
Сырье каталитического крекинга-1
.pdfкаталитического крекинга. Тяжелый газойль используют либо при приготовлении мазутов, либо в качестве сырья для термического крекинга и коксования. В последнее время его использует как сырье для производства сажи.
4 Катализаторы каталитического крекинга
Реакции каталитического крекинга протекают на поверхности катализатора. Направление реакций зависит от свойств катализатора, сырья и условий крекинга. В результате крекинга на поверхности катализатора отлагается кокс, поэтому важной особенностью каталитического крекинга является необходимость частой регенерации катализатора (выжигание кокса). Для каталитического крекинга применяются алюмосиликатные катализаторы. Это природные или искусственно полученные твердые высокопористые вещества с сильно развитой внутренней поверхностью.
Взаводской практике применяют алюмосиликатные активированные
природные глины и синтетические алюмосиликатные катализаторы в виде порошков, микросферических частиц диаметром 0,04-0,06 мм или таблеток и шариков размером 3- 6мм. В массе катализатор представляет собой сыпучий материал, который можно легко транспортировать потоком воздуха или углеводородных паров.
На установках крекинга применяются следующие алюмосиликатные катализаторы:
1.Синтетические пылевидные катализаторы с частицами размеров 1-150 мк.
2.Природные микросферические или пылевидные катализаторы, приготовляемые из природных глин (бентониты, бокситы и некоторые другие) кислотной и термической обработкой или только термической обработкой.
3.Микросферический формованный синтетический катализатор с частицами размером 10-150 мк. По сравнению с пылевидным, микросферический катализатор при циркуляции меньше измельчается и в меньшей степени вызывает абразивный износ аппаратуры и катализаторопроводов. Удельный расход его ниже, чем расход пылевидного катализатора.
4.Синтетический катализатор в виде стекловидных шариков диаметром 3-6 мм.
5.Природные и синтетические катализаторы с частицами размером 3-4мм искаженной цилиндрической. формы. Их часто называют таблетированными, они характеризуются меньшей прочностью, чем шариковые, и используются преимущественно на установках с неподвижным катализатором. Указанные выше 5 типов катализаторов являются аморфными.
6.Синтетические кристаллические цеолитсодержащие катализаторы, содержащие окись хрома (что способствует лучшей регенерации), а также окиси, редкоземельных металлов (улучшающие селективность катализатора и увеличивающие выход бензина с некоторым улучшением его свойств). Они вырабатываются гранулированными - для установок с нисходящим потоком катализатора - и микросферическими - для установок в кипящем слое.
Катализаторы современных крупнотоннажных процессов каталитического крекинга, осуществляемых при высоких температурах (500-800 °С) в режиме интенсивного массо- и теплообмена в аппаратах с движущимся или псевдоожиженным слоем катализатора, должных обладать не только высокими активностью, селективностью
итермостабильностью, но и удовлетворять повышенным требованиям к ним по регенерационным, механическим и некоторым другим эксплуатационным свойствам. Промышленные катализаторы крекинга представляют собой в этой связи сложные многокомпонентные системы, состоящие из: 1) матрицы (носителя); 2) активного компонента — цеолита; 3) вспомогательных активных и неактивных добавок.
8
консорциум н е д р а
Матрица катализаторов крекинга выполняет функции как носителя — поверхности, на которой затем диспергируют основной активный компонент — неолит и вспомогательные добавки, так и слабого кислотного катализатора предварительного (первичного) крекирования высокомолекулярного исходного нефтяного сырья. В качестве материала матрицы современных катализаторов крекинга преимущественно применяют синтетический аморфный алюмосиликат с высокой удельной поверхностью и оптимальной поровой структурой, обеспечивающей доступ для крупных молекул крекируемого сырья.
