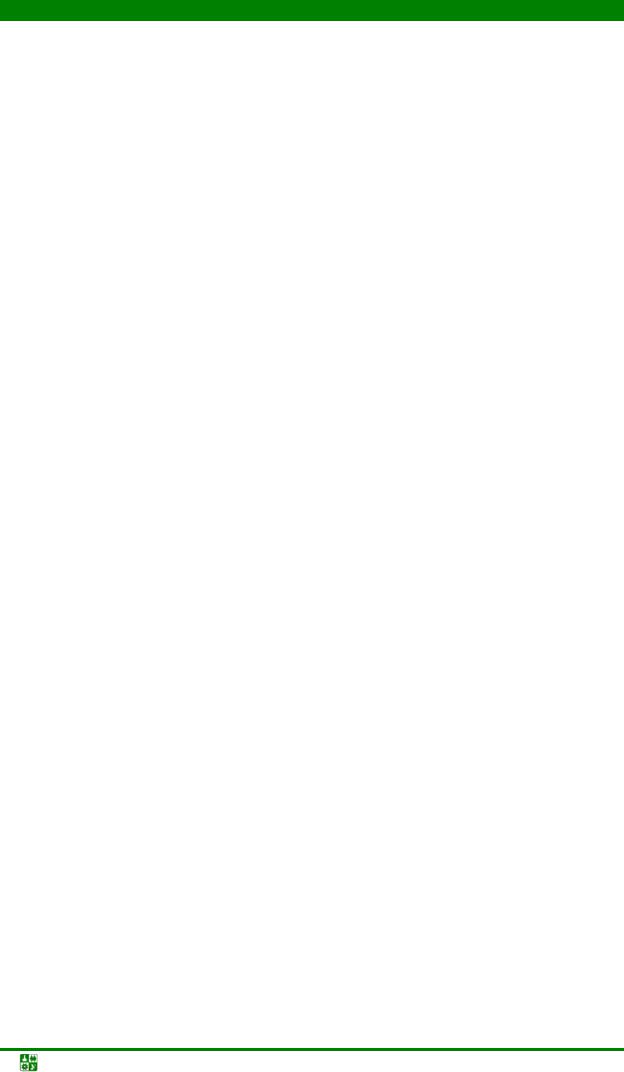
РАЗДЕЛ II. МАТЕРИАЛОВЕДЕНИЕ СТАЛЕЙ И ЧУГУНОВ
Глава 4. Стали, сплавы системы железо–углерод. Маркировка, структура, свойства сплавов
мартенситную структуру, высокую твердость (50–60 HRC) и достаточную устойчивость против коррозии.
Сталь 95Х18 является износостойкой подшипниковой, после закалки и низкого отпуска она характеризуется высокой твердостью (более 59 HRC).
Коррозионно-стойкие покрытия. Металлические и неметаллические коррозионно-стойкие покрытия являются распространенным средством повышения долговечности изделий при работе в коррозионной среде.
Металлические покрытия по механизму своего влияния делят на катодные и анодные.
Катодные покрытия изготовляют из более электроположительного металла; они экранируют анодные участки металла и повышают электродный потенциал поверхности. Вследствие высокой коррозионной стойкости эти покрытия долговечны, но не выносят механических повреждений. Если есть царапины, то основной металл при наличии покрытия второго катода корродирует быстрее, нежели без покрытия.
Покрытие оловом или свинцом (лужение) для железа и низкоуглеродистых сталей является катодным. Луженую сталь применяют в пищевой промышленности, а покрытие свинцом – в химической промышленности.
Анодные покрытия изготавливают из более электроотрицательного материала. Разрушаясь, он предохраняет металл от коррозии.
Неметаллические покрытия представляют собой вещества с ионным или молекулярным типом связи, являющимися по своим электрическим свойствам диэлектриками или полупроводниками. Вследствие большого омического сопротивления электрохимическая коррозия в них не развивается. Ионным типом связи обладают покрытия из оксидов, создаваемые на сталях при нагреве на воздухе или при анодировании алюминия. Высокомолекулярные соединения входят в состав лаковых покрытий, а также совместно с оксидами
всостав красок и эмалей.
4.9.13.Жаростойкостьметалловисплавов
Под жаростойкими (окалиностойкими) сталями и сплавами понимают стали и сплавы, обладающие стойкостью против химического разрушения поверхности в газовых средах при температурах выше 550 °С и работающие в ненагруженном или слабонагруженном состоянии.
Конструкционные металлические материалы в процессе обработки и эксплуатации при нагреве в коррозионно-активных средах подвергаются химической коррозии и разрушению.
Жаростойкость (окалиностойкость) характеризуется сопротивлением металла окислению при высоких температурах.
Начальная стадия окисления стали представляют собой чисто химический процесс. Но дальнейшее течение окисления – уже сложный процесс, заключающийся не только в химическом соединении кислорода и металла, но и в диффузии атомов кислорода и металла через многофазный окисленный
Материаловедение. Учеб. пособие |
-265- |
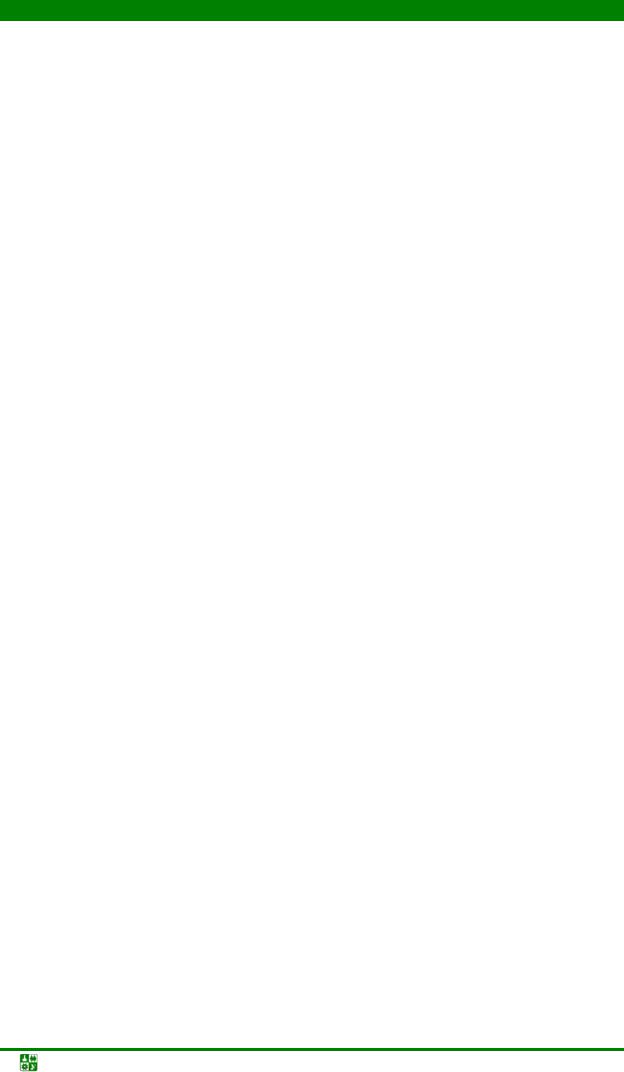
РАЗДЕЛ II. МАТЕРИАЛОВЕДЕНИЕ СТАЛЕЙ И ЧУГУНОВ
Глава 4. Стали, сплавы системы железо–углерод. Маркировка, структура, свойства сплавов
слой. При плотной окисной пленке скорость нарастания окалины определяется скоростью диффузии атомов сквозь толщину окалины, что в свою очередь зависит от температуры и строения окисной пленки.
Железо с кислородом образует ряд химических соединений: FeO (вюстит), Fe3О4 (магнетит) и Fe2О3 (гематит). При температурах ниже эвтектоидной (570 °С) окисленный слой состоит из двух зон окислов: Fe2О3 и Fe3О4. Кристаллическая структура этих окислов сложна, и скорость диффузии в них мала.
При температурах выше 570 °С структура окалины состоит из трех окислов: Fe2О3, Fe3О4 и FeO, причем основным слоем окалины является окись FeO. Скорость окисления возрастает при переходе через эвтектоидную температуру (570 °С), что является следствием более ускоренной диффузии атомов сквозь простую кристаллическую решетку вюстита, кристаллизующегося, как и фазы внедрения, с дефицитом в неметаллических атомах (кислорода).
Врезультате введения в сталь соответствующих количеств хрома, алюминия или кремния, обладающих большим сродством к кислороду, чем железо, в процессе окисления на поверхности образуются плотные окислы
Сr2О3, А12О3 или SiO2, диффузия сквозь которые происходит с трудом. Образовавшаяся тонкая пленка из этих окислов затрудняет процесс дальнейшего окисления. Чем выше содержание хрома, алюминия или кремния в стали, тем выше окалиностойкость стали и тем выше может быть рабочая температура. Как известно, при рабочей температуре 900 °С для достаточной окалиностойкости сплав (сталь) должен содержать не менее 10 % Сr, а при рабочей температуре 1 100 °С – не менее 20–25 % Сr.
Важно, что жаростойкость, столь существенно зависящая от состава стали или сплава, не зависит от его структуры, т.е. это свойство структурно нечувствительное.
Жаростойкими являются высоколегированные хромистые стали ферритного и мартенситного класса, хромоникелевые и хромомарганцевые стали аустенитного класса. Чем больше хрома содержит сталь, тем выше максимальная температура ее применения и больше срок эксплуатации изделий. Жаростойкие стали поставляются по ГОСТ 5632-72 и ГОСТ 59 49-75.
Следует отметить, что стали 08Х17Т и 15Х25Т ферритного класса (в структуре преобладает феррит) нежаропрочны, поэтому их используют в изделиях, которые не испытывают больших нагрузок, особенно ударных. Сплавы 20Х23Н18 и 20Х25Н20С2 аустенитного класса не только жаростойки, но и жаропрочны.
Вжаростойких сталях содержание алюминия и кремния ограничено, т.к. эти элементы охрупчивают сталь и ухудшают технологические свойства при обработке давлением. Этот недостаток можно исключить, если использовать их при поверхностном легировании. Жаростойкие стали Х13Ю4 и Х23Ю5Т, легированные хромом и алюминием, так же, как и сплав Х20Н80, используют в качетве материалов с повышенным электрическим сопротивлением.
Легирующие элементы в медных сплавах имеют большее химическое сродство к кислороду, чем медь, и при достаточном их количестве образуют
Материаловедение. Учеб. пособие |
-266- |
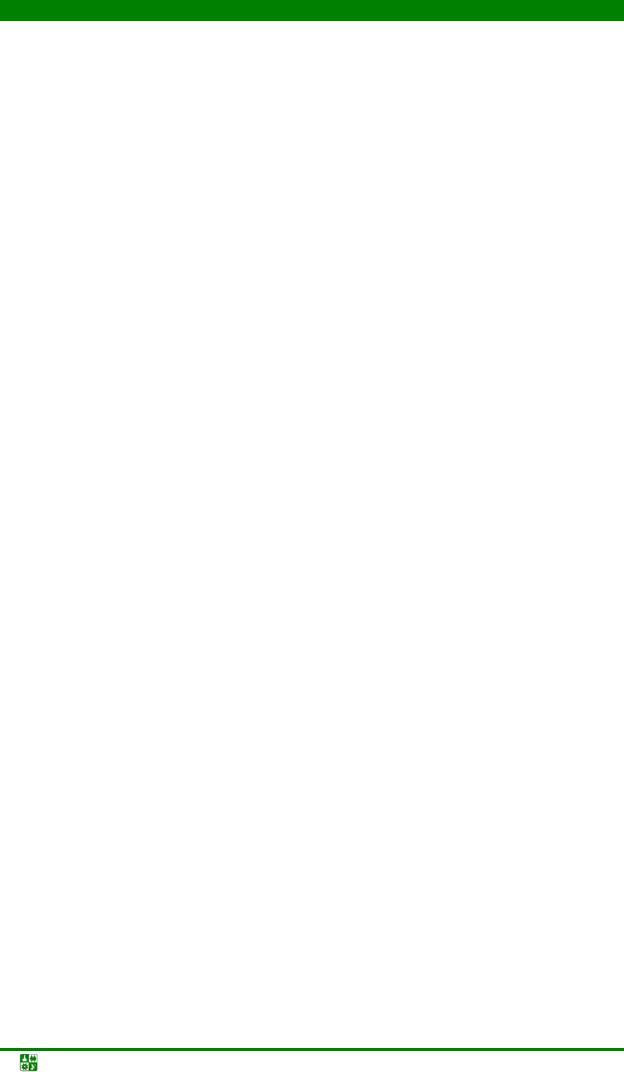
РАЗДЕЛ II. МАТЕРИАЛОВЕДЕНИЕ СТАЛЕЙ И ЧУГУНОВ
Глава 4. Стали, сплавы системы железо–углерод. Маркировка, структура, свойства сплавов
при нагреве собственные оксиды, обладающие лучшими защитными свойствами, чем Cu2O. Сплавы меди с бериллием, алюминием, марганцем отличаются высокой жаростойкостью; несколько уступают им сплавы меди с цинком, оловом и кремнием.
Титановые и цирконевые сплавы поглощают кислород, поэтому защитные оксиды на поверхности не образуются и жаростойкость титана при легировании не улучшается. Повысить жаростойкость удается лишь применением жаростойких покрытий.
4.9.14. Критериижаропрочности. Жаропрочныематериалы
Жаропрочностью называется способность материала длительное время сопротивляться деформированию и разрушению, когда рабочие температуры деталей превышают 0,3Tпл. Многие детали современных паросиловых установок, металлургических печей, двигателей внутреннего сгорания, газовых турбин и других машин нагреваются до высоких температур и несут большие нагрузки.
Ползучесть представляет собой медленное нарастание пластической деформации под действием напряжений, меньше предела текучести.
Критериями жаропрочности являются предел ползучести, предел длительной прочности, сопротивление релаксации.
Пределом ползучести называется напряжение, под действием которого материал деформируется на определенную величину за определенное время при заданной температуре. При обозначении предела ползучести указывают
температуру, деформацию и время, за которое она возникает. Например, σ5501/100000 = 100 МПа означает, что под действием напряжения 100 МПа за 100 000 ч при 550 °С в материале появится пластическая деформация 1 %.
Пределом длительной прочности называется напряжение, которое вызывает разрушение материала при заданной температуре за определенное
время. В обозначении предела длительной прочности указывают температуру и время до разрушения. Например, σ60010000 = 130 МПа означает, что при 600 °С материал выдерживает действие напряжения, равное 130 МПа, в течение
10 000 ч.
Ползучесть металлов вызывает релаксацию напряжений в предварительно нагруженных деталях. Критерием сопротивления релаксации является падение напряжения ∆σ = σ0 – στ за время τ при заданной температуре.
Большинство жаропрочных материалов – поликристаллические. Деформация ползучести в таких материалах развивается благодаря перемещению дислокаций в зернах, зернограничному скольжению и диффузионному переносу.
Для обеспечения жаропрочности требуется ограничить подвижность дислокаций и замедлить диффузию. Это достигается повышением прочности межатомных связей, созданием препятствий для перемещения дислокаций внутри зерен и на их границах, увеличением размеров зерен.
Материаловедение. Учеб. пособие |
-267- |
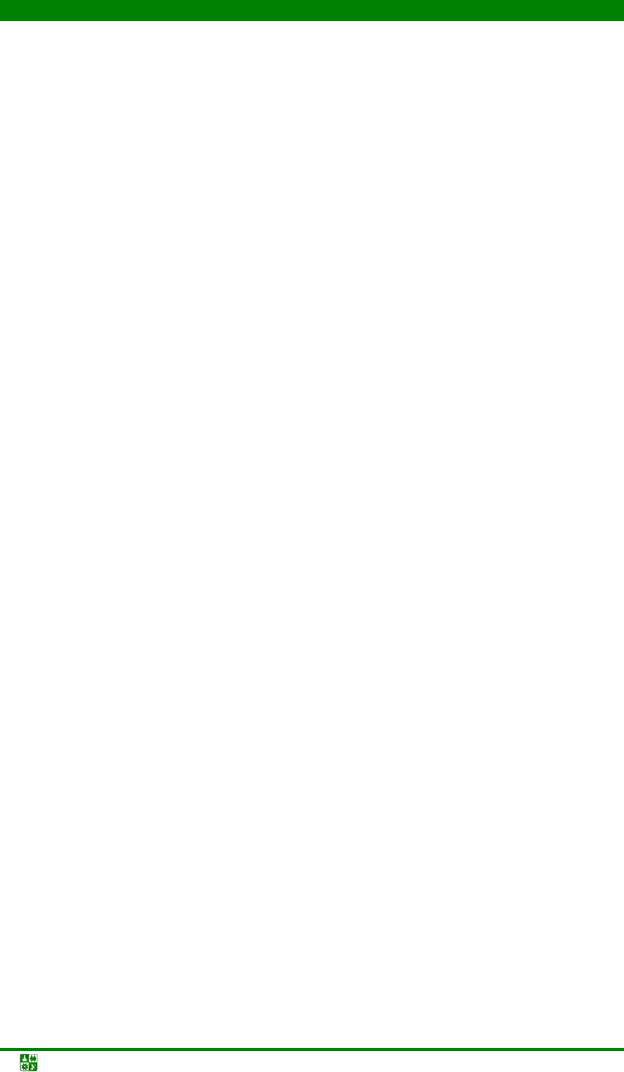
РАЗДЕЛ II. МАТЕРИАЛОВЕДЕНИЕ СТАЛЕЙ И ЧУГУНОВ
Глава 4. Стали, сплавы системы железо–углерод. Маркировка, структура, свойства сплавов
Прочность межатомной связи увеличивают легированием, изменением типа кристаллической решетки, переходом от металлической связи к более прочной ковалентной.
Подвижность дислокаций существенно снижается в многофазной структуре с мелкими частицами упрочняющих фаз. Материалы с многофазной структурой, получаемой термической обработкой, называются дисперси-
онно-упрочненными.
Крупнозернистость – характерная особенность структуры жаропрочных материалов. Чем крупнее зерно, тем меньше протяженность межзеренных границ и слабее зернограничное скольжение и диффузионый перенос. Для упрочнения границ зерен в жаропрочные стали и сплавы вводят малые добавки (0,1–0,01 %) легирующих элементов, которые концентрируются на границах.
К дополнительным мерам повышения жаропрочности относят: термомеханическую обработку для получения структуры полигонизации; упорядочение твердого раствора металла-основы и создание анизотропной структуры.
Жаропрочные материалы. Перлитные, мартенситные и аустенитные жаропрочные стали используют при 450–700 °С. По масштабам применения они занимают ведущее место среди жаропрочных материалов. Ниже 450 °С вполне пригодны обычные конструкционные стали и нет необходимости заменять их жаропрочными.
Жаропрочные сплавы на основе алюминия, магния и титана легче сталей, однако они менее жаропрочны. Используют их при следующих температурах: сплавы алюминия до 300–350 °С (исключением являются сплавы САП, которые можно применять до 500–550 °С); сплавы магния до 300–350 °С, сплавы титана до 500–600 °С.
Тугоплавкие металлы и их сплавы, керамика на основе SiC и Si3C4, графит – это материалы с высокой жаропрочностью, применяемые при температурах выше 1 000 °С.
Перлитные стали (12Х1МФ, 25Х2М1Ф) предназначены для длительной эксплуатациипри450–580 °С, используютглавнымобразомвкотлостроении.
Оптимальной термической обработкой являются нормализация после нагрева до ≈ 1 000 °С и последующий отпуск при 650–750 °С в течение 2–3 ч.
Стали пластичны в холодном состоянии, удовлетворительно обрабатываются резанием и свариваются. Стали, содержащие 0,12–0,15 % углерода, используют в паросиловых установках для изготовления труб пароперегревателей, паропроводов и других деталей, температура эксплуатации, которых не превышает 570–580 °С. Стали, содержащие 0,25–0,30 % углерода, используют для изготовления валов и цельнокованых роторов стационарных и транспортных паровых турбин, плоских пружин и крепежных деталей, работающих при температурах 525–565 °С.
Мартенситные стали предназначены для изделий, работающих при 450–600 °С. От перлитных они отличаются повышенной стойкостью к окис-
Материаловедение. Учеб. пособие |
-268- |
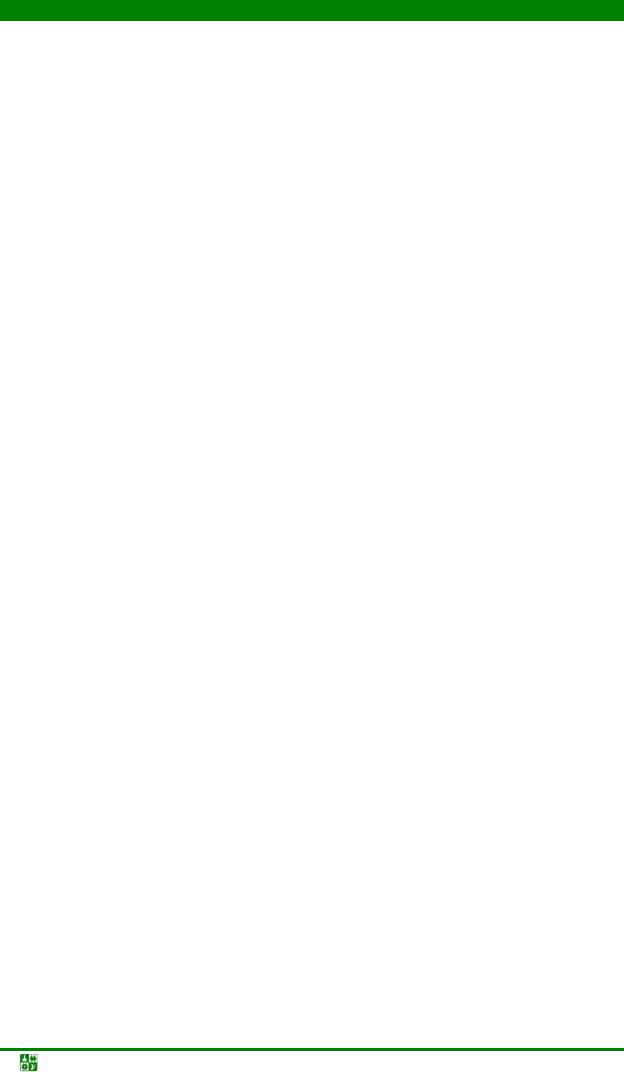
РАЗДЕЛ II. МАТЕРИАЛОВЕДЕНИЕ СТАЛЕЙ И ЧУГУНОВ
Глава 4. Стали, сплавы системы железо–углерод. Маркировка, структура, свойства сплавов
лению в атмосфере пара или топочных газов. По жаропрочности они превосходят перлитные.
