
Tekhnologiya_sborki_integralnyh_skhem
.pdf
шат, а затем пленку разрезают на ленты определенной ширины. Лента выпускается шириной одного-двух стандартных форматов (обычно 8 и 16 мм). В ленте с помощью автоматического пуансона вырубают краевую перфорацию и отверстия, куда на последующих операциях помещаются кристаллы. При этом строго соблюдаются размеры перфораций. Затем на ленту с краевой перфорацией наклеивается медная или алюминиевая фольга. Для этого ленту и медную (алюминиевую) фольгу подают с двух различных катушек в автоматический пресс, где их подвергают кратковременному нагреву при механическом давлении
(1,5–2,0) 105 Па. После охлаждения при температуре окружающей среды обратную сторону ленточного носителя покрывают лаком и сматывают на катушку. Медная или алюминиевая фольга протравливается фотолиграфическим методом до получения тонких паукообразных выводов, которые нависают над центральным вырезом, т. е. получаются определенной формы балочные выводы. После травления медной фольги электрохимическим осаждением на нее наносится припойное покрытие на основе сплава олово-висмут. Для изготовления ленточных носителей обычно используются полиимидные пленки, марка которыхопределяется типом адгезива и термостойкостью пленки.
На рис. 5.8 приведена схема изготовления ленточного носителя на основе полиимидной пленки.
а |
|
б |
|
в |
г д
Рис. 5.8. Схема изготовления ленты-носителя на основе полиамидной пленки:
а– Cu-пленка; б – полиамид; в – перфорация и прошивка отверстий под кристаллы
вполиамиде; г – полиамидная лента с наклеенной Cu-фольгой; д – лента-носитель после травления Cu-фольги со сформированными паучковыми выводами
На механические качества паучковых выводов большое влияние оказывают класс обработки, ровность (плоскостность), толщинаи микроструктура фольги, а также адгезия фольги к полиимидной пленке.
120

Паучковые выводы закреплены на гибкой диэлектрической пленке и не соединены друг с другом, вследствие чего возможно измерять электрические параметры микросхем после присоединения кристаллов. Выводы кристаллов присоединяют к паучковым выводам микропайкой или ультразвуковой сваркой в зависимости от используемых материалов.
При микропайке с импульсным нагревом (рис. 5.9) паучковые выводы 2, закрепленные на диэлектрической пленке 3, совмещаются со столбиковыми выводами 4 на кристалле 5. Головка 1 опускается, прижимая паучковые выводы к столбиковым контактам. Через нее пропускается импульс тока, и места контакта нагреваются до температуры пайки. Слой клеящего вещества 6, удерживающий кристалл на подложке 7 в ориентированном положении, расплавляется, и при поднятии инструмента кристалл, припаянный к паучковым выводам, отрывается от подложки под действием силы, вызванной упругой предварительной деформацией паучковых выводов. Силы сцепления кристалла с клеящим веществом и подложкой должны быть меньше этой силы.
Рис. 5.9. Схема микропайки паучковых выводов
скосвенным импульсным нагревом инструмента:
1– нструмент; 2 – паучковый вывод; 3 – диэлектрическая пленка; 4 – контакт на кристалле; 5 – кристалл; 6 – слой клеящего вещества; 7 – подложка
При микропайке с общим нагревом (рис. 5.10) после совмещения паучковых выводов 1 с шариковыми контактами 5 кристалла 4 вакуумный присос 3 перемещается вверх, деформируя выводы на некоторую величину L. В результате упругой деформации выводов возникающая сила стремится их прижать к шариковым контактам
121

на кристалле. Включается нагревательный элемент 2, в местах соприкосновения выводов достигается температура плавления припоя (шариковые выводы кристалла покрыты легкоплавким припоем). После остывания в местах контакта образуется спай. Алюминиевые паучки присоединяются к алюминиевым контактным площадкам кристалла с помощью ультразвуковой сварки. Применение ультразвука исключает нагрев кристаллов микросхем при сварке, который может приводить к выходу их из строя. Внешне микросхемы с такими выводами подобны пауку, причем радиальное расположение выводов соответствует на одной стороне контактным площадкам на кристалле, а на другой – выводам внешней платы или корпуса.
