
10790
.pdf
100
Иногда в расчетах используется понятие средней относительной
скорости Аср
;ср = |
ср |
|
мв . |
(9.11) |
В справочной литературе (см. табл.) приводятся рекомендуемые значения средних относительных скоростей для различных видов твердых примесей.
Таблица 9.2 Рекомендуемая средняя относительная скорость твердых примесей
Транспортируемый материал |
Аср при |
b |
|
Транспортируемый |
Аср при |
b |
|
µ ≤ 2 |
|
|
материал |
µ ≤ 2 |
|
Опилки мелкие |
0,9 |
7 |
|
Щепа длиной до 35 мм |
0,7 |
11 |
|
|
|
|
|
|
|
Стружка мелкая |
0,85 |
9 |
|
То же, более 40 мм |
0,6 |
13 |
@м
µ = @в – массовая расходная концентрация древесно-воздушной смеси;
b – опытный коэффициент, характеризующий вид перемещаемого
материала.
Для обеспечения устойчивого перемещения материалов системами аспирации и пневмотранспорта скорости на различных участках системы должны быть больше скоростей витания, трогания. Такие скорости называются
транспортирующими.
Транспортирующая скорость
Транспортирующая скорость – это скорость воздушного потока, при которой обеспечивается надежная работа системы по перемещению материалов без образования “пробок”.
Транспортирующая скорость на горизонтальном участке определяется по зависимости, предложенной ЛТА им. Кирова :
vтр. гор. = A ·B |
CDр |
+ 0,01 Iм + JK, |
(9.12) |
Eср |
где Сv – коэффициент, характеризующий изменение скорости воздушного потока в местном сопротивлении.
Сv = 1,1…1,15 – для внутрицеховых систем с большим числом
101
|
отводов; |
Сv = 1,05…1,10 – для межцеховых систем протяженностью до 30 м; |
|
Сv = 1,0 |
– для межцеховых систем протяженностью более 30 м. |
ρм – плотность перемещаемого материала, кг/м3.
µр и b – см. выше.
Формула справедлива для измельченных древесных отходов при значении µ ≤ 2.
Результаты экспериментальных исследований ряда авторов показывают, что для полидисперсной смеси (стружки, опилки …) транспортирующая скорость в горизонтальных участках должна находиться в пределах
vтр. гор = (1,5…2,0) vs.
Ввертикальных участках систем аспирации ипневмотранспорта
скорость должна быть выше, т.к. движение с той же скоростью, что и в горизонтальных участках приводит под действием силы тяжести частиц к постепенному росту концентрации смеси. Увеличение концентрации может привести к засору вертикальных участков, чему способствуют и фасонные части (отводы), устанавливаемые при переходе к вертикальным участкам.
Для предотвращения засоров в вертикальных участках, скорость в них увеличивают по сравнению с горизонтальными на величину скорости витания, т.е.
υтр.верт = υтр.гор. + υs. |
(9.13) |
На разных участках системы скорости могут быть различны, поэтому для обеспечения надежности работы системы используют различные приемы.
Метод 1
При конструировании систем аспирации и пневмотранспорта на горизонтальном участке перед отводом на вертикальный (за 5…6 диаметров)
изменяют диаметр в меньшую сторону, так чтобы увеличить скорость потока на вертикальном участке.
102
Метод 2
Является наиболее распространенным способом.
Система конструируется и рассчитывается таким образом, чтобы на каждом из участков выполнялось условие
υтр ≥ υтр.гор. + υs |
(9.14) |
В вышеприведенной таблице с характеристиками местных отсосов от
деревообрабатывающего оборудования дана минимальная скорость, которая является минимальной транспортирующей скоростью υmin.
