
Автоматизация Бобриков Гричачина не готов
.pdf1
АВТОМАТИЗАЦИЯ ТЕХНОЛОГИЧЕСКИХ ПРОЦЕССОВ
Методические указания к выполнению практического задания (на примере создания концептуального проекта
ГАУ изготовления детали «Вал»)
2
Указания по оформлению
Пояснительная записка оформляется на листах формата А4 14 шрифтом с межстрочным интервалом 1.5. Размеры полей: левого – 30 мм, правого – 15 мм, верхнего и нижнего 20 мм.
В работе должны быть приведены исходные данные для заданного варианта. Варианты задаются в соответствии с методическими указаниями.
Работа должна иметь сквозную нумерацию страниц и рисунков. При использовании в записке формул, справочных данных необходимо делать ссылки на литературные источники (название источника, номер таблицы или страницы). Следует избегать сокращения слов. В конце записки делается список использованной литературы и оглавление.
Содержание пояснительной записки излагается в ясной и сжатой форме, технически грамотным языком на одной стороне листа с тем, чтобы с другой стороны можно было внести дополнения или исправления после рецензирования.
3
Методические указания к выполнению практического задания
Структура пояснительной записки к практическому заданию должна соответствовать следующей последовательности:
ТИТУЛЬНЫЙ ЛИСТ
1.СОДЕРЖАНИЕ.
2.ЗАДАНИЕ
3.ОСНОВНАЯ ЧАСТЬ
3.1.Анализ исходных данных
3.2.Определение потребности в технологическом оборудовании
3.3.Разработка компоновок ГПМ
3.4.Разработка структуры ГАУ
3.5.Описание функционирования подсистемы
3.6. Система управления ГАУ
3.7. Алгоритм и циклограмма перемещения элемента материального потока
4. ИСТОЧНИКИ ЛИТЕРАТУРЫ.
Оформление титульного листа приведено в приложении 1.
Содержание основой части следует делать в соответствии со следующими рекомендациями:
1. В разделе «Анализ исходных данных» требуется:
1.1. Проанализировать конструкцию детали. Описывается ее тип,
материал, массогабаритные показатели и дается оценка ее технологичности.
1.2.Описать технологический процесс изготовления детали и дать его оценку с точки зрения готовности к автоматизации.
1.3.Определить степень автоматизации используемого оборудования и сделать выводы о его готовности работать в составе ГПС. Определить возможные варианты модернизации, дооснащения вспомогательными средствами или замены используемого оборудования.
4
2.В разделе «Определение потребности в технологическом оборудовании» оценку уровня автоматизации станочной подсистемы ГПС,
обеспечивающей производственную программу в соответствии с заданной производительностью. Рассчитать степень загрузки оборудования и определить потребность в технологическом оборудовании каждого наименования.
3. В разделе «Разработка компоновок ГПМ», на основе принятых решений в разделе 1.3, определить структуру ГПМ и (или) ГПК. При разработке можно использовать как готовые типовые решения автоматизации, так и осуществлять подбор и компоновку средств обеспечения работы оборудования в автоматическом режиме поэлементно.
Компоновки ГПМ представить в виде их схем.
4. В разделе «Разработка компоновок ГПМ»Используя типовые решения определить структуру ГАУ и определить состав ее компонентов и подсистем.
Компоновочное решение представить в виде схема компоновки ГАУ.
5.В разделе «Описание функционирования подсистемы …» описание элементы подсистемы, их функционирования и выполнение расчета степени автоматизации подсистемы ГАУ производится применительно к особенностям используемого оборудования, разработанной компоновки и организации участка.
6.В разделе «Система управления ГАУ» необходимо представить структуру системы управления ГАУ. При разработке схемы управления ГАУ учитывать, что системы управления сложными техническими объектами строятся на основе иерархического подхода. Выполняя этот пункт задания КР нужно определить подчиненность каждого из элементов ГАУ.
4. В разделе «Алгоритм и циклограмма перемещения элемента материального потока» разрабатывается алгоритм и циклограмма.
При разработке алгоритма действий по перемещению элемента материального потока подсистем ГАУ в соответствии с заданным маршрутом для простоты описания избегания ошибок рекомендуется на схему
5
участка нанести маршрут элемента материального потока от исходного до конечного пункта перемещения. Алгоритм оформляется в виде блок-схемы в соответствие с ГОСТ 19.701-90.
