
Пособие надежность. Ч1
.pdf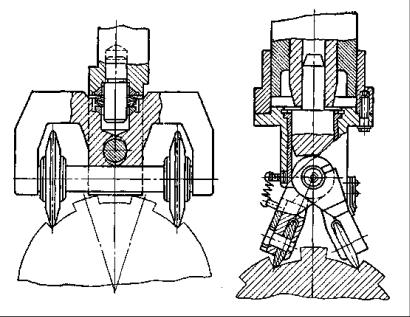
карьерных экскаваторов. Приспособление для накатки впадин шлицев оснащено двумя роликами (рис. 4.13).
Шлицы упрочняются после закалки с нагревом т. в. ч. Закалка с нагревом т. в. ч. повысила контактную и изгибную прочность шлицев, но по границам закаленной зоны прочность, как и в случае с зубчатыми колесами, оказалась сниженной. Поверхностный наклеп устраняет этот недостаток, как бы дополняя закалку. Наряду с формообразованием, эффективно обкатывание по впадинам предварительно нарезанной резьбы. Она применяется при шаге резьбы более 8...10 мм. Особенно результативны в этом случае приспособления с вибрирующими роликами.
а б
Рис. 4.13. Приспособление для упрочнения впадин шлицев на валах: а – накаткой, б – чеканкой
Выше уже приводились примеры, когда в приспособлениях для обкатывания вместо роликов применяются шарики. Они позволяют уменьшить усилие обкатывания. В приспособлении, показанном на рис. 4.14, давление создается центробежной силой шариков, размещенных в гнездах диска, вращающегося со скоростью шлифовального круга. Для увеличения силы удара заготовка вращается в направлении обратном вращению диска с шариками, скорость вращения заготовки равна 30...90 м/мин. Чем больше диаметр шариков и вели-
200
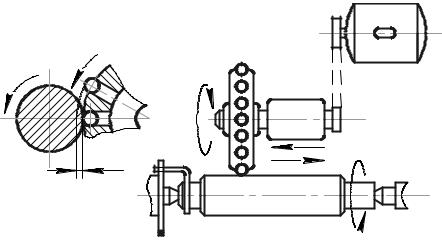
чина их выхода из сепаратора h, тем больше при данной скорости сила удара шариков, тем интенсивнее наклеп.
Шариковые обкатники, наряду с роликами, применяют для упрочнения плоскостей и торцов. Сжимающие напряжения, создаваемые при этом, достигают 300...700 Н/мм2, на 30...40 % может быть повышена твердость и до 9...11-го классов улучшена шероховатость поверхности. Процесс отличается высокой производительностью и имеет ряд преимуществ перед шлифованием, шабрением и другими способами обработки плоскостей, особенно в отношении повышения износостойкости.
h |
Рис. 4.14. Приспособление для обкатывания валов центробежной силой шариков
Обкатывание плоскостей может производиться на строгальных, токарных, вертикально-фрезерных станках. На рис. 4.15 представлена фреза-обкатник, являющаяся комбинированным инструментом для обработки плоскостей на вертикально-фрезерном станке. Совмещение обработки резанием с упрочнением поверхности обкатыванием позволяет сократить цикл и трудоемкость обработки. Фреза-обкатник состоит из корпуса фрезы 1, в котором установлен и закреплен корпус 6 обкатной головки. Резцы 9 закреплены в корпусе клиньями 2 и винтами 3 Шары 7 расположены в сепараторе 5, который может свободно вращаться относительно корпуса головки на шарикоподшипнике 4. Шары 7 упираются в кольцо 8 упорного шарикоподшипника, напрессованного на выступ корпуса головки. Выступание шаров относительно вершин резцов (натяг) регулируется гайкой 10. Давление шаров на обрабатываемую по-
201
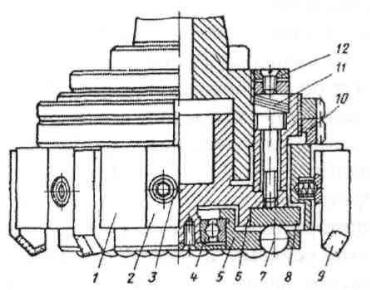
верхность создается гайками 12 через тарельчатые пружины 11. Рекомендуется натяг 0,05...0,15 мм при подаче на шар 0,03...0,08 мм и глубине резания
1...3 мм
Рис. 4.15. Фреза-обкатник
К недостаткам комбинированных инструментов для совмещенной обработки деталей, в том числе на станках токарного типа, следует отнести неодинаковую скорость изнашивания резцов и шаров (роликов) Более быстрый износ резцов меняет условия упрочнения, неблагоприятно отражается на точности и шероховатости обработки. Кроме того, процесс часто затрудняется из-зa попадания под упрочняющие шары или ролики стружки. Комбинированные инструменты к тому же являются менее универсальными. При упрочнении деталей обкатыванием в зону обработки подается масло или сульфофрезол, которые снижают коэффициент трения и уменьшают температуру нагрева и потребляемую мощность. Смазка улучшает также качество поверхности. В качестве смазки применяют смесь машинного масла (40 %) и веретенного (60 %). Весьма эффективны паста ВНИИ МП-232 или порошок дисульфида молибдена. Порошок предварительно втирается в поверхность, подлежащую обработке, войлочным или фетровым притиром, расход порошка составляет 5...8 г/м2 поверхности.