Различают две группы мартенситных сталей:
•стали с содержанием хрома 10–12 %, добавками Mo, V, Nb, W и низким (0,10–0,15 %) содержанием углерода;
•сильхромы с содержанием хрома 5–10 %, добавками кремния в количестве до 2–3 % и повышенным содержанием углерода (до 0,4 %).
Стали первой группы используют в термически обработанном состоянии. Оптимальная термическая обработка заключается в закалке или нормализации после нагрева до 950–1 100 °С (для растворения карбидов) и отпуске при 600–740 °С. Структура термически обработанной стали (смесь легированного феррита и мелких карбидов) обеспечивает необходимую жаропрочность, сопротивление коррозии и релаксационную стойкость.
Мартенситные стали данной группы имеют разнообразное применение
впаровых турбинах: диски, лопатки, бандажи, диафрагмы, роторы, а также и крепежные детали.
Стали второй группы – сильхромы – характеризуются повышенной жаростойкостью в среде горячих выхлопных газов и используются для изготовления клапанов двигателей внутреннего сгорания. Оптимальные свойства сильхромы имеют после обработки на сорбит. Так, сталь 40Х10С2М закаливают после нагрева до 1 030 °С и отпускают при 720–780 °С. Чем больше содержания хрома и кремния в стали, тем выше ее рабочая температура. Жаропрочность сильхромов позволяет применять их при температурах не выше 600–650 °С. При более сложных условиях эксплуатации клапаны мощных двигателей изготовляют из аустенитных сталей. Сильхромы не содержат дорогих легирующих элементов и используются не только для клапанов двигателей, но и для крепежных деталей моторов. Технологические свойства сильхромов хуже, чем у перлитных сталей. Особенно затруднена их сварка, требуются подогрев перед сваркой и последующая термическая обработка.
Аустенитные стали по жаропрочности превосходят перлитные и мартенситные стали, используют их при температурах выше 600 °С. Основные легирующие элементы – хром и никель. Соотношение между ними выбирают таким, чтобы получить устойчивый аустенит, не склонный к фазовым превращениям.
Аустенитные жаропрочные стали подразделяют на три группы:
•однофазные стали, не упрочняемые термической обработкой;
•стали с карбидным упрочнителем;
•стали с интерметаллидным упрочнителем.
Однофазные стали имеют устойчивую структуру однородного аустенита с незначительным содержанием карбонитрида титана или ниобия (для предупреждения межкристаллитной коррозии). Такая структура получается после закалки от 1 020–1 100 °С. Стали этой группы применяют как жаропрочные в теплоэнергетике (например, 12Х18Н10Т).
Жаропрочность однофазных сталей увеличивают при помощи наклепа, пользуясь тем, что температура рекристаллизации аустенитных сталей высо-
Материаловедение. Учеб. пособие |
-269- |
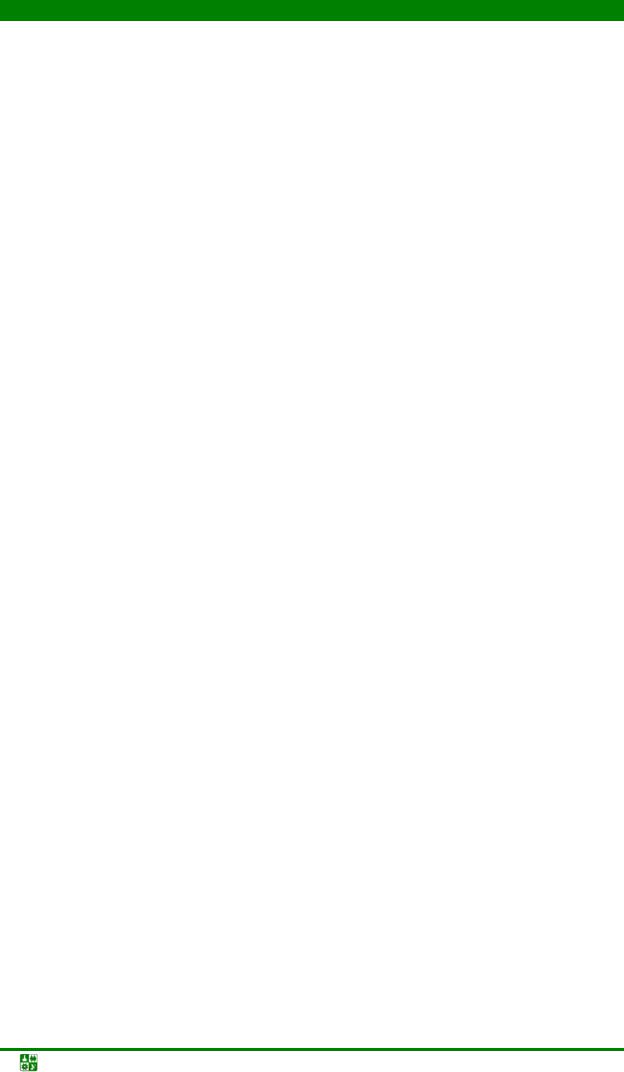
РАЗДЕЛ II. МАТЕРИАЛОВЕДЕНИЕ СТАЛЕЙ И ЧУГУНОВ
Глава 4. Стали, сплавы системы железо–углерод. Маркировка, структура, свойства сплавов
ка (около 1 000 °С). Другой путь создания жаропрочности – создание полигонизованной структуры.
Аустенитные стали с карбидным упрочнением обычно содержат несколько карбидообразующих элементов: W, Mo, Ti, Nb, V, а также В – для обеспечения наивысшей жаропрочности. Из-за высокого содержания ферритообразующих элементов содержание никеля повышают до 14 %. Оптимальная структура получается после закалки от 1 100–1 150 °С и старения полученного аустенита при 700–800 °С для выделения карбидов.
Аустенитные стали с интерметаллидным упрочнением – самые жаропрочные. Стали легируют Cr, Mo, W, добавки Al, Ti, Nb и Ta служат для формирования выделений упрочняющей фазы типа Ni3Al.
Их упрочняют закалкой и старением. Например, сталь 10Х11Н20Т3Р закаливают от 1 100–1 170 °С и старят при 700–750 °С в течение 15–25 ч.
Аустенитные стали отличаются большой пластичностью, хорошо свариваются, однако по сравнению с перлитными сталями труднее обрабатываются давлением и резанием.
Жаропрочные никелевые сплавы содержат, как правило, 10–12 % Cr и такие элементы, как W, Mo, V, Со, Аl, Ti, В и др.
Термическая обработка сплавов заключается в закалке и старении. Детали нагревают до 1 150–1 250 °С для получения однородного раствора и охлаждают на воздухе.
Помимо основного назначения – изготовление лопаток и других ответственных деталей современных газотурбинных двигателей, эти сплавы применяют для производства штампов и матриц горячего деформирования металлов. Их используют при температурах от 750 °С, но не выше 950–1 000 °С. Недостаток жаростойкости исправляется химико-термической обработкой деталей, в частности алитированием и хромоалитированием. Жаропрочные никелевые сплавы с трудом подвергаются горячему деформированию и резанию. Как и аустенитные стали, они имеют низкую теплопроводность и значительное тепловое расширение.
К тугоплавким относят металлы, у которых температура плавления превышает 1 700 °С. Наибольшее применение получили металлы VА подгруппы – V, Nb, Ta и металлы VIA подгруппы – Cr, W, Mo. Тугоплавкие металлы имеют прочные межатомные связи и отличаются высокими температурами плавления, малым тепловым расширением, небольшой теплопроводностью, повышенной жесткостью. Однако при высоких температурах все важнейшие тугоплавкие металлы (за исключением хрома) быстро окисляются. Низкая жаростойкость – большой недостаток тугоплавких металлов.
Сплавы на основе тугоплавких металлов подразделяют на две группы: сплавы со структурой твердого раствора и сплавы, упрочняемые закалкой и старением.
Сплавы на основе ниобия пригодны для использования до 1 300 °С, а при кратковременной эксплуатации выдерживают температуры до 1 500 °С. Их достоинство – небольшая плотность.
Материаловедение. Учеб. пособие |
-270- |
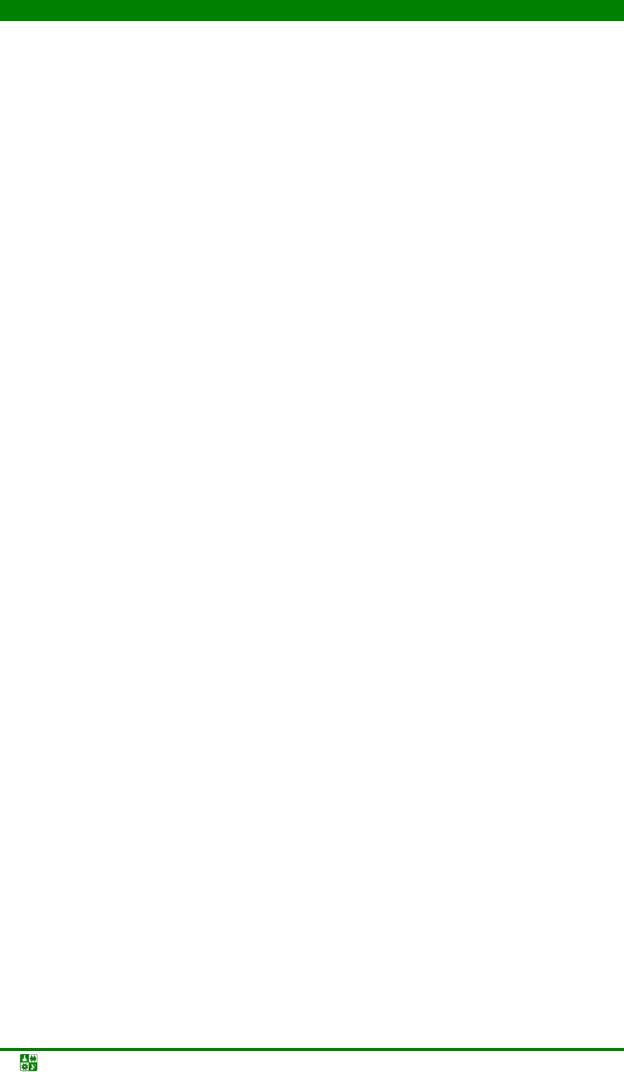
РАЗДЕЛ II. МАТЕРИАЛОВЕДЕНИЕ СТАЛЕЙ И ЧУГУНОВ
Глава 4. Стали, сплавы системы железо–углерод. Маркировка, структура, свойства сплавов
Сплавы на основе молибдена можно использовать до 1 300–1 400 °С, на основе тантала – до 2 000 °С, а на основе вольфрама – до 2 000–2 200 °С. При температурах до 1 900–2 000 °С многие сплавы на основе тугоплавких металлов более жаропрочны, чем вольфрам; выше 2 000–2 500 °С нелегированный вольфрам является самым жаропрочным металлом.
Неметаллические жаропрочные материалы. Графит и специальная керамика – наиболее важные неметаллические материалы, пригодные для службы при температурах выше 1 000 °С. В этих материалах преобладает ковалентный тип связи, и поэтому лишь при температурах выше 0,8tпл они быстро теряют жаропрочные свойства.
Уникальной особенностью графита является увеличение модуля упругости и прочности при нагреве. До 2 200–2 400 °С прочность графита повышается максимально на 60 %, и лишь при более высоких температурах он ее теряет. Графит, не плавясь, возгоняется при температурах, близких к 3 800 °С. При нагреве графит мало расширяется, хорошо проводит теплоту и поэтому устойчив против тепловых ударов. Ползучесть у графита проявляется при температуре выше 1 700 °С и характеризуется небольшой скоростью при 2 300–2 900 °С под действием напряжений 30–10 МПа соответственно. Серьезным недостатком графита является легкость окисления, уже при 520–560 °С потеря массы составляет 1 % за 24 ч, поэтому поверхность графитовых изделий защищают покрытиями.
Керамические материалы на основе SiC, Si3N4 и системы Si–Al–O–N
являются легкими, прочными и износостойкими веществами. В качестве конструкционных жаропрочных материалов их начинают применять в двигателях внутреннего сгорания для изготовления поршней, головок блока цилиндров и других теплонапряженных деталей. Керамические детали способны работать при высоких температурах (Si3N4 до 1 500 °С, SiC до 1 800 °С), стойки против коррозии и эрозии, не боятся перегрева и не нуждаются в принудительном охлаждении. В отличие от графита керамика меньше подвержена окислению и в несколько раз прочнее. Керамика изготовляется из недефицитных материалов. К недостаткам высокотемпературной керамики относятся хрупкость, сложность получения плотного беспористого материала и трудности изготовления деталей. По сравнению с керамикой, графит легче прессуется в горячем состоянии и хорошо обрабатывается резанием.
4.10.Инструментальныематериалы
4.10.1.Инструментальныестали
Основные свойства, которыми должен обладать материал для режущих инструментов, – износостойкость и теплостойкость.
Условия работы инструментов зависят от режимов резания и свойств обрабатываемого материала. Чем больше скорость резания, сечение снимаемой стружки, а также прочность и вязкость обрабатываемого материала, тем выше температура нагрева режущей кромки инструментов. При этих усло-
Материаловедение. Учеб. пособие |
-271- |
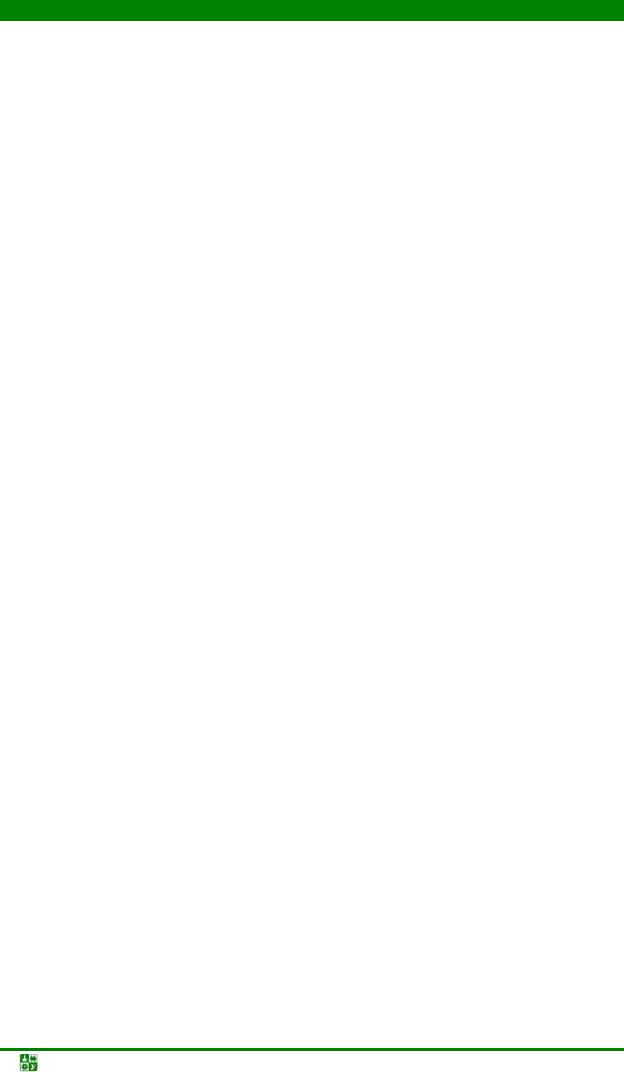
РАЗДЕЛ II. МАТЕРИАЛОВЕДЕНИЕ СТАЛЕЙ И ЧУГУНОВ
Глава 4. Стали, сплавы системы железо–углерод. Маркировка, структура, свойства сплавов
виях работоспособность инструментов определяется высокой «горячей» твердостью и способностью материала сохранять ее при длительном нагреве, т.е. теплостойкостью. От теплостойкости материала зависит производительность резания.
По теплостойкости применяемые материалы подразделяют на следующие группы:
1)углеродистыеинизколегированныестали степлостойкостьюдо200 °С;
2)высоколегированные быстрорежущие стали с теплостойкостью до
600–640 °С;
3)твердые сплавы с теплостойкостью до 800–1 000 °С;
4)сверхтвердые материалы с теплостойкостью до 1 200 °С. Углеродистые стали. Углеродистые стали (ГОСТ 1435-99) производят
качественными (У7, У8, У9, ..., У13) и высококачественными (У7А, У8А, У9А, ..., У13А). Буква У в марке показывает, что сталь углеродистая, а цифра – среднее содержание углерода в десятых долях процента. Углеродистые стали поставляют после отжига на зернистый перлит. Благодаря невысокой твердости в состоянии поставки (1 870–2 170 НВ), углеродистые стали хорошо обрабатываются резанием и деформируются, что позволяет применять накатку, насечку и другие высокопроизводительные методы изготовления инструментов.
Из-за низкой прокаливаемости (10–12 мм) углеродистые стали пригодны для мелких инструментов или инструментов с поперечным сечением до 25 мм с незакаленной сердцевиной, в которой режущая часть приходится на поверхностный слой (метчики, развертки, напильники и т.п.). Несквозная закалка уменьшает деформацию инструментов и повышает благодаря вязкой сердцевине их устойчивость к ударам и вибрациям. Инструмент с поперечным сечением 15–25 мм охлаждают в воде или водных растворах солей и щелочей. Инструменты с незакаленной сердцевиной меньшего сечения для уменьшения деформаций и опасности растрескивания охлаждают в масле или расплавах солей при 160–200 °С.
Режущие инструменты (мелкие метчики, сверла, напильники, пилы, шаберы и др.) изготовляют из заэвтектоидных сталей У10, У11, У12 и У13. Их подвергают неполной закалке и низкому отпуску при 150–180 °С на структуру мартенсита с включениями цементита. Такие инструменты обладают повышенной износостойкостью и высокой твердостью (62–64 HRC) на рабочих гранях, которая сильно снижается при нагреве свыше 200 °С. Поэтому инструменты из этих сталей пригодны для обработки сравнительно мягких материалов и при небольших скоростях резания.
Стали У7, У8, У9, обеспечивающие более высокую вязкость, применяют для инструментов, подвергающихся ударам: деревообрабатывающих, слесарных, кузнечных, а также пуансонов, матриц и др. После полной закалки их отпускают на структуру троостита при 275–325 °С (48–55 HRC) или при
400–450 °С (38–45 HRC).
Низколегированные стали. Такие стали содержат до 5 % легирующих элементов (табл. 4.17), которые вводят для увеличения закаливаемости, про-
Материаловедение. Учеб. пособие |
-272- |
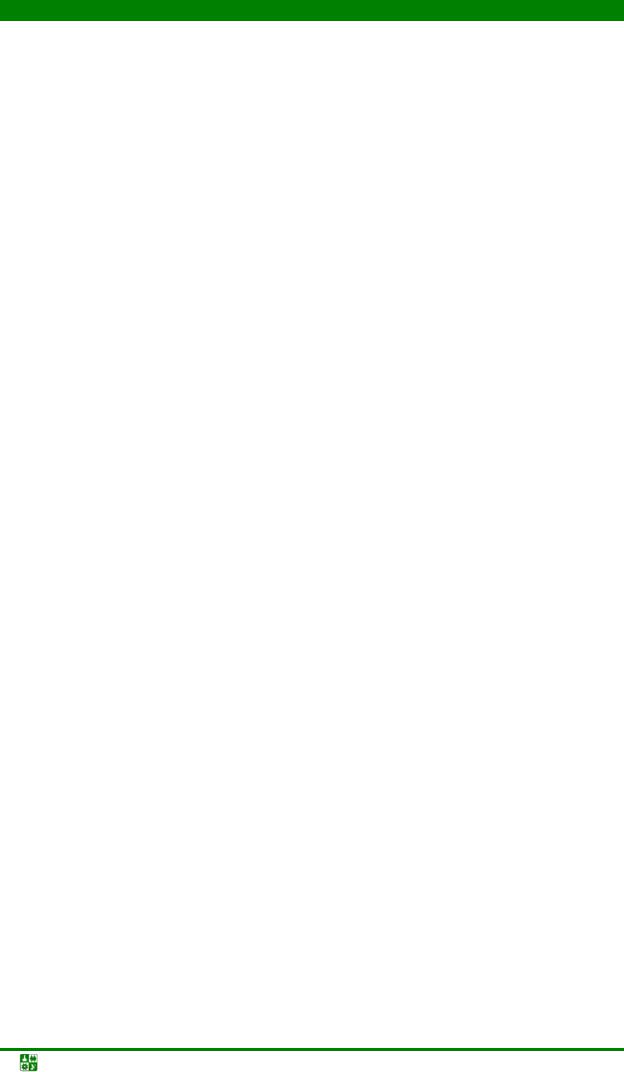
РАЗДЕЛ II. МАТЕРИАЛОВЕДЕНИЕ СТАЛЕЙ И ЧУГУНОВ
Глава 4. Стали, сплавы системы железо–углерод. Маркировка, структура, свойства сплавов
каливаемости, уменьшения деформаций и опасности растрескивания инструментов. Хром – постоянный элемент низколегированных сталей. Для улучшения свойств в них дополнительно вводят марганец, кремний, вольфрам.
Марганец (1–2 %) обеспечивает минимальное изменение размеров инструментов при закалке. Интенсивно снижая интервал температур мартенситного превращения, он способствует сохранению в структуре повышенного количества остаточного аустенита (15–20 %), который частично или полностью компенсирует увеличение объема в результате образования мартенсита. Кремний (1–1,5 %) несколько повышает сопротивление отпуску и способствует образованию легко отделяющейся окалины. Вольфрам (1–5 %) повышает износостойкость.
