
3 сем / ТКМ. Лаб. практикум_2022 - копия
.pdfАнтифрикционные (подшипниковые) материалы (баббиты и сплавы на основе цинка и алюминия) применяют для изготовления вкладышей подшипников скольжения дизелей, турбин, двигателей, прокатных станов и металлообрабатывающих станков, автомобильного и железнодорожного транспорта.
Основные типы баббитов: оловянные Б88, Б83, Б83С и свинцовые
Б16, БН, БС6 (ГОСТ 1320-74); кальциевые БКА, БК2, БК2Ш, БК2Ц (ГОСТ 1209-90). Оловянные баббиты применяют для особо ответственных изделий из-за хорошей прирабатываемости к валу и износостойкости. У баббитов на свинцовистой основе нет равномерного распределения твердых частиц сурьмы и их износостойкость ниже. Для предупреждения ликвации при литье из-за различия в плотности основных компонентов (олова, свинца и более легкой сурьмы) в эти баббиты вводят медь (2…7 %). Никель (0,5...1,1 %), вводимый в баббит марки БН улучшает форму включений и измельчает структуру. Кальциевые баббиты на свинцовистой основе без олова имеют добавки кальция, алюминия, натрия, цинка.
Обозначение баббитов носит условный характер, не показывая полностью состав сплава. В оловянных и свинцовых баббитах, например, Б88, Б16 следующие за буквой «Б» числа показывают только содержание олова в процентах. В маркировке кальциевых баббитов БКА, БК2Ц следующие за буквой «Б» буквы означают элементы, а числа – их содержание в процентах.
В обозначении антифрикционных сплавов на основе цинка (ГОСТ 21437-95), например, ЦАМ10-5 и на основе алюминия (ГОСТ 14113-78), например, АН2,5; АСМ первая буква указывает на основу сплава: цинк или алюминий. Следующие буквы означают элементы, а цифры – их среднее количество в процентах. В марках сплавов на основе алюминия, например, АО9-2 и АО20-1 идущие после букв через тире цифры обозначают среднее количество олова в процентах и среднее содержание меди. В марках сплавов без олова АСМ, АМСТ и АМК буквой С обозначают сурьму, М – магний (в АСМ) или медь (в АМСТ и АМК), Т – теллур. Литейные антифрикционные сплавы на основе цинка в конце марки обозначаются буквой Л, например: ЦАМ9-1,5Л; ЦАМ10-5Л.
23
Содержание работы
Работа включает: изучение классификации, правил маркировки и назначения машиностроительных материалов, определение по исходным данным индивидуального задания химического состава, качества сталей и области применения конкретных металлов и сплавов, составление отчёта.
Последовательность выполнения работы
1.Ознакомьтесь с классификацией и основными правилами маркировки сталей, чугуна, цветных металлов и сплавов.
2.Получите и выполните индивидуальное задание (таблица 1.5) по расшифровке марок машиностроительных материалов с указанием химического состава и их области применения.
3.Составьте отчёт по индивидуальному заданию.
Содержание отчёта
1.Наименование работы.
2.Классификация и принцип маркировки сталей и сплавов.
3.Номер и исходные данные индивидуального задания.
4.Расшифровка марок машиностроительных материалов с указанием заданной марки сплава, наименования материала, химического состава и области применения (по форме Приложения к работе 1).
