
Пособие надежность. Ч1
.pdf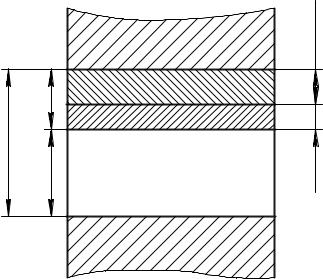
равен разности между наибольшим Òmax |
и наименьшим Òmin |
допустимы- |
ô |
ô |
|
ми значениями этого размера, определенными, исходя из допустимого изменения эксплуатационных показателей изделия (рис. 2.1).
|
|
ýê |
|
|
Ò |
|
ô |
|
|
Ò |
|
max ô |
|
|
Ò |
in |
ê |
|
m ô |
Ò |
|
T |
|
Рис. 2.1. Схема расположения полей допусков |
В функциональный допуск Тф входят эксплуатационный Тэк и конструкторский Тк допуски. Первый характеризует запас точности, необходимый для сохранения требований точности детали в процессе длительной эксплуатации, второй идет на компенсацию различных погрешностей. В случае сопрягаемых поверхностей конструкторский допуск учитывает погрешности изготовления деталей, погрешности сборки соединений и машин, их регулировки, а также компенсирует прочие погрешности.
Конструкторские допуски также связаны с функциональным (служебным) назначением машины и условиями ее работы. Собственно допуск устанавливают на основе анализа работы машины с учетом затрат на ее изготовление и последующую эксплуатацию (с помощью теоретических и экспериментальных данных).
Погрешности, возникающие на различных этапах ТП, взаимосвязаны. Точность сборки машины зависит от точности изготовления ее деталей, а последняя в свою очередь зависит от точности изготовления заготовок,
40
поскольку их свойства в определенной степени наследуются готовыми деталями. Поэтому вопросы точности должны решаться не изолированно, а комплексно для всего производственного процесса.
Допуски на промежуточные размеры, возникающие в ходе ТП, называют технологическими. Они связаны со сложным влиянием комплекса технологических факторов на возникновение погрешностей обработки. Чтобы технологический допуск был меньше конструкторского, такие погрешности должны быть сведены к минимуму. В этом случае облегчается процесс сборки отдельных соединений и машин в целом. Анализ соотношений между конструкторскими и технологическими допусками позволяет судить о совершенстве ТП.
Механическая обработка заготовок резанием обеспечивается на металлорежущих станках, оснащенных различными приспособлениями, режущими и вспомогательными инструментами. Собственно станок (С), заготовка (3), приспособление (П) и инструмент (И) образуют кинематическую и динамическую системы, элементы которых связаны между собой и замыкаются через линию или линии контакта режущей части инструмента с заготовкой. Если такого замыкания не происходит, процесс обработки осуществить нельзя. На рис. 2.2, а показано нарезание цилиндрического зубчатого колеса с косым зубом на зубофрезерном станке, а на рис. 2.2, б – принципиальная кинематическая схема фрезерования зубьев методом обкатывания. Обкатывание осуществляется звеньями обката, которыми служат сменные зубчатые колеса 4, связывающие вращение фрезы 3 с вращением делительного червяка 6, находящегося в зацеплении с делительным червячным колесом 1; последнее жестко связано со столом 5, на котором крепится оправка с нарезаемой заготовкой 2. Сменные зубчатые колеса 4 сообщают заготовке 2 такое согласованное вращение, которое она должна была бы иметь, если бы зубья заготовки находились в постоянном зацеплении с червяком (вращающейся фрезой 3). Каждый из указанных элементов не является идеальным по своим функциональным показателям. Все элементы переносят свои отклонения функциональных показателей, в какой-то степени
41
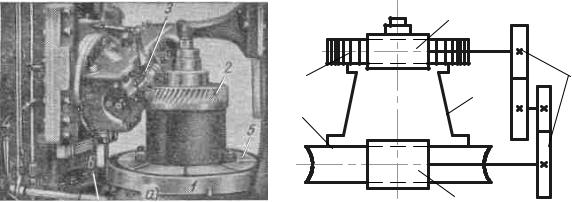
на обрабатываемые поверхности заготовки при изготовлении из нее детали. Кроме того, сам процесс резания характеризуется нестабильностью технологических факторов, которые также вносят свои изменения в показатели качества деталей. В данном случае термин «качество» употребляется в широком смысле как «совокупность свойств продукции, обуславливающих ее пригодность удовлетворять определенные потребности в соответствии с ее назначением» (ГОСТ
15467-79).
