
гидроочистки дизельных фракций
.pdf11
Таблица 1.3
Результат гидроочистки [9]
Наименование |
Показатели качества фракции |
Показатели качества гидрогенизата |
|||||
фракции |
|
|
|
|
|
|
|
содержание серы, % масс. |
содержание олефиновых углеводородов, % масс. |
содержание ароматических углеводородов, % масс. |
содержание серы, % масс. |
содержание олефиновых углеводородов, % масс. |
содержание ароматических углеводородов, % масс. |
||
|
|||||||
|
|
|
|
|
|
|
|
Прямогонная |
|
|
|
|
|
|
|
дизельная |
0,78 |
0,99 |
5,16 |
0,049 |
0,56 |
3,23 |
|
фракция |
|
|
|
|
|
|
|
|
|
|
|
|
|
|
|
|
|
|
2. Технологические установки процесса |
На отечественных нефтеперерабатывающих предприятиях гидроочистку средних дистиллятов проводят преимущественно на установ-
ках Л-24-5, Л-24-6, Л-24-7, ЛЧ-24-2000 и ЛК-6У.
Таблица 2.1
Характеристики установок дизельного топлива
Показатели |
|
Установка |
|
||
|
|
|
|
||
Л-24-5 |
Л-24-6 |
Л-24-7 |
ЛК-6У |
||
|
|||||
|
|
|
|
|
|
Мощность, тыс. т/год |
900 |
900 |
1200 |
2000 |
|
|
|
|
|
|
|
Давление, МПа |
5 |
5 |
4 |
5,8-6 |
|
|
|
|
|
|
|
Температура, ºС |
380-425 |
380-425 |
380-400 |
370-400 |
|
|
|
|
|
|
|
Кратность циркуляции ВСГ, |
400-500 |
500-600 |
400 |
400 |
|
нм3/нм3 сырья |
|||||
|
|
|
|
||
Объемная скорость подачи |
1,5 |
1,5-2,6 |
3-3,5 |
4,3-5 |
|
сырья, ч-1 |
|||||
|
|
|
|
||
Длительность межрегенераци- |
4-6 |
6-10 |
7 |
12 |
|
|
|
|
|
|
Консорциум н е д р а |
Консорциума Н е д р а |

12
онного цикла, мес.
Рассмотрим, например, установку ЛЧ-24-2000 (рис 2.1).
Сырье смешивается с циркуляционным водородсодержащим газом, нагнетаемым центробежным компрессором. Газо-сырьевая смесь нагревается сначала с теплообменниках потоком стабильного топлива, поступающего из нижней части стабилизационной колонны, затем в теплообменнике потоком газо-продуктовой смеси, в печи и направляется в реактор. После реактора газо-продуктовая смесь отдает свое тепло газо-сырьевой смеси и подается в горячий сепаратор. Парогазовая смесь из горячего сепаратора используется для нагрева гидрогенизата из холодного сепаратора и получения водяного пара в рибойлере. Затем смесь газа и нефтепродукта охлаждается последовательно в воздушном и водяном холодильниках и поступает в холодный сепаратор, где выделяется циркуляционный водородсодержащий газ. Гидрогенизат из холодного сепаратора, предварительно нагретый в теплообменнике парогазовой смесью из горячего сепаратора, и направляется в колонну стабилизации.
Циркуляционный газ подвергается очистке от сероводорода и возвращается в цикл. Для поддержания нужной концентрации водорода в циркуляционном газе перед сепаратором на компрессор постоянно подается свежий водородсодержащий газ, а часть циркуляционного газа отдувается. Отдуваемый ВСГ, предварительно нагретый в подогревателе печи, направляется в стабилизационную колонну с целью снижения парциального давления паров нефтепродукта. В колонне из дизельного топлива выделяются углеводородные газы и бензин для получения дизельного топлива с требуемой температурой вспышки. Тепловой режим колонны обеспечивается теплотой сырья, подаваемого в стабилизационную колонну. Выходящее из нижней части колонны стабильное дизельное топливо охлаждается в теплообменниках и воздушном холодильнике, после чего выводится с установки. С верха колонны отбирается бензин и углеводородный газ; после охлаждения они поступают в сепаратор, в котором бензин отстаивается от водного конденсата.