Аморфные алюмосиликаты являлись основными промышленными катализаторами крекинга до разработки цеолитсодержащих катализаторов. Синтезируются они при взаимодействии растворов, содержащих оксиды алюминия и
кремния, |
|
например жидкого стекла Na2O 3SiO2 |
и сернокислого алюминия |
Al2 (SO4 ) |
3 . |
||||||||
Химический |
состав |
аморфного |
алюмосиликата |
может |
быть |
выражен |
формулой |
||||||
Na |
O( Al |
2 |
O |
xSiO ) , |
где х — |
число молей |
|
SiO на 1 |
моль |
Al O . |
Обычно |
в |
|
2 |
|
3 |
2 |
|
|
|
2 |
|
2 |
3 |
|
|
промышленных аморфных алюмосиликатах содержание оксида алюминия находится в пределах 6-30% мас.
Аморфные алюмосиликаты обладают ионообменными свойствами, а для
придания каталитической активности |
обрабатывают их раствором сернокислого |
||||
алюминия для замещения катионов |
Na |
+ |
на Al |
3+ |
. Высушенные и прокаленные аморфные |
|
|
алюмосиликаты проявляют протонную и апротонную кислотности. При этом по мере повышения температуры прокаливания происходит превращение протонных кислотных центров в апротонные.
Активным компонентом катализаторов крекинга является цеолит, который позволяет осуществлять вторичные каталитические превращения углеводородов сырья с образованием конечных целевых продуктов.
Цеолиты (от греческого слова цео — кипящий, литос — камень) представляют собой алюмосиликаты с трехмерной кристаллической структурой.
Недостатком всех цеолитов является их не очень высокая механическая прочность в чистом виде, и поэтому они в качестве промышленного катализатора не используются. Обычно их вводят в диспергированном виде в матрицу катализаторов в количестве 10-20% мас.
Вспомогательные добавки улучшают или придают некоторые специфические физико-химические и механические свойства цеолитсодержащих алюмосиликатных катализаторов (ЦСК) крекинга. ЦСК без вспомогательных добавок не могут полностью удовлетворять всему комплексу требований, предъявляемых к современным промышленным катализаторам крекинга. Так, матрица и активный компонент – цеолит, входящий в состав ЦСК, обладают только кислотной активностью, в то время как для организации интенсивной регенерации закоксованного катализатора требуется наличие металлических центров, катализирующих реакции окислительно-восстановительного типа. Современные и перспективные процессы каталитического крекинга требуют улучшения и оптимизации дополнительно таких свойств ЦСК, как износостойкость, механическая прочность, текучесть, стойкость к отравляющему воздействию металлов сырья и т.д., а также тех свойств, которые обеспечивают экологическую чистоту газовых выбросов в атмосферу.
9
консорциум н е д р а
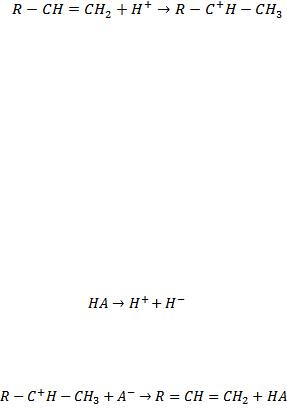
5 Физико-химические основы процесса
Химизм процесса. Наиболее распространенной теорией, объясняющей механизм каталитического крекинга на алюмосиликатных катализаторах, является теория карбонийиона. Эта теория была впервые предложена для объяснения механизма полимеризации над кислотными катализаторами (H2SO4, H3PO4, AlCl3). Теперь эта теория распространяется и на каталитический крекинг в присутствии алюмосиликатного катализатора, так же имеющего кислотный характер. В основе этой теории лежат следующие представления:
Ионы карбония аналогичны ионам аммония и содержат трехвалентный положительно заряженный атом углерода. Легче всего они образуются при взаимодействии протона катализатора с олефинами.
Путем внутренней перегруппировки или взаимодействия с другими молекулами сырья, неустойчивые ионы карбония стремятся перейти в более устойчивые формы. Они отличаются очень большой реакционной способностью и могут вступать в самые разнообразные реакции. Это:
а) Перегруппировка атомов в молекуле с перемещением водорода или метильных групп (иначе говоря, скелетная изомеризация, приводящая к образованию изомерного иона)
б) Взаимодействие с нейтральными молекулами с образованием новых ионов карбония и новых молекул как предельных, так и непредельных.
