
8267
.pdf10
рыхлые породы - пемзу, вулканические пески и пеплы, а затем некоторая часть обломков под влиянием геологических процессов слеживалась или цементировалась, образуя цементированные породы.
Важнейшими представителями обломочных пород являются пемза и вулканические туфы.
Осадочные горные породы образовались в результате длительных геологических процессов - при выветривании первичных изверженных пород или путем постепенного накопления веществ, выделенных из растворов, суспензий и механических взвесей, а также в результате накопления продуктов отмирания животных и растительных организмов. Под влиянием воды, ветра и перемены температур изверженные массивные породы, находящиеся на поверхности земли, растрескивались, разделялись на глыбы, куски и более мелкие частицы. Продукты разрушения размывались и переносились водными потоками, ветром, ледниками на большие расстояния, где затем осаждались в виде пластов.
Впроцессе физических (механических) процессов образуются такие рыхлые породы, как глина, песок, гравий, щебень или цементированные — песчаник, конгломерат, брекчия.
Врезультате химических процессов образуются: гипс, ангидрит, магнезит, доломит.
Наряду с этим, источником образования осадочных пород являются отложения отмирающего растительного мира и мелких животных организмов морей. Скелеты мелких организмов, осаждаясь на морское дно и уплотняясь, образуют пластовые отложения органогенных пород - мела, известняка, ракушечника, диатомита и др.
Метаморфические (видоизмененные) горные породы появились в результате воздействий громадных давлений и высоких температур на ранее образовавшиеся изверженные или осадочные породы. Под влиянием физикохимических процессов, протекавших в недрах земной коры, происходили глубокие внутренние изменения минералогического состава и перекристаллизация изверженных и осадочных пород и формирование новых структур метаморфических пород. Эти породы встречаются в виде массивных и сланцевых разновидностей, сохраняя иногда строение первичных изверженных или осадочных пород.
К ним относятся гнейсы, глинистые сланцы, кварцит, мраморы.
2.2. Добыча и обработка природного камня
Каменные природные материалы очень прочны, долговечны, огнестойки. Из-за положительных эксплуатационных и эстетических качеств они широко применяются для облицовочных работ, устройства полов, дорожных покрытий и пр. Отходы горнодобывающей и камнеобрабатывающей промышленности используются в качестве заполнителя для бетонов, изготовления других искусственных каменных изделий на минеральном и органическом вяжущем.
Для получения тех или иных природных каменных материалов горные
11
породы разрабатывают в карьерах и подвергают затем механической обработке. Разработка каменных карьеров производится открытым и закрытым способами в зависимости от условий залегания и сложения породы. Наиболее экономичным и эффективным способом разработки месторождений горных пород является открытый способ, однако он наиболее неблагоприятен с экологической точки зрения. Выбор способа добычи, как правило, зависит от вида горной породы и условий её залегания.
Для изготовления изделий от горного массива породы отделяют блокполуфабрикат крупных размеров (4 - 5м3). Эту операцию производят взрывным, механическим способом или вручную при помощи металлических клиньев.
Природные каменные материалы и изделия получают из горных пород путём механической обработки (дробления, распиливания, раскалывания и т.п.), после которой почти полностью сохраняется структура и свойства исходной породы.
Распиловку блоков производят рамными пилами со стальными полосами, дисковыми пилами со сменными зубьями из твердых сплавов или алмазов. Для обрезки плит используются специальные дисковые станки.
Используя ударную и абразивную обработку, природному камню придают ту или иную фактуру - различный характер поверхности.
Ударная обработка дает возможность получить следующие фактуры: фактуру скалы с буграми и впадинами, как при естественном расколе породы; рифленую с правильным чередованием гребней и впадин глубиной до 2 мм; бороздчатую - с параллельными прерывистыми бороздками глубиной 0,5 -1 мм; точечную - шероховатую с точечными углублениями 0,5 - 2 мм.
Абразивная обработка включает распиливание, фрезерование, шлифовку и полировку.
