
3 сем / ТКМ. Лаб. практикум_2022 - копия
.pdfособенностей подготовки заготовок (наличие разделки кромок и вид сварного шва);
2.6. Запишите в протоколе измерений (Приложение к работе 9) технический паспорт электрода, его диаметр и длину;
3.6. Проведите клеймение и определите вес исходных заготовок; 4.6. Проследите за сваркой заготовок, соблюдая правила техники
безопасности для сварочных работ. Зафиксируйте среднее значение сварочного тока Iсв и время горения дуги t0.
Примечание. Опыт повторить 2...3 раза при смене пространственного положения сварного шва или с использованием электродов разных марок.
5.6. Очистите сварной шов от шлака и брызг расплавленного металла. Определите расход сварочно-наплавочных материалов, измерив длину электрода и взвесив каждое сварное изделие. Результаты измерений занесите в таблицу П.1 протокола измерений;
6.6. Рассчитайте по формулам 9.11÷9.15 коэффициенты наплавки αн, расплавления αр и потерь ψ, производительность П сварки:
αн |
Gн |
/ Iсв |
t0 |
|
, |
(9.11) |
|
|
|
|
|
||
αр |
Gр |
/ Iсв |
t0 |
|
, |
(9.12) |
|
|
|
|
|
где αр – коэффициент расплавления, характеризующий массу расплавленного электрода (стержня) в единицу времени при токе 1 А, г/А∙ч; Gр – масса расплавленного электрода, определяемая по разности масс электрода до и после сварки:
G ρ l |
l |
πd 2 |
/4 |
, |
(9.13) |
|
р |
эл |
св |
э |
|
где ρ – плотность металла электрода (ρ = 7,85 г/см3); lэ и lсв – длина электрода до и после сварки, см; dэ – диаметр электрода, см.
Коэффициент потерь металла электрода при сварке на угар и разбрызгивание ψ, % :
ψ |
Gр |
Gн |
100 % (1 |
|
α |
н |
) 100 % , |
(9.14) |
Gр |
|
|
||||||
|
|
|
αр |
|
||||
Производительность сварки П, г/ч определите по формуле: |
|
|||||||
|
|
|
П αн Iсв , |
|
|
|
|
(9.15) |
123
Скорость сварки vсв, м/ч, определите по формуле 9.10. Расчетные данные занесите в таблицу П.2 протокола.
7.6. Оформите отчёт и сделайте выводы о влиянии условий проведения и параметров сварки на расход электродов и производительность сварочного процесса.
Содержание отчёта
1.Наименование работы.
2.Номер, формулировка и исходные данные индивидуального задания (табл. 9.2) «Определение технологических параметров ручной дуговой сварки».
3.Эскиз заданного сварного шва с указанием его размеров и обозначением сварного соединения (ГОСТ, вид, способ сварки и вспомогательные знаки).
4.Марка, обозначение и характеристики выбранного электрода.
5.Расчёты напряжения и силы сварочного тока Iсв по формулам (9.1) и (9.5), полной и эффективной тепловой мощности дуги по формулам (9.2) и (9.3). Сводная таблица результатов расчета (по форме таблицы 9.3).
6.Расчёты по формулам (9.6)÷(9.10) массы наплавленного металла Gн, времени горения дуги t0, полного времени T и скорости сварки vсв, расхода электродов Gм и электроэнергии Pэ (таблица 9.4)
7.Сварочное оборудование и его характеристики.
8.Приложение. Протокол измерений (по далее приведенной форме).
9.Выводы о влиянии параметров сварочного процесса на условия ее выполнения
Приложение к работе 9
ПРОТОКОЛ ИЗМЕРЕНИЙ
к лабораторной работе «Технология ручной дуговой сварки» Дата проведения эксперимента «___» _____________20__г.
