
10452
.pdf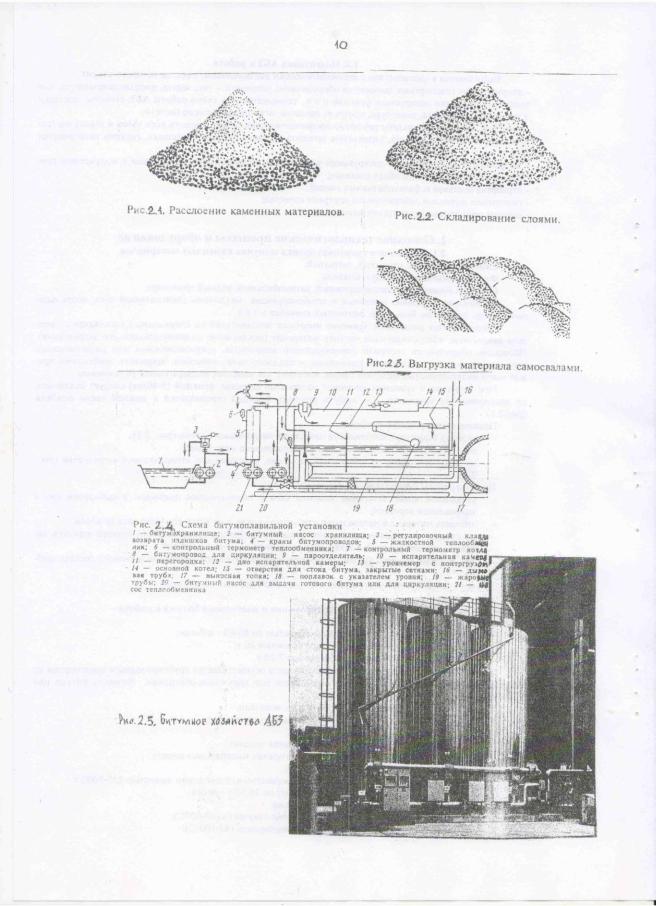
11
Наиболее предпочтительными для выпаривания воды являются цистерны-термосы непрерывного действия с масляным теплоносителем (рис.2.4). В случае работы с только что привезенным с завода битумом (работа «с колес»), т.е. имеющим необходимую технологическую текучесть, операции 1-2 могут не производится.
12
Битум, нагретый до температуры транспортировки, подают в емкость, внутри которой по системе труб теплообменников, расположенных в нижней ее части, циркулирует теплоноситель. По мере нагрева вязкость битума уменьшается, он поднимается вверх, а на его место приходит менее нагретый, вступая в контакт с поверхностью труб. Цистерна, а также подводящая (из хранилища или битумовоза) и отводящая (подача в смеситель) магистрали теплоизолируются. Магистрали располагаются ближе ко дну цистерны. АБЗ имеют, как правило, несколько расходных емкостей для хранения битума (рис.2.5). Перекачка нагретого битума в смеситель, а также циркуляция его из цистерны в цистерну выполняется с помощью шестеренчатого насоса. Магистраль возврата нагретого битума от насоса в цистерну расположена на уровне, не превышающем уровень битума в емкости с тем, чтобы он не входил в контакт с воздухом. Количество битума, находящегося в цистерне, определяют по тарировочным таблицам, представляемым заводом изготовителем, предварительно измерив с помощью щупа расстояние от верхнего края цистерны до поверхности битума. Уровень битума в цистерне должен всегда быть выше мест подключения магистралей (закачки, подачи, возврата).
Не допускается неконтролируемое смешение битумов с разных нефтеперегонных заводов или разных марок, т.к. может произойти его расслоение внутри емкости. При вынужденном смешении, например, когда после полной откачки битум остался на дне цистерны ниже теплообменников, их тщательно перемешивают с помощью насоса и устанавливают полученную марку вяжущего. При заполнении пустой емкости ее проверяют на наличие конденсата воды, герметичность предохранительных клапанов в магистралях во избежание повышения давления, что может привести к взрыву.