По структуре низколегированные стали относятся к заэвтектоидным сталям перлитного класса. Их подвергают неполной закалке от температуры несколько выше точки A1 и низкому отпуску. Структура мартенсита и избыточных карбидов (легированный цементит) обеспечивает им твердость (62–69 HRC) и высокую износостойкость. Однако из-за низкой теплостойкости низколегированные стали имеют практически одинаковые с углеродистыми сталями эксплуатационные свойства. Их применяют для инструментов, работающих при небольших скоростях резания, не вызывающих нагрева свыше 200–260 °С. В отличие от углеродистых, они меньше склонны к перегреву и позволяют изготовлять инструменты больших размеров и более сложной формы.
Сталь ХВ4 отличается особо высокой твердостью и износостойкостью благодаря тому, что в ней кроме легированного цементита присутствуют карбиды вольфрама типа M6C, которые практически не растворяются при температуре закалки. Из-за высокой твердости (67–69 HRC) ее называют алмазной и применяют для чистовой обработки твердых материалов.
Материаловедение. Учеб. пособие |
-273- |

|
|
|
|
|
|
РАЗДЕЛ II. |
МАТЕРИАЛОВЕДЕНИЕ СТАЛЕЙ И ЧУГУНОВ |
|
|
|
|
|||||||||
|
|
Глава 4. Стали, сплавы системы железо–углерод. Маркировка, структура, свойства сплавов |
|
|
||||||||||||||||
|
|
|
|
|
|
|
|
|
|
|
|
|
|
|
|
|
|
|
Таблица 4.17 |
|
|
|
Режимы термической обработки наиболее применяемых инструментальных сталей |
|
|
||||||||||||||||
|
|
|
|
|
|
|
(ГОСТ 5950-73, ГОСТ 19265-73, ГОСТ 28393-89) |
|
|
|
|
|||||||||
|
|
|
|
|
|
|
|
|
|
|
|
|
|
|
|
|
|
|
|
|
|
Cталь |
|
|
|
|
|
Массовая доля элементов, % |
|
|
|
|
Температура, °С |
|
|||||||
|
|
|
|
|
|
|
|
|
|
|
|
|
|
|
|
|
|
|
|
|
|
C |
Si |
|
Cr |
W |
Mo |
|
V |
|
Прочие |
|
Закалка |
Отпуск |
|
||||||
|
|
|
|
|
|
|
||||||||||||||
|
|
|
|
|
элементы |
|
|
|||||||||||||
|
|
|
|
|
|
|
|
|
|
|
|
|
|
|
|
|
|
|
|
|
|
|
|
|
|
|
|
|
|
Низколегированные стали |
|
|
|
|
|
|
|
||||
|
|
|
|
|
|
|
|
|
|
|
|
|
|
|
|
|
|
|
||
|
ХВ4 |
1,25–1,45 |
– |
|
0,4–0,7 |
3,5–4,3 |
– |
|
0,15–0,3 |
|
– |
|
800–820 |
100–140 |
|
|||||
|
9ХС |
0,85–0,95 |
1,2–1,6 |
|
0,95–1,25 |
– |
– |
|
– |
|
– |
|
840–860 |
140–180 |
|
|||||
|
ХВГ |
0,9–1,05 |
– |
|
0,9–1,2 |
1,2–1,6 |
– |
|
– |
|
0,8–1,1 Мn |
|
830–850 |
140–170 |
|
|||||
|
|
|
|
|
|
|
|
|
Быстрорежущие стали |
|
|
|
|
|
|
|
||||
|
|
|
|
|
|
|
|
|
|
|
|
|
|
|
|
|
|
|
||
|
Р18 |
0,73–0,83 |
|
– |
|
3,8–4,4 |
17–18,5 |
≤1 |
|
1,0–1,4 |
|
– |
1 |
270–1 290 |
550–570 |
|
||||
|
Р9 |
0,85–0,95 |
|
– |
|
3,8–4,4 |
8,5–10 |
≤1 |
|
2,3–2,7 |
|
– |
1 |
220–1 240 |
550–570 |
|
||||
|
Р6М5 |
0,82–0,9 |
|
– |
|
3,8–4,4 |
5,5–6,5 |
4,8–5,3 |
|
1,7–2,1 |
|
– |
1 |
210–1 230 |
540–560 |
|
||||
|
|
|
|
|
|
|
Стали для штампов холодной обработки давлением |
|
|
|
|
|
||||||||
|
|
|
|
|
|
|
|
|
|
|
|
|
|
|
|
|
|
|
||
|
Х12 |
2–2,2 |
|
– |
|
11,5–13 |
– |
– |
|
– |
|
– |
1 |
000–1 040 |
150–170 |
|
||||
|
Х12М |
1,45–1,65 |
|
– |
|
11–12,5 |
– |
0,4–0,6 |
|
0,15–0,3 |
|
– |
1 |
020–1 040 |
150–170 |
|
||||
|
Х6ВФ |
1,05–1,15 |
|
– |
|
5,5–6,5 |
1,1–1,5 |
– |
|
0,5–0,8 |
|
– |
|
950–970 |
150–170 |
|
||||
|
|
|
|
|
|
|
Стали для штампов горячей обработки давлением |
|
|
|
|
|
||||||||
|
|
|
|
|
|
|
|
|
|
|
|
|
|
|
|
|
|
|||
|
5ХНМ |
0,5–0,6 |
|
– |
|
0,5–0,8 |
|
– |
|
0,15–0,3 |
|
– |
|
1,4–1,8Ni |
|
820–740 |
480–580 |
|
||
|
5ХНВ |
0,5–0,6 |
|
– |
|
0,5–0,8 |
|
0,4–0,7 |
|
– |
|
– |
|
1,4–1,8Ni |
|
840–860 |
500–560 |
|
||
|
3Х2В8Ф |
0,3–0,4 |
|
– |
|
2,2–2,7 |
|
7,5–8,5 |
|
– |
|
0,2–0,5 |
|
– |
1 |
075–1 125 |
600–650 |
|
||
|
4Х2В5МФ |
0,3–0,4 |
|
– |
|
2,2–3 |
|
4,5–5,5 |
|
0,6–0,9 |
|
0,6–0,9 |
|
– |
1 |
050–1 080 |
600–650 |
|
Материаловедение. Учеб. пособие |
-274- |
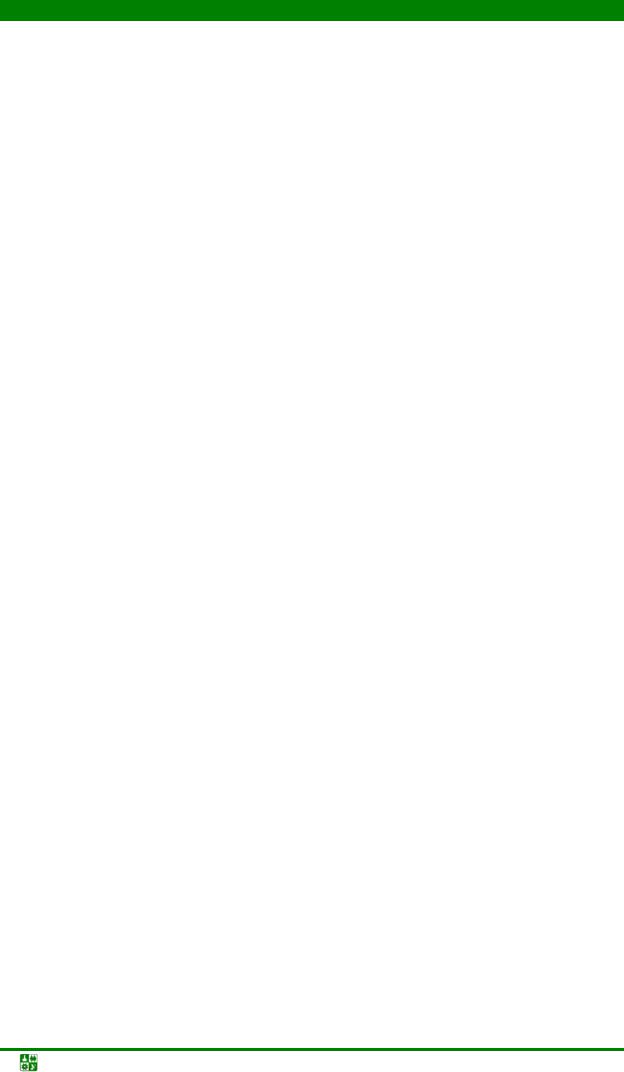
РАЗДЕЛ II. МАТЕРИАЛОВЕДЕНИЕ СТАЛЕЙ И ЧУГУНОВ
Глава 4. Стали, сплавы системы железо–углерод. Маркировка, структура, свойства сплавов
Стали X, 9ХС, ХВГ, ХВСГ закаливаются в масле и относятся к сталям глубокой прокаливаемости. Сталь 9ХС, в отличие от стали Х (1,5 % Сr), имеет более высокую устойчивость к разупрочнению при отпуске (до 260 °С), повышенные эксплуатационные свойства и применяется для изготовления фрез, сверл, резьбонарезных и других инструментов с поперечным сечением до 35 мм. Недостаток стали 9ХС – склонность к обезуглероживанию. Сталь ХВГ характеризуется малой деформацией при закалке и применяется для длинных стержневых инструментов (сверла, развертки, протяжки и т.п.) с поперечным сечением до 45 мм. Сложнолегированная сталь ХВСГ сочетает в себе лучшие свойства сталей 9ХС и ХВГ и используется для изготовления инструментов большого поперечного сечения (до 100 мм).
Быстрорежущие стали. К ним относят высоколегированные стали, предназначенные для изготовления инструментов высокой производительности.
Основное свойство этих сталей – высокая теплостойкость. Она обеспечивается введением большого количества вольфрама совместно с другими карбидообразующими элементами: молибденом, хромом, ванадием.
Вольфрам и молибден в присутствии хрома связывают углерод в специальный труднокоагулируемый при отпуске карбид типа М6С и задерживают распад мартенсита. Выделение дисперсных карбидов, которое происходит при повышенных температурах отпуска (500–600 °С), вызывает дисперсионное твердение мартенсита – явление вторичной твердости. Особенно эффективно вторичная твердость и теплостойкость повышаются при введении нескольких сильных карбидообразователей, например вольфрама (одного или совместно с молибденом) и ванадия. При отпуске ванадий, выделяясь в виде карбидов, усиливает дисперсионное твердение, а вольфрам (молибден), сохраняясь в мартенсите, задерживает его распад.
Увеличению теплостойкости способствует также кобальт. Он не образует карбидов, но, повышая энергию межатомных сил связи, затрудняет коагуляцию карбидов и увеличивает их дисперсность.
В результате комплексного легирования инструменты из быстрорежущих сталей сохраняют высокую твердость до 560–640 °С и допускают в 2–4 раза более производительные режимы резания, чем инструменты из углеродистых и низколегированных сталей.
Быстрорежущие стали обозначают буквой Р, цифра после буквы указывает содержание (в процентах) вольфрама – основного легирующего элемента (ГОСТ 19265–79). Содержание ванадия (до 2 %) и хрома, количество которого примерно 4 % во всех сталях, в марке не указывается. Стали, содержащие дополнительно молибден, кобальт или повышенное количество ванадия, имеют в марке, соответственно, буквы М, К, Ф и цифры, показывающие их массовую долю в процентах (например, Р6М5, Р10К5Ф5). В ГОСТ 19265-73 предусмотрено 14 марок быстрорежущих сталей, которые по эксплуатационным свойствам делятся на две группы: нормальной и повышенной производительности.
Материаловедение. Учеб. пособие |
-275- |

РАЗДЕЛ II. МАТЕРИАЛОВЕДЕНИЕ СТАЛЕЙ И ЧУГУНОВ
Глава 4. Стали, сплавы системы железо–углерод. Маркировка, структура, свойства сплавов
Группу сталей нормальной производительности образуют вольфрамовые (Р18, Р12, Р9, Р9Ф5) и вольфрамомолибденовые (Р6МЗ, Р6М5) стали, сохраняющие твердость не ниже 58 HRC до температуры 620 °С. При одинаковой теплостойкости эти стали отличаются главным образом механическими и технологическими свойствами. Лучшей обрабатываемостью давлением и резанием, а также прочностью и вязкостью обладают стали Р6МЗ и Р6М5. Стали Р9, Р9Ф5 плохо шлифуются из-за присутствия твердых карбидов ванадия.
К группе сталей повышенной производительности относятся стали, содержащие кобальт и повышенное количество ванадия: Р6М5К5, Р9М4К8, Р9К5, Р9К10, Р10К5Ф5, Р18К5Ф2. Они превосходят стали первой группы по теплостойкости (630–640 °С), твердости (HRC ≥ 64) и износостойкости, но уступают им по прочности и пластичности. Стали повышенной производительности предназначены для обработки высокопрочных сталей, коррозионностойких и жаропрочных сталей с аустенитной структурой и других труднообрабатываемых материалов.
Быстрорежущие стали, особенно второй группы, отличаются высокой стоимостью. Для уменьшения расхода дорогих и дефицитных элементов, особенно вольфрама, преимущественно используют экономно-легированные стали. Из них наиболее широкое применение имеет сталь Р6М5. Разрабатываются безвольфрамовые быстрорежущие стали.
Особенности термической обработки, структуры и свойств быстрорежущих сталей представлены на примере сталей Р18 и Р6М5.
По структуре после отжига быстрорежущие стали относятся к ледебуритному классу. В литом виде они имеют ледебуритную эвтектику, которую устраняют горячей деформацией путем измельчения первичных карбидов.
При недостаточной проковке этих сталей, возникает карбидная ликвация – местное скопление карбидов в виде участков неразрушенной эвтектики. Карбидная ликвация снижает стойкость инструмента и увеличивает его хрупкость. Деформированную сталь для снижения твердости (до 2 070–2 550 НВ) подвергают изотермическому отжигу. Структура отожженных сталей состоит из сорбитообразного перлита, вторичных и более крупных первичных карбидов. Общее количество карбидов в стали Р18 составляет примерно 28 %, в стали Р6М5 – 22 %. Основным карбидом стали Р18 является сложный карбид вольфрама переменного состава Fe3W3C (М6С), который растворяет в себе часть ванадия и хрома. В остальных сталях кроме М6С и небольшого количества карбида (Fe, Сr)23С6, присутствует карбид VC(MC).
В карбидах содержится 80–95 % вольфрама и ванадия и 50 % хрома. Остальная часть легирующих элементов раcтворена в феррите.
Высокие эксплуатационные свойства инструменты из быстрорежущих сталей приобретают после закалки и трехкратного отпуска (рис. 4.39). Из-за низкой теплопроводности быстрорежущие стали при закалке нагревают медленно с прогревами при 450 и 850 °С, применяя соляные ванны для уменьшения окисления и обезуглероживания. Особенность закалки быстрорежущих сталей – высокая температура нагрева. Она необходима для обеспечения теплостойкости – получения после закалки высоколегированного мар-
Материаловедение. Учеб. пособие |
-276- |
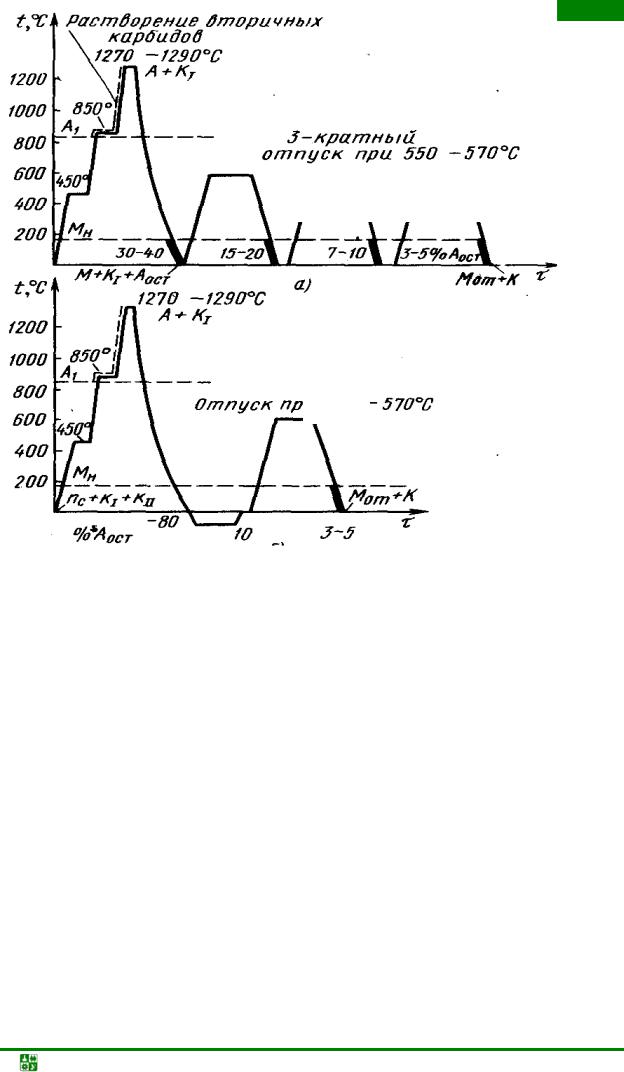
РАЗДЕЛ II. МАТЕРИАЛОВЕДЕНИЕ СТАЛЕЙ И ЧУГУНОВ
Глава 4. Стали, сплавы системы железо–углерод. Маркировка, структура, свойства сплавов
тенсита в результате перехода в раствор максимального количества специальных карбидов.
а
б
Рис. 4.39. Схема термической обработки быстрорежущей стали: а – без обработки холодом; б – с обработкой холодом
Степень легирования аустенита (мартенсита) увеличивается с повышением температуры нагрева (рис. 4.39). При температуре 1 300 °С достигается предельное насыщение аустенита – в нем растворяется весь хром, около 8 % W, 1 % V и 0,4–0,5 % С.
Легирование аустенита происходит при растворении вторичных карбидов. Первичные карбиды не растворяются и тормозят рост зерна аустенита, поэтому при нагреве, близком к температуре плавления, в быстрорежущих сталях сохраняется мелкое зерно.
Быстрорежущие стали по структуре после нормализации относятся к мартенситному классу. От температуры закалки мелкие инструменты охлаждают на воздухе, крупные – в масле.
Материаловедение. Учеб. пособие |
-277- |
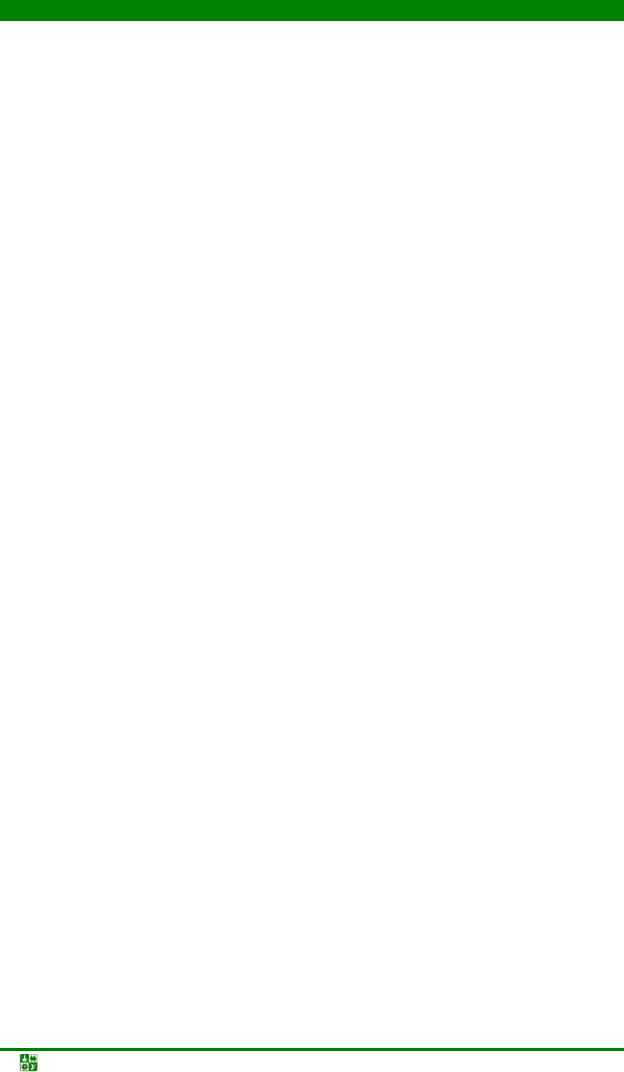
РАЗДЕЛ II. МАТЕРИАЛОВЕДЕНИЕ СТАЛЕЙ И ЧУГУНОВ
Глава 4. Стали, сплавы системы железо–углерод. Маркировка, структура, свойства сплавов
Сложные по форме инструменты для уменьшения деформаций подвергают ступенчатой закалке с выдержкой в горячих средах при температуре
500–550 °С.
После закалки не достигается максимальная твердость сталей (60–62 HRC), т.к. в структуре кроме мартенсита и первичных карбидов содержится 30–40 % остаточного аустенита, присутствие которого вызвано снижением температуры точки Мк ниже 0 °С.
Остаточный аустенит превращают в мартенсит при отпуске или обработке холодом. Отпуск проводят при температуре 550–570 °С. В процессе выдержки при отпуске из мартенсита и остаточного аустенита выделяются дисперсные карбиды М6С. Аустенит, обедняясь углеродом и легирующими элементами, становится менее устойчивым и при охлаждении ниже точки Мн испытывает мартенситное превращение. Однократного отпуска недостаточно для превращения всего остаточного аустенита. Применяют двух-, трехкратный отпуск с выдержкой по 1 ч и охлаждением на воздухе. При этом количество аустенита снижается до 3–5 %. Применение обработки холодом после закалки сокращает цикл термической обработки. В термически обработанном состоянии быстрорежущие стали имеют структуру, состоящую из мартенсита отпуска и карбидов и твердость 63–65 HRC.
