
ФЕДЕРАЛЬНОЕ ГОСУДАРСТВЕННОЕ АВТОНОМНОЕ ОБРАЗОВАТЕЛЬНОЕ УЧРЕЖДЕНИЕ ВЫСШЕГО ОБРАЗОВАНИЯ
«САНКТ-ПЕТЕРБУРГСКИЙ ПОЛИТЕХНИЧЕСКИЙ УНИВЕРСИТЕТ ПЕТРА ВЕЛИКОГО»
Институт машиностроения, материалов и транспорта Высшая школа машиностроения
Задание №1
по дисциплине «Режущие инструменты»
Фасонный резец
Выполнил студент |
Гричачина А. А . |
гр. 3331505/10101 |
|
Работу принял |
Слатин В. И. |
Санкт-Петербург
2024
«САНКТ-ПЕТЕРБУРГСКИЙ ПОЛИТЕХНИЧЕСКИЙ УНИВЕРСИТЕТ ПЕТРА ВЕЛИКОГО»
Институт машиностроения, материалов и транспорта ЗАДАНИЕ
по выполнению курсового проекта Студенту Гричачиной Алине Антоновне
1.Тема работы: Проектирование фасонного резца
2.Срок сдачи: 13.12.2024 г.
3.Исходные данные по работе:
•Вариант задания №2
•Эскиз детали
•Материал детали: Чугун
4.Содержание пояснительной записки: выбор величины заднего, переднего угла; проверка на минимально допускаемое значение на конических участках; вычисление глубины профиля детали; определение узловых точек профиля детали; подбор габаритных и присоединительных размеров резца; расчет установочных и эксплуатационных параметров; расчет глубины профиля резца от базовой линии для всех узловых точек; расчет отклонения фактической формы конических участков детали от теоретической в средней точки этих участков; расчет корригированного радиуса в профильной плоскости резца; спроектировать участок под отрезной резец; эскиз взаимного расположения резца и детали в двух проекциях; выбор материала для изготовления резца.
5.Перечень графического материала: чертеж фасонного резца (А3).
6.Дата получения задания: 06.09.2024 г.
Преподаватель |
Слатин В. И. |
Задание принял к исполнению. |
Гричачина А. А. |
|
Оглавление |
|
Техническое задание ............................................................................................... |
4 |
|
1. |
Выбор величины заднего угла α...................................................................... |
5 |
2. |
Выполнение проверки заднего угла α на минимально допускаемое |
|
значение на конических участках .......................................................................... |
5 |
|
3. |
Выбор переднего угла ɣ ................................................................................... |
5 |
4. |
Вычисление глубины профиля........................................................................ |
5 |
5. |
Определение узловой точки профиля детали................................................ |
6 |
6. |
Выбор габаритных и присоединительных размеров дискового резца........ |
7 |
7. |
Расчет установочных и эксплуатационных параметров............................... |
7 |
8. |
Расчет глубины профиля для каждой узловой точки.................................... |
8 |
9. |
Отклонения формы конических участков .................................................. |
9 |
10. Расчет корригированного радиуса в профильной плоскости резца....... |
10 |
|
11. Проектирование участка под отрезной резец .......................................... |
10 |
|
12. Эскизы относительного положения детали и резца ................................ |
11 |
|
13. Выбор материала для изготовления резцов.............................................. |
12 |
|
Литература ............................................................................................................. |
12 |
3
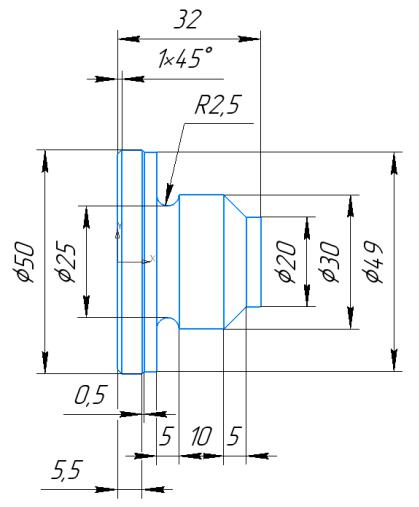
Техническое задание
Исходные данные представлены в таблице 1, эскиз детали на рисунке 1.
