
3 сем / ТКМ. Лаб. практикум_2022 - копия
.pdf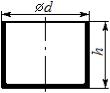
5.Произведите под руководством учебного мастера вытяжку колпачков из плоских заготовок, меняя комплекты матриц и пуансонов, фиксируя
втабл. 8.2 наибольшее усилие вытяжки, размеры изделия, а также наличие и вид дефектов. Изобразите эскизы деталей с полученными размерами.
6.Произведите повторную вытяжку из полученных бездефектных колпачков на меньший диаметр, выполняя требования п. 5.
7.Определите предельно допустимую степень вытяжки для первой и последующих операций.
8.Разрежьте по диаметру один колпачок, измерьте толщину на донной части и цилиндрической стенке с шагом 2...5 мм. Значения толщины ука-
жите на эскизе детали. Найдите отклонения hj полученной толщины hj от исходной h0 ( hj = hj − h0) и постройте эпюру относительного изменения толщины стенки и донной части детали hj /h0 в продольном разрезе.
|
|
|
|
|
|
|
|
Таблица 8.2 |
|
|
|
Параметры вытяжки деталей |
|
|
|
||||
|
|
|
|
|
|
|
|
|
|
Номер |
Мате- |
|
Размеры, мм |
|
Степень вы- |
Усилие |
|
Наличие |
|
|
|
|
|
|
|
|
|
||
Заготовка |
Деталь |
тяжки |
пресса |
|
и вид |
||||
опыта |
риал |
|
|||||||
|
|
|
|
ki |
P, кН |
|
дефекта |
||
|
|
h0 |
Di-1 |
di |
H |
|
|||
|
|
|
|
|
|
|
|
|
|
9.Получите индивидуальное задание (таблица 8.3) по определению диаметра исходной заготовки.
10.Составьте отчёт по работе.
Таблица 8.3
Индивидуальные задания
№ |
Эскиз детали |
|
|
Размеры поковки, мм |
|
|
|||
п/п |
|
|
|
|
|
|
|
|
|
d |
d1 |
d2 |
h |
r |
S |
|
|
||
|
|
|
|||||||
1. |
|
70 |
- |
- |
90 |
- |
2,0 |
|
|
|
|
|
|
|
|
|
|
|
|
2. |
|
60 |
- |
- |
80 |
- |
1,6 |
|
|
|
|
|
|
|
|
|
|
|
|
3. |
|
50 |
- |
- |
70 |
- |
1,5 |
|
|
|
|
|
|
|
|
|
|
|
|
4. |
|
40 |
- |
- |
60 |
- |
1,0 |
|
|
|
|
|
|
|
|
|
|
|
|
5. |
|
30 |
- |
- |
50 |
- |
0,8 |
|
|
|
|
|
|
|
|
|
|
|
|
103

|
|
|
|
|
|
|
Окончание табл. 8.3 |
|||
|
|
|
|
|
|
|
|
|
|
|
№ |
Эскиз детали |
|
|
Размеры поковки, мм |
|
|||||
п/п |
|
|
|
|
|
|
|
|
|
|
d |
d1 |
d2 |
h |
r |
|
S |
|
|
||
|
|
|
|
|||||||
|
|
|
|
|
|
|
|
|
|
|
6. |
|
60 |
40 |
- |
70 |
10 |
|
2,0 |
|
|
|
|
|
|
|
|
|
|
|
|
|
7. |
|
50 |
34 |
- |
60 |
8 |
|
1,6 |
|
|
|
|
|
|
|
|
|
|
|
|
|
8. |
|
40 |
28 |
- |
50 |
6 |
|
1,2 |
|
|
|
|
|
|
|
|
|
|
|
|
|
9. |
|
30 |
20 |
- |
40 |
5 |
|
1,0 |
|
|
|
|
|
|
|
|
|
|
|
|
|
10. |
|
20 |
12 |
- |
30 |
4 |
|
0,8 |
|
|
|
|
|
|
|
|
|
|
|
|
|
11. |
|
80 |
- |
100 |
55 |
- |
|
1,6 |
|
|
|
|
|
|
|
|
|
|
|
|
|
12. |
|
70 |
- |
90 |
50 |
- |
|
1,2 |
