
Защита объектов транспорта и хранения нефти и газа от коррозии 8
.pdfЗащита объектов транспорта и хранения нефти и газа от коррозии
Физико-химические основы коррозионных процессов и защитные покрытия трубопроводов и резервуаров
ВВЕДЕНИЕ
Металлические сооружения и конструкции, машины и механизмы, эксплуатируемые на открытом воздухе или проложенные под землей и водой, в постепенно подвергаются неизбежному самопроизвольному разрушению - коррозии.
Потери металла в различных отраслях народного хозяйства в странах СНГ в результате коррозии в настоящее время превышает 20 млн. тонн в год. Большая доля этих потерь приходится и на сооружения трубопроводного транспорта нефти, газа и продуктов их переработки.
К началу ХХI века общая протяженность подземных магистральных трубопроводов в странах СНГ превышала 350 тыс. км при массе металла более 130 млн. тонн. Подземные металлические сооружения представляют собой дорогостоящие конструкции, срок службы которых определяется в основном их коррозионной стойкостью. Коррозионные повреждения ответственных подземных коммуникаций наносят колоссальный материальный и экологический ущерб народному хозяйству. Он особенно ощутим в трубопроводном транспорте углеводородов, т.к. коррозия приводит к разрушению сооружений, что сопряжено с потерями металла, транспортируемых по трубам продуктов, с загрязнением окружающей среды, перерывами в перекачке и т.д.
Рациональное использование металла во многих отраслях народного хозяйства в значительной степени зависит от степени использования эффективных методов противокоррозионной защиты металлоконструкций.
1
Консорциум « Н е д р а »
Коррозия металлов – это одна из старейших и технически сложных проблем на Земле. Наука о коррозии и защите металлов изучает взаимодействие металлов и их сплавов с коррозионно-активной окружающей средой, раскрывая механизм этого взаимодействия, его общие закономерности, разрабатывает способы защиты металлов от коррозии в различных условиях.
Защитой металлов от коррозии человечество начало заниматься очень давно – почти с началом применения металлов. Еще в V веке до н.э. древнегреческий историк Геродот упоминал о применении олова для защиты железа от коррозии.
С древнейших времен стальные доспехи и оружие воинов подвергались полированию и воронению не только для улучшения внешнего вида, но и с целью защиты их от коррозии.
Начало научного изучения коррозии было положено работами великого русского естествоиспытателя М.В. Ломоносова, которому принадлежит открытие в 1748 г. закона о сохранения массы. В 1773 г. опыты М.В. Ломоносова были повторены французским химиком А. Лавуазье, который установил, что окисление металла есть соединение его с кислородом. Исключительное значение для обоснования электрохимического механизма коррозии имели работы выдающихся ученых Г. Дэви и М. Фарадея, установивших закон электролиза.
Большой вклад в мировую практику защиты металлов от коррозии внесли отечественные ученые, такие как: С.П. Власов (им были разработаны стойкие краски в 1820 г.), Б.С. Якоби (предложил защиту от коррозии цинком в 1856 г.), А.И. Онуфрович (создал устойчивое кровельное железо в 1910 г.) и др.
Новый этап в развитии науки о коррозии связан с именами таких исследователей как В.А.Кистяковский, Н.А. Изгарышев, Ю.Р. Эванс, А.Н. Фрумкин, Г.Г. Улига и многих других.
Наука о коррозии, которая является предметом изучения процессов химического или электрохимического взаимодействия металла с коррозионной средой, базируется на материаловедении и физической химии, в первую очередь на таких её разделах, как термодинамика и кинетика гетерогенных химических и электрохимических процессов.
