
Реакторный блок установки каталитического крекинга
.pdfконсорциум н е д р а
Переработки нефти.
Реакторный блок установки каталитического крекинга
Исходные данные к проекту:
Производительность реактора по свежему сырью GС = 260 т/ч
Количество рециркулирующего 28.4 масс. % на свежее каталитического газойля сырье Режим процесса:
Температура крекинга Тр= 763К
Массовая кратность циркуляции Катализатора по свежему сырью 7 : 1
Введение Промышленные установки каталитического крекинга. Изменяя технологический режим, а также используя разные
сырье и катализатор, можно в весьма широких пределах изменять выход и качество получаемых продуктов. Данные показывают, что эффективность применения цеолитсодержащих катализаторов, особенно содержащих окислы редкоземельных металлов очень высока.
Процесс каталитического крекинга стали внедрять в промышленность в конце 30-х гг. Это были установки Гудри со стационарным слоем аморфного катализатора, сложной и дорогой системой автоматического управления. С тех пор процесс каталитического крекинга непрерывно совершенствуется. Установки Гудри были вытеснены более экономичными и менее сложными системами с подвижным циркулирующим слоем катализатора. В промышленности стали эксплуатировать установки двух типов: на установках первого типа каталитический крекинг сырья и регенерация
консорциум н е д р а
катализатора осуществляются в сплошном, медленно опускающемся слое шарикового катализатора (диаметр 3-6 мм);
На установках второго типа процессы каталитического крекинга и регенерации катализатора протекают в «кипящем»
(псевдоожиженном) слое порошкообразного или сферического катализатора. Большое значение для совершенствования установок первого типа имело пневмотранспортирование катализатора с одним подъемом его (реактор над регенератором), впервые в мире осуществленное на установке 43-1 в г. Грозном.
Вдальнейшем аморфные алюмосиликатные катализаторы были заменены кристаллическими
(цеолитсодержащимися). Вскоре стали применять установки нового типа - двухступенчатые: в первой ступени крекинг происходит в восходящем потоке в катализаторопроводе после контакта его с нагретым сырьем (эту ступень часто называют крекингом в лифт-реакторе), во второй ступени - в ограниченном объеме псевдоожиженного («кипящего»)
слоя. Иногда ограничиваются крекингом только в восходящем потоке (лифт-реакторе). Широкому применению установок последнего типа в значительной степени способствовало использование высокоактивных цеолитсодержащих катализаторов. Наконец, в последнее время стали применять установки с практически полным дожигом окисла углерода не в котлах-утилизаторах, а непосредственно в регенераторах. Совершенствуется также конструкция аппаратуры и оборудования на этих установках, а также катализаторы и технология процесса.
Каталитический крекинг по сравнению с термическим характеризуется меньшим выходом метана, этана и олефинов, большим выходом углеводородов С3-С4, а также бензинов с повышенным содержанием ароматических и изопарафиновых углеводородов. В этом заключается главное преимущество каталитического крекинга перед термическим.
1.
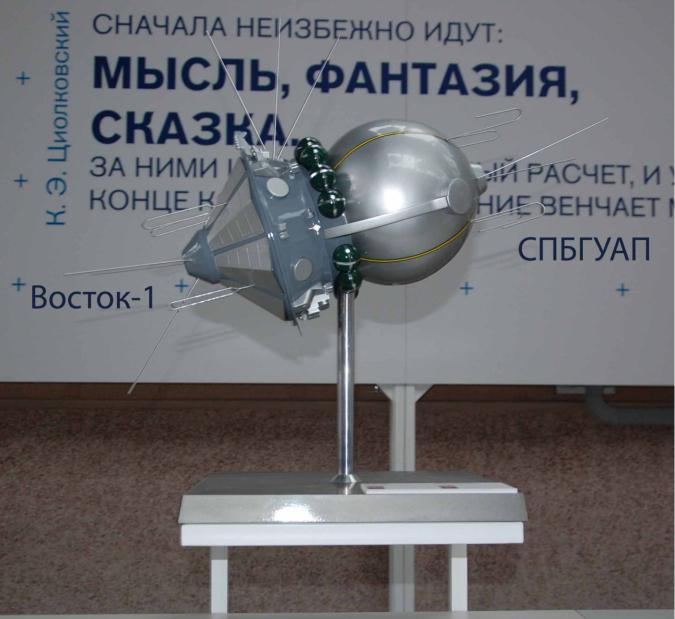
Макет космического корабля «Восток-1» в павильоне «Космос» на ВДНХ. За ним — цитата К. Э. Циолковского:
«Сначала неизбежно идут: мысль, фантазия, сказка. За ними шествует научный расчёт. И уже в конце концов исполнение венчает мысль»
консорциум н е д р а
Технологическая часть
1.1 Теоретические основы процессакаталитический крекинг гидроочищенный Процесс каталитического крекинга гидроочищенного сырья является целевым в наборе процессов установки и
позволяет получать следующие продукты:
жирный газ и нестабильный бензин, используемые в качестве сырья на секции абсорбции и газофракционирования, с целью получения пропан-пропиленовой (С3), бутан-бутиленовой (С4)фракций, сухого газа
(С2) и высокооктанового компонента автобензина АИ-92,А-80 (фракция К-205°С;
легкий газойль, используемый в качестве компонента дизельного топлива или товарного печного топлива
(фракция 195-270°С);
фракцию 270-420°С, используемую в качестве компонента сырья для производства технического углерода,
компонента котельного топлива или добавки к сырью висбрекинга;
фракцию > 420°С, используемую в качестве компонента сырья для производства технического углерода,
компонента котельного топлива или сырья для установки замедленного коксования с целью получения кокса игольчатой структуры.