Таблица 1.5
|
Индивидуальные задания |
|
|
|
|
№ |
Марки материала |
|
|
|
|
1. |
08кп, 35ХГСА, 55ХГР, 06ХН28МТ, 10Х18Н9Т, У7А, АС38ГМ, Ст3сп, |
|
СЧ10, ТТ10К8Б, АМг10ч, Вт1-0, Л85, БрО6Ц6С2х, ПСрМО68-27-5 |
||
|
||
|
|
|
2. |
10кп, 40ХН2МА, 70С3А, 20Х3МВФ; 12Х13, У12, АС19ХГН, Ст3Гпс, СЧ 15, |
|
ВК20-КС, АК6М2, ПТ-7М, ЛМцА57-3-1, БрО10Ф1, ПСр2 |
||
|
||
|
|
|
3. |
15пс, 30Х3МФ, 70Г, 45Х14Н14В2М, ХН60ВТ, У9А, АЦ35Г2, Ст6сп, СЧ 25, |
|
ТТ20К9; АМ4,5Кд; АТ3, Л96, БрА7Мц15Ж3Н2Ц2, ПСрО3-97 |
||
|
||
|
|
|
4. |
20Р, 38ХГМ, 60С2Н2А, ХН35ВТ, 10Х17Н13М3Т, У7, АС12ХН, Ст2пс, |
|
СЧ 30, ВК6-ОМ, АК12М2МгН, ПТ-3В, ЛК80-3, БрБ2, БК2 |
||
|
||
|
|
24
Продолжение табл. 1.5
№ |
Марки материала |
|
|
|
|
5. |
05кп, 20Н2М, 55С2А, ХН28ВМАБ, 20Х13, У10А-Ш, АЦ35Х, Ст3Гпс, |
|
ЧЮ22Ш, Т14К8, АК10Су, ВТ5Л, ЛС59-1, БрО4Ц7С5, ЦАМ 10-5Л |
||
|
||
|
|
|
6. |
35, 12ХН, 65С2ВА, ХН56ВМКЮ, 40Х13, У8ГА, АС20ХГНМ, Ст6пс, |
|
КЧ 30-6, ТТ8К6; АМгК1,5М; МЛ10, ЛАЖ60-1-1, БрА7, ПСр12М |
||
|
||
|
|
|
7. |
45Р, 14ХГН, 65Г, ХН75МБТЮ, 09Х15Н18Ю, 9ХС, АС35Г2, Ст2кп, КЧ 45-7, |
|
ВК6-М, АК9с, МА2-1пч, ЛЦ16К4, БрС30, ПОССу35-0,5 |
||
|
||
|
|
|
8. |
20пс, 50Г, 60С2ХФА, 18Х3МВ, 30Х13, 5ХНМ, АЦ30ХМ, Ст3Гсп, КЧ 70-2, |
|
Т5К10, АК12М2МгН, МА15, ЛЦ23А6Ж3Мц2, БрМц5, БКА |
||
|
||
|
|
|
9. |
15кп, 40ХГТР, 60С2, 20Х1М1Ф1БР, 20Х13, ХВГ, АС12ХН, Ст2сп, ВЧ 35, |
|
ВК6-В, АМг6лч, ОТ-4, Л63, БрАЖНМц9-4-4-1, ПСрОСу8 |
||
|
||
|
|
|
10. |
08пс, 20ХГСА, 55С2ГФ, 12Х1МФ, 12Х18Н10Т, 9ХФ, А45Е, Ст4кп, |
|
КЧ 80-1,5; ТТ8К7, АК12М2, ОТ4-1, ЛЦ14К3С3, БрАМц9-2, ПМЦ36 |
||
|
||
|
|
|
11. |
30, 10Г2, 50ХФА, 10Х11Н23Т3МР, 12Х13, 5ХНВ, А40ХЕ, Ст1сп, ВЧ 40, |
|
ВК8-ВК, АМг5Мц, МА8пч, ЛЖМц59-1-1, БрКд1, АО6-1 |
||
|
||
|
|
|
12. |
25Р, 12ХН2, 60Г, 03ХН28МДТ, 20Х17Н2, Х12Ф1, АС14ГН, Ст3пс, ЧВГ 30, |
|
Т15К6, АК5М2, Вт20, ЛЦ40Мц3А, БрА9Ж3Л, ПОССу8-3 |
||
|
||
|
|
|
13. |
08, 20ХГНТР, 85, 45Х14Н14В2М, 15Х28, 4ХВ2С, АС40ХГНМ, Ст3кп, |
|
ЧВГ 45, ВК8-В, АМг7, МЛ5он, ЛО70-1, БрО4Ц4С17, ПОССу35-2 |
||
|
||
|
|
|
14. |