в) Распад карбоний-иона с большим числом углеродных атомов. Расщепление, как правило, происходит по β-связи, считая от заряженного атома углерода. Продукты распада – это олефин и меньший карбоний-ион.
В целом, согласно теории ионов карбония, механизм каталитического крекинга представляется в виде цепных реакций. Зарождение цепи происходит под действием иона водорода катализатора
Здесь под HA подразумевается алюмосиликатный катализатор.
Развитие цепи идет по линии разнообразных превращений ионов карбония и водородного обмена с нейтральными молекулами. Наконец, обрыв цепи происходит в результате реакции между ионом карбония (катион) и анионом алюмосиликата.
Катализатор в конечном итоге регенерируется в исходное состояние и процесс может начинаться снова. Если поверхность катализатора еще сохраняет свою активность. Химизм каталитического крекинга значительно отличается. На это влияют как кинетические факторы, так и специфические свойства катализатора. Основные особенности химизма каталитического крекинга следующие:
Термический крекинг |
|
Каталитический крекинг |
|
Парафины |
|
Олефины |
|
Олефины |
|
Ароматические |
углеводороды с |
|
|
большим числом боковых цепей |
|
Нафтены |
|
Нафтены |
|
Алкиллированные |
ароматические |
Парафины |
|
углеводороды |
|
|
|
Голоядерные |
ароматические |
Голоядерные |
ароматические |
углеводороды |
|
углеводороды |
|
1. Склонность к превращениям у различных классов углеводородов при каталитическом и термическом крекинге различны. Выше в таблице расположены для сравнения основные группы углеводородов в ряды, возрастающие по термической
10
консорциум н е д р а
стабильности. Особенно характерно при каталитическом крекинге высокая реакционная способность олефинов и малая парафинов. Указанная последовательность объясняется избирательной адсорбцией различных углеводородов на поверхности катализатора. В первую очередь катализатор адсорбирует ненасыщенные богатые энергией соединения. Это диолефины, олефины, ароматические соединения. Адсорбция парафинов при работе с сырьем сложного состава незначительна. Именно поэтому ускорение реакции крекинга в присутствии катализаторов для олефинов и ароматических углеводородов в сотни и даже тысячи раз превышает ускорение распада парафинов. Однако, по мере обеднения реакционной смеси ненасыщенными углеводородами, парциальное давление предельных углеводородов над катализатором увеличивается. Это приводит к усилению адсорбции и увеличению скорости превращений. Селективная адсорбция служит причиной ступенчатого последовательного хода процесса, при котором углеводороды, сильно сорбирующиеся катализатором, тормозят реакции слабо сорбирующихся углеводородов. При термическом крекинге все компоненты сырья претерпевают превращения одновременно и кажущаяся селективность процесса объясняется лишь различием в величине констант скорости тех или иных реакций.
2. Наиболее характерной особенностью химических превращений углеводородного сырья при каталитическом крекинге является значительное развитие реакции изомеризации. Изомерные превращения хорошо объясняются с точки зрения теории карбоний-иона. В результате изомеризации ненасыщенных осколков и дальнейшего их насыщения их водородом, в продуктах крекинга накапливаются изопарафиновые углеводороды. В частности весьма характерно высокое содержание изобутана в крекинггазе.
Связь продуктов каталитического крекинга с механизмом и кинетикой процесса. Химический состав продуктов каталитического крекинга имеет характерные
особенности:
1.Этот бензин содержит много изопарафинов и ароматических
2.Газ получается тяжелый с высокой концентрацией изобутана и олефинов
3.Газойлевые фракции богаты полициклическими и ароматическими углеводородами
Это своеобразие химического состава объясняется следующими причинами:
1.Различие механизма реакции термического и каталитического крекинга. Реакции термического крекинга протекают по радикально-цепному механизму, а каталитического через карбоний-ион.
2.Способностью активной поверхности катализатора селективно ускорять некоторые реакции (например, изомеризацию олефинов, скорость которой при термическом крекинге очень мала). Однако в присутствии катализатора может повыситься скорость только тех реакций, которые для данного интервала температур термодинамически вероятны.