Таблица 1
№ |
l1 |
|
l2 |
l3 |
|
l4 |
l5 |
l6 |
|
l7 |
l8 |
|
d1 |
d2 |
d3 |
d4 |
d5 |
d6 |
d7 |
r |
L |
Вари- |
|
|
|
|
|
|
|
|
|
|
|
|
|
|
|
|
|
|
|
|
|
анта |
|
|
|
|
|
|
|
|
|
|
|
|
|
|
|
|
|
|
|
|
|
|
|
|
|
|
|
|
|
|
|
|
|
|
|
|
|
|
|
|
|
|
|
|
|
|
|
|
|
|
|
|
|
|
|
|
мм |
|
|
|
|
||||
|
|
|
|
|
|
|
|
|
|
|
|
|
|||||||||
|
5 |
|
10 |
- |
|
- |
5 |
- |
|
0,5 |
5,5 |
|
20 |
20 |
30 |
30 |
25 |
49 |
50 |
2,5 |
32 |
2 |
|
|
|
|
|
|
|
|
|
|
|
|
|
|
|
|
|
|
|
|
|
|
Материал |
|
|
Направление |
|
Суппорт |
Тип резца |
||||||||||||||
|
|
|
детали |
|
|
вращения |
|
|
|
|
|
|
|
|
|
||||||
|
|
|
|
|
|
|
|
|
|
|
|||||||||||
|
|
|
Чугун |
|
|
|
Правое |
|
Передний |
Дисковый |
|||||||||||
|
|
|
|
|
|
|
|
|
|
|
|
|
|
|
|
|
|
|
|
|
|
Рисунок 1 - Эскиз детали
4

1. Выбор величины заднего угла α
Для дисковых фрез рекомендуется брать задний угол α в диапазоне
10…12°. Выбираем величину заднего угла α=10°.
2. Выполнение проверки заднего угла α на минимально допускаемое значение на конических участках
Профильный угол φ вычисляется по формуле 3.1.
= |
|
|
|
|
, |
(2.1) |
|
|
|
|
|||
|
|
− |
|
|||
|
|
|
|
|
|
|
l – длина конического участка; |
rmax, |
rmin |
|
– больший и меньший радиусы |
конического участка соответственно. На детали присутствует два конических участка с одинаковым углом, поэтому расчет будет происходить по одному из них:
= 5 мм, = 15 мм, = 10 мм.
5= 15 − 10 = 1
Нормальный задний угол αn |
вычисляется по формуле 3.2. |
|
||
|
|
≈ |
∙ |
(2.2) |
|
|
|
|
|
|
|
≈ |
10° 45° = 0,125 |
|
|
|
|
|
|
= 0,125 = 7,107° ≈ 7° |
|
|||
|
|
|
|
|
= 7° > 2°, значит |
задний угол α проходит на |
минимально |
||
|
|
|
|
|
допускаемое значение на конических участках.
3. Выбор переднего угла ɣ
Передний угол ɣ = 7°, что соответствует чугуну (см. таблицу 3.1).
Таблица 3.1
Обрабаты- |
|
Сталь σв, МПа |
|
Бронза, |
Алюминий, |
||
|
|
|
|
|
|
|
|
ваемый |
|
|
|
|
Чугун |
латунь |
медь |
500 |
|
500-800 |
800-1200 |
||||
материал |
|
|
красная |
||||
|
|
|
|
|
|
||
|
|
|
|
|
|
|
|
γ |
20 |
|
15−10 |
10−5 |
5−10 |
0−5 |
25−30 |
|
|
|
|
|
|
|
|
4. Вычисление глубины профиля
Наибольшая глубина профиля детали вычисляется по формуле 4.1.