L
Рис. 5.10. Микропайка с общим нагревом:
1 – паучковые выводы; 2 – нагреватель элементов; 3 – вакуумный присос; 4 – кристалл; 5 – шариковый контакт
5.6. Присоединение выводов с помощью ультразвуковой микросварки
УЗС – это метод соединения металлов в твердом состоянии, отличающийся от других видов сварки способом введения энергии в зону сварки. Сближение свариваемых материалов (проволока с контактной площадкой) и образование соединения происходит при пластической деформации материалов от совместного воздействия усилия напряжения и тепловой энергии за счет процессов трения и воздействия на материалы УЗ-полем частотой 66±10 % кГц для микросварки. Метод является базовым при выполнении технологических операций сборки полупроводниковых приборов алюминиевой проволокой. Основными достоинствами метода УЗС-выводов являются: возможность соединения широкой номенклатуры материалов; получение
122
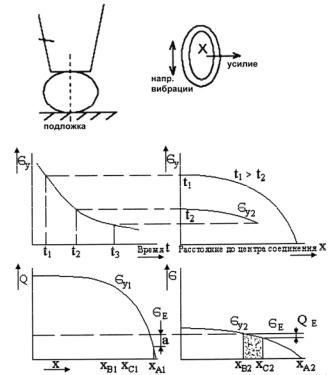
соединений материалов с окисленными поверхностями; высокая механическая прочность соединений. Для образования соединения важны процессы, происходящие в зоне контактирования соединяемых материалов. Процесс протекает наиболее эффективно в случае хорошего сцепления между сварочным инструментом и проводником. На рис. 5.11, а показано поперечное сечение проводника во время соединения с помощью инструмента типа клин.
аб
вг
де
Рис. 5.11. Процесс УЗ-сварки:
а– поперечное сечение при соединении клином; б – напряжение вибраций;
в– зависимость нормального напряжения в центре проволоки от времени сварки;
г– зависимость нормального напряжениявмоментвремениигоризонтального напряжения, введенногопульсацией, определяющих зону соединения;
д– зависимость распределения вертикального напряжения для двух значений времени сварки и расстояния до центра соединения;
е– те же взаимосвязи, но для позднего момента времени
123
В то время как проволока находится под нагрузкой, механическое перемещение или вибрация инструмента для УЗС вызывает скачок уплотнения на алюминиевой контактной площадке (рис. 5.11, б). Распространение волнового фронта по проволоке обусловливает образование волнистой структуры посредством воздействия напряжения сдвига на алюминиевой контактной площадке перпендикулярно к направлению вибраций. До или во время движения волнового фронта УЗ-энергия поглощается проволокой, при этом она размягчается и под действием нагрузки течет, разрывая поверхностный оксид
иоставляя незащищенной чистую поверхность проволоки и контактной площадки. Эти чистые незащищенные поверхности металлов быстро свариваются. Соединение образуется в тороидальной области вокруг центра контактной площадки и проволоки. На рис. 5.11, в, г показана модель, поясняющая механизм соединения. Поскольку проволока размягчается и деформируется, вертикальное напряжение уменьшается во времени. Вибрирующее воздействие инструмента для УЗС вызывает появление горизонтального напряжения.
При среднем вертикальном напряжении происходит соединение,
исвариваемая область растет с увеличением времени, так как вертикальное напряжение уменьшается (рис. 5.11, е). Увеличение сцепления инструмента с проводником можно добиться за счет состояния (формы) поверхности инструмента, либо за счет увеличения контактного усилия. Однако оно ограничивается узкой зоной пластичности
иповышенной склонностью к образованию внутренних напряжений
итрещин в полупроводниковых материалах и диэлектрических подложках. Необходимые условия сцепления обеспечиваются соответствующей шероховатостью рабочего торца инструмента и созданием специального профиля (продольная или поперечная канавка или продольное углубление, рис. 5.12).
Впервый момент контактного взаимодействия проволоки с инструментом формируется контакт, обеспечивающий хорошую передачу колебаний, и исключаются условия смещения проволоки. Создано несколько способов УЗС: с модуляцией частоты генератора, автоматическим поиском частоты преобразователя с последующей фиксацией частоты генератора и автоподстройкой частоты. Эти способы обеспечивают воспроизводимость параметров и с успехом используются. Наиболее перспективной считается создание адаптирующих систем для микросварки, позволяющих в условиях массового производства
124

получать достаточно высокие механические свойства свариваемых соединений. Более точный контроль за качеством соединений имеют системы, в которых управление сваркой ведется в зависимости от изменения амплитуды колебаний инструмента, тока или напряжения в электрической цепи преобразователя. Повышение точности обусловлено тем, что изменение указанных параметров вызвано увеличением тормозящей силы в процессе образования соединений, величина которой зависит от свойства контакта инструмент–проволока. Изменение этих свойств вносит неопределенность в передачу ультразвуковых колебаний в зону сварки, что существенно влияет на длительность каждой из трех стадий формирования соединений от сварки к сварке. Поэтому предусматривается разработка систем управления параметрами процесса УЗС с учетом кинетики образования соединений, обеспечивающих условия формирования высокопрочных соединений и контроль их качества непосредственно в процессе сварки.