Очистка бензина от сероводорода осуществляется путем его продувки в колонне очищенным углеводородным газом. Водяной конденсат направляется в деаэратор для отдува сероводорода водяным паром. Конденсат, освобожденный от сероводорода, после охлаждения сбрасывается в производственную канализацию, а сероводород – в факельную линию.
Углеводородный газ очищается от сероводорода раствором МЭА и используется в качестве топлива для печи. Насыщенный кислыми газами раствор МЭА дегазируется при пониженном давлении и направляется на десорбцию в отгонную колонну. Температурный режим в колонне поддерживается циркулирующим через термосифонный шаровой рибойлер раствором МЭА. Образующийся сероводород выводится с установки для получения серной кислоты или элементарной серы. Механические примеси удаляются из части регенерированного раствора МЭА. Для предотвращения вспенивания раствора МЭА на тарелках абсорберов в систему подается антивспениватель.
При падении активности катализатора проводится его газовоздушная регенерация по замкнутому циклу с применением содового рас-
твора [1, c.62-64].
Консорциум н е д р а |
Консорциума Н е д р а |
13
Основное оборудование установки следующее:
−реактор со стационарным слоем катализатора;
−трубчатая печь вертикально-секционного типа, состоящая из двух секций, каждая из которых имеет радиантную и конвекционную камеры; в конвекционной части расположен змеевик нагрева газа для поддува в стабилизационную колонну;
−сырьевой теплообменник кожухотрубчатый с плавающей головкой, одноходовой; уплотнение – сильфонный компенсатор; диаметр корпуса 1300 мм;
−воздушные холодильники типа АВГ с коэффициентом оребрения 22;
−стабилизационная колонна с клапанными тарелками, число тарелок – 25;
−колонны очистки циркуляционного и углеводородного газа стабилизации, а также отгонная колонна с S-образными тарелками;
−насадочный абсорбер для очистки углеводородного газа, поступающего из колонны отдува бензина, и насадочная колонна отдува бензина; в качестве насадки используются седля Инталокс [1, c.64-65].
Консорциум н е д р а |
Консорциума Н е д р а |
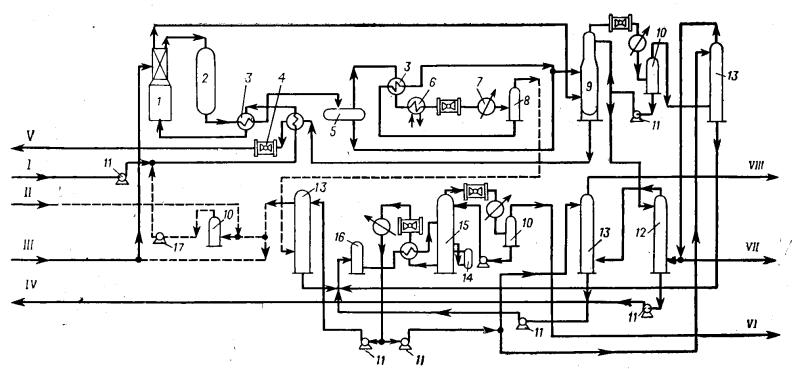
Принципиальная технологическая схема установки Л-24-2000
Рис. 4.1
1 – трубчатая печь, 2 – реактор, 3 – теплообменники, 4 – воздушный холодильник, 5 – горячий сепаратор, 6 – теплообменник для получения пара, 7 – холодильники, 8 – холодный сепаратор, 9 – стабилизационная колонна, 10 – сепараторы, 11 – насосы, 12 – колонна для отдува сероводорода из бензина, 13 – абсорберы, 14 – термосифонный рибойлер, 15 – отгонная колонна, 16 – дегазатор, 17 – центробежный компрессор
Линии: I – сырье, II – водородсодержащий газ, III – углеводородный газ (или отдуваемый ВСГ), IV – бензин, V – очищенное дизельное топливо, VI – сероводород, VII – углеводородный газ с установки, VIII – углеводородный газ к печам
|
14 |
Консорциум н е д р а |
Консорциума Н е д р а |
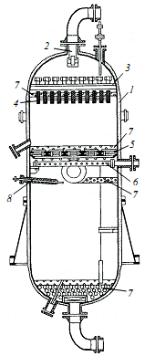
15
Двухсекционный реактор гидроочистки дизельного топлива (рис. 2.2) представляет собой вертикальный цилиндрический аппарат с эллиптическими днищами. Корпус реактора выполнен из двухслойной стали 12ХМ и 08Х18Н10Т. Верхний слой катализатора засыпают на колосниковую решетку, а нижний – на фарфоровые шарики, которыми заполняют сферическую часть нижнего днища. Для отвода избыточного тепла реакций под колосниковой решеткой вмонтирован коллектор для подачи холодного ВСГ. Сырье, подаваемое через штуцер в верхнем днище, распределяют по всему сечению и сначала для задерживания механических примесей пропускают через фильтрующие устройства, состоящие из сетчатых корзин, погруженные в верхний слой катализатора. Промежутки между корзинами заполняют фарфоровыми шарами. Газосырьевую смесь пропускают через слой катализатора в обеих секциях и по штуцеру нижней секции выводят из реактора [8, с. 776].