5
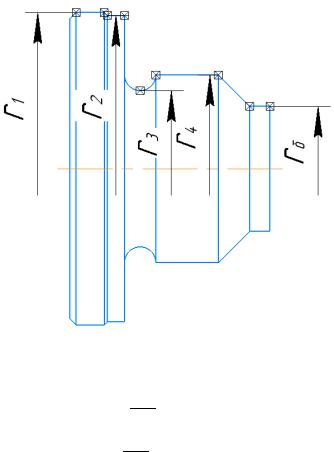
|
|
|
= |
− |
(4.1) |
||
|
|
|
|
|
|||
|
|
|
|
2 |
|
|
|
|
|
|
|
|
|
||
, |
|
− наибольший и |
наименьший диаметры детали |
||||
|
|
|
|
|
|
|
|
соответственно |
|
|
|
|
|
|
|
|
|
|
= |
50 − 20 |
|
= 15 (мм). |
|
|
|
|
|
||||
|
|
|
|
2 |
|
|
|
|
|
|
|
|
|
5. Определение узловой точки профиля детали
Под узловой точкой понимают все точки профиля одного радиуса
(диаметра), в которых пересекаются линии разного типа (прямые и дуги окружности) или одного типа, но с разными параметрами (для прямых – с
разными профильными углами, для дуг – с разными центрами окружностей).
Узловая точка с наименьшим радиусом – базовая (формулы 5.1 и 5.2).
|
= |
|
|
(5.1) |
|
|
|
||||
б |
2 |
|
|||
|
|
||||
r |
= |
di |
|
(5.2) |
|
|
|||||
i |
2 |
|
|
||
|
|
|
Радиусы узловых точек 1 и 2 равны 18 мм и 10 мм соответственно. Выбор узловых точек показан на рисунке 5.1.
Рисунок 5.1- Выбор узловых точек профиля детали
50
r1 = 2 = 25 (мм)
49
r2 = 2 = 24,5 (мм)
6
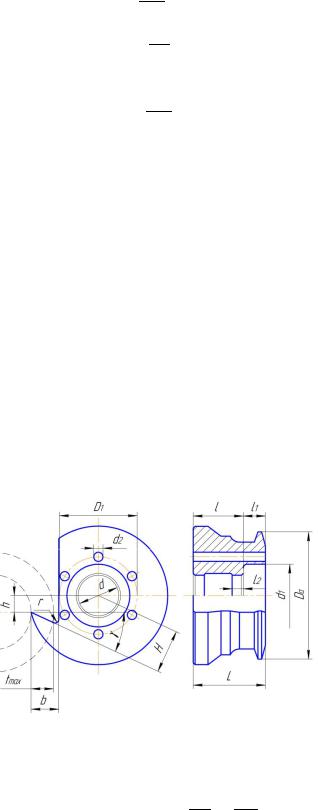
25
r3 = 2 = 12,5 (мм)
30
r4 = 2 = 15 (мм)
20
rб = 2 = 10 (мм)
6. Выбор габаритных и присоединительных размеров дискового резца
Габаритный размеры резца выбраны согласно глубине профиля = = 15 мм (см. таблицу 6.1 и рисунок 6.1). Размер L зависит от длины изготавливаемой детали. Размеры l1 = (0,25 … 0,5 ) L; l2 = 0,25l.
Таблица 6.1
tmax |
Da |
b |
d |
d1 |
d2 |
D1 |
r |
до |
|
|
(H8) |
|
|
|
|
|
|
|
|
|
|
|
|
18 |
100 |
23 |
27 |
40 |
8 |
52 |
2 |
|
|
|
|
|
|
|
|
Рисунок 6.1- Выбор габаритных и присоединительных размеров дискового резца
Наружный радиус резца равен = 2 = 1002 = 50 (мм)
7. Расчет установочных и эксплуатационных параметров
Смещение оси резца относительно линии центров станка
рассчитывается по формуле 7.1.
