
книги / Электронно-лучевая сварка и смежные технологии
..pdfцинк, бронза (кадмий >0,6%, свинец >0,5%), латунь. Это объясня ют тем, что под действием высококонцентрированного электрон ного пучка в вакууме происходит их взрывное вскипание, это при водит к выбросу основной массы расплава, т. е. сплошность литой зоны не достигается; реализуются скорее условия резки, чем свар ки. Не свариваются также автоматные, цементированные и низко углеродистые стали с высокой концентрацией углерода, серы, фос фора и других элементов из-за образования трещин и ряда других дефектов, а также из-за низких механических и прочностных ха рактеристик сварного соединения.
Электронно-лучевая сварка позволяет соединять довольно большое количество комбинаций разнородных и разноименных ма териалов, в том числе из растворимых и нерастворимых друг в друге материалов: нержавеющая сталь+инвар, нержавеющая сталь+алю м иний, 12Х18Н 10Т+ВН 2АЭ, 12Х18Н10Т+ЭЛН1, 12X 18H 10T+N b, нерж авею щ ая сталь+УУ-сплав (10% С,1% С о,1% С г), нержавею щ ая сталь+тантал, нержавеющая сталь SUS316+хастеллой X, нержавеющая сталь 8118304+никель, нержаве ющая сталь SUS304+Meflb, нержавеющая сталь 8118304+углеродистая сталь, нержавеющая сталь ЗиЭЗОФщиркаллой 2 (вставка из Ад), не ржавеющая сталь SUS304(nnn321 )+сталь 2,25 Cr-Мо, сталь слаболетрованная 2,25 Сг-Мо+хасгеллой X (иногда применяют вставку из AI), сталь 20+медь М1, быстрорежущая сталь (S6-5-2-5 или S6-5-2)+ynpy- гая сталь (48 CrMoV67; 50CrV4; 45CrV19), инструментальная сталь+- ни зко угл е р о д и ста я сталь, сталь 45+бронза ОЦН, чугун GRB20+6poH3a ОЦН, алюминий+титан, алюминий+медь, алюминий+никель, медь+инвар, медь+серебро, медь+вольфрам, медь+ +никель, медь+манганин, медь+ниобий, бериллиевая медь+фосфористая бронза, Бр.ХУ (или Бр. ХЦрТ)+ЭП666, сплав 73,5%Си- 22,7%Zn-3.4AI-0,4%Co+Ag, 48КНФ+36 НХТЮ, вольфрам+Сг-Си- сплав, вольфрам+серебро, вольфрам+молибден, вольфрам+тантал, молибден+ниобий, молибден+тантал, керамика, напыленная W +медь (сварка-пайка), керамики 22ХС.М7, ЦМ-332+нержаве- ющая сталь 12Х18Н10Т, титан, ниобий, цирконий, тантал, молиб ден, вольфрам (нагрев+сварка).
Количество соединяемых пар может быть увеличено, если в стык свариваемых деталей вводить вставку в виде фольги толщиной 0,1-0,8 мм из специально подобранного связующего металла. Для соединения разнородных материалов используется как режим сварки, так и режим сварки-пайки.
электронно-лучевой сварки |
141 |
Типы стыковых соединений
Для однопроходной электронно-лучевой сварки прим еня ют разнообразные типы соединений (рис. 57), многие из кото рых используют и для других способов сварки плавлением. Х а рактерны ми типами соединений для электронно-лучевой свар ки являются соединения под сварку проникающим электронным
142 |
Технология |
пучком (рис. 57, ж), под сварку в углублении и труднодоступных местах (рис. 57, г), под сварку тавров через полку (рис. 57, л). От бортовку кромок (рис. 57, в) применяют, обычно, в изделиях ра диоэлектроники и приборостроения. Соединения под сварку про никающим электронным пучком допускаются для металлов ма лых и средних толщин. Тавровые соединения (рис. 57, л) можно выполнять на металлах толщиной не более 10-12 мм. Остальные соединения допускаются для металлов любой толщины.
