
3 сем / ТКМ. Лаб. практикум_2022 - копия
.pdf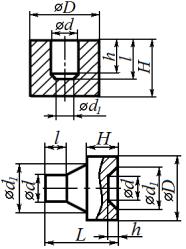
Окончание таблицы 7.4
№ |
Эскиз детали |
|
|
Размеры детали |
|
|
|||
п/п |
|
|
|
|
|
|
|
||
D |
d |
d1 |
L |
l |
H |
h |
|||
|
|||||||||
|
|
|
|
|
|
|
|
|
|
21. |
|
40 |
30 |
20 |
|
80 |
90 |
70 |
|
|
|
|
|
|
|
|
|
|
|
22. |
|
35 |
30 |
25 |
|
70 |
80 |
75 |
|
|
|
|
|
|
|
|
|
|
|
23. |
|
30 |
20 |
10 |
|
60 |
70 |
50 |
|
|
|
|
|
|
|
|
|
|
|
24. |
|
25 |
20 |
15 |
|
50 |
60 |
45 |
|
|
|
|
|
|
|
|
|
|
|
25. |
|
20 |
15 |
10 |
|
45 |
50 |
40 |
|
|
|
|
|
|
|
|
|
|
|
26. |
|
15 |
10 |
5 |
|
35 |
40 |
30 |
|
|
|
|
|
|
|
|
|
|
|
27. |
|
40 |
30 |
35 |
90 |
35 |
50 |
10 |
|
|
|
|
|
|
|
|
|
|
|
28. |
|
35 |
25 |
30 |
80 |
30 |
45 |
9 |
|
|
|
|
|
|
|
|
|
|
|
29. |
|
30 |
20 |
25 |
70 |
25 |
40 |
8 |
|
|
|
|
|
|
|
|
|
|
|
30. |
|
25 |
15 |
20 |
60 |
20 |
35 |
7 |
|
|
|
|
|
|
|
|
|
|
8. ИССЛЕДОВАНИЕ ТЕХНОЛОГИЧЕСКИХ ВОЗМОЖНОСТЕЙ ОПЕРАЦИЙ ЛИСТОВОЙ ШТАМПОВКИ
Цель работы: знания устройства штампов, особенностей технологии и области применения операций листовой штамповки, умения оценивать их возможности и проектировать технологические процессы изготовления деталей из листового проката при небольших отходах металла и отсутствии брака.
Общие сведения
Листовая штамповка [1, 2] является одним из распространенных технологических методов в машиностроении. Она позволяет получать плоские и пространственные детали без последующей механической обработки. В качестве исходной заготовки используют полученные прокаткой лист, полосу или ленту, свёрнутую в рулон.
В разделительных операциях листовой штамповки осуществляют процесс резки – отделение одной части материала от другой по замкнутому или незамкнутому контуру. Основные операции этой группы: резка
93

листового металла ножницами (параллельными, гильотинными, дисковыми и др.) и штампами – вырубка и пробивка.
При вырубке происходит полное отделение металла по замкнутому контуру, при этом отделяемая часть заготовки является изделием. Пробивка – операция, в результате которой в металле создаются сквозные отверстия заданных форм и размеров. Обычно при вырубке часть материала, проталкиваемая пуансоном в матрицу, является заготовкой или деталью, а при пробивке – отходом.
При вырубке характер пластического деформирования, форма среза и качество поверхности зависят от величины зазора между матрицей и пуансоном (рис. 8.1). Штамповка без заусенцев и надрывов металла возможна, когда скалывающие трещины (см. рис. 8.1, а), возникающие у кромок инструмента, имеют встречную направленность. Это происходит при оптимальном зазоре, который обеспечивает и наименьшее сопротивление срезу ср. Величина этого зазора зависит от свойств материала и его толщины h и обычно определяется из соотношения опт = (0,02...0,05)h.
Рис. 8.1. Схема вырубки (а) и формы среза при нормальном (б), уменьшенном (в) и увеличенном (г) зазорах
Гибка характеризуется локальной пластической деформацией. В отличие от упругого изгиба нейтральный слой (рис. 8.2, б) смещается к внутренним слоям, а толщина заготовки h уменьшается на h. Пластическое растяжение наружных волокон не должно превышать относительного уд-
94

линения материала при растяжении 10, что ограничивает минимальный относительный радиус rmin /h, определяемый из следующего условия:
rmin /h 50/(0,8...0,9) 10 − 0,5.
Данное условие справедливо для гибки тонколистового материала при радиусе кривизны более (2...3)h. При гибке с малыми радиусами необходимо учитывать анизотропию механических свойств, при наличии которой пластичность поперек направления прокатки меньше, чем вдоль. Упругие деформации (пружинение) влияют на размеры инструмента. Угол пружинения рассчитывают или выбирают по диаграммам, но его корректировка должна проводиться по результатам натурных испытаний при фиксированных значениях удельного давления.
Рис. 8.2. Схема гибочного штампа (а) и зона изгиба (б):
1 – пуансон; 2 – заготовка; 3 – матрица; 4, 5 – положение действительного и идеального нейтрального слоя
Формовка происходит за счет локального утонения материала и применяется для получения элементов выпукло-вогнутой формы, ребер жесткости и т. п. Степень деформации при формовке в случае одноосного растяжения не должна быть больше относительного равномерного удлинения материала р ≈ (0,8...0,9) 10.
Использование универсальных с эластичными полиуретановыми подушками (рис. 8.3) штампов существенно снижает их стоимость. Деформирование в этом случае осуществляется за счет давления полиуретана на заготовку, которая формуется по матрице – подкладному шаблону.
95
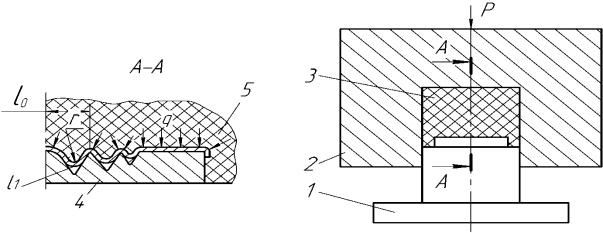
Рис. 8.3. Схема штампа для рельефной формовки полиуретаном: 1 – опорная плита; 2 – контейнер; 3 – полиуретановая подушка; 4 – матрица; 5 – заготовка
Вытяжка – превращение плоской заготовки в полую деталь любой формы или дальнейшее изменение ее размеров. Вытяжкой получают детали различной сложности и формы: цилиндрические, коробчатые, сферические, ступенчатые, несимметричной конфигурации и т. д.
Рассмотрим напряженно-деформированное состояние заготовки при вытяжке с прижимом (рис. 8.4) в цилиндрической системе координат. На первой стадии процесса вытяжки происходит растяжение и утонение кольцевого участка заготовки, находящегося в промежутке между контактными зонами по пуансону и матрице. К концу этой стадии возникает значительное утонение (10...15 %) у части заготовки на переходе от скругленной кромки пуансона к цилиндрической стенке и незначительное утонение (2...5 %) на донной (центральной) части заготовки. После достижения равновесия между усилием Рв и сопротивлением деформированию фланцевой части заготовки начинается вторая стадия процесса вытяжки, заключающаяся в пластической деформации фланца и втягивании его в матрицу.
Пластическая деформация фланцевой части заготовки сопровождается перемещением всех материальных точек к центру под действием растягивающего радиального напряжения ρ и некоторым утолщением заготовки под действием сжимающего тангенциального напряжения θ. Напряжение θ возникает вследствие воздействия клиновых участков заготовки друг на друга. Для осуществления пластической деформации должно выполняться условие пластичности: | ρ| = 1,15 s – | θ|.
96

Рис. 7.4. Схема вытяжки: а – вытяжка из плоской заготовки; б – последующая вытяжка; в – форма изделий по переходам вытяжки;
1 – матрица; 2 – прижим; 3 – пуансон
Сжимающие тангенциальные напряжения θ на фланце вызывают образование радиальных складок, для предотвращения которых служит прижим. При большой разнице диаметров D0 и d1 или при величине усилия прижима Рпр больше необходимого возрастают силы трения, действующие на фланцевую часть заготовки со стороны матрицы и прижима. Это приводит к пластической деформации на цилиндрическом участке и может привести к разрушению заготовки в опасном сечении – зоне перехода от дна к стенке из-за возникшего здесь в начальной стадии вытяжки значительного утонения материала. Для снижения растягивающего напряжения в опасном сечении усилие прижима должно быть минимально необходимым для предотвращения складкообразования.
