
3 сем / ТКМ. Лаб. практикум_2022 - копия
.pdf
Последовательность выполнения работы
Опыт 1. Влияние давления формования на плотность
1.Изучите особенности и область применения порошковой металлургии. По лабораторному стенду и учебному фильму изучите типовые изделия порошковой металлургии, их назначение и особенности технологии.
2.Зафиксируйте условия проведения эксперимента: оборудование, материал и его массу m, применяемая оснастка с рабочими размерами, измерительный инструмент и приборы.
3.Соберите пресс-форму (см. рис. 4.1) и засыпьте в нее железный порошок ПЖ4М2 ГОСТ 9849-74, используя мерную емкость объемом 10 см3. Под руководством преподавателя отформуйте заготовки при удельном давлении p = 100, 200, 300 и 400 МПа, предварительно определив усилие
пресса P p πd4 2 – где d – внутренний диаметр полости пресс-формы.
4. Измерьте размеры полученных образцов и рассчитайте объём V и плотность отформованных образцов ρ m/V (г/см3). Определите относительную плотность прессовок / к, где к = 7,85 г/см3 (для железа) – плотность компактного материала. Результаты измерений и расчетов занесите в таблицу П.1 протокола измерений (см. Приложение к данной работе). В графе “Примечание” укажите визуальную оценку формы брикетов и наличие внешних дефектов: выкрашивание, разрушение образца при выталкивании.
5. Постройте график зависимости относительной плотности / к от удельного давления формования p. Выполните экстраполяцию кривой / к до значений давления p = 600...700 МПа.
Опыт 2. Механические свойства спечённых порошковых материалов
1.Проанализируйте внешний вид спеченных образцов, проведите по три измерения каждого параметра. Результаты замеров запишите в таблицу П.2 протокола измерений (см. Приложение к данной работе).
2.Рассчитайте пористость спеченного материала П по формуле:
П(1 ρ/ρк ) 100 %.
43

3.Измерьте диаметр лунки dотп на образцах. Полученные значения занесите в таблицу П.2 протокола измерений. Рассчитайте твёрдость при диаметре шарика D = 10 мм и нагрузке P = 10 кН по формуле:
4.Сравните предел прочности спеченного образца в с пределом прочности компактного материала соответствующего химического состава вк.
Относительный предел прочности определить через относительную
твёрдость: в/ вк = HB /HBк (HBк = 1100 МПа – твёрдость компактного сплава аналогичного химического состава). Результаты расчётов занесите
втаблицу П.2 протокола измерений.
5.Постройте и проанализируйте график зависимости относительной
прочности в/ вк от пористости спечённого материала. 6. Оформите отчёт.
Содержание отчета
1.Сущность и область применения порошковой металлургии.
2.Эскиз пресс-формы для двухстороннего формования порошков.
3.Расчёт усилия пресса.
4.Таблица параметров формования (см. табл. 4.1).
5.Примеры расчёта абсолютной и относительной плотности / к порошковых брикетов.
6.График зависимости относительной плотности / к от удельного давления формования p.
7.Таблица измерений размеров и диаметра отпечатка спечённых образцов (см. табл. П.1).
8.Примеры расчета абсолютной и относительной плотности / к, пористости П, твердости HB и относительного предела прочности в/ вк спечённых порошковых брикетов.
9.График зависимости относительного предела прочности в/ вк от пористости П.
10.Выводы о минимальном давлении формования порошков, когда брикет сохраняет свою форму, и о способах повышения плотности. Ука-
44
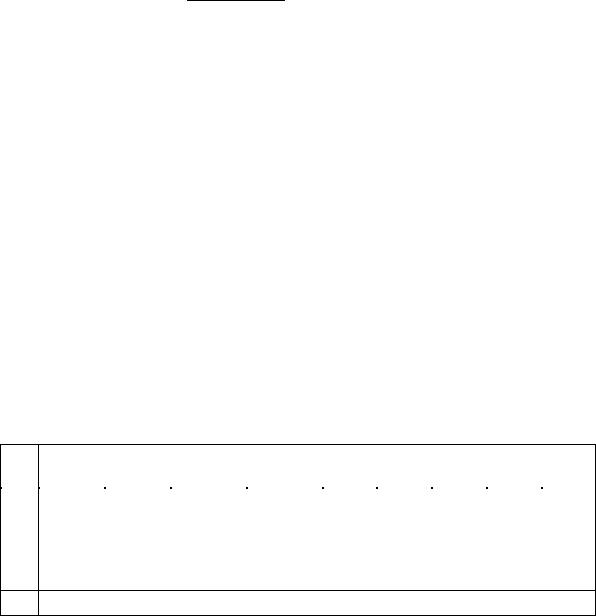
жите предельно возможную плотность, пористость и прочность спечённых брикетов.