|
|
|
|
|
|
|
|
|
|
|
|
|
13. |
|
60 |
- |
80 |
45 |
- |
|
1,0 |
|
|
|
|
|
|
|
|
|
|
|
|
|
14. |
|
50 |
- |
60 |
35 |
- |
|
0,8 |
|
|
|
|
|
|
|
|
|
|
|
|
|
15. |
|
40 |
- |
50 |
30 |
- |
|
0,5 |
|
|
|
|
|
|
|
|
|
|
|
|
|
16. |
|
90 |
70 |
130 |
60 |
10 |
|
2,0 |
|
|
|
|
|
|
|
|
|
|
|
|
|
17. |
|
80 |
64 |
120 |
50 |
8 |
|
1,6 |
|
|
|
|
|
|
|
|
|
|
|
|
|
18. |
|
70 |
58 |
100 |
40 |
6 |
|
1,2 |
|
|
|
|
|
|
|
|
|
|
|
|
|
19. |
|
60 |
50 |
80 |
30 |
5 |
|
1,0 |
|
|
|
|
|
|
|
|
|
|
|
|
|
20. |
|
50 |
42 |
60 |
25 |
4 |
|
0,8 |
|
|
|
|
|
|
|
|
|
|
|
|
|
21. |
|
120 |
100 |
130 |
50 |
10 |
|
2,0 |
|
|
|
|
|
|
|
|
|
|
|
|
|
22. |
|
100 |
84 |
120 |
40 |
8 |
|
1,6 |
|
|
|
|
|
|
|
|
|
|
|
|
|
23. |
|
80 |
68 |
110 |
30 |
6 |
|
1,2 |
|
|
|
|
|
|
|
|
|
|
|
|
|
24. |
|
60 |
50 |
90 |
25 |
5 |
|
1,0 |
|
|
|
|
|
|
|
|
|
|
|
|
|
25. |
|
50 |
42 |
80 |
20 |
4 |
|
0,8 |
|
|
|
|
|
|
|
|
|
|
|
|
|
26. |
|
90 |
70 |
- |
50 |
- |
|
2,0 |
|
|
|
|
|
|
|
|
|
|
|
|
|
27. |
|
80 |
60 |
- |
45 |
- |
|
1,6 |
|
|
|
|
|
|
|
|
|
|
|
|
|
28. |
|
70 |
50 |
- |
35 |
- |
|
1,2 |
|
|
|
|
|
|
|
|
|
|
|
|
|
29. |
|
60 |
40 |
- |
30 |
- |
|
1,0 |
|
|
|
|
|
|
|
|
|
|
|
|
|
30. |
|
50 |
30 |
- |
25 |
- |
|
0,8 |
|
|
|
|
|
|
|
|
|
|
|
|
|
31. |
|
100 |
80 |
120 |
55 |
- |
|
2,0 |
|
|
|
|
|
|
|
|
|
|
|
|
|
32. |
|
90 |
70 |
100 |
50 |
- |
|
1,6 |
|
|
|
|
|
|
|
|
|
|
|
|
|
33. |
|
80 |
60 |
80 |
45 |
- |
|
1,2 |
|
|
|
|
|
|
|
|
|
|
|
|
|
34. |
|
70 |
50 |
60 |
35 |
- |
|
1,0 |
|
|
|
|
|
|
|
|
|
|
|
|
|
35. |
|
60 |
40 |
50 |
30 |
- |
|
0,8 |
|
|
|
|
|
|
|
|
|
|
|
|
|
104
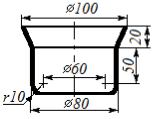
Содержание отчёта
1.Схема вытяжки и ее описание.
2.Напряженно-деформированное состояние материала.
3.Расчет коэффициентов вытяжки.
4.Расчет усилия вытяжки.
5.Эскизы заготовки и полученных изделий.
6.Таблица опытных данных (см. табл. 8.2).
7.Эпюра изменения толщины стенки детали.
8.Выводы о допустимой для данного материала степени вытяжки, соответствии опытных и расчетных значений, характере и причинах разнотолщинности деталей, об основных приемах расширения технологических возможностей вытяжки.
9.Номер, формулировка и исходные данные индивидуального задания: «Определение диаметра исходной заготовки для вытяжки» (по форме Приложения к работе 8).
9.1.Эскиз детали с размерами по индивидуальному заданию.
9.2.Эскизы отдельных поверхностей детали, формулы для определения их площади и расчеты.
9.3.Расчет площади поверхности готовой детали и диаметра исходной заготовки.