а |
|
|
|
в |
|
б |
|||
|
|
|
|
|
Рис. 5.12. Конструкция сварного инструмента для УЗС:
а– с продольной канавкой; б – с продольным углублением;
в– профиль инструмента
Параметры УЗС определяются свойствами свариваемых материалов и поверхностных пленок. Основными параметрами являются величина амплитуды колебаний сжимаемого усилия и время, взаимосвязанное при сварке. От качества свариваемых поверхностей зависят условия протекания процесса сварки. Соединения одинаковой прочности могут быть получены в различных сочетаниях основных факторов, но время образования сварочного соединения (стадия формирования зон схватывания) для конкретных материалов и качества подготовки их поверхностей являются величиной, не зависящей от выбора режима. Для каждой пары свариваемых материалов время, в течение кото-
125
рого скорость осадки постоянна, является характерной величиной. Если сварочный режим обеспечивает малое время протекания осадка, то соединение образуется лишь на части площади контакта и прочность сварки мала. При завышенных режимах, когда постоянная скорость осадки высока, контактное соединение получается некачественным либо из-за высокой осадки, либо из-за разрушения под воздействием колебаний образовавшегося контактного соединения. Следовательно, между кинетикой образования соединения и параметрами процесса существует сложная взаимосвязь, которая определяет качество сварки. Например, алюминиевую проволоку легируют кремнием (1 %) для увеличения твердости и жесткости. Необходимо соблюдать требования к состоянию поверхности, на которой бы отсутствовали механические повреждения и загрязнения. Поверхности контактных площадок должны быть одинаковой толщины. Оптимальных результатов при УЗС можно достичь, подбирая значения параметров так, чтобы обеспечить максимальную воспроизводимость качества соединения в сочетании с высокой прочностью соединений (наотрыв). Для обычных при сборке микросхем параметров проводников в пределах 25–50 мкм параметры процесса сварки варьируются из следующих основных составляющих: частота сварочных импульсов – от 60 до 72 кГц и выходная мощность УЗ частоты от 0,63 до 6,3 Вт; усилие сжатия присоединяемых элементов от 0,1–1,2 Н; время присоединения 0,01–0,2 с. При применении ультразвуковой сварки существует угроза поглощения УЗэнергии, передаваемой инструментом к выводам корпуса. Это происходит, когда вывод имеет большую свободную длину – вылет и может наблюдаться отслаивание сварных соединений или образование низкопрочных соединений. Причиной является уменьшение резонансной частоты вывода с увеличением его длины, приводящее к резонансному возбуждению вывода. Такие колебания частично или полностью расходуют ультразвуковую энергию. Круглый вывод диаметром – 0,5 мм и длиной – 1,5 мм, применяемый в корпусах ГИС, имеет резонансную частоту – 60 кГц и практически полностью гасит проводимую УЗэнергию. Для приведенного типа надежная сварка возможна при длине вывода менее 1 мм, т. е. прочность сварки приближенно прямопропорциональна длине вывода. Плоские горизонтальные выводы корпуса также могут поглощать УЗ-энергию, но для них проблема сварки решается выбором места сварки ближе к месту крепления вывода. При необходимости использования более длинных выводов рекомендуется
126
точное определение момента касания проволоки с выводом корпуса с помощью контактных или бесконтактных датчиков и создание вибрации стола с корпусом в момент включения необходимой для сварки мощности УЗ-генератора. Эта вибрация компенсирует потерю энергии на возбуждение вывода. При этом программируется величина перемещения стола и количество циклов сканирования. Причинами отказов при УЗС часто являются плохое закрепление корпуса прибора, инструмента в держателе, неправильно выбранная конструкция корпуса и длина инструмента. Повреждение полупроводникового материала под контактной площадкой является результатом использованияслишком твердой проволоки, чрезмерно длительной сварки или недостаточной нагрузки на инструмент. Нагрузка на инструмент не должна вызвать перемещения проволоки в процессе сварки. Конкретное значение усилия нагружения зависит от размера и конструкции сварочного инструмента, материала сечения, твердости присоединяемого проводника и металлизации подложки, кристалла. Недостаточная нагрузка на инструмент может привести к повреждению материала полупроводника под контактной площадкой вследствие вибрации инструмента, а слишком большая нагрузка – к разрушению соединения. Область оптимальных усилий нагружения определяют испытаниями на отрыв, сохраняя постоянными время и мощность УЗ-колебаний. Полученные оптимальные значения усилия сжатия перепроверяются после нахожденияобласти оптимальных значениймощности ивремени (рис. 5.13).