7
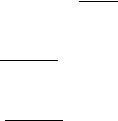
= |
∙ |
(7.1) |
|
|
|
= 50 ∙ sin 10 ° = 8.682 мм
Смещение передней грани (или плоскости заточки) от оси резца
рассчитывается по формуле 8.2. |
|
|
|
|
= |
∙ ( + ) |
(7.2) |
|
|
|
|
= 50 ∙ (10° + 7 °) = 14.619 (мм)
8.Расчет глубины профиля для каждой узловой точки
Глубина профиля узловой точки от базовой линии рассчитывается по
формулам 9.1 в плоскости передней грани и в профильной плоскости
(нормальной к задней поверхности) 9.3.
|
= |
∙cos( − )−б |
|
cos |
|||
|
|
где sinδi = rб∙sinγ ri
sin 1 = 10∙sin7°=0,049; 1 = 2°48′
25
sin 2 = 10∙24.5sin7°=0,05; 2 = 2°51′
|
sin 3 = |
10∙sin7° |
=0,097; 3 = 5°35′ |
||||||||||
|
12.5 |
||||||||||||
|
|
|
|
|
|
|
|
|
|
|
|
|
|
|
sin 4 = |
10∙sin7° |
=0,081; 4 = 4°40′ |
||||||||||
|
15 |
||||||||||||
|
|
|
|
|
|
|
|
|
|
|
|
|
|
|
|
|
= |
|
25∙cos(7°−2°48′)−10 |
|
= 15,045 (мм) |
||||||
|
|
|
|
||||||||||
1 |
|
|
|
|
|
|
cos7° |
||||||
|
|
|
|
|
|
|
|
||||||
|
|
= |
24.5∙cos(7°−2°51′)−10 |
|
= 14,544 (мм) |
||||||||
|
|
|
|
|
|||||||||
2 |
|
|
|
|
|
|
|
cos7° |
|||||
|
|
|
|
|
|
|
|
||||||
|
|
|
= |
12.5∙cos(7°−5°35′)−10 |
= 2,515 (мм) |
||||||||
|
|
|
|
|
|||||||||
3 |
|
|
|
|
|
|
|
cos7° |
|||||
|
|
|
|
|
|
|
|
||||||
|
|
|
= |
15∙cos(7°−4°40′)−10 |
= 5,025 (мм) |
||||||||
|
|
|
|||||||||||
4 |
|
|
|
|
|
cos7° |
|||||||
|
|
|
|
|
|
|
|
(8.1)
(8.2)
8
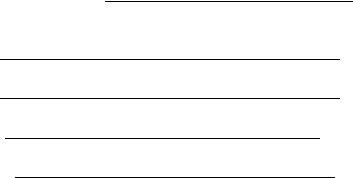
|
|
= |
− √ |
2 + |
|
2 − 2 |
|
cos( + ) |
(8.3) |
|
|
|
|
|
|
|
1 = 50 − √502 + 15,0452 − 2 ∙ 50 ∙ 15,045 ∙ cos(17°)= 14,117 (мм)
2 = 50 − √502 + 14,5442 − 2 ∙ 50 ∙ 14,544 ∙ cos(17°)= 13,659 (мм)
350 − √502 + 2,5152 − 2 ∙ 50 ∙ 2,515 ∙ cos(17°)= 2,399 (мм)
4 = 50 − √502 + 5,0252 − 2 ∙ 50 ∙ 5,025 ∙ cos(17°)= 4,782 (мм)
Полученные данные представлены в таблице 8.1.
