
Сернокислотное алкилирование изобутана олефинами
.pdfПути повышения технико-экономических показателей работы установок процесса сернокислотного алкилирования изобутана олефинами
Введение На крупных нефтеперерабатывающих заводах в технологической схеме переработки нефти имеется установка сернокислотного
алкилирования изобутана алкенами С3 – С5 для получения высокооктанового компонента автобензина – алкилата.
Известно, что бензины с каталитических крекингов и, в особенности, каталитических риформингов содержат до 70% ароматических углеводородов, которые не только ухудшают пусковые свойства бензинов, но и являются экологически вредными компонентами, поэтому во всем мире внесены изменения в стандарты на бензин по уменьшению содержания в них аренов. Алкилат, в основном состоящий из изооктана, наряду с полимер-бензином и изомеризатом является ценным компонентом бензинов, повышающим их качество по указанным показателям. Процесс сернокислотного алкилирования давно известен и хорошо освоен. Современные алкилирующие установки позволяют получать алкилат с минимальными затратами энергоресурсов и реагентов. На Куйбышевском НПЗ успешно работает модернизированная установка типа 24-36.
Процесс алкилирования изопарафинов олефинами предназначен для получения высокооктановых добавок к бензинам. Бензины – алкилаты, состоящие из разветвленных парафиновых углеводородов, главным образом, из изооктанов, удовлетворяют самым строгим современным требованиям, предъявляемым к бензинам новых поколении. Они имеют высокое октановое число (96 по исследовательскому методу)- не содержат бензола, не токсичны. имеют низкое давление насыщенных паров, следовательно. мало испаряются при хранении и транспортировке. практически не содержат серы. Поэтому понятно, что алкилирование в настоящее время является одним из направлений развития нефтепереработки, где за последние годы появилось наибольшее число новых технологий. Доля алкилатов в составе бензинов в мире составляет около 8%, в США она достигла 13% и в ближайшие годы может быть на уровне 20-25%, доля алкилата в товарных бензинах России в настоящее время менее 1%.
Повышение глубины переработки нефти приведет к увеличению ресурсов нефтезаводских газов, богатых олефинами. Вовлечение нефтезаводских олефинов в химическую переработку с целью дополнительного получения моторных топлив является актуальной задачей
2
Консорциум н е д р а |
Консорциума Н е д р а |
отечественной и мировой нефтепереработки. Поэтому структурная перестройка нефтеперерабатывающей промышленности России потребует резкого наращивания мощностей алкилирования.
1. Теоретические основы процесса
1.1 Сырье и продукты процесса
Сырьем сернокислотного алкилирования является бутан-бутиленовая фракция. Она состоит из углеводородов С4 на 80-85%,
остальное - примеси углеводородов С3 и С5; ее получают с АГФУ. Желательно, чтобы на каждый 1% бутилена приходилось 1,2% изобутана.
Пропан и бутан, содержащиеся в сырье, хотя и не вступают в реакцию, но оказывают влияние на процесс, так как занимают объем в реакционной зоне и снижают содержание изобутана. Для улучшения условий алкилирования из сырья необходимо как можно полнее удалять нормальные парафины, для чего на установках алкилирования имеются бутановая и пропановая ректификационные колонны.
Всырье не должно содержаться этилена и бутадиена, так как они при контакте с серной кислотой образуют этил- и бутилсульфаты и полимеры олефинов, которые, растворяясь в кислоте, разбавляют ее. Нежелательно присутствие в сырье воды, серо- и азоторганических соединений.