Битум должен храниться в емкости при постоянной температуре. Максимальное время нахождения битума в емкости при рабочей температуре до момента его использования – 5 часов. Неизрасходованный битум охлаждают до температуры 80 оС, который также можно хранить не более 12 часов в связи с ускоренным старением. Перед началом работ производится тарировка битумных дозаторов.
2.3. Приготовление асфальтобетонных смесей в установках периодического действия
Асфальтосмесительная установка периодического действия состоит из следующих основных узлов (рис.1.3,
1.4):
-агрегат питания;
-сушильный агрегат;
-система дозирования и подачи битума;
-система дозирования и подачи минерального порошка;
-смесительный агрегат;
-система пыле- и газоочистки;
-накопительный бункер для готовой смеси.
2.3.1. Первичное дозирование каменных материалов
Агрегат питания является расходным бункером для щебня и песка и обеспечивает предварительное дозирование холодных и влажных материалов различных фракций для подачи в сушильный агрегат или непосредственно в смеситель (рис.2.11). Основные узлы агрегата питания:
-бункеры для хранения инертных заполнителей;
-дозаторы (питатели) сыпучих материалов;
-сборный конвейер;
-загрузочный транспортер.
Бункеры для хранения инертных заполнителей
В зависимости от типа асфальтосмесительной установки бункеры могут быть одноили многосекционные (до 6 секций), разъемные, одноили двухрядные общей емкостью 10-60 т (рис.2.6). Бункеры имеют форму конического четырехгранника, сужающегося к низу. В нижней его части устраивают отверстие прямоугольного или трапецеидального сечения (рис.2.8, 2.9) и заслонку, с помощью которой регулируется подача материала на ленточный транспортер. Наиболее эффективными являются отверстия трапецеидальной формы. Между бункерами в верхней части размещают перегородки, для исключения попадания материалов из одного бункера в другой. На входе в бункер устанавливается колосниковая решетка для отделения негабарита. В целях исключения налипания влажных материалов к стенкам бункера на его корпус устанавливается виброплита или сводообрушители. Загрузка бункера ведется с помощью автопогрузчика либо бульдозера. При этом склады минеральных материалов должны быть в непосредственной близости от асфальтосмесительной установки.
Дозаторы агрегата питания
Дозаторы (питатели) служат для первичного дозирования инертных материалов в целях недопущения дальнейшего переполнения горячих бункеров смесительного агрегата.
Способы дозирования холодных материалов: весовой, объемный.
По продолжительности работы различают питатели циклического и непрерывного действия. Типы питателей циклического действия с объемным дозированием материалов:
кареточный (рис.2.12), тарельчатый, вибрационный (рис.2.13).
Дозаторы непрерывного действия как правило представлены ленточными питателями с объемным или весовым дозированием материалов (рис.2.6). В настоящее время наибольшее распространение получили ленточные питатели с постоянной или переменной скоростью ленты.