Режущие свойства некоторых видов инструментов (фасонные резцы, сверла, фрезы, протяжки и др.) дополнительно улучшают созданием на неперетачиваемых поверхностях тонкого слоя (10–50 мкм) нитридов или карбонитридов. Такой слой характеризуется высокой твердостью (10 000 HV и более) и износостойкостью
Новым технологическим направлением повышения качества инструмента является его производство из распыленных порошков. Благодаря сильному измельчению карбидов и равномерному их распределению в спеченной стали, стойкость инструмента увеличивается в 1,5–2 раза.
Стали для измерительных инструментов. Основные свойства, кото-
рыми должны обладать стали этого назначения, – это высокая износостойкость, постоянство размеров и формы в течение длительного срока службы. К дополнительным требованиям относятся возможность получения низкой шероховатости поверхности и малой деформации при термической обработке. Наиболее широко применяют заэвтектоидные низколегированные стали X, ХГ, ХВГ, 9ХС, обрабатываемые на высокую твердость (60–64 HRC). Термическая обработка сталей проводится таким образом, чтобы затруднить процесс старения, который происходит в закаленной стали и вызывает объемные изменения, недопустимые для измерительных инструментов. Для уменьшения количества остаточного аустенита закалку проводят с более низкой температуры. Кроме того, инструменты высокой точности подвергают обработке холодом при температуре 50–80 °С. Отпуск проводят при 120– 140 °С в течение 24–48 ч. Более высокий нагрев не применяют из-за снижения износостойкости.
Инструменты повышенной точности подвергают неоднократному чередованию обработки холодом и кратковременного (2–3 ч) отпуска.
Материаловедение. Учеб. пособие |
-278- |
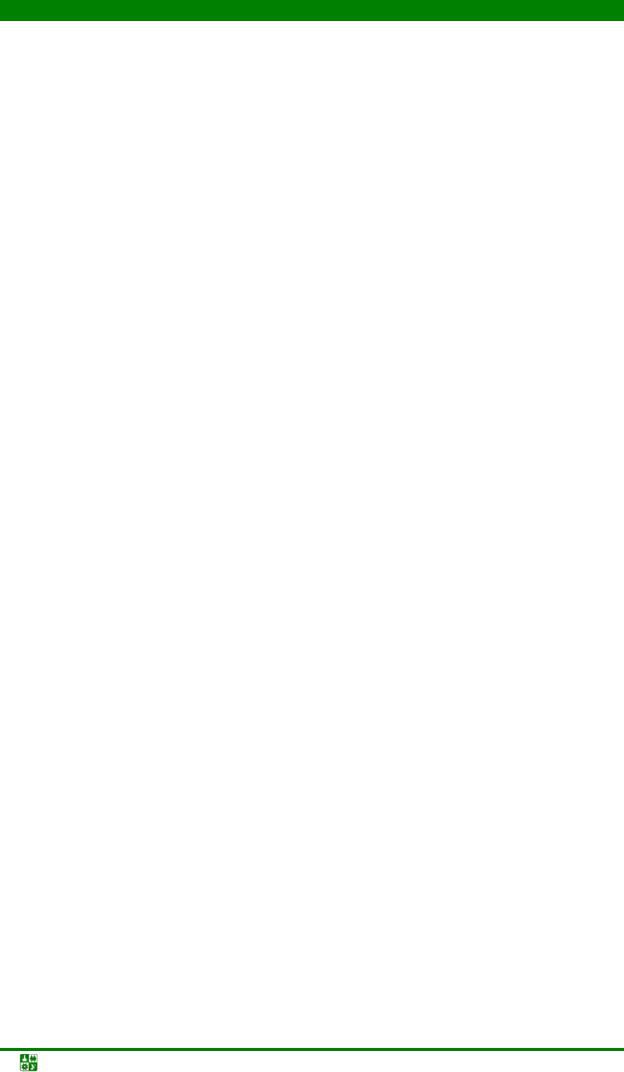
РАЗДЕЛ II. МАТЕРИАЛОВЕДЕНИЕ СТАЛЕЙ И ЧУГУНОВ
Глава 4. Стали, сплавы системы железо–углерод. Маркировка, структура, свойства сплавов
Плоские инструменты (скобы, линейки, шаблоны и т.п.) нередко изготовляют из листовых сталей 15, 20, 15Х, 20Х, 12ХНЗА, подвергаемых цементации, или из сталей 50 и 55, закаливаемых с поверхности с нагревом ТВЧ. Поскольку неравновесная структура в этих сталях образуется только в поверхностном слое, происходящие в нем объемные изменения мало отражаются на размерах всего инструмента.
Для инструментов сложной формы и большого размера применяют азотируемую сталь 38Х2МЮА.
Стали для инструментов обработки металлов давлением. Основ-
ные свойства, которыми должны обладать стали для штампов и других инструментов холодной обработки давлением, – высокая твердость, износостойкость, прочность, сочетающиеся с удовлетворительной вязкостью. При больших скоростях деформирования, вызывающих разогрев кромки инструментов до 450 °С, от сталей требуется достаточная теплостойкость. Для штампов со сложной гравюрой важно обеспечить минимальные объемные изменения при закалке.
Низколегированные стали Х, 9ХС, ХВГ, ХВСГ так же, как и углеродистые У10, У11, У12, используют для вытяжных и высодочных штампов, которые из-за несквозной прокаливаемости имеют твердый износостойкий слой и вязкую сердцевину. Вытяжные штампы после неполной закалки отпускают при 150–180 °С на твердость 52–54 HRC.
Высокохромистые стали Х12, Х12М, Х12Ф1 (табл. 4.17) обладают высокой износостойкостью и глубокой прокаливаемостью (150–200 мм). Их применяют для изготовления крупных инструментов сложной формы: вырубных, обрезных, чеканочных штампов повышенной точности, калибровочных волочильных досок, накатных ролиов. Эти стали близки к быстрорежущим: по структуре после отжига относятся к ледебуритному классу.
Хромокремнистые стали 4ХС, 6ХС, 4ХВ2С, 5ХВ2С, 6ХВ2С образуют группу сталей повышенной вязкости, используемых для изготовления инструментов, подвергающихся ударам (зубила, гибочные штампы и др.). Их отпускают на твердость 52–55 HRC при температуре 240–270 °С.
Стали для штампов горячей обработки давлением работают в тяжелых условиях, испытывая интенсивное ударное нагружение, периодический нагрев и охлаждение поверхности. Кроме достаточной прочности, износостойкости, вязкости и прокаливаемости (для крупных штампов), эти стали должны обладать также теплостойкость, окалиностойкостью и разгаростойкостью. Под разгаростойкостью понимают устойчивость к образованию поверхностных трещин, вызываемых объемными изменениями в поверхностном слое при резкой смене температур. Это свойство обеспечивается снижением содержания углерода в стали. Поэтому для штампов горячей обработки давлением применяют легированные стали, содержащие 0,3–0,6 % С, которые после закалки подвергаю отпуску при 550–680 °С на структуру троостита или троостосорбита.
Сталь 5ХНМ применяют для изготовления крупных штампов сложной формы. Стали 5ХГМ и 5ХНВС при одинаковой прокаливаемости со сталью
Материаловедение. Учеб. пособие |
-279- |
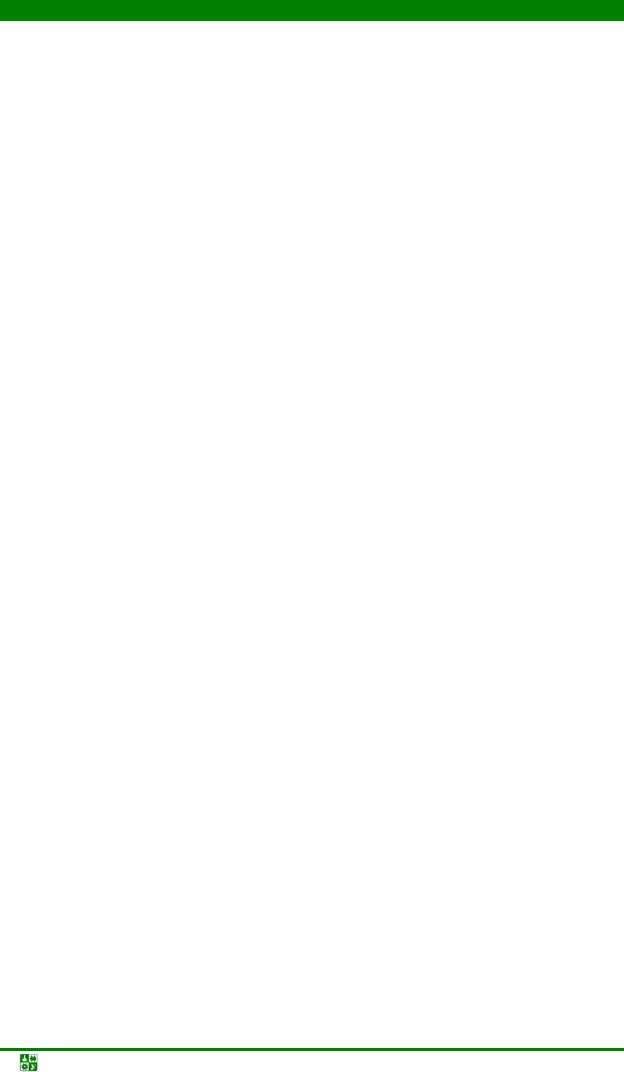
РАЗДЕЛ II. МАТЕРИАЛОВЕДЕНИЕ СТАЛЕЙ И ЧУГУНОВ
Глава 4. Стали, сплавы системы железо–углерод. Маркировка, структура, свойства сплавов
5ХНМ уступают ей в вязкости. Они предназначены для средних штампов (наибольшая сторона заготовок 300–400 мм) или более крупных, но простой формы.
Штампы горячей высадки, протяжки и прессования испытывают при работе высокие давления без больших ударных нагрузок, имеют меньшие размеры, чем молотовые штампы, но нагреваются до более высоких температур. Для них наиболее важны свойства – теплостойкость и разгаростойкость. При тяжелых условиях работы применяют комплексно-легированные стали 3Х2В8Ф, 4Х2В5МФ, 4Х5МФС и другие, которые по составу и видам превращений при термической обработке сходны с быстрорежущими сталями.
4.10.2. Инструментальныесплавыиматериалы
Порошковые твердые сплавы. К таким сплавам относят материалы, состоящие из высокотвердых и тугоплавких карбидов вольфрама, титана, тантала, соединенных металлической связкой.
Твердые сплавы изготовляют порошковой технологией. Порошки карбидов смешивают с порошком кобальта, выполняющего роль связки, прессуют и спекают при 1 400–1 500 °С. При спекании кобальт растворяет часть карбидов и плавится. В результате получается плотный материал, структура которого на 80–95 % состоит из карбидных частиц, соединенных связкой. Увеличение содержания связки вызывает снижение твердости, но повышение прочности и вязкости. Твердые сплавы производят в виде пластин, которыми оснащают резцы, сверла, фрезы и другие режущие инструменты. Такие инструменты сочетают высокую твердость 85–92 НRА (74–76 НRС) и износостойкость с высокой теплостойкостью (800–1 000 °С). По своим эксплуатационным свойствам они превосходят инструменты из быстрорежущих сталей
иприменяются для резания с высокими скоростями.
Взависимости от состава карбидной основы порошковые твердые сплавы выпускают трех групп.
Первую (вольфрамовую) группу составляют сплавы системы WС–Со. Их маркируют буквами ВК и числом, показывающим содержание кобальта в процентах. Карбидная фаза сплавов этой группы состоит из зерен WС. При одинаковом содержании кобальта, они, в отличие от сплавов двух других групп, характеризуются наибольшей прочностью, но более низкой твердостью. Сплавы вольфрамовой группы теплостойки до 800 °С.
Сплавы ВК3–ВК8 применяют для режущих инструментов при обработке материалов, дающих прерывистую стружку (чугуны, цветные металлы, фарфор, керамика).
Сплавы ВК10 и В15, обладающие из-за повышенного содержания кобальта более высокой вязкостью, используют для волочильных и буровых инструментов, стойкость которых в десятки раз превышает стойкость стальных. Сплавы с высоким содержанием кобальта (ВК20, ВК25) применяют для изготовления штамповых инструментов, а также в качестве конструкционно-
Материаловедение. Учеб. пособие |
-280- |
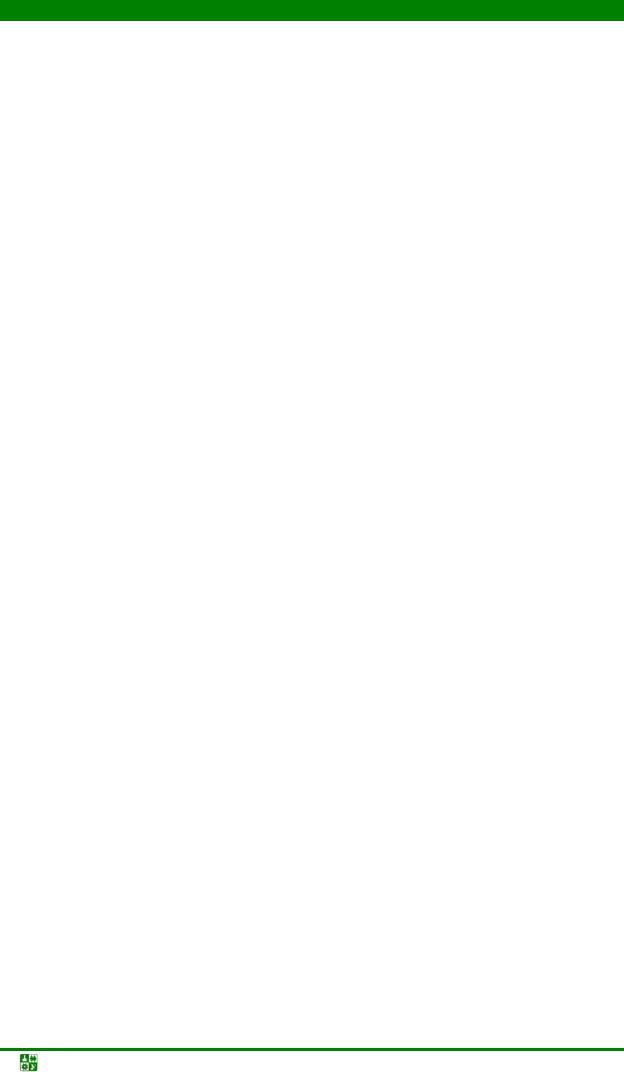
РАЗДЕЛ II. МАТЕРИАЛОВЕДЕНИЕ СТАЛЕЙ И ЧУГУНОВ
Глава 4. Стали, сплавы системы железо–углерод. Маркировка, структура, свойства сплавов
го материала для деталей машин и приборов, от которых требуется высокое сопротивление пластической деформации или изнашиванию.
Вторую (титановольфрамовую) группу образуют сплавы системы Ti– WC–Cо. Их маркируют буквами Т и К, а также числами, показывающими процентное содержание карбидов титана и кобальта. При температурах спекания карбид титана растворяет до 70 % WC и образует твердый раствор (Ti,W)C, обладающий более высокой твердостью, чем WC. Структура карбидной основы зависит от соотношения карбидов в шихте. В сплаве Т30К4 образуется одна карбидная фаза – твердый раствор (Ti, W)C, который придает ему наиболее высокие режущие свойства, но понижает прочность. В остальных сплавах этой группы количество WC превышает его предельную растворимость в TiC, поэтому карбиды вольфрама присутствуют в виде избыточных кристаллов.
Сплавы второй группы характеризуются более высокой, чем у сплавов первой группы, теплостойкостью (900–1 000 °С), которая повышается по мере увеличения количества TiС. Их наиболее широко применяют для высокоскоростного резания сталей.
Третью (титанотанталовольфрамовую) группу образуют сплавы системы TiС–ТаС–WС–Со. Число, стоящее в марке после букв ТТ, обозначает суммарное процентное содержание карбидов TiС + ТаС, а после буквы К – количество кобальта в процентах. От сплавов предыдущей группы эти сплавы отличаются большой прочностью и лучшей сопротивляемостью вибрациям и выкрашиванию. Их применяют при наиболее тяжелых условиях резания (черновая обработка слитков, отливок, поковок).
Сверхтвердые материалы. Сверхтвердые материалы широко применяют для оснащения (вставками) лезвийных инструментов (резцы, сверла, торцовые фрезы). Такие инструменты используют для чистовой обработки при высоких скоростях резания.
Среди сверхтвердых материалов первое место принадлежит алмазу, твердость которого (10 000 HV) в шесть раз превосходит твердость карбида вольфрама (1 700 HV) и в восемь раз – твердость быстрорежущей стали (1 300 HV). Преимущественное применение имеют синтетические алмазы (борт, баллас, карбонадо) поликристаллического строения, которые по сравнению с монокристаллами отличаются меньшей хрупкостью и стоимостью. Алмаз теплостоек до 800 °С (при большем нагреве он графитизируется). Относительно небольшая теплостойкость компенсируется его высокой теплопроводностью, снижающей разогрев режущей кромки инструментов при высоких скоростях резания.
Область применения алмазных инструментов ограничивается высокой адгезией к железу, что является причиной его низкой износостойкости при точении сталей и чугунов. Алмазным инструментом обрабатывают цветные металлы и их сплавы, а также пластмассы, керамику, обеспечивая при этом низкую шероховатость поверхности.
Большой универсальностью обладают инструменты из поликристаллического нитрида бора ВN с кубической решеткой, называемого кубиче-
Материаловедение. Учеб. пособие |
-281- |
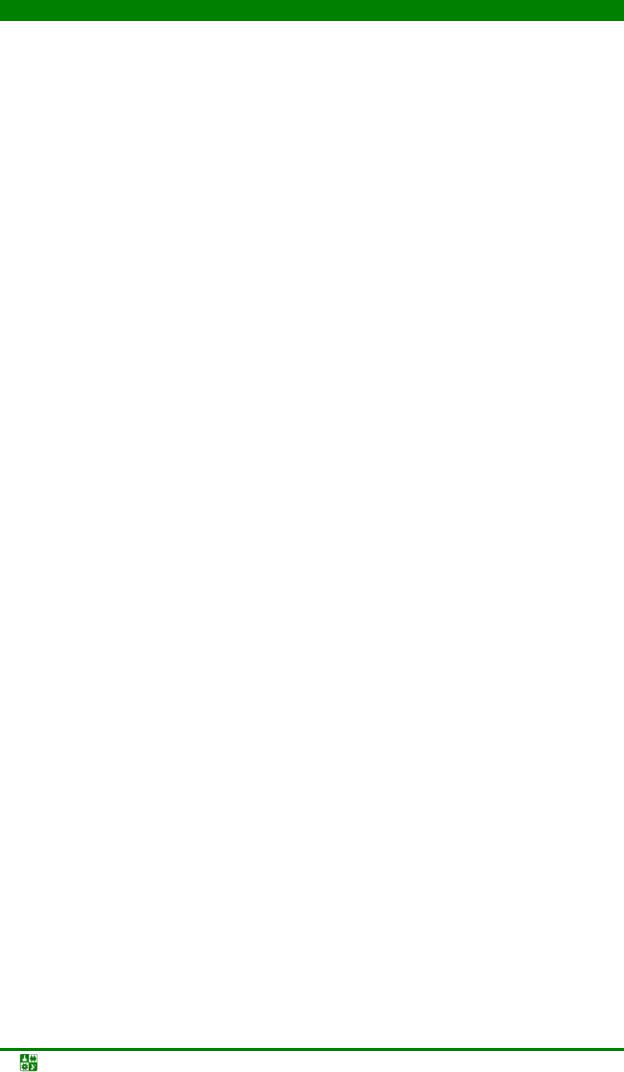
РАЗДЕЛ II. МАТЕРИАЛОВЕДЕНИЕ СТАЛЕЙ И ЧУГУНОВ
Глава 4. Стали, сплавы системы железо–углерод. Маркировка, структура, свойства сплавов
ским нитридом бора. Его получают спеканием микропорошков нитрида бора (гексагонального, кубического или вюрцитоподобного) при высоких температурах и давлениях или прямым синтезом из нитрида бора с гексагональной решеткой. В зависимости от технологии получения кубический нитрид бора выпускают под названием «эльбор», «эльбор-Р», «боразон».
Кубический нитрид бора имеет такую же, как алмаз, кристаллическую решетку и близкие с ним свойства. По твердости (9 000 HV) он не уступает алмазу, но превосходит его по теплостойкости (1 200 °С) и химической инертности. Отсутствие у кубического нитрида бора химического сродства к железу позволяет эффективно использовать его для обработки различных труднообрабатываемых сталей, в том числе цементованных закаленных. При этом высокоскоростное точение закаленных сталей может заменить шлифование, сокращая в 2–3 раза время обработки и обеспечивая низкую шероховатость поверхности.
Контрольныевопросыизадания
1.Какой тип кристаллической решетки имеет железо при температуре выше и ниже 911 °С?
2.Укажите предельную растворимость углерода в аустените, δ и α- феррите.
3.Опишите кристаллическую структуру твердых растворов на основе железа в системе Fe–Fe3C.
4.При какой температуре происходит эвтектическое и эвтектоидное превращение в метастабильной диаграмме Fe–Fe3C?
5.При каких температурах и в каких сплавах в системе Fe–Fe3C образуется первичный, вторичный и третичный цементит?
6.Укажите концентрацию углерода, соответствующую эвтектоидной точке в системе Fe–Fe3C.
7.В каких сплавах системы Fe–Fe3C структурно выявляется третичный цементит?
8.Какие фазы входят в перлит?
9.Как меняется тип структуры доэвтектоидных сталей с увеличением содержания углерода?
10.Какие структурные составляющие определяют структуру заэвтектоидных сталей?
11.Укажите фазовый состав и изобразите структуру отожженной ста-
ли 20. Определите по диаграмме Fe–Fe3C количество структурных составляющих в сплаве.
12.Опишите фазовые превращения в стали 50 по диаграмме Fe–Fe3C.
13.Укажите фазовый состав и изобразите структуру стали У10.
14.В каких условиях в стали У8 формируется структура пластинчатого
изернистого перлита?