1. Условия проведения эксперимента
1.Сварочное оборудование: _____________________________________
2.Марка электрода: ___________________________________________
3.Вид шва: ___________________________________________________
124
4. Исходные размеры образцов: длина образцов L = |
мм; |
толщина |
||||||||||||
металла S0 = |
мм; масса исходных заготовок Gисх, = |
г. |
|
|
||||||||||
2. Таблица измерений |
|
|
|
|
|
|
|
|
||||||
|
|
|
|
|
|
|
|
|
|
|
|
|
Таблица П. 1 |
|
|
Измерение размеров электрода и параметров сварки |
|||||||||||||
|
|
|
|
|
|
|
|
|
|
|
|
|
||
№ опыта |
|
Размеры электрода, мм |
|
Параметры сварки |
||||||||||
|
|
|
|
|
|
|
|
|
|
|
|
|
|
|
|
dэ |
|
lэ |
lсв |
Iсв, А |
|
t0, ч |
|
Gн, г |
|
Gр, г |
|||
|
|
|
|
|
|
|||||||||
|
|
|
|
|
|
|
|
|
|
|
|
|
|
|
1 |
|
|
|
|
|
|
|
|
|
|
|
|
|
|
|
|
|
|
|
|
|
|
|
|
|
|
|
|
|
2 |
|
|
|
|
|
|
|
|
|
|
|
|
|
|
|
|
|
|
|
|
|
|
|
|
|
|
|
|
|
3. Результаты расчёта |
|
|
|
|
|
|
|
|
||||||
|
|
|
|
|
|
|
|
|
|
|
|
|
Таблица П. 2 |
|
|
|
Расчетные характеристики сварочного процесса |
|
|
||||||||||
|
|
|
|
|
|
|
|
|
|
|
||||
№ опыта |
αн, г/А∙ч |
αр, |
г/А∙ч |
|
ψ, % |
|
П, г/ч |
|
|
vсв, м/ч |
||||
1 |
|
|
|
|
|
|
|
|
|
|
|
|
|
|
|
|
|
|
|
|
|
|
|
|
|
|
|
|
|
2 |
|
|
|
|
|
|
|
|
|
|
|
|
|
|
|
|
|
|
|
|
|
|
|
|
|
|
|
|
|
10. ИССЛЕДОВАНИЕ ВЛИЯНИЯ ХИМИЧЕСКОГО СОСТАВА СПЛАВОВ НА СВАРИВАЕМОСТЬ
Цель работы: знания методики технологических испытаний материалов на свариваемость, основных дефектов сварного шва и причин их возникновения; умения оценить свариваемость сплавов при известном химическом составе и правильно выбрать материал для сварного изделия.
Общие сведения
Технологические свойства сплавов при сварке оцениваются свариваемостью, т. е. способностью образовывать соединения, равнопрочные с основным металлом, без разрушения и трещин. На свариваемость сплавов влияют их механические свойства, в первую очередь пластичность, химический состав, а также условия сварки (температура изделий и окружающей среды, режим последующего охлаждения).
125

Испытания сплавов на свариваемость проводят различными методами. Наиболее простым испытанием является заварка кольцевой V-образной проточки на металлических пластинах (рис. 10.1) ручной дуговой сваркой. При этом можно обеспечить различные условия сварки: с предварительным подогревом изделия, при комнатной температуре, а также при отрицательной температуре (на морозе). Данное условие можно создать при охлаждении пластины водой, подаваемой снизу. Этот прием соответствует также сварке толстолистовых деталей и сварке при воздействии атмосферных осадков вне производственных помещений.
Основными дефектами сварных соединений, зависящими от квалификации сварщика, являются непровары, подрезы, наплывы, газовые и шлаковые включения. Коробление изделия, микро- и макротрещины появляются из-за неравномерного теплового расширения и усадки – уменьшения размеров шва при кристаллизации металла.
В зоне сварного шва происходит локальная пластическая деформа-
ция, вызывающая появление дефектов в виде трещин при недостаточной пластичности материала. Вероятность появления трещин, которые в сварных изделиях недопустимы, зависит от химического состава сплава (например, от содержания углерода в стали), определяющего пластические свойства и склонность к закалке.
Рис. 10.1. Образец для оценки свариваемости
126
Основные способы улучшения свариваемости:
1.Выбор для сварных изделий высокопластичных материалов.