Получение детали без разрушения возможно при степени вытяжки kв1 = D0 /d1 ≤ 1,7...2,2. Большие значения соответствуют высокопластичным и сильно упрочняющимся металлам (латунь, сталь коррозионно-стойкая и др.). Кроме утонения заготовки у перехода дна к стенке при вытяжке может происходить утолщение верхней части цилиндрической стенки детали на 15...25 % по сравнению с исходной толщиной заготовки.
97

Раздача и обжим (рис. 8.5) приводят к изменению диаметра полой заготовки. Основное деформирующее усилие при обжиме является сжимающим, что может привести к потере устойчивости заготовки в виде кольцевых складок. В этих операциях угол конической части инструмента не превышает 10...20о. Большие углы требуют больших деформирующих усилий, а меньшие – увеличивают размеры очага пластической деформации, и вероятность образования складок возрастает.
Рис. 8.5. Схема раздачи (а) и обжима (б) трубчатых заготовок: 1 – пуансон; 2 – матрица; 3 – заготовка
При раздаче заготовок происходит разрыв заготовки, если степень деформации соизмерима с относительным удлинением. Раздача и обжим средних частей заготовки усложняют процесс и конструкцию жестких штампов, так как необходимы уже разъемные матрицы и сложные разжимные пуансоны. Здесь успешно могут быть использованы специальные виды штамповки: электрогидроимпульсная, электромагнитная, штамповка эластичной средой (резиной или полиуретаном) и другие.
Содержание работы
Работа включает изучение особенностей и предельных возможностей операций листовой штамповки, разработку технологических процессов изготовления деталей, подготовку отчёта.
98

Последовательность выполнения работы
До начала занятий необходимо изучить сущность операций листовой штамповки и их назначение, принципиальные схемы процессов и штампов (см. рис. 8.1÷8.5), выполнить необходимые эскизы и подготовить исходные данные для оформления отчёта (см. последовательность выполнения работы и содержания отчётов в опытах 1÷5).
Опыт 1. Вырубка деталей из листового материала
1.Изучите устройство и выполните эскиз вырубного штампа.
2.Произведите под руководством учебного мастера вырубку деталей из двух-трех заготовок различной толщины при смене пуансонов, т. е. при различных зазорах между матрицей и пуансоном. Для каждой вырубки зафиксировать наибольшее усилие пресса P и записать его в табл. 8.1.
|
|
|
|
|
|
|
|
Таблица 8.1 |
|
|
|
|
Параметры процесса вырубки |
|
|
|
|||
|
|
|
|
|
|
|
|
|
|
|
Материал |
Зазор в штампе |
Усилие |
|
Сопро- |
|
Высота |
||
№ |
|
|
|
|
вырубки |
|
тивление |
|
заусенца |
|
Толщи- |
Радиаль- |
Относи- |
|
|
||||
п/п |
Марка |
на h, |
ный , |
тельный |
P, |
|
срезу ср, |
|
hз, |
|
|
мм |
мм |
/h |
кН |
|
МПа |
|
мм |
|
|
|
|
|
|
|
|
|
|
|
|
|
|
|
|
|
|
|
|
3. Найдите сопротивление срезу ср и сравните его с расчётным ср.р:
τ |
ср |
P |
k L h ; |
τ |
ср.р |
0,7 0,8 σ |
в , |
|
|
|
|
где P – усилие вырубки; k = 1,2 – коэффициент, учитывающий затупление режущей кромки инструмента, неравномерность зазора по периметру штампа; L – периметр вырубаемой детали; h – толщина заготовки; в – временное сопротивление разрыву (предел прочности).
4.Зафиксируйте форму среза. Измерьте микрометром в четырех диаметрально противоположных точках высоту заусенцев. Среднее значение высоты заусенца hз укажите на эскизах деталей и в табл. 8.1.
5.Постройте графики зависимости высоты заусенца hз и сопротивления
срезу ср от относительного зазора в штампе /h.
99
6. Оформите отчёт по опыту.
Содержание отчёта
1.Назначение и сущность вырубки, эскиз штампа.
2.Эскизы вырубленных деталей и форма их среза.
3.Опытные параметры процесса вырубки (см. табл. 8.1).
4.Расчет сопротивления срезу ср.
5.График зависимости ср и высоты заусенца hз от относительного зазора между матрицей и пуансоном /h.
6.Анализ качества вырубленных деталей.
7.Выводы о влиянии величины относительного зазора /h на качество вырубки и соответствии опытного и расчетного сопротивления срезу.