Материаловедение. Учеб. пособие |
-282- |
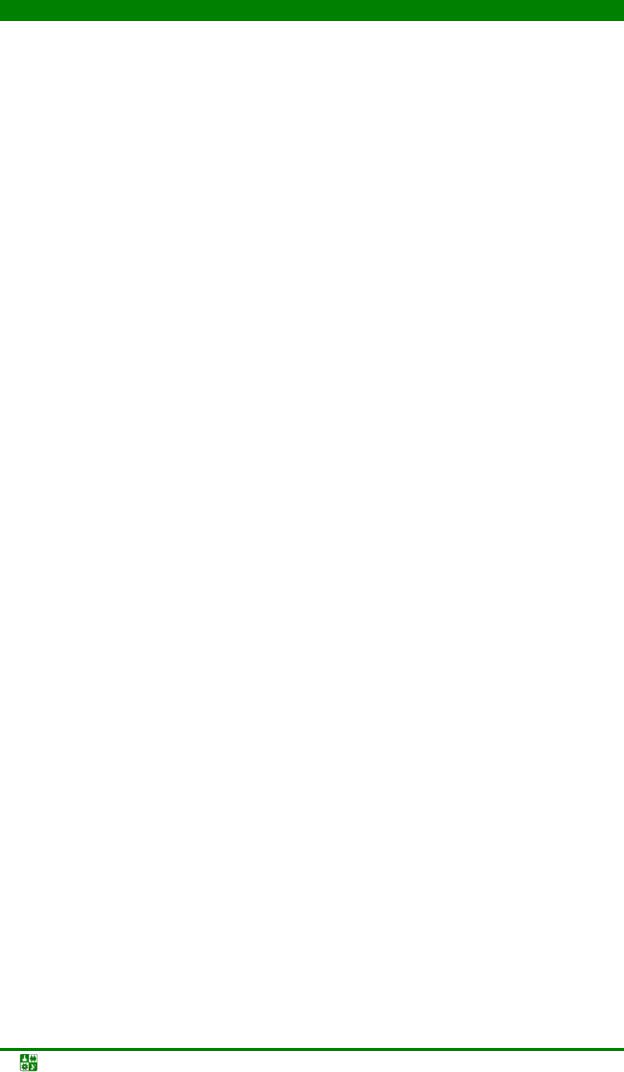
РАЗДЕЛ II. МАТЕРИАЛОВЕДЕНИЕ СТАЛЕЙ И ЧУГУНОВ
Глава 4. Стали, сплавы системы железо–углерод. Маркировка, структура, свойства сплавов
15.При каких условиях охлаждения формируется видманштеттова структура литых доэвтектоидных сталей?
16.Как влияет С и примеси Mn, Si на свойства углеродистых сталей?
17.Как влияет S и P на свойства углеродистых сталей?
18.Приведите классификацию углеродистых сталей по металлургическому качеству.
19.Охарактеризуйте виды термической обработки.
20.С какой целью применяется отжиг первого рода?
21.Что такое пережог стали?
22.Назовите особенности мартенситного превращения в сталях.
23.Как выбирается режим закалки в доэвтектоидных сталях?
24.Как выбирается режим закалки в заэвтектоидных сталях?
25.Назовите способы закалки сталей.
26.Какие превращения протекают в закаленных сталях при нагреве?
27.Укажите виды отпуска.
28.С какой целью проводится цементация сталей?
29.Какие свойства имеют стали после азотирования?
30.Назовите преимущества ионного азотирования.
31.Чем отличается нитроцементация от цианирования?
32.Опишите технологию диффузионного насыщения сплавов.
33.Какую структуру после отжига имеет эвтектоидная низколегированная сталь?
34.Приведите классификацию конструкционных сталей по назначению.
35.Как изменяется положение критических точек в стали при растворении никеля и марганца?
36.Какой легирующий элемент повышает прокаливаемость и увеличивает вязкость стали?
37.Как влияют карбидообразующие элементы на кинетику распада ау-
стенита?
38.Какое количество углерода содержится в улучшаемых сталях?
39.Какие свойства приобретает конструкционная улучшаемая сталь после закалки и высокого отпуска?
40.Как изменяется количество остаточного аустенита при закалке стали, которая легирована элементами, понижающими точки мартенситного превращения?
41.Какая термическая обработка позволяет получить наибольшие упругие свойства у пружин, изготовленных из стали 60СГ?
42.Опишите структуру цементованной поверхности стальной детали после закалки и низкого отпуска?
43.Охарактеризуйте окончательную термическую обработку для стали ШХ15.
44.Укажите наиболее опасный вид коррозионного повреждения.
45.Какие стали называются ферритными?
46.Какие легирующие элементы увеличивают жаростойкость стали?
Материаловедение. Учеб. пособие |
-283- |
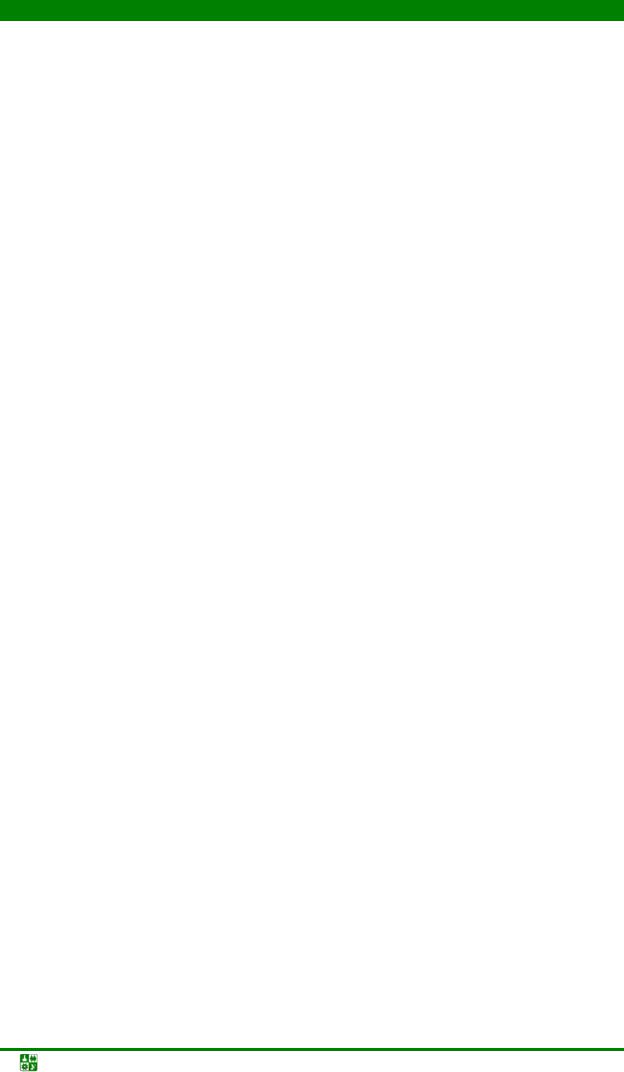
РАЗДЕЛ II. МАТЕРИАЛОВЕДЕНИЕ СТАЛЕЙ И ЧУГУНОВ
Глава 4. Стали, сплавы системы железо–углерод. Маркировка, структура, свойства сплавов
47.При каком содержании хрома сталь становится коррозионностойкой во многих агрессивных средах?
48.Для чего вводят титан в сталь 12Х18Н10Т?
49.Почему из углеродистых сталей изготавливают инструмент небольшого диаметра?
50.Что такое теплостойкость сталей?
51.Какие стали обладают максимальной теплостойкостью?
52.Как выбирается температура закалки в быстрорежущих сталях?
53.Какие процессы происходят при отпуске быстрорежущих сталей?
54.Назовите основные свойства, которыми должны обладать стали для измерительного инструмента.
Глава5. Чугуны, сплавысистемыжелезо–углерод
5.1. Фазовыеиструктурныепревращениявбелыхчугунах
Чугуны относятся к материалам с высокими литейными свойствами и являются наиболее распространенными сплавами для фасонного литья. У чугунов более низкая, чем у сталей, температура плавления, высокая жидкотекучесть, малая усадка, высокое сопротивление образованию усадочных трещин, что и позволяет отливать детали сложной формы.
Промышленные чугуны содержат 2,0–4,5 % С, 1,0–3,5 % Si, 0,5–1,0 % Mn,
до 0,3 % P, и до 0,2 % S. Содержание кремния в чугунах соизмеримо с содержанием углерода и поэтому кремний является не примесью, а легирующим элементом чугуна.
В зависимости от назначения чугуны подразделяются на чугуны общего и специального применения. К чугунам общего назначения относятся: серые, высокопрочные, ковкие и чугуны с вермикулярным графитом. Чугуны специального назначения: легированные, антифрикционные чугуны. При легировании повышаются механические и специальные свойства чугунов. Легированные чугуны применяют в качестве износостойких, коррозионностойких, жаропрочных, жаростойких материалов.
К высокоуглеродистым сплавам системы железо–углерод относятся белые чугуны. В белых чугунах присутствует С (графит) не в свободном состоянии, а только в виде соединения Fe3C– цементита.
Фазовое состояние белых чугунов описывает метастабильная диаграмма железо–углерод в области концентраций углерода от 2 до 6,67 % (см. рис. 4.2). Чугун с содержанием углерода 4,3 % называется эвтектическим; если в нем содержится углерода более 4,3 % – заэвтектическим, а если менее 4,3 % – доэвтектическим. Структура эвтектического чугуна при комнатной температуре – колонии ледебурита. На кривой охлаждения такого чугуна имеются две критические точки. Формирование структуры чугуна можно описать структурной цепочкой (табл. 5.1).
Материаловедение. Учеб. пособие |
-284- |
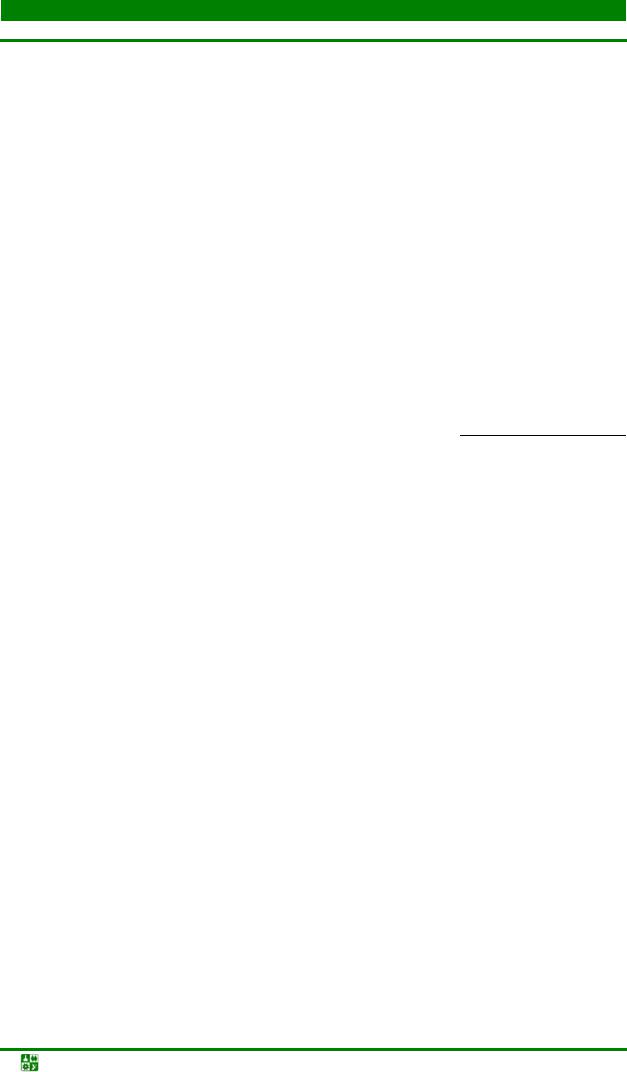
РАЗДЕЛ II. МАТЕРИАЛОВЕДЕНИЕ СТАЛЕЙ И ЧУГУНОВ
Глава 5. Чугуны, сплавы системы железо–углерод
При охлаждении жидкого чугуна эвтектического состава до точки С жидкий раствор, являющийся ненасыщенным по обоим компонентам, по достижении температуры 1 147 °С становится насыщенным, а при последующем переохлаждении – пересыщенным как по железу, так и по углероду. В связи с этим при переохлаждении ниже точки С будет идти одновременная кристаллизация аустенита и цементита в виде взаимно прорастающих и разветвляющихся кристаллов с характерным регулярным строением, основу которого составляет цементитный кристалл, пронизанный ветвями аустенита. Такая эвтектическая структура (рис. 5.1) носит название ледебурит.
Таблица 5.1
Схема фазовых и структурных превращений в эвтектическом чугуне с содержанием 4,3 % С
Исходное состояние системы |
|
Условия развития превращения |
||||
t = const в точке С |
t = const на линии PSK |
|||||
|
|
|||||
Фазовый состав |
L |
→ |
(γ + Fe3C)э |
→ |
[(α + Fe3C)э + Fe3C]э |
|
Структура |
Ж |
→ |
Л |
→ |
Л |
Переохлаждение такой структуры ниже 727 °С приводит к распаду аустенита в составе ледебурита на перлит. Поэтому, после охлаждения ниже указанной температуры ледебурит оказывается состоящим из перлита и цементита с прежним внешним эвтектическим строением, сформировавшимся при кристаллизации.
Ледебурит в чугуне может иметь пластинчатое (пакетное) или, наиболее часто, сотовое строение.
Рис. 5.1. Структура эвтектического чугуна (ледебурит)
Вплоскости шлифа сечения ветвей аустенитного (перлитного) дендрита часто выглядят как изолированные участки перлита в цементитной матрице.
Вряде случаев эвтектические колонии ледебурита на периферии имеют весьма грубое строение, так что распавшийся аустенит кажется обособленным от эвтектики и его можно принять ошибочно за первичные выделения аустенита, как в доэвтектических чугунах.
Доэвтектический чугун (сплав с содержанием углерода от 2,14 до 4,3 %) имеет следующую структуру: перлит, ледебурит (перлит + цементит) и вторичный цементит. Формирование структуры доэвтектического чугуна определяется процессами кристаллизации (табл. 5.2).
Материаловедение. Учеб. пособие |
-285- |

РАЗДЕЛ II. МАТЕРИАЛОВЕДЕНИЕ СТАЛЕЙ И ЧУГУНОВ
Глава 5. Чугуны, сплавы системы железо–углерод
В доэвтектических чугунах из жидкой фазы по механизму кристаллизации твердых растворов выделяется в дендритной форме первичный аустенит. Это приводит к обогащению оставшейся жидкости углеродом, концентрация которого в ней при температуре 1 147 °С достигает 4,3 %.
Таблица 5.2
Схема фазовых и структурных превращений в доэвтектическом чугуне с содержанием 2,14–4,3 % С
Условия развития |
t ниже |
t = const |
|
t ниже |
|
t = const |
|||
превращения |
линии BС |
на линии ECF |
линии ECF |
|
на линии PSK |
||||
Фазовый |
L |
→ |
L |
→ |
(γ + Fe3C)э |
→ |
(γ + Fe3C)э |
→ |
[(α + Fe3C)э + Fe3C]э |
состав |
|
|
+ |
|
+ |
|
+ |
|
+ |
|
|
|
γ |
|
γ |
→ |
γ |
→ |
(α + Fe3C)э |
|
|
|
|
|
|
|
+ |
|
+ |
|
|
|
|
|
|
|
Fe3Cп |
→ |
Fe3Cп |
Структура |
Ж |
→ |
Ж +А |
→ |
Л + А |
→ |
Л + А + Цп |
→ |
Л + П + Цп |
Жидкость будет предельно насыщена железом и углеродом аналогично эвтектическому чугуну. Дальнейшее переохлаждение сплава ниже 1 147 °С вызывает развитие эвтектической кристаллизации жидкости по реакции с образованием ледебурита: LС (γЕ + Fe3C)э.
При охлаждении в интервале температур 1 147–727 °С аустенит обедняется углеродом и его состав изменяется по линии ES, что приводит к выделению из аустенита вторичного цементита. При переохлаждении ниже 727 °С аустенит состава точки S распадается на эвтектоидную смесь (перлит), которая имеет внешние очертания аустенита. Перлит образуется как в дендритах аустенита, так и в эвтектическом аустените, входящем в состав ледебурита. Чем больше в чугуне углерода, тем меньше в его структуре перлита и больше ледебурита (рис. 5.2).
Вторичный цементит, выделяющийся по границам зерен первичного аустенита, сливается с цементитом ледебурита. Под микроскопом можно увидеть только иглы вторичного цементита, пронизывающие распавшийся аустенит (перлит).
Итак, в доэвтектических белых чугунах можно увидеть три структурные составляющие – (α + Fe3C)э – перлит (распавшийся первичный аустенит), Fe3Cп – вторичный цементит и [(α + Fe3C)э + Fe3C]э – превращенный ледебурит. Причем аустенит, который входит в состав ледебурита так же, как и первичный аустенит, выделяет вторичный цементит и затем образует эвтектоид.
Материаловедение. Учеб. пособие |
-286- |
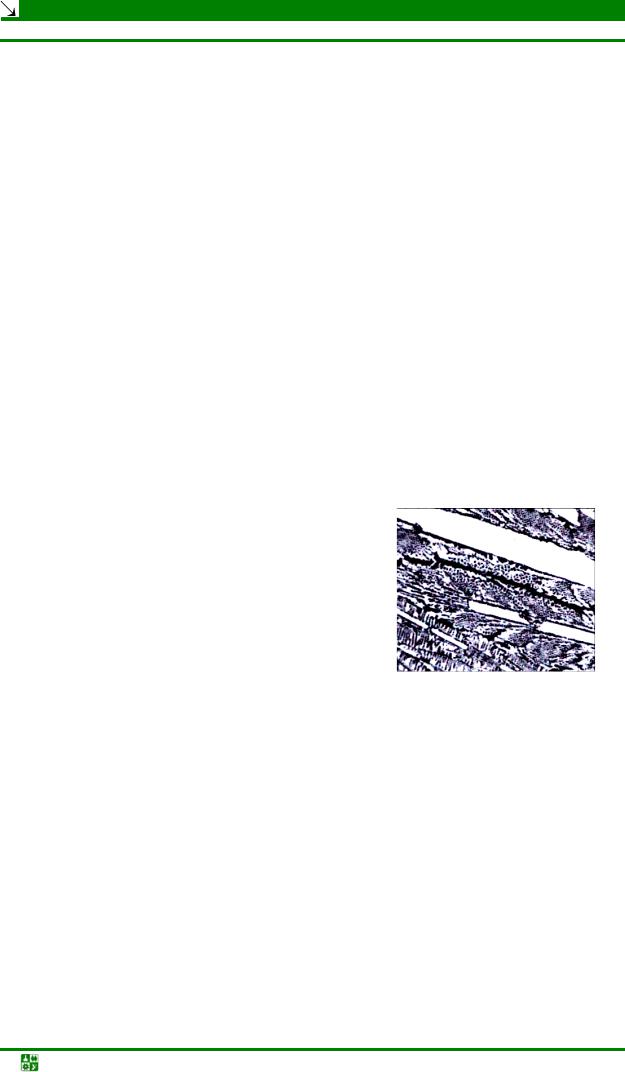
РАЗДЕЛ II. МАТЕРИАЛОВЕДЕНИЕ СТАЛЕЙ И ЧУГУНОВ
Глава 5. Чугуны, сплавы системы железо–углерод
Внутри округлых мелких частиц распавшегося ледебуритного аустенита при малых увеличениях трудно рассмотреть эвтектоидные колонии и выделение вторичного цементита. В микроскопе они представляют собой хорошо травящиеся темные включения. Структуру и кривую охлаждения, подобную данному сплаву, имеют чугуны с содержанием углерода от 2,14 до 4,3 %.
Заэвтектический чугун (4,3 < С < 6,67 %) имеет следующую структуру: пластины первичного цементита и колонии превращенного ледебурита. Схема формирования структуры включает, как и в предыдущих случаях, процессы кристаллизации и фазовых превращений в твердом состоянии (табл. 5.3).
Таблица 5.3
Схема фазовых и структурных превращений в заэвтектическом чугуне с содержанием 4,3 – 6,67 % С
Условия развития |
|
|
t ниже |
t = const |
|
t = const |
|||
превращения |
|
|
линии СD |
на линии ECF |
|
на линии PSK |
|||
Фазовый состав |
L |
|
→ |
L |
→ |
|
(γ + Fe3C)э |
→ |
[(α + Fe3C)э + Fe3C]э |
|
|
|
|
+ |
|
|
+ |
|
+ |
|
|
|
|
Fe3CI |
→ |
|
Fe3CI |
→ |
Fe3CI |
Структура |
Ж |
|
→ |
Ж + ЦI |
|
Л + ЦI |
→ |
Л + ЦI |
|
Процесс затвердевания заэвтектиче- |
|
|
|
||||||
ского чугуна начинается с выделения из |
|
|
|
||||||
расплава кристаллов первичного цементи- |
|
|
|
||||||
та в виде плоских дендритов, дающих в |
|
|
|
||||||
сечении шлифа вытянутые полоски, похо- |
|
|
|
||||||
жие на иглы (рис. 5.3). |
|
|
|
|
|
|
|
||
Первичная кристаллизация заканчи- |
|
|
|
||||||
вается образованием ледебурита. Далее |
|
|
|
||||||
идут такие же процессы, как и в доэвтек- |
Рис. 5.3. Структура заэвтектического |
||||||||
тическом чугуне. |
Фазовый |
состав белых |
|
белого чугуна |
чугунов при комнатной температуре такой же, как и у отожженных углеродистых сталей: феррит и цементит.
5.2. Эвтектическаякристаллизация
Эвтектическая кристаллизация – типичное превращение для высокоуглеродистых сплавов на основе железа – чугунов. Эвтектическая кристаллизация происходит как в стабильной, так и в метастабильной системе железо– углерод.
