
основы процесса каталитического риформинга
.pdfтехнология вторичных процессов переработки нефти
основы процесса каталитического риформинга
ВВЕДЕНИЕ Ароматические углеводороды являются одним из основных видов сырья для тяжелого органического синтеза и нефтехимии.
Наибольшее применение получили низшие ароматические углеводороды — бензол, толуол и ксилолы. На их основе получают пластмассы,
пластификаторы, синтетические смолы и волокна, красители, ПАВ, антиокислители, пестициды, медикаменты и др. [1]. В последние годы наблюдается стремительный рост спроса на ароматические углеводороды как на мировом рынке, так и на рынке отечественной нефтехимии в связи с динамичным развитием рынка конечных продуктов [2]. В настоящее время промышленное производство ароматических углеводородов в основном базируется на гидропереработке жидких продуктов пиролиза и каталитическом риформинге бензиновых фракций
[3, 4].
Процесс каталитического риформинга для большинства нефтеперерабатывающих заводов России — базовый процесс производства высокооктановых компонентов автомобильных бензинов и ароматических углеводородов. На некоторых НПЗ мощности по риформированию достигают 17 – 24% от мощности первичной переработки. В среднем по России это значение составляет около 11%.
Поскольку процесс каталитического риформинга обеспечивает низкую себестоимость продукта и занимает центральное место при производстве ароматических углеводородов и автомобильных бензинов, постоянно совершенствуется его технология, осуществляется поиск способов интенсификации уже действующих производственных установок. Основным направлением в развитии технологии каталитического риформинга является увеличение производительности установок и жесткости процесса с целью повышения выхода риформата и водорода, однако при этом падает стабильность процесса.
консорциум « Н е д р а»
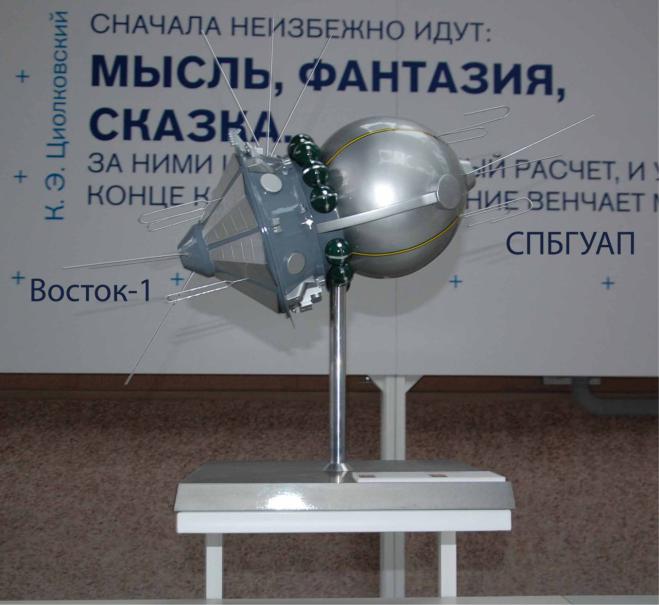
Макет космического корабля «Восток-1» в павильоне «Космос» на ВДНХ. За ним — цитата К. Э. Циолковского:
«Сначала неизбежно идут: мысль, фантазия, сказка. За ними шествует научный расчёт. И уже в конце концов исполнение венчает мысль»
2
1 Теоретические основы процесса каталитического риформинга бензиновых фракций
1.1 Назначение, сырье и продукты процесса
Процесс каталитического риформинга бензиновых фракций является одним из важнейших процессов современной нефтеперерабатывающей и нефтехимической промышленности.
Процесс предназначен для производства высокооктановых компонентов автомобильных бензинов и легких ароматических углеводородов — бензола, толуола и ксилолов. Весьма важным продуктом процесса каталитического риформинга является водородсодержащий газ с высоким содержанием водорода, который используется для гидроочистки широкого ассортимента нефтяных фракций, для процесса гидрокрекинга тяжелых нефтяных фракций и других гидрогенизационных процессов [5].
Бензиновые фракции большинства нефтей содержат 60 – 70 % парафиновых, 10% ароматических и 20 – 30 % пяти- и шестичленных нафтеновых углеводородов. Среди парафиновых преобладают углеводороды нормального строения и монометилзамещен-ные их изомеры.
