
Технология машиностроения Гричачина
.pdf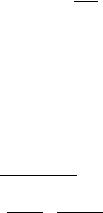
где: Сv и m, х, у - коэффициент и показатели степени при соответствующих параметрах резания, зависящие от вида обработки, материала режущей части резка и характеристики подачи; T -— период стойкости инструмента, мин; t — глубина резания, мм; s — подача, мм/об, К, — поправочный коэффициент, являющийся произведением коэффициентов Кмv, Кпv, Киv, учитывающих качество обрабатываемого материала, состояние поверхности заготовки и качество материала инструмента соответственно.
Период стойкости инструмента принимаем 55 минут, коэффициент Сv =332 и показателей степеней m= 0,2, х=0,1, у=0,4 определим по [табл. 39, стр. 283, 8]. Данные значения были получены Согласно значениям подачи и глубины резания для резца с пластиной Т15К6.
Значения коэффициентов Кмv рассчитать по формуле (8.2.2):
Кмv= К ( |
750 |
) , |
(8.2.2) |
|
|||
г |
|
|
|
|
в |
|
где: Кг — коэффициент, характеризующий группу стали по обрабатываемости и —
показатель степени, зависящий от группы стали, в — предел прочности обрабатываемой стали.
Предел прочности стали 40 в = 570 МПа, показатель степени = 0,9 Кг = 1 [табл. 2, стр.
283, 8], так как материал режущего инструмента — твёрдый сплав.
Тогда Кмv= 1(750570)0,9=1.27
Кпv = 0.8, так как стальная отливка c коркой [табл. 5, 8].
Киv= 1.15, так как при обработке конструкционной стали используется пластинки Т15К6 [табл. 6, стр. 283, 8].
= 1.27 ∙ 0.8 ∙ 1.15 = 1.17
Значение скорости:
332
v=500.220.12.40.4 1.17 = 116 м/мин
n1=1000∙ = 1000∙116 = 369 об/мин∙ ∙100
Режимы резания для остальных технологических переходов указаны в таблице 8.2.1.
Таблица 8.2.1 – Режимы резания
Операция |
Поверхности |
Глубина |
Подача |
Скорость |
Частота |
|
|
резания t, |
S, |
резания |
вращения |
|
|
мм |
мм/об |
v, м/мин |
шпинделя, |
|
|
|
|
|
об/мин |
|
|
|
|
|
|
015 — Фрезерная с ЧПУ |
1 |
2 |
0,24 |
116 |
369 |
|
|
|
мм/зуб |
|
|
|
|
|
|
|
|
|
3 |
1 |
0,1 |
125 |
1900 |
|
|
|
|
|
|
025 — Шлифовальная |
1 |
0.01 |
0,4 |
26 |
2000 |
|
|
|
|
|
|
030 — Фрезерная с ЧПУ |
2 |
2 |
0,24 |
880 |
2700 |
|
|
|
|
|
|
|
4,5 |
70 |
0,24 |
880 |
2700 |
|
|
|
|
|
|
|
6,7,8,9,10 |
2 |
0,16 |
195 |
2500 |
|
|
|
|
|
|
|
11,12,13 |
4 |
0,49 |
294 |
4500 |
|
|
|
|
|
|
|
14,15 |
45 |
0,27 |
177 |
6200 |
|
|
|
|
|
|
|
16, 17, 18, 19 |
20 |
0,27 |
177 |
6200 |
|
|
|
|
|
|
|
16, 17, 18, 19 |
17 |
1,25 |
41,4 |
1600 |
|
|
|
|
|
|
|
20 |
13 |
0,2 |
25 |
795 |
|
|
|
|
|
|
|
20 |
13 |
0,1 |
15 |
477 |
|
|
|
|
|
|
|
20 |
13 |
0,1 |
190 |
954 |
|
|
|
|
|
|
|
21 |
6 |
0,15 |
33 |
1000 |
|
|
|
|
|
|

|
22, 23 |
8 |
0,27 |
177 |
6200 |
|
|
|
|
|
|
|
22,23 |
8 |
0.8 |
41,4 |
1600 |
|
|
|
|
|
|
|
24, 25 |
8 |
0,2 |
25 |
795 |
|
|
|
|
|
|
|
24, 25 |
8 |
0,1 |
15 |
477 |
|
|
|
|
|
|
|
24, 25 |
8 |
0,1 |
190 |
954 |
|
|
|
|
|
|
|
26 |
8 |
0,24 |
880 |
2700 |
|
|
|
|
|
|
|
27 |
6 |
0,2 |
25 |
795 |
|
|
|
|
|
|
|
27 |
6 |
0,1 |
15 |
477 |
|
|
|
|
|
|
|
27 |
6 |
0,1 |
190 |
954 |
|
|
|
|
|
|
8.3. Расчёт норм времени на операции
Технические нормы времени в условиях серийного производства устанавливают расчётноаналитическим методом. Штучно-калькуляционное время рассчитывается по формуле (7):
Тпз
Тшк= То+ Тв + Торг.обсл + Ттехн.обсл + Тотд + n , (7)
То - основное технологическое время; Тв — вспомогательное время; Торг.обсл. — время организационного обслуживания; Ттехн.обсл — Время технического обслуживания; Тотд — время на отдых и личные нужды рабочего; Тпз — подготовительно-заключительное время, затрачиваемое на подготовку выпуска партии изделий; n — количество изделий в партии.