3 |
|
3 |
2 |
2 |
4 |
|
|
5 |
|
1 |
|
|
5 |
|
6 |
|
|
1 |
|
6 |
|
|
|
а |
|
б |
Рис. 2.2. Работа на фрезерном станке:
а – нарезание косого зуба на заготовке, б – схема фрезерования зубьев методом обкатки: 1 – червячное колесо; 2 – заготовка; 3 – фреза; 4 – сменные зубчатые колеса; 5 – стол; 6 – червяк
Известно, что в процессе обработки сила резания изменяется в результате неравномерности глубины резания из-за непостоянства размеров заготовки в пределах допуска, нестабильности физико-механических свойств материала заготовок и прогрессирующего затупления режущего инструмента. Сила резания при обработке вызывает упругие отжатия элементов технологической системы. Их величина зависит как от силы резания, так и от жесткости элементов, т. е. их способности противостоять действующей силе. Нестабильность силы резания и жесткости элементов технологической системы в их различных сечениях вызывает неравномерность упругих отжатий, в результате чего возникают погрешности формы обработанной поверхности у индивидуальных заготовок и колебания выдерживаемых размеров при изготовлении партии деталей
42
Каждая деталь машины представляет собой сочетание поверхностей. При всем многообразии деталей современных машин число видов поверхностей ограничено. Это – цилиндрические, конические, плоские и фасонные поверхности. Точность механической обработки заготовок, связанная с функционированием замкнутой технологической системы элементов, проявляется в трех аспектах: точность размеров, точность формы и точность расположения поверхностей.
Точность размеров различных поверхностей деталей должна соответствовать допускам. Так, возникающие отклонения диаметров шеек валов, отверстий втулок, толщины зубьев зубчатых колес, различных углов наклона поверхностей и т. п. могут колебаться в соответствии со значениями допусков. Точность размера в значительной степени определяет качество продукции. По своему назначению размеры могут быть отнесены к различным группам. Координирующие размеры используют для определения взаимного расположения поверхностей деталей, а также их осей. Это размеры, как правило, ответственных поверхностей, определяющих служебное назначение детали. Например, у корпусных деталей типовыми являются плоские привалочные поверхности и основные отверстия для размещения опорных подшипников валов. Координирующие размеры увязывают между собой расположение плоских и посадочных поверхностей отверстий корпусов, взаимное расположение основных отверстий и других поверхностей.
Сборочные размеры определяют положение одних элементов машин относительно других. Это размеры прежде всего присоединительных поверхностей. У корпусных изделий присоединительными чаще всего бывают плоские поверхности, кольцевые выступы или выточки. Кроме указанных применяют технологические межоперационные размеры, которые необходимы при изготовлении деталей и их контроле по ходу технологических процессов.
К какой бы группе не относился размер, его точность непосредственно влияет на качество машины, т. е. на способность выполнять свои функции в установленных пределах.
Решение проблемы точности требует еще одного аспекта рассмотрения понятия «размер». Различают номинальные, действительные и предельные
43
размеры. Относительно номинального определяют предельные размеры. Номинальный размер служит началом отсчета отклонений и устанавливается конструктором, исходя из служебного назначения детали. Поскольку технологическая система «станок – приспособление – инструмент – заготовка» не может обеспечить постоянный (номинальный) размер из-за особенностей ее функционирования, вводят понятие действительного размера. Его определяют измерением с допустимой погрешностью. Действительные размеры не должны отличаться от номинальных более, чем на допустимую величину. Поэтому различают два предельных размера – наибольший и наименьший. Значение номинального размера находится между наибольшим и наименьшим, а также может быть равно одному из них.
Размер, называемый действительным, для оценки качества продукции имеет особое значение. В ходе изготовления детали в каждый момент времени этот размер оказывается различным. Физическая природа этого явления связана с использованием в машиностроении реальных технологических систем, которые имеют погрешности собственного изготовления, работают в условиях постоянного изнашивания инструмента и, следовательно, постоянно изменяющихся силовых факторов. Кроме того, они воспринимают действие нестационарного теплового поля, переменной жесткости. На качество детали по параметру точности влияют также погрешности настройки инструмента, установки обрабатываемой заготовки и ряд других факторов.
Детали, изготовленные с соблюдением допусков на размеры, способствуют созданию качественной машины, несмотря на то, что каждая деталь ограничена поверхностями, размеры которых отличаются от номинальных.
Детали лишь на чертежах характеризуются номинальными геометрически правильными (идеальными) поверхностями, а фактически ограничены реальными поверхностями. Детали всегда имеют отклонения формы.