9.4. Определение потерь давления в системе при подъёме материала
При подъеме материала на высоту h должна быть затрачена работа,
значение которой может быть определено по формуле
Lв · ∆Рпод = Gм · h · g, |
(9.15) |
||||||||
где Lв – объемный расход воздуха, м3/ч; |
|
||||||||
∆Рпод – потери давления при подъеме материала, Па; |
|
||||||||
Gм – массовый расход материала, кг/ч. |
|
||||||||
Выразив объемный расход воздуха через массовый, получим |
|
||||||||
|
Gв |
|
Р |
= G |
м |
h g . |
(9.16) |
||
|
|
||||||||
|
ρв |
|
под |
|
|
|
|||
|
|
|
|
|
|
|
|
||
Тогда потери давления на подъем материала равны |
|
||||||||
∆ Р |
= |
Gм |
h ρв |
g , |
(9.17) |
||||
|
|||||||||
|
под |
|
Gв |
123 |
|
||||
|
|
|
{ |
|
|
γв |
|
||
|
|
|
|
µ р |
|
|
|
|
|
|
∆Рпод = µр · h · γв |
(9.18) |
Потери давления при подъеме материала на отметку h зависят от
массовой концентрации материала, от высоты подъема и удельного веса
транспортирующего воздуха.
Расчет потерь давления в воздуховодах, по которым перемещается смесь
древесных отходов и воздуха ∆pсм проводят как для обычного (”чистого”)
103
воздуха ∆p с использованием поправочных коэффициентов на транспорт
материала (уравнение И.Гастерштадта):
∆pсм = ∆p (1 + k·µ), |
(9.19) |
где k – опытный коэффициент сопротивления древесно-воздушной смеси, определяемый по справочной литературе в зависимости от состава смеси и диаметра воздуховода.
9.5. Особенности конструирования систем аспирации и пневмотранспорта
1.Так как пылевые вентиляторы имеют высокий уровень звукового давления (высокие характеристики по шуму), то их размещают снаружи здания.
2.Древесные отходы относятся к горючим веществам, поэтому между циклоном и стеной здания необходимо предусматривать противопожарный разрыв не менее 10 м.
3.Системы конструируются с пылевым вентилятором, если через них проходит смесь воздуха и древесных отходов, т.е. циклон или сепаратор находится после вентилятора по ходу движения воздуха. Если циклон или сепаратор размещаются до вентилятора по ходу движения воздуха, то применяют вентилятор обычного исполнения, но среднего или высокого давления.
4.Воздуховоды систем конструируются по временной нормали для
проектирования АЗ-187 (“Временная нормаль на металлические воздуховоды
круглого сечения для систем аспирации”):
-применяются воздуховоды только круглого сечения;
-используется сталь с толщиной δ = 1 мм и более;
-воздуховоды соединяются на фланцах, они являются сварными и относятся к классу плотных;
-радиус изгиба отводов должен составлять 2D, полуотводы имеют угол поворота 30°, 45° и 60° с радиусом загиба 2D;
-тройники и крестовины имеют углы врезки под 30° или 45°.
104
Основные положения, используемые при конструировании
систем аспирации и пневмотранспорта:
1.Системы компонуются в зависимости от объемно-планировочных решений и с расходом, не превышающим 10 тыс. м3/ч.
2.Вентиляторы устанавливаются снаружи здания.
3.Учитываются все особенности конструирования систем, рекомендуемые нормативными документами по проектированию ДОЦ.
4.Воздухораспределение конструируют таким образом, чтобы было кратчайшее расстояние траектории струи от воздухораспределителя до зоны дыхания человека.
5.Воздухораспределители рекомендуется размещать над рабочими местами и проездами.
6.Запрещается устанавливать воздухораспределители над воздуховодами и технологическим оборудованием.
7.Приточные струи не должны сбивать факел местных отсосов.
8.Емкость бункера для отходов циклона или сепаратора рассчитывается из производительности данной системы таким образом, чтобы заполнение бункера происходило бы не чаще, чем за 3 суток. Наиболее оптимальной является емкость, когда очистка бункера происходит 1 раз в неделю.
9.6.Пылевые вентиляторы для систем аспирации и пневмотранспорта
Пылевые вентиляторы предназначены для перемещения невзрывоопасных неабразивных пылегазовоздушных смесей с температурой не выше 80°С с содержанием пыли и других механических твердых примесей в количестве не более 1 кг/м3 при отсутствии липких веществ и волокнистых материалов.