Втаблице 1 дана характеристика сырья по основным показателям качества [8]
Таблица 1
Показатели качества и |
Бутан- |
Бутан-бутиленовая |
|
Изобутановая |
|
||||||
нормы |
бути- |
фракция по ТУ |
|
|
фракция по ТУ |
|
|||||
|
леновая |
|
|
|
|
|
|
|
|
|
|
|
фракция |
|
|
|
|
|
|
|
|
|
|
|
СТП |
Высшая |
А |
|
Б |
Высшая |
|
А |
Б |
|
В |
1. Углеводородный |
|
|
|
|
|
|
|
|
|
|
|
состав, |
|
|
|
|
|
|
|
|
|
|
|
% масс: |
|
|
|
|
|
|
|
|
|
|
|
а) сумма |
- |
- |
- |
|
- |
- |
|
- |
- |
|
- |
углеводородов |
|
|
|
|
|
|
|
|
|
|
|
С1-С2 |
|
|
|
|
|
|
|
|
|
|
|
|
|
|
|
|
|
3 |
|
|
|
|
Консорциум н е д р а |
Консорциума Н е д р а |
б) сумма |
4,5 |
0,5 |
|
3,0 |
|
5,0 |
|
- |
|
- |
|
- |
|
- |
|
|
углеводородов |
|
|
|
|
|
|
|
|
|
|
|
|
|
|
|
|
С3, не более |
|
|
|
|
|
|
|
|
|
|
|
|
|
|
|
|
в) пропан, не более |
- |
- |
|
- |
|
- |
|
1,3 |
|
1,5 |
|
4,5 |
|
8,0 |
|
|
г) изобутан, не |
- |
- |
|
- |
|
- |
|
98,0 |
|
97,0 |
|
90,0 |
|
70,0 |
|
|
менее |
|
|
|
|
|
|
|
|
|
|
|
|
|
|
|
|
д) сумма бутиленов |
- |
<40 |
|
<35 |
|
<25 |
|
>0,5 |
|
>0,5 |
|
>0,5 |
|
не |
|
|
|
|
|
|
|
|
|
|
|
|
|
|
|
|
норм |
|
|
е) нормальный |
- |
- |
|
- |
|
- |
|
0,7 |
|
2,0 |
|
6,0 |
|
не |
|
|
бутан |
|
|
|
|
|
|
|
|
|
|
|
|
|
норм |
|
|
не более |
|
|
|
|
|
|
|
|
|
|
|
|
|
|
|
|
|
|
|
|
|
|
|
|
|
|
|
|
|
|
|
|
продолжение таблицы 1 |
ж) сумма |
6,0 |
1,0 |
|
3,0 |
|
6,0 |
|
отс. |
|
отс. |
|
0,5 |
|
1,0 |
|
|
углеводородов |
|
|
|
|
|
|
|
|
|
|
|
|
|
|
|
|
С5 и выше |
|
|
|
|
|
|
|
|
|
|
|
|
|
|
|
|
з) дивинил |
- |
не |
|
не |
|
не |
|
- |
- |
|
- |
|
- |
|
|
|
|
|
норм |
|
норм |
|
норм |
|
|
|
|
|
|
|
|
|
|
2. Содержание H2S и |
0,02 |
0,015 |
|
0,02 |
|
0,02 |
|
0,005 |
0,005 |
|
0,005 |
|
0,01 |
|
|
|
меркап- |
|
|
|
|
|
|
|
|
|
|
|
|
|
|
|
|
тановой серы, % масс., |
|
|
|
|
|
|
|
|
|
|
|
|
|
|
|
|
не более |
|
|
|
|
|
|
|
|
|
|
|
|
|
|
|
|
3. Содержание |
- |
отс. |
|
отс. |
|
отс. |
|
отс. |
|
отс. |
|
отс. |
|
отс. |
|
|
свободной |
|
|
|
|
|
|
|
|
|
|
|
|
|
|
|
|
воды и щелочи |
|
|
|
|
|
|
|
|
|
|
|
|
|
|
|
|
В случае присутствия последних сырье защелачивают и до контакта с серной кислотой удаляют из него воду. Это способствует снижению расхода серной кислоты. Большое значение имеют также содержание и состав олефинов в сырье. При алкилировании изобутана бутиленами в присутствии низших олефинов увеличивается расход кислоты и снижается октановое число алкилата. Высшие олефины склонны к образованию полимеров, что также снижает октановую характеристику алкилата.
4
Консорциум н е д р а |
Консорциума Н е д р а |
Бутадиен действует как разбавитель, то 1 кг его разбавляет 58 кг 98%-ной серной кислоты до 90%-ной концентрации. Поэтому
содержание бутадиена во фракции С4 не должно превышать нескольких долей процента.
При наличии в сырье меркаптанов и сероводорода увеличивается расход кислоты: 1 кг этих примесей разбавляет 65 кг 98%-ной кислоты до 90%-ной концентрации. Аналогично 1 кг воды, поступающей с углеводородами в реактор, разбавляет 11 кг кислоты в тех же
пределах концентрации.
Поэтому желательно удаление из сырья и таких примесей. Для снижения содержания сернистых соединений обычно проводят одно-
или двухступенчатую щелочную очистку сырья до реактора, а для освобождения от воды - отстой предварительно охлажденного до 10-12°С
сырья в специальных отстойниках и последовательную очистку его адсорбентами (например, алюмогелем) [1].
Алкилат является ценным компонентом высококачественных бензинов, так как состоит из парафиновых углеводородов изостроения,
отличающихся высокой детонационной стойкостью, хорошей приемистостью к ТЭС, незначительным различием значений октанового числа
(определяемого разными методами) и малым нагарообразованием. Применение алкилатов для этой цели делает алкилирование одним из важнейших процессов современной нефтепереработки. Их качество и выход зависят от состава олефинового сырья, условий процесса и типа
катализатора.