2.Предварительный подогрев деталей, повышающий пластичность стали, снижающий перепады температуры, а также скорость охлаждения зоны сварки.
3.Термическая обработка (отжиг) после сварки для снятия внутренних напряжений и получения требуемой микроструктуры.
Исходя из химического состава, все конструкционные стали разделяют по свариваемости на четыре группы, которые требуют различных условий сварки для обеспечения надежного равнопрочного сварного соединения.
I группа – хорошо сваривающиеся стали. К ним относятся стали углеродистые с содержанием углерода менее 0,25 %, а также малолегированные стали с содержанием углерода менее 0,2 %. Эти стали свариваются без
трещин при температуре окружающей среды до –20 С, так как они обладают высокой пластичностью и не подвержены закалке.
II группа – удовлетворительно сваривающиеся стали. У них содержание углерода или его эквивалента находится в пределах 0,25...0,35 %. Эти стали свариваются без дефектов при температуре окружающей среды выше 5 С. В иных случаях, а также при толщине металла более 25 мм необходим подогрев перед сваркой до температуры 50...100 С.
III группа – ограниченно сваривающиеся стали. Имеют содержание углерода или его эквивалента 0,35...0,45 %. Эти стали для обеспечения равнопрочного соединения требуют подогрев деталей перед сваркой до температуры 100...200 С и термическую обработку после сварки.
IV группа – плохо сваривающиеся стали. Это стали с содержанием углерода или его эквивалента более 0,5 %. В данном случае должны быть осуществлены предварительный подогрев до температуры 250...350 С и термообработка после выполнения сварки.
Содержание работы
Работа включает: изучение методики технологических испытаний материалов на свариваемость, основных дефектов сварного шва и причин
127
их возникновения; умения оценить свариваемость сплавов при известном химическом составе и правильно выбрать условия сварки и термической обработки сварного изделия, составление отчёта
Последовательность выполнения работы
1.Укажите сущность сварки плавлением и свариваемости сталей и сплавов.
2.Изобразите схему ручной дуговой сварки с обозначением основных элементов сварочного процесса.
3.Ознакомьтесь с методикой оценки свариваемости и выполните эскиз образца для оценки свариваемости (см. рис. 10.1).
4.Определите эквивалентное содержание углерода Cэ сплавов заданных образцов и группу их свариваемости (I, II, III, IV), используя формулу:
,
где Cэ – эквивалентное содержание углерода, %, позволяющее оценить влияние химического состава на свариваемость сталей при содержании в них легирующих элементов до 5 %; C, Mn, Ni, Cr, Mo, V – содержание в стали углерода, марганца, никеля, хрома, молибдена или ванадия, %.
5.Изучите с помощью лупы качество сварного шва, выявите наличие (отсутствие) трещин в сварном шве и/или в зоне термического влияния. Заполните таблицу 10.1 (см. Приложение к работе 10).
6.Объясните причины возникновения сварных трещин. Укажите в таблице 10.2 условия бездефектной сварки для различных групп стали и чугуна, вид термической обработки после сварки изделий.
7.Сопоставьте группы сталей по свариваемости для всех рассматриваемых технологических проб и объясните в выводах причины возникновения сварных трещин.
8.Оцените свариваемость сталей, чугуна и цветных сплавов по индивидуальному заданию к работе 1 (см. табл. 1.5).
9.Оформите отчёт по работе.
Содержание отчёта
1. Название и цель работы.
128
2.Сущность сварки плавлением. Свариваемость сталей и сплавов.
3.Схема ручной дуговой сварки с обозначением основных элементов сварочного процесса.
4.Эскиз образца для оценки свариваемости с изображением сварного шва и его дефектов.
5.Расчет эквивалентного содержания углерода для заданных марок сплавов. Определение группы стали по свариваемости.
6.Результаты расчетов и визуального осмотра образцов на наличие трещин в сварных швах (см. табл. 10.1).
7.Рекомендации по условиям бездефектной сварки заданных групп сталей и чугуна (см. табл. 10.2).
8.Выводы о причинах фактических дефектов на пробах.
9.Номер, исходные данные индивидуального задания и оценка свариваемости заданных материалов (см. табл. 10.3).
