
Реферат Чижова АВ 2Д12
.pdf
МИНИСТЕРСТВО НАУКИ И ВЫСШЕГО ОБРАЗОВАНИЯ РОССИЙСКОЙ ФЕДЕРАЦИИ
Федеральноегосударственноеавтономноеобразовательноеучреждениевысшегообразования
«НАЦИОНАЛЬНЫЙИССЛЕДОВАТЕЛЬСКИЙТОМСКИЙПОЛИТЕХНИЧЕСКИЙУНИВЕРСИТЕТ»
Инженерная школа новых производственных технологий Научно-образовательный центр Н.М. Кижнера 18.03.01 «Химическая технология»
МАТЕМАТИЧЕСКАЯ МОДЕЛЬ КАТАЛИТИЧЕСКОЙ ДЕПАРАФИНИЗАЦИИ ДИЗЕЛЬНОГО ТОПЛИВА
РЕФЕРАТ
по дисциплине:
Моделирование химико-технологических процессов
Исполнитель: |
|
|
|
студент группы |
2Д12 |
Чижова Анастасия Васильевна |
26.05.2024 |
Руководитель: |
|
|
|
преподаватель |
|
Мойзес Ольга Ефимовна |
|
Томск – 2024
ОГЛАВЛЕНИЕ |
|
ВВЕДЕНИЕ ............................................................................................................. |
3 |
ТЕХНОЛОГИЧЕСКАЯ СХЕМА И УСТРОЙСТВО КАТАЛИТИЧЕСКОЙ |
|
ДЕПАРАФИНИЗАЦИИ ......................................................................................... |
4 |
МАТЕМАТИЧЕСКЯ МОДЕЛЬ ПРОЦЕССА КАТАЛИЧЕСКОЙ |
|
ДЕПАРАФИНИЗАЦИИ ......................................................................................... |
9 |
ЗАКЛЮЧЕНИЕ ..................................................................................................... |
13 |
СПИСОК ЛИТЕРАТУРЫ..................................................................................... |
14 |
2
ВВЕДЕНИЕ
В последнее время наблюдается тенденция истощения запасов легкоиз-
влекаемой нефти, в результате чего прирост нефтедобычи обеспечивается за счет тяжелой и трудно извлекаемой нефти [1]. Однако тяжелое нефтяное сы-
рье имеет ряд недостатков, затрудняющих переработку, а именно: высокая плотность и вязкость, высокое содержание смол и асфальтенов, парафинов,
серы и металлов (ванадия, никеля).
Для решения задач по переработке тяжелой нефти широкое примене-
ние находят гидрогенизационные процессы, одним из которых является ката-
литическая депарафинизация дизельного топлива. Процесс каталитической депарафинизации позволяет перерабатывать средние дистилляты в компо-
ненты низкозастывающих сортов дизельного топлива [2, 3].
Также одной из важных задач нефтеперерабатывающих процессов яв-
ляется подбор оптимальных технологических условий для увеличения вы-
хода целевых продуктов без потери качества и прогнозирование состава про-
дуктов в условиях нестацонарности протекания химических процессов. Для решения данной задачи широко применяют компьютерные моделирующие системы, разработанные на основании физико-химических свойств процесса.
Цель работы заключается в исследовании установки каталитической депарафинизации в ходе получения дизельного топлива зимнего различного класса с применением усовершенствованной математической модели про-
цесса каталитической депарафинизации и специализированной программы для расчета газожидкостного равновесия.
Объектом исследования является установка и математическая модель процесса каталитической депарафинизации дизельных фракций.
3
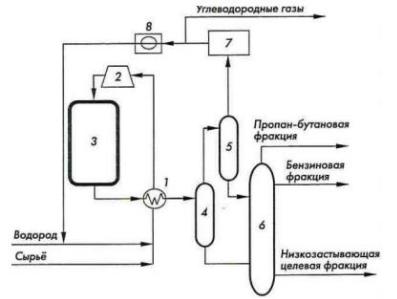
ТЕХНОЛОГИЧЕСКАЯ СХЕМА И УСТРОЙСТВА КАТАЛИТИЧЕСКОЙ ДЕПАРАИФНИАЦИИ
Современные процессы каталитической депарафинизации, как правило,
состоят из реакторного, ректификационного и очистного блоков. Типичная установка каталитической депарафинизации представлена на рисунке 1.