Для получения профилированных изделий (ступеней, карнизов и т.п.) на камнеобрабатывающих заводах применяют камнефрезерные и универсальные профилирующие машины.
Шлифовку и полировку производят на шлифовально-полировальных станках с применением зернового абразива: корунда или мелких пылевидных алмазов. После шлифовки камень имеет гладкую матовую поверхность.
Полировка осуществляется войлочными полировальными дисками с использованием мастик и тонких полирующих порошков из оксидов металлов (алюминия хрома, олова, железа и др.) или азотнокислого олова. После полировки поверхность плотного камня становится зеркально гладкой.
Для обработки некоторых видов горных пород применяют термический метод, основанный на воздействии струи газа с высокой температурой. При такой обработке камень нагревается неравномерно, и возникающие термические напряжения вызывают скалывание верхнего слоя. В некоторых случаях с помощью термической обработки оплавляется поверхностный слой камня, что позволяет получить своеобразную «глазурованную» фактуру и изменить естественный цвет породы.
12
2.3. Материалы и изделия из горных пород
Ниже приведены основные виды природных каменных материалов и изделий, применяемых в строительстве.
Бутовый камень (бут) - куски камня неправильной формы размером не более 50 см по наибольшему измерению. Бутовый, камень может быть рваный (неправильной формы) и постелистый. Из бута возводят плотины и другие гидротехнические сооружения, его применяют для подпорных стенок и кладки фундаментов.
Щебень - куски камня размером 5-70 мм (для гидротехнического строительства до 150 мм). Получают его дроблением бутового камня. Для обеспечения нужного зернового состава щебня процесс дробления осуществляют в несколько стадий.
Гравий состоит из окатанных зерен тех же размеров, что и у щебня. Его получают просеиванием рыхлых осадочных пород, в необходимых случаях (для повышения качества) применяют промывку для удаления вредных примесей (глины, пыли).
Песок состоит из зерен различных минералов (кварца, полевого шпата, слюды и др.) с размерами менее 5 мм. Применяют природные и искусственные (дробленые) пески.
Стеновые камни получают из туфов и пористых известняков путем выпиливания механизированным способом из массива горной породы или распиловки блоков-заготовок. Камни применяют для кладки наружных и внутренних стен и перегородок.
Плиты для облицовки производятся различных размеров и различной структуры. Применяются они для наружной и внутренней облицовки зданий, сооружений, облицовки пола.
Специальные облицовки применяют для защиты от коррозии и действия высоких температур. Для защиты от растворов кислот используют андезит, гранит, сиенит, диабаз, кварцит, кремнистый песчаник и другие кислотостойкие породы.
Цокольные плиты, а также детали карнизов, поясков и других выступающих частей сооружений изготовляют из стойких к атмосферным воздействиям пород. Эти изделия не должны иметь волосных трещин, им придается такая форма и качество поверхности, чтобы на них не задерживалась вода от дождя и тающего снега.
Бортовые камни, отделяющие проезжую часть дороги от тротуара, изготовляют из плотных изверженных пород (гранита, диабаза и т.п.), отличающихся высокой морозо-, износостойкостью и прочностью.
Брусчатка для мощения дорог имеет форму бруска, слегка суживающегося книзу. Брусчатку изготовляют из однородных мелко- и среднезернистых пород (диабаза и др.). Из таких пород изготовляют шашку для мозаиковой мостовой (приближающуюся по форме к кубу) и шашку для мощения (в виде усеченной пирамиды).
13
Тротуарные плиты изготовляют из гнейсов и подобных ему слоистых горных пород. Они имеют форму прямоугольной или квадратной плиты со стороной 20-80 см с ровной поверхностью, толщиной не менее 4 см и не более
15 см.
Природные каменные материалы, работая в конструкциях или сооружениях, разрушаются под действием замерзания воды в порах и трещинах, частого изменение температуры и влажности, растворяющего действия воды и т.п.