Обеспечение точности формы всегда связано с преодолением технологических трудностей, гораздо более ощутимых, чем в случае достижения за44
данного размера. В частности, в производственных условиях возникают отклонения от круглости и цилиндричности поверхностей вращения. Они непосредственно сказываются на качестве соединений, имеющих цилиндрические поверхности, потому что определяют фактическую площадь контакта сопрягаемых поверхностей, по которым устанавливают ответственные детали и, прежде всего, подшипники скольжения или качения. Подшипники вследствие отклонения формы могут быстрее утратить свои первоначальные характеристики и в конечном итоге надежность.
Условия формообразования деталей оказываются настолько сложными, что одновременно возникает целый ряд отклонений геометрического характера: отклонение от цилиндричности, плоскостности и др. Технологическое обеспечение геометрических параметров в заданных пределах является одним из условий обеспечения качества машин. Так, у пары «вал – втулка корпуса» при имеющихся отклонениях от цилиндричности опорных шеек вала и отверстий втулок общая ось вращения вала не совпадает с геометрически правильной осью сопрягаемых поверхностей. Следовательно, такая пара из-за отклонений формы не обеспечивает необходимого качества соединения.
При оценке точности формы необходимо использовать количественные показатели. На рис. 2. 3 представлено схематическое изображение отклонений размеров, формы и расположения поверхностей детали типа двухступенчатого вала. В любом поперечном сечении размеры вала определяются переменным радиусом Ri(φi, xi), отсчитываемым от центра О номинального сечения диаметром DH. Радиус Ri(φi, xi), являющийся текущим размером, зависит от угловой φi и осевой xi координат. Текущий размер будет также меняться от осевой координаты xi. Любой профиль поперечного сечения вала удовлетворяет условию замкнутости, т. е. f(φi)=f(φi+2π). Период функции равен
2π.
Реальный профиль диаметром D на левом торце вала ограничен прилегающей окружностью (на рис. 2. 3 показана пунктиром). Отклонение от круглости, характерное для каждого поперечного сечения, определяют по
45
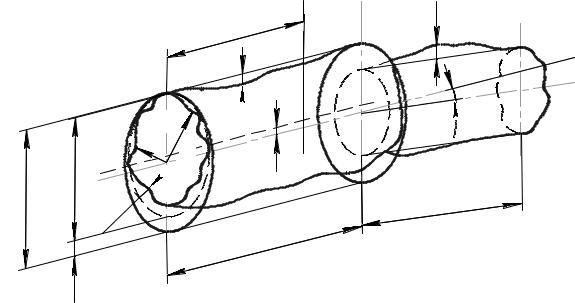
круглограммам по специальной методике и обозначают ∆Ф. Следовательно, для каждого сечения можно определить ∆D – отклонение размера. Прилегающая окружность имеет центр в точке О1. Поэтому действительный контур детали отличается от номинального (идеального) прилегающего цилиндра, а их оси смещены на величину эксцентриситета е. При более тщательном анализе геометрической картины образования действительного контура детали можно убедиться, что его ось в общем виде не является прямой линией. Тот факт, что на практике оси часто считают прямыми, является условностью, которая, однако, в большинстве случаев удовлетворяет машиностроителей. Приведенный анализ характерен для любого сечения ступени А вала длиной l1.
Í D
D
DD
DÔ
R |
R |
1 |
|
Î1
Î
z
D
å
l1
A
1 D
Q
l2
B
Z
Рис. 2. 3. Схема определения отклонений размеров, формы и расположения
Отклонения формы весьма удобно описывать с помощью рядов Фурье. Рассмотрим функцию погрешности действительного профиля f(φi) в полярной системе координат
|
a0 |
k=∞ |
|
f (ϕi ) = |
+ ∑(ak cos kϕi +bk sin kϕi ) , |
||
|
|||
2 |
k=1 |
46
где а0/2– нулевой член разложения; ak ,bk – коэффициенты ряда Фурье k – ой гармонической составляющей, k – порядковый номер соответствующей гармоники.
Вместо рядов для практических целей удобно пользоваться тригонометрическим полиномом
|
Ñ0 |
k=p |
|
f (ϕi ) = |
+ ∑(Ck cos kϕi + γk ) , |
||
2 |
|||
|
k=1 |
где p – порядковый номер высшей гармоники разложения.
Отношение С0/2 можно принять в качестве среднего значения функции f(φi) за период τ = 2π и определять как расстояние от базового значения текущего размера до средней линии геометрических отклонений профиля. Поэтому значение C0/2 представляет собой отклонение размера.