Физико-химические явления процесса. Применительно к каталитическому крекингу необходимо рассматривать не только химизм протекания процесса, но и сопровождающие его физико-химические явления. Постадийно процесс каталитического крекинга может быть представлен следующим образом:
1.Поступление сырья к поверхности катализатора (внешняя диффузия)
2.Движение сырья в поры катализатора (внутренняя диффузия)
3.Хемосорбция на активных центрах катализатора
4.Химические реакции на поверхности катализатора
5.Десорбция продуктов крекинга и непрореагировавшего сырья с поверхности и диффузия из пор катализатора
6.Удаление продуктов крекинга и неразложившегося сырья из зоны реакции.
11
консорциум н е д р а

В зависимости от режима процесса, качества сырья и степени дисперсности катализатора, роль диффузионных и адсорбционных процессов может быть больше или меньше. Так установлено, что при нормальном режиме реактора каталитического крекинга с кипящим слоем порошкообразного катализатора при температурах от 480 до 535°С решающее значение имеют адсорбция и химические реакции на поверхности катализатора. При крекинге на крупногранулированном катализаторе скорость реакции тормозится диффузией молекул сырья к внутренней поверхности катализатора. Глубина превращения сырья возрастает, если увеличивается время контакта его с катализатором. Это условие определяется величиной объемной скорости подачи сырья.
Объемной скоростью подачи сырья называется отношение расхода сырья к объему загруженного в реактор катализатора.
Величина обратная – это время контакта сырья с катализатором.
Закоксовывание и регенерация катализатора каталитического крекинга.
По мере подачи сырья, активность катализатора падает, так как поверхность его покрывается слоем смолисто-коксовых отложений. Катализатор приобретает интенсивнотемную окраску уже при поступлении первых порций сырья. Условно эти смолистококсовые отложения называют коксом, хотя элементарный анализ показывает, что содержание водорода в них довольно значительно (от 5 до 7% массовых, а может достигать и 10%). Источником образования кокса на катализаторе являются в первую очередь смолисто-асфальтеновые вещества, содержащиеся в сырье.
Так, например, в производственных условиях при переработке легкий керосиногазойлевых фракций, выход кокса составляет от 2-3% до 4-5% на сырье, а при крекинге тяжелых вакуумных газойлей – до 5-6% массовых, однако, большую роль играет и углеводородный состав сырья. Максимальные выходы кокса получаются при наличии ароматических углеводородов би- и трициклического строения. Известна склонность к коксообразованию сырья вторичного происхождения, например, газойлей коксования, содержащих ароматические углеводороды с непредельными боковыми цепями.
Длительность пребывания катализатора в зоне реакции, то есть, продолжительность работы катализатора между двумя периодами регенерации составляет на современных промышленных установках от 2 до 30 минут. Естесственно, что чем меньше продолжительность работы катализатора, тем выше его средняя активность за этот период. Регенерация катализатора обычно значительно сложнее, чем проведение самого крекинга.
Сущность регенерации заключается в сгорании коксовых отложений при их контактировании с кислородом воздуха. В результате такого контакта происходит значительное выделение тепла (от 6000 до 7500 ккал/кг кокса), которое необходимо отводить из зоны регенерации, чтобы не перегреть всю массу катализатора. При этом продолжительность регенерации не должна быть очень большой, чтобы регенератор был приемлемых размеров.
Исследование кинетики регенерации позволило определить пути интенсификации этого процесса в промышленных условиях. Было показано, что в области умеренных температур (450-500°С) регенерация протекает в кинетической области, то есть интенсивность её определяется скоростью реакции окисления. Энергия активации процесса регенерации в кинетической области составляет от 31 до 35 ккал/моль. С повышением температуры до 500-550°С процесс переходит во внешнюю или внутреннюю диффузионную область.
Варианты промышленных процессов каталитического крекинга.
12
консорциум н е д р а
В настоящее время имеется много схем и промышленных процессов каталитического крекинга, различающихся технологическим и аппаратурным оформлением:
1. Процесс со стационарным слоем катализатора.
