
Sysoev_TeorosnovyTMSlekc
.pdf4.6.Перерасчёт размеров и допусков при смене баз
Зачастую размеры в КД не соответствуют условиям техпроцесса и неудобны для измерения. В этих случаях, когда приходится изменять конструкторские базы на измерительные, необходимо пересчитывать размеры и допуски на основе геометрического анализа связей между конструкторскими размерами и принятыми базами.
Пример 1. Изменение конструкторской базы на измерительно-технологиче-
скую.
Условия КД (рис. 4.10): для эксплуатации важны размеры l1; l2; L. При этом размер L имеет небольшой допуск.
Технологические особенности при изготовлении коленчатого вала: размер L измерить трудно, удобнее измерить размеры x/ или x//. Тогда надо задать допуск на x/ ( x//), обеспечивающего соблюдение размера L.
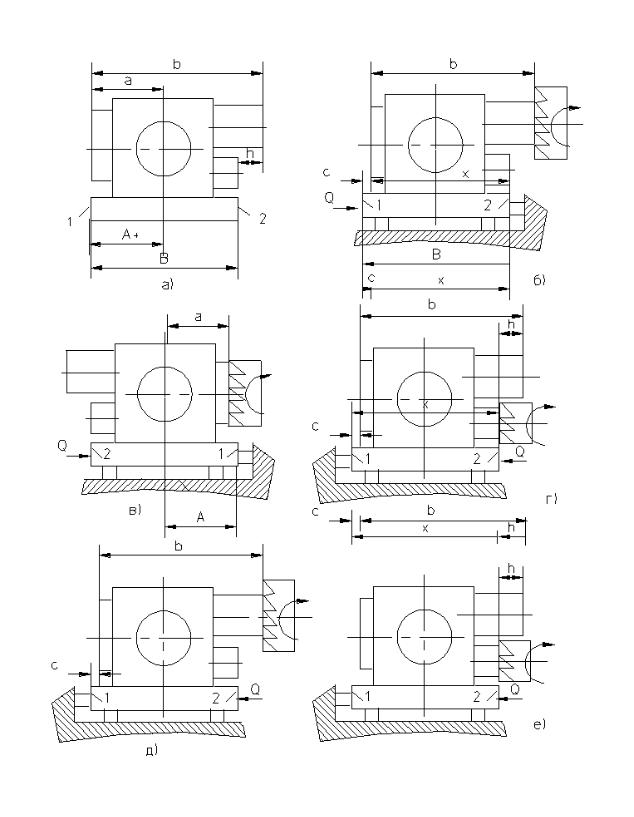
Рис. 4.9. Расчетные технологические схемы обработки корпуса
Решение:
Для размерной цепи

δ |
L |
= δ′l1 |
+ δl2 + δx′, |
|
2 |
2 |
|
|
|
где δL-допуск на замыкающее звено размерной цепи, который должен быть выдержан. Тогда
δ x′ = δ L − δ l1 + δ l 2 . 2
Из этого видно, что допуски на размеры l1 и l2 должны быть меньшими, чем на размер L, а допуск на x/ меньше допуска на δL.
Пример 2. Изменить измерительную и технологическую базу (рис. 4.11).
Условия КД: заданы l1 и l2, т.к. растачиваемые отверстия определяют положение корпуса, установленного сверху.
Задача: найти допуски на новые размеры L1,L2 и H. 1. Из размерной цепи 1, где l1 – замыкающее звено:
δ l1 = δ L1 + δ H = 85 мм.
Например, примем δH=50 мкм;δL1=35 мкм.
2. Из размерной цепи 2, где l2-замыкающее звено:
δl2 = δ L2 + δH/ = 200мкм.
Отсюда δL2=200-50=150 мкм.
Следовательно, при перерасчёте размеров допуски на новые размеры существенно уменьшились.
Пример 3. Изменить измерительную базу (рис. 4.12).
Условия КД: размеры проставлены по цепному способу.
Задача: изменить цепной способ простановки размеров на координатный от единой измерительной базы. Дополнительное условие: каждый размер конструктора является замыкающим звеном и допуски на размеры должны быть выдержаны.