Пылевые вентиляторы применяются:
1.для удаления древесных стружек и опилок, металлической пыли от станков, пыли и шлаков при сварочном производстве
2.в системах отбора запыленного воздуха при производстве цемента и
105
железобетонных конструкций;
3.в системах пневмотранспорта зерна и при производстве круп.
Внастоящее время различными российскими (“Мовен”, “Консар”, “Евромаш” и др.) и зарубежными (“Nestro”, Германия) производителями выпускается широкий модельный ряд пылевых вентиляторов среднего и высокого давления. Среди вентиляторов российского производства наибольшее распространение получили вентиляторы следующих марок: В-ЦП6-45, В-ЦП7- 40, ВР-100-45 (ВРП-100-45), ВР-6-27. В основном пылевые вентиляторы выпускают следующего номерного ряда: №№ 4; 5; 6,3; 8.
Через пылевые вентиляторы проходит воздух с механическими примесями, поэтому они их схемы исполнения и аэродинамические характеристики отличаются от вентиляторов общего назначения.
Основные конструктивные особенности пылевых вентиляторов по сравнению с вентиляторами общего назначения:
1. массивный сварной корпус из стали толщиной листа δ = 3÷5 мм (у
обычных вентиляторов δ = 1÷2 мм);
2.выпускаются только с клиноременной передачей ( 6 исполнения) с
мощным электродвигателем, установленным на раме;
3.крыльчатка вентилятора выполнена в виде лопастей (количество для различных моделей различно- 6…8). Использование подобной конструкции предотвращает забивание межлопаточного пространства перемещаемыми примесями.
4.корпус пылевых вентиляторов в основном выполняется неповоротным
сположением 0о.
5.номер вентилятора не обозначает диаметра всасывающего отверстия
(у вентиляторов общего назначения, например, № 6,3 соответствует dвх = 630 мм). Для пылевых вентиляторов часто имеет место соответствия диаметра входного отверстия эквивалентному диаметру выхлопного патрубка (dвх =
dэкв.вых.).
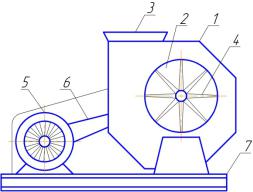
106
На рисунке 9.2 показан вентилятор ВР-100-45 производства компании
“Мовен”.
Рис. 9.2 Пылевой вентилятор ВРП-100-45:
1 – корпус вентилятора; 2 – всасывающее отверстие; 3 – нагнетательное отверстие; 4 – лопатки рабочего колеса;
5 – электродвигатель; 6 – клиноременная передача; 7 – рама основания.
Производительность – до 25 тыс. м3/ч; Давление – до 4 кПа.
Пылевые вентиляторы подбираются так же, как и обычные, по соответствующим универсальным характеристикам, приведенным в справочной литературе.
Несмотря на то, что системы аспирации и пневмотранспорта изготавливают из воздуховодов класса плотности П (плотные), рекомендуется производительность и развиваемое давление нагнетателя принимать с запасом на неучтенный дополнительный расход, т.е.
Lвент = 1,1 Lс
Рвент = 1,1 ∆Рс + ∆Роб
10. ВЕНТИЛЯЦИЯ ГАЛЬВАНИЧЕСКИХ УЧАСТКОВ 10.1. Краткие сведения о технологических процессах
Применение металлопокрытий (гальванических покрытий) является одним из наиболее распространенных способов защиты изделий из металла от коррозии в различных отраслях промышленности - машиностроении, приборостроении и др. Гальваническую обработку применяют также как способ сообщения специальных физических и химических свойств (например, электропроводимости) либо изменения механических (прочностных) свойств поверхности.
107
Гальванические покрытия представляют собой металлическую пленку толщиной от долей мкм до десятых долей мм, которые наносят методом электролитического осаждения на поверхность металлических изделий.
Гальванотехника – область прикладной электрохимии, охватывающая процессы электролитического осаждения металлов на поверхность металлических и неметаллических изделий.