Нафтены представлены преимущественно алкилгомологами циклогексана и циклопентана, а ароматические – алкилбензолами. Такой состав обуславливает низкое октановое число прямогонного бензина, обычно не превышающего 50 пунктов (по ММ).
Помимо прямогонных бензинов, как сырье каталитического риформинга используют бензины вторичных процессов – коксования и термического крекинга после их глубокого гидрооблагораживания, а также гидрокрекинга.
Существует два варианта каталитического риформинга: для получения высокооктанового бензина (КРб) и для получения ароматических углеводородов (КРа). Для этих двух вариантов исходный бензин н.к. – 180 °C разделяется на более узкие фракции (рис. 1).
Сырье каталитического риформинга для получения высокооктанового компонента бензинов (КРб) — это обычно фракция 85 – 180°C.
Легкая фракция н.к. – 85°C для процесса нежелательна, так как в ней мало углеводородов C6, и она дает большой выход газа C1 – C4, фракция же с температурой кипения выше 180°C дает большой процент накопления кокса на катализаторе [6].
Сырьем для каталитического риформинга с целью получения индивидуальных ароматических углеводородов (КРа) являются узкие фракции, содержащие углеводороды C6 (62 – 85°C), C7 (85 – 105°C) и C8 (105 – 140°C).
консорциум « Н е д р а»
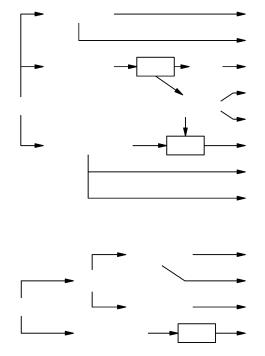
н.к. − 62. C
62 −140. C
н.к. −180. C
140 −180. C
КРа |
АрУ |
Рафинат |
|
|
КРб |
3
Получение петролейного эфира Изомеризация (компонент автобензина)
На нефтехимический синтез Растворители Компонент бензинов
Высокооктановый компонент бензинов Компонент дизельных топлив «З» и «А» На пиролиз
а
н.к. −180. C
н.к. − 62. C |
|
н.к. −85. C |
|
62 −85. C |
|
85 −180. C |
КРб |
Получение петролейного эфира Изомеризация (компонент автобензина)
Растворитель или на пиролиз Компонент автобензина
б
Рис. 1. Варианты каталитического риформинга: а – производство ароматических углеводородов;
б – производство высокооктанового компонента бензина
Предпочтительный групповой состав исходного бензина — преобладание парафино-нафтеновых углеводородов.
Процесс каталитического риформинга предъявляет высокие требования к качеству исходного сырья, в частности по содержанию в нем серы, азота и воды:
консорциум « Н е д р а»

4
−содержание серы в сырье допускается не более 1 ∙ 10– 4% масс., поэтому в составе установок риформинга всегда есть блок гидроочистки сырья;
−содержание азота допускается не более 0,5 ∙ 10 – 4% масс., т.к. азот (особенно азотистые основания) является ядом для катализаторов, разрушающим их кислотные центры;
−содержание воды в сырье ограничивается величиной не более 1,5 ∙ 10– 4% масс., поскольку влага вымывает галоген, которым обрабатывается катализатор [7].
1.2Химические основы процесса
Каталитический риформинг - сложный химический процесс, включающий в себя разнообразные реакции, в результате которых происходит глубокое изменение углеводородного состава бензиновых фракций с преимущественным образованием и накоплением ароматических углеводородов [8 – 10].
Основные реакции процесса, приводящие к образованию ароматических углеводородов:
− дегидрирование циклогексана и его гомологов:
+ 3H2 ;
− дегидроизомеризация гомологов циклопентана:
+ 3H2 ;
консорциум « Н е д р а»
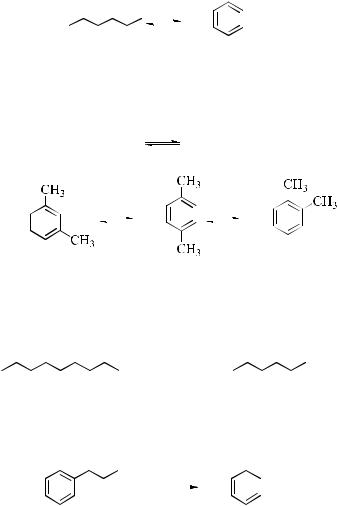
5
− дегидроциклизация (ароматизация) парафинов:
+ |
4H |
|
2 |
. |
|
Изомеризация углеводородов — другой тип реакций, характерных для каталитического риформинга. Наряду с изомеризацией пятичленных и шестичленных нафтенов изомеризации подвергаются как парафины, так и ароматические углеводороды:
н - C |
H |
14 |
6 |
|
изо - C |
H |
14 |
; |
6 |
|
|
.