55, 20ХНР, 50ХГА, 15Х6СЮ, 12Х18Н10Т, ХВСГ, АЦ12ХН3, Ст1пс, АЧС-2, |
|
Т30К4, АК5Мч, МА2-1, ЛЦ37Мц2С2К, БрА9Мц2Л, ЦА30М5 |
||
|
||
|
|
|
15. |
10пс, 15ХФ, 55С2А, 30Х13Н7С2, ХН70Ю, Х12М, АС30ХМ, Ст3Гсп, АЧВ-1, |
|
ТТ17К12, АК7Ц9, ВТ3-1, ЛС63-3; БрБНТ1,9Мг; ПОСК2-18 |
||
|
||
|
|
|
16. |
20пс, 38Х2Ю, 51ХФА, 12Х17, ХН45Ю, 5Х3В3МФС, АЦ35Г, Ст5Гпс, |
|
АЧК-2, ВК10-КС, АК7пч, МА18, ЛМш68-0,05; БрАМц10-2, Б83С |
||
|
||
|
|
|
17. |
30Р, 15Х, 60С2Н2А, 15Х6СЮ, 08Х18Н9Т, Р10К5Ф5, АС45Г2, Ст5пс, ЧХ3Т, |
|
ВК3, АК9Ц6, МЛ15, ЛЦ40Мц3Ж, БрОЦС4-4-4, ПСрОС2-58 |
||
|
||
|
|
|
18. |
20кп, 38ХГМ, 55С2, 40Х9С2, 08Х21Н6М2Т, Р6М5, АЦ20ХН3, Ст4сп, |
|
ЧС15М4, ВК6, АК9ч, ВТ5-1, ЛС60-1, БрСу3Н3Ц3С20Ф, ЦА4М1о |
||
|
||
|
|
|
19. |
58, 25ХГНМТ, 70С2ХА, 15Х28, ХН77ТЮР, ШХ15СГ, А40Г, Ст5сп, ЧГ7Х4, |
|
ВК20, АЦ4Мг, МА2, ЛЖС58-1-1, БрОФ8,0-0,3; ПОС61М |
||
|
||
|
|
|
20. |
15, 45ХНМФА, 70, 20Х20Н14С2, 25Х1МФ, ШХ15-ШД, А12, Ст1кп, |
|
ЧН3ХМДШ, ВК10, АК12, МЛ19, ЛА77-2, БрАЖН10-4-4, ПСр50Кд |
||
|
||
|
|
25

Окончание табл. 1.5
|
№ |
|
|
|
Марки материала |
|
|
|
|
|
|
|
|
|
|
|
|||
21. |
|
08пс, 10Г2, 60Г, 15Х28, 25Х1МФ, Х12М, АЦ20ХН3, Ст5, КЧ45-7, Т17К12, |
|||||||
|
АК12, ПТ-7М, ЛС59-1, БРО4Ц7С5, ЦАМ10-5Л |
|
|
|
|||||
|
|
|
|
|
|
||||
|
|
|
|
|
|
|
|||
22. |
|
05кп, 45ХНМФА, 55С2, 45Х14Н14В2М, 20Х13, Р10К5Ф5, А40Г, Ст4, ЧХ3Т, |
|||||||
|
Т30К4, АК6М2, МА2-1, Л85, БрО6Ц6С2х, ПСрМО68-27-5 |
|
|
||||||
|
|
|
|
|
|||||
|
|
|
|
|
|
|
|||
23. |
|
30, 20ХГНТР, 60С2ХФА, 20Х20Н14С2, 12Х18Н10Т, 5Х3В3МФС, АС45Г2, |
|||||||
|
Ст3Гсп, КЧ70-2, Т30К4, АЦ4МГ, МЛ10, ЛАЖ60-1-1, БРА7, ПСР12М |
|
|||||||
|
|
|
|
||||||
|
|
|
|
|
|
|
|||
24. |
|
20Р, 38ХГМ, 70Г, 40Х9С2, 25Х1МФ, У12, АС12ХН, Ст4пс, СЧ25, ВК10, |
|||||||
|
АК10СУ, МА2-1пч, Л63, БРАЖНМЦ9-4-4-1, ПСрОСу8 |
|
|
||||||
|
|
|
|
|
|||||
|
|
|
|
|
|
|
|||
25. |
|
10пс, 40ХГТР, 50ХФА, ХН56ВМКЮ, 15Х28, ХВГ, А40ХЕ, Ст5сп, КЧ45-7, |
|||||||
|
ВК6-М, АК12, ПТ-3В, 60С2Н2А, ЛА77-2, БрАЖН10-4-4, ПСрО3-97 |
|
|||||||
|
|
|
|
||||||
|
|
|
|
|
|
|
|||
26. |
|
15; 40ХГТР; 50ХФА; 15Х28; 10Х17Н13М3Т; Р6М5; А12; Ст2сп; ЧС15М4; |