2
Консорциум « Н е д р а »
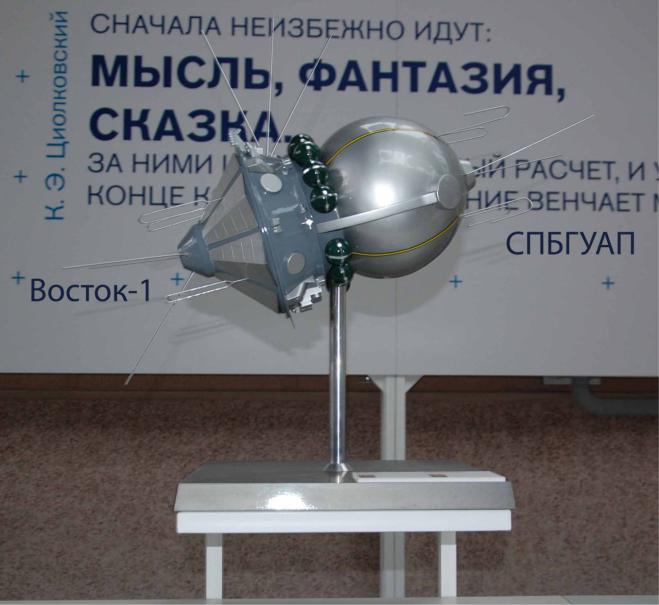
vk.com/id446425943
Макет космического корабля «Восток-1» в павильоне «Космос» на ВДНХ. За ним — цитата К. Э. Циолковского:
«Сначала неизбежно идут: мысль, фантазия, сказка. За ними шествует научный расчёт. И уже в конце концов исполнение венчает мысль»
Конечной целью науки о коррозии является разработка практических мероприятий, обеспечивающих долговечную и надежную работу различного вида технологического оборудования и конструкций в самых разнообразных условиях эксплуатации.
Впоследнее время в России и за рубежом освоены и продолжают разрабатываться новые технические средства противокоррозионной защиты металлов. Уточнены методы определения критериев коррозионной опасности и защищенности металлических сооружений – трубопроводов и резервуаров, достигнуты новые успехи в области практического осуществления эффективных мероприятий по борьбе с коррозией.
МЕТОДЫ ПРОТИВОКОРРОЗИОННОЙ ЗАЩИТЫ РЕЗЕРВУАРОВ ОТ ВНУТРЕННЕЙ КОРРОЗИИ
1.Антикоррозионная защита резервуаров
Впроцессе эксплуатации резервуары подвергаются коррозии как с наружной, так и с внутренней стороны. Снаружи резервуары корродируют под действием атмосферной влаги и содержащихся в воздухе частиц агрессивных веществ. Внутри резервуаров коррозия зависит в основном от частоты заполнения их нефтепродуктами, химического состава нефтепродуктов, наличия в топливе воды. Скорость и характер коррозионного процесса наиболее ярко выражены на внутренней поверхности резервуаров в местах раздела двух сред; например, нефтепродукт — подтоварная вода, нефтепродукт — паровоздушная смесь. На интенсивность коррозии оказывают влияние влага и температура окружающей среды, а также стойкость стали, из которой изготовлен резервуар, против коррозии.
Состояние антикоррозионной защиты наружной поверхности наземных резервуаров периодически контролируют.
Впроцессе контроля проверяют наличие дефектов в наружном слое защитного покрытия, сплошность антикоррозионных покрытий по всей наружной поверхности, степень адгезии защитного покрытия к металлической поверхности резервуара. Работы по защите от коррозии наружной поверхности наземных резервуаров необходимо проводить согласно РД 112-РСФСР-015-89.
3
Консорциум « Н е д р а »
Способы защиты резервуаров от коррозии
Способы защиты подземных резервуаров от коррозии подразделяются на способ защиты от почвенной коррозии (электрохимической) и способ защиты от коррозии блуждающими токами. От почвенной коррозии и коррозии блуждающими токами используют катодную, протекторную и дренажную защиты.
Наружные поверхности резервуаров эффективно могут быть защищены нанесением на предварительно подготовленную поверхность изоляционных антикоррозионных покрытий в виде полимерных лент, битумно резиновых или битумно полимерных мастик.
От почвенной коррозии днища резервуаров защищают гидроизоляционным слоем, а также используют протекторную защиту, когда к днищу резервуара электрически присоединяют алюминиево-магниевые протекторы, находящиеся на глубине 1,5 м вокруг резервуара. Кроме этого, днища резервуаров эффективно защищают, применяя катодную защиту.
Антикоррозионную защиту наружной поверхности подземных резервуаров осуществляют согласно ГОСТ 9.602 и
ГОСТ 25812.
При выполнении работ по защите подземных и наземных резервуаров стационарных, передвижных и контейнерных АЗС от коррозии следует руководствоваться СНиП 2.03.11 -85 и ГОСТ 1510.
2.Особенности коррозии резервуаров от нефти и нефтепродуктов
Вкачестве основного конструкционного материала для изготовления резервуаров используются углеродистые и низколегированные стали различных марок (ВСтЗпс, 09Г2С, 16Г2АФ, 18Г2АФпс, 12ХГ2СМФ и др.). Эти стали не обладают достаточно высокой коррозионной стойкостью к действию рабочих сред, находящихся внутри резервуаров. Типовой резервуар имеет участки и узлы, коррозионное разрушение которых может наступить в первые годы эксплуатации. На ремонты резервуаров расходуется до 60...80 % капитальных затрат.