Приложение к работе 10. Пример оформления фрагмента отчета
«Исследование влияния химического состава сплавов на свариваемость»
6. Эквивалентное содержание углерода. Группа стали по свариваемости. Наличие и виды дефектов сварных швов.
|
|
|
|
|
|
Таблица 10.1 |
|
|
|
Условия сварки, наличие и вид дефектов |
|
||||
|
|
|
|
|
|
|
|
|
|
|
|
Условия сварки пробы |
|||
№ |
|
C, |
Группа |
|
|
|
|
Сплав |
Предвари- |
Естественное |
Охлаждение |
||||
п/п |
Сэ,% |
стали |
тельный по- |
охлаждение |
водой (сварка |
||
|
|||||||
|
|
|
|
догрев |
на воздухе |
на морозе) |
|
|
|
|
|
|
|
|
|
1 |
10Г |
С 0,2 |
I |
– |
Нет |
Нет |
|
|
|
|
|
|
|
|
|
|
|
С=0,4 |
|
350 С |
Трещины в |
Трещины в |
|
2 |
40Х |
0Сэ=0, |
IV |
||||
Нет |
шве и в ЗТВ |
шве и в ЗТВ |
|||||
|
|
5 |
|
||||
|
|
|
|
|
|
||
|
|
|
|
|
|
|
7. Рекомендации по условиям бездефектной сварки заданных групп сталей и чугуна
129

|
|
Таблица 10.2 |
|
|
Рекомендации по бездефектной сварке |
||
|
|
|
|
|
|
Вид и режимы терми- |
|
Сплав |
Условия бездефектной сварки |
ческой обработки |
|
|
|
сварного изделия |
|
|
|
|
|
1-ой группы |
Естественные условия, допустима сварка |
не требуется |
|
на морозе при температуре до –20 С |
|||
|
|
||
|
|
|
|
2-ой группы |
|
|
|
|
|
|
|
3-ей группы |
|
|
|
|
|
|
|
4-ой группы |
|
|
|
|
|
|
|
|
1. Холодная сварка: |
|
|
Чугун |
2. Горячая сварка: |
|
|
|
|
||
|
|
|
8.Выводы о причинах фактических дефектов на пробах: __________
9.Оценка свариваемости заданных материалов.
|
|
|
|
|
Таблица 10.3 |
|
Свариваемость сталей и сплавов |
|
|||
|
|
|
|
|
|
Заданная |
Химиче- |
Углеродный |
Сваривае- |
|
Условия бездефектной |
ский состав |
эквивалент |
|
|||
марка |
мость |
|
сварки |
||
сплава |
Сэ, % |
|
|||
|
|
|
|
||
|
|
|
|
|
|
|
0,4 % С, |
|
Плохо сва- |
|
Подогрев до |
40ХН |
≈ 1 % Cr, |
0,57 |
риваемая |
|
200...300 С, после |
|
≈ 1 % Ni |
|
сталь |
|
сварки – отжиг |
|
|
|
|
|
|
|
0,1 % С, |
|
Ограниченно |
|
При наличии требова- |
10Х23Н18 |
23 % Cr, |
>0,5 |
|
ний к МКК подогрев |
|
свариваемая |
|
||||
|
18 % Ni |
|
|
до 350 С |
|
|
|
|
|
||
|
|
|
|
|
|
|
|
|
|
|
при толщине > 10 мм с |
АК7Ц9 |
≈ 7 % Si, |
|
|
|
предварительным ме- |
≈ 9 % Zn, |
– |
Хорошая |
|
стным или общим по- |
|
(АЛ11) |
|
||||
≈ 83 % Al |
|
|
|
догревом до темпера- |
|
|
|
|
|
||
|
|
|
|
|
туры 200 С |
|
|
|
|
|
|
130
11. ЛИТЕЙНОЕ ПРОИЗВОДСТВО
Цель работы: знание основ литейного производства и последовательности изготовления отливок; формирование представления о модельном комплекте и технологии изготовления литейной формы и отливки; умения выделять особенности литейного производства; развитие технологического мышления в области методов производства заготовок.