Наиболее полно описывает механизм и кинетику эвтектического превращения кристаллизация ледебурита, которая в чистом виде происходит в эвтектическом белом чугуне при содержании углерода 4,3 %. Температура
Материаловедение. Учеб. пособие |
-287- |
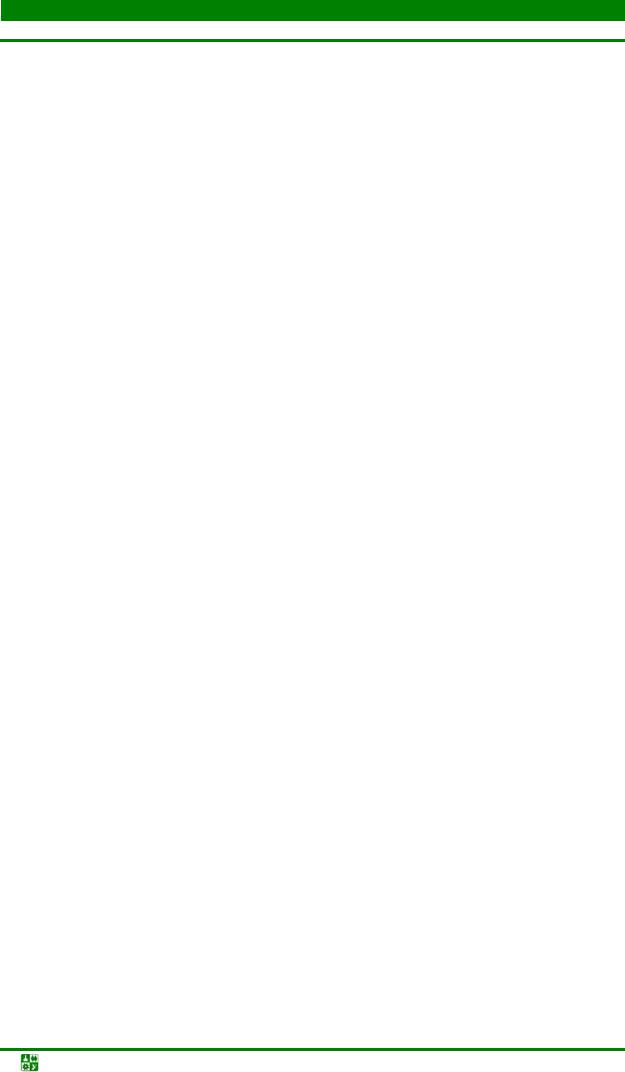
РАЗДЕЛ II. МАТЕРИАЛОВЕДЕНИЕ СТАЛЕЙ И ЧУГУНОВ
Глава 5. Чугуны, сплавы системы железо–углерод
эвтектической кристаллизации 1 147 °С, что соответствует эвтектической точке С.
Эвтектическая кристаллизация заключается в одновременном выделении из переохлажденной жидкой фазы двух разнородных твердых фаз в изотермических условиях. В результате эвтектической кристаллизации образуется специфичная структурная составляющая – эвтектика, представляющая собой смесь регулярно чередующихся высокодисперсных частиц двух (или более) фаз, образовавшихся в результате диффузионного разделения переохлажденной жидкости.
В составе ледебурита такими составляющими являются аустенит состава точки Е и цементит состава точки F. В соответствии с диаграммой железо– углерод эвтектика образуется при кристаллизации сплавов, ограниченных протяженностью эвтектической линии ECF (E'C'F' – в стабильной системе).
Эвтектическое превращение в двухфазной системе является одним из случаев трехфазного равновесия. Число степеней свободы, отвечающее этому превращению, равно нулю. Это означает, что на термических кривых охлаждения и нагрева сплавов должна выявляться изотермическая ступенька, связанная с выделением (поглощением) скрытой теплоты эвтектической реакции. Эти ступеньки, соответствующие изотермическим условиям развития превращения, можно наблюдать на термических кривых, отвечающих лишь двойным железоуглеродистым сплавам. В реальных чугунах, содержащих дополнительно, кроме основных компонентов, постоянные примеси: кремний и марганец, эвтектическая кристаллизация происходит в интервале температур.
Рассмотрим кристаллизацию ледебурита (рис. 5.4). Жидкий сплав эвтектического состава при температуре эвтектической точки С получает значение термодинамического потенциала, отвечающее равновесию этой жидкости с аустенитом и цементитом. Прямая, соединяющая значения минимума свободной энергии аустенита и цементита, одновременно является и касательной к линии изменения свободной энергии жидкости.
При переохлаждении до температуры точки а термодинамический потенциал жидкости увеличивается более значительно, чем смеси γ + Fe3C, в связи с чем появляется термодинамический стимул превращения F.
Для развития эвтектической кристаллизации, кроме того, необходимы флуктуации концентраций, которые также появляются в жидкости, поскольку в этих условиях жидкость оказывается пересыщенной как железом, так и углеродом. Таким образом, в условиях переохлаждения оказывается возможным одновременное выделение и фазы, обогащенной железом (аустенита состава точки Е), и фазы, богатой углеродом (цементита состава точки F).
Переохлаждение сплава ниже 1 147 °С вызывает развитие эвтектической кристаллизации жидкости по реакции
LС (γЕ + Fe3C)э.
Степень переохлаждения жидкости должна быть такой, чтобы возникающая разница термодинамических потенциалов жидкости и смеси твердых фаз была бы достаточной для образования поверхностей раздела формирую-
Материаловедение. Учеб. пособие |
-288- |
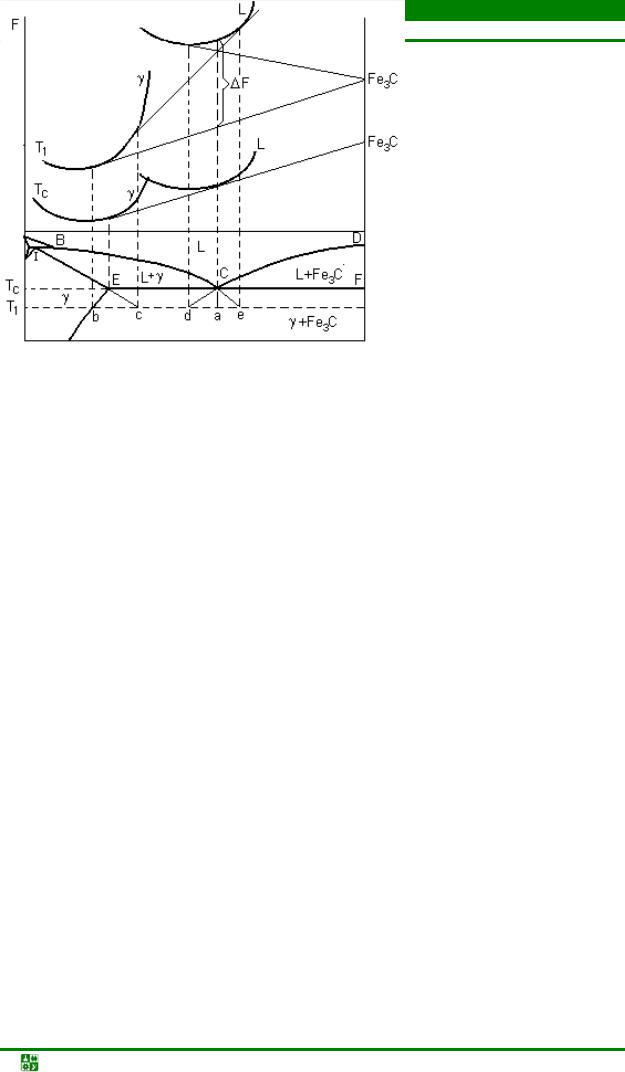
РАЗДЕЛ II. МАТЕРИАЛОВЕДЕНИЕ СТАЛЕЙ И ЧУГУНОВ
Глава 5. Чугуны, сплавы системы железо–углерод
щихся фаз с жидкостью. Причем чем больше величина термодинамического стимула кристаллизации (больше степень переохлаждения), тем интенсивнее развивается эвтектическая кристаллизация.
Рис. 5.4. Кривые изменения свободной энергии фаз при эвтектической кристаллизации
При малых степенях переохлаждения кристаллы аустенита и цементита могут зарождаться и расти раздельно. В результате будет образовываться структура грубого конгломерата, не являющаяся, по существу, типичной структурой эвтектического чугуна.
Наиболее характерным признаком эвтектической кристаллизации является одновременный рост аустенитных и цементитных кристаллов, образующих в большинстве случаев своеобразную колонию сотового строения. В общем случае зарождение эвтектических фаз неодновременное, однако зарождение частицы одной из фаз (цементита) приводит к быстрому обеднению C и обогащению Fe жидкости, окружающей эту частицу. Это способствует появлению на границе растущего кристалла (цементита) зародыша новой фазы (аустенита). Кристаллы новой фазы (аустенита), образовавшись, приостанавливают рост первой фазы (цементита) и растут сами, обогащая приграничную область жидкости компонентом (углеродом), необходимым для зарождения нового слоя первой фазы (цементита). Таким образом, процесс повторяется, способствуя образованию пакета тонких цементитных пластин, разделенных аустенитом.
Такой пластинчатый ледебурит является типичным зародышем, на котором формируются колонии сотового ледебурита. Зарождение сотового ледебурита связано с появлением неровностей на поверхности пластины аустенита. В результате чего в жидкости перед фронтом кристаллизации начинается перераспределение углерода, который скапливается преимущественно в
Материаловедение. Учеб. пособие |
-289- |
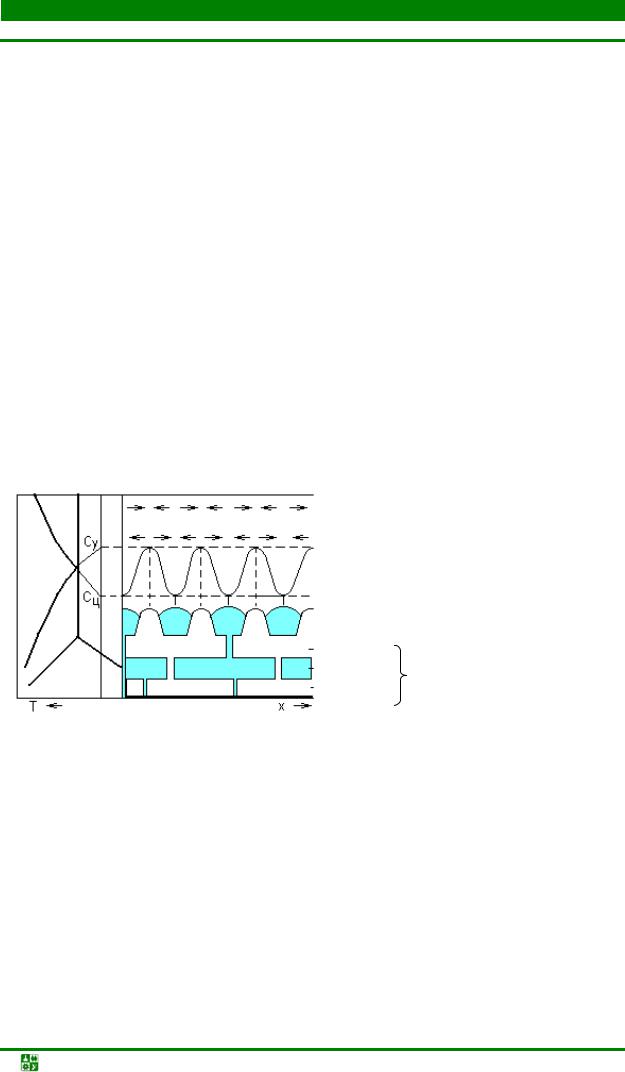
РАЗДЕЛ II. МАТЕРИАЛОВЕДЕНИЕ СТАЛЕЙ И ЧУГУНОВ
Глава 5. Чугуны, сплавы системы железо–углерод
ямках неровностей на поверхности аустенитной пластины. При росте сотового ледебурита создается двухфазный фронт кристаллизации, продвижение которого в жидкость происходит благодаря диффузионному разделению жидкости перед фронтом растущей колонии (рис. 5.5).
Диффузионное разделение жидкости оказывается возможным, в связи с установлением перед фронтом растущей двухфазной колонии не одинаковой равновесной концентрации жидкости в контакте с различными частицами кристаллизующихся фаз. Равновесные концентрации жидкости на межфазных границах L + γ и L + Fe3C в условиях переохлаждения описываются точками пересечения продолжений линий ликвидус с изотермой, соответствующей данной степени переохлаждения, соответственно, Сγ и Сц, где Сγ > Сц. В связи с этим в жидкости происходит разделительная диффузия, приводящая к установлению равновесных концентраций на всех межфазных границах перед фронтом растущей колонии. Такое установление равновесных концентраций происходит в результате взаимодействия растущих кристаллов с прилежащими к ним тонкими слоями жидкости. При этом жидкость около аустенитного выступа получает равновесное содержание углерода Сγ более высокое по сравнению с жидкостью на межфазной границе с цементитом Сц
(рис. 5.5).
Направление диффузии железа перед фронтом растущей колонии
Направление диффузии углерода перед фронтом растущей колонии
Распределение равновесной концентрации углерода перед фронтом растущей колонии сотового ледебурита
Аустенит |
зародыш ледебурита |
|
Цементит |
||
(пластинчатый пакет) |
||
Аустенит |
||
|
Рис. 5.5. Описание диффузионного разделения жидкости при росте сотовой колонии ледебурита
Наличие градиентного распределение железа и углерода в жидкости является движущим фактором выравнивающей диффузии. В результате разницы концентраций углерод в жидкости непрерывно перемещается от аустенитных выступов к цементитным, обеспечивая рост последних.
Железо же, наоборот, устремляется от цементитных выступов к аустенитным, также обеспечивая продольный рост аустенитных стержней. Колонии сотового ледебурита растут описанным образом в продольном и поперечном направлениях до столкновения с другими растущими колониями.
Материаловедение. Учеб. пособие |
-290- |
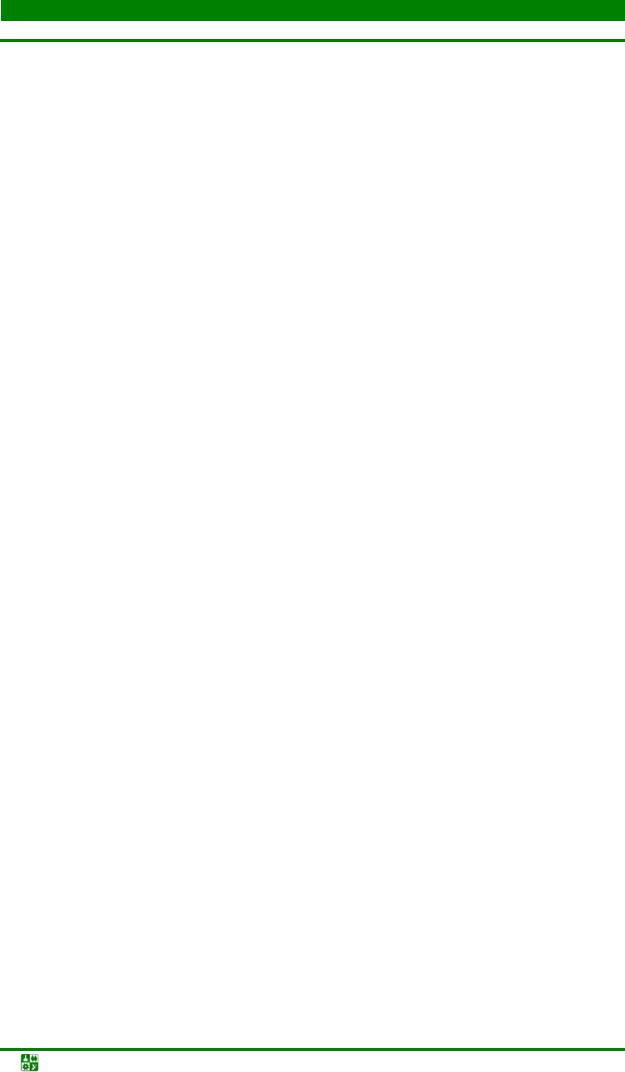
РАЗДЕЛ II. МАТЕРИАЛОВЕДЕНИЕ СТАЛЕЙ И ЧУГУНОВ
Глава 5. Чугуны, сплавы системы железо–углерод
Увеличение степени переохлаждения при кристаллизации эвтектики увеличивает термодинамический стимул превращения, в связи с чем образование зародышей той или иной фаз облегчается.
Кроме того, исследуя диффузионные процессы, развитие которых приводит к перемещению межфазных границ и зарождению чередующихся слоев разных фаз, составляющих эвтектику, при образовании эвтектических колоний, можно показать, что эти процессы зависят от интенсивности обменной диффузии на межфазных границах и гомогенизирующей диффузии в жидкости.
Первый процесс, например, при росте аустенитного зародыша приводит к перераспределению избыточного углерода, появляющегося при замене жидкого раствора, имеющего состав 4,3 % С, на аустенит, содержащий всего 2,14 % С, к границе раздела фаз γ-L, непрерывно обогащая жидкость в тонком слое около растущей аустенитной пластинки, создает в жидкости градиент концентрации между этим слоем и остальным объемом жидкости. Этот градиент концентрации углерода становится стимулом развития гомогенизирующей диффузии, стремящейся уменьшить концентрацию углерода в слое вблизи межфазной границы за счет перераспределения его в удаленные от границы объемы исходной жидкости, уменьшая вероятность образования цементитной пластинки на рассматриваемой границе.
Интенсивность обменной диффузии на границе раздела фаз в связи с малой протяженностью диффузионных путей очень велика и практически не зависит от степени переохлаждения. Выравнивающая же диффузия есть диффузия на большие расстояния, в связи с чем она протекает тем интенсивнее, чем выше температура превращения (чем меньше степень переохлаждения). Поэтому длительность периода достижения флуктуации концентраций на межфазной границе γ–L, необходимой для появления зародыша частицы новой фазы (цементита), будет зависеть практически только от интенсивности выравнивающей диффузии в жидкости и, следовательно, от степени переохлаждения.
При малой степени переохлаждения этот период оказывается значительным, и толщина первично растущей аустенитной частицы увеличивается. С увеличением степени переохлаждения длительность периода образования необходимой флуктуации уменьшается, что приводит к появлению зародыша новой (цементитной) пластинки в тот момент, когда растущая аустенитная пластинка имеет еще малую толщину. Чем больше степень переохлаждения, тем более тонкими оказываются частицы в составе колонии, тем выше степень дисперсности образующейся эвтектической колонии.
Вдоэвтектических и заэвтектических сплавах зарождение эвтектических колоний может начинаться на выпавших ранее из жидкости первичных кристаллах аустенита или цементита.
Втом и другом случае продолжение роста первичных кристаллов в условиях переохлаждения ниже эвтектической температуры приводит к появлению вокруг растущих кристаллов избыточных фаз тонкого слоя жидкости, обогащенной (или обедненной) по содержанию углерода, в которой в сле-
Материаловедение. Учеб. пособие |
-291- |
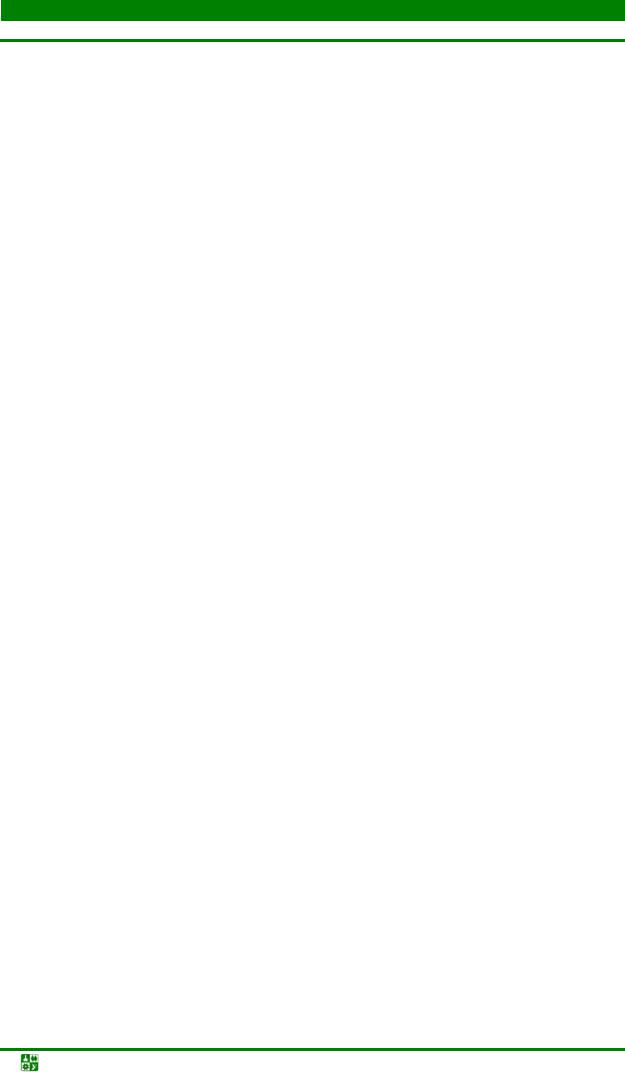
РАЗДЕЛ II. МАТЕРИАЛОВЕДЕНИЕ СТАЛЕЙ И ЧУГУНОВ
Глава 5. Чугуны, сплавы системы железо–углерод
дующий момент времени формируется зародыш цементита (или, соответственно, аустенита), окружающий по всей поверхности первичные кристаллы.
Первичные кристаллы теперь уже не могут далее расти, а образовавшийся слой новой фазы становится своеобразным зародышем эвтектических колоний. Зарождение и рост эвтектических колоний сотового ледебурита на этом слое происходит аналогично вышеописанному механизму при зарождении таких колоний на кристаллах пластинчатого ледебурита.
5.3. Серыечугуны
Серые литейные чугуны получают при меньшей скорости кристаллизации, чем белые чугуны, поэтому процесс формирования их структуры описывается стабильной диаграммой состояния железо–углерод (рис. 4.3, рис. 4.4), где пунктирные линии показывают фазовые равновесия с графитом. Диаграмма железо-углерод, точки, линии, фазовые и структурные составляющие описаны ранее.
В сером чугуне жидкость состава точки С' кристаллизуется в виде эвтектики, состоящей из аустенита и графита:
LС' (γЕ' + Г)э.
Эвтектические колонии растут как бикристалл, состоящий из графита (ведущая фаза), который растет в виде разветвленного крабовидного кристалла, и аустенита, отлагающегося на поверхности графитового скелета. На шлифе сечения разветвленных крабовидных кристаллов графита видны как изолированные включения в аустенитной матрице (рис. 5.6).
В сером чугуне жидкость состава точки С' кристаллизуется в виде эвтектики, состоящей из аустенита и графита:
LС' (γЕ' + Г)э.
Эвтектическая кристаллизация в стабильной системе в основном начинается с кристаллизации графитных включений. Эти включения растут, разветвляясь в процессе кристаллизации. Затем на отдельных участках поверхности графита появляются зародыши аустенита, которые растут, заполняя пространства между растущими графитными включениями.
Чем больше степень переохлаждения, тем больше разветвляются графитные включения и тем они оказываются тоньше. Чугун с такой структурой обладает пониженными механическими свойствами, поскольку разветвленные включения графита играют роль надрезов при разрушении образца или изделия.
Материаловедение. Учеб. пособие |
-292- |
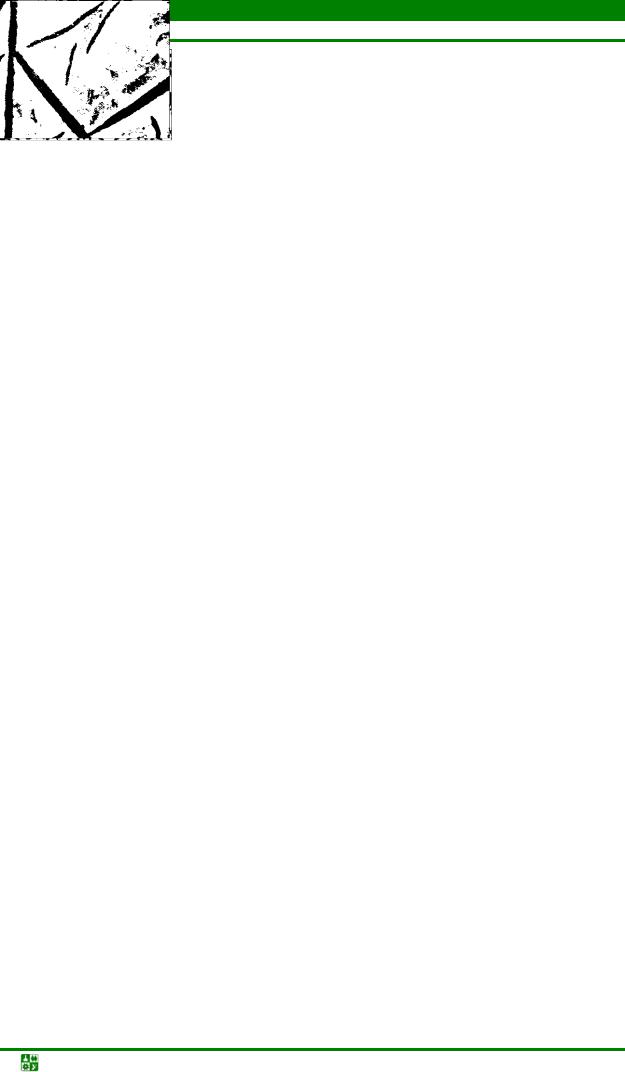
РАЗДЕЛ II. МАТЕРИАЛОВЕДЕНИЕ СТАЛЕЙ И ЧУГУНОВ
Глава 5. Чугуны, сплавы системы железо–углерод
а |
б |
в |
Рис. 5.6. Форма и расположение графита в структуре серых чугунов: а – эвтектическом; б – доэвтектическом; в – заэвтектическом
При определенных условиях кристаллизации (например, после модифицирования жидкого чугуна магнием) графит кристаллизуется в виде сферолитных включений. Аустенит в этом случае окружает зародыш сферолитного графита со всех сторон, и дальнейший рост графитного включения в этом случае происходит путем диффузионного переноса атомов углерода от жидкости к графитному зародышу через слой окружающего его аустенита. В этом случае образуется чугун с шаровидным графитом, обладающий повышенным комплексом механических свойств.
Формы и размеры таких выделений зависят от формы и разветвленности графитного скелета эвтектической колонии. С изменением условий кристаллизации изменяется форма графита. На шлифе он выглядит в виде грубых или дисперсных изогнутых прожилок, завихренных включений, точечных выделений. Т.к. графит мягкий, то он плохо полируется и рассеивает свет, поэтому выглядит в виде темных включений на светлом фоне нетравленого шлифа. По нетравленому шлифу оценивают форму и дисперсность графита, которые сильно влияют на механические свойства серого чугуна. В доэвтектических серых чугунах (сплавы с содержанием углерода от 2,03 до 4,25 %) первично кристаллизуются дендриты аустенита (рис. 5.6, б), а затем – эвтектика аустенит – графит. Цепочки фазовых и структурных превращений, протекающих в стабильной системе, можно проанализировать самостоятельно, опираясь на аналогичные методы, рассмотренные выше для метастабильной диаграммы железо–цементит.
В заэвтектических серых чугунах (сплавы с содержанием углерода более 4,25 %) первично кристаллизуется графит. Он, как и эвтектический, растет в форме разветвленных кристаллов, которые видны на шлифе в виде грубых кристаллов (рис. 5.6, в). Оставшаяся жидкость кристаллизуется как эвтектическая. Кристаллы первичного графита более грубые по сравнению с эвтектическими. После завершения кристаллизации в твердом состоянии аустенит изменяет свой состав по линии E'S' и из него выделяется вторичный графит, осаждающийся на ранее образовавшихся первичных и эвтектических кристаллах графита, что практически не изменяет структуры чугуна.
Переохлаждение аустенита состава точки S' (0,69 % С) ниже эвтектоидной температуры 738 °С вызывает развитие эвтектоидной реакции с образованием феррито-графитной смеси:
Материаловедение. Учеб. пособие |
-293- |
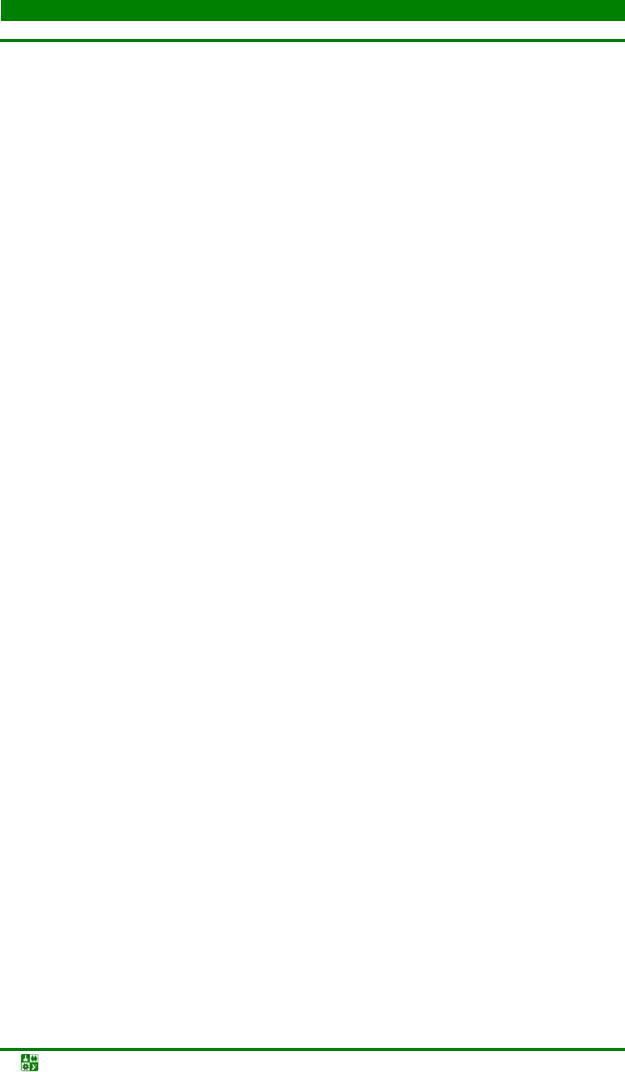
РАЗДЕЛ II. МАТЕРИАЛОВЕДЕНИЕ СТАЛЕЙ И ЧУГУНОВ
Глава 5. Чугуны, сплавы системы железо–углерод
γS' (αP' + Г)э.
Феррито-графитная смесь, образующаяся по эвтектоидной реакции, характеризуется более тонким строением. При очень малых степенях переохлаждения эвтектоидный графит может отлагаться на ранее образовавшихся первичных или эвтектических кристаллах графита, аналогично вторичному, принципиально не изменяя структуру чугуна. По структуре трудно подразделить серые чугуны на доэвтектические, эвтектические и заэвтектические.
Серые чугуны подразделяются по микроструктуре металлической основы в зависимости от полноты графитизации, которую оценивают по количеству свободного выделившегося (не связанного) углерода (рис. 5.7). Если графитизация в твердом состоянии прошла полностью, то чугун содержит две фазовые составляющие – графит и феррит. Такой чугун называют серым
чугуном на ферритной основе.
а |
б |
в |
Рис. 5.7. Серый чугун на различной металлической основе: а – ферритный; б – перлитный; в – феррито-перлитный
Если эвтектоидный распад аустенита прошел не в соответствии со стабильной диаграммой (γS′ (αP' + Г)э), а в соответствии с метастабильной (γS (αP + Fe3C)э), то структура чугуна состоит из графита и перлита. Чугун с такой структурой называют серым чугуном на перлитной основе. Увеличение доли химически связанного углерода в чугуне вызывает рост его прочностных свойств, уменьшение пластичности. Если при кристаллизации серого чугуна аустенит частично распадается по эвтектоидной реакции на феррит и графит, а частично – на феррит и цементит, т.е. перлит, то чугун содержит графит, феррит и перлит. Такой чугун называют серым чугуном на ферритоперлитной основе. Полнота графитизации зависит от многих факторов, но прежде всего от скорости охлаждения и состава сплава. При быстром охлаждении кинетически более выгодно образование цементита, а не графита. С уменьшением скорости охлаждения возрастает степень графитизации. Кремний в чугуне способствует графитизации, аналогично замедлению охлаждения, а марганец затрудняет графитизацию.
Серые чугуны содержат повышенное количество фосфора, который увеличивает жидкотекучесть, дает тройную эвтектику (γ + Fe3C + Fe3P)э. В металлической основе серого чугуна фосфидная эвтектика (стадит) видна в виде светлых хорошо очерченных участков.
Материаловедение. Учеб. пособие |
-294- |
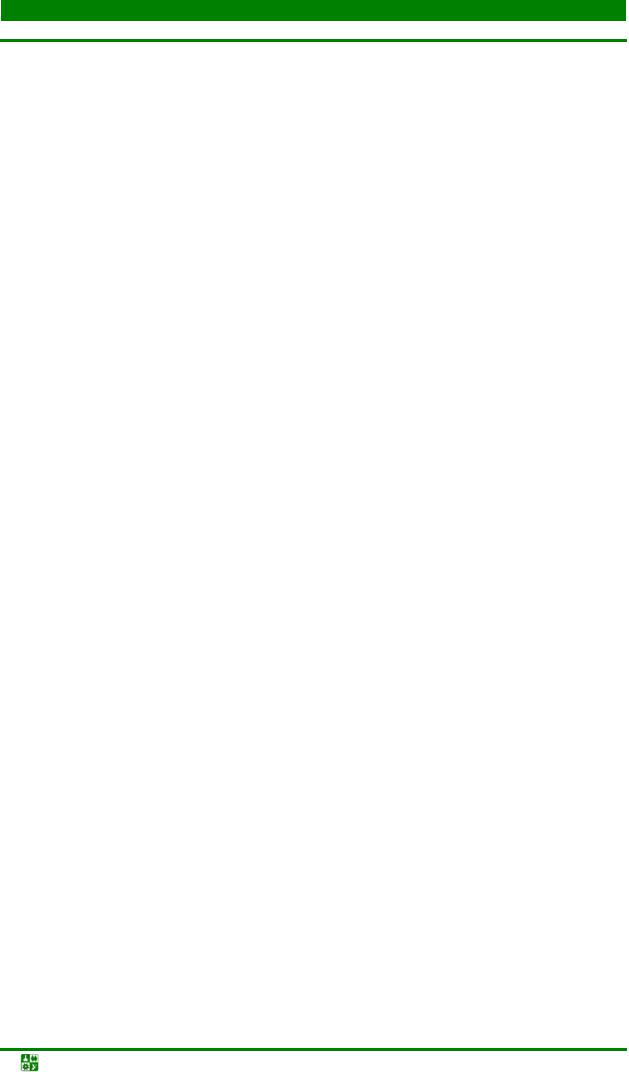
РАЗДЕЛ II. МАТЕРИАЛОВЕДЕНИЕ СТАЛЕЙ И ЧУГУНОВ
Глава 5. Чугуны, сплавы системы железо–углерод
Серые чугуны имеют невысокие механические свойства, потому что пластинчатые ответвления крабовидных образований графита действуют как надрезы в металлической основе.
Серые чугуны – это основная группа литейных материалов. Принадлежность чугуна к серому чугуну определяется пластинчатой формой графита. По ГОСТ 1412-85 – Чугун с пластинчатым графитом для отливок – определяются марки, механические свойства и химический состав серых чугунов. Для изготовления отливок предусматриваются следующие марки чугуна: СЧ
10, СЧ 15, СЧ 18, СЧ 20, СЧ 21, СЧ 24, СЧ 25, СЧ 30, СЧ 35. Условное обо-
значение марки включает буквы СЧ – серый чугун и цифровое обозначение величины минимального временного сопротивления при растяжении в МПа ×10-1. Например чугун СЧ10 имеет временное сопротивления при растяжении не менее 100 (10) МПа (кгс/мм2). Чугун СЧ 10 имеет ферритную, а чугун СЧ 35 – перлитную основу. Свойства серого чугуна приведены в табл. 5.4. Механические свойства чугуна зависят от толщины стенки отливки, с увеличением толщины стенки отливки уменьшается прочность и твердость серого чугуна.
Таблица 5.4
Ориентировочные данные о временном сопротивлении при растяжении в отливках разного сечения
|
|
Толщина стенки, мм |
|
Марка чугуна |
8 |
50 |
150 |
|
Временное сопро |
тивление при растяжени |
и, МПа, не менее |
СЧ 10 |
120 |
75 |
65 |
СЧ 25 |
270 |
180 |
150 |
СЧ 35 |
380 |
260 |
205 |
По действующему стандарту серые чугуны в зависимости от марки содержат углерода 2,9–3,7 %, кремния 1,2–2,6 %, марганца 0,5–1,1 %, фосфора до 0,3 % и серы до 0,15 %. Химический состав серого чугуна приведен в базе данных СЧ. Сера снижает прочность чугуна и поэтому является вредной примесью. Фосфор повышает жидкотекучесть чугуна, но может снижать прочность и ударную вязкость.
Основные области применения серого чугуна – станкостроение и тяжелое машиностроение, автомобильная промышленность и сельскохозяйственное машиностроение. Из чугуна изготавливают станины станков, корпусные детали, картеры, шкивы, крышки, санитарно-техническое оборудование.
5.4. Высокопрочные, свермикулярнымграфитомиковкиечугуны
Модифицирование серого чугуна магнием приводит к образованию глобулярного графита. В структуре чугуна наблюдается большое количество мелких округлых включений графита. Такой чугун называется высоко-
Материаловедение. Учеб. пособие |
-295- |
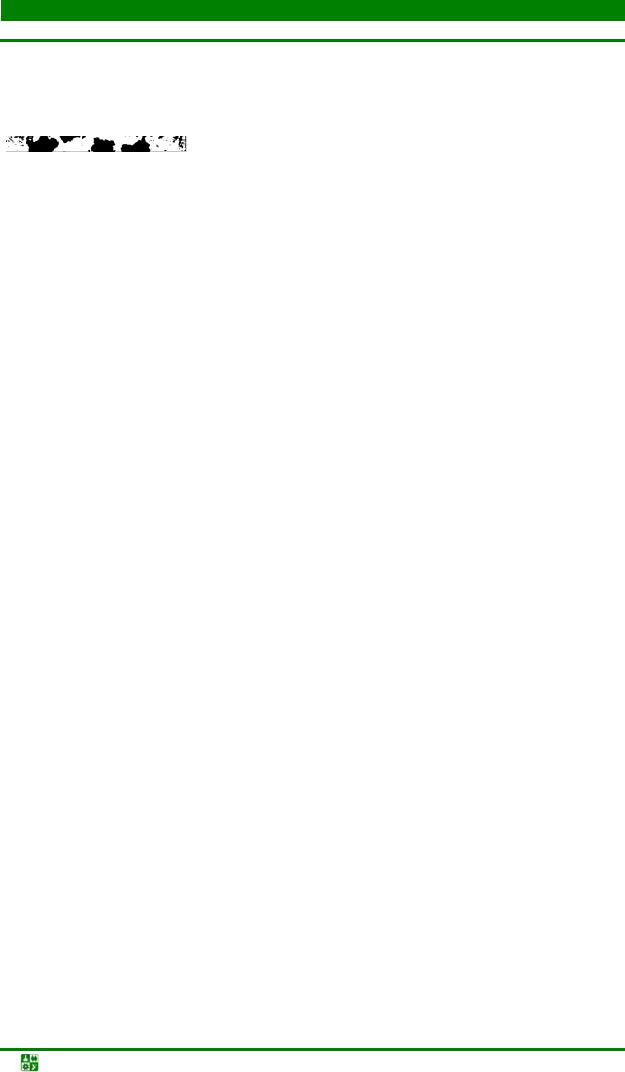
РАЗДЕЛ II. МАТЕРИАЛОВЕДЕНИЕ СТАЛЕЙ И ЧУГУНОВ
Глава 5. Чугуны, сплавы системы железо–углерод
прочным серым чугуном. Модифицирование повышает прочностные и особенно пластические свойства чугуна.
а |
б |
Рис. 5.8. Микроструктура ферритного ковкого (а) и феррито-перлитного высокопрочного (б) чугунов
Ковкий чугун получают путем отжига отливок из белого чугуна. При высоких температурах (1 000 °С) происходит переход неустойчивого цементита белого чугуна в графит. Такой графитизирующий отжиг идет путем растворения метастабильного цементита в аустените и одновременного выделения из аустенита более стабильного графита. Степень графитизации зависит от температуры отжига белого чугуна, времени выдержки, скорости охлаждения, состава исходного чугуна и других параметров. Чем больше время выдержки при отжиге и меньше скорость охлаждения, тем полнее идет графитизация. В зависимости от полноты графитизации, как и в серых чугунах, в ковких чугунах различают три основных типа их структур: ковкие чугуны на ферритной, феррито-перлитной и перлитной основах. От серых чугунов ковкие отличаются по микроструктуре – формой графита, и по механическим свойствам – более высокой прочностью и пластичностью (рис. 5.8).
Графит в ковких чугунах находится в форме компактных хлопьевидных включений – его называют углеродом отжига. Такой чугун имеет сравнительно однородную по сечению отливки ферритную структуру металлической основы. Реже он может иметь структуру феррито-перлитную или перлитную. Компактная форма графита придает чугуну повышенные механические свойства по сравнению с серым чугуном. Ковкий ферритный чугун мягче и пластичнее перлитного.
При отжиге белого чугуна образуется графит в благоприятной для механических свойств компактной, хлопьевидной форме. Относительное удлинение ковкого чугуна может достигать гарантированного уровня 10–12 %, у исходного белого чугуна не превышает 0,2 %, а у чугуна с пластинчатым графитом – 1 %. Механические свойства ковких чугунов приведены в табл. 5.5.
Материаловедение. Учеб. пособие |
-296- |
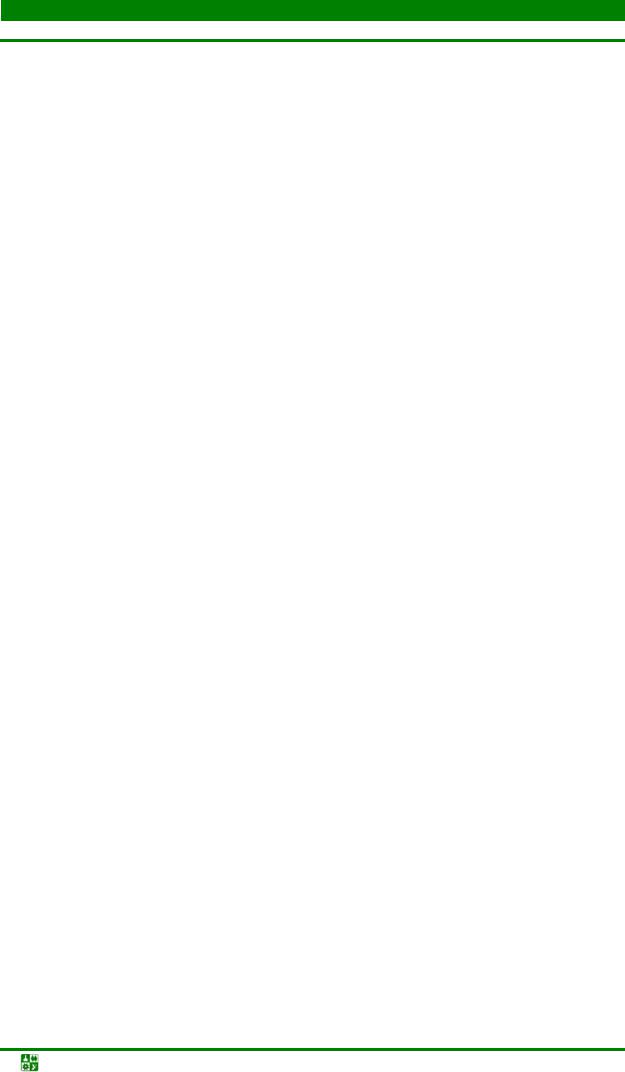
РАЗДЕЛ II. МАТЕРИАЛОВЕДЕНИЕ СТАЛЕЙ И ЧУГУНОВ
Глава 5. Чугуны, сплавы системы железо–углерод
Таблица 5.5
Механические свойства ковкого чугуна
(ГОСТ 1215-79)
Марка |
Временное сопротивление раз- |
Относительное удлине- |
Твердость |
чугуна |
рыву, МПа (кгс/мм2), не менее |
ние, %, не менее |
по Бринеллю НВ |
КЧ 30-6 |
294 (30) |
6 |
100–163 |
КЧ 37-12 |
362 (37) |
12 |
110–163 |
КЧ 45-7 |
441 (45) |
7 |
150–207 |
КЧ 60-3 |
588 (60) |
3 |
200–269 |
КЧ 80-1,5 |
784 (80) |
1,5 |
270–320 |
Белый чугун, предназначенный для отжига на ковкий, содержит
2,4–2,9 % С, 1,0–1,6 % Si, 0,3–1,0 % Mn, не более 0,18 % P и 0,20 % S. Со-
держание углерода и кремния в ковком чугуне должно быть меньше, чем в сером. В таком случае при кристаллизации обеспечивается формирование структуры белого чугуна по всему сечению отливки.