Технологические схемы сварки
Сварку электронным пучком можно осуществлять с определен ными ограничениями в любых пространственных положениях. Напри мер, для листовых материалов сварку в нижнем положении (рис. 58, а, 6) выполняют как без подкладки, так и на подкладке. Ее применя ют для соединения сталей толщиной до 40 мм, титановых и алюмини евых сплавов толщиной до 80 мм. Наиболее предпочтительна свар ка на боку (рис. 58, в-д ) и на подъем (рис. 58, е), которую выполняют для металлов любой толщины, в основном без подкладки. Для пре дотвращения вытекания расплава из сварочной ванны при сварке с глубоким проплавлением иногда устанавливают ограничительную планку вдоль нижней кромки стыка (рис. 58, г). Сварку в по толочном положении (рис. 58, ж ) выполняют на металлах толщиной до 20 мм и приме няют чрезвычайно редко.
Аналогичныетехнологичес кие схемы сварки тел враще ния показаны на рис. 59 и 60.
Подготовка стыка
Р азделка кром ок. Для однопроходной электронно лучевой сварки не требует ся обязательной разделки кром ок. Разделку кром ок применяют лишь в необхо димых случаях для улучше ния качества формирования сварного шва и для обеспе чения надежной работоспо собности систем слежения
электронно-лучевой сварки |
143 |
за стыком. Для предотвращения или уменьшения усиления или уширения верхней части сварного шва обычно используются V - и П-образные разделки кромок (рис. 61, а, б). V-образную раздел ку используют также для систем слежения за стыком. В нижней части стыка иногда выполняют П -образную разделку кром ок (рис. 61, в) для исключения обратного валика сварного шва или для установки фиксирующего буртика узкой подкладки либо L-образ- ную разделку (рис. 61, г) для подварки корневой части сварного шва дуговыми методами сварки. Для предотвращения занижения (неполномерности) шва при сварке тонкостенных конструкций приме
няют о тб о р то вку к р о м о к
(рис. 61, д).
Допустимая ширина зазо ра в стыке для электронно лучевой сварки не должна превышать 0,1 -0,2 м м при толщ ине м еталла 3 - 3 0 и 0,3 мм — при толщине бо лее 30 мм.
Очистка. Для обеспече ния высокого качества свар ного шва очистке от средств консервации, загрязнений, ржавчины и оксидных пле нок подвергают в обязатель ном порядке стыкуемые по верхности, внешние и внут ренние (в случае сквозного проплавления) поверхности деталей на расстоянии до 100 мм от кром ки при свар ке толстолистовых металлов и до 10 мм при сварке тонко листовых металлов. Предва рительную очистку выполня ют механически, а оконча тельную — в зависимости от свариваемого металла и сте пени шероховатости очищае мой поверхности различными
144 |
Технология |
физико-химическими спосо бами (химическое травле ние, электрополировка, тле ющий разряд, шабрение). Н е по ср е д стве нно перед сваркой внешнюю поверх ность свариваемых деталей в области стыка и стыкуемые поверхности (насколько воз можно через зазор в стыке) очищают с помощью нагре ва маломощным сканирую
щим элек-тронным пучком, |
Рис. 60. Основные технологические |
|||
не заплавляя при этом стык. |
схемы внутритрубной сварки |
|||
Размагничивание. Эле |
электронным пучком: а — дуговая |
|||
менты конструкций, детали |
прихваточная подварка наружной части |
|||
механизмов и конструкции в |
стыка; б, г — сварка изнутри |
|||
целом в зависимости от мар |
вертикальным или горизонтальным |
|||
электронным пучком; в — окончательная |
||||
ки материала в процессе из |
||||
дуговая заварка наружной части стыка с |
||||
готовления приобретают ос |
одновременной переваркой корневой |
|||
таточную намагниченность. |
части внутреннего шва |
|||
Осредненные значения при |
|
|
|
|
ращения остаточной намаг |
|
|
|
|
ниченности конструкций в |
|
|
|
|
ходе выполнения укрупнен |
|
|
|
|
ных технологических опера |
Ш |
2 |
E J |
|
ций приведены на рис. 62. |
||||
Реальные уровни магнит |
|
|
|
|
ных полей на поверхности |
|
р ц |
|
|
деталей и конструкций из ста |
в |
|
|
|
лей, склонных к остаточному |
1-2 мм |
Г |
||
намагничиванию, могут дос |
|
|
|
|
тигать нескольких единиц и |
|
|
|
|
даж е десятков мТл. |
|
|
Рис. 61. Типы |
|
Кроме того, детали, узлы |
|
\ '\ \ Ц |
разделок кромок |
|
и целые конструкции из фер |
|
— |
для электронно |
|
|
|
лучевой сварки |
ромагнитных материалов в процессе эксплуатации (особенно при использовании технологий
с магнитными полями) также приобретают дополнительную намаг ниченность.