Общие сведения
Литейным производством называют процессы получения фасонных изделий (отливок) путем заливки расплавленного металла в полую форму, воспроизводящую конфигурацию и размеры будущей детали. Литьём изготавливают металлические отливки различной формы, размеров и массы с разной степенью точности и шероховатости поверхности, как в единичном, так и в массовом производстве.
В настоящее время доля деталей, изготовляемых из отливок, составляет 30...80 % от массы изделия (примерно 60 % у сельскохозяйственных машин, до 85 % у металлорежущих станков и прессового оборудования). Производство отливок может осуществляться различными способами. Среди них наиболее распространенным является литье в разовые песчаноглинистые формы.
Литьё в разовые песчано-глинистые формы
Производство отливок в разовых песчано-глинистых формах характеризуется универсальностью, доступностью формовочных материалов и относительно невысокой стоимостью. К недостаткам этого способа следует отнести: пониженные механические свойства материала, невысокую точность и грубую поверхность отливок, большой объем исходных материалов и значительные отходы, загрязняющие окружающую среду.
Технологический процесс производства отливок (рис. 11.1) состоит из ряда основных и вспомогательных операций, осуществляемых как параллельно, так и последовательно на различных участках литейного цеха. После разработки технологичной конструкции отливки производится проектирование и изготовление модельно-опочного комплекта оснастки (мо-
131
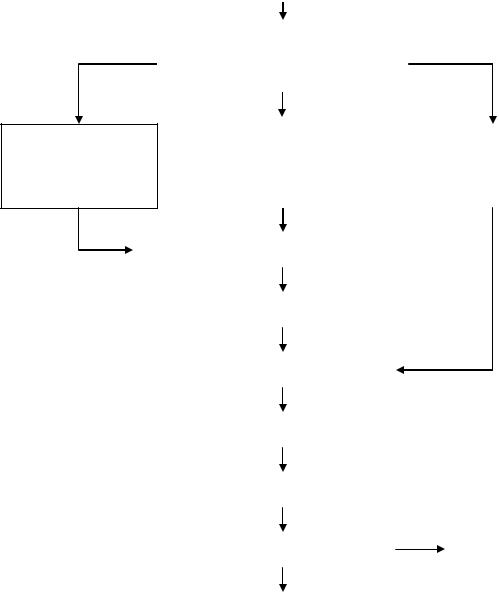
дели отливки и элементов литниковой системы, стержневые ящики, опоки и модельные плиты).
Изготовление
модельного
комплекта
Проектирование технологич- |
|
|
||
|
ной отливки |
|
|
|
|
|
|
|
|
|
|
|
|
|
Разработка технологического |
|
|
||
процесса и технологической |
|
|
||
|
документации |
|
|
|
|
|
|
|
|
|
|
|
|
|
|
Приготовление |
|
|
|
|
|
|
Приготовление |
|
|
формовочных и |
|
|
|
|
|
|
расплавленного |
|
|
стержневых смесей |
|
|
|
|
|
|
металла |
|
|
|
|
|
|
|
|
|
|
|
Изготовление стержней и полуформ |
|
|
||
|
|
|
|
|
|
|
|
|
|
|
Сборка форм |
|
|
|
|
|
|
|
|
|
|
|
|
|
|
Заливка форм |
|
|
|
|
|
|
|
|
|
|
|
|
|
|
Выбивка форм |
|
|
|
|
|
|
|
|
|
|
|
|
|
|
Очистка и обрубка отливок |
|
|
|
|
|
|
|
|
|
|
|
|
|
|
|
|
|
Исправление |
|
Контроль качества отливок |
|
||
|
|
|
дефектов |
|
|
|
|
|
|
|
|
|
|
|
|
|
|
|
|
|
|
|
|
|
|
Термообработка |
|
|
|
|
|
|
|
|
Рис. 11.1. Структурная схема получения отливок
Модель – приспособление, с помощью которого в литейной форме получают полость, которая по размерам и внешним очертаниям соответствует будущей отливке. Для получения отливок с отверстиями или углубле-
132