В соответствии с ГОСТ 1215-79 отливки из ковкого чугуна изготавливают следующих марок: КЧ 30-6, КЧ 33-8, КЧ 35-10, КЧ 37-12 ферритного класса с ферритной или феррито-перлитной металлической основой, КЧ 45-7,
КЧ 50-5, КЧ 55-4, КЧ 60-3, КЧ 65-3, КЧ 70-2, КЧ 80-1,5 перлитного класса.
Обозначение марки включает буквы КЧ – ковкий чугун и цифровые обозначения: величины минимального временного сопротивления при растяжении в кгс/мм2 (первые две цифры) и величины минимального относительного удлинения в % (последующие цифры).
При введении в чугун 0,05 % магния или церия графит чугуна кристаллизуется в шаровидной или близкой к ней формы. Такой чугун относят к модифицированному чугуну. Чугуны с шаровидным графитом называют высокопрочными. Высокопрочные чугуны маркируются следующим обра-
зом: ВЧ 35, ВЧ 40, ВЧ 45, ВЧ 50, ВЧ 60, ВЧ 70, ВЧ 80, ВЧ 100, ГОСТ 7293-85
– Чугун с шаровидным графитом для отливок. Обозначение марки включает буквы ВЧ – высокопрочный чугун и цифровое обозначения величины минимального временного сопротивления при растяжении в МПа ×10-1. Например, чугун ВЧ100 имеет временное сопротивления при растяжении не менее 1 000 (100) МПа (кгс/мм2).
Чугуны ВЧ35 и ВЧ 40 имеют ферритную, ВЧ 45 и ВЧ 50 – перлитоферритную, и ВЧ60, ВЧ 70, ВЧ 80 – перлитную металлическую основу. По ГОСТ 7293-85 в высокопрочном чугуне регламентируется временное сопротивление при растяжении, условный предел текучести отливок из чугуна, а также твердость и относительное удлинение (табл. 5.6).
Материаловедение. Учеб. пособие |
-297- |
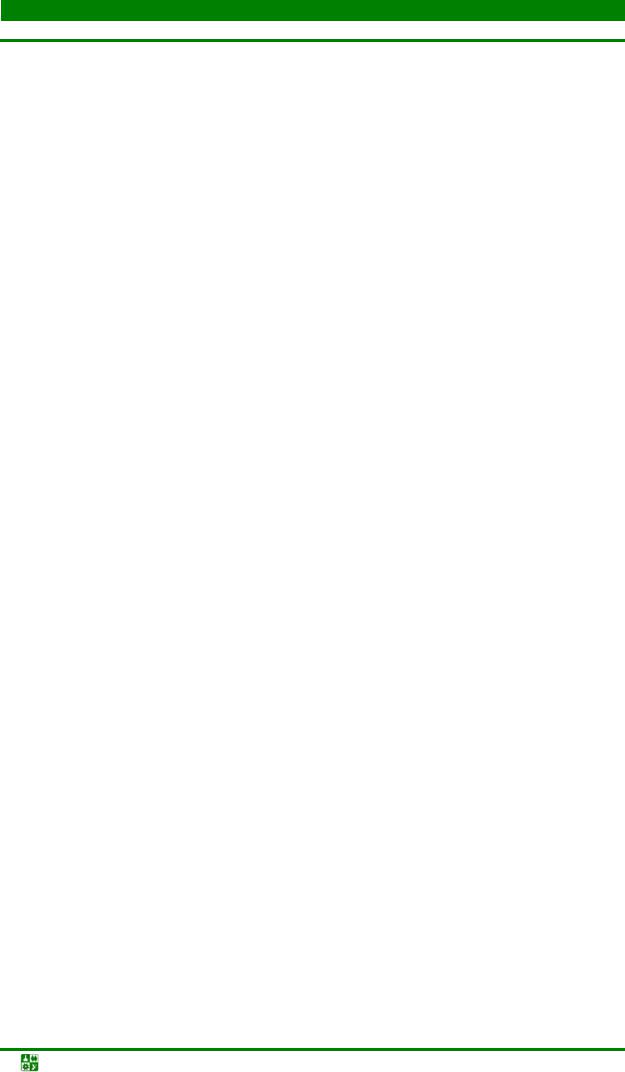
РАЗДЕЛ II. МАТЕРИАЛОВЕДЕНИЕ СТАЛЕЙ И ЧУГУНОВ
Глава 5. Чугуны, сплавы системы железо–углерод
Таблица 5.6
Механические свойства чугуна с шаровидным графитом для отливок (ГОСТ 7293-85)
Марка чугуна |
σв, МПа (кгс/мм2) |
σ0,2, МПа (кгс/мм2) |
δ, % |
Твердость, НВ |
|
ВЧ 35 |
350 |
(35) |
220 (22) |
22 |
140–170 |
ВЧ45 |
450 |
(45) |
310 (31) |
10 |
140–225 |
ВЧ60 |
600 |
(60) |
370 (37) |
3 |
192–277 |
ВЧ80 |
800 |
(80) |
480 (48) |
2 |
218–351 |
ВЧ100 |
1 000 |
(100) |
700 (70) |
2 |
270–360 |
В отличие от серых чугунов с пластинчатым графитом, во всех высокопрочных чугунах содержание углерода практически одинаково и высокое, что обеспечивает хорошие литейные свойства. Примесь фосфора снижает пластичность, поэтому его содержание не должно превышать 0,1 %. Особенно вредна сера, она снижает механические свойства и ослабляет действие модификаторов. Содержание серы не должно превышать 0,02–0,01 %, это меньше допуска в качественных сталях.
Высокопрочные чугуны с шаровидным графитом используют для замены литой стали в изделиях ответственного назначения: валки горячей прокатки, станины и рамы прокатных станов, молотов, прессов, коленчатые валы дизельных двигателей. Высокопрочный чугун применяют и для замены серого чугуна, если необходимо увеличить срок службы изделия или снизить его массу.
Чугун с вермикулярным графитом (табл. 5.7) по свойствам и внутрен-
нему строению занимает промежуточное положение между серым и высокопрочным чугуном. Графит вермикулярной формы представляет переходную форму от пластинчатой к шаровидной. В чугуне с вермикулярным графитом может содержаться не более 40 % шаровидного графита. По ГОСТ 28394-89 для изготовления отливок применяются чугуны следующих марок: ЧВГ 30, ЧВГ 35, ЧВГ 40, ЧВГ 45. Обозначение марки включает: буквы ЧВГ – чугун с вермикулярным графитом и цифровое обозначение минимального значения временного сопротивления разрыву при растяжении в МПа ×10-1. Чугуны марок ЧВГ прочнее, а при одинаковой прочности пластичнее чугунов марок СЧ. Они превосходят чугуны марок ВЧ по демпфирующей способности и обрабатываемости резанием.
Материаловедение. Учеб. пособие |
-298- |
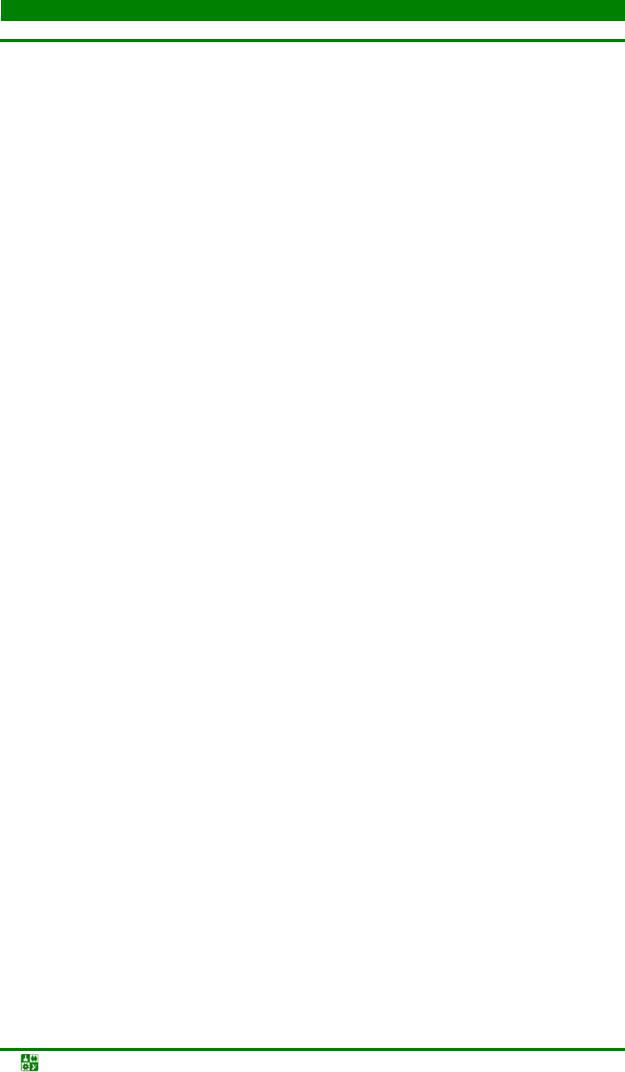
РАЗДЕЛ II. МАТЕРИАЛОВЕДЕНИЕ СТАЛЕЙ И ЧУГУНОВ
Глава 5. Чугуны, сплавы системы железо–углерод
Таблица 5.7
Механические свойства чугуна с вермикулярным графитом
(ГОСТ 28394-89)
Марка чугуна |
σв, МПа (кгс/мм2) |
σ0,2, МПа (кгс/мм2) |
δ, % |
Твердость, НВ |
ЧВГ 30 |
300 (30) |
240 (24) |
3,0 |
130–180 |
ЧВГ 35 |
350 (35) |
260 (26) |
2,0 |
140–190 |
ЧВГ 40 |
400 (40) |
320 (32) |
1,5 |
170–220 |
ЧВГ 45 |
450 (45) |
380 (38) |
0,8 |
190–250 |
Чугуны с вермикулярным графитом применяют взамен серых чугунов для отливок базовых деталей станков и кузнечно-прессового оборудования, массивных изложниц, кокильной оснастки.
5.5. Чугуныспециальногоназначения
Антифрикционные чугуны применяют для работы в узлах трения со смазкой, подшипников скольжения, втулок, вкладышей. В качестве антифрикционных используют серые чугуны с пластинчатым графитом АЧС-1, АЧС-2, АЧС-6, высокопрочные чугуны с шаровидным графитом АЧВ-1, АЧВ-2 и ковкие чугуны АЧК-1, АЧК-2, ГОСТ 1585-85 – Антифрикционные чугуны. В обозначении марки цифра означает порядковый номер, от которого зависит химический состав чугуна.
Чугуны, легированные углеродом, хромом, кремнием, алюминием, никелем, медью и другими элементами относятся к чугунам со специальными свойствами: износостойкие, жаростойкие, жаропрочные и коррозионностойкие.
Чугун подразделяется на виды и марки по легированию и назначению, ГОСТ 7769-82 – Чугун легированный для отливок со специальными свойствами. К хромистым чугунам относятся чугуны марок ЧХ1, ЧХ3, ЧХ16, ЧХ22С, ЧХ28Д2; к кремнистым – ЧС5, ЧС17, ЧС15М4; к алюминиевым – ЧЮ6С5, ЧЮ22Ш; к марганцевым – ЧГ6С3Ш, ЧГ8Д3; к никелевым – ЧНХТ, ЧН2Х2, ЧН19Х3Ш. В обозначении марок чугуна первая буква Ч – чугун, последующие буквы определяют легирующие элементы: Х – хром, С – кремний, Г – марганец, Н – никель, Д – медь, М – молибден, Т – титан, П – фосфор, Ю – алюминий; буква Ш указывает на шаровидную форму графита. Цифры, стоящие после каждой буквы, означают примерную массовую долю основных легирующих элементов в процентах.
Механические свойства легированных чугунов регламентируются по действующему стандарту (табл. 5.8).
Материаловедение. Учеб. пособие |
-299- |
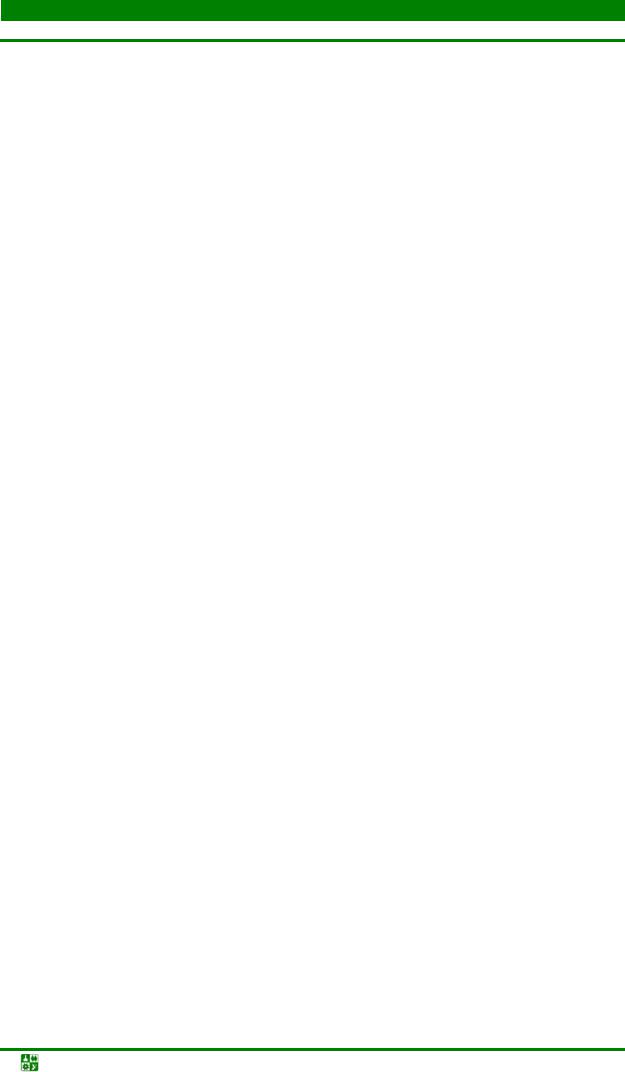
РАЗДЕЛ II. МАТЕРИАЛОВЕДЕНИЕ СТАЛЕЙ И ЧУГУНОВ
Глава 5. Чугуны, сплавы системы железо–углерод
|
|
|
|
Таблица 5.8 |
|
Механические и эксплуатационные свойства чугунов |
|||
|
|
|
|
|
Марка |
Временное сопротивле- |
Твердость |
|
|
ние, МПа, не менее |
Эксплуатационные свойства |
|||
чугуна |
|
|
НВ |
|
Растяжение |
Изгиб |
|
||
|
|
|
|
|
ЧХ3 |
150 |
310 |
228–364 |
Жаростойкий до 973 К, износо- |
стойкий |
||||
ЧХ32 |
290 |
460 |
245–340 |
Жаростойкий до 1 423 К, изно- |
состойкий |
||||
ЧС15М4 |
60 |
140 |
390–450 |
Коррозионно-стойкий в кисло- |
тах, щелочах, солях |
||||
ЧХ22С |
290 |
540 |
215–340 |
Коррозионно-стойкий в газовых |
средах до 1 273 К |
||||
ЧЮХШ |
390 |
590 |
187–364 |
Жаростойкий до 923 К |
ЧХ9Н5 |
350 |
700 |
490–610 |
Износостойкий |
ЧГ8Д3 |
150 |
330 |
176–285 |
Магнитный, износостойкий |
Отливки из легированных чугунов используются в условиях повышенных температур, в агрессивных средах, при значительном трении изделий. Хромистые чугуны ЧХ1, ЧХ2, ЧХ3, относящиеся к жаростойким и износостойким, применяются для изготовления деталей термических печей, колосников, горелок, кокилей. Кремнистые чугуны с высокой коррозионной стойкостью и износостойкостью ЧС5, ЧС15М4, ЧС15 используются для изготовления топочной арматуры котлов, деталей компрессоров, теплообменников и деталей химической аппаратуры. Марганцевые чугуны, относящиеся к износостойким и маломагнитным ЧГ7Х4, ЧГ8Д3, применяют для деталей насосов, мельниц, дробе- и пескоструйных камер, немагнитных деталей арматуры.
Контрольныевопросыизаданиия
1.Какие фазы входят в состав ледебурита и превращенного ледебурита? Изобразите структуру ледебурита.
2.Охарактеризуйте эвтектическое превращение по стабильной и метастабильной диаграмме Fe–C. Изобразить структуру аустенито-графитовой эвтектики.
3.Как влияет степень переохлаждения и модифицирование на форму
иразмеры графита в аустенито-графитовой эвтектике.
4.Какие примеси способствуют и какие препятствуют образованию графита при кристаллизации?
5.Укажите, в какой форме присутствует первичный, вторичный и третичный цементит в сталях и белых чугунах. Приведите примеры.
6.При каких температурах и в каких сплавах в системе Fe–Fe3C образуется первичный, вторичный и третичный цементит?
Материаловедение. Учеб. пособие |
-300- |
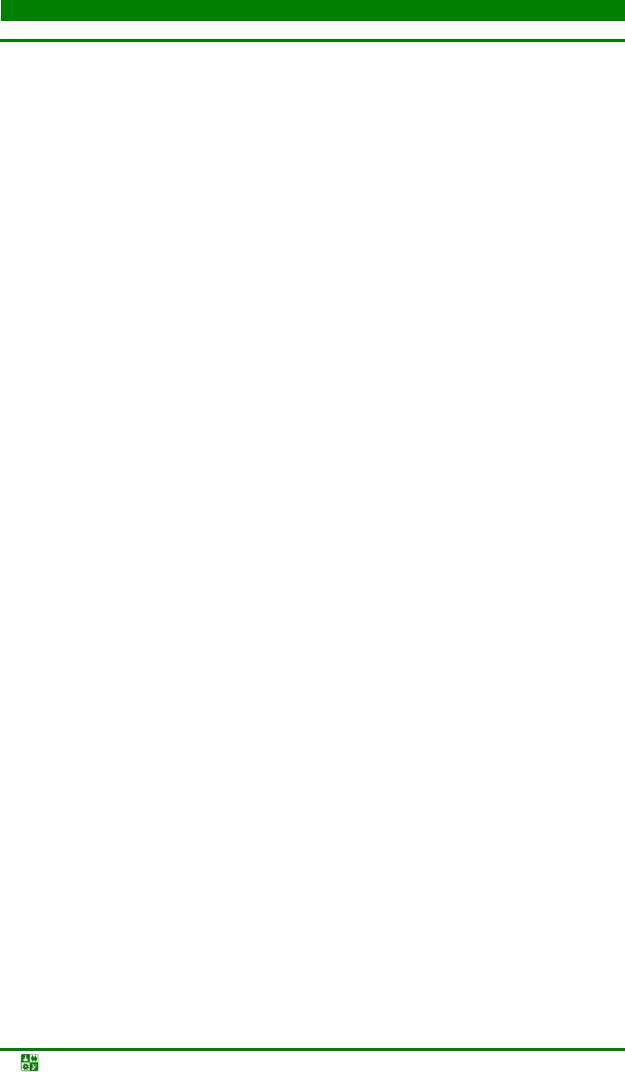
РАЗДЕЛ II. МАТЕРИАЛОВЕДЕНИЕ СТАЛЕЙ И ЧУГУНОВ
Глава 5. Чугуны, сплавы системы железо–углерод
7.При какой температуре происходит эвтектическое и эвтектоидное
превращение в метастабильной диаграмме Fe–Fe3C? Докажите, для реализации какогопревращениянеобходимыболеевысокиестепенипереохлаждения.
8.Укажите предельную растворимость углерода в аустените, δ- и α-феррите? Почему в аустените растворимость углерода выше?
9.Опишите кристаллическую структуру твердых растворов на основе железа в системе Fe–Fe3C.
10.Укажите фазовый состав и изобразите структуру отожженной стали 20 при комнатной температуре.
11.Приведите фазовый состав и изобразите структуру стали 45 при
температуре 740 °С.
12.Укажите фазовый состав и изобразите структуру отожженной стали У10 при комнатной температуры.
13.Приведите фазовый состав и изобразите структуру стали У8 после медленного охлаждения до комнатной температуры.
14.Укажите фазовый состав и изобразите структуру стали 30 в литом состоянии. Каковы особенности литой структуры?
15.Приведите фазовый состав и изобразите структуру стали 10 при комнатной температуре.
16.Укажите фазовый состав и изобразите структуру доэвтектического белого чугуна при комнатной температуре.
17.Изобразите структуру высокопрочного ферритного чугуна. Приведите его маркировку. Как условия охлаждения и модифицирования влияют на структуру чугуна?
18.Изобразите структуру серого ферритного чугуна. Приведите его маркировку. Какое влияние Si и Mn оказывает на получение ферритной основы чугуна?
19.Изобразите структуру серого перлитного чугуна. Приведите его маркировку. Какая схема охлаждения обеспечит получение перлитной основы чугуна?
20.Изобразите структуру серого феррито-перлитного чугуна. Приведите его маркировку. Какая схема охлаждения обеспечит получение ферритоперлитной основы чугуна?
Материаловедение. Учеб. пособие |
-301- |