В таблице 2 приведены результаты алкилирования изобутана различными олефинами в следующих условиях [3]:
содержание изо-C4H10 в реакционной зоне – 40-80% (об.);
отношение изо-С4Н10 к олефинам 3-12 : 1;
температура в реакторе 2-15 °С;
объемная скорость подачи олефина 0,1- 0,6 ч-1;
содержание H2SO4 в эмульсии 40-60% (масс.).
Таблица 2
Показатели |
|
Олефины |
|
|
|
|
|
|
|
|
C3H6 |
C3H6(40%) |
C4H8 |
C5H10 |
|
|
5 |
|
Консорциум н е д р а |
Консорциума Н е д р а |
|
|
C4H8(60%) |
|
|
|
Выход алкилата. % (об.) |
178 |
174 |
172 |
160 |
|
на олефины |
|||||
|
|
|
|
||
Расход изобутана. % (об.) |
127 |
117 |
11 |
96 |
|
на олефины |
|||||
|
|
|
|
||
Октановое число алкилата |
|
|
|
|
|
|
|
|
|
|
|
по ИМ |
89-92 |
92-95 |
94-97 |
90-93 |
|
|
|
|
|
|
|
по ММ |
87-90 |
90-93 |
92-94 |
90-92 |
|
|
|
|
|
|
Зарубежные, а также отечественные данные показывают, что наилучшие результаты достигаются при алкилировании изобутана бутенами. Однако из-за недостатка сырья для процессов алкилирования приходится использовать пропилен и в некоторой степени амилены.
Анализ данных о процессе алкилирования сырья с различным содержанием пропилена показывает, что даже в случае использования сырья с
97% пропилена можно получить алкилат удовлетворительного качества (октановое число по ИМ 88,6). Однако это достигается изменением режима, особенно температуры и концентрации серной кислоты в эмульсии, а также значительным увеличением ее расхода. Кроме указанных выше продуктов имеется и отработанная кислота, которую используют для очистки других продуктов или регенерируют (в новых проектах - прямо на установках алкилирования).
1.2 Химические реакции, протекающие в процессе сернокислотного алкилирования изобутана олефинами
Процесс сернокислотного алкилирования состоит из следующих стадий: подготовки сырья, реакции алкилирования, нейтрализации и ректификации продуктов реакции.
Реакции алкилирования изопарафиновых углеводородов олефинами в общем виде описываются уравнением:
CnH2n+2+CmH2m → Cn+mH2[(n+m)+2]
6
Консорциум н е д р а |
Консорциума Н е д р а |
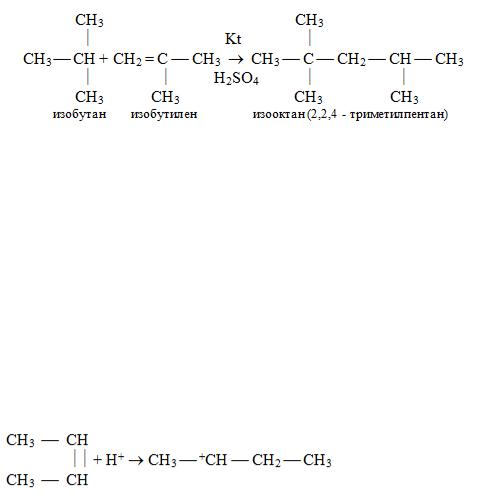
Из парафиновых углеводородов наиболее активно вступает в реакции алкилирования изобутан.
Реакция алкилирования изобутана изобутиленом может быть представлена в следующем виде [3, 7]:
Большинство исследователей считают, что для объяснения первичных реакций, протекающих при алкилировании, наиболее вероятным является предположение о цепном характере реакции алкилирования. Реакция инициируется взаимодействием небольших порций олефина с протоном кислоты. Возникающий ион реагирует с изопарафином и получается новый ион и парафин, образующийся из олефина (вторая стадия реакции). Третья стадия – присоединение нового иона ко второй молекуле олефина с образованием иона большего молекулярного веса.
В четвертой стадии происходит перегруппировка этого иона за счет миграции вдоль основной углеродной цепи атома водорода или метильной группы. Пятая (последняя) стадия взаимодействия этих ионов с изопарафином по третичной углеводородной связи с образованием конечных продуктов реакции и новых карбоний – ионов, способных продолжать цепь.