Реактор гидроочистки дизельного топлива
1 – корпус, 2 – распределитель и гаситель потока, 3 – распределительная непровальная тарелка, 4 – фильтрующее устройство, 5 – опорная колосниковая решетка,
6 – коллектор ввода водорода, 7 – фарфоровые шары, 8 - термопара
Консорциум н е д р а |
Консорциума Н е д р а |
16
Рис. 2.2
3.Современные требования к качеству дизельных топлив
Впоследнее десятилетие во многих странах предъявляются все более жесткие требования к качеству моторных топлив. Например, в США и государствах, входящих в Европейский Союз, действуют стандарты, согласно которым в топливах резко ограничивается содержание сернистых соединений. Так, в соответствии с Европейским стандартом EN 590:2010, содержание сернистых соединений (в пересчете на серу) в дизельных топливах и бензинах не должно превышать 10 ppm (мг серы/кг топлива). Это связано с тем, что повышенное содержание сернистых соединений приводит к коррозии оборудования и увеличению выбросов оксидов серы в атмосферу при сгорании топлива.
Еще одной важной характеристикой дизельных топлив является содержание в них ароматических соединений. Дело в том, что повышенное содержание ароматических углеводородов ухудшает экологические и технологические свойства топлив: увеличивается склонность
кнагарообразованию, повышаются выбросы твердых частиц в атмосферу. Кроме того, ароматические соединения обладают высокой токсичностью.
ВРоссии ежегодно производится порядка 70 млн. тонн дизельного топлива, половина которого потребляется внутри страны. Техническим регламентом, принятым в 2011 г. Таможенным союзом (Россия, Белоруссия и Казахстан), установлены требования, предъявляемые к различным видам топлив на территории этих стран, а также определены сроки перехода на выпуски топлива определенного класса. С 1 января 2013 года все дизельное топливо, выпускаемое в обращение на территории России, должно иметь показатели не ниже Класса 3 (аналог Евро-3): содержать не более 350 ppm серы и не более 11% масс. полициклических ароматических соединений, а также иметь цетановое число не ниже 51 (для летних сортов) (таблица 3.1) [5].
Таблица 3.1
Требования к характеристикам дизельного топлива
Показатели |
|
Нормы в отношении класса |
|
||
|
|
|
|
||
Класс 2 |
Класс 3 |
Класс 4 |
Класс 5 |
||
|
|||||
|
|
|
|
|
|
Цетановое число для летнего |
45 |
51 |
51 |
51 |
|
дизельного топлива, не менее |
|||||
|
|
|
|
||
|
|
|
|
|
|
Массовая доля серы, не более |
500 ppm |
350 ppm |
50 ppm |
10 ppm |
|
|
|
|
|
|
|
Массовая доля полицикличе- |
|
|
|
|
|
ских ароматических углево- |
- |
11 % масс. |
11 % масс. |
8 % масс. |
|
дородов, не более |
|
|
|
|
|
|
|
|
|
|
Консорциум н е д р а |
Консорциума Н е д р а |
17
4. Производство экологически чистых дизельных топлив
Развитие технологии процесса гидроочистки среднедистиллятного сырья до содержания серы в гидрогенизате 10 млн-1 идет по двум направлениям.
Первое направление – двухступенчатое гидрирование сырья, при котором сначала осуществляется гидроочистка до остаточного содержания серы 50-100 млн-1 в присутствии сероустойчивого катализатора, а затем – дополнительное гидрирование на автономном блоке деароматизации в присутствии «благородного» платинового катализатора. Процесс, как правило, проводится при давлении 3-5 МПа, температуре 240-340ºС, объемной скорости подачи сырья 0,5-1,0 ч-1. Типичным представителем такого типа процессов является Unicap (компания
UOP).