2. Процесс с подвижным гранулированным или сферическим катализатором.
3. Крекинг с пылевидным или микросферическим движущимся катализатором.
В этом варианте крекинга в аппарате образуется псевдокипящий слой катализатора. Установка работает непрерывно благодаря непрерывной циркуляции катализатора. Транспорт катализатора осуществляется по принципу газлифта, что значительно упрощает установку. Применение пылевидного катализатора, образующего кипящий слой, дает ряд особых преимуществ. Принцип кипящего слоя твердого измельченного материала в настоящее время широко применяется во всех новых областях химической технологии.
Режимы работы установок
Каталитический крекинг происходит, как правило, в паровой фазе в системе без притока и отдачи тепла, поэтому его относят к адиабатическим процессам. При адиабатическом процессе внешняя работа полностью затрачивается на изменение внутренней энергии системы.
В зависимости от характеристик перерабатываемого сырья и системы или типа установки, а также от состава и свойств катализатора устанавливается определенный технологический режим. К основным показателям технологического режима установок каталитического крекинга следует отнести температуру, давление, соотношение количества сырья и катализатора, находящегося в зоне крекинга, а также кратность циркуляции катализатора.
Каталитический крекинг проводят в следующих условиях: температура, °С
крекинга - 450-525;
регенерации катализатора - 540-680; давление, ат в реакторе - 0,6-1,4; в регенераторе - 0,3 - 2,1;
Рассмотрим основные закономерности процесса.
Температура. С повышением температуры увеличивается октановое число бензина, возрастает выход газов С1-С3 и олефинов С4 и выше, снижается выход бензина и кокса, но повышается соотношение бензин: кокс и снижается соотношение выходов легкого и тяжелого газойля.
Давление. При повышении давления увеличивается выход парафиновых углеводородов и бензина, снижается выход газов С1-С3, олефинов и ароматических углеводородов. Выход кокса в условиях промышленного процесса от давления практически не зависит.
Глубина крекинга. Рециркуляция. Глубину превращения (или глубину крекинга) принято оценивать количеством сырья, превращенного в бензин, газ или кокс. При крекинге в одну ступень (однократный крекинг) глубина превращения равна 45-60%. Примерный выход продуктов при однократном каталитическом крекенге керосина - соляровой фракции прямой перегонки нефти приведен ниже (индекс активности катализатора 28-32):
глубина крекинга,% - 50 - 60 выход, вес.% сухой газ (С3 и легче) - 5-6,5 7-8,5
бутан - бутиленовая фракция - 5,5-9 9-10,5 дебутанизированный бензин (к. к. 205 - 210°С) - 31-32, 36-38 газойль - 50 40
13
консорциум н е д р а
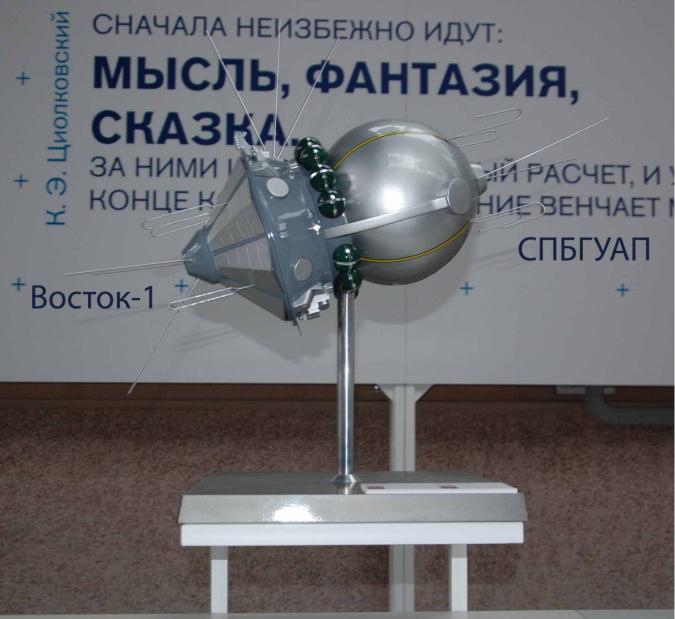
Макет космического корабля «Восток-1» в павильоне «Космос» на ВДНХ. За ним — цитата К. Э. Циолковского:
«Сначала неизбежно идут: мысль, фантазия, сказка. За ними шествует научный расчёт. И уже в конце концов исполнение венчает мысль»
кокс - 3 - 4, 5 - 4, 5-6
Когда хотят достигнуть более глубокого превращения, т.е. получить из сырья больше бензина, подвергают крекингу не только исходное сырье, но и образующиеся в процессе газойлевые фракции. На большинстве промышленных установок каталитическому крекингу подвергают именно смесь исходного сырья с газойлем каталитического крекинга или иногда раздельно свежее сырье и газойлевые фракции. Таким образом газойль возвращается в систему для использования его в качестве вторичного сырья - рециркулятор. В зависимости от того, сколько газойля подвергается каталитическому крекингу, глубина крекинга может достигать 80-90%.