Конструктивную защиту открытых частей сооружений (цоколей, карнизов, поясков, столбов, парапетов) сводят к приданию им такой формы, которая облегчает отвод воды. Этому же способствует гладкая полированная поверхность облицовки. Стойкость пористых каменных материалов, которые не полируются, повышают путем пропитки поверхностного слоя уплотняющими составами и нанесения на лицевую поверхность гидрофобизующих (водоотталкивающих) составов.
3.КЕРАМИЧЕСКИЕ МАТЕРИАЛЫ И ИЗДЕЛИЯ
3.1.Сырье для производства керамических материалов
Керамическими называют искусственные каменные материалы и изделия, полученные в процессе технологической обработки глиняного сырья с органическими и минеральными добавками и последующего обжига при высоких температурах. Материал, из которого состоят керамические изделия после обжига, в технологии керамики называют керамическим черепком.
Основным сырьевым материалом для производства строительных керамических изделий является глинистое сырье, применяемое в чистом виде, а чаще в смеси с добавками - отощающими, порообразующими, плавнями, пластификаторами и др.
Глинистое сырье (глины и каолины) - продукт выветривания изверженных полевошпатных горных пород, содержащий примеси других горных пород. Глинистые минеральные частицы диаметром 0,005 мм и менее обеспечивают способность при затворении водой образовывать пластичное тесто, сохраняющее при высыхании приданную форму, а после обжига приобретающее водостойкость и прочность камня.
Помимо глинистых частиц в составе сырья имеется определенное содержание пылевидных частиц с размерами зерен 0,005-0,16 мм и песчаных частиц с размерами зерен 0,16-2 мм.
Глинистые частицы имеют пластинчатую форму, между которыми при смачивании образуются тонкие слои воды, вызывая набухание частиц и способность их к скольжению относительно друг друга без потери связности. Поэтому глина, смешанная с водой, дает легко формуемую пластичную массу.
Различное сочетание химического, минералогического и гранулометрического состава компонентов обуславливает различные свойства
14
глинистого сырья и пригодность его для получения керамических изделий тех или иных свойств и назначения.
Глины, как сырьевой материал для керамической промышленности, характеризуются рядом показателей, основные из которых приведены ниже.
Пластичность - свойство глин во влажном состоянии принимать под влиянием внешнего воздействия желаемую форму без образования разрывов и трещин. Техническим показателем пластичности является число пластичности.
Усадка - уменьшение линейных размеров и объёма глиняного сырца при его сушке (воздушная усадка) и обжиге (огневая усадка). Усадку выражают в процентах от первоначального размера изделия.
Спекаемость - свойство глин уплотняться при обжиге и образовывать в результате этого камнеподобный черепок.
3.2. Общая схема производства керамических изделий
При всем многообразии керамических изделий по свойствам, формам, назначению, виду сырья и технологии изготовления основные этапы производства керамических изделий являются общими и состоят из следующих операций: добыча сырьевых материалов, подготовка массы, формование изделий, их сушка и обжиг.
Добыча глины осуществляется в карьерах обычно открытым способом экскаваторами и транспортируется на предприятие керамических изделий рельсовым, автомобильным или другим видом транспорта.
Карьерная глина в естественном состоянии обычно непригодна для получения керамических изделий. Поэтому проводится ее обработка с целью подготовки массы. Подготовку глин целесообразно вести сочетанием естественной и механической обработки. Естественная обработка заключается в вылеживании предварительно добытой глины в течение 1-2 лет при периодическом увлажнении атмосферными осадками или искусственном замачивании и периодическом замораживании и оттаивании. Механическая обработка глин производится с целью дальнейшего разрушения их природной структуры, удаления или измельчения крупных включений, удаления вредных примесей, измельчения глин и добавок а также перемешивания всех компонентов до получения однородной и удобоформуемой массы с использованием специализированных машин, некоторые из которых представлены на рис. 2.
Подготовку керамической массы в зависимости от свойств исходного сырья (карьерной влажности, содержания примесей, однородности) и вида изготовляемой продукции осуществляют полусухим, пластическим и шликерным (мокрым) способами. Способ приготовления массы определяет и способ формования и название в целом способа производства.