Для осуществления процесса каталитического крекинга в составе секции 200 предусмотрены следующие блоки:
реакторный блок;
блок ректификации и очистки технологического конденсата;
воздушная компрессорная.
Сущность процесса каталитического крекирования углеводородов основана на расщеплении высокомолекулярных
консорциум н е д р а
компонентов сырья на более мелкие молекулы с перераспределением освобождающихся по месту разрыва связи
"углерод-углерод" водорода.
В итоге образуется газ, бензин, и кокс, отлагающийся на поверхности катализатора.
Постадийно процесс каталитического крекинга может быть представлен следующим образом:
поступление сырья к поверхности катализатора(внешняя диффузия);
химабсорбция на активных центрах катализатора;
химическая реакция на поверхности катализатора;
десорбция продуктов крекинга непрореагировавшей части сырья с поверхности катализатора и частично из внутренних пор;
вывод продуктов крекинга из зоны реакции на последующую их ректификацию.
Наиболее типичными компонентами сырья каталитического крекинга являются парафиновые углеводороды, при крекинге которых доминируют разложения С16Н34 ---> С8Н18 + С8Н16.
Наиболее часто разрыв молекулы парафинового углеводорода происходит по средней ее части.
Термическая стабильность парафинов понижается с увеличением молекулярного веса углеводородов.
При крекинге парафиновых углеводородов нормального строения протекают и вторичные реакции с образованием ароматических углеводородов и кокса. Изопарафиновые углеводороды крекируются легче.
Водорода и метана при этом получается больше, чем при крекинге нормальных парафинов, а углеводородов С3 и
С4 меньше.
Нафтеновые углеводороды являются идеальными компонентами сырья каталитического крекинга, так как крекинг
консорциум н е д р а
нафтенов идет с большими скоростями, с более высоким выходом бензина и меньшим газообразованием.
Большой интерес для технологии каталитического крекинга представляет поведение ароматических углеводородов. Крекинг ароматических углеводородов сопровождается их деалкилированием и конденсацией.
1.(CН2)5-СН3 → СН2-СН3+СН3-СН2-СН=СН2
.СН2-СН2-СН3 → +СН3-СН2-СН2-СН2-СН2-СН3
Между молекулами ароматических углеводородов или между ароматическими и олефиновыми протекают реакции конденсации, в результате которых образуется полициклическая ароматика вплоть до асфальтена и кокса.
Поэтому при переработке сырья со значительным содержанием полициклической ароматики образуется значительно больше кокса, чем при переработке сырья, содержащего моноциклические ароматические углеводороды.
Крекинг олефинов, образующихся в результате расщепления парафиновых, нафтеновых, ароматических, а также самих олефиновых, является вторичной реакцией. Возможность изомеризации олефинов позволяет получать бензин с более высоким октановым числом с одновременным увеличением выхода изобутана.
Полимеризация олефинов также является важной реакцией процесса, поскольку в сочетании с последующим крекингом, приводит к образованию олефинов и парафинов
СН2=СН2+СН2=СН2 → СН3-СН=СН-СН3.
Однако глубокая полимеризация ведет к образованию тяжелых продуктов, абсорбирующихся и разлагающихся на
консорциум н е д р а
катализаторе на кокс и газ.
Обычно одним из лучших критериев интенсивности побочных реакций является отношение выходов бензина и кокса. Высокое отношение указывает на преобладание желательных реакций (при условии сохранения высокого октанового числа бензина). Низкое отношение указывает на интенсивное протекание побочных реакций.
На основании вышеизложенного можно сделать следующие выводы:
тяжелое сырье дает большой выход бензина и меньший выход газа;
ароматическое сырье дает наибольший выход кокса и наименьший выход бензина;
нафтеновое сырье дает лучший выход бензина и наименьший выход кокса в сравнении с ароматическим и парафиновым сырьем;
низкокипящее сырье позволяет получить высокооктановый бензин, высококипящее - низкооктановый;
сырье с высоким содержанием серы дает низкооктановый бензин;
сырье с очень высокой температурой кипения и значительным содержанием кокса по Конрадсону дает высокий выход кокса, ограничивающий мощность секции из-за чрезмерной перегрузки регенератора.