Рисунок 1 – Типичная установка каталитической депарафинизации [4]:
1 – теплообменник; 2 – печь; 3 – реакторный блок; 4 и 5 – сепараторы высокого и низкого давления соответственно; 6 – ректификационная колонна; 7 – блок очистки газов;
8 – компрессор.
Главное отличие современных установок заключается в устройстве и принципе работы реакторного блока. В реакторном блоке протекают про-
цессы гидроочистки и депарафинизации, с помощью которых получают ди-
зельное топливо с низкими низкотемпературными свойствами. В зависимо-
сти от содержания серы и азота в сырье каталитической депарафинизации
(для катализаторов депарафинизации на основных металлах) существуют различные комбинации расположения катализаторов гидроочистки и депара-
финизации по ходу сырья (рисунок 2) [5].
4
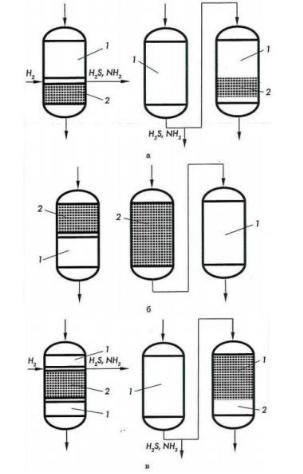
Рисунок 2 – Расположение катализаторов депарафинизации и гидроочистки в зависимости от содержания серы и азота в сырье депарафинизации:
1 – катализатор гидроочистки; 2 – катализатор депарафинизации:
а– среднее содержания серы (1,0 %); б – низкое содержание серы (0,5 %);
в– высокое содержание серы (1,5 %)
Для депарафинизации сырья с низким содержанием серы (или в про-
цессе депарафинизации без учета серы) в реакторном блоке используется только катализатор депарафинизации (только процесс депарафинизации).
Независимо от расположения катализаторов гидроочистки и депарафиниза-
ции, промежуточное очищение водорода от соединений серы и азота, значи-
тельно уменьшает ингибирующую активность сырья для обоих катализато-
ров [6].
Основное количество дизельного топлива в России посредством ката-
литической депарафинизации вырабатывается на семи заводах [4]:
5
1.НПЗ г. Ухта, установка ГДС-850.
2.ЗСК г. Сургут, установка ЛКС 35-64.
3.НПЗ г. Кириши, установка Л-24-10/2000.
4.НПЗ г. Ачинск, установка ЛК-6Ус.
5.НПЗ г. Комсомольск.
6.НПЗ г. Омск, установки Л-24-9х и Л-24-6.
7.НПЗ г. Ярославль, установка ЛЧ-24/7.
Процесс гидродепарафинизации и изодепарафинизации, как и любой каталитический процесс проводится в химическом реакторе. Задача любого реактора заключается в обеспечении тепло- и массообменных процессов.
В процессах депарафинизации в основном применяются реакторы вы-
теснения с аксиальным движением (вводом) сырья. Главное преимущество аксиальных реакторов перед другими это простота эксплуатации. Основными недостатками данного реактора являются [8]:
неравномерность работы катализатора в слое;
значительное повышение перепада давления на слое катализатора
впроцессе эксплуатации;
уменьшение соотношения водород/сырье по высоте слоя катали-
затора;
неравномерность температур в слое при проведении регенерации катализатора, что приводит к уменьшению срока службы катализатора.
По материальному оформлению реактора с аксиальным движением
(вводом) сырья бывают двух типов [9]:
с наружной тепловой изоляцией (теплоизоляция поверх корпуса
реактора);
с внутренней защитной футеровкой торкрет-бетоном (теплоизо-
ляция внутри корпуса реактора).
6
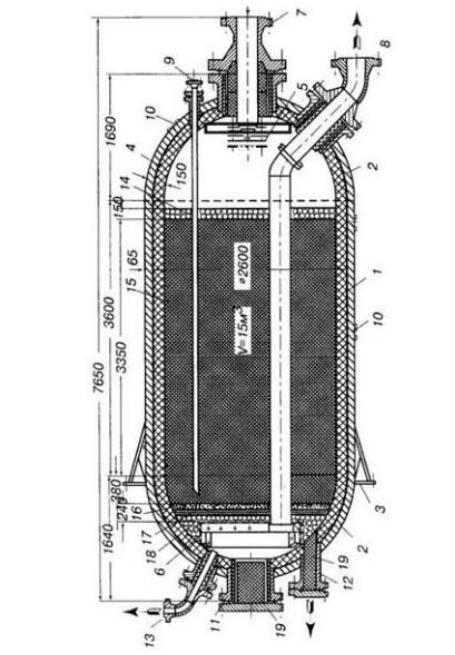
Рисунок 3 – Аксиальный реактор с наружной тепловой изоляцией:
1 – корпус; 2 – днище; 3 – опорной кольцо; 4 – футеровка; 5 – распределитель; 6 – опорная решетка; 7 – вход парогазовой смеси; 8 – выход парогазовой смеси;
9 – штуцер; 10 – наружные термопары; 11 – люк; 12 – люк для выгрузки катализатора; 13 – штуцер для эжекции газов; 14 – фарфоровые шарики; 15 – катализатор; 16 – шарики диаметров 6 мм; 17 – шарики диаметром 13 мм; 18 – шарики диаметром 20 мм; 19 – легкий шамот; 20 – защитный стакан; 21 – отбойный зонт; 22 – лючок для очитки; 23 – вход охлаждающего газа.