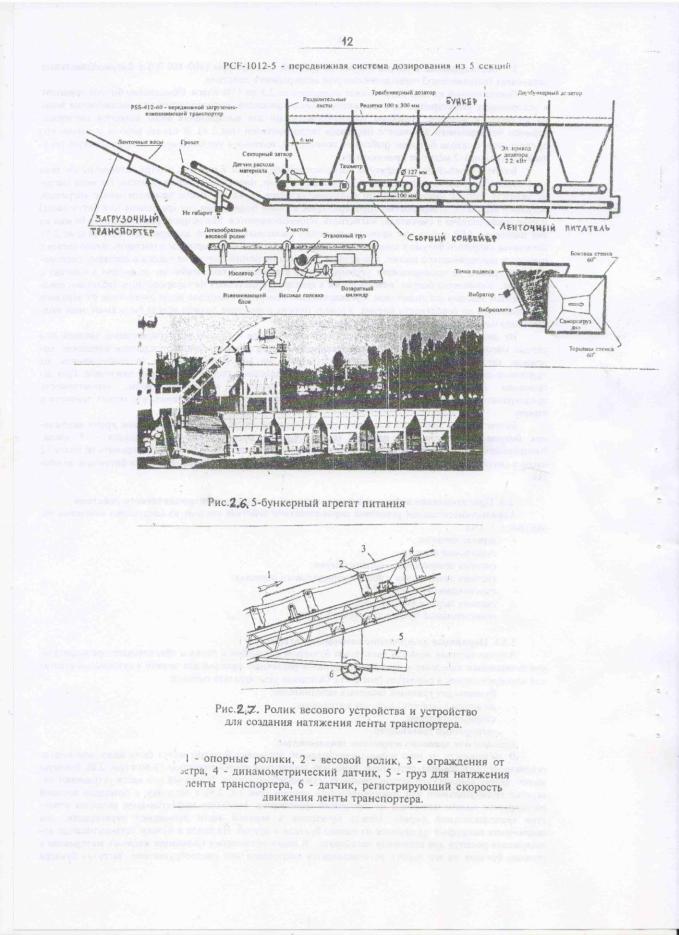
13

14
15
Объемное дозирование
Количество подаваемого из бункера материала на питателях с постоянной скоростью ленты регулируется только положением заслонки (затвора). Путем поднятия или опускания заслонки, корректируется ширина зазора между стенкой бункера и поверхностью ленточного транспортера. Перемещение (настройку) заслонки выполняют либо вручную, либо с помощью электропривода.
На питателях с переменной скоростью ленты дозирование производят следующим образом. Сначала идет грубая настройка дозатора при помощи заслонки, а затем устанавливается точный расход материала путем регулировки скорости ленты. В дальнейшем при необходимости незначительного изменения количества подаваемого материала корректируется только скорость ленточного питателя. При определении положения заслонки расчет ведется в интервале 20-80% скорости ленты с тем, чтобы оператор мог варьировать расходом материала без изменения положения заслонки. Скорость работы ленточного питателя (в процентах от максимально возможной скорости) высвечивается на дисплее в кабине управления. Если питатель работает со скоростью, превышающей указанные пределы, то требуется перенастройка оборудования.
Скорость каждого ленточного питателя регулируется отдельно для обеспечения независимой работы бункеров в соответствии с заданным рецептом смеси. Однако скорости всех ленточных питателей синхронизируют для того, чтобы в случае изменения режима работы одного из них автоматически происходило пропорциональное изменение скорости всех остальных питателей.
Каждая пара бункеров оборудуется устройством, фиксирующим количество материала в бункере. Если бункер пуст, материал не проходит через отверстие или не поступает на сборный конвейер, то срабатывает датчик (звуковой сигнал), после чего происходит автоматическое выключение смесителя.
Весовое дозирование материалов осуществляют при помощи специальных взвешивающих устройств, установленных на всех ленточных питателях бункеров (рис.2.14), кроме ближайшего к сушильному барабану. Его функции выполняет весовое устройство, расположенное на загрузочном транспортере по информации о суммарном весе компонентов, находящихся на ленте. Система управления показывает количество материала, отгруженное из каждого бункера. Фактический расход заполнителя определяется путем вычитания из общей массы поправки на влажность материала. Влажность каждого материала следует проверять не реже двух раз за смену. Среднее значение влажности компонентов заносится вручную в компьютер для установки параметров работы горелки, вычисления веса сухого заполнителя, для определения общей производительности установки и расхода энергоносителей.
Сборный конвейер и загрузочный транспортер
С ленточных питателей исходные материалы поступают на сборный конвейер, работающий с постоянной скоростью. Для предотвращения налипания материала на ленту сначала следует подавать на конвейер крупный заполнитель, а затем мелкий. В противном случае ленту конвейера требуется постоянно очищать. Если материал с ленты не удалять, то компьютер будет фиксировать завышенный расход инертных заполнителей, что в конечном итоге приведет к передозировке битума.