Существенную роль в процессе также играют реакции гидрокрекинга. Гидрокрекинг парафинов, содержащихся в бензиновых фракциях, сопровождается газообразованием, что ухудшает селективность процесса:
+ |
H |
|
2
+ |
C |
|
3 |
H |
. |
8 |
|
С другой стороны, аналогичные реакции деалкилирования алкилбензолов позволяют увеличить выход низкомолекулярных ароматических углеводородов, представляющих наибольший практический интерес:
+ |
H |
|
2
+ C3H8 .
консорциум « Н е д р а»
6
Наиболее важные реакции риформинга, ведущие к образованию ароматических углеводородов из нафтенов и парафинов, идут с поглощением тепла, реакции изомеризации нафтенов и парафинов имеют тепловой эффект, близкий к нулю, а реакции гидрокрекинга экзотермичны.
В условиях каталитического риформинга наиболее легко и быстро протекают реакции дегидрирования гомологов циклогексана.
Относительно этой реакции скорость ароматизации из пятичленных нафтенов примерно на порядок ниже. Наиболее медленной из реакций ароматизации является дегидроциклизация парафинов, скорость которой (на два порядка ниже) лимитируется наиболее медленной стадией циклизации.
Превращения нафтеновых и парафиновых углеводородов в ароматические – обратимые реакции, протекающие с увеличением объема и поглощением тепла. Следовательно, по принципу Ле-Шателье, равновесная глубина ароматизации увеличивается с ростом температуры и понижением парциального давления водорода. Однако промышленные процессы риформинга вынужденно осуществляют либо при повышенных давлениях с целью подавления реакций коксообразования, при этом снижение равновесной глубины ароматизации компенсируют повышением температуры, или с непрерывной регенерацией катализатора при пониженных давлениях [32].
В условиях риформинга протекают также реакции, практически не влияющие на выход основных продуктов реакции, но оказывающие существенное влияние на активность и стабильность катализатора. К ним относятся реакции распада сернистых, азотистых и хлорорганических соединений, а также реакции уплотнения (полимеризации и конденсации), приводящие к образованию кокса на катализаторе и, следовательно, его дезактивации.
1.3 Основные параметры и их влияние на процесс
Основными параметрами процесса, влияющими не только на выход и состав продуктов каталитического риформинга, но и на скорость дезактивации катализатора, которая, в свою очередь, зависит от скорости его закоксовывания, являются качество сырья
консорциум « Н е д р а»
7
риформинга, температура, давление, кратность циркуляции водородсодержащего газа, объемная скорость подачи сырья и содержание хлора
на катализаторе [8–10].
Качество сырья риформинга
Качество сырья риформинга определяется фракционным и химическим составом бензина.
Фракционный состав сырья выбирается в зависимости от целевого назначения процесса. Если процесс проводится с целью получения индивидуальных ароматических углеводородов, то для получения бензола, толуола и ксилолов используются фракции, содержащие углеводороды С6 (62 – 85°С), С7 (85 – 105°С) и С8 (105 – 140°С). Если риформинг проводится с целью получения высокооктанового бензина,
то сырьем обычно служит фракция 85 – 180°С, соответствующая углеводородам С7 – С10.
С увеличением молекулярной массы фракции и ее температуры кипения выход риформата постепенно возрастает, что особенно заметно при жестких условиях процесса (495°С). Аналогичная зависимость от фракционного состава и молекулярной массы фракции наблюдается по выходу ароматических углеводородов и по октановому числу риформата.
