
9534
.pdf
Объем проводимого контроля качества сварных швов
Метод контроля, |
Тип контроли- |
Объем |
|
ГОСТ |
руемых швов |
контроля |
Примечания |
|
по таблице 1 |
|
|
|
|
|
|
Ультразвуковой |
1 и 2 |
100 % |
- |
(ГОСТ 14782) |
3 |
10 % |
Без учета объема, предусмотренного |
или |
|
|
для швов типов 1 и 2 |
радиографичес- |
4 |
5 % |
То же |
кий (ГОСТ 7512) |
5и8 |
1 % |
То же |
|
|
|
|
Примечания: 1. Методы и объем контроля сварных соединений в узлах повышенной жесткости, где увеличивается опасность образования трещин, должны быть дополнительно указаны в проектной документации.
2.В конструкциях и узлах, характеризующихся опасностью образования холодных и слоистых трещин в сварных соединениях, контроль качества следует производить не ранее, чем через двое суток после окончания сварочных работ.
3.Указанный в таблице объем контроля качества сварных швов не распространяется на соединения стальных конструкций железнодорожных и автодорожных мостов; резервуаров и газгольдеров; корпусов доменных печей и кауперов; сосудов, работающих под давлением; гидротехнических сооружений; магистральных технологических трубопроводов.
По результатам неразрушающего контроля швы сварных соединений должны удовлетворять требованиям, указанным в таблице 9.1.3.
Т а б л и ц а 9.1.3
Допустимые размеры дефектов сварных швов, установленных по результатам ультразвукового контроля
|
|
Категория |
|
|
Вид |
шва (тип |
Допустимые размеры и расположение дефекта |
|
|
дефекта |
шва) |
|
|
|
|
|
|
|
|
Трещины |
Все |
Не допускаются трещины любой ориентации и длины |
|
|
|
|
|
|
|
|
|
|
Не допускаются кроме дефектов глубиной не более 1 мм, |
|
|
|
I |
расположенных на ребрах жесткости, к которым не |
|
Подрезы. |
|
прикрепляются элементы связи и прочее |
|
|
|
|
|
||
Несплавле |
|
Не допускаются дефекты, расположенные поперек усилий. |
|
|
ния по |
|
|
||
|
Допускаются дефекты, расположенные вдоль усилий, |
|
||
кромкам |
II и III |
|
||
глубиной не более 1 мм при ширине до 2 мм и плавных |
|
|||
|
|
|
|
|
|
|
|
очертаниях |
|
|
|
|
|
|
|
|
|
Окончание табл. 9.1.3 |
|
Поры. |
|
I |
Не допускаются скопления и цепочки дефектов. |
|
Шлако- |
|
Допускаются единичные дефекты диаметром не более 1 |
|
|
|
|
|
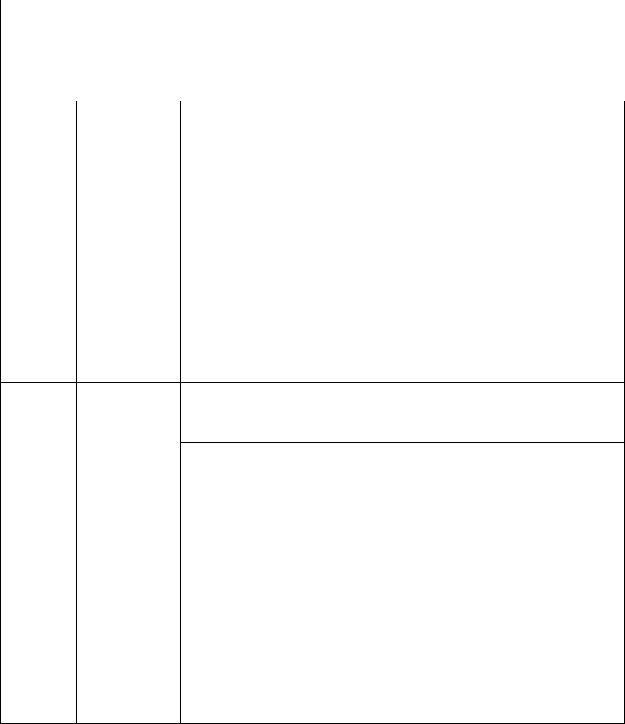
вые |
|
мм для проката толщиной до 25 мм и не более 4 % |
|
включе- |
|
толщины для проката толщиной свыше 25 мм. При этом |
|
ния |
|
количество дефектов не должно превышать четырех на |
|
|
|
|
участке длиной 400 мм, а расстояние между ними должно |
|
|
|
быть не менее 50 мм |
|
|
|
Допускаются скопления и цепочки дефектов на отдельных |
|
|
|
участках шва суммарной площадью не более 5 % площади |
|
|
|
продольного сечения шва на участке длиной не более 50 |
IIмм, при этом расстояние между близлежащими концами цепочки должно быть не менее 400 мм. Допускаются единичные дефекты диаметром не более 2 мм в количестве не более шести на участке длиной 400 мм при расстоянии между ними не менее 10 мм
Допускаются |
скопления |
и |
цепочки |
дефектов |
IIIпротяженностью не более 20 % длины шва. Допускаются единичные дефекты диаметром не более 3 мм в количестве не более шести на участке длиной 400 мм
IНе допускается кроме угловых швов нахлесточных и тавровых соединений, в которых полный провар не предусмотрен в проектной документации
Непро- |
|
|
вары в |
|
Допускаются непровары высотой не более 5 % толщины |
корне |
|
свариваемых элементов и длиной не более 50 мм при |
шва |
II (тип 4) |
расстоянии между концами не менее 400 мм (возможность |
|
|
установления более льготных требований может быть |
|
|
согласована с проектной организацией в зависимости от |
|
|
условий эксплуатации) |
Межва- |
I |
Допускаются глубиной не более 0,5 мм |
ликовые |
II (тип 4) |
Допускаются глубиной не более 1 мм |
впадины |
|
|
в много- |
|
Допускаются: глубиной не более 1,5 мм для угловых швов |
про- |
II (тип 5) |
с катетом 10-12 мм и не более 2 мм при размерах катета |
ходных |
|
14-20 мм |
швах |
|
|
9.2. Требования к объему ультразвукового контроля и оценке качества сварных швов стальных сосудов и аппаратов низкого и
среднего давления

Метод контроля качества стыковых и угловых сварных соединений в сосудах и аппаратах низкого и среднего давления определяется в соответствии с требованиями нормативно-технической документации по промышленной безопасности. При этом обязательному контролю подлежат:
а) стыковые, угловые, тавровые сварные соединения, доступные для этого контроля в объеме не менее указанного в табл. 9.2.2.
б) места сопряжения (пересечений) сварных соединений; в) сварные соединения внутренних и наружных устройств по указанию в
проекте или технических условиях на сосуд (сборочную единицу, деталь); г) сварные соединения элементов из стали перлитного класса с элементами из
сталей аустенитного класса в объеме 100%; д) сварные стыковые соединения "поковка + лист", "лист + литье", "поковка +
поковка", "поковка + труба", "поковка + сортовой прокат", доступные для этого контроля, в объеме 100%;
е) перекрываемые укрепляющими кольцами участки сварных швов корпуса, предварительно зачищенные заподлицо с наружной поверхностью корпуса;
ж) прилегающие к отверстию участки сварных швов корпуса, на которых устанавливаются люки и штуцера, на длине, равной D S , (D - внутренний диаметр корпуса, S - толщина стенки корпуса в месте расположения отверстия).
Объем ультразвукового контроля сварных швов сосудов и аппаратов низкого и среднего определяется в зависимости от группы сосуда (табл. 9.2.1).
Контроль сварных соединений, в том числе и мест сопряжений сварных соединений, сосудов 5б группы, работающих под давлением не более 0,03 МПа (0,3 кгс/см2) или без давления, а также сварных швов опор физическими методами допускается не проводить, если нет специальных указаний в проекте.
При выявлении недопустимых дефектов в сварном соединении сосудов 3, 4, 5а и 5б групп обязательному контролю тем же методом подлежат все однотипные сварные соединения по всей длине соединений.
В сварных соединениях элементов сосудов и аппаратов не допускаются следующие внутренние дефекты: трещины всех видов и направлений; свищи; непровары (за исключением местных внутренних непроваров в области смыкания корневых швов и в корне шва, см. ниже), расположенные в сечении сварного соединения; поры, шлаковые и вольфрамовые включения.
Т а б л и ц а 9.2.1.
Определение групп сосудов и аппаратов низкого и среднего давления
Групп |
Расчетное давление, |
Температура стенки, |
|
Рабочая среда |
||
а |
МПа (кгс/см2) |
°С |
|
|||
|
|
|
||||
|
|
|
Взрывоопасная |
или |
||
1 |
Более 0,07 (0,7) |
Независимо |
пожароопасная |
или 1- |
||
го, |
2-го |
классов |
||||
|
|
|
||||
|
|
|
опасности |
|
||
|
Более 0,07 (0,7) |
Выше 400 |
Любая, за исключением |
|||
|
До 2,5 (25) |
|||||
2 |
|
|
указанной для 1-й |
|||
Более 2,5 (25 |
|
|
||||
|
Выше 200 |
|
группы сосудов |
|||
|
До 5,0 (50) |
|
||||
|
|
|
|
|

|
Более 5,0 (50) |
Независимо |
|
|
|
|
|
Более 4,0 (40) |
Ниже минус 40 |
|
|
|
|
|
До 5,0 (50) |
|
|
|
|
|
|
|
|
|
|
|
|
|
Более 0,07 (0,7) |
Ниже минус 20 |
|
|
|
|
|
До 1,6 (16) |
|
От 200 до 400 |
|
|
|
|
Более 1,6 (16) |
до |
До 400 |
|
|
|
|
2,5 (25) |
|
|
|
|
|
3 |
|
|
|
|
|
|
Более 2,5 (25) |
до |
|
|
|
|
|
|
До 200 |
|
|
|
||
|
4,0 (40) |
|
|
|
|
|
|
|
|
|
|
|
|
|
Более 4,0 (40) |
до |
От минус 40 до 200 |
|
|
|
|
5,0 (50) |
|
|
|
|
|
|
|
|
|
|
|
|
4 |
Более 0,07 (0,7) |
до |
От минус 20 до 200 |
|
|
|
1,6 (16) |
|
|
|
|
||
|
|
|
|
|
|
|
|
|
|
|
Взрывоопасная |
|
или |
5а |
До 0,07 (0,7) |
|
Независимо |
пожароопасная |
или |
1, |
|
2, 3-го |
классов |
||||
|
|
|
|
|||
|
|
|
|
опасности |
|
|
|
|
|
|
Взрывобезопасная |
или |
|
5б |
До 0,07 (0,7) |
|
Независимо |
пожаробезопасная |
или |
|
|
|
|
|
4-го класса опасности |
Т а б л и ц а 9.2.2.
Объем проводимого ультразвукового контроля качества сварных швов стальных сосудов и аппаратов низкого и среднего давления
Группа сосуда |
Длина контролируемых сварных |
|
соединений от общей длины, % |
||
|
||
1,2 |
100 |
|
3 |
50 |
|
4,5а |
25 |
|
5б |
10 |
Примечание. Требование относится к каждому сварному соединению.
В сварных соединениях элементов сосудов и аппаратов допускается местный внутренний непровар, расположенный в области смыкания корневых швов, глубиной не более 10% толщины стенки корпуса, но не более 2 мм и суммарной протяженностью не более 5% длины шва:
-в двухсторонних угловых и тавровых сварных соединениях с полным проплавлением патрубков внутренним диаметром не более 250 мм;
-в сварных швах сосудов 2, 3, 4, 5а и 5б групп, предназначенных для работы в средах, не вызывающих водородную и сероводородную коррозию.
Также допускается непровар в корне шва глубиной (высотой) не более 10% номинальной толщины свариваемых элементов, но не более 2мм и суммарной протяженностью не более 20% длины шва:
-в кольцевых стыковых сварных соединениях, доступных для сварки только с

одной стороны и выполненных без подкладного кольца, сосудов 4-й и 5б групп, предназначенных для работы при температуре выше 0°С, а также в змеевиках;
- в угловых сварных соединениях.
9.3. Требования к объему ультразвукового контроля и оценке качества сварных швов стальных сосудов, цистерн, бочек, баллонов, барокамер высокого давления
Для установления объемов контроля сварных соединений сосудов, работающих под высоким давлением, определяется группа сосуда в зависимости от расчетного давления, температуры стенки и характера среды (табл.9.3.1.).
В тех случаях, когда в табл.9.3.1 отсутствуют указанные сочетания параметров по давлению и температуре, для определения группы следует руководствоваться максимальным параметром.
Температуру стенки определяют на основании теплотехнического расчета или результатов измерений, а при отсутствии этих данных принимают равной температуре среды, соприкасающейся со стенкой сосуда.
Объем ультразвукового контроля сварных швов сосудов, работающих под высоким давлением, в зависимости от группы сосуда приведен в табл. 9.3.2. При этом следует отметить, что указанные в табл.9.3.2 объемы неразрушающего контроля качества сварных соединений могут быть уменьшены по согласованию с Ростехнадзором в случае массового изготовления, в том числе при неизменном технологическом процессе, специализации сварщиков на отдельных видах работ и высоком их качестве, подтвержденном результатами контроля за период не менее 6 месяцев. Копия разрешения вкладывается в паспорт сосуда.
Т а б л и ц а 9.3.1.
Определение групп сосудов, работающих под высоким давлением
Групп |
Расчетное давление, |
Температура стенки, |
Рабочая среда |
|
а |
МПа (кгс/см2) |
°С |
||
|
||||
|
|
|
Взрывоопасная или |
|
|
|
|
пожароопасная или 1- |
|
1 |
Более 0,07 (0,7) |
Независимо |
го, 2-го классов |
|
|
|
|
опасности по ГОСТ |
|
|
|
|
12.1.007. |
|
|
До 2,5 (25) |
Ниже - 70, выше 400 |
|
|
|
Свыше 2,5 (25) до 4 (40) |
Ниже - 70, выше 200 |
|
|
2 |
Свыше 4 (40) до 5 (50) |
Ниже - 40, выше 200 |
|
|
Свыше 5 (50) |
Независимо |
Любая, за исключением |
||
|
||||
|
До 1,6 (16) |
От - 70 до - 20. |
указанной для 1-й |
|
|
От 200 до 400 |
группы сосудов |
||
|
|
|||
|
Свыше 1,6 (16) до |
От - 70 до 400 |
|
|
3 |
2,5(25) |
|
||
|
|
|||
|
Свыше 2,5 (25) до 4(40) |
От - 70 до 400 |
|
|
Свыше 4 (40) до |
5(50) |
От - 40 до 200 |
|
4 |
До 1,6 (16) |
|
От - 20 до 200 |
|
Т а б л и ц а 9.3.2.
Объем проводимого ультразвукового контроля качества сварных швов стальных сосудов, работающих под высоким давлением
Группа сосуда |
Длина контролируемых сварных |
|
соединений от общей длины, % |
||
|
||
1 |
100 |
|
2 |
100 |
|
3 |
Не менее 50 |
|
4 |
Не менее 25 |
Примечания: 1. Требование относится к каждому сварному соединению.
2.Сварные соединения сосудов, снабженных быстросъемными крышками, подлежат неразрушающему контролю в объеме 100%.
3.Для сосудов 3-й и 4-й групп места неразрушающего контроля устанавливаются отделом технического контроля организации-изготовителя после окончания сварочных работ по результатам внешнего осмотра.
Качество сварных соединений считается неудовлетворительным, если в них при любом виде контроля будут обнаружены внутренние или наружные дефекты, выходящие за пределы норм, установленных Правилами и техническими условиями.
Всварных соединениях сосудов, работающих под давлением, и их элементов не допускаются следующие дефекты:
-трещины всех видов и направлений, расположенные в металле шва, по линии сплавления и в околошовной зоне основного металла; непровары (несплавления) в сварных швах, расположенные в корне шва или по сечению сварного соединения (между отдельными валиками и слоями шва и между основным металлом и металлом шва); подрезы основного металла, поры, шлаковые и другие включения, размеры которых превышают допустимые значения, указанные в НД; наплывы (натеки); незаваренные кратеры и прожоги; свищи; смещение кромок свыше норм, предусмотренных Правилами.
Возможность допущения местных непроваров в сварных соединениях сосудов оговаривается в нормативной документации, согласованной в установленном порядке.
9.4. Требования к объему ультразвукового контроля и оценке качества сварных швов вертикальных цилиндрических стальных резервуаров для нефти и нефтепродуктов низкого давления
Объем контроля сварных соединений резервуаров физическими методами определяется в рабочей документации КМ в зависимости от:
-класса резервуара по степени опасности;
-категории сварного шва;
-уровня расчетных напряжений в сварном соединении;
-условий и режима эксплуатации резервуара, включая температуру

эксплуатации, цикличность нагружения, сейсмичность района и т.д.
В зависимости от объема и места расположения резервуары подразделяются на три класса:
класс I - особо опасные резервуары объемом 10000 м3 и более, а также резервуары объемом 5000 м3 и более, расположенные непосредственно по берегам рек, крупных водоемов и в черте городской застройки;
класс II - резервуары повышенной опасности объемом от 5000 до 10000м3;. класс III - опасные резервуары объемом от 100 до 5000 м3;.
Степень опасности учитывается при проектировании специальными требованиями к материалам, объемами контроля в рабочей документации КМ, а также при расчете коэффициентом надежности по назначению.
Объем ультразвукового контроля сварных швов стенки вертикальных цилиндрических стальных резервуаров для нефти и нефтепродуктов, изготавливаемых и монтируемых методом рулонирования, в зависимости от класса резервуара, приведен в табл. 9.4.1.
Объем ультразвукового контроля сварных швов стенки вертикальных цилиндрических стальных резервуаров для нефти и нефтепродуктов, изготавливаемых и монтируемых методом полистовой сборки, в зависимости от класса резервуара приведен в табл. 9.4.2.
Обязательному контролю подлежат участки всех вертикальных сварных соединений в зонах примыкания к днищу длиной не менее 240 мм на резервуарах объемом более 1000 м3.
При выборе зон контроля вертикальных и горизонтальных соединений преимущественное внимание уделяется проверке качества мест пересечения швов.
Т а б л и ц а 9.4.1
Объем контроля сварных соединений рулонных полотнищ стенки резервуаров, изготавливаемых и монтируемых методом рулонирования, %
|
РВС III класса |
|
|
Зона контроля |
объемом 1000м3 |
РВС II класса |
РВС I класса |
|
и более |
|
|
Вертикальные |
|
|
|
сварные |
|
|
|
соединения в |
|
|
|
поясах |
|
|
|
1, 2 |
10 |
25 |
50 |
3, 4 |
5 |
10 |
25 |
остальных |
- |
5 |
10 |
Горизонтальные |
|
|
|
сварные |
|
|
|
соединения между |
|
|
|
поясами |
|
|
|
1-3 |
5 |
10 |
15 |
3-5 |
2 |
5 |
10 |
остальными |
- |
2 |
5 |

Т а б л и ц а 9.4.2
Объем контроля сварных соединений рулонных полотнищ стенки резервуаров, изготавливаемых и монтируемых
методом полистовой сборки, %
|
РВС III класса |
|
|
Зона контроля |
объемом 1000м3 |
РВС II класса |
РВС I класса |
|
и более |
|
|
Вертикальные |
|
|
|
сварные |
|
|
|
соединения в |
|
|
|
поясах |
|
|
|
1, 2 |
25 |
50 |
100 |
3, 4 |
10 |
25 |
50 |
5,6 |
5 |
10 |
25 |
остальных |
- |
5 |
10 |
Горизонтальные |
|
|
|
сварные |
|
|
|
соединения |
|
|
|
между поясами |
|
|
|
1-2 |
5 |
10 |
20 |
2-3 |
2 |
5 |
10 |
3-4 |
- |
2 |
5 |
остальными |
- |
1 |
2 |
При обнаружении недопустимых дефектов сварного шва должны быть определены границы дефектного участка. Если в сварном соединении установлен уровень дефектности более 10%, то объем контроля таких швов удваивается.
Т а б л и ц а 9.4.3
Максимально допустимые размеры объемных дефектов для 4-го класса сварного соединения на участке сварного шва длиной 100мм
Толщина |
Поры или включения |
Суммарная |
||
свариваемых |
Ширина (диаметр), |
|
||
Длина, мм |
длина, мм |
|||
элементов, мм |
мм |
|||
|
|
|||
До 3 |
0,5 |
1,5 |
5,0 |
|
3 5 |
0,6 |
2,0 |
6,0 |
|
5 8 |
0,8 |
2,5 |
8,0 |
|
8 11 |
1,0 |
3,0 |
10,0 |
|
11 14 |
1,2 |
3,5 |
12,0 |
|
14 20 |
1,5 |
5,0 |
15,0 |
|
20 26 |
2,0 |
6,0 |
20,0 |
|
26 34 |
2,5 |
8,0 |
25,0 |
|
34 45 |
3,0 |
9,0 |
30,0 |

Т а б л и ц а 9.4.4
Максимально допустимые размеры объемных дефектов для 5-го класса сварного соединения на участке сварного шва длиной 100мм
Толщина |
Поры или включения |
Суммарная |
||
свариваемых |
Ширина (диаметр), |
|
||
Длина, мм |
длина, мм |
|||
элементов, мм |
мм |
|||
|
|
|||
До 3 |
0,6 |
2,0 |
6,0 |
|
3 5 |
0,8 |
2,5 |
8,0 |
|
5 8 |
1,0 |
3,0 |
10,0 |
|
8 11 |
1,2 |
3,5 |
12,0 |
|
11 14 |
1,5 |
5,0 |
15,0 |
|
14 20 |
2,0 |
6,0 |
20,0 |
|
20 26 |
2,5 |
8,0 |
25,0 |
|
26 34 |
3,0 |
10,0 |
30,0 |
|
34 45 |
4,0 |
12,0 |
40,0 |
Оценку допустимости объемных дефектов (пор, шлаковых и окисных включений) сварных швов соединения поясных листов можно проводить как при радиографическом контроле в зависимости от класса сварного соединения (ГОСТ 23055-78). При этом сварные соединения резервуаров III-го класса относятся к 6- му классу; соединения резервуаров II-го класса – к 5-му классу; соединения резервуаров I-го класса – к 4-му классу.
В табл. 9.4.3 – 9.4.5 приведены максимальные допустимые размеры объемных дефектов для участка проверки сварного шва длиной 100мм указанных выше классов сварных соединений при толщине свариваемых элементов до 45мм.
Т а б л и ц а 9.4.5
Максимальные допустимые размеры объемных дефектов для 6-го класса сварного соединения на участке сварного шва длиной 100 мм
Толщина |
Поры или включения |
Суммарная |
||
свариваемых |
Ширина (диаметр), |
|
||
Длина, мм |
длина, мм |
|||
элементов, мм |
мм |
|||
|
|
|||
До 3 |
0,8 |
3,0 |
8,0 |
|
3 5 |
1,0 |
4,0 |
10,0 |
|
5 8 |
1,2 |
5,0 |
12,0 |
|
8 11 |
1,5 |
6,0 |
15,0 |
|
11 14 |
2,0 |
8,0 |
20,0 |
|
14 20 |
2,5 |
10,0 |
25,0 |
|
20 26 |
3,0 |
12,0 |
30,0 |
|
26 34 |
4,0 |
15,0 |
40,0 |
|
34 45 |
5,0 |
20,0 |
50,0 |
Примечание (к табл. 9.4.3 – 9.4.5). При различной толщине свариваемых элементов максимально допустимый размер пор или включений выбирается по меньшей толщине.
В сварных соединениях элементов стенки резервуаров для нефти и нефтепродуктов не допускаются следующие дефекты: трещины всех видов и направлений, расположенные в металле шва, по линии сплавления и в околошовной зоне основного металла; непровары (несплавления) в сварных швах; подрезы основного металла; поры, шлаковые и другие включения, размеры которых превышают допустимые значения, указанные в нормативных документах (табл. 9.4.3 - 9.4.5); наплывы (натеки); незаваренные кратеры и прожоги; свищи; смещение кромок свыше норм, предусмотренных Правилами (ПБ 03-605-03).
10. УЛЬТРАЗВУКОВОЙ КОНТРОЛЬ НЕСПЛОШНОСТЕЙ ТОЛСТОЛИСТОВОГО ПРОКАТА
10.1. Проведение контроля несплошностей толстолистового проката
При подготовке листового проката к контролю выполняют следующие операции:
-оценивают визуально состояние проката с целью проверки соответствия требованиям стандартов и технических условий по геометрическим размерам и форме;
-для реализации заданной чувствительности контроля в зависимости от качества поверхности листового проката проводят частичную или сплошную обработку поверхности. Подготовку поверхности под контроль проводят аналогично подготовке под ультразвуковую дефектоскопию сварных соединений
итолщинометрию;
-проверяют при частичной обработке поверхности проката величины местных уклонов, которые должны быть не более 2% при длине зачищенного участка 50мм.
Для ультразвукового контроля могут применяться любые дефектоскопы и установки с техническими характеристиками, обеспечивающими выявление несплошностей металла, указанных в стандартах или технических условиях на продукцию.
Относительное перемещение преобразователя (преобразователей) с учетом заданной скорости сканирования должны обеспечить надежное выявление и фиксацию дефектов.
Контроль и выявление дефектов (несплошностей) листового проката выполняется эхо- и эхо-сквозным методами в сочетании с теневым.
10.2. Основные измеряемые характеристики выявленных несплошностей толстолистового проката
Оценку выявленных несплошностей металла и определения их условных размеров выполняют в соответствии с ГОСТ 28831-90.
Основными контролируемыми характеристиками при проведении ультразвукового контроля качества листового проката являются:
- чувствительность контроля;