|||||||
|
Т17К12; АК9с; Вт20; ЛМцА57-3-1; БрОФ1; ПСр2 |
|
|
||||||
|
|
|
|
|
|||||
|
|
|
|
|
|
|
|||
27. |
|
20пс; 14ХГН; 70; 10Х11Н23Т3МР; 40Х13; 5Х3В3МФС; АЦ20ХН3; Ст1сп; |
|||||||
|
АЧК-2; ВК8-В; АМг10ч; МА18; ЛК80-3; БрС30; ПСр50Кд |
|
|
||||||
|
|
|
|
|
|||||
|
|
|
|
|
|
|
|||
28. |
|
25; 38Х2Ю; 50ХГА; 45Х14Н14В2М; 12Х13; 5ХНВ; АС12ХН; Ст1кп; ВЧ40; |
|||||||
|
ТТ8К7; АК7Ц9; Вт20; ЛЦ40Мц3Ж; БрОЦС4-4-4; ПСрОС2-58 |
|
|
||||||
|
|
|
|
|
|||||
|
|
|
|
|
|
|
|
||
|
|
|
|
|
|
|
Приложение к работе 1 |
||
|
|
|
|
|
Пример оформления фрагмента отчёта |
|
|
||
|
|
|
|
“Расшифровка марок машиностроительных материалов” |
|||||
|
|
|
|
|
|
|
Таблица 1.6 |
||
|
|
|
|
|
|
|
|
|
|
|
|
Заданная |
|
Наименование мате- |
Химический |
Область применения сплава |
|||
|
марка сплава |
|
риала |
состав сплава |
|||||
|
|
|
|
|
|||||
|
|
|
|
|
|
|
|
||
|
|
|
|
|
Сталь конструкцион- |
0,4 % С, |
Крупные ответственные дета- |
||
|
|
|
|
|
ли: шатуны, коленчатые валы, |
||||
|
|
|
40ХН |
|
ная легированная, |
Х ≈ 1 % Cr, |
|||
|
|
|
|
оси, зубчатые колеса, цилинд- |
|||||
|
|
|
|
|
качественная |
Н ≈ 1 % Ni |
|||
|
|
|
|
|
ры низкого давления и другие. |
||||
|
|
|
|
|
|
|
|||
|
|
|
|
|
|
|
|
|
|
|
|
|
|
|
Сталь инструмен- |
≈ 1 % С, |
Металлорежущий |
и |
измери- |
|
|
|
|
|
Х ≈ 1 % Cr, |
тельный инструмент; |
пуансо- |
||
|
|
|
ХВГ |
|
тальная легированная, |
||||
|
|
|
|
В ≈ 1 % W, |
ны и матрицы |
вырубных |
|||
|
|
|
|
|
высококачественная |
||||
|
|
|
|
|
Г ≈ 1 % Mn |
штампов |
|
|
|
|
|
|
|
|
|
|
|
||
|
|
|
|
|
|
|
|
|
|
|
|
|
|
|
Латунь двухфазная |
59 % Cu, |
|
|
|
|
|
ЛС59-1 |
|
С ≈ 1 % Pb, |
Листы, трубы, прутки |
|
|||
|
|
|
деформируемая |
|
|||||
|
|
|
|
|
≈ 40 % Zn |
|
|
|
|
|
|
|
|
|
|
|
|
|
|
|
|
|
|
|
|
|
|
|
|
26
2. МЕХАНИЧЕСКИЕ СВОЙСТВА МАТЕРИАЛОВ
Цель работы: знания основных механических характеристик материалов, назначения и методики построения диаграмм растяжения; умения определять показатели твердости, прочности и пластичности металлов и сплавов.
Общие сведения
Поведение металлов и сплавов под действием внешнего воздействия характеризуется их физическими и механическими свойствами. Физические свойства определяют поведение материалов в тепловых, гравитационных, электромагнитных и радиационных полях. К ним относят плотность, теплоемкость, температуру плавления, термическое расширение, электропроводность, магнитную проницаемость и т. д.
Механические свойства характеризуют поведение материалов под действием внешних нагрузок при разных условиях нагружения. Механические свойства зависят от вида напряженного состояния, создаваемого в образцах при испытании, скорости деформирования, температуры и характера нагрузок, которые могут быть статическими, динамическими или циклическими. К механическим свойствам относят прочность и пластичность, твердость и ударную вязкость.
Прочность – способность материалов сопротивляться деформации или разрушению под влиянием нагрузки. Показателями прочности являются предел пропорциональности σпц, предел текучести (физический σт или условный σ0,2) и временное сопротивление (предел прочности) σв.
Пластичность – способность материала деформироваться (изменять свою форму и размеры) под действием внешних нагрузок не разрушаясь и сохранять измененную форму после прекращения действия усилий. Показатели пластичности – относительное удлинение после разрыва δ (δ5 или δ10), относительное равномерное удлинение δр и относительное сужение поперечного сечения ψ.
Твёрдость – свойство материала сопротивляться упругой и пластической деформации или разрушению при локальной контактной нагрузке. Твёрдость определяют путем вдавливания в испытуемое изделие
27

с заданным усилием алмазного конуса (твёрдость по Роквеллу), четырехгранной алмазной пирамиды (твердость по Виккерсу) или стального закаленного шарика (твёрдость по Бринеллю).
На приборе Бринелля (рис. 2.1) стальной шарик диаметром D под действием усилия P оставляет лунку диаметром dотп. Значение твердости материала HB определяют по формуле:
(2.1)
где P измеряется в ньютонах, D и dотп – в миллиметрах.
Показатели прочности и пластичности исследуемого материала определяют по результатам испытания стандартных образцов на растяжение (ГОСТ 1497-84). Для испытания применяют пропорциональные плоские или цилиндрические образцы с диаметром рабочей части d0 и начальной расчетной длиной l0 (рис. 2.2, а), которая больше диаметра d0 в пять (пятикратный образец) или в
десять раз (десятикратный образец). Концевые утолщенные участки образцов служат для размещения их в захватах разрывной испытательной машины.
При испытании к образцу прикладывают осевое растягивающее усилие Р, измеряемое в ньютонах (Н), и записывают диаграмму растяжения (кривые 1...3 на рисунке 2.2, б): зависимость между усилием Pi, действующим на образец в данный момент испытания, и удлинением ∆li (кривые 1–3). С увеличением усилия Pi длина образца изменяется на величину
, |
(2.2) |
где li – длина образца при действии на него силы Pi; l0 – начальная длина образца.
Вплоть до точки A (кривая 2) деформация является только упругой, и при снятии нагрузки длина образца уменьшается до исходной длины l0.