202
В условиях производства контроль качества упрочнения обкатыванием сводится к наблюдению за стабильностью усилия при обкатывании. Устройства для обкатывания часто оснащают самописцами, позволяющими получить объективную картину изменения усилия при обработке каждой детали. Иногда об эффективности упрочнения судят по приросту твердости. Такой контроль, однако, может привести к ошибкам, так как прирост твердости нередко наблюдается и тогда, когда уровень остаточных сжимающих напряжений, больше всего влияющих на повышение усталостной прочности, из-за наступающего перенаклепа начинает снижаться.
5. Упрочнениедеталейчеканкой
Чеканка применяется для упрочнения канавок, выточек, шлицев, шпоночных пазов, галтелей и других поверхностей, являющихся концентраторами напряжений, а также для упрочнения зубчатых колес, сварных швов и т. д. Малые размеры бойка позволяют достичь большой энергии удара на единицу поверхности. Эффект упрочнения поэтому может быть очень высоким: остаточные напряжения могут составлять 600...800 Н/мм2, степень наклепа – 30...50 %, глубина – несколько миллиметров, долговечность деталей увеличиваться в 1,5 раза и более. Чеканку можно также применять для создания нужного рельефа поверхности в целях лучшего удержания на ней смазки, повышения сопротивления относительному перемещению, восстановления плотности неподвижных посадок, уменьшения влияния контактной коррозии.
При выборе режима упрочнения чеканкой исходными данными являются требуемые глубина и степень наклепа, а также шероховатость поверхности. Проф. И. В. Кудрявцев степень наклепа оценивает коэффициентом ε, представляющим собой отношение диаметра отпечатка d, образующегося при ударе сферическим бойком (шариком), к диаметру D самого шарика, т. е. ε=d/D. Для малоуглеродистых сталей рекомендуется 0,3≤ ε ≤ 0,5, а для конструкционных 0,3 ≤ ε ≤ 0,7. При меньших значениях ε эффект упрочнения,
203
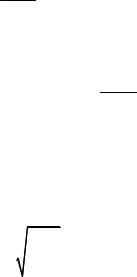
оцениваемый по приросту твердости, незначителен, при больших – сильно повышается шероховатость поверхности, замедляется и прирост твердости.
Динамическое, приложение нагрузки, по сравнению со статическим нагружением, увеличивает диаметр отпечатка в 1,25...1,58 раза, т. е.
=1.25...1.58 ;
или в общем виде
=1.54 −1000HB .
Глубина наклепа задается в зависимости от сечения детали и задач упрочнения. Ее зависимость от предела текучести стали при растяжении σт и диаметра получаемого отпечатка устанавливается формулой
a = |
Ð |
1,5dmax , |
|
||
|
2σò |
где Р – усилие, прикладываемое к бойку (пуансону).
Для значительной части конструкционных сталей σт=НВ/6.
Диаметр шарика (сферического наконечника) может быть выбран в зависимости от желательной глубины наклепа в пределах а ≤D≤2,2а. При ориентировочных расчетах потенциальной энергии упрочнителя, предназначенного для обработки наклепом конструкционных сталей средней твердости (НВ 110...210), можно пользоваться формулой
Ý |
1,2Ý |
= |
Í Âd 4 |
, |
|
||||
ï |
ó |
|
6D |
|
|
|
|
|
где Эу – энергия удара.
В рассмотренной методике эффективность наклепа оценивалась только по приросту твердости. Во многих случаях не менее важной характеристикой является уровень получаемых остаточных напряжений сжатия. Закономерность их изменения может не совпадать с изменением твердости.