Рис. 5.13. Зависимость прочности соединения от ширины сварного соединения
127
Обычно предпочтение отдается более высокой мощности при минимальном времени сварки. Оптимальное значение определяется также испытаниями на отрыв. Зная оптимальную величину нагружения
ивремени присоединения, находят близкое к оптимальному значение мощности. Испытанием нескольких соединений на отрыв, выполненным на разных значениях УЗ-мощности, находят ее оптимальное значение. Качественное присоединение проволочных выводов обеспечивается конструкцией инструмента. Наиболее надежен инструмент с вогнутой рабочей поверхностью и продольной канавкой (рис. 5.12). Для варианта 5.12, а отполированные передний и задний радиусы создают плавный переход проводника в соединение, а матовая (неотполированная) рабочая площадка инструмента обеспечивает минимум перемещений на границе инструмент–проводник. Вогнутая с малой кривизной поверхность рабочего торца создает небольшую деформацию и высокую прочность соединения на отрыв.
Для присоединения проводников различного диаметра используются сварочные инструменты с разными размерами рабочей площадки. При больших размерах контактной площадки и кристалла
иправильной топологии рекомендуемая величина рабочей площади инструмента должна составлять 2,5–3,0 диаметра проводника. Чем она больше, тем менее критичным будет режим сварки, т. е. возрастет выход годных изделий.
Типичный инструмент для УЗС имеет (рис. 5.12) передний ра-
диус r, рабочую площадку b и задний радиус r1. Рабочая площадка плоская либо слегка вогнутая, либо имеет продольную канавку. Глубина вогнутости должна составлять 20–30 % диаметра проводника. Передний радиус формирует плавный переход проводника в соединение первой сварки и выполняет отделение проволоки после второй сварки. Задний радиус составляет 40–100 % диаметра проводника в зависимости от рабочей площадки инструмента. Задний радиус обычно меньше, чем передний. В процессе сварки происходят перемещения в основном на границе проводник – подложка. Инструмент с отполированной рабочей площадкой после нескольких сотен сварок прирабатывается и выполняет качественные соединения. Передний
изадний радиусы инструмента полируются. Канавки на инструменте выполняются на его рабочей поверхности, чтобы улучшить сцепление с проводником. Инструмент с поперечными канавками рекомендуется в случае соединения трудносвариваемых материалов. Проч-
128
ность соединения, выполняемого с помощью вогнутого инструмента выше, чем соединения, выполненного инструментом с плоским торцом. При сварке инструментом с вогнутой поверхностью присоединение в центре происходит на большей поверхности, чем при сварке инструментом с плоским торцом. Инструмент периодически очищается, для проволоки диаметром 15–35 мкм не реже чем через 50 тысяч сварок, а для более толстых – ежедневно. Качество очистки и износ инструмента проверяются визуально под микроскопом. Присоединение толстой проволоки имеет ряд особенностей, связанных с затруднениями при ее подаче в процессе образования петли: чрезмерная деформация соединения, повреждения при изгибах для формирования петли, появление царапин. Для отделения толстой проволоки после второй сварки пользуются одним из двух методов. Первый состоит в натяжении проволоки и отрыве ее, как и для проволоки, диаметром 25–35 мкм. В этом случае применяют инструмент с вогнутой рабочей поверхностью. Другой метод заключается в отрезании проволоки ножом. Применяют инструмент с продольной канавкой. Первую сварку при УЗС выполняют на кристалле, так как это исключает замыкание краем кристалла (рис. 5.14, а). Однако при монтаже в корпус с углублением трудно обеспечить первую сварку на кристалле, а вторую на выводе с помощью стандартного инстру-
мента с углом подачи проволоки 30 . Для преодоления этой трудности используют обратный метод формирования перемычки. Сварка выполняется с выводом корпуса на кристалле (рис. 5.14, б).
а |
б |
Рис. 5.14. Прямой (а) и обратный (б) методы формирования проволочной перемычки при УЗС
129