11. Приложение. Протокол измерений (по далее приведенной форме).
Приложение к работе 4
ПРОТОКОЛ ИЗМЕРЕНИЙ
к лабораторной работе «Исследование свойств изделий из порошковых материалов»
1.Условия проведения эксперимента
1.1.Материал: ________________________________________________
2.1.Масса засыпки: m = г_________________________________
3.1. Размеры пресс-формы: H0 |
= |
мм; h |
0 |
= |
мм; d |
0 |
= |
мм |
____ |
4.1.Измерительные инструменты: _______________________________
2.Таблицы измерений
Таблица П. 1
Влияние давления формования на плотность образцов
образцаНомер |
МПа,pДавление |
кН,PУсилие |
|
Параметры образца |
|
Относительная |
/плотность |
Примечание |
||
|
|
|
|
|
||||||
|
|
|
|
|
|
|
|
|
к |
|
|
|
|
Диаметр |
Высота |
Объем |
Масса |
Плотность |
|
|
|
|
|
|
d, мм |
h, мм |
V, см3 |
m, г |
, г/см3 |
|
|
|
|
|
|
|
|
|
|
|
|
|
|
1 |
100 |
|
|
|
|
|
|
|
|
|
|
|
|
|
|
|
|
|
|
|
|
2 |
200 |
|
|
|
|
|
|
|
|
|
|
|
|
|
|
|
|
|
|
|
|
Номер образца
1
Таблица П. 2
Механические свойства спеченных порошковых материалов
|
Параметры образца |
|
Относительная |
плотность/ |
Пористость ,П% |
Диаметрлунки d |
ТвердостьHB, |
|
Относительная |
вк |
||
|
|
|
|
|
МПа |
прочность |
||||||
|
|
|
|
|
|
к |
|
|
|
|
|
/ |
|
|
|
|
|
|
|
|
|
|
|
|
в |
Диа- |
|
|
|
Плот- |
|
|
|
мм, |
|
|
|
|
метр |
Высота |
Объём |
|
ность |
|
|
|
отп |
|
|
|
|
|
|
|
|
|
|
|
|
|
|
|||
hср, мм |
V, см3 |
|
|
|
|
|
|
|
|
|
||
dср, мм |
|
, г/см3 |
|
|
|
|
|
|
|
|
||
|
|
|
|
|
|
|
|
|
|
|
||
|
|
|
|
|
|
|
|
|
|
|
|
|
45
5. ТЕХНОЛОГИИ КОВКИ
Цель работы: знание основных операций ковки и области их применения; умение выполнять технологические расчеты и правильно выбирать последовательность основных операций; навыки выполнения операций и приемов ковки.
Общие сведения
Ковка – процесс горячей обработки металлов давлением путем многократного воздействия на отдельные части заготовки универсальным инструментом простой формы при свободном течении металла в стороны. Для изготовления поковок массой до 500...1000 кг используют пневматические и паровоздушные молоты, для ковки более крупных поковок – гидравлические прессы [6]. Для ковки используют слитки и сортовой прокат (квадрат, круг, полосовая сталь и т. д.). Слитки являются заготовками для крупных поковок и имеют массу от 1,2 т до 500 т.
Ковка применяется в единичном и мелкосерийном производстве поковок ответственного назначения с мелкозернистой структурой и высокими механическими свойствами. Качество проработки структуры металла при ковке характеризует уков – отношение площади поперечного сечения заготовки к площади поперечного сечения поковки (при протяжке). Для исходной заготовки из проката уков должен быть не менее 1,3...1,8. При изготовлении поковок из слитков уков принимают для углеродистых сталей не менее 2,5 (на фланцах и выступах не менее 1,75), для легированных сталей – не менее 2 (на фланцах и выступах не менее 1,5).