Наиболее распространены разработанные в ЦНИИТМАШ чеканочные приспособления пневматического типа ЧМ-1, ЧМ-2, ЧМ-3 с энергией удара со-
204
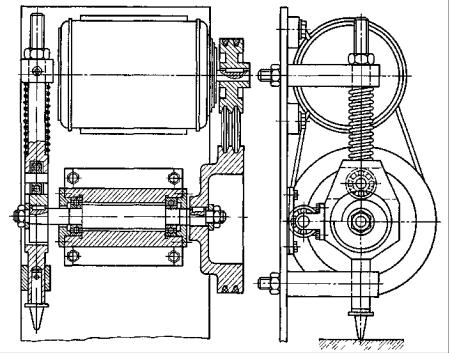
ответственно 30; 34 и 45 Н·м. Часть из них создана на базе пневматических молотков. Они могут закрепляться в суппорте токарного станка или использоваться для внестаночного упрочнения. Для чеканки галтелей крупных валов приспособление можно закреплять с помощью переходной муфты с кронштейном на шейке вала. Чеканочные пружинные приспособления (рис. 4.16) устанавливают на станине станка, они могут быть одно- и многошпиндельными.
Рис. 4.16. Приспособление для чеканки с механическим приводом
Галтели коленчатых валов упрочняют бойками с радиусом сферы меньше радиуса галтели за два или три прохода, т. е. с образованием двух или трех канавок. Такая чеканка не менее эффективна, чем однопроходная. Шероховатость поверхности после чеканки может быть улучшена последующей подшлифовкой или полировкой, а также дополнительным проходом бойком большего диаметра.
Упрочнение коленчатых валов некоторых двигателей производят виброгидравлической чеканкой. Валы изготовлены из стали 45, шейки закалены после нагрева т. в. ч. на глубину 2,5...4,5 мм до твердости HRC 52...54. Статическая нагрузка при виброгидравлической чеканке сочетается с ударной; глубина наклепа при Р = 20 кН достигает 4,5...5 мм, т. е. составляет 0,1R шейки (d =
205
88 мм). Наклеп при такой большой его глубине можно проводить до окончательного шлифования, тогда небольшое коробление, которое возникает при чеканке, устраняется шлифованием.
Установка для виброгидравлической чеканки имеет насос-пульсатор и упрочняющие головки, которые навешиваются на шейки вала, установленного в центрах станка, и опираются на станину станка. Пульсирующее усилие от насоса передается через два плунжера державке с двумя самоустанавливающимися шариками. Шарики контактируют сразу с обеими галтелями шейки вала. Зона пластической деформации перекрывает галтель и выходит на щеку и шейку. Максимальное увеличение твердости при чеканке в средней части галтели составляет 217 %, в крайних точках – 11...12 %. При диаметре шариков 11 мм и шаге чеканки 0,10...0,12 мм шероховатость поверхности улучшается на 2...3 класса и достигает 8...9-го класса, что исключило необходимость последующего шлифования галтелей. Предел выносливости при симметричном цикле нагружения в результате такого упрочнения увеличился на 77 %. За час упрочняется 15...17 валов, весь процесс завершается за 1,25 оборота вала.
6. Применениеметодовпластического деформированиядляотделочноупрочняющей обработкиотверстий
Обработка точных отверстий является более трудоемкой и сложной задачей, чем обработка точных наружных поверхностей.
Применяется два основных метода обработки отверстий пластическим деформированием: 1) дорнование отверстий одноили многозубыми прошивками или протяжками (дорнами), проталкиваемыми или протягиваемыми через отверстие; в отдельных случаях эту же роль могут выполнять калибрующие шарики; 2) раскатывание отверстий роликовыми или шариковыми вращающимися раскатниками.
206

5 |
2 |
4 |
2 |
4 |
2 |
4 |
2 |
4 |
2 |
3 |
1 |
3 |
5 |
Рис. 4.17. Калибрующая протяжка Дорнование отверстий многозубыми дорнами может выполняться с не-
большими или большими натягами. Дорнование с небольшими натягами является калибрующе-отделочной операцией. Инструмент, применяемый для этих целей, состоит из оправки 1 (рис. 4.17), на которую установлены рабочие 2, калибрующие и концевые кольца 3, распорные втулки 4; по концам в отверстия оправки ввернуты хвостовики 5. Рабочие и калибрующие кольца изготовляют из быстрорежущей стали Р18 или твердого сплава ВК15. Кольца из стали Р18 закаливают на твердость HRС 62...65, шлифуют до 12-го класса шероховатости и цианируют на глубину 0,02...0,05 мм. Установка их на оправке производится по скользящей посадке (кольца из твердого сплава – по напряженной посадке). Каждое кольцо имеет заборный и обратный конусы, равные 4°, между ними – цилиндрическая ленточка шириной 1,8...2 мм. Число колец может быть различным и зависит от длины отверстия и величины припуска на обработку. Наилучшие результаты по качеству поверхности обеспечивают дорны с переменной схемой увеличения натяга, так что натяг каждого последующего зуба меньше предыдущего (рис. 4.18). В противном случае нагрузка на каждый следующий зуб возрастает в связи с упрочнением металла предшествующими зубьями. Общее количество деформирующих зубьев определяют по формуле
zd = d3 +(3...5).