28

Рис. 2.2. Образцы (а) и диаграммы растяжения (б)
Участок ОA является прямолинейным и для него справедлив закон Гука, т. е. величина упругой деформации прямо пропорциональна нагрузке Если усилие превышает значение Pпц, то наряду с упругой появляется пластическая деформация и диаграмма растяжения становится криволинейной. Вследствие упрочнения большинства сплавов наблюдается повышение растягивающего усилия (участок AC) вплоть до максимального Pв. (точка C). До этого момента пластическая деформация, заключающаяся в увеличении длины и уменьшении диаметра образца, равномерна по всей длине. Затем деформация становится локальной, т. е. уменьшение поперечного сечения происходит только на отдельном (местном) участке рабочей части образца. Локализация деформации ведет к образованию шейки и снижению нагрузки (участок CD). В дальнейшем происходит разрушение образца (точка D) из-за накопления внутренних дефектов.
Для получения характеристик конкретного материала, диаграмму растяжения изображают в координатах “напряжение σ – относительная деформация ε”. Для этого, ординаты кривой соответствующие силе Pi, делят на первоначальную площадь сечения образца Fo, а абсциссы li – на рабочую длину образца до испытаний l0:
σ |
Pi |
, |
(2.3) |
F |
|||
|
0 |
|
|
|
|
|
29 |
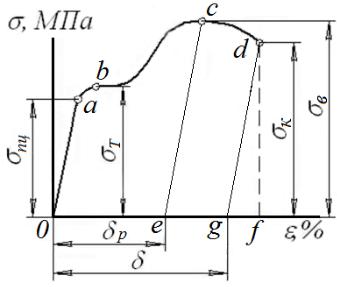
где |
F0 |
|
πd02 |
– площадь поперечного сечения образца до испытания. |
|
|
4 |
|
|||||
|
|
|
|
|
|
|
|
|
|
|
ε |
li 100 % . |
(2.4) |
|
|
|
|
|
l0 |
|
Типичный вид диаграммы для низкоуглеродистой стали приведен на рис. 2.3. На диаграмме растяжения может быть четко выраженная площадка текучести, т. е. образец деформируется без заметного увеличения растягивающей нагрузки Pт (кривая 1, рис. 2.2). Напряжение, соответствующее данному моменту, называют физическим пределом текучести σт.
Рис. 2.3. Диаграмма напряжение – относительная деформация
Хрупкие материалы не допускают большой деформации, кривая растяжения у них не имеет площадки текучести, и наибольшее усилие наблюдается при незначительном удлинении (кривая 3, рис. 2.2). Для металлических сплавов, у которых площадка текучести отсутствует, находят условный предел текучести σ0,2.
Условный предел текучести – это напряжение, при котором пластическая деформация образца составляет 0,2 % от рабочей длины образца или начальной расчетной длины по тензометру. Соответствующее усилие P0,2 находят по диаграмме (кривая 2, рис. 2.2), проводя линию, параллельную участку нагружения ОА и смещенную вдоль оси абсцисс на величину
30
∆l0,2 = 0,002l0. Точка пересечения с диаграммой растяжения (точка B) определяет нагрузку P0,2. Условный предел текучести вычисляют по формуле:
σ0,2 |
P0,2 |
, |
(2.5) |
|
|||
|
F0 |
|
где F0 – площадь поперечного сечения образца до испытания.
Предел пропорциональности σпц – это напряжение, при котором отступление от линейной зависимости между усилием и удлинением достигает такого значения, что тангенс угла наклона, образованного касательной к кривой нагружения в координатах “усилие-удлинение” в точке Pпц с осью усилий увеличивается на 50 % от своего значения на упругом (линейном) участке (точка a, рис. 2.3):
σ |
Pпц |
|
|
пц |
F |
. |
(2.6) |
|
|
|
|
|
0 |
|
|
Временное сопротивление (предел прочности) σв – напряжение, соответствующее наибольшему усилию Pв, предшествующему разрыву образца (точка c, рис. 2.3):
σв |
Pв |
. |
(2.7) |
|
|||
|
F |
|
|
|
0 |
|
|
Размеры образца до и после испытания позволяют найти показатели пластичности: относительное удлинение после разрыва δ (δ5 при l0 = 5d0 и δ10 при l0 = 10d0), относительное равномерное удлинение δр и относительное сужение ψ.