Решение.
1. Из размерной цепи можно принять
δl2=δL1+δL2=50 мкм.
2. Из размерной цепи видно, что
δl4=δL3+δL4=100 мкм, имеем δL3=δL4=100/2=50 мкм.
При найденных допусках L1,L2,L3,L4 допуски на l2 и l4 будут выдер-
жаны.
3. |
Таким образом, допуск на размер L1=25 мкм вместо 800 мкм. |
4. |
Допуск на размер l3: |
|
δL3 +δL2 =25+50=75 мкм вместо 500 мкм. |
Если бы допуски на l1....l4 были одинаковы, то их надо было бы уменьшить примерно в 2 раза.
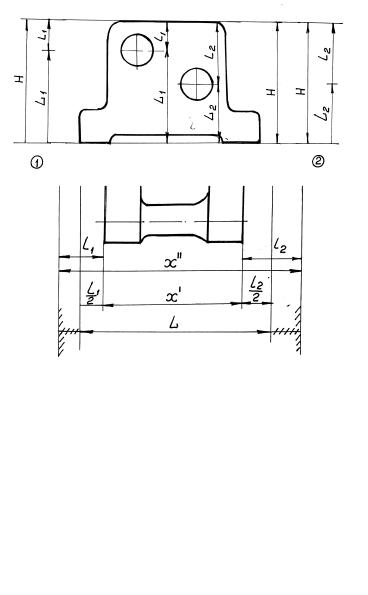
Рис. 4.10. Схема перерасчета размеров коленчатого вала при смене баз
Рис. 4.11. Схема перерасчета размеров корпуса при смене базы
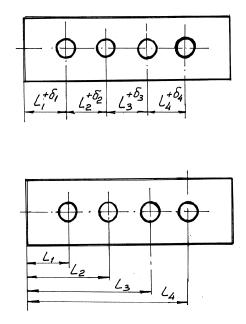
Рис. 4.12. Схема перерасчета размеров при изменении измерительной базы
Вопросы для самопроверки
1.Назовите поверхности заготовки при механической обработке.
2.Дайте определения: база, комплект баз, опорная точка, схема базирования. Приведите примеры обозначения опор, зажимов, рабочих поверхностей.
3.Дайте полную классификацию баз и назовите комплект баз на примерах базирования деталей в табл. 4.4.
4.Почему возникает погрешность изготовления детали, если не соблюдается принцип совмещения баз?
5.В какой последовательности следует выполнять операции?
6.Как уменьшить погрешность изготовления в случае несовмещения
баз?
7.Назовите основные правила при выборе базы для установки заготов-
ки.
8.Как рассчитать погрешность в случае изменения исходной базы?
9.Как рассчитать погрешность при изменении конструкторской базы на измерительную, измерительной базы на технологическую и при смене измерительной базы?
5. ТОЧНОСТЬ ОБРАБОТКИ ДЕТАЛЕЙ
5.1.Основные понятия о точности
Точность обработки (механической, электрофизической и др.) – это степень соответствия размеров и формы заготовки, а также относительного поло-

жения ее поверхностей чертежу. На точность обработки деталей влияет ряд факторов, являющихся следствием движения режующей кромки инструмента по обрабатываемой поверхности:
погрешность настройки, возникающая от неправильного взаимного расположения инструмента и заготовки в начале перехода и неточности настройки технологической системы;
погрешность работы станка, возникающая вследствие неточности кинематической схемы станка, свойств инструмента и заготовки.
Основными причинами погрешности обработки являются: неточности кинематической схемы станка; геометрическая неточность станка в ненагруженном состоянии; неточность режущего инструмента и его износ; деформация упругой системы СПИД;
температурные деформации узлов станка, обрабатываемой заготовки и режущего инструмента; остаточные напряжения заготовки;
неточность измерения в процессе обработки; неточность настройки на размер.
Таким образом, точность механической обработки зависит от большого числа факторов (первичных погрешностей). Характер и степень влияния этих факторов определяется методом обеспечения точности и видом обработки.