Технология ковки включает в себя основные, вспомогательные и отделочные операции. Назначение последовательности ковочных операций с указанием необходимого инструмента и приспособлений является наиболее ответственной частью разработки технологического процесса.
Основные операции ковки
Осадка – это операция, при которой увеличивается площадь поперечного сечения исходной заготовки за счет уменьшения ее высоты. Осадку применяют для коротких поковок типа дисков и шестерен, а также как
46
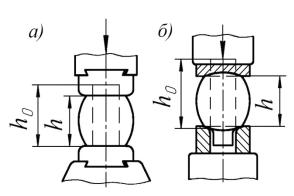
предварительную операцию перед прошивкой отверстий в пустотелых поковках. Осадка может быть назначена и при ковке из слитков длинных поковок с целью обеспечения требуемого укова (отношение поперечного сечения заготовки к площади поперечного сечения поковки) для устранения литой структуры и повышения механических свойств материала поковок.
Осадку заготовки выполняют на молотах или прессах плоскими бойками (рис. 5.1, а), а при получении ступенчатых заготовок – в подкладных кольцах. Осадку слитка с хвостовиком (рис. 5.1, б), который предварительно оттягивают и вставляют в отверстие нижней плиты, производят преимущественно при получении поковок типа валов. Рабочие поверхности осадочных плит имеют сферическую форму для устранения вогнутости торца поковки при последующей протяжке слитка.
Разновидностью осадки является высадка, при которой осуществляют увеличение поперечного сечения заготовки на некоторой ее части по длине. Предельная высота высаживаемой части или осаживаемой заготовки h0 не должна быть больше 2,5...3 диа-
Рис. 5.1. Схема осадки заготовок: |
метров во избежание искривления |
|
|
без хвостовика (а) и с хвостовиком (б) |
оси (потери устойчивости) поков- |
|
|
|
ки. После осадки часто применяют |
отделочную операцию – обкатку по диаметру для устранения бочкообразности заготовки.
Прошивка – операция, при которой в заготовке с помощью прошивня получают отверстие или углубление (рис. 5.2). Обычно прошивке предшествуют отрубка прибыльной и донной части слитка, а затем осадка заготовки. Помимо сплошных или пустотелых прошивней, используют соответствующие надставки, подкладные плиты и кольца.
Прошиваемую заготовку 3 помещают на нижний боек, прошивень 2 устанавливают на торец заготовки и легкими ударами или нажатием верхнего бойка 1 вдавливают в заготовку, при этом используют надставки 4 и 5. После переворота заготовки 3 перемычка 7, называемая выдрой , уда-
47
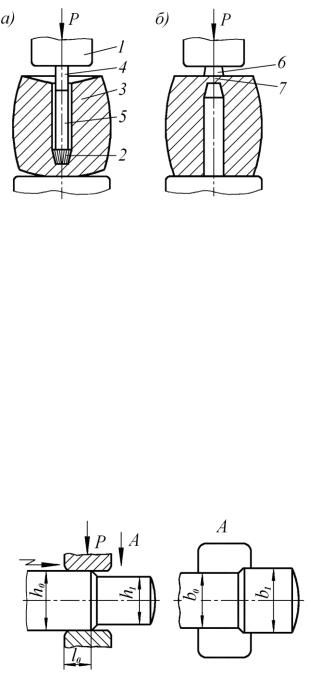
ляется просечным прошивнем 6. Высота выдры составляет 0,1...0,2 высоты прошиваемой заготовки, но не более 0,3 диаметра прошивня. Возникшие искажения формы заготовки при прошивке (торцы заготовки искривляются, усиливается бочкообразность) убирают правкой и обкаткой по диаметру.
Заготовки под прошивку должны быть невысокими и
|
обычно отношение высоты к диа- |
|
|
метру h/d не превышает значений |
|
|
0,8...1. В противном случае потре- |
|
|
буется большое количество над- |
|
|
ставок, а прошивень может откло- |
|
|
ниться от требуемого направле- |
|
|
ния. |
|
Рис. 5.2. Схема прошивки отверстий: |
Протяжка – операция, при |
|
|
||
а – внедрение прошивня; б – просечка |
которой увеличивают длину заго- |
|
выдры после кантовки заготовки |
||
товки за счет уменьшения попе- |
||
|
речного сечения. Протяжка плоскими бойками (рис. 5.3) заключается в последовательных обжатиях части заготовки с кантовкой ее на 90 градусов вокруг оси, продольной подачей заготовки и деформированием следующего участка. Деформирование заготовки сопровождается удлинением, а также уширением (b1 – b0). Если уширение не требуется, то его устраняют вторым проходом после кантовки поковки на 90 градусов.
