
3 сем / ТКМ. Лаб. практикум_2022 - копия
.pdf
|
|
|
Таблица 5.5. |
|
|
Последовательность кузнечных операций |
|||
|
|
|
|
|
№ п\п |
Название операции |
Оборудование |
Инструмент |
|
|
|
|
|
|
1. |
Нагрев штанги |
Щелевая печь |
Пирометр. |
|
|
|
|
|
|
2. |
Отрубка |
|
Плоские бойки. Топор куз- |
|
|
|
|
||
3. |
Осадка |
Молот с массой |
||
нечный. Прошивни и над- |
||||
|
|
подвижных |
||
4. |
Прошивка, правка |
|||
ставки. Кольца подкладные. |
||||
|
|
частей 2 т |
||
|
Осадка в подкладное |
|||
5. |
Кронциркуль, линейка. |
|||
кольцо |
|
|||
|
|
|
||
|
|
|
|
|
6. |
Клеймение |
|
Клейма, молоток. |
|
|
|
|
|
|
7. |
Контроль размеров и |
|
Штангенциркуль. |
|
качества поковки |
|
|||
|
|
|
||
|
|
|
|
6. ГОРЯЧАЯ ОБЪЁМНАЯ ШТАМПОВКА
Цель работы: знания особенностей горячей объёмной штамповки и устройства штампов; умения выбора исходной заготовки и переходов штамповки для основных типов поковок, выполнять инженерные расчёты.
Общие сведения
Объёмная штамповка – процесс обработки металлов давлением, при котором происходит принудительное перераспределение металла заготовки с заполнением полости инструмента (штампа). Полость штампа, которую заполняет металл, называют ручьем. Штамповку осуществляют на молотах, кривошипных горячештамповочных прессах (КГШП), горизон- тально-ковочных машинах (ГКМ) и другом оборудовании [7]. Исходные заготовки – сортовой прокат круглого и прямоугольного сечений.
По сравнению с ковкой горячая объёмная штамповка имеет высокую производительность, позволяет получать поковки более сложной формы и с лучшим качеством поверхности. Припуски на механическую обработку снижаются в 2...3 раза, а точность размеров повышается до 11...12-го квалитета точности, что позволяет подвергать механической обработке только сопрягаемые поверхности.
63
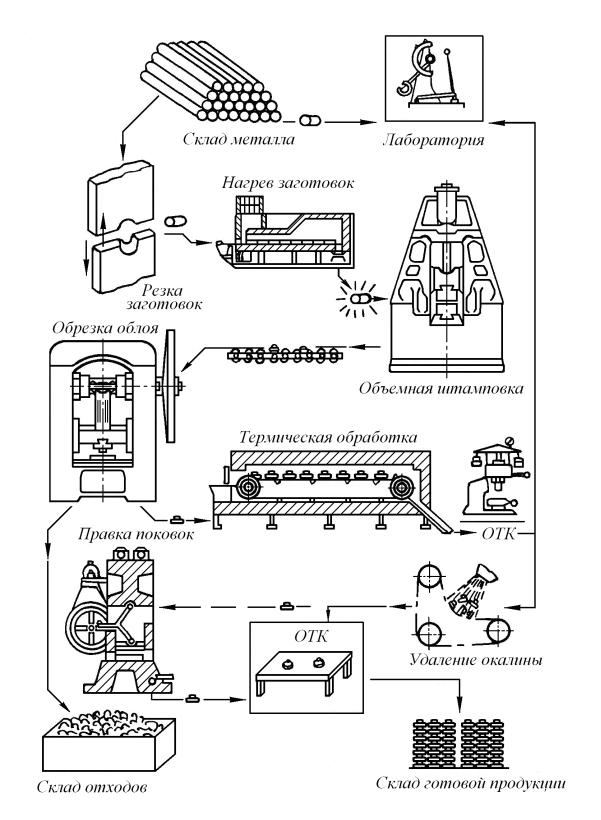
Рис. 6.1. Общая схема технологического процесса горячей штамповки поковок
64
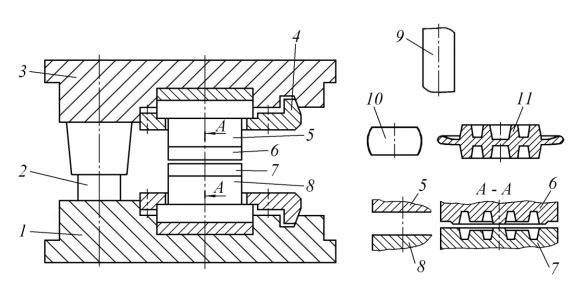
К недостаткам объёмной штамповки относят высокую стоимость инструмента и оборудования, ограничение изделий по форме и массе (обычно до 100 кг). Горячая объёмная штамповка широко применяется в серийном и массовом производстве деталей ответственного назначения. Последовательность изготовления поковок штамповкой показана на рис. 6.1.