Приложение к работе 8 Пример оформления фрагмента отчёта
«Определение диаметра исходной заготовки для вытяжки»
9.1.Эскиз детали
9.2.Эскизы отдельных поверхностей детали и расчёт площади поверхности (см. табл. 8.4).
105

Таблица 8.4
Площадь отдельных поверхностей детали
№ |
Эскиз поверхности |
|
Площадь поверхности, мм2 |
||
п/п |
|
||||
|
|
|
|
|
|
|
|
|
|
|
|
1. |
|
|
|
|
|
|
|
|
|
|
|
|
|
|
|
|
2.
3.
4.
9.3. Площадь поверхности детали и диаметр исходной заготовки Площадь поверхности готовой детали:
Диаметр исходной заготовки:
9. ТЕХНОЛОГИЯ РУЧНОЙ ДУГОВОЙ СВАРКИ
Цель работы: знания о назначении сварки, об особенностях технологии ручной дуговой сварки; умения выбирать тип сварного шва и электроды для получения неразъемных соединений, определять технологические параметры сварки; формировать конструкторско-технологическое мышление и компетенции в области производства сварных конструкций.
Общие сведения
Сварка является наиболее распространенным способом получения неразъемных соединений. Она применяется практически во всех областях техники для получения сложных по форме изделий любых размеров. Сваривают металлы, некоторые виды керамики и пластмасс, стекло и разно-
106
родные материалы. Сварку осуществляют на земле, под водой и в космосе. Сварные конструкции работают при знакопеременных и динамических нагрузках, при высоких температурах и давлениях.
Сварка – процесс получения неразъемного соединения путем образования межатомных связей по контактируемым поверхностям соединяемых заготовок при их нагреве, пластическом деформировании или при совместном действии того и другого. Для осуществления соединения необходимо освободить свариваемые поверхности от загрязнений (органических пленок, оксидов и адсорбированных газов), сблизить поверхности на расстояние, соизмеримое с параметром кристаллической решетки свариваемых материалов, или обеспечить энергетическую активацию поверхностных атомов для облегчения их взаимодействия друг с другом. В зависимости от степени воздействия внешних факторов и состояния металла в зоне соединения различают способы сварки плавлением и давлением.
При сварке плавлением атомно-молекулярные связи между деталями создают, оплавляя примыкающие поверхности заготовок так, чтобы получилась смачивающая их общая ванна расплавленного металла, который затвердевает при охлаждении и соединяет детали в единое целое. Для заполнения зазора между соединяемыми деталями и формирования сварочной ванны расплавляют дополнительный (присадочный) металл. К сварке плавлением относят дуговую сварку, электрошлаковую, газовую, плазменную, лазерную, электронно-лучевую и термитную.
При сварке давлением обязательным условием является совместная пластическая деформация соединяемых заготовок. Для уменьшения усилия деформирования может применяться подогрев металла в зоне контакта до пластичного состояния, при этом температура нагрева обычно ниже температуры плавления. В некоторых процессах осуществляется кратковременный нагрев зоны соединения до расплавления с последующим сжатием заготовок. Виды сварки давлением: холодная, ультразвуковая, трением, взрывом, контактная, высокочастотная, диффузионная и другие.
Дуговая сварка
Дуговой сваркой называется сварка плавлением, при которой нагрев кромок свариваемых деталей осуществляется теплотой электрической ду-
107
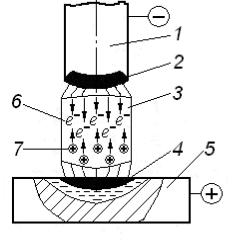
ги. В зависимости от способов защиты зоны сварки от кислорода воздуха различают: ручную дуговую сварку, автоматическую сварку под слоем флюса и дуговую сварку в среде защитных газов.
Сварочная дуга представляет собой стабильный электрический разряд (электрический ток высокой плотности) в ионизированной среде газов и паров металла. Ионизация дугового промежутка происходит во время зажигания дуги и непрерывно поддерживается в процессе ее горения. По длине дугового промежутка дуга разделяется на три области (рис. 9.1): катодную, анодную и находящийся между ними столб дуги.
Катодная область включает в себя нагретую поверхность электрода 1, называемую катодным пятном 2, и часть дугового промежутка, примыкающую к ней. Температура катодного пятна для стальных электродов достигает 2400...2700 °С. На нем выделяется до 38 % общей теплоты дуги. Основным физическим процессом в этой области является электронная эмиссия и разгон электронов 6.