Для случая алкилирования изобутана бутеном – 2 механизм реакции по этой теории можно представить следующим образом:
Первая стадия:
Вторая стадия:
7
Консорциум н е д р а |
Консорциума Н е д р а |
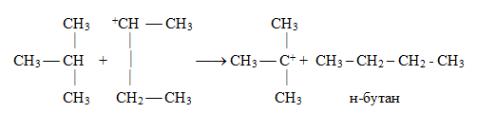
Третья стадия:
8
Консорциум н е д р а |
Консорциума Н е д р а |
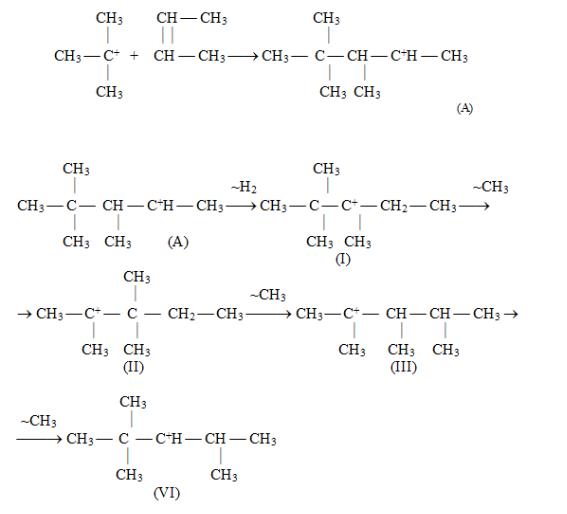
Четвертая стадия *: Знак ~ указывает на миграцию группы СН3 или атома водорода.
Пятая стадия:
9
Консорциум н е д р а |
Консорциума Н е д р а |
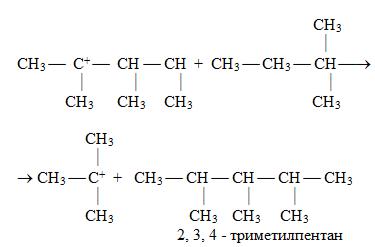
Сизобутаном в первую очередь реагируют третичные высокомолекулярные карбоний-ионы (I, II, IV), а затем вторичные.
1.3Термодинамика и кинетика реакций, протекающих в процессе сернокислотного алкилирования изобутана олефинами
Для кислотно-каталитического алкилирования изопарафинов ациклическими олефинами имеется ряд общих факторов, определяющих
выход и качество алкилатов:
-несмотря на то, что алкилирование н-бутана и изобутаиа термодинамически равновероятно, в реакции кислотно-каталитического алкилирования вступают только изопарафины, имеющие третичный атом углерода;
-лишь сильные кислоты обеспечивают переход гидрид-иона, причем скорость таких переходов снижается с уменьшением концентрации кислоты;
-олефиновые углеводороды хорошо и быстро растворяются в кислотах, что способствует протеканию побочных реакций,
ухудшающих качество алкилатов, поэтому первоначальное содержание олефинов в реакционной среде должно быть минимальным;
10
Консорциум н е д р а |
Консорциума Н е д р а |
- плохая растворимость парафинов в кислотах требует высокой степени диспергирования реакционной массы с целью создания максимально большей границы раздела кислотной и углеводородной фаз, на которой и протекают реакции перехода гидрид-ионов,
лимитирующие скорость образования целевых продуктов алкилирования;
- селективность реакций алкилирования изопарафинов тем выше, чем ниже температура реакционной смеси.
Реакции алкилирования изопарафинов олефинами протекают с выделением значительного количества теплоты, необходимость отвода которой следует учитывать при проектировании реакторных устройств. Установленные экспериментально значения тепловых эффектов реакций алкилирования изобутана различным олефиновым сырьем представлены в таблице 1.
Расчетным путем тепловой эффект реакции для любого состава олефинового сырья определяют по уравнению [7]:
∆ = 1∆1 + 2∆2 + + ∆
где ∆ - общий тепловой эффект реакции алкилирования изобутана смесью олефинов; ∆1 (∆2, ∆ - частные тепловые эффекты реакций алкилирования изобутана индивидуальными олефинами смеси; 1, 2, - массовые концентрации индивидуальных олефинов в сырье, % от их суммы.
Частные тепловые эффекты рассчитывают по уравнению:
∆ |
= ∆′ |
|
+ ∆′′ |
|
+ ∆′′′ |
|
|
|
100 |
||||
1 |
1 100 |
1 100 |
1 |
Таблица 2
Экспериментальные значения тепловых эффектов (∆) реакций алкилирования изобутана олефинами
Олефины |
Мольное соотноше- |
Тепловой |
эффект |
|
ние изобутан/олефин |
реакции, |
кДж/моль |
|
|
олефина |
|
Изобутилен |
3:1* |
67 |
|
|
|
|
|
Диизобутилен |
2:1* |
57 |
|
|
|
|
|
|
|
11 |
|
Консорциум н е д р а |
Консорциума Н е д р а |