По сборному конвейеру минеральная смесь подается на загрузочный транспортер и далее через загрузочный лоток в сушильный барабан. Гибкая лента транспортера также движется с постоянной скоростью. В целях контроля за крупностью частиц смеси между сборным конвейером и сушильным барабаном может устанавливаться одноили двухситный грохот с размером ячеек чуть большим максимального диаметра разрешенной фракции. Грохот оборудуется перепускным и отводным лотками, с помощью которых в первом случае при необходимости смесь может подаваться сразу на конвейер, минуя грохот, а во втором – освобождаться от негабарита. В ряде модификаций агрегатов питания используют несколько грохотов, устанавливаемых под каждый бункер между ленточным питателем и сборным конвейером.
На части установок монтируется дополнительное весовое устройство, контролирующее количество подаваемой в сушильно-смесительный агрегат минеральной смеси. Чувствительным элементом устройства является весовой ролик (рис.2.7), расположенный в центре транспортера. Он соединен с динамометрическим датчиком и может свободно перемещаться. В процессе прохождения материала над весовым роликом его вес преобразуется в электрический сигнал и поступает на пульт управления. Кроме того, транспортер оборудуется тахометром, регистрирующим скорость ленты, который устанавливают на натяжном ролике. При снятии показаний лента всегда должна находится в натянутом состоянии. Для определения расхода материала (т/час) используются оба сигнала. Полученное значение показывает вес влажного материала, который компьютер пересчитывает в вес сухого и затем назначает необходимое количество битума.
Установки с раздельным агрегатом питания могут иметь несколько сборных конвейеров (рис.2.10) в случае, когда согласно технологической схеме требуется самостоятельная подача материалов в сушильно-смесительный агрегат. Для получения качественной смеси минеральные материалы должны поступать в смеситель в строго определенных пропорциях. Поэтому перед началом работы завода каждый бункер агрегата питания должен пройти тарировку.
Тарирование агрегата питания выполняют путем определения расхода материала, отгруженного из бункера. В случае объемного дозирования для этого: взвешивают пустое инвентарное устройство (тару), через перепускной лоток из бункера наполняют его материалом, регистрируют время подачи с последующим взвешиванием тары с материалом. Процесс повторяется несколько раз: для установок, работающих с постоянной скоростью при различных положениях заслонки, с переменной скоростью – так же для трех различных скоростей ленты. Далее строят тарировочные графики и заносят информацию в компьютер. При необходимости тарирования весового устройства материал, прошедший через весовой ролик, отбирают в тару и взвешивают. Фактический вес сравнивают со значением, вычисленным систе
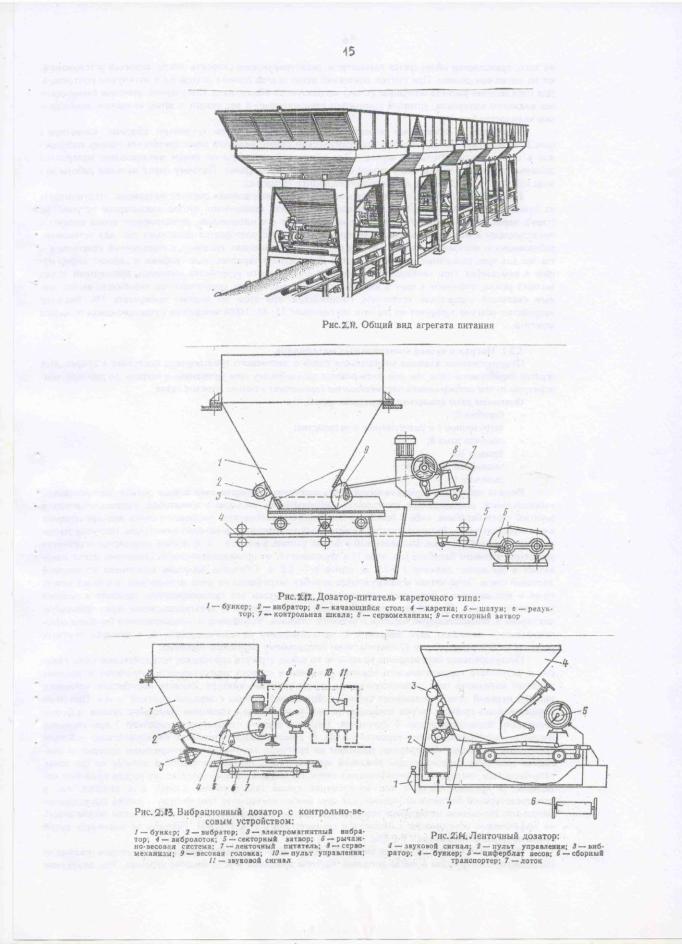
16
17
мой управления установки. Расхождение при этом не должно превышать 1%. Весовое устройство обычно тарируют из расчета обеспечения 75, 85, 100% мощности сушильно-смесительного агрегата.