7
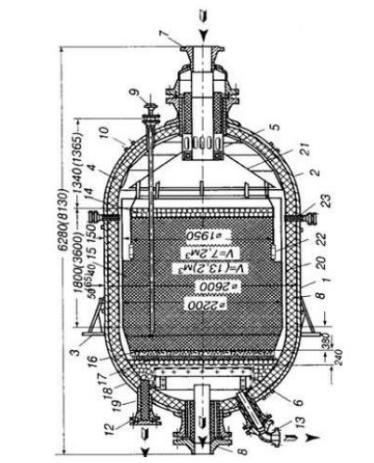
Рисунок 4 – Аксиальный ректор с внутренней тепловой изоляцией:
1 – корпус; 2 – днище; 3 – опорное кольцо; 4 – футеровка; 5 – распределитель; 6 – опорная решетка; 7 – вход парогазовой смеси; 8 – выход парогазовой смеси;
9 – штуцер; 10 – наружные термопары; 11 – люк; 12 – люк для выгрузки катализатора; 13 – штуцер для эжекции газов; 14 – фарфоровые шарики; 15 – катализатор; 16 – шарики диаметром 6 мм; 17 – шарики диаметром 13 мм; 18 – шарики диаметром 20 мм; 19 – легкий шамот; 20 – защитный стакан; 21 – отбойный зонт; 22 – лючок для очистки; 23 – вход охлаждающего газа.
Принцип действия аксиальных реакторов прост. В верхний штуцер по-
дается газо-сырьевая смесь, после чего она равномерно распределяется на распределителе. Продукты, прошедшие слой катализатора, выходят по цен-
тральной трубе через верхний штуцер.
В процессах каталитической депарафинизации возможно применение и других реакторов, например, реактора с радиальным вводом сырья. Главное преимущество такого реактора перед аксиальным, заключается в меньшем гидравлическом сопротивлении [8].
8
МАТЕМАТИЧЕСКАЯ МОДЕЛЬ КАТАЛИТИЧЕСКОЙ ДЕПАРАФИНИЗАЦИИ
База данных компьютерной моделирующей системы процесса катали-
тической депарафинизации, которую я использую в своей научной работе,
содержит:
данные о химизме процесса и механизмах протекающих в про-
цессе реакций;
термодинамические характеристики реакций (изменение энталь-
пии, изменение энергии Гиббса, изменение энтропии в ходе реакций);
кинетические параметры реакций (энергия активации, предэкспо-
ненциальный множитель в уравнении Аррениуса);
характеристики реактора (размеры, конструкция);
состав и свойства сырья, состав водородсодержащего газа, техно-
логические параметры процесса за длительный период эксплуатации про-
мышленной установки.
Основные реакции процесса каталитической депарафинизации и их термодинамические и кинетические параметры приведены в таблице 1.