Циклограмма последовательности работы механизмов и узлов оборудования, входящего в состав ГПМ, является иной формой представления алгоритма его работы с привязкой к оборудованию и его элементам и служит исходной информацией для создания системы управления всем участком.
Следует отметить отсутствие необходимости включать в циклограмму все механизмы комплекса, т.к. многие группы механизмов управляются самостоятельно от своих систем управления. Например, из всех механизмов станка в циклограмму следует включить механизм зажима детали, привод главного движения, ограждение. Работу позиционных промышленных роботов можно описать положением схвата в основных точках позиционирования, т.е.
в точках зажима и разжима схвата. Циклограмму роботов с цикловой системой управления лучше строить для отдельных степеней подвижности.
Главная особенность циклограмм последовательности состоит в том,
что она не временная, а потактовая. Каждый такт циклограммы отражает новое положение механизмов автоматической системы, при этом соблюдается строгая последовательность их срабатывания от такта к такту.
Для удобства составления циклограммы, весь комплекс следует разбить на модули, а последние, в свою очередь, на отдельные виды оборудования. В
результате анализа построенной циклограммы даются рекомендации для разработки системы управления автоматическим комплексом и проектируется ее структурная схема. Рисунок структурной схемы системы управления дополняется необходимыми подписями, а также пояснительным текстом с описанием составных элементов и информационных связей между ними.
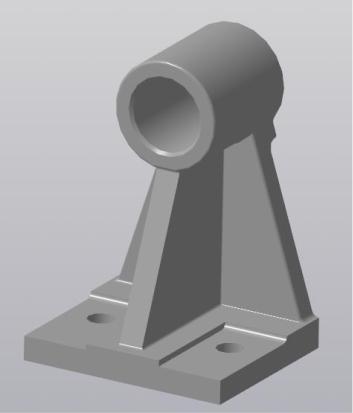
6
ЗАДАНИЕ
Деталь–представитель «Кронштейн».
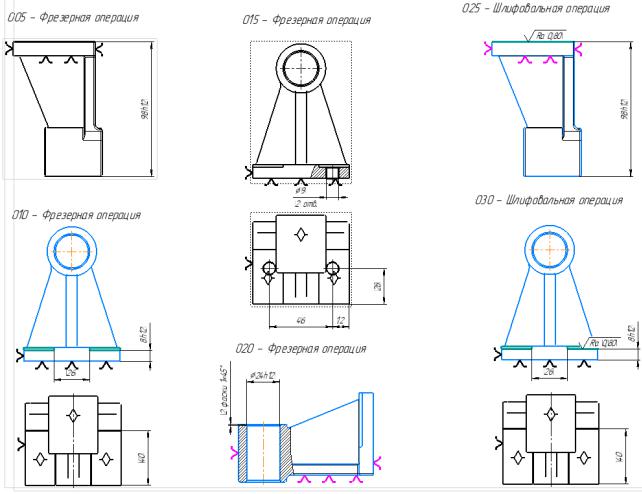
7
Рис. 2 Типовой технологический процесс изготовления детали-представителя
№ операции |
005 |
010 |
015 |
020 |
025 |
030 |
|
|
|
|
|
|
|
|
|
Время выполнения, мин |
5 |
4 |
5 |
5 |
6 |
6 |
31 |
|
|
|
|
|
|
|
|
Производственная программа 18000 шт. Элемент материального потока – деталь
Система контроля состояния режущего инструмента
8
Выполнение практическогозадания начинается с анализа изделия и технологического процесса его изготовления.
1. Анализ исходных данных
1.1. Анализ детали «Кронштейн».
Деталь «Кронштейн» с габаритными размерами: длина 70 мм, ширина 60 мм, высота 98 мм.
«Кронштейн» изготавливается из СЧ18 марка серого чугуна с пластинчатым графитом для отливок, изготовленного по ГОСТ 1412-85
Масса детали 0.7 кг.
1.2. Анализ технологического процесса изготовления детали «Вал». Заготовка кронштейна - литая. Основные формообразующие операции,
выполняются на фрезерном станке марки 6Р12. Для их окончательной обработки используются шлифовальные станки марки 3Б722
1.3. Анализ оборудования, используемого в технологическом процессе.
1.3.4. Станок 6Р12
На операции 005, 010, 015, 020 используется станок 6Р12 – консольный вертикально-фрезерный.