2.3.2. Нагрев и сушка минеральных материалов
Отдозированная влажная минеральная смесь с ленточного транспортера поступает в сушильный агрегат барабанного типа, где она подвергается дальнейшему просушиванию и нагреву до рабочей температуры путем непрерывного перемешивания (вращения) в потоке горячих газов.
Основные узлы сушильного агрегата (рис.2.15):
-барабан 2;
-загрузочное 1 и разгрузочное 6 устройства;
-опорная рама 8;
-привод 10;
-топливная система 9;
-дымосос 13.
Подача материала осуществляется через загрузочное устройство в виде лотков (неподвижных, вибрационных, вращающихся наклонных), виброжелобов, кольцевых элеваторов, устанавливаемых в верхней части барабана, либо с помощью ленточного транспортера, подающего смесь непосредственно в его нижнюю часть. Разгрузка нагретых каменных материалов происходит самотеком, поступая на лоток разгрузочной коробки, выполненный в форме улитки, а из него – в приемное устройство «горячего» элеватора. Размеры барабана (см. табл.1) в зависимости от производительности смесителя могут изменяться в пределах: диаметр 1.5-3.0 м, длина 6.7-12.2 м. Обечайка барабана выполнена из сварной листовой стали. Загрузочная и разгрузочные коробки закреплены на раме неподвижно, а в пазах между ними и вращающимся барабаном установлены уплотнители для предотвращения пыления и подсоса холодного воздуха. Привод (вращение) барабана осуществляется от электродвигателя через приводную шестерню 3, опоясывающую барабан с внешней стороны. Устойчивость вращающегося барабана обеспечивается с помощью двух бандажей 4, расположенных на компенсаторах 5, и четырех опорных роликов 11. Упорные ролики 12 препятствуют продольному смещению барабана.
Поступательное перемещение материала по длине агрегата происходит под действием силы тяжести в результате горизонтального наклона барабана в сторону разгрузочного устройства и наличия лопастей ковшового типа, установленных по его внутреннему контуру. Лопасти поочередно, начиная с нижней мертвой точки, поднимают смесь, и сбрасывают ее вниз с верхней мертвой точки. При этом осуществляется сушка и нагрев материала за счет теплообмена с горячими дымовыми газами в форме конвекции, теплопроводности и излучения. Тепловая энергия генерируется горелкой 7 при сгорании жидкого, газообразного или твердого топлив. В смесительных установках периодического действия сушильные барабаны, как правило, работают по принципу противотока: минеральные материалы двигаются навстречу горячим газам. Тепловой процесс (рис.2.16) внутри барабана делится на три зоны, отличающихся температурой отработанных газов. На входе в барабан происходит нагрев влажного материала. В средней части – его интенсивная сушка (выпаривание влаги), а в нижней, т.е. в непосредственной близости от горелки, где газы имеют наивысшую температуру – нагрев высушенного материала. На выходе из барабана температура нагрева минеральных материалов должна обеспечивать их эффективное объединение с битумом в соответствии с ГОСТ 12801. Предельная влажность сухой смеси не должна быть выше 0.2-0.5%.