При полусухом способе производства глину вначале дробят, подсушивают, затем измельчают и с влажностью 8—12% подают на формование. При пластическом способе формования глину подвергают дроблению, затем
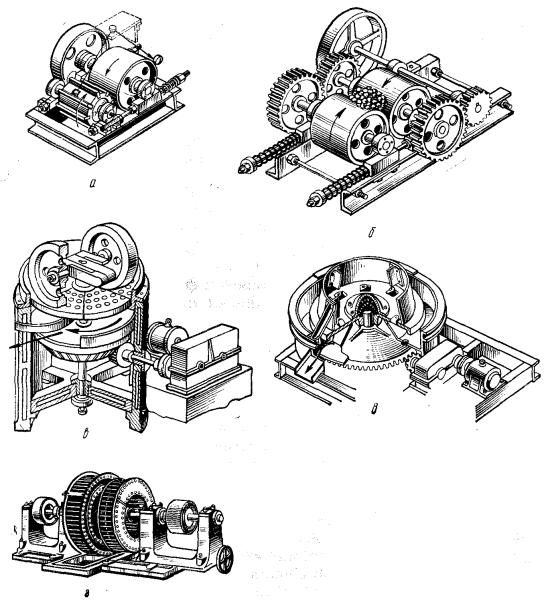
15
направляют в глиносмеситель, где производят ее перемешивание с отощающими добавками и одновременно увлажняют до получения однородной пластичной массы с влажностью 20—25%.
Рис. 2. Механизмы для измельчения глины: а - валковая дробилка; б - дезинтеграторные вальцы; в - бегуны; г - дезинтегратор; д - ножевая глинорезка
Формование керамических изделий при пластическом способе осуществляют преимущественно на ленточных прессах. При полусухом способе глиняную массу формуют на гидравлических или механических прессах под давлением. По шликерному способу исходные материалы измельчают и смешивают с большим количеством воды (до 60%) до получения однородной массы - шликера.
После формования изделия должны быть высушены до содержания влаги 5-6% во избежание неравномерной усадки, искривлений и растрескивания при обжиге. Сушка производится преимущественно в туннельных непрерывного действия или камерных периодического действия сушилах в течение
16
нескольких (до 72-х) часов в зависимости от свойств сырья, влажности сырца и вида изделий.
Обжиг - важнейший и завершающий процесс в производстве керамических изделий. Этот процесс можно разделить на три периода: прогрев высушенного сырца, собственно обжиг и регулируемое охлаждение. При нагреве сырца до 1200C удаляется физически связанная вода, и керамическая масса становится непластичной. Но если добавить воду, пластические свойства массы сохраняются. В температурном интервале от 4500C до 6000C происходит отделение химически связанной воды, разрушение глинистых минералов, и глина переходит в аморфное состояние. При этом и при дальнейшем повышении температуры выгорают органические примеси и добавки, а керамическая масса безвозвратно теряет свои пластические свойства. При 8000C начинается повышение прочности изделий благодаря протеканию реакций в твердой фазе на границах поверхностей частиц компонентов.
Впроцессе нагрева до 10000C возможно образование новых
кристаллических силикатов, например силлиманита Аl2O3•SiO2, а при нагреве до 12000C - и муллита 3Аl2O3•2SiO2. Одновременно с этим легкоплавкие соединения керамической массы и минералы - плавни создают некоторое количество расплава, который обволакивает нерасплавившиеся частицы, стягивает их, приводя к уплотнению и усадке массы в целом. После остывания изделие приобретает камневидное состояние, водостойкость и прочность.
Взависимости от назначения обжиг изделий ведется до различной степени спекания при различной температуре.
После обжига изделия остывают, штабелируются, упаковываются и поступают на склад готовой продукции.
3.3. Виды керамических изделий и способы их производства
В настоящее время керамическая промышленность выпускает целый ряд материалов и изделий, применяемых в строительстве. Основные из них, а также способы их производства представлены ниже.
Керамические кирпичи и камни изготовляются из легкоплавких глин с добавками или без них и применяются для кладки наружных и внутренних стен и других элементов зданий и сооружений, а также для изготовления стеновых панелей и блоков.
Кирпич керамический производится в форме прямоугольного параллелепипеда с размерами 250×120×65мм (одинарный) - принимается за условную единицу при пересчёте количества кирпича больших размеров или 250×120×88мм (утолщённый). Камни керамические имеют размер
250×120×138мм и др.
Кирпич может быть полнотелым и пустотелым, а камни только пустотелыми. Утолщенный и одинарный кирпич должен быть также только с круглыми или щелевыми пустотами, чтобы масса одного кирпича не превышала 4 кг. Поверхность граней может быть гладкой и рифленой.
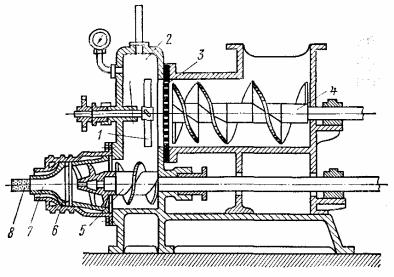
17
В зависимости от показателей прочности кирпич подразделяется на марки:75, 100, 125, 150, 175, 200, 250, 300. Марки кирпича и камней по морозостойкости: F15, F25, F35 и F50.
Производства керамического кирпича осуществляется пластическим способом по следующей схеме. Поступившую на завод глину подвергают обработке до получения пластичной однородной массы. Затем смесь поступает в глиносмеситель, где она увлажняется до 18—25% и перемешивается до получения однородной пластичной массы. Тщательно приготовленная однородная масса поступает затем в вакуумный ленточный пресс, представленный на рис.3. Поступающую в ленточный пресс глиняную массу с помощью шнека уплотняют, после чего она поступает к выходному отверстию - мундштуку. Из последнего выходит непрерывный глиняный брус, который
попадает на автомат для резки и укладки кирпичасырца на вагонетки камерных или туннельных сушил.
Производительность ленточных прессов - до 10000 шт. условного кирпича в час.
Плитки керамические и ковры из них
выпускаются методом пластического и полусухого прессования. Применяются для облицовки стен зданий, цоколей, подземных переходов и оформления других эле-
ментов зданий. Плитки выпускаются глазурованные и неглазурованные, рядовые и специального назна-чения с гладкой и рельефной поверхностью различных типоразмеров. Морозостойкость рядовых плиток, предназначенных для наружной облицовки, должна составлять не менее 35 циклов. Плитки могут поставляться в коврах. Заводы выпускают ковры с наклейкой плитки лицевой стороной на крафт-бумагу.
Изготовление керамических плиток, как правило, производится методом полусухого прессования на специальных прессах. Технологический процесс осуществляется конвейерным способом.
Черепица, имеет долговечность до 300 лет, и по этому показателю значительно превышает любые другие кровельные материалы, а по качеству и
18
по стоимости не уступает им. К недостаткам черепицы относятся необходимость большого уклона (не менее 30%) кровли и значительный вес кровли, что требует особой прочности конструкции стропил, и высокая трудоемкость кровельных работ.
Санитарно-технические керамические изделия - умывальники, унитазы,
сливные бачки, биде, писсуары, раковины и аналогичные изделия производятся из фарфоровых, полуфарфоровых или фаянсовых масс шликерным способом. Изделия покрываются блестящей однотонной или цветной глазурью.
Трубы керамические канализационные применяют для строительства безнапорных сетей канализации, транспортирующих промышленные, бытовые, дождевые, агрессивные и неагрессивные воды. Трубы изготовляются из пластичных тугоплавких и огнеупорных глин, цилиндрической формы длиной 1000-1500 мм с внутренним диаметром 150-600 мм. На одном конце имеется раструб для соединения отдельных звеньев трубопровода. Трубы должны быть водонепроницаемыми и выдерживать внутреннее давление не менее 0,15 МПа.
4. НЕОРГАНИЧЕСКИЕ ВЯЖУЩИЕ ВЕЩЕСТВА
4.1. Общие сведения и классификация
Неорганическими вяжущими веществами называют порошкообразные материалы, которые при смешивании с водой образуют пластично-вязкое тесто, способное со временем самопроизвольно затвердевать в результате физикохимических процессов. Неорганические вяжущие вещества подразделяют на воздушные и гидравлические.
Воздушные вяжущие вещества способны затвердевать и длительное время сохранять прочность только на воздухе. По химическому составу они делятся на четыре группы: гипсовые, известковые, магнезиальные и жидкое стекло.
Гидравлические вяжущие твердеют и длительное время сохраняют прочность (или даже повышают ее) не только на воздухе, но и в воде. По своему химическому составу гидравлические вяжущие вещества представляют собой сложную систему, состоящую в основном из соединений четырех видов: СаО-SiO2-Аl2Оз-Fе2О3. Эти соединения образуют три основные группы гидравлических вяжущих: силикатные цементы, состоящие преимущественно (на 75%) из силикатов кальция; к ним относятся портландцемент и его разновидности - главные вяжущие современного строительства; алюминатные цементы, вяжущей основой которых являются алюминаты; главным из них является глиноземистый цемент и его разновидности; гидравлическая известь и романцемент.
В отдельную группу выделяют вяжущие автоклавного твердения - это вещества, способные при автоклавном синтезе, происходящем в среде
19
насыщенного водяного пара, затвердевать с образованием плотного, прочного камня. В эту группу входят: известково-кремнеземистые, известково-зольные, известково-шлаковые вяжущие и др., хотя по существу они тоже относятся к гидравлическим вяжущим.
4.2. Воздушные вяжущие вещества
Гипсовые вяжущие вещества - это воздушные вяжущие, состоящие в основном из полуводного гипса или ангидрида и получаемые тепловой обработкой сырья и помолом.
Сырьем для получения гипсовых вяжущих чаще всего служит горная порода гипс, состоящая преимущественно из минерала гипса CaSO4·2H2O. Используются в качестве сырья также ангидрит CaSO4 и отходы промышленности (фосфогипс - от переработки природных фосфатов в суперфосфат, борогипс и др.).
Гипсовые вяжущие вещества подразделяются в зависимости от температуры тепловой обработки на две группы: низкообжиговые и высокообжиговые.
Низкообжиговые гипсовые вяжущие получают тепловой обработкой природного гипса при низких температурах (110-180°С). Они состоят в основном из полуводного гипса, так как дегидратация сырья при указанных температурах приводит к превращению двуводного гипса в полугидрат:
CaSO4·2H2O =CaSO4·0,5H2O+1,5H2O.
К низкообжиговым гипсовым вяжущим веществам относятся строительный, формовочный и высокопрочный гипс. Строительный гипс изготовляют низкотемпературным обжигом гипсовой породы (гипсового камня) в варочных котлах или печах. В первом случае гипсовый камень сначала размалывают, а потом в виде порошка нагревают в котлах. Имеются промышленные установки, в которых совмещены помол и обжиг. При обжиге в незамкнутом пространстве вода выделяется и удаляется в виде пара, поэтому строительный гипс состоит в основном из кристаллов CaSO4·0,5H2O, называемых β- модификацией.
Высокопрочный гипс получают термической обработкой высокосортного гипсового камня в герметичных аппаратах под давлением насыщенного водяного пара. В таких условиях вода выделяется и удаляется в капельножидком виде, поэтому высокопрочный гипс состоит в основном из полуводного сульфата кальция называемого α-модификацией, более активной, чем β- модификация. Поэтому прочность высокопрочного гипса при сжатии (1525МПа, а при специальной технологии производства - до 60МПа) превышает прочность строительного гипса. Из него изготавливают элементы стен и сборных перегородок, камни для стен.
По срокам схватывания гипсовые вяжущие делят на три группы: А - быстросхватывающиеся (2-15 мин), Б - нормальносхватывающиеся (6-30 мин) и В - медленно схватывающиеся (начало схватывания не ранее 20 мин, конец