Протяжка вырезными бойками позволяет интенсифицировать про-
|
цесс |
деформирования |
на |
|
20...40 % по сравнению с про- |
||
|
тяжкой плоскими бойками. Часто |
||
|
на практике применяют комби- |
||
|
нированные бойки (рис. 5.4), т. е. |
||
|
верхний боек 1 – плоский, ниж- |
||
|
ний боек 2 – вырезной. |
|
|
Рис. 5.3. Схема протяжки прямоугольной |
|
Основными дефектами по- |
|
|
|
|
|
пластины на плоских бойках |
ковок |
при протяжке являются |
|
|
|
|
|
|
зажимы, вогнутость торца, |
тре- |
48
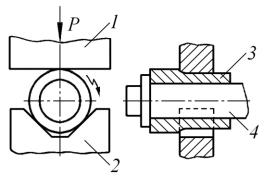
щины и саблевидность. Зажимы могут образовываться при продольной подаче заготовки l0 на величину большую 80 % ширины бойка. В этом случае металл «наплывает» на деформированный ранее участок заготовки, образуя в дальнейшем зажим. Вогнутость торца может возникать при слабых обжатиях, когда деформируются только поверхностные слои металла. Выпуклость торца, полученная при предварительной осадке слитка с применением осадочных плит вогнутой формы (см. рис. 5.1, б) компенсирует неравномерное течение металла. Саблевидность появляется чаще всего при протяжке на прессе из-за неравномерного охлаждения поковки при контактировании с холодным нижним бойком. При появлении искривления, заготовку поворачивают на 180о и деформируют.
Протяжка на оправке (см. рис. 5.4) применяется при ковке пустотелых поковок (валов, цилиндров, стволов, обечаек и др.). Она заключается в том, что предварительно прошитую заготовку 3 надевают на оправку 4 и проводят протяжку в вырезных или комбинированных бойках 1, 2. Для облегчения съема поковок оправки выполняют конической формы (конусность 1 100). Бурт на оправке способствует деформированию металла при обжатии новых участков заготовки в сторону предварительно обжатых участков. При ковке крупных заготовок применяют оправку со сквозным
Рис. 5.4. Протяжка на оправке в внутренним отверстием для охлажде-
комбинированных бойках
ния ее водой.
Раскаткой на оправке производят одновременное увеличение наружного и внутреннего диаметров полой заготовки за счет уменьшения толщины ее стенок. Для выполнения этой операции предварительно прошитую заготовку с наружным диаметром D0 (рис. 5.5) надевают на оправку и их размещают на стойке. Ковку осуществляют верхним бойком, при этом оправку вместе с заготовкой после каждого нажатия поворачивают. При раскатке уменьшается толщина, увеличивается диаметр (D1 D0) и высота кольца H1. Обычно высоту заготовки H0 перед прошивкой отверстия выбирают на 20 % меньше требуемой H1 для небольших поковок и на 10 % –
49

для крупных поковок. Диаметр отверстия под прошивку назначают не более 0,25...0,35 наружного диаметра заготовки после осадки.
Отрубка служит для отделения от исходной заготовки отходов или для разделения её на части. Инструментом для отрубки служат топоры длиной 150...1000 мм. Для подачи крупных топоров под бойки пресса применяют специальные подъемники или инструментальные манипуляторы.
Рис. 5.5. Схема раскатки |
Рис. 5.6. Схема отрубки топором |
на оправке |
с двух сторон |
В зависимости от габаритов и формы заготовок используют способы рубки: с одной стороны – для тонких заготовок; с двух сторон; с трех сторон – для круглых заготовок с применением нижнего вырезного бойка для уменьшения смятия металла; с четырех сторон – для крупных заготовок. При отрубке с двух сторон (рис. 5.6) сначала осуществляется предварительная надрубка на глубину 0,5...0,75 высоты заготовки, после кантовки на 180о проводится окончательная рубка. При отрубке с трех сторон заготовку поворачивают на 120о, первые две надрубки выполняют прямым топором, а окончательную – трапецеидальным топором. Основными дефектами являются заусенцы и трещины, образующиеся в зоне отрубки из-за пониженной пластичности металла (недостаточный нагрев заготовки или ее охлаждение в процессе ковки).