электронно-лучевой сварки |
145 |
Остаточная намагниченность изделий приводит к ряду негатив ных явлений:
■возникновению «магнитного дутья» при дуговой электро сварке и наплавке, что ведет к повышенному разбрызгива нию жидкого металла из сварочной ванны и образованию различных дефектов сварного соединения, а также к непо паданию в свариваемый стык или в место наплавки;
■искривлению траектории электронного пучка при электрон но-лучевой сварке и соответствующему непровару стыка по всей толщине;
■налипанию металлической стр уж ки при ш там п о вке или обработке деталей металлорежущим инструментом, что ухудшает качество обработки и ускоряет изнашивание штам пов и инструмента;
■электроэрозионны м разрушениям подш ипников, муфт, уплотнений и других узлов турбоагрегатов при возникнове нии паразитны х электрических токов от вращающихся на-
магни ченных узлов.
Остаточные магнитные поля в изделиях из ферромагнитных ма териалов отклоняют электронный пучок и электрическую дугу при сварке от плоскости стыка. Компенсировать этот уход электронно го пучка от стыка возможно лишь при сварке тонколистовых мате риалов (при условии однородного распределения намагниченнос ти вдоль стыка) с помощью отклоняющей системы сварочной элек тронной пушки. В остальных случаях необходимо размагничива ние изделия.
Операцию размагничивания необходимо осуществлять после сборки стыкового соединения непосредственно перед загрузкой из делия в вакуумную камеру или подачей в зону сварки/наплавки.
Размагничивание — это процесс воздействия внешнего магнит ного поля, в результате которого уменьшается намагниченность ферромагнитного материала. Намагниченному ферромагнетику со ответствует преимущественная ориентация доменов, которая в процессе размагничивания дезориентируется так, что результиру ющая намагниченность равняется нулю.
Способы размагничивания классифицируют следующим образом:
■термическое размагничивание, выполняемое повышением температуры ф ерромагнитного материала выш е точки Кюри и последующим охлаждением до температуры окру ж а ю щ е й среды при отсутствии в неш него м а гни тно го поля;
146 |
Технология |
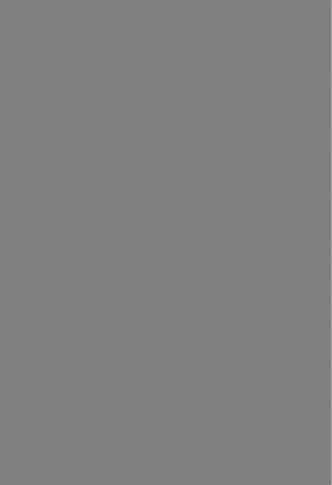
свойства кристаллов и изменяются структура кристаллической ре шетки, теплоемкость, электропроводность и другие физические ха рактеристики.
Наиболее применяемым способом размагничивания является периодическое перемагничивание с убывающей амплитудой, на пример с помощью соленоидов или намагничивающих контуров. Недостаток размагничивания изделия переменным током промыш ленной частоты состоит в том, что электромагнитное периодичес кое поле в ферромагнитном металле быстро затухает и проникает в него на незначительную глубину. Таким образом, в плавно убы вающем периодическом поле промышленной частоты (50 Гц) из делие размагничивается только снаружи. После удаления размаг ничивающей катушки глубинные остаточные магнитные поля сно ва наводят магнитные полюса в поверхностном слое, т. е. полное размагничивание не происходит.
Для преодоления указанного недостатка предложен метод, зак лючающийся в намагничивании изделий реверсивным постоянным током в пределах гистерезисной петли с убывающей амплитудой тока намагничивания в катушке тороида 1н (рис. 63).
Намагничивание максимально при замкнутом магнитопроводе. Поэтому при размагничивании колец диаметром 500 мм с тол щиной стенки 100 мм использована схема тороида — непосред ственно на изделие наматывают 20 витков мягкого сварочного ка беля. Могут быть применены другие формы электромагнитных ка тушек в зависимости от конфигурации изделий.