Относительное удлинение после разрыва δ – отношение абсолютного удлинения рабочей части образца (lк – l0) после разрушения к начальной расчетной длине l0, выраженное в процентах:
δ |
( lK |
l0 ) 100 % |
|
|
|
|
, |
(2.8) |
|
|
|
l0 |
|
где lк – длина рабочей части образца после испытаний.
Относительное равномерное удлинение δр – отношение приращения длины участка в рабочей части образца после разрыва, на котором определяется δр, к длине до испытания, выраженное в процентах.
31
Относительное сужение после разрыва ψ определяется как отношение разности F0 и минимальной площади поперечного сечения образца после разрушения Fш к начальной площади поперечного сечения F0, выраженное в процентах. Для цилиндрических образцов относительное сужение ψ вычисляют по формуле
ψ |
( d 2 |
d 2 |
) 100 % |
|
|
0 |
ш |
|
|
|
|
|
|
|
|
||
|
|
d |
2 |
, |
(2.9) |
|
|
|
0 |
|
|
где d0 и dш – начальный диаметр образца и минимальный диаметр шейки на образце после разрыва.
В табл. 2.1 приведены справочные значения механических свойств конструкционных сталей, используемых при проведении данной работы.
Содержание работы
Работа включает изучение основных механических характеристик материалов, диаграмм растяжения, определение показателей твердости, прочности и пластичности сплавов, составление отчета.
Таблица 2.1
Механические свойства конструкционных сталей
№ |
Марка |
σ0,2, |
σв, |
|
δ, |
Ψ, |
HB, |
||||
п/п |
сплава |
МПа |
МПа |
% |
% |
МПа |
|||||
|
|
|
|
|
|
|
|
|
|
|
|
1 |
Ст3 кп |
195... |
235 |
360... |
460 |
24 |
...27 |
50... |
60 |
1240... |
1540 |
|
|
|
|
|
|
|
|
|
|
|
|
2 |
Ст3 |
205... |
245 |
370... |
480 |
23... |
26 |
50... |
59 |
1260... |
1560 |
|
|
|
|
|
|
|
|
|
|
|
|
3 |
Ст4 кп |
225... |
255 |
400... |
510 |
22... |
25 |
48... |
55 |
1500... |
1800 |
|
|
|
|
|
|
|
|
|
|
|
|
4 |
Ст4 пс |
235... |
265 |
410... |
530 |
21... |
24 |
47... |
54 |
1520... |
1820 |
|
|
|
|
|
|
|
|
|
|
|
|
5 |
Ст5 |
255... |
285 |
490... |
630 |
19... |
22 |
45... |
52 |
1580... |
1880 |
|
|
|
|
|
|
|
|
|
|||
6 |
08 |
200 |
315... |
330 |
33 |
60 |
1090... |
1310 |
|||
|
|
|
|
|
|
|
|
|
|||
7 |
08Ю |
220 |
255... |
360 |
36 |
60 |
1100... |
1180 |
|||
|
|
|
|
|
|
|
|
|
|||
8 |
10 кп |
210 |
275... |
330 |
31 |
55 |
1140... |
1430 |
|||
|
|
|
|
|
|
|
|
|
|||
9 |
10 |
210 |
315... |
340 |
31 |
60 |
1230... |
1430 |
|||
|
|
|
|
|
|
|
|
|
|||
10 |
20 |
250 |
350... |
430 |
25 |
55 |
1370... |
1670 |
|||
|
|
|
|
|
|
|
|
|
|||
11 |
30 |
300 |
430... |
500 |
21 |
50 |
1430... |
1790 |
|||
|
|
|
|
|
|
|
|
|
|||
12 |
40 |
340 |
530... |
580 |
19 |
45 |
1670... |
1970 |
|||
|
|
|
|
|
|
|
|
|
|
|
|
Последовательность выполнения работы
32