При механической обработке на предварительно настроенном станке суммарная погрешность в общем случае складываются из следующих основных первичных погрешностей:
ω = ω |
+ ω + ω + ω + ω + ∑ωФ |
(5.1) |
||
y3i |
y H |
И |
τ |
|
где ωy3i - погрешность, возникающая при установке заготовки;
ωy - погрешность, возникающая в результате упругого отжатия звеньев технологической системы вследствие нестабильности сил резания;
ωH - погрешность настройки станка;
ωИ- погрешность, вызываемая размерным износом режущего инструмента; ωτ - погрешность, вызываемая тепловыми деформациями системы; ∑ωФ - суммарная погрешность формы обработанной поверхности.
Учитывая, что распределение погрешностей ωy, ωy3i и ωH близко к нормальному, распределения погрешностей ωИ и ωτ подчиняются закону равной вероятности, при риске 0,27% формула суммарной погрешности обработки принимает вид:
ω= |
|
+ ∑ωф . |
(5.2) |
ωy23i +ωy2 +ωH2 + 3ωИ2 + 3ωτ2 |
Рассмотрим подробнее факторы, входящие в формулу (5.2).
5.2. Погрешность установки
Погрешность установки - это часть операционной погрешности, связанная с базированием и установкой заготовки на станок или приспособление.
Основными факторами, влияющими на точность установки заготовки являются:
упругие и пластические деформации установочной поверхности заготов-
ки. При установке детали для фрезерования поверхности Б (рис. 5.1) под действием сил зажима Q и силы резания Py происходит упругая и пластическая деформация поверхности Б в месте контакта её с установочными элементами приспособления. Плоскость Б опускается на величину y. Величина деформации зависит от степени шероховатости поверхности, механических свойств материала, величины сил зажима, поэтому:
ω y/ 3i = ymax − ymin .
По экспериментальным данным:
ωy3i=0,005....0,01 мм - при установке на чисто обработанную поверхность; ωy3i=0,05...0,08 мм - при установке на необработанную поверхность.
Для уменьшения ωy3i применяют притирку установочных поверхностей приспособлений и обеспечивают постоянство зажимных сил.
Рис. 5.1. Схема образования погрешности за счёт деформации опорной поверхности
влияние геометрических и динамических неточностей приспособления:
а) силы зажима, возникающие при вращении винта (гидропривода или пневмопривода), образуются силами реакции, действующими от заготовки на губки тисков (рис. 5.2), в результате чего заготовка с губками тисков приподнимается и теряется контакт нижней плоскости с установочными элементами на величину y. Условия закрепления изменяются, поэтому:
ω y 3i =y max −ymin
По экспериментальным данным:
ω//y3i=0,01.....0,02 мм для мало изношенных и малогабаритных тисков;
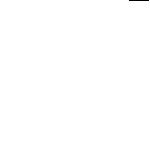
ω//y3i=0,1......0,15 мм для старых тисков и крупных заготовок.
Рис. 5.2. Схема образования погрешности установки от деформации приспособления от сил зажима.
б) при закреплении заготовки в самоцентрирующем патроне возникает смещение оси заготовки на величину l, т.е. при повороте шпинделя будет биение
///y3i=2l, которое приведёт к неконцентричности обработанной цилиндрической поверхности относительно базирующей поверхности.
влияние системы простановки операционных размеров:
1 вариант. База А1,т.е. за базу взята ось валика. Искомая величина О1О2 определяется из треугольника из О1О2К2 (рис.1.5.3)
O1O2 |
= |
|
O1K3 |
|
, |
но O1K3= dD ,aÐO1O2K = a |
||||
|
|
|
|
|||||||
|
|
sin ÐO O K |
|
2 |
2 |
|||||
|
|
|
1 |
2 |
3 |
|
|
|||
тогда |
ωy 3i |
= O1O2 |
= |
δD |
(5.3) |
|||||
α |
|
|||||||||
|
|
|
|
|
|
|
|
2 sin |
|
|
|
|
|
|
|
|
|
|
2 |
|
|
2 вариант. База А2 ( нижняя образующая цилиндрической поверхности). Искомая величина М1М2.