Анодная область состоит из анодного пятна 4, находящегося на поверхности расплавленного металла изделия 5, и части дугового промежутка, примыкающего к нему. Анодное пятно является местом входа и нейтрализации свободных электронов в материале анода. В результате бомбардировки электронами на нем выделяется больше тепловой энергии, чем на катоде. Температура анода достигает 2500…2900 °С. При сварке дугой переменного тока температуры анода и катода выравниваются вследствие периодической смены полярности.
В столбе дуги 3 основным физическим процессом является ионизация газа 7, которая происходит в результате соударения заряженных (в первую очередь электронов) и нейтральных частиц газа. Температура столба дуги достигает 6000...7000 °С. Электрические свойства дуги опи-
сываются статической вольт-амперной характеристикой, представляю-
108
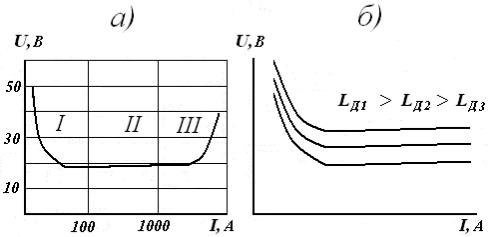
щей собой зависимость между напряжением и током дуги в состоянии устойчивого горения при постоянной длине дуги.
Кривая статической характеристики (рис. 9.2, а) состоит из трех участков: падающего I, жесткого II и возрастающего III. На участке I с повышением силы тока увеличивается степень ионизации среды с увеличением площади сечения столба дуги и его электропроводности, и напряжение для поддержания дуги уменьшается. Дуга в этой области отличается малой устойчивостью, что ограничивает ее применение.
Рис. 9.2. Статическая вольт-амперная характеристика дуги (а) и зависимость напряжения дуги от ее длины (б)
На участке II пропорционально силе тока возрастает сечение столба дуги, а плотность тока и падение напряжения в дуге остаются постоянными. Дуга при этом горит устойчиво и обеспечивает нормальный процесс сварки. На участке III при повышении тока рост сечения дуги ограничивается сечением электрода, т. е. диаметр катодного пятна становится равным диаметру электрода и увеличиваться дальше не может. В результате чего возрастает плотность тока и напряжение дуги.
При изменении длины дуги кривая вольт-амперной характеристики будет менять свое месторасположение (рис. 9.2, б). Напряжение дуги UД в диапазоне устойчивых режимов пропорционально ее длине:
UД a b LД , |
(9.1) |
где LД – длина дуги (0 < LД <8 мм); a – сумма падений напряжения в катодной и анодной области; b – коэффициент, выражающий среднее падение
109
напряжения на единицу длины дуги. Величины a и b зависят от рода свариваемого металла, состава газовой среды (например, наличия легко ионизующихся компонентов Ca, Na, K и т. п.) и других факторов (для стальных электродов а = 10 В, b = 2 В/мм при LД = 2... 8 мм).
Разные участки вольт-амперной характеристики дуги соответствуют внешней характеристике источника питания (зависимость напряжения на его клеммах от тока в электрической цепи) конкретного способа сварки. При ручной дуговой и сварке в защитных газах неплавящимся электродом внешняя характеристика дуги – падающая с переходом к жесткой, при автоматической сварке под флюсом – жесткая с переходом к возрастающей, при сварке в защитном газе плавящимся электродом – возрастающая.
Подводимая к свариваемому изделию теплота характеризуется величиной тепловой мощности дуги. Полная тепловая мощность дуги Q, Дж/с:
Q k Jсв UД , |
(9.2) |
где k – коэффициент несинусоидальности напряжения и тока (для постоянного тока k = 1, для переменного – k = 0,7…0,97), Jсв – сварочный ток, А; UД – напряжение дуги, В.
Часть мощности дуги теряется в результате теплоотдачи в окружающую среду. Количество теплоты, используемое на нагрев и расплавление электрода и основного металла в единицу времени, называется эффектив-
ной тепловой мощностью дуги Qэф, Дж/с:
Qэф η Q , |
(9.3) |
где – коэффициент полезного действия дуги, зависящий от способа сварки, вида и состава сварочных материалов. Для сварки в защитных газах, ручной дуговой сварки металлическими электродами и автоматической сварки под флюсом среднее значение соответственно равно 0,6; 0,8 и 0,9.