Время нахождения материала внутри барабана (обычно 5-9 мин) зависит от геометрии (размеров) последнего, конструкции и числа лопастей, частоты вращения и угла наклона агрегата. Так, изменение наклона барабана на 2.5-6% обеспечивает скорость прохождения материала соответственно 25-65 мм/мин. Если влажность материала на выходе превышает допустимый предел, то необходимо увеличить плотность потока смеси путем уменьшения угла наклона барабана. В сушильном барабане наблюдается заметная разница в степени нагрева разных фракций: крупные нагреваются меньше, чем мелкие. В дальнейшем в процессе перемешивания их температура несколько выравнивается, однако тепловой баланс достигается не всегда. По мере прохождения барабана минеральная смесь может менять свой первоначальный зерновой состав, прежде всего за счет количества мелких фракций. Во-первых, часть пылеватых частиц вместе с газами улетает в дымосос. Вместе с тем, при сушке загрязненных щебней процент пыли чаще всего увеличивается на 0.2-2% за счет ее отслаивания от крупного заполнителя. Если для очистки газов используется мокрый способ, то все удаленные в виде шлама пылеватые частицы должны быть удалены из состава смеси.
Каждый производитель установок использует свою конструкцию лопастей сушильного (сушильносмесительного) барабана с учетом принятой технологической схемы. Подаваемый в барабан материал не должен попадать непосредственно в пламя горелки, иначе она может погаснуть. По мере движения количество захватываемого и сбрасываемого лопастями материала увеличивается. Примерно в средней части смесь перемещается по всему поперечному сечению агрегата, что повышает эффективность теплообмена, а материал подвергается интенсивному высушиванию и нагреву. При необходимости замедлить продвижение материала на части установок применяют специальные устройства (кольца, уменьшенного диаметра, лопасти с отрицательным углом атаки, заслонки). Внутренние элементы барабана подвергаются сильному абразивному износу, что требует постоянного контроля за их состоянием и своевременной замены.
Температура нагрева минеральных материалов определяется маркой битума, погодными условиями, влажностью исходных компонентов. Главное правило при работе сушильного барабана – температурный режим должен быть «щадящим», т.е. исключать перегрев компонентов смеси. Ошибочным является стремление повысить эффективность сушки за счет чрезмерного нагрева заполнителя. Это приводит к необратимым изменениям в структуре битума (ста
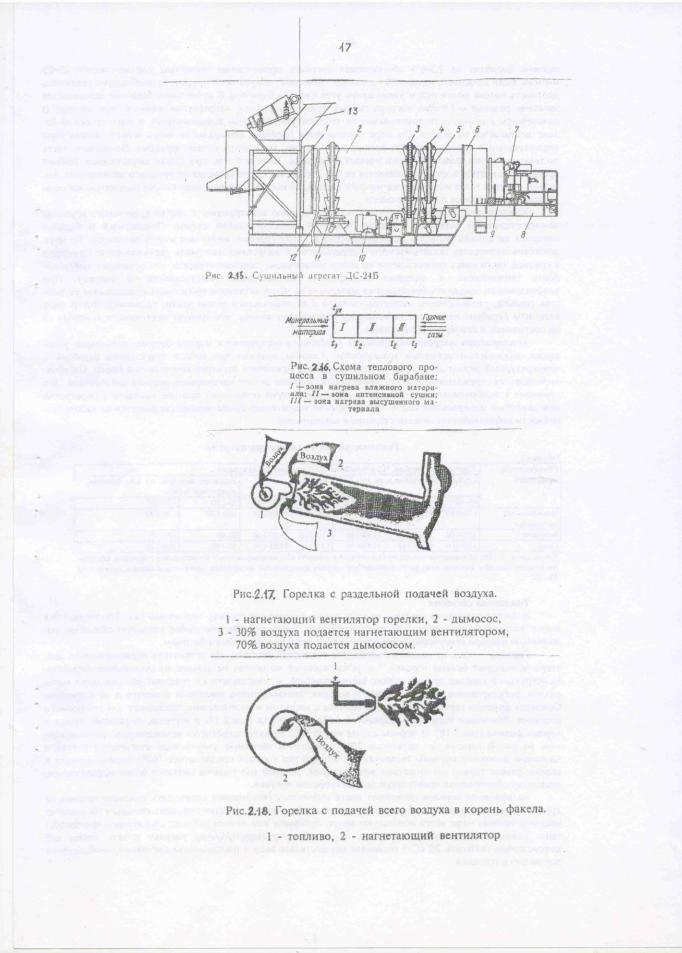
18
19
рению) при его контакте с перегретой поверхностью минеральной части. Термостарение значительно существеннее сказывается на работоспособности асфальтобетона нежели старение в конструкции.