Таблица 1 – Термодинамические и кинетические параметры основных реакций каталитической депарафинизации
Реакция |
Н, |
, |
Еа, |
0 |
|
кДж/моль |
кДж/моль |
кДж/моль |
|
|
|
|
|
|
Дегидрирование н-парафинов |
-144,93 |
-77,48 |
110 |
13,1 ∙ 106 |
|
|
|
|
|
Гидрокрекинг олефинов |
-36,70 |
-52,20 |
140 |
10,0 ∙ 106 |
|
|
|
|
|
Изомеризация и гидрирование |
-146,91 |
-83,07 |
130 |
10,0 ∙ 106 |
олефинов |
|
|
|
|
|
|
|
|
|
Циклизация олефинов |
-91,22 |
-52,77 |
180 |
10,0 ∙ 106 |
|
|
|
|
|
Дегидрирование нафтенов |
-231,33 |
-55,31 |
140 |
10,0 ∙ 106 |
|
|
|
|
|
Образование кокса |
-87,90 |
-252,90 |
190 |
6980,0 ∙ 106 |
|
|
|
|
|
Крекинг н-парафинов |
82,80 |
-3,79 |
200 |
10,0 ∙ 106 |
|
|
|
|
|
Образование меркаптанов |
-97,88 |
-24,27 |
80 |
10,0 ∙ 106 |
|
|
|
|
|
9
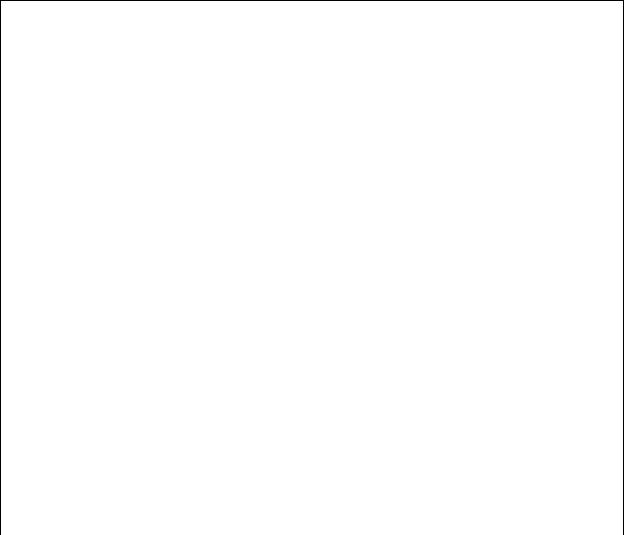
Как говорили выше, актуальный реактор процесса каталитической де-
парафинизации – вертикальный аппарат с аксиальным вводом сырья. При-
нято допущение о поршневом течении потока внутри реактора при отсут-
ствии продольного перемешивания и равномерном распределении реакцион-
ной массы в направлении, перпендикулярном движению потока.
Время нахождения всех частиц в системе одинаково и определяется как отношение объема системы к объемному расходу жидкости. В таблице 2
представлен фрагмент базы данных по составу и свойствам сырья, техноло-
гическим параметры процесса.
Таблица 2 – Фрагмент базы данных по составу, свойствам и технологи-
ческим условиям процесса депарафинизации
Состав и плотность сырья
Точка |
|
Фракционный состав |
|
Плотность сырья при |
|||
отбора |
|
|
|
|
20 0С, |
|
|
Т10%, |
|
Т50%, |
Т90%, |
|
|||
|
0С |
|
0С |
0С |
кг/м3 |
|
|
1 |
239 |
|
277 |
342 |
849 |
|
|
|
|
|
|
|
|
|
|
2 |
246 |
|
285 |
349 |
851 |
|
|
|
|
|
|
|
|
|
|
3 |
249 |
|
290 |
351 |
847 |
|
|
|
|
|
|
|
|
|
|
4 |
248 |
|
290 |
353 |
848 |
|
|
|
|
|
|
|
|
|
|
5 |
249 |
|
291 |
355 |
850 |
|
|
|
|
|
|
|
|
|
|
|
|
|
Технологические параметры |
|
|
|
|
|
|
|
|
|
|
|
|
Точка |
Расход сырья, |
|
Расход ВСГ вР-3, |
Температура |
Темпера- |
|
Давле- |
отбора |
м3/ч |
|
м3/ч |
сырья на вы- |
тура ВСГ, |
|
ние в Р- |
|
|
|
|
ходе из печи, |
0С |
|
3, |
|
|
|
|
0С |
|
|
МПа |
1 |
234 |
|
9589 |
343,7 |
85,0 |
|
7,5 |
|
|
|
|
|
|
|
|
2 |
247 |
|
16515 |
346,5 |
85,0 |
|
7,5 |
|
|
|
|
|
|
|
|
3 |
247 |
|
19151 |
347,4 |
85,1 |
|
7,5 |
|
|
|
|
|
|
|
|
4 |
242 |
|
18059 |
346,9 |
85,2 |
|
7,5 |
|
|
|
|
|
|
|
|
5 |
242 |
|
24472 |
349,3 |
85,7 |
|
7,5 |
|
|
|
|
|
|
|
|
Т10%, Т50%, Т90% - температура выкипания 10 %, 50 %, 90 % фракции, соответственно; ВСГ – водородсодержащий газ.
10