Ручная дуговая сварка
Ручная дуговая сварка (см. рис. 9.3) относится к технологиям дуговой сварки плавящимся электродом, когда сварка выполняется вручную с использованием стержневого электрода с покрытием. Все операции по зажиганию, поддержанию и перемещению дуги 7 относительно изделия
110

(Vсв), а также подачи электрода 9 с покрытием 10 в зону сварки (Vэл) выполняет сварщик, манипулируя электрододержателем 11.
Зажигание дуги осуществляют следующим образом: после короткого замыкания на заготовку 1 электрод 9 отводят на расстояние 3…6 мм до возникновения устойчивой сварочной дуги 7. Стержень электрода 9 плавится, и расплав-
ленный металл 8 стекает в
Рис. 9.3. Схема ручной дуговой сварки сварочную ванну 2. Покры-
тие электрода 10 также плавится и образует защитную атмосферу 6 вокруг дуги и шлаковую ванну 5 на поверхности металла. По мере движения дуги расплавленный металл затвердевает и формирует сварной шов 3. Жидкий шлак 5 превращается в твердую корку 4, удаляемую после сварки.
При ручной дуговой сварке применение источник питания 12 постоянного тока повышает устойчивость горения дуги, улучшает условия сварки в различных пространственных положениях, обеспечивает сварку электродами с тугоплавкими покрытиями и т. д. Для защиты лица сварщика от разбрызгивания металла, светового, инфракрасного и ультрафиолетового излучения применяется сварочная маска. Ручной дуговой сваркой выполняют сварные швы произвольной формы во всех пространственных положениях. В процессе сварки электроду сообщается поступательное движение в трех направлениях [8]. Все три движения накладываются друг на друга, создавая сложную траекторию перемещения электрода.
Первое движение направлено по оси электрода для поддержания постоянной длины дуги. При длине дуги меньше половины диаметра электрода dэл существенно ухудшается формирование шва и возможно короткое замыкание. При длине дуги более 1,2dэл снижается глубина проплавления, увеличивается разбрызгивание электродного металла и ухудшается
111
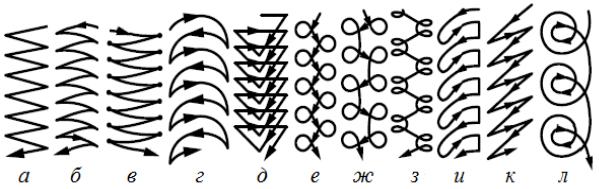
качество шва (по форме и по механическим свойствам), а сварка электродами с покрытием основного вида приводит к порообразованию.
Второе движение – перемещение электрода вдоль оси валика для образования шва. Скорость этого движения зависит от силы тока, скорости плавления электрода, вида шва и других факторов. При сварке тонких листов или при наложении первого (корневого) слоя многослойного шва поперечные движения электрода обычно отсутствуют, и получается узкий шов (ниточный валик) шириной примерно 1,5dэл.
Третье движение – перемещение электрода поперек шва для получения нужной глубины проплавления, ширины и формы шва. Траектории движения конца электрода (см. рис. 9.4) определяются формой разделки, размерами и положением шва, свойствами свариваемого материала и квалификацией сварщика. Для получения валика постоянной ширины амплитуда поперечных колебаний конца электрода не должна превышать значений (2...4)dэ при постоянной скорости его перемещения вдоль шва.
Рис. 9.4. Траектории движения конца электрода:
при слабом (а, б), усиленном (в - з) прогреве свариваемых кромок, усиленном прогреве одной кромки (и, к) и прогреве корня шва (л)
В ряде случаев применяют неплавящиеся электроды: угольные, графитовые и вольфрамовые. Угольные электроды используют обычно для воздушно-дуговой резки металлов, удаления прибылей и дефектов отливок, удаления прихваток, выполнения разделки для сварных швов и других работ. Металлические электроды изготавливают из сварочной проволоки диаметром 1,6; 2; 2,5; 3; 4; 5, 6, 8, 10 и 12 мм и длиной 150…450 мм (ГОСТ
9466-75). Проволока имеет буквенно-цифровое обозначение, включающее диаметр (0,3…12 мм), ее назначение («Св» – сварочная) и химический со-
112