Рекомендуемая температура нагрева
Таблица 2.1.
Наименование |
Температура нагрева, °С, в зависимости от показателей вяжущего |
|
|
|||||
материалов |
Глубина проникания иглы при 25 °С, 0,1 мм |
|
Условная |
вязкость по вискозиметру с |
||||
|
|
|
|
|
|
отверстием 5 мм, с |
||
|
40-60 |
61-90 |
91-130 |
131-200 |
201-300 |
70-130 |
|
131-200 |
Минеральные |
170-180 |
165-175 |
160-170 |
150-160 |
140-150 |
100-120 |
|
120-140 |
материалы |
|
|
|
|
|
|
|
|
Вяжущее |
150-160 |
140-150 |
130-140 |
110-120 |
100-110 |
80-90 |
|
90-100 |
Смесь |
150-160 |
145-155 |
140-150 |
130-140 |
120-130 |
80-100 |
|
100-120 |
Примечание — При применении поверхностно-активных веществ или активированных минеральных порошков для приготовления смесей с вязкими вяжущими температуру нагрева минеральных материалов, вяжущего и смесей снижают на
10—20 °С.
Топливная система
В состав топливной системы входит: топка, горелка (форсунка), топливный бак. Топливный бак имеют установки, работающие на жидком топливе. Топка представляет собой стальную обечайку, выложенную изнутри огнеупорным кирпичом или покрытую жаростойким бетоном.
Горелка – один из основных элементов топливной системы. На установках периодического действия используют осевые горелки, т.е. установленные по центру на выходе из сушильного барабана. Конструкцией горелки предусмотрено автоматическое, в зависимости от температуры каменных материалов, регулирование подачи топлива и воздуха, дистанционное зажигание и контроль за пламенем. Основная функция горелки – смешение топлива с воздухом в соотношении, требуемом для его полного сгорания. Различают горелки с раздельной подачей воздуха (рис.2.17) и горелки, подающие воздух в корень факела (рис.2.18). В первом случае около 30% воздуха нагнетается вентилятором, расположенным на самой горелке, а остальные 70% подаются в топочную зону в виде вторичного потока с помощью дымососа системы пылеочистки. Второй тип горелок предполагает 100% подачу воздуха в корень факела только нагнетающим вентилятором. Данный тип горелок является более эффективным, поскольку обеспечивает практически полное сгорание топлива.
Большинство горелок позволяют после небольших регулировок переходить с одного топлива на другой. С экологической точки зрения природный газ считается самым предпочтительным. В качестве жидкого топлива чаще всего используют мазут, соляровое или печное топливо, сжиженный пропан (бутан). Тяжелые виды жидкого топлива подвергают предварительному нагреву с тем, чтобы его консистенция (вязкость 20 сСт) позволяла осуществлять ввод в
распыленном состоянии, необходимом для полного сгорания.
При неполном сгорании топлива возможны:
-сбои в работе горелки (засорение, трудности с розжигом);
-загрязнение системы пылеочистки (масляная пленка на фильтрах или на поверхности воды);
-снижение теплоотдачи (увеличенный расход топлива, уменьшение температуры газов, появление конденсата в пылеуловителе);
-ухудшение свойств готовой асфальтобетонной смеси (остатки топлива понижают вязкость битума и смачиваемость минеральных частиц).
Способы обнаружения неполного сгорания топлива:
-электронный контроль цвета пламени (автоматическое отключение горелки);
-прерывистый, «кашляющий» звук при работе горелки (должен быть ровный гул горелки).
При нарушении соотношения между воздухом (недостаток воздуха в горелке, подсос воздуха в магистрали дымососа) и топливом эффективность работы горелки резко падает. Мощность дымососа является определяющим фактором при сушке и нагреве материалов. Объем перекачиваемого дымососом газа (воздух, влага, продукты сгорания) должен быть постоянным и регулироваться положением заслонки.
Контроль температуры горячих минеральных материалов осуществляется на выходе из сушильного барабана с помощью датчика (термопары) в днище ссыпного лотка и отградуированного милливольтметра на пульте управления, соединенных кабелем (рис.2.19). Температура факела горелки превышает 370оС. Температура газов на входе в оборудование дымососа в зависимости от вязкости битума – 120-150оС. Эффективность теплообмена, расхода топлива и работы установки в целом определяется по разнице температур дымовых газов и смеси непосредственно в точке ее выгрузки, либо газа в вытяжной трубе, расположенной между барабаном и системой пылеочистки, а смеси в точке ее выгрузки. В первом случае должно быть равенство температур, в во втором – газ должен иметь температуру не более, чем на 10-20оС выше температуры смеси. Нельзя сравнивать температуру газов, измеренную на выходе из вытяжной трубы. Температура отработанных газов определяется также с помощью термопары. Если из вытяжной трубы наблюдается синий дым, это свидетельствует о возгонке легких фракций углеводородов за счет слишком высокой температуре минерального заполнителя (газа) в точке подачи битума в технологическое оборудование завода. Температура возгонки легких фракций битума – 315оС.
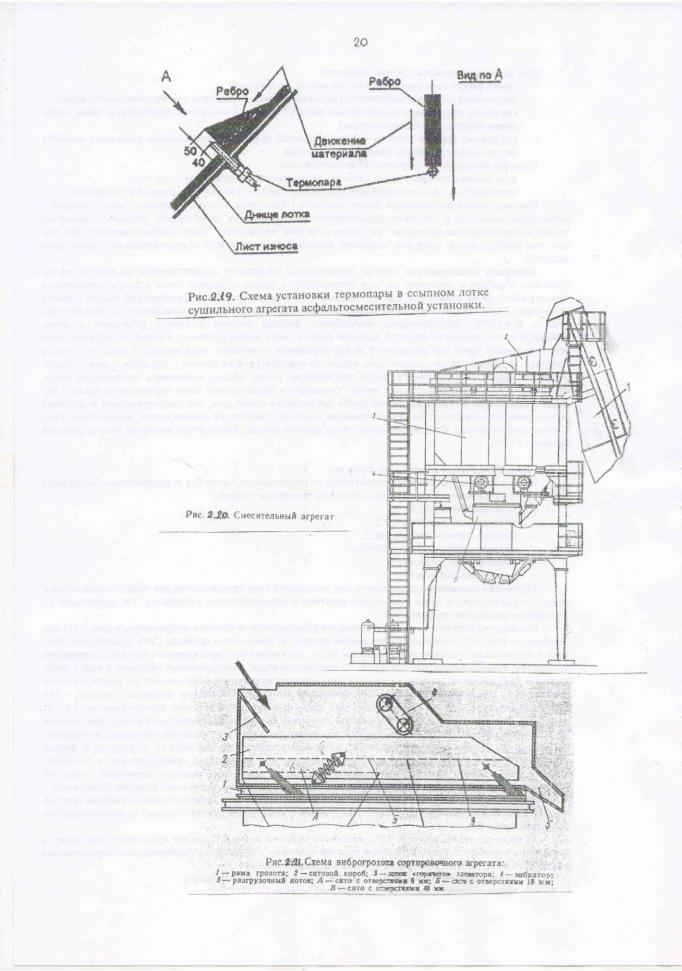
20