|
|
|
|
Таблица 8.1 |
|
|
|
|
|
|
|
Номер узловой |
ri |
hi = ri - rσ |
hpi |
hxi |
|
точки i |
|
|
|
|
|
|
|
|
|
|
|
1 |
25 |
15 |
15,045 |
14,117 |
|
|
|
|
|
|
|
2 |
24,5 |
14,5 |
14,544 |
13,659 |
|
|
|
|
|
|
|
3 |
12,5 |
2,5 |
2,515 |
2,399 |
|
|
|
|
|
|
|
4 |
15 |
5 |
5,025 |
4,782 |
|
|
|
|
|
|
|
9. Отклонения формы конических участков
Радиус средней точки С высчитывается по формуле 9.1:
|
|
|
|
|
|
|
|
( |
+ |
|
) |
|
|
||||||
|
|
|
|
с = |
|
|
|
|
|
|
|
(9.1) |
|||||||
|
|
|
|
|
|
2 |
|
|
|
|
|
|
|
|
|||||
|
|
|
|
|
|
|
|
|
|
|
|
|
|
|
|
|
|
|
|
с1 |
= |
|
(15 + 10) |
|
= 12.5 мм |
||||||||||||||
|
|
||||||||||||||||||
|
|
|
|
|
|
|
|
2 |
|
|
|
|
|
|
|
|
|
|
|
с2 |
= |
(25 + 24.5) |
= 24.75 мм |
||||||||||||||||
|
|
|
|||||||||||||||||
|
|
|
|
|
|
|
|
2 |
|
|
|
|
|
|
|
|
|
|
|
Теоретическая глубина профиля соответствующей ей точки Ст |
|||||||||||||||||||
высчитывается по формулам 9.1, 9.3. |
|
|
|
|
|
|
|
|
|
|
|||||||||
sin |
|
|
= |
10∙sin7° |
= 0,097; |
= 5°35′ |
|||||||||||||
|
|
|
|||||||||||||||||
с1 |
12,5 |
|
|
|
|
|
|
|
|
|
1 |
|
|||||||
|
|
|
|
|
|
|
|
|
|
|
|
|
|
|
|
||||
sin |
|
|
= |
10∙sin7° |
= 0,049; |
= 2°49′ |
|||||||||||||
|
|
|
|||||||||||||||||
с2 |
12,5 |
|
|
|
|
|
|
|
|
|
2 |
|
|||||||
|
|
|
|
|
|
|
|
|
|
|
|
|
|
|
|
||||
с1 = |
|
12,5∙cos(7°−5°35′)−10 |
= 2,515 (мм) |
||||||||||||||||
|
|
|
|
|
cos7° |
|
|
|
|
|
|
||||||||
|
|
|
|
|
|
|
|
|
|
|
|
|
|
|
|
|
|||
с2 = |
24.75∙cos(7°−2°49′)−10 |
|
= 14,795 (мм) |
||||||||||||||||
|
|||||||||||||||||||
|
|
|
|
|
|
|
cos7° |
|
|
|
|
|
|
|
|
|
|
9

ст1 = 50 − √502 + 2,5152 − 2 ∙ 50 ∙ 2,515 ∙ cos(17°)= 2,399 (мм)
ст2 = 50 − √502 + 14,7952 − 2 ∙ 50 ∙ 14,795 ∙ cos(17°)= 13,888 (мм)
Фактическая глубина профиля соответствующей ей точки Сф рассчитывается по формуле 9.2:
|
|
хсф = |
+ |
(9.2) |
||||
|
|
2 |
|
|||||
|
|
|
|
|
|
|||
|
хсф1 = |
4,782 |
= 2,391 (мм), |
|
||||
|
|
|
||||||
|
|
2 |
|
|
|
|
|
|
хсф2 |
= |
14,117 + 13,659 |
= 13,888 (мм), |
|
||||
|
|
|||||||
|
|
2 |
|
|
|
|
|
|
где hxmax и hxmin - глубины профиля крайних узловых точек конического |
||||||||
участка. |
|
|
|
|
|
|
|
|
Отклонение профиля на коническом участке считается по формуле 9.3: |
||||||||
|
|
∆ = хст− хсф |
(9.3) |
∆ 1 = 2,399 − 2,391 = 0,08 (мм) ∆ 2 = 13,888 − 13,888 = 0
10. Расчет корригированного радиуса в профильной плоскости резца
Глубина дугового участка в профильной плоскости резца рассчитана по
формуле 10.1:
= |
х4 |
− |
х3 |
(10.1) |
|
|
|
= 4,782 − 2,399 = 2,382 (мм)
Корригированный радиус rx в профильной плоскости резца для дугового участка детали с радиусом r рассчитан по формуле 10.2
|
|
|
( 2+ 2) |
|
||
|
= |
|
|
(10.2) |
||
|
2∙ |
|||||
|
|
|
|
|||
|
|
|
|
|
||
= |
(2,52 |
+ 2,3822) |
= 2,503 мм |
|||
|
|
|
|
|
||
|
2 ∙ 2,382 |
|
||||
|
|
11. Проектирование участка под отрезной резец
Согласно эскизу, общая ширина резца составляет L= 32+2+1+1+2+2 =
40мм (рис. 11.1).
10