Конструкция штампа зависит от типа используемого оборудования. Штамп в большинстве случаев состоит из двух половин: нижняя закреплена на столе, а верхняя – на подвижном рабочем органе пресса (ползуне) или молота (бабе). Молотовые штампы, испытывающие ударные нагрузки, выполняют монолитными из инструментальной стали. Верхняя и нижняя половина штампа крепятся с помощью клиньев, забиваемых в крепежные пазы, к бабе молота и штамподержателю, который закреплен на шаботе.
Штампы КГШП изготовляют сборными на базе унифицированных блоков. Штамповый блок (рис. 6.2) содержит верхнюю и нижнюю плиты 1 и 3, соединенные двумя направляющими колонками 2. Для осуществления штамповки в блоке установлены парные верхние и нижние штамповые вставки 5, 8 и 6, 7 из инструментальной стали. Количество пар вставок (от одной до трех) определяется сложностью и типом поковок. Верхние и нижние вставки устанавливаются в посадочные гнезда плит 1, 3 и закрепляются прихватами 4.
Рис. 6.2. Конструкция штампа и переходы штамповки круглой в плане поковки на кривошипном прессе
65

Во вставках 6, 7 штампового блока выполнена полость (ручей). По всему периметру ручья расположена облойная канавка, профиль которой представлен на рис. 6.3, б.
На вставках 5 и 8 предусмотрена открытая осадочная площадка, на которой штамповщик, удерживая заготовку клещами, производит осадку нагретой исходной заготовки 9 требуемого объема. После переноса осаженной заготовки 10 в ручей штампа осуществляют окончательную штамповку поковки 11. При движении верхней половины штампа вниз происходит осадка заготовки. После соприкосновения заготовки с боковыми стенками штампа сопротивление пластическому деформированию в этой зоне увеличивается, и металл начинает заполнять узкие элементы ручья. При подходе верхней половины штампа к нижней металл вытесняется в боковой зазор – облойную канавку. При этом сопротивление пластическому деформированию металла в боковом зазоре резко возрастает и происходит окончательное заполнение ручья с образованием облоя по периметру поковки 11. Облой служит для компенсации погрешности объема исходной заготовки и гарантированного заполнения ручья. После окончания штамповки облой удаляют на обрезном прессе.
Вид облойной канавки определяется типом штампа (см. рис. 6.3). При штамповке на КГШП не допускается беззазорное смыкание половин штампа из-за возможного заклинивания, поэтому нижнее положение ползуна КГШП фиксировано высотой h0 мостика. Канавки высотой hм делают открытыми, т. е. выполняют до боковой поверхности штампа.
Рис. 6.3. Облойные канавки молотового (а) и прессового (б) штампов
66

Различают штамповку осаживанием (см. рис. 6.2), когда преобладает осадка заготовки, и выдавливанием: прямым (рис. 6.4, а) и обратным (рис. 6.4, б) способами, когда основная часть металла 3 вытесняется в отверстие или в зазор между неподвижной матрицей 2 и подвижным пуансоном 1. Удаляется поковка выталкивателем 4.
Рис. 6.4. Схема штамповки прямым (а) и обратным (б) выдавливанием
жать выталкиватели.
Выдавливанием получают изделия со стержнем постоянного поперечного сечения или полые заготовки типа стакана.
Поковки с концевыми утолщениями можно получать высадкой на ГКМ и КГШП. При штамповке на КГШП длина хвостовика должна быть небольшой из-за ограничения хода ползуна пресса и размеров штампа. Поковка, в том числе и на хвостовике, должна иметь штамповочные уклоны, а штамп – содер-
Способы подготовки заготовки под штамповку
Исходные заготовки отрезают на пресс-ножницах, нагревают и штампуют в черновом и чистовом ручьях на прессе или молоте. Обычно перед укладкой в чистовой ручей необходима предварительная подготовка заготовки (за исключением поковок, получаемых высадкой или выдавливанием). Характер технологического процесса принципиально различен для двух групп поковок: I – удлинённые, штампуемые перпендикулярно оси заготовки (штамповка плашмя), и II – круглые в плане или близкие к ним (при отношении длины к ширине меньше двух), штампуемые вдоль оси заготовки (штамповка осадкой в торец).
Подготовка заготовок для штамповки круглых в плане поковок
заключается в предварительной осадке заготовки на осадочных площадках штампов. Осадку назначают для обеспечения устойчивости и правильной
67

ориентации заготовки в чистовом ручье, ликвидации косины и неровности отрезанной на пресс-ножницах заготовки, удаления окалины.
Устойчивое положение высокой заготовки 9 (см. рис. 6.2.) в чистовом ручье, выполненном во вставках 6 и 7, невозможно, поэтому слева на вставках 5 и 8 предусмотрена открытая осадочная площадка, на которой производят ее осадку. Зазор между осадочными вставками в нижнем положении равен высоте осаженной заготовки, диаметр которой должен быть таким, чтобы заготовка центрировалась по боковым стенкам ручья. Для этой же цели иногда на верхней части осадочной площадки предусматривают специальные выступы или впадины, для получения впадины или выступа на заготовке в соответствии с конфигурацией нижней части ручья штампа.
Подготовка заготовок для удлинённых поковок заключается в по-
лучении фасонной заготовки переменного поперечного сечения по длине путем перераспределения объемов металла. Необходимость фасонирования вызвана тем, что в ручьях штампа течение металла по длине затруднено, так как металл вытесняется в поперечном направлении, т. е. в облой. Равенство длины заготовки и поковки вызовет большой отход металла.
При проектировании технологии штамповки необходимо рассчитать площадь поковки в плоскости разъема штампа (в плане) Sпп, периметр (в плане) Пп, объем поковки Vп, площадь поперечного сечения облоя Fоб, объем заготовки Vисх и построить профиль исходной (расчётной) заготовки для определения технологических переходов, конструирования ручьев штампа. Расчётной заготовкой называется условная заготовка с круглыми поперечными сечениями, площади Fэi которых равны суммарной площади соответствующих сечений поковки Fпi и облоя Fоблi с двух сторон поковки:
.
Для определения профиля фасонной заготовки по чертежу поковки выбирают характерные поперечные сечения, находят площадь сечения расчетной заготовки Fэi и строят эпюру сечений. Далее определяют значения диаметра расчётной заготовки (координаты эпюры диаметров):
.
68

Отложив в масштабе под чертежом поковки значения dэi и соединив точки отрезками прямых и плавными кривыми, получают эпюру диаметров (рис. 6.5). Обычно эпюра диаметров имеет сложные очертания и получение соответствующей заготовки затруднительно. На отдельных участках целесообразно форму заготовки упростить, заменив простыми элементами (цилиндр, сфера, параллелепипед), т. е. выровнять эпюру диаметров, сохранив постоянство объема в каждой отдельной зоне. Окончательно выровненная эпюра диаметров соответствует требуемой форме и очертаниям фасонной заготовки круглого поперечного сечения или эквивалентного ему квадратного.
Для определения необходимости фасонирования находят усредненный диаметр dср исходной заготовки, т. е. условный диаметр заготовки постоянного сечения длиной lэ, равной длине поковки, и объёмом, равным
объёму расчетной заготовки: .
Значение среднего диаметра наносят на эпюру диаметров (см. рис. 6.5). Находят сечение, в котором dср = dэi. Это сечение делит расчетную заготовку на стержень длиной lс и головку длиной lг. Затем определяют коэффициенты, характеризующие степень сложности превращения исходной заготовки в фасонную: степень разновысотности поковки = dmax /dср, ее относительную длину = lэ /dср и конусность стержня К = (dк – dmin) /lс.
В зависимости от массы поковки, величин , и К по диаграмме (см. рис. 6.5) выбирают комбинацию заготовительных ручьев молотового штампа, необходимых для фасонирования заготовки. Если точка пересечения и попадает в область БЗ, то фасонирование не требуется; если в область ПЕРЕЖ – необходимо предусмотреть в штампе пережимной ручей. Во всех остальных случаях требуется фасонирование или на ковочных вальцах или в заготовительных ручьях молотового штампа. Причем областям ПО и ПЗ будет соответствовать подкатной открытый или закрытый ручей, области ПРОТ – протяжной ручей. При конусности К ≥0,2 к протяжному ручью добавляют открытый или закрытый подкатной ручей.
При серийной штамповке на молоте фасонирование можно производить непосредственно в штампе в заготовительных ручьях. Заготовительные ручьи обычно располагают на боковых участках штампа, так как уси-
69
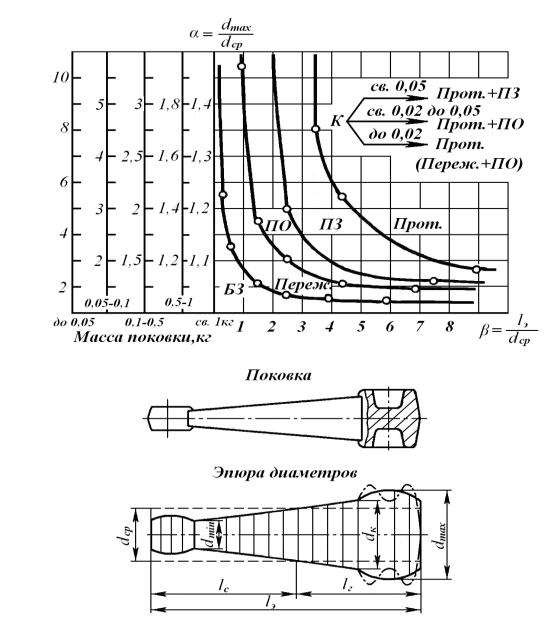
лие деформирования в них существенно ниже по сравнению с усилием штамповки в черновом или чистовом ручье.
Рис. 6.5. Диаграмма выбора способа фасонирования заготовки:
ПО – подкатной открытый, ПЗ – подкатной закрытый, Переж. – пережимной, Прот. – протяжной ручей, БЗ – без заготовительных ручьев
На рис. 6.6 изображена конструкция молотового штампа для штамповки рычага. В штампе кроме чистового ручья (сечение А–А) выполнены протяжной (Б–Б), подкатной (В–В) и гибочный (Г–Г) ручьи. Протяжной ручей имеет два выступа, которыми деформируют среднюю или концевую
70
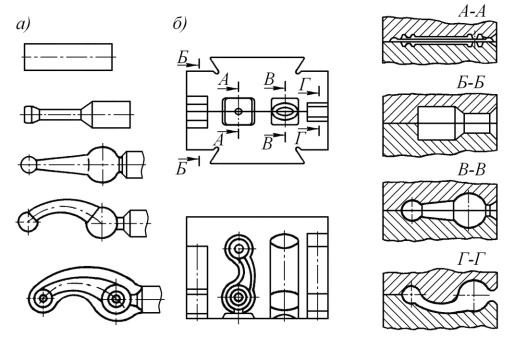
часть заготовки аналогично протяжке на плоских бойках с нанесением серии ударов, кантовкой вокруг оси на 90о и с последующей подачей заготовки вдоль ручья.
В подкатном ручье деформирование осуществляют серией ударов с кантовкой заготовки вокруг оси без подачи по длине. Заготовка после подкатки имеет округлые поперечные сечения, соответствующие профилю расчётной заготовки, включая наличие конических участков. Подкатной закрытый ручей в отличие от открытого ручья имеет форму поперечных сечений не в виде параллельных отрезков, а овальную или близкую к ней. В этом случае подкатка происходит за меньшее количество ударов.
Рис. 6.6. Переходы штамповки рычага (а) в четырехручьевом молотовом штампе (б)
Гибочный ручей (Г–Г) применяют для поковок с изогнутой осью в плоскости разъема штампа. Глубина гибочного ручья на 5...10 % меньше соответствующих поперечных размеров поковки, а ширина на 10...20 мм больше размеров заготовки. Гибку осуществляют обычно за один удар. Если поковки имеют кривизну в плоскости движения штампа, то гибку осуществляют в процессе штамповки в основных ручьях.
71
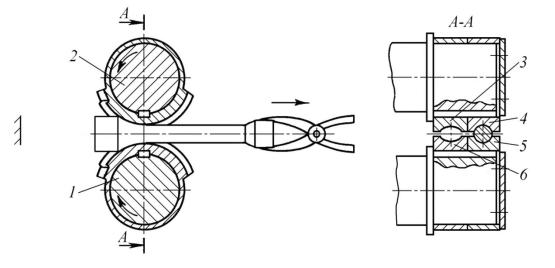
Пережимной ручей служит для местного уменьшения толщины заготовки за один удар, что приводит к уширению и незначительному удлинению ее вдоль оси. Устройство пережимного ручья аналогично протяжному ручью, но длина деформирующего участка соответствует эпюре диаметров, а зазор между выступами на 20...30 % меньше. Кантовку заготовки вокруг оси и подачу ее по длине в пережимном ручье не производят.
Заготовительные ручьи в штампах на КГШП обычно только пережимные или гибочные. При использовании КГШП фасонирование осуществляют на встроенных в поточную линию ковочных вальцах. Вальцовка позволяет существенно повысить производительность труда, поэтому целесообразна и при штамповке на молотах в массовом производстве.
Ковочные вальцы работают по принципу прокатных станов для продольной прокатки. Вальцы (см. рис. 6.7) имеют одну клеть, состоящую из двух валков 1, 2, на которых закреплены сменные секторные штампы 3, 4, 5, 6 переменного профиля. Секторные штампы образуют один, два и более ручьёв, в которых происходит деформирование заготовки 7 с уменьшением поперечных размеров и увеличением длины.
Рис. 6.7. Схема фасонирования заготовки на ковочных вальцах
Вальцовку круглой или квадратной заготовки ведут последовательно в нескольких ручьях с кантовкой на 90о, при этом поперечное сечение уменьшается по системе: круг – овал – квадрат – овал – квадрат или круг – овал – круг – овал – круг. Могут быть и другие сочетания ручьёв. Ширина каждого ручья должна быть равна высоте заготовки после предыдущего
72