Отношение массы рециркулирующего газойля к массе свежего сырья называется коэффициентом рециркуляции; оно изменяется от нуля до 2,3 при крекинге с рециркуляцией. Глубина крекинга возрастает с увеличением коэффициента рециркуляции.
Характерно, что выход жидких углеводородов, включая фракцию С3-С4, увеличивается до глубины крекинга 80%, а затем снижается. Если же выделить фракцию С3 - С4, то сумма получаемых жидких продуктов по мере увеличения глубины крекинга непрерывно снижается, в данном случае до 62,9 объемн.%. По мере увеличения глубины крекинга выход газойля падает, а при 100% -ной глубине крекинга становится равным нулю.
Объемная скорость. Отношение объема сырья, подаваемого в реактор за 1 ч, к объему катализатора, находящегося в зоне крекинга, называется объемной скоростью. Обычно на одну весовую единицу катализатора, находящегося в зоне крекинга, подается от 0,6 до 2,5 вес. ед. сырья в час. Часто объемную скорость выражают в объемных единицах - объем/ (объем*ч) или м3/ (м3*ч) и записывают в виде ч-1
Кратность циркуляции катализатора. В системах каталитического крекинга с циркулирующим пылевидным или микросферичёским катализатором на 1 т поступающего в реактор сырья вводится 7-20 т регенерированного катализатора, а на установках каталитического крекинга, где применяются крупнозернистые катализаторы (частицы диаметром 3 - 6мм), - от 2 до 5 - 7 т в зависимости от конструкции установки. Указанное отношение (7 - 20 т/т) называют весовой кратностью циркуляции катализатора. Иногда это соотношение выражают в объемных единицах, тогда оно называется объемной кратностью циркуляции катализатора.
Следует различать кратность циркуляции катализатора по свежему сырью и по всей загрузке реактора (свежее сырье плюс рециркулят). В последнем случае при одном и том же количестве катализатора кратность циркуляции будет меньше.
Жесткость крекинга. Известно, что снижение объемной скорости так. же как и увеличение, кратности циркуляции катализатора, способствует повышению выхода бензина и глубины крекинга. Влияние этих параметров на глубину крекинга можно выразить отношением кратности циркуляции к объемной скорости. Это отношение называется фактором жесткости крекинга. Фактор жесткости может быть вычислен по свежему сырью реактора и по суммарной загрузке реактора (свежее сырье плюс рециркулирующий газойль).
Эффективность крекинга. Отношение суммарного выхода (в объемных или весовых процентах) дебутанизированного бензина и фракции С4 к глубине крекинга исходного сырья (в объемных или весовых процентах) именуют эффективностью крекинга. Эффективность (коэффициент) обычно равна 0,75 - 0,8, если она была подсчитана на основе весовых процентов.