Все процессы гальванотехники протекают в гальванических ваннах. Различают ванны:
1.стационарные (покрываемые изделия которых неподвижны);
2.полуавтоматические (изделия вращаются или перемещаются по кругу или подковообразно);
3.автоматические (загрузка, выгрузка и транспортировка изделий вдоль ряда ванн проходит автоматически).
Цикл технологических операций при обработке изделий в гальванических цехах рассматривают обычно как ряд отдельных взаимосвязанных технологических линий и участков.
По назначению все технологические операции делят на группы:
1 – механическая обработка поверхности деталей (шлифование, полировка, обработка сварных швов, снятие заусенцев и др.);
2 – обезжиривание (химическое или электрохимическое);
3 - травление (шлифование, полирование, глубокое травление, часто называемое химическим фрезерованием, нанесение изоляции перед глубоким травлением, декапирование);
4 – нанесение металлических покрытий электролитическим или химическим способами (цинкование, кадмирование, хромирование, никелирование, меднение, нанесение сплавов и многослойных покрытий, и др.);
5 – анодное оксидирование металлов и сплавов;
108
6 – окончательная обработка поверхности деталей после нанесения металлических покрытий (полирование , пассивирование, промасливание и др.).
По уровню механизации и автоматизации технологических операций различают две основные разновидности технологических линий:
-Механизированные линии гальванических ванн с дистанционным управлением процессами. Встречаются в цехах в цехах опытного или малосерийного производства.
-Автоматы с программным управлением. Операции по загрузке и выгрузке деталей, перемещение изделий из одной ванны в другую выполняются операторами с программным управлением. Размещение деталей подлежащих обработке на устройства транспортировки и снятие готовых изделий осуществляется вручную.
Нанесение металлопокрытий гальваническим способом связано с использованием опасных для здоровья человека различных цианистых соединений, щелочных и кислых электролитов повышенной температуры, растворов содержащих соли меди, свинца, никеля, индия и хромового ангидрида.
Особую опасность представляют цианиты. Их растворы ядовиты и при соединении с кислотами способны образовывать опасные для людей соли синильной кислоты.
К классу наиболее вредных относят также операции с хромсодержащими
растворами. Процесс хромирования сопровождается выделением газообразного водорода, кислорода, образующих туман над поверхностью электролита.
10.2. Основные рекомендации по проектированию систем вентиляции гальванических и травильных цехов
Вытяжные системы:
1. Вытяжные воздуховоды от бортовых отсосов необходимо
прокладывать с уклоном i=0,005÷0,01 в сторону вентилятора. В нижней части
109
участков воздуховодов и кожуха вентилятора необходимо предусматривать устройства для отвода конденсата в канализацию.
На расстоянии до 10 м от источника вредных выделений предусматривают съемные отводы для ревизии воздуховодов.
2. Системы компонуются по видам вредных выделений.
В отдельные системы следует выделять местные отсосы от ванн:
-обезжиривания органическими растворителями;
-хромирования;
-никелирования;
-с цианистыми процессами.
3. Вентиляторы и фильтры располагают в отдельном отапливаемом помещении.
4.На выхлопных шахтах желательно устраивать “факельный выброс”. Установка зонтов не рекомендуется.
5.Вентиляторы необходимо применять в антикоррозионном исполнении.
6.При проектировании систем должно быть минимальное количество проходов через перекрытие и покрытие.
7.В системах, удаляющих загрязненный воздух от ванн с токсичными парами, необходима установка резервного вентилятора.
8.Запрещается укрывать пеной ванны, над которыми возможно образование водорода.
Удаление воздуха от таких ванн осуществляют эжекторными установками.
9.Общеобменную вытяжку из верхней зоны допускается не устраивать, если местные вытяжные системы обеспечивают воздухообмен более 5 крат. При значении кратности воздухообмена n < 5 ч-1 необходимо предусмотреть механическую общеобменную вытяжку из верхней зоны с кратностью 1 ч-1.
Приточные системы:
1. Для обеспечения бесперебойной работы приточной вентиляции
необходимо предусматривать установку не менее двух приточных систем с