При этом относительный натяг на зуб не должен превышать 0,009...0,011 мм; при большем натяге растет шероховатость.
Шаг между зубьями выбирают так, чтобы в работе одновременно находилось 2...3 зуба. Диаметр калибрующих зубьев принимают равным диаметру деформирующих зубьев, имеющих максимальный натяг, этим обеспечивается хорошее центрирование дорна в отверстии и возможность перешлифовки де207
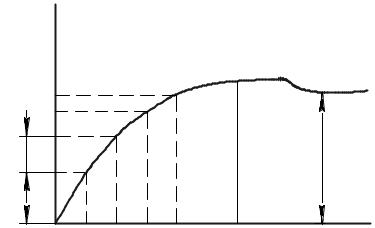
формирующих зубьев при износе. Концевые зубья, являющиеся также калибрующими, выполняются с размерами, постепенно уменьшающимися до диаметра готового отверстия. Они обеспечивают плавный выход инструмента.
протяжки,мм
Dh Dh Диаметрзубьев 1 2
1 2
последорна
îòâ |
d |
0 |
1 2 3 4 |
¹ зубьев |
Рис. 4.18. Измерение величины натяга у зубьев калибрующей протяжки: 0-1 – участок деформирующих зубьев, 1-2 участок калибрующих зубьев, ∆h1 – натяг 1-ого зуба, ∆h2 – натяг 2-ого зуба
Протяжки и прошивки, применяемые в тракторной промышленности, выполняются в виде оправок, на которых устанавливаются выглаживающие элементы из сплавов ВК8 или ВК6М (рис. 4.19). Прошивки могут быть и монолитными, а также с наплавленной рабочей частью. Но наиболее характерной особенностью рассматриваемых инструментов является применение в них выглаживающих элементов, выполненных в виде монолитных твердосплавных блоков, конструктивно оформленных в виде нескольких колец. Они имеют рабочую ленточку шириной 0,2...2 мм и два конуса – передний и задний. Такие блоки позволяют получать более точные по форме отверстия, чем при выглаживающих элементах, выполненных в виде отдельных колец. Чтобы не допустить появления волнистости на обрабатываемой поверхности, блоки выполняют
сразличным шагом между зубьями.
Вкомбинированных протяжках диаметром более 100 мм режущая часть имеет черновую и чистовую секции, по 5...6 зубьев в каждой, их изготовляют
208
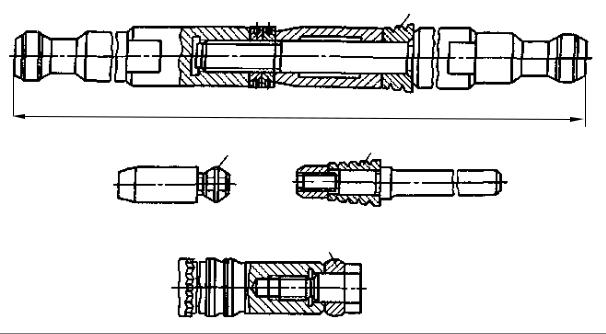
из быстрорежущей стали и устанавливают на оправке по 6-му квалитету точности, выглаживающий же элемент выполняют в виде монолитного блока. На рис. 4.19, г представлена комбинированная протяжка конструкции П. Г. Кацева, отличающаяся наибольшей простотой: в конце режущей части установлено простое выглаживающее кольцо. Чем больше у инструмента выглаживающих элементов, тем выше качество обработки и стойкость инструмента, но тем больше нагрев и усилие при протягивании (обычно инструмент имеет 2...3 элемента). Обработка ведется при сравнительно небольших скоростях резания – 5...7 м/мин для протяжек и 2...3 м/мин для прошивок. Пластическая деформация составляет 20...30 % от суммарного натяга для тонкостенных деталей (d/D≥0,7) и 30...45 % – для деталей со средней толщиной стенок
(0,5<d/D<0,7).
1
450... |
1000 |
1 а |
1 |
б |
1 |
в |
|
|
г
Рис. 4.19. Конструкции протяжек и прошивок с твердосплавными выглаживающими элементами: а – протяжка выглаживающая, б – прошивка одношаговая для 12...18 мм, в – прошивка сборная с напрессованным передним направлением; г – протяжка комбинированная конструкции П. Г. Кацева: 1 – выглаживающий элемент
209