Вспомогательные и отделочные операции
Вспомогательные операции служат для подготовки заготовки к выполнению основных операций. К отделочным операциям относят проглаживание поковок (шлихтовку), правку поковок и клеймение.
50
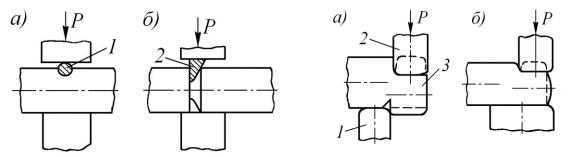
Биллетировка (обкатка) – разновидность протяжки, которую выполняют с целью устранения огранки и конусности слитков. При ковке валов эта операция следует за оттяжкой хвостовика. При ковке полых поковок после биллетировки отрубают прибыльную и донную части слитка, годный остаток, используемый в дальнейшем.
Намётка – вспомогательная операция, посредством которой на поверхности исходной заготовки наносят разметочные углубления для разбивки ее на отдельные участки при помощи круглых раскаток небольшого диаметра (рис. 5.7, а).
Пережим – вспомогательная операция, при помощи которой получают местные или по всему периметру углубления. Пережим осуществляется раскатками или пережимками (рис. 5.7, б), которые могут быть треугольными и фасонными. Пережим металла обычно предшествует протяжке ступенчатых поковок, образованию уступов и выемок.
Передача – операция, при которой одну часть заготовки смещают по отношению к другой с сохранением параллельности их осей (рис. 5.8). Передачу применяют при ковке эксцентриковых, кривошипных и коленчатых валов, при этом передаче всегда предшествует пережим заготовки. Инструмент для передачи – плоские бойки с разной шириной или одинаковые, но смещенные относительно друг друга, а также подставки или цепи кантователя для поддержания свободного конца поковки.
Рис. 5.7. Схема намётки (а)
Рис. 5.8. Схема двусторонней
и пережима (б): 1 – раскатка круглая;
передачи металла (а) и образования
2 – пережимка треугольная
одностороннего уступа (б): 1, 2 – бойки; 3 – заготовка
51
Разгонка – вспомогательная операция, служащая для увеличения размеров в плане заготовки или ее части за счет уменьшения толщины.
Гибкой заготовке придают заданную изогнутую форму. Гибку заготовки, зажатой между бойками, осуществляют вручную кувалдой или с помощью крана. При гибке наружные слои заготовки на участке изгиба подвергаются изгибу, а внутренние сжатию. При этом происходит искажение начальной формы поперечного сечения заготовки: квадратное сечение приобретает форму неправильной трапеции, а круглое – форму овала. Гибка может сопровождаться утяжкой – уменьшением площади поперечного сечения заготовки в месте изгиба.
Скручивание – это операция, в процессе которой часть заготовки поворачивается вокруг продольной оси. Если при гибке ось заготовки получает изгиб, то при скручивании направление оси остается неизменным. Эту операцию применяют при ковке коленчатых валов, крупных сверл и производят вручную или с помощью крана.
Проглаживание поковок (шлихтовка) – отделочная операция для уменьшения неровностей (огранка, уступы) путем легких ударов молота или нажатий пресса широкими бойками по аналогии с протяжкой.
Правка применяется для устранения кривизны поковок на гидравлических прессах, подкладывая на нижний боек одну или две подкладки. Деформирование (изгиб до прямолинейности) осуществляют верхним бойком.
Клеймение – это нанесение знаков марки стали, номера плавки, шифра поковки и т. п. Место клеймения обычно указывают на необрабатываемой поверхности. При механической обработке всех поверхностей перенесение клейма производят на ранее обработанную поверхность.
Ковка должна обеспечить при наименьших затратах хорошее качество металла. Поэтому при ковке убирают неблагоприятные зоны металла в исходной заготовке: донную и прибыльную части слитка отрубают, а для крупных ответственных пустотелых поковок удаляют его центральную зону пустотелым прошивнем. Для получения равномерных по всему объему поковки механических свойств металла для поковок типа валов назначают обычно после отрубки осадку заготовки с последующей протяжкой до требуемых размеров с обеспечением укова не менее 2,5.
52