Основными факторами, влияющими на процесс каталитического крекинга, являются: свойства применяемого для крекирования катализатора, температура процесса, кратность циркуляции катализатора, продолжительность контакта сырья и катализатора, качество крекируемого сырья.
Для обеспечения максимального выхода целевых продуктов и минимального количества побочных, а также для достижения высоких технико-экономических показателей процесса, катализатор крекинга должен иметь следующие основные свойства:
консорциум н е д р а
высокую активность, способствующую большей глубине превращения исходного сырья при прочих равных условиях;
высокую селективность, которая оценивается способностью катализатора ускорять реакции получения бензина и снижать скорость побочных реакций: образования газа и кокса;
стабильность.
Стабильность активности, селективности и механических свойств катализатора в процессе эксплуатации особенно важна в системах с кипящим слоем катализатора. Катализатор должен быть стойким к истиранию, растрескиванию и давлению вышележащих слоев, а также
не должен истирать аппаратуру;
высокие регенерационные свойства, характеризующиеся способностью быстро и многократно восстанавливать свою активность и селективность при окислительной регенерации без нарушения поровой структуры и разрушения частиц.
Заложенный в проекте микросферический цеолитсодержащий катализатор в значительной степени отвечает всем перечисленным требованиям, предъявляемым к современным катализаторам крекинга.
Химический и фракционный состав сырья крекинга оказывает значительное влияние на процесс каталитического крекинга.
Присутствие в сырье сернистых, азотистых и металлоорганических соединений дезактивирует применяемый катализатор, ухудшает качество продуктов крекинга.
С целью улучшения качества сырья каталитического крекинга в состав комплекса введена предварительная
консорциум н е д р а
гидроочистка сырья, что позволяет полностью исключить влияние колебаний в изменении качественного состава сырья на результаты процесса крекинга и стабилизировать работу реакторно-регенераторного блока.
Процесс с применением гидроочищенного сырья протекает более глубоко и селективно, в результате чего возрастает абсолютный выход бензина и снижается выход кокса.
Отличительной особенностью продуктов крекинга, полученных при переработке гидроочищенного сырья,
является низкое содержание в них серы, это исключает дополнительные затраты по их гидрооблагораживанию.
Влияние оперативных условий на процесс каталитического крекинга
. Увеличение объемной скорости подачи сырья в реактор понижает глубину превращения сырья, т.к. уменьшается время контактирования углеводородных фракций с катализатором и приводит к снижению выхода кокса.
. Температура в реакторе - наиболее общий параметр, влияющий на выход бензина, октановое число и конверсию.
Повышение температуры в реакторе увеличивает конверсию, выход кокса и повышает температуру в регенераторе. По результатам исследований установлено, что увеличивая температуру в реакторе на 10°С можно повысить октановое число (ИОЧ) на 0,7-1,8п., однако, повышая октановое число бензина, снижается выход бензина и увеличивается выход сухого газа и, при повышении температуры в реакторе до 540°С значительно возрастает скорость вторичных секций.
Повышение температуры в реакторе в большей степени влияет на увеличение октанового числа тяжелых бензинов, т.к.
рост температуры в реакторе способствует в большей мере образованию олефинов в тяжелых бензинах.
. Кратность циркуляции - соотношение потоков катализатора и сырья влияет на глубину разложения сырья и выход основных продуктов крекинга и, изменяется в пределах от 5:1 до 10:1.
При увеличении кратности циркуляции повышается глубина разложения сырья, растет выход бензина,
консорциум н е д р а
увеличивается процент отложения кокса на катализаторе но, при чрезмерном увеличении кратности циркуляциирезко возрастает разложение целевых продуктов, выход бензина падает, а количество кокса и газа увеличивается. При постоянной производительности по сырью, с увеличением кратности циркуляции катализатора происходит уменьшение температуры в регенераторе, с одновременным увеличением количества кокса, циркулирующего в системе.
. Температура ввода сырья в реактор определяется из теплового баланса реактора-регенератора и влияет на изменение кратности циркуляции катализатора. С увеличением температуры ввода сырья в реактор, температура в зоне выжига кокса регенератора увеличивается и понижается кратность циркуляции.
Пониженная температура подогрева сырья увеличивает конверсию и снижает температуру регенератора. При пониженной температуре значительно увеличивается выход кокса и повышается циркуляция катализатора.
. Содержание кислорода в дымовых газах.
Увеличение процента кислорода в дымовых газах регенерации, за счет увеличения подачи воздуха, понизит содержание кокса на регенерированном катализаторе, образование углерода в реакторе и температуру в регенераторе.
Однако слишком высокий процент кислорода может привести к догоранию СО в СО2 в объеме регенератора и послужить причиной аварийной ситуации.
. Подача шлама в реактор.
Направление шлама в реактор позволяет повысить эффективность процесса крекинга, сделать более гибкой регулировку температурного режима системы реактор-регенератор, за счет увеличения коксовой нагрузки на регенератор. Увеличение подачи шлама в реактор может
быть вызвано необходимостью замыкания теплового баланса системы реактор-регенератор при относительно