Регулирование и реверсирование силы тока при этом осущ е ствляют вручную с периодическим включением и отключением преобразователя ЗП -7,5/30 с выдержкой >3 с (рис. 64).
Размагничивание происходит по всему сечению до полного снятия магнитных полей, если начальное значение амплитуды Н заведомо больше коэрцитивной силы Нс. Для соленоида напря женность магнитного поля определяется по формуле
H=0,47ENIH/L, |
(153) |
где N — число витков; 1н — намагничивающий ток; L — длина со леноида.
Намагниченность изделий измеряют гауссметром. Остаточные матитные поля можно обнаружить с достаточной точностью и при помощи иголки с ниткой. Иголка должна быть из магнитомягкого мате риала (например, из трансформаторного железа). Перед контрольной проверкой иголку размагничивают нагревом выше температуры Кюри.
148 |
Технология |
+200
|
|
|
" |
| - | |
|
|
|
|
П п г-. |
|
|
|
|
□"U L T+n |
_ |
- |
- |
- |
-I L |
|
|
|||
|
|
|
|
-2 0 0
Рис. 63. Изменение силы тока в намагничивающей катушке. Число циклов п=100
Рис. 64. Принципиальная схема размагничивания тороида (изделия с намотанной катушкой): Р — реверсивный переключатель тока 1н; Ш — шунт;П — микроамперметр М265; Г — преобразователь постоянного тока с независимым возбуждением и размагничивающей последовательной обмоткой (ПР); Н О — обмотка независимого возбуждения, питается от маломощного генератора-возбудителя ГВ типа С И П -30
Таким образом, полностью снять магнитные поля по всему се чению изделия можно только при намагничивании его реверсив ным постоянным током в пределах гистерезисной петли с постепенно убывающей амплитудой. Максимальную начальную амплитуду на пряженности размагничивающего поля устанавливают в 5-10 раз больше коэрцитивной силы материала изделия. Снижение ампли туды напряженности поля после каждого периода перемагничивания должно составлять примерно 1%. Частота перемагничива-
электронно-лучевой сварки |
149 |
ния для изделий толщиной более 5 мм не должна превышать 0,5 Гц. При этом объект перемагничивается по безгистерезисной кривой намагничивания. Магнитодинамические процессы, связанные с за вершением всех необратимых процессов смещения и вращения междоменных границ, обеспечивают за счет энергии электромаг нитного поля специальной рабочей обмотки. При электромагнитной обработке больших конструкций используют временные обмотки:
■рабочую шпангоутную (РШ О) в виде секций соленоида из кабеля НРШ М сечением 200-300 мм2, которая генерирует энергию электромагнитного поля, необходимую для раз магничивания;
■компенсационные (КГО, КБО), из кабеля НРШ М сечением 50-70 м м 2,которые при размагничивании ком пенсирую т магнитное поле Земли в объеме конструкции.
Много времени (несколько суток) затрачивают на монтаж рабо чей обмотки РШ О (километры кабеля), весьма тяжелые (физичес кие) и трудоемкие монтажные работы обычно выполняют вручную.
Размагничивание конструкций протекающим током основы ва ется на способе электрофизической обработки (ООО «ДС», Нико лаев), использующем энергию электромагнитного поля от протека ющего электрического тока. Размагничивание осуществляют про пуская по толще конструкции импульсов электрического тока, из меняющихся по заданному закону. Способ не требует применения соленоидов и рабочих контуров.
Поток энергии, который вносится при электрофизической обра ботке непосредственно в объем материала, зависит от плотности электрического тока. Неравномерность распределения плотности тока возрастает по мере увеличения размеров конструкции и име ет максимум вблизи оси протекания тока между точками подклю чения. Варьирование точек подключения зажимов позволяет на правленно изменять уровень воздействия электромагнитного поля от протекающего тока на заданный объем металла крупногаба ритной конструкции (локальное размагничивание).
Новая технология размагничивания позволяет быстро и высо кокачественно устранить остаточную намагниченность изделий без применения традиционных соленоидов и рабочей обмотки РШ О .
Рассмотрим физический механизм электрофизической обра ботки (пропускание по толще стали импульсов электрического тока, изменяющихся по определенному закону). Условие завер шения всех необратимы х процессов см ещ ения и вращ ения
150 |
Технология |