4
Консорциум « Н е д р а »
Сложность процесса коррозионного разрушения внутренней поверхности резервуаров заключается в том, что физикохимические характеристики сред изменяются по высоте резервуара в результате чередования технологических операций (наполнение - отстой - опорожнение). Коррозионная активность нефти и нефтепродуктов обусловливается наличием в них воды, кислорода и кислородсодержащих веществ, солей, сернистых соединений.
Материальный ущерб, наносимый коррозией резервуарному парку страны, достигает огромных размеров. Но гораздо больший ущерб происходит в результате засорения топлив и масел продуктами коррозии. Очистить полностью топлива и масла от ржавчины перед их применением в двигателях внутреннего сгорания существующими методами фильтрации и отстоя практически невозможно.
Ржавчина вызывает усиленный износ двигателей и агрегатов топливных систем, что увеличивает расход топлив и масел, засоряет топливную аппаратуру и может вызвать аварии и даже катастрофы эксплуатируемой техники, особенно в авиации.
Обеспечить необходимую чистоту топлив и масел при хранении можно только при условии изоляции этих нефтепродуктов от стальной поверхности резервуара и снижения коррозии металла применением других противокоррозионных мероприятий.
Использование резервуаров без внутренней противокоррозионной защиты в 3...4 раза уменьшает срок их службы, приводит к излишнему расходу металла и удорожанию стоимости резервуаров, в 2...3 раза уменьшает срок службы двигателей внутреннего сгорания и реактивных двигателей.
Как показывает практика эксплуатации резервуаров и емкостей с внутренней противокоррозионной защитой, затраты на нее окупаются в течение 4-5 лет за счет уменьшения амортизационных расходов.
Резервуары подвержены наружной (атмосферной, почвенной) и внутренней коррозии, протекающей, в основном, по электрохимическому механизму. Замечено, что резервуары интенсивнее корродируют в промышленно развитых регионах, а также вблизи морского побережья, что связано с более коррозионно-активным составом атмосферы.
5
Консорциум « Н е д р а »
Атмосферной коррозии подвержена наружная поверхность кровли и обечайки. Разрушению в результате почвенной коррозии подвергается наружная поверхность днища. Механизм коррозии в данном случае тот же, что и трубопроводов.
По характеру коррозионных повреждений внутренней поверхности и степени воздействия коррозионноактивных компонентов нефтепродуктов резервуар разделяют на следующие характерные зоны:
внутренняя поверхность кровли и верхняя часть корпуса, находящаяся в контакте с паровоздушной
• |
часть корпуса, находящаяся в области попеременного смачивания (зона ватерлинии); |
• |
часть корпуса, находящаяся в области постоянного смачивания нефтью (нефтепродуктами); |
днище и нижний (первый) пояс, находящиеся в контакте с подтоварной водой.
Скорость коррозионного разрушения кровли определяется составом подсасываемого в резервуары воздуха и его влажностью. При уменьшении температуры кровли и обечайки резервуара (например, ночью) на их внутренней поверхности, контактирующей с газовым пространством, происходят обильная конденсация паров воды и насыщение образовавшегося конденсата кислородом. В условиях наличия электролита (вода) и активного деполяризатора (кислород) происходит электрохимическое разрушение металла.
Вобласти попеременного смачивания коррозия протекает достаточно интенсивно. Здесь не только присутствуют необходимые для этого компоненты (вода, кислород), но также сказывается эффект дифференциальной аэрации.
Врезультате образуется гальванический элемент, в котором анодом является несмоченная поверхность, а катодом
—смоченная, разделенные ватерлинией.
Вобласти постоянного смачивания нефтью (нефтепродуктами) также происходит коррозионное разрушение металла. При повышении температуры обечайки пристенные слои нефти (нефтепродукта) также нагреваются и из
них выделяется растворенный кислород. Одновременно с этим нагретая нефть (нефтепродукт) поднимается вверх,
6
Консорциум « Н е д р а »
увлекая за собой подтоварную воду. В результате слои нефти (нефтепродукта), примыкающие к обечайке, обогащаются не только кислородом, но и водой, что создает благоприятные условия для коррозии металла.