Второе направление – одноступенчатое (в отдельных случаях - двухступенчатое) гидрирование на сероустойчивых катализаторах, как правило, никельмолибденовых или никельвольфрамовых. Этот вид процесса осуществляют при давлении 5-10 МПа, температуре 320-420ºС, объемной скорости подачи сырья 0,5-1,0 ч-1. К числу таких процессов относится Sincat (компаний «Criterion» и «Lummus») [6, c.191].
Учитывая практические аспекты производства дизтоплива со сверхнизким содержанием серы, можно сделать следующие выводы.
1.Происходят изменения спецификаций (технических условий на качество) дизтоплива России. При этом основной целью является снижение содержания серы. Перспективы изменения цетанового числа, плотности, температуры выкипания 95%-й фракции и т.д. могут оказаться не такими уж отдаленными. Явным доказательством работы в этом направлении является Технический регламент, требования к дизельному топливу в котором значительно повышены.
2.Возможность реконструкции существующей установки для производства дизельного топлива со сверхнизким содержанием серы (ДСНС) будет во многом зависеть от ее устройства и рабочих условий. Многие НПЗ могут найти, что большая реконструкция их существующей одноступенчатой установки не является самым практичным решением по производству ДСНС. Для многих более выгодной будет реконструкция с интеграцией второй стадии или со строительством новой установки в качестве второй для доочистки [6, c. 193].
3.Актуальна разработка и внедрение новых видов катализаторов, обеспечивающих сверхнизкое содержание серы.
4. Более жесткий режим работы, необходимый для производства ДСНС, может отрицательно повлиять на его выход и привести к повышенному потреблению энергоносителей.
5. При производстве ДСНС НПЗ фактически придется производить топливо для транспорта, аналогичное химически чистым продуктам. Поэтому работа на установке станет намного сложнее.
Все вышеперечисленное существенно повлияет на НПЗ и инфраструктуру системы распределения. Потребуются дополнительные резервуары, утилизация отходов, загрузка (выгрузка) катализаторов, методы распределения и т.д.
Консорциум н е д р а |
Консорциума Н е д р а |
18
В заключение стоит отметить, что производство ДСНС будет сложным и дорогостоящим. Решение каждого НПЗ и его расходы будут разными. НПЗ будут вынуждены работать с поставщиками технологий и катализаторов, чтобы выработать решения, которые дадут максимальную гибкость для удовлетворения постоянно изменяемых и все более жестких технических условий на дизельное топливо [6, c.194].
Библиографический список
1.Аспель Н. Б., Демкина Г. Г. Гидроочистка моторных топлив. Л., «Химия», 1977.
2.Справочник нефтепереработчика: Справочник/Под ред. Г.А. Ластовкина, Е.Д. Радченко и М.Г. Рудина. – Л.: Химия, 1986. – 648 с.,
ил.
3. Суханов В. П. Каталитические процессы в нефтепереработке. М.: Химия, 1979. – 344 с.
4. Орочко Д. И., Сулимов А. Д. Гидрогенизационные процессы в нефтепереработке. Л.: Химия, 1971.
5.Технический регламент «О требованиях к автомобильному и авиационному бензину, дизельному и судовому топливу, топливу для реактивных двигателей и мазуту». Утвержден постановлением Правительства РФ от 27.02.2008 г. №118.
6.Капустин В.М., Гуреев А.А. Технология переработки нефти. В 2 ч. Часть вторая. Деструктивные процессы. – М.: КолосС, 2007. – 334
с.: ил.
7.Смидович Е.В. Технология переработки нефти и газа. Ч. 2-я. Крекинг нефтяного сырья и переработка углеводородных газов. 3-е изд., пер. и доп. – М.: Химия, 1980 г. – 328 с., ил.
8.Ахметов С.А. и др. Технология и оборудование процессов переработки нефти и газа: Учеб. пособие / С.А. Ахметов, Т.П. Сериков, И.Р. Кузеев, М.И. Баязитов; Под ред. С.А. Ахметова. – СПб.: Недра, 2006. – 868 с.; ил.
9.«Нефтехимия», 2013, том 53, №3, с. 199-202
Консорциум н е д р а |
Консорциума Н е д р а |