Влияние температуры
Процесс каталитического риформинга проводят обычно в интервале температур на входе в реакторы 470 – 540°C. С повышением температуры в процессе каталитического риформинга при прочих равных условиях уменьшаются выход стабильного катализата и содержание водорода в циркулирующем газе; повышаются содержание ароматических углеводородов в катализате и его октановое число. С
повышением температуры усиливается и коксообразование на катализаторе, поэтому температуру процесса следует подбирать в сочетании с другими параметрами.
Влияние давления
консорциум « Н е д р а»
8
Давление - основной, наряду с температурой, параметр, оказывающий существенное влияние на выход и качество продуктов риформинга. С понижением рабочего давления возрастает как термодинамически, так и кинетически возможная глубина ароматизации сырья. Увеличиваются выход риформата и водорода, возрастает содержание ароматических углеводородов в катализате и его октановое число. Повышается селективность превращений парафиновых углеводородов, поскольку снижение давления благоприятствует протеканию реакций дегидроциклизации и дегидрирования и тормозит реакции гидрокрекинга.
Однако при снижении давления резко увеличивается скорость дезактивации катализатора за счет его закоксовывания, что сокращает межрегенерационные циклы работы установки.
Влияние кратности циркуляции водородсодержащего газа
Кратность циркуляции ВСГ определяется как отношения объема циркулирующего ВСГ, приведенного к нормальным условиям, к
объему сырья, проходящего через реакторы в единицу времени (м3/м3). Повышение кратности циркуляции ВСГ способствует снижению коксообразования на катализаторе, позволяет продлить срок его службы, увеличить межрегенерационный период работы установки. Однако увеличение кратности циркуляции ВСГ связано со значительными энергозатратами, ростом гидравлического сопротивления и объема аппаратов и трубопроводов. Выбор этого параметра производят с учетом стабильности катализатора, качества сырья и продуктов, жесткости процесса и заданной продолжительности межрегенерационного цикла.
Влияние объемной скорости подачи сырья
Объемная скорость подачи сырья влияет на процесс риформинга как параметр, обратный времени контакта сырья с катализатором.
Для оптимизации каталитического риформинга объемную скорость подачи сырья принимают равной 1,4 – 2,5 ч– 1 в зависимости от активности катализатора, а соотношение загрузки катализатора по ступеням риформинга с целью повышения селективности процесса устанавливают равным от 1:2:4 до 1:3:7 для трехреакторного блока, 1:1,5:2,5:5 — для четырехреакторного в зависимости от химического состава сырья, технологического режима и целевого назначения процесса.
Повышение объемной скорости подачи сырья приводит к увеличению выхода риформата, но с пониженным октановым числом и меньшим содержанием ароматических углеводородов; снижению выхода ВСГ с более высокой концентрацией водорода; повышению
консорциум « Н е д р а»
9
селективности процесса и удлинению продолжительности межрегенерационного цикла. С другой стороны, при снижении объемной скорости снижается производительность установок риформинга по сырью.
Влияние содержания хлора на катализаторе
Стабильная активность катализаторов риформинга, кислотным промотором которых является хлор, возможна только при его достаточном содержании на катализаторе и низкой влажности в реакционной системе. Хлорирование и дехлорирование носителя катализатора является равновесным процессом.
Увеличение содержания хлора на катализаторе выше оптимальных значений повышает активность катализатора, но при этом также значительно возрастают реакции гидрокрекинга, приводящие к уменьшению выхода риформата и водорода и увеличению скорости коксообразования. Также происходит снижение перепада температур в реакторах, в последнем реакторе возможен положительный перепад температуры. Содержание хлора на катализаторе регулируется количеством вводимого хлорорганического соединения (дихлорэтана или
1,1,1-трихлорэтана).
1.4 Разновидности технологических установок
Первая промышленная установка каталитического риформинга на алюмохромомолибденовом катализаторе (гидрориформинг,
проводимый под давлением водорода 4 – 4,5 МПа и температуре 540°С) была пущена в 1940 г. и получила широкое развитие на НПЗ США и Германии. Основным целевым назначением гидрориформинга являлось получение высокооктановых компонентов (с ОЧИМ 80 пунктов)
авто- и авиабензинов, а в годы II мировой войны – производство толуола – сырья для получения тринитротолуола.
В1949 г. была введена в эксплуатацию разработанная фирмой «UOP» первая промышленная установка каталитического риформинга
смонометаллическим алюмоплатиновым фторированным катализатором – платформинг.
консорциум « Н е д р а»