|
M 1M 2 = D - dD + O1O2 |
- D |
|
|||||
|
|
2 |
|
|
|
2 |
|
|
после подстановки: |
|
|
|
|
|
|
|
|
|
|
δ |
|
|
|
|
|
|
ωy 3i |
|
D |
|
1 |
|
|
|
|
= M1 M2 = |
|
|
|
− 1 |
(5.4) |
|||
2 |
α |
|||||||
|
|
|
|
|
|
|
||
|
|
|
|
sin 2 |
|
|
|
3 вариант. База А3 (верхняя образующая цилиндрической поверхности). Искомая величина N1N2
ωy 3i = N1 N2 = |
D |
+ O1O2 − |
D − δD |
|||||
2 |
2 |
|
||||||
|
|
|
|
|
|
|||
|
|
δ |
|
|
|
|
|
|
тогда ωy 3i |
|
|
1 |
|
|
|
||
= |
|
|
|
|
+ 1 |
(5.5) |
||
2 |
|
α |
||||||
|
|
|
|
|
|
|
||
|
|
|
sin 2 |
|
|
|

Сравнение уравнений (5.3…5.5) показывает, что система указания операционного размера оказывает большое влияние на величину погрешности установки заготовки в приспособление, т.к.
ωy33i > ω 1y 3i > ω y23i ,
ас увеличением α до π значения ωy3i уменьшаются, а при уменьшении α-воз- растают.
Рис. 5.3. Схемы к определению погрешности установки цилиндрической заготовки на призме при различных схемах простановки операционного размера
влияние схемы установки заготовки.
В общем случае (рис. 5.4) погрешность установки заготовки в приспособлении на призму - это проекция разности предельных расстояний исходной базы относительно установочных элементов приспособления на направление заданного размера.
Решим задачу: фрезеровать площадку на валике с Д-δД. Исходная база - ось детали:
А) Схема а) (β=0): ωy3i= |
|
D |
|
|
|
|
|
|
|
α . Формула аналогична (5.3). |
|||||||
|
2 sin |
|
|
|
|
|
|
|
|
|
2 |
|
|
|
|
|
|
Б) Схема б) (β=45°, α=90°): |
ωy 3i = |
δD |
|
|
cos45 = |
δD |
|
|
2 sin |
90 |
|
2 . |
|||||
|
|
|
||||||
|
|
|
2 |
|
|
|
|
|
|
|
|
|
|
|
|
|
Рис. 5.4. Влияние схемы установки цилиндрической заготовки на призме на величину погрешности установки.
В) Схемы в) (β=90°): ωy3i=0.
Если исходная база - нижняя образующая, то:
|
|
|
|
|
|
|
|
|
|
|
δD |
|
1 |
|
|
ω |
|
= |
|
− 1 cos β , |
(5.6) |
||
|
|
α |
|||||
|
y 3i |
|
2 |
|
|||
|
|
|
|
sin 2 |
|
|
а если – верхняя образующая, то
|
|
|
|
|
|
|
|
|
|
|
δD |
|
1 |
|
|
ω |
|
= |
|
+ 1 cos β |
(5.7) |
||
|
|
α |
|||||
|
y 3i |
|
2 |
|
|||
|
|
|
|
sin 2 |
|
|
Если β=0, то из (5.6) получим (5.4), а из (5.7)→ (5.5), следовательно, приведенные расчётные случаи могут быть использованы для анализа влияния систем простановки операционных размеров и для других случаев.
влияние неточности размеров и формы базирующей поверхности.
а) Задача: прошлифовать наружную поверхность втулки (рис. 5.5) с установкой заготовки по отверстию на оправке с зазором.
Максимальная величина зазора:
Smax = Smin + δопр + δD,
где Smin - минимальный зазор, гарантирующий возможность одевания втулки на оправку; δопр - допуск на диаметр оправки; δD - допуск размер базирующей поверхности.