Первый член разложения С1cos(φi+ γ1) характеризует расстояние между центрами вращения О1 и геометрическим центром О, т. е. эксцентриситет е (см. рис. 2.3). Такой эксцентриситет указывает на отклонение расположения реального профиля поверхности и выражает его количественно. Последующие члены полинома (начиная со второго) описывают спектр гармонических составляющих отклонений формы детали в поперечном сечении.
Второй член C2(cos2φi+γ2) характеризует овальность сечения, третий С3(cos3φi+γ3) – огранку с трехвершинным профилем и т. д. Поэтому поперечное сечение детали следует представлять очерченным сложным контуром, имеющим отклонение размера, с центром, смещенным от геометрического центра. Контур имеет овальную форму, на которую наложены огранки с различным числом вершин Дальнейшее рассмотрение членов ряда приводит к высокочастотным составляющим, соответствующим волнистости и шероховатости.
Высказанные соображения характерны и для ступени В вала длиной l2 (см. рис. 2.3). Однако у этой ступени может оказаться своя ось, повернутая на угол Θ в любой из плоскостей относительно оси OZ, а также могут возникать свои собственные погрешности. Отклонения профилей поперечных сечений
47
по длине ступеней, т.е. погрешности формы вдоль оси, целесообразно представлять и в продольных сечениях. Тригонометрический полином для описания профиля продольного сечения может быть применен на основе цилиндрической системы координат.
Первый член разложения в этом случае характеризует конусообразность, второй – выпуклость, а при сдвиге фазы – вогнутость контура. Так, применительно к рис. 2.3, на ступени А вала возникла седлообразность (вогнутость) с отклонением ∆, а на ступени В – бочкообразность (выпуклость) с отклонением ∆1.
По аналогии с предыдущим профиль детали в продольном направлении представляет собой сложное сочетание конических поверхностей с наложением на них седлообразных, бочкообразных, волнистых профилей поверхностей. Все профили в поперечных и продольных сечениях всегда формируются из-за несовершенства технологических систем. Отклонения от идеальных профилей при определенных условиях осуществления ТП могут быть малы. Но только сравнение их с допустимыми величинами может показать, можно ли ими пренебречь. Если отклонения больше допустимых, необходимо принимать меры к тому, чтобы технологическая система обеспечивала бы необходимую точность. Поэтому возникает проблема управления точностью обработки с помощью соответствующих технологических решений при построении отдельных операций и ТП в целом.
Качество деталей оценивают также отклонениями расположения поверхностей, т. е. отклонениями реального расположения поверхностей от номинального. Такие отклонения возникают в результате функционирования технологических систем и при смене схем базирования при выполнении отдельных операций ТП.
При оценке отклонений расположения поверхностей отклонения формы из рассмотрения исключают, а реальные поверхности заменяют идеальными, называемыми прилегающими поверхностями. Каждое из отклонений расположения поверхностей имеет свое точное определение и методику произ48
водственной оценки. Прилегающими элементами могут быть прямые линии, окружности, плоскости, цилиндры.
Оценить качество деталей по отклонению от параллельности можно, измерив расстояние между двумя прилегающими к реальным поверхностям плоскостями в различных точках нормируемого участка. Отклонения расположения поверхностей можно определить и с помощью осей или плоскостей симметрии. На рис. 2.3 ступени А и В вала имеют прямолинейные оси. Взаимное расположение ступеней вала определяется несоосностью с величиной смещения е и углом перекоса осей Θ. В общем случае оси различных поверхностей деталей могут иметь отклонения от параллельности, соосности, а также перекос или отклонение от пересечения. Типичным для деталей, имеющих отверстия (например, корпусных или класса втулок), является отклонение от соосности. Такое отклонение решающим образом влияет на надежность подшипников, установленных в отверстиях корпусов.
С помощью прилегающих элементов определяют отклонение от перпендикулярности, которое, например, можно оценивать углом между двумя плоскостями, прилегающими к реальным поверхностям конкретной детали. При оценке отклонений от симметричности относительно базовой плоскости определяют положение последней и от нее измеряют расстояние до плоскости симметрии реального профиля.
Все отклонения формы и расположения поверхностей должны быть рассмотрены применительно к конкретным деталям, исходя из их служебного назначения. Так, в одном случае решающее влияние на качество функционированиядеталей оказывает отклонение от круглости, в другом – перекос осей и т. д. Числовые значения отклонений формы и расположения поверхностей в каждой стране представлены соответствующими нормами.
Для практики удобно указывать отклонения формы и расположения в процентах от допуска на размер. Для этого потребовалось дополнительно ввести понятие уровня точности. Так, для первого уровня точности отклоне-
49