Для расчёта основного времени используется формула (8):
То = |
+ 1+ 2 |
∙ , |
(8) |
|
∙ |
||||
|
|
|
где: l— длина обрабатываемой поверхности; l1 — расстояние врезания и пробега инструмента; l2
— дополнительная длина на взятие пробной стружки, учитываемая при точении резцами, кроме фасонных и отрезных; n — скорость вращения заготовки или инструмента: S — подача; i — число рабочих ходов.
Рассчитаем норму времени для операции 015 торцевого фрезерования 1) Основное технологическое время:
То = 369∙2,4180 ∙ 2 =0.407
2) Вспомогательное время:

Тв = tуст+ tупр + tиз
tуст = 0,35 мин - время на установку, закрепление и снятие детали; tупр = 0,45 мин - время на управления станком, связанное с технологическими переходами; : tиз = 0,20 мин - время на контрольные измерения Таким образом: Тв = 0.35 + 0.45 + 0.20 = 1 мин;
3)Т орг.обсл. = 0,08∙ (То + Тв) = 0,113 мин;
4)Т техн.обсл = 0,06∙(То + Тв) = 0,084 мин;
5)Т отд = 0,04∙(То + Тв) =0,056 мин; 6) Тпз= 10
Штучно-калькуляционное время:
Тшк= 0.407 + 1 + 0.113 + 0.084 + 0.056 + 300010 = 1.163
Нормы времени для операций показаны в таблице 6.
|
Таблица 6 — Нормы времени для операций |
|
|
|
|
Операция |
Тшк |
|
015 |
2.243 |
|
025 |
1.641 |
|
030 |
15.119 |
|
9. Оформление технологической документации
Заключительная часть работы — составление и оформление комплекта необходимой технологической документации. Состав и вид карт, входящих в комплект технологических документов на изделие, зависит от технологического процесса, типа производства, степени цифровизации процесса разработки. В данном случае комплект технологических документов включает в себя: маршрутную карту, операционные карты, карты эскизов,
контрольную карту. Все документы объединены в технологический процесс и приведены в приложении.
Заключение
В данной работе разработан технологический процесс изготовления детали
«Корпус». Деталь проанализирована и рассчитана на технологичность изготовления. По полученным данным разработан комплект технологической документации.
Список литературы
1. Технология машиностроения. Часть I: Учеб. Пособие / Э.Л. Жуков, Козарь, Б.Я.
Розовский, В.В. Дягтярев, А.М. Соловейчик: Под ред. С.Л. Муракшина. СПб.: Изд-во Политехн. ун-та, 2005, 190 с.
2. Технология машиностроения. Часть П: Проектирование технологических процессов: Учеб. Пособие / Э.Л. Жуков, И.И. Козарь, Б.Я. Розовский, В.В. Дягтярев, А.М.
Соловейчик; Под ред. С.Л. Муракшина. СПб.: Изд-во Политехн. ун-та, 2008, 498 с.; 3. Технология машиностроения. Часть Ш: Правила оформления технологической
документации: Учеб. Пособие / Э.Л. Жуков, И.И. Козарь, Б.Я. Розовский, В.В. Дягтярев,
А.М. Соловейчик; Под ред. СЛ. Муракшина. СПб.: Изд-во Политехн. ун-та, 2008, 59 с.;\ 4. Малькевич А.В., Серяков Е.И., Радкевич М. М. Технологические основы
проектирования штампованных и кованых изделий: Учебное пособие. — СПб.: СПОГТУ
1993. - 96 с.
5. Справочник конструктора-машиностроителя: в 3-х т. / Анурьев В.И. — 9-е изд.,
перераб. и доп./ под ред. И.Н. Жестковой. - М.: Машиностроение, 2006; 6. Справочник фрезеровщика / Косовский В.Л. - 4-е изд., стер. — М.: Высшая школа;
Издательский центр «Академия», 2001 — 400 с.: ил.;
7.Справочник технолога-машиностроителя. В 2-х т. Т. 1/ Под ред. А.Г. Косиловой и Р.К. Мещерякова. - 4-е изд., перераб. и доп. — М.: Машиностроение, 1986. 656 с., ил.:
8.Справочник технолога-маптиностроителя. В 2-х т. Т. 2/ Под ред. А.Г. Косиловой и Р.К. Мещерякова. - 4-е изд., перераб. и доп. — М.: Машиностроение, 1985. 496 с., ил.: