
- •CHAPTER - 1
- •PIPING MATERIAL SELECTION & CHARACTERISTICS
- •1. Pipe Material Selection
- •1.1. Selection Criteria
- •1.1.1. Service Life
- •1.1.2. Code Requirements
- •1.1.3. Allowable Stresses
- •1.1.4. Design Temperature
- •1.1.5. Design Pressure
- •1.1.6. Corrosion
- •1.1.7. Economics
- •1.2. Characteristics of Piping Materials
- •1.2.1. Strength
- •1.2.2. Young’s Modulus (Modulus of Elasticity)
- •1.2.3. Stress-Strain Curve
- •1.2.4. Yield Point or Yield strength
- •1.2.5. Ultimate strength
- •1.2.6. Modulus of Elasticity
- •1.2.7. Ductility
- •1.2.8. Malleability
- •1.2.9. Hardness
- •1.2.10. Brittleness
- •1.2.11. Toughness
- •1.2.12. Creep
- •MATERIALS – METALLIC PIPING
- •2. METALLIC PIPES
- •2.1. Piping Material Specifications – ASME/ASTM
- •2.2. ASTM Material Designation
- •2.3. Pipe Grades
- •2.4. Carbon Steel (CS) Pipes
- •Characteristics
- •Applications
- •Standards
- •2.5. Killed Carbon Steel Pipes
- •2.6. Alloy Steel Pipes
- •2.6.1. Low Alloy Steel Characteristics
- •Standards - Pipes
- •2.6.2. High Alloy Steel Characteristics
- •2.7. Chromium Steel Pipes
- •2.8. Stainless Steel Pipes
- •2.8.1. Categories of stainless steels
- •2.8.2. Austenitic Stainless Steels
- •2.8.3. Ferritic Stainless Steel
- •2.8.4. Duplex and Super Duplex Steel
- •2.8.5. Martensitic Stainless Steels
- •2.8.6. Precipitation Hardening Stainless Steel
- •2.9. Cast Iron (CI) Pipes
- •2.10. Nickel and Nickel Alloys
- •2.11. Titanium
- •2.12. Zirconium
- •Some of the common service applications of Zirconium Piping include:
- •2.13. Chrome - Moly
- •2.14. Brass
- •2.15. Aluminium
- •2.16. Copper
- •2.17. Boiler and Heater Tubes
- •CHAPTER - 3
- •SPECIAL PIPING MATERIALS
- •3. PIPING MATERIALS FOR SPECIAL APPLICATIONS
- •3.1. Piping for High Temperature Service
- •3.2. High Temperature Materials
- •3.4. Cold Temperature Materials
- •3.6. Piping for Hydrocarbon Service
- •3.7. Typical Piping Specifications for Various Hydrocarbon Services
- •3.7.2. Sour Water Services
- •3.7.3. Hydrogen Exposure
- •3.7.4. Offshore Environment
- •3.7.5. Sulfides, Sulfurous Gases & Sulfur Environment
- •3.7.6. Oxidation
- •3.7.7. Halogenation Environments
- •3.7.8. Carburizing Environments
- •3.7.9. Nitriding
- •3.7.10. Amine Environment
- •3.7.11. Caustic Environment
- •3.7.12. Corrosion by Acids
- •3.7.13. Corrosion by Salts
- •3.7.14. Chloride Environment
- •3.7.15. Water Corrosion
- •3.7.16. Microbiological Induced Corrosion (MIC)
- •3.8. Applications for Cooling Water and Fire Water Systems
- •3.9. Measures for Corrosion Protection
- •3.9.1. External Corrosion Protection
- •3.10. Material Traceability
- •3.11. Material Test Reports (MTR)
- •3.12. Quality Assurance (QA)
- •3.13. Material Certificates
- •MATERIALS – UNDERGROUND PIPING
- •4. BURIED PIPING
- •4.1. Ductile Iron Pipe
- •4.2. Plastic Pipes
- •4.3. Types of Plastic Pipes
- •4.3.1. Thermoplastics
- •4.3.2. Thermoset Plastics
- •4.4. PVC Pipes
- •4.5. ABS (Acrylonitrile Butadiene Styrene)
- •4.6. Polypropylene (PP) Pipe
- •4.7. Polyethylene (PE) Pipe
- •4.8. PTFE (TEFLON) and PFA Pipe
- •4.9. Plastic Pipe Terminology
- •4.10. Plastic Pipe Designation
- •4.11. Standard Diameters
- •4.12. Dimension Ratio (DR)
- •4.12.1. Standard Dimension Ratio (SDR)
- •4.13. Pressure Rating
- •4.15. Plastic Pipe Standards
- •4.16. HDPE v/s PVC
- •4.17. Standard Sizes
- •4.18. Standard Lengths
- •4.19. Lined Piping
- •4.20. Cost Comparisons
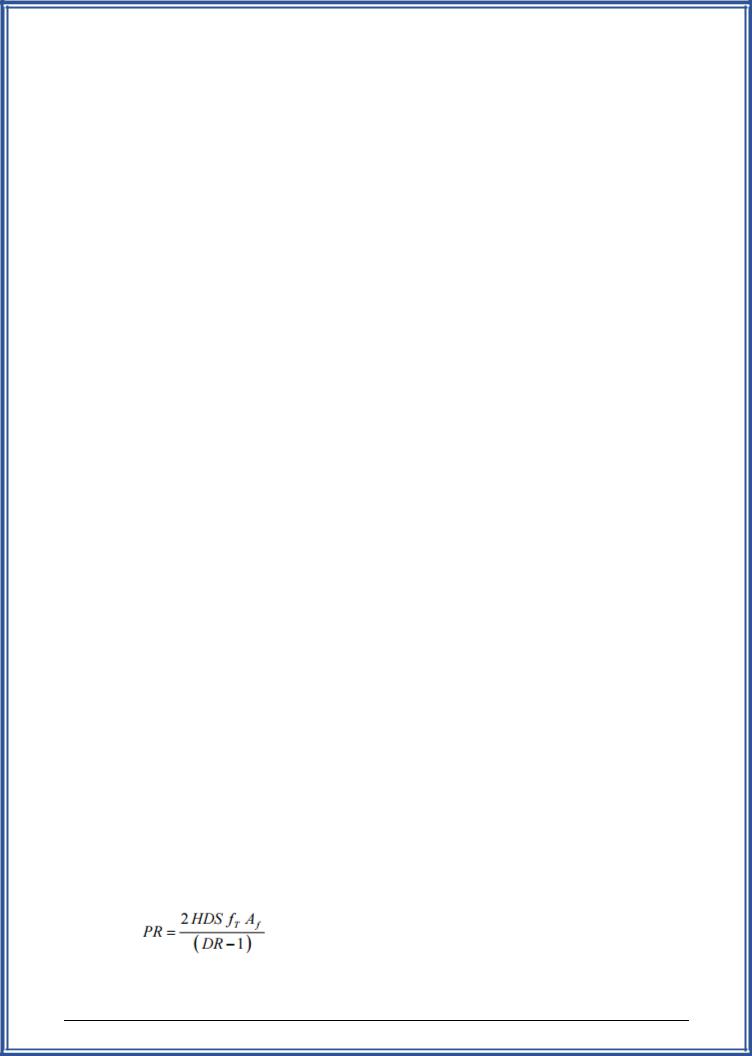
|
|
|
Process Piping Materials – Module 2 – M06-036 |
||
|
|
|
|
|
|
|
50.0 |
51.0 |
|
49.0 |
|
|
63.0 |
64.0 |
|
62.0 |
|
And, the standard pressure ratings for water, at 73°F (23°C), which are commonly recognized by DR-PR standard specifications for PE pipe, are as follows: 250; 200; 160; 125; 100; 80; 63; 50; and 40 psig. However, individual standards generally only cover a selected portion of this broad range.
The result of the use of these standard preferred number values is that a pipe’s standard pressure rating (PR) is a consistent result, independent of pipe size, which simply depends on its standard dimension ratio and the standard HDS of the material from which the pipe was made. This relationship is shown below:
Standard Pressure Ratings for Water, at 73°F (23°C), for SDR-PR Pipes, psig
Standard Dimension Ratio |
Standard Pressure Rating (psig) as a function of a |
|||
|
|
Material’s HDS for Water, at 73°F (23°C), psi |
||
SDR (In the |
SIDR (In the |
HDS = 630psi |
HDS = 800psi |
HDS = 1000psi |
Case of Pipes |
Case of Pipes |
(4.34 MPa) |
(5.52 MPa) |
(6.90 MPa) |
Made to |
Made to |
|
|
|
Standard |
Standard ID’s) |
|
|
|
OD’s) |
|
|
|
|
32.5 |
30.5 |
40 |
50 |
63 |
26.0 |
24.0 |
50 |
63 |
80 |
21.0 |
19.0 |
63 |
80 |
100 |
17.0 |
15.0 |
80 |
100 |
125 |
13.5 |
11.5 |
100 |
125 |
160 |
11.0 |
9.0 |
125 |
160 |
200 |
9.0 |
7.0 |
160 |
200 |
250 |
Important:
Pipes with a lower SDR can withstand higher pressures.
4.13.Pressure Rating
For the purposes of pressure pipe design, the pipe’s pressure rating (PR) is determined by the hydrostatic design stress (HDS) that is assigned to the material from which the pipe is made.
x For example, HDPE (PE4710) DR 17 pipe has a static pressure rating for water of 125 psig.
x OD controlled pressure pipes are pressure rated per ASTM F714 using the formula below.
77
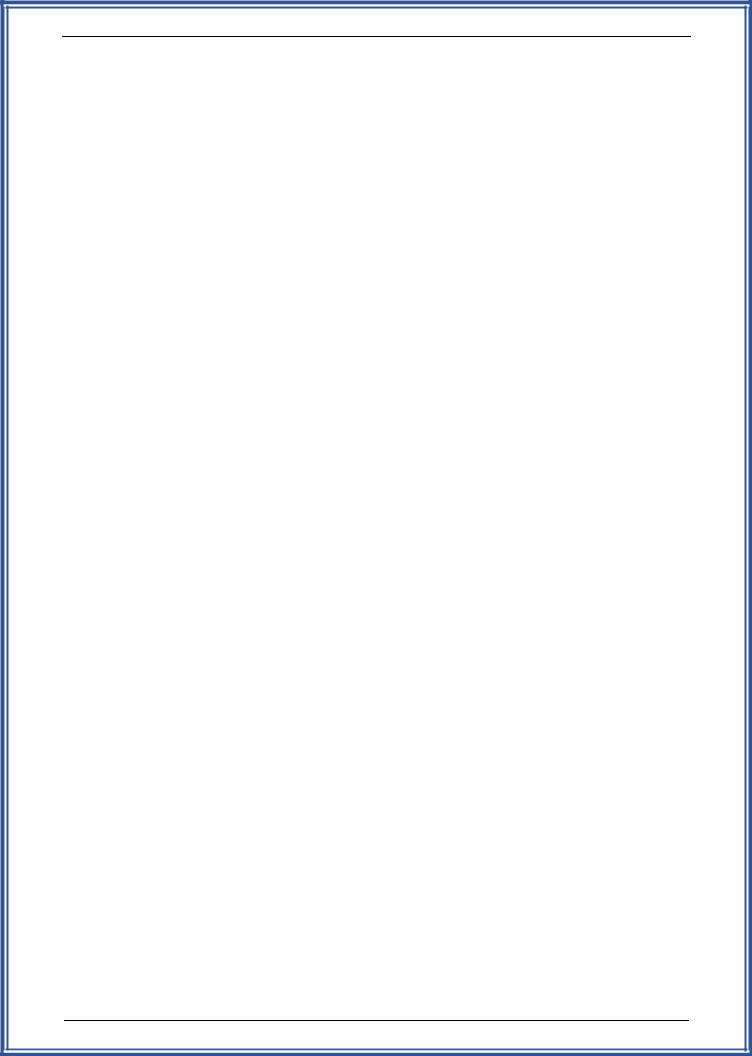
Process Piping Materials – Module 2 – M06-036
Where:
PR = Pressure Rating, psi
HDS = Hydrostatic Design Stress at 73°F, psi (refer vendor info)
Af = Environmental Application Factor, Af = 1 for Water: Aqueous solutions of salts, acids and bases, Sewage, Wastewater, Alcohols, Glycols (anti-freeze solutions) etc. and Af = 0.5 for Fluids such as solvating/permeating chemicals in pipe or soil (typically hydrocarbons) in >2% concentrations, crude oil, fuel oil etc.
fT = Service Temperature Design Factor, fT = 1 for ≤ 80°F (27°C), fT = 0.8 for ≤ 100°F (38°C); fT = 0.63 for ≤ 120°F (49°C) and fT =
0.5 for ≤ 140°F (60°C)
DR = OD Controlled Pipe Dimension Ratio
x Working Pressure Rating
The working pressure rating (WPR) is based on the actual system requirements and is a pressure rating for pipe with flowing water. The WPR includes an allowance for water hammer surge pressures.
At a daily recurring average flow surge velocity of 5 fps and at 80°F, the working pressure rating of HDPE (PE4710) DR 17 pipe is also125 psig; similarly, the working pressure rating for PVC DR 18 is 120 psig (reference - AWWA C900-07, Equation 4). As such, PE 4710 has a higher working pressure rating than PVC at these common conditions.
The table below provides Pressure Rating and Allowable Total Pressure during Surge for PE4710 pipe at 80°F.
|
Pipe |
|
Pressure |
Pressure |
Allowable |
Allowable |
|
Dimension |
|
Class |
Rating |
Total |
Total |
|
Ratio (DR) |
|
|
|
Pressure |
Pressure |
|
|
|
|
During |
During |
|
|
|
|
|
|
||
|
|
|
|
|
Recurring |
Occasional |
|
|
|
|
|
Surge |
Surge |
|
|
|
|
|
|
|
|
DR 9 |
250 psi |
250 psi |
375 psi |
500 psi |
|
|
|
|
|
|
|
|
|
DR 11 |
200 psi |
200 psi |
300 psi |
400 psi |
|
|
|
|
|
|
|
|
78
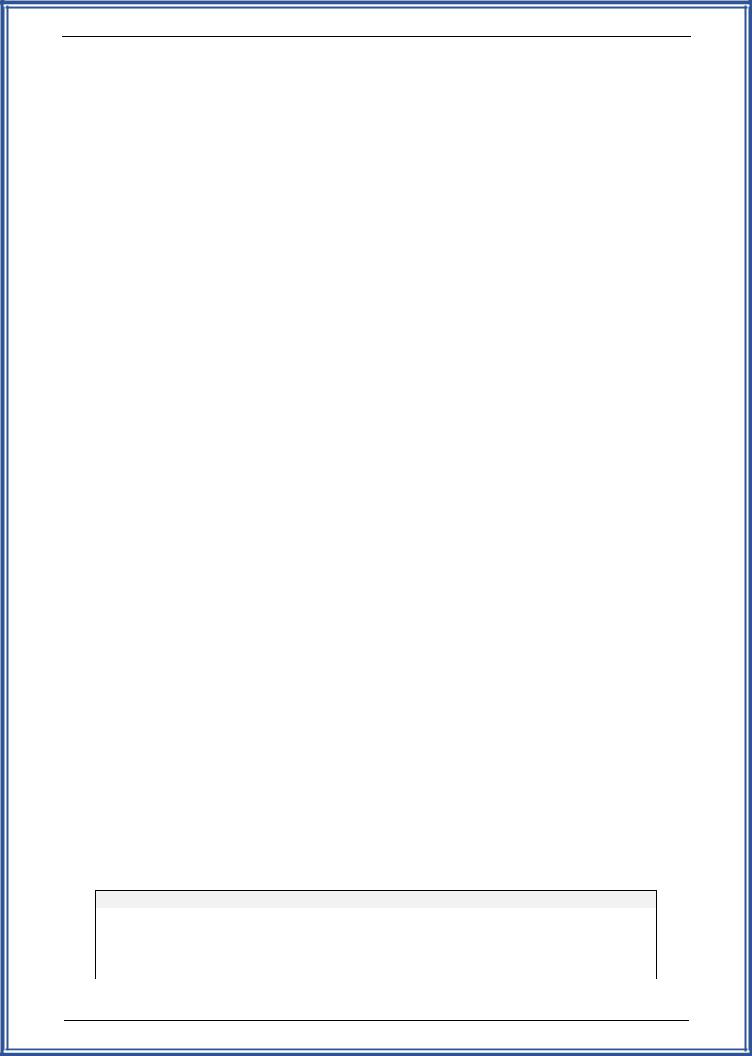
Process Piping Materials – Module 2 – M06-036
DR 17 |
125 psi |
125 psi |
185 psi |
250 psi |
|
|
|
|
|
(Source Reference - AWWA C901-08)
4.14.Plastic Pipe De-rating
The pressure rating of a plastic pipe is determined at 73.4°F. The strength of a plastic pipe decreases as the fluid temperature becomes warmer and therefore the plastic pipe needs to be de-rated for higher temperatures. The table below shows a derating factor for the increase in fluid temperature.
Temperature (°F) |
Multiply Pressure Rating by: |
|
|
73.4 |
1.00 |
|
|
80 |
.93 |
|
|
90 |
.77 |
|
|
100 |
.67 |
|
|
110 |
.51 |
|
|
120 |
.43 |
|
|
130 |
.33 |
|
|
140 |
.23 |
|
|
For example, the maximum working pressure for PVC piping is above 150 psig for all pipe sizes through 8 inches in diameter, but this is only for temperatures of 73.4°F. Any temperature above 73.4°F will result in a reduced working pressure within the piping system up to a maximum of 140°F. At this temperature the de-rating factor is 0.23, where it is 1.0 at 73°F.
4.15.Plastic Pipe Standards
Pipe manufacturers follow requirements set by the American Society of Testing Materials (ASTM) or American Water Works Association (AWWA) for specific pipe materials. Specification standards cover the manufacture of pipes and specify parameters such as internal diameters, loadings (classes), and wall thicknesses (schedules). The methods of pipe construction vary greatly with the pipe materials.
Poly vinyl chloride (PVC) Pipe
Plastic pipe - Schedule 40, 80, or 120 |
ASTM D1785 or D2466 |
Pressure rated pipe - SDR Series |
AWWA C900 or ASTM D2241 |
Plastic drain, waste, and vent pipe and fittings |
ASTM D2665 |
Composite sewer pipe |
ASTM D2680 |
79
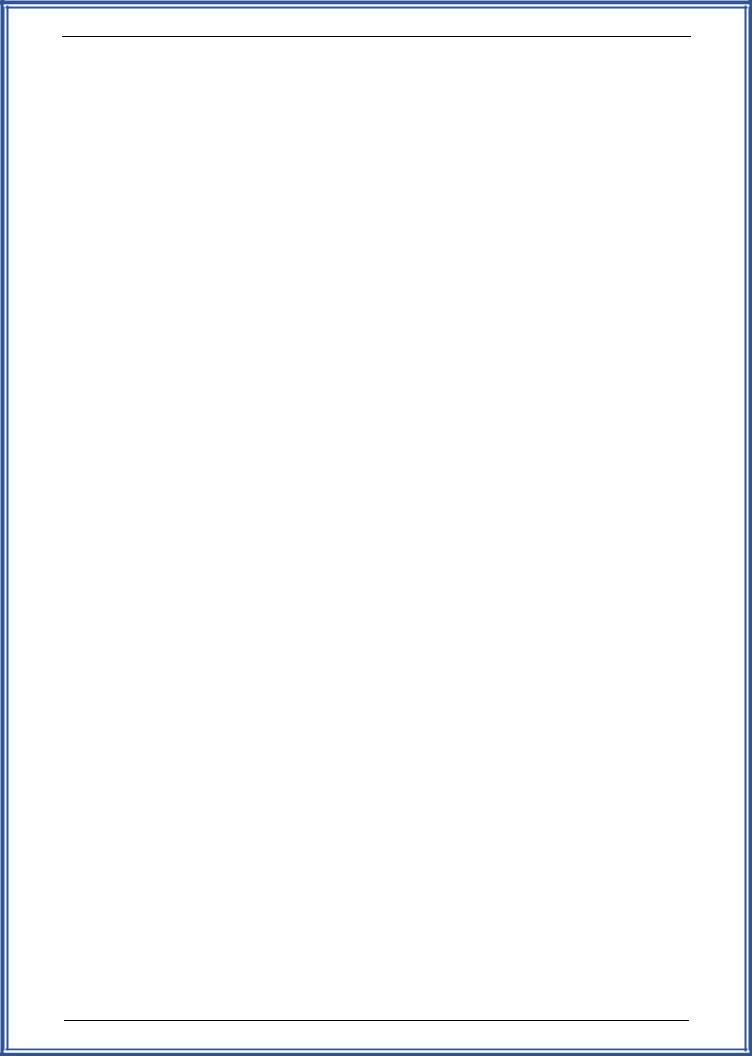
Process Piping Materials – Module 2 – M06-036
Type PSM PVC sewer pipe and fittings |
ASTM F3034 |
|||||
Large-diameter gravity sewer pipe and fittings |
ASTM F679 |
|||||
Smooth-wall Underdrain Systems for |
ASTM F758 |
|||||
Highway, Airport, and Similar Drainage |
|
|
||||
Type PS-46 gravity flow sewer pipe and |
ASTM F789 |
|||||
fittings |
|
|
|
|
|
|
Profile gravity sewer pipe and fittings based |
ASTM F794 |
|||||
on controlled inside diameter |
|
|
||||
Corrugated sewer pipe with a smooth interior |
ASTM F949 |
|||||
and fittings |
|
|
|
|
|
|
Pressure pipe, 4-inch through 12-inch for |
AWWA C900 |
|||||
water distribution |
|
|
|
|
|
|
Water transmission pipe, nominal diameters |
AWWA C905 |
|||||
14-inch through 36-inch |
|
|
|
|
|
|
Polyethylene (PE) pipe |
|
|
|
|
|
|
Schedule 40 |
|
|
|
ASTM D2104 |
||
SIDR-PR based on controlled inside |
|
ASTM D2239 |
||||
diameter |
|
|
|
|
|
|
Schedules 40 and 80 based on outside |
|
ASTM D2447 |
||||
diameter |
|
|
|
|
|
|
SDR-PR based on controlled outside |
|
ASTM D3035 |
||||
diameter |
|
|
|
|
|
|
High density polyethylene (HDPE) pipe |
|
|
|
|||
Plastic pipe and fittings |
|
|
|
ASTM D3350 |
||
SDR-PR based on controlled outside |
ASTM F714 |
|||||
diameter |
|
|
|
|
|
|
Plastic moldings and extrusion compounds |
ASTM D1248 |
|||||
Heat joining polyolefin pipe and fittings |
ASTM D2657 |
|||||
Acrylonitrile-Butadine-Styrene (ABS) pipe |
|
|
||||
Plastic pipe, schedules 40 and 80 |
|
ASTM D1527 |
||||
Plastic pipe, SDR-PR |
|
|
|
ASTM D2282 |
||
Schedule 40 plastic drain, waste, and vent |
|
ASTM D2661 |
||||
pipe |
|
|
|
|
|
|
Composite sewer pipe |
|
|
|
ASTM D2680 |
||
Sewer pipe and fittings |
|
|
|
ASTM 2751 |
||
4.16. |
HDPE v/s PVC |
|
|
|
|
|
|
|
|
|
|
||
Description |
|
PE |
|
PVC |
||
|
|
|
|
|
|
|
Type |
|
|
HDPE is Semi-Crystalline |
PVC is Amorphous |
||
|
|
|
Thermoplastic. |
|
Thermoplastic |
|
|
|
|
|
|
||
Life Expectancy |
|
Generally good life |
|
Long life expectancy if |
||
Resistance to |
|
expectancy. However, has |
properly laid and |
|||
Corrosion Underground |
|
low stress resistance and |
backfilled. |
|||
|
|
|
poor rigidity. |
|
|
|
|
|
|
|
|||
*Safe Working |
|
Rating from 80-160 PSI. |
Ratings from 80-600 PSI. |
|||
Pressures (PSI) |
|
(Surge pressures in HDPE |
|
|||
|
|
|
|
80
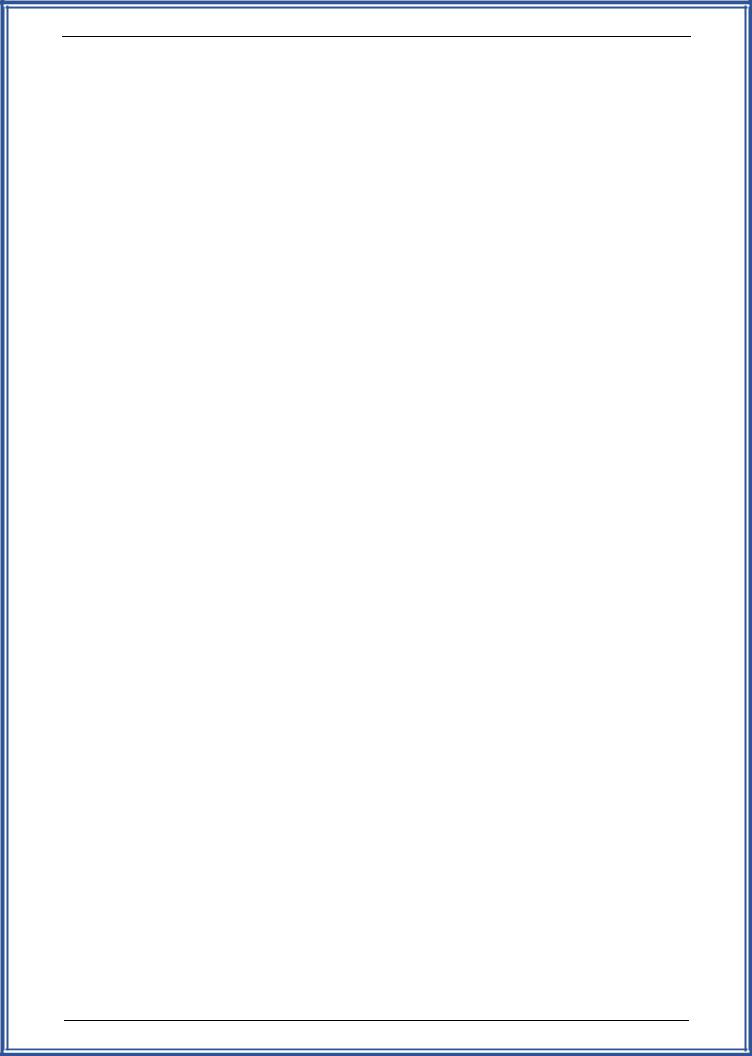
Process Piping Materials – Module 2 – M06-036
|
pipe are significantly lower |
|
|
than PVC pipe due to the |
|
|
lower value of dynamic |
|
|
modulus. For example, a |
|
|
velocity change of 5 fps |
|
|
would cause a 51 psig |
|
|
surge in 7 HDPE DR 17 |
|
|
pipe and 87 psig surge in |
|
|
PVC DR 18 pipe. Lower |
|
|
surge pressures often |
|
|
means longer life for |
|
|
pumps and valves in an |
|
|
HDPE pipeline, as well as |
|
|
lower pressure class |
|
|
pipes). |
|
|
|
|
Resistance to |
Low resistance. |
Much stronger and stiffer. |
Puncturing and |
|
|
Rodents |
|
|
|
|
|
Effect of Sun and |
Weakens with exposure. |
Weakens with exposure. |
Weather |
|
|
|
|
|
Ease of Joining, Laying |
Easy to join using the heat |
PVC pipes use gasketed – |
and Bending |
fusion procedure. Fused |
push-on joints. |
|
joints are self –restrained |
Rigid, but will bend on |
|
and do not require thrust |
|
|
long radius. Can be bent |
|
|
blocks. |
|
|
by heating. |
|
|
Can be installed with |
|
|
PVC pipes require Bolt on, |
|
|
horizontal directional |
|
|
or Thrust Blocks. |
|
|
drilling (HDD) techniques, |
|
|
|
|
|
which is a trenchless |
|
|
installation technique. |
|
|
|
|
Leakage |
The joints are tighter and |
PVC installations have |
|
the leakage rate is zero. |
leakage rates as high as |
|
|
10 percent. |
|
|
|
Cost |
Low cost. |
Costlier than HDPE pipes. |
|
|
|
PE pipe can withstand impact much better than PVC pipe, especially in cold weather installations where other pipes are more prone to cracks and breaks. Because heat fused PE joints are as strong as the pipe itself, it can be joined into long runs conveniently above ground and later, installed directly into a trench or pulled in via directional drilling or by using the re-liner process.
Many of the PE resins used in PE pipes are stress rated not only at the standard temperature, 73°F, but also at an elevated temperature, such as 140°F. Typically, PE materials retain greater strength at elevated temperatures compared to other thermoplastic materials such as PVC. At 140°F, PE materials retain about 50% of
81