В результате каталитического крекинга на установках получают до 15 вес % газа, содержащего водород, аммиак и легкие углеводороды, 30 - 55 вес % высокооктанового компонента автомобильного бензина (или 27 - 50 вес % авиационного бензина), 2 - 9 вес % кокса и легкий и тяжелый газойли. Газ после очистки и газофракционирования используется для технологических или бытовых нужд. Компоненты автомобильного (или авиационного) бензина после стабилизации
14
консорциум н е д р а
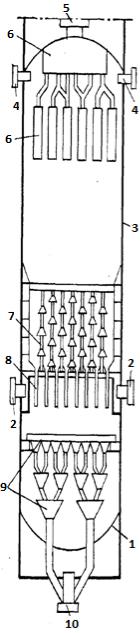
компаундируются с другими компонентами и используются в качестве товарных топлив. Легкий газойль используется как компонент дизельного топлива (при необходимости - после гидроочистки) или, вместе с тяжелым газойлем, как сырье для получения сажи или приготовления сортовых мазутов.
7 Аппаратурное оформление
Рис. 1. Реактор установки каталитического крекинга с шариковым катализатором: 1 - днище; 2 - штуцеры для выхода паров; 3 - корпус; 4 - штуцеры для ввода сырья;5 - штуцер для ввода катализатора: 6 - верхний распределитель катализатора; 7 - патрубки для отвода паров («гирлянды»); 8 - переточные трубы для катализатора; 9 - нижний распределитель катализатора; 10 - штуцер для вывода катализатора.
Реактор отечественной установки каталитического крекинга производительностью 800 т/сутки по свежему сырью представляет собой цилиндрический аппарат из углеродистой стали с внутренней обкладкой из легированной стали диаметром около 4 метра и объемом реакционной зоны 30 - 50 м3. Днища реактора эллиптические. В центре верхнего днища имеется штуцер для подачи катализатора из бункера, смонтированного над реактором. Высота реактора с бункером 41 метр. Штуцер соединяется с верхним распределительным устройством, которое посредством переточных труб равномерно распределяет катализатор по всему сечению реактора. В верхнюю часть реактора через штуцеры вводятся пары сырья. Они равномерно контактируют с катализатором, двигаясь сверху вниз через реакционную зону. Под реакционной зоной находится сепарационное устройство для вывода продуктов реакции - гирлянда патрубков с прорезями, защищенными колпачками от попадания катализатора. Все патрубки нижним открытым концом соединяются со сборной камерой, из которой через штуцеры пары продукта удаляются из реактора. Ниже имеется зона отпарки адсорбированных на катализаторе паров углеводородов водяным паром, подаваемым через специальный штуцер. Закоксованный катализатор выводится из реактора через выравниватель потока.
15
консорциум н е д р а
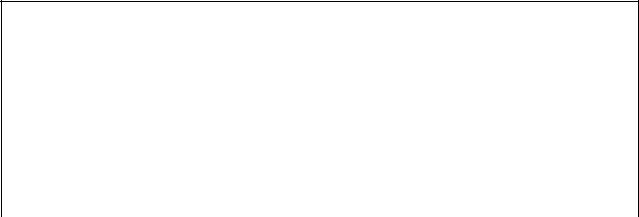
Из реактора в регенератор катализатор перемещается при помощи дымового газа, а из регенератора в реактор - при помощи горячего воздуха. Нижняя часть пневмоподъемника, называемая дозатором, служит для попадания катализатора в поток газа. Скорость газовой струи с катализатором 14 - 20 м/с.
8 Мощность и материальный баланс установок каталитического крекинга.
Мощность установки каталитического крекинга, например, на НПЗ ЛУКОЙЛ в Бургасе составляет 1,7 млн. тонн в год.
Материальный баланс:
Поступило:
Сырье: прямогонный вакуумный газойль |
100% |
Получено: |
|
Углеводородный газ (С1-С4) |
22,4% |
Бензиновая фракция (НК-195°С) |
48,2% |
Легкий газойль (195-280°С) |
9% |
Сырье для производства технического |
9,5% |
углерода (280-420°С) |
|
Тяжелый газойль (выше 420°С) |
3,2% |
Кокс выжигаемый |
6,7% |
Потери |
1% |
16
консорциум н е д р а