Ночью, при охлаждении слоев продукта, прилегающих к стенке, конвективные токи направлены вниз. При этом нефть (нефтепродукт) захватывает кислород из газового пространства и капельки воды, осаждающиеся на холодной стенке из паровоздушной смеси, что также способствует коррозии обечайки резервуаров. Более высокая скорость коррозии смоченной поверхности резервуаров с бензином (до 0,5 мм/год), чем резервуаров с дизельным топливом (до 0,25 мм/год) или мазутом (не более 0,025 мм/год) объясняется тем, что в углеводородах с меньшей плотностью растворимость кислорода больше.
Аналогичная связь между скоростью коррозии резервуаров и плотностью жидкости наблюдается у нефтяных резервуаров.
Коррозия днища и нижнего (первого) пояса резервуара происходит от контакта с подтоварной водой. В резервуаре для нефти и нефтепродуктов подтоварная вода содержит соли и кислоты. Наиболее интенсивно разрушается днище в области приемо-раздаточного патрубка, где на процесс электрохимической коррозии накладывается механическое разрушение металла твердыми частицами перемещающимися с трением по днищу во время операций приемаотпуска (коррозионная эрозия).
Из сказанного можно сделать вывод, что коррозия резервуаров – процесс неизбежный. Однако человек, вооруженный знанием механизма коррозии, может затормозить его таким образом, чтобы обеспечить сохранение работоспособности этих сооружений в течение длительного времени.
7
Консорциум « Н е д р а »
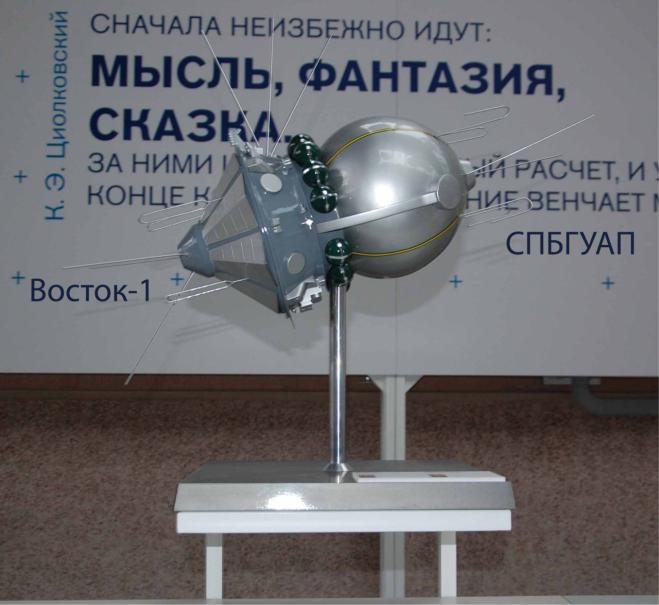
Макет космического корабля «Восток-1» в павильоне «Космос» на ВДНХ. За ним — цитата К. Э. Циолковского:
«Сначала неизбежно идут: мысль, фантазия, сказка. За ними шествует научный расчёт. И уже в конце концов исполнение венчает мысль»
3.Противокоррозионная защита резервуаров
Защиту резервуаров от коррозии также осуществляют пассивными и активными методами. К пассивным методам относится применение защитных покрытий всех видов, которые изолируют агрессивную среду от поверхности резервуара, и ингибиторов коррозии. В качестве активной защиты используют катодную поляризацию и протекторы.
3.1Пассивные методы защиты резервуаров от коррозии
Для предотвращения контакта наружной поверхности днища резервуара с почвенной влагой под ним устраивают гидрофобизированное основание. Чаще всего для этих целей используют пески, смешанные в соотношении 9:1 с одним из вяжущих: мазут, нефть, жидкие нефтяные битумы, дегти и т.п. Толщина гидрофобизированного основания составляет 0,1-0,3 м.
Защиту от наружной коррозии производят лакокрасочными материалами (краски и эмали) светлых тонов для снижения температурных влияний на потери нефтепродуктов от испарения при «малых дыханиях».
Пассивную защиту внутренней поверхности резервуара осуществляют с помощью покрытий на основе
лакокрасочных и полимерных материалов, цинка и др.
Лакокрасочными называют вещества жидкой консистенции, способные после нанесения их тонким слоем на поверхность отверждаться (высыхать) с образованием пленки (лакокрасочного покрытия). Для покрытия резервуаров наибольшее применение получили эпоксидные лакокрасочные материалы, отличающиеся сравнительно простой технологией нанесения и позволяющие получать стойкие качественные покрытия.
Перед нанесением покрытий поверхность резервуаров подвергается дробеструйной, пескоструйной обработке или обрабатывается специальными преобразователями ржавчины для придания шероховатости и обеспечения хорошей адгезии.
8
Консорциум « Н е д р а »