Опыт 2. Определение наименьшего радиуса изгиба и угла пружинения
1.Изучите устройство лабораторного штампа (см. рис. 8.2), поместите его эскиз в отчет.
2.Для заданного материала рассчитайте минимально допустимый ра-
диус изгиба rmin = h [50 /(0,8...0,9) 10 − 0,5].
3.Произведите гибку трех-четырех заготовок при различных радиусах пуансона поперек и вдоль направления прокатки.
4.Измерьте наименьшие радиусы изгиба на заготовках без трещин и сравните с расчетными значениями.
5.Измерьте угломером угол на полученных деталях и определите угол пружинения.
6.Оформите отчёт по данному опыту.
Содержание отчёта
1.Эскиз и описание гибочного штампа.
2.Расчет минимально допустимого радиуса изгиба.
3.Эскизы заготовки и полученных деталей с указанием дефектов и действительных размеров (радиус, угол).
4.Выводы о влиянии свойств материала на минимально допустимый радиус гибки, о причинах разрушения заготовки, изменении толщины материала после гибки, способах учета угла пружинения.
100
Опыт 3. Определение предельно допустимой деформации и необходимого давления при формовке полиуретаном
1.Выполните эскиз лабораторного штампа (см. рис. 8.3).
2.Произведите формовку детали из листовой заготовки. Зафиксируйте наибольшее усилие Pmax пресса в процессе штамповки.
3.Определите наибольшую деформацию при формовке по результатам изменения исходной длины l0 или толщины h0 заготовки на участке локальной деформации:
max = (l1 − l0) /l0 = (h0 − h1) /h0,
где l1, h1 – длина и толщина заготовки после формовки (см. рис. 8.3). Сравните значение max с относительным удлинением материала. Объ-
ясните причину разрушения.
4.Измерьте радиусомером наименьший радиус на отформованной де-
тали.
5.Рассчитайте давление pрас, необходимое для формовки, и его опытное значение pоп по формулам:
pрас |
2σs h0 |
; |
pоп |
Pmax |
, |
|
r |
F |
|||||
|
|
|
|
где s – напряжение текучести материала при исследуемой степени деформации (задается преподавателем); r – радиус кривизны; Pmax – наибольшее усилие пресса при формовке; F – площадь контейнера в плане.
6.Сделайте выводы о предельно допустимой деформации металла заготовки, соответствии расчетного и опытного давления при формовке.
7.Оформите отчёт.
Содержание отчёта
1.Схема формовки, сущность, назначение и область ее применения.
2.Эскизы заготовки и изделия с размерами.
3.Расчёт деформации max и давления полиуретана.
4.Выводы по работе.
Опыт 4. Определение предельной деформации при раздаче и обжиме
1. Выполните эскиз штампов и заготовки (см. рис. 8.5).
101
2.Произведите деформирование заготовки на прессе до появления дефектов: разрыв заготовки, образование складок.
3.Выполните эскизы полученного изделия с указанием размеров и вида дефектов. Объясните причины изменения исходных размеров.
4.Определите предельный коэффициент раздачи kр = D/d и степень де-
формации εmax = 100(D – d)/d (0,7...0,8) 10, сравнив ее с относительным удлинением материала 10.
5.Определите предельно допустимый коэффициент обжима kоб = d /D, объясните причины его ограничения.
6.Оформите отчёт.
Содержание отчёта
1.Схемы раздачи и обжима, описание напряженно-деформированного состояния.
2.Эскизы заготовки и полученных изделий.
3.Расчет коэффициентов раздачи и обжима.
4.Выводы о пределах допускаемого формоизменения при раздаче и обжиме.
Опыт 5. Определение предельной степени вытяжки и изучение характера деформации
1.Изобразите схему вытяжки. Укажите напряженно-деформированное состояние материала на различных участках заготовки в процессе деформирования. Измерьте диаметры сменных матриц и пуансонов.
2.Измерьте и занесите в табл. 8.2 толщину h0 и диаметр заготовки D0.
3.Рассчитайте степень вытяжки для каждого опыта ki = Di-1/di, где Di-1 – диаметр исходной заготовки или диаметр изделия, полученного предыдущей вытяжкой; di – диаметр вытягиваемого изделия; i – номер вытяжной операции.
4.Рассчитайте необходимое для вытяжки усилие пресса
Pmax πdi h0 σв ,
где h0 – исходная толщина заготовки, в – предел прочности материала.
102