Станок вертикально-фрезерный консольный модель 6Р12 Станок предназначен для фрезерования разнобразных изделий из черных
и цветных металлов, обработка производится торцовыми, концевыми и специальными фрезами.
Класс точности станка Н.
Вращение шпинделя и подача стола осуществляются от отдельных электродвигателей через кору скоростей и коробку подач.
Стол может совершать быстрые перемещения рабочие подачи в продольном, поперечном и вертикальном направлениях.
Механический привод стола и привод вручную сблокированы. Выключение механического перемещения стола может производиться
упорами или вручную. Торможение шпинделя обеспечивается электромагнитной муфтой.
Повышенная мощность электродвигателей и жесткость станка, широкий диапазон скоростей шпинделя и подач стола обеспечивают высокопроизводительную обработку изделий на скоростных режимах резания.
Год исполнения установочной серии—1972.
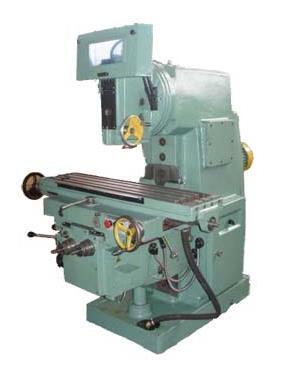
9
ОСНОВНЫЕ ДАННЫЕ Размеры рабочей поверхности стола, мм . 1250 х 320 Наибольшее перемещение стола, мм:
продольное |
800 |
|
|
поперечное |
250 |
|
|
вертикальное |
420 |
|
|
Электродвигатель привода главного движения: |
|||
мощность, кВт . ' . . . ■ . |
7,5 |
|
|
частота вращения, об/мин . . . 2000 |
|
||
подач: |
|
|
|
мощность, кВт |
2,2 |
|
|
частота вращения об/мин . . . |
2000 |
|
|
Габарит станка, мм |
2305 х 1950 |
х 2020 |
|
Масса станка, кг |
3120 |
|
|
|
|
|
Табл. 1.5. |
|
Расчет коэффициента автоматизации станка модели 6Р12 |
|
|
|
|
|
|
№ п/п |
Наименование функции |
Уровень |
Значение |
|
|
автоматизации |
|
1. |
Включение оборудования |
ручное |
0 |
2. |
Установка заготовки на станке |
ручная |
0 |
3. |
Закрепление заготовки на станке |
ручное |
0 |
4. |
Обработка заготовки |
автоматизированная |
0,5 |
5. |
Контроль обрабатываемой |
ручной |
0 |
|
поверхности |
|
|
6. |
Контроль режущего инструмента |
ручной |
0 |
7. |
Смена инструмента |
ручная |
0 |
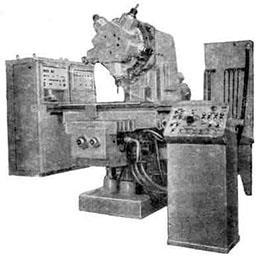
10
8. |
Очистка базовой поверхности стола |
ручная |
0 |
9. |
Удаление стружки |
ручная |
0 |
10. |
Выключение оборудования |
ручная |
0 |
ИТОГО: |
|
0,5 |
Ka(6Р12) = 0.5/10 = 0.05
Учитывая низкий уровень автоматизации и то что станок не автоматизирован его не возможно использовать в составе ГПС без глубокой модернизации.
Возможные варианты действий:
1.вынести фрезерную операцию за пределы ГАУ в отдельную, не автоматизированную позицию
2.заменить используемое оборудование на автоматизированное, например
6Р11Ф3-1 или 6Р13РФ3
Произведенм замену используемого оборудование на его аналог или
6Р13РФ3 6Р13РФ3. Станок вертикальный консольно-фрезерный с ЧПУ и
револьверной головкой Станки предназначены для многооперационной обработки деталей
сложной конфигурации из стали, чугуна, цветных и легких металлов, а также других материалов. Наряду с фрезерными операциями на станках можно производить точное сверление, растачивание, зенкерование и развертывание отверстий
Технические характеристики: |
|
Характеристика |
Наименование |
Длина рабочей поверхности стола, мм |
1600 |
Ширина стола, мм |
400 |
Наибольшее перемещение по осям X,Y,Z, мм |
1000_400_380 |
Серия |
1975 |