
книги / Электронно-лучевая обработка в сварке
..pdfДля обеспечения таких скоростей испарение приходится вести из жидкой (расплавленной) фазы. Испарение из твердого состояния, т.е. путем сублимации, проводят только в специальных случаях.
На скорость испарения существенно влияет наличие загрязнений, например оксидов и карбидов. Плотность их меньше, чем плотность расплава; они всплывают на поверхность и частично покрывают ее, снижая тем самым скорость испарения. Это нежелательное явление отсутствует в тех случаях, когда загрязнения имеют высокое давление пара, когда они испытывают термическое разложение или когда пар способен диффундировать сквозь слой загрязнений. Высокие температуры поверхности, характерные для прямого нагрева, стимулируют процессы термического разложения загрязняющих слоев на поверхности расплава. Применяя исходные материалы высокой чистоты и осуществляя испарение из водоохлаждаемых тиглей, можно свести влияние загрязнений на скорость испарения до малого уровня.
Нанесение покрытий из сплавов требует обеспечения одинакового соотношения компонентов сплава как по всей поверхности подложки, так и по толщине слоя. Слои из сплавов напыляют двумя методами – многотигельного испарения или однотигельного испарения [1].
При многотигельном испарении компоненты испаряются порознь, каждый из своего тигля, а конденсируются на подложке совместно. При однотигельном испарении поток пара создается и конденсируется, имея тот состав, который требуется для покрытия. Вариантом однотигельного испарения является процесс, аналогичный фракционной возгонке, когда из тигля с большим количеством расплавленного вещества его испаряют покомпонентно, изменяя мощность подогрева по определенному графику. Для электронно-лучевого испарения более характерен вариант однотигельного испарения расплава, запас которого в тигле непрерывно пополняется подачей материала, имеющего тот же состав, который требуется для наносимого слоя.
21
Испарение соединений сопровождается частичной или полной их диссоциацией, и получить из таких соединений простым испарением тонкие пленки заданного состава невозможно. Однако для ряда соединений, таких как хлориды, сульфиды, селениды, теллуриды, а также полимеры, благодаря малой степени диссоциации или вследствие рекомбинации компонентов при конденсации, возможность термического напыления все же существует.
Пригодность соединения для указанной цели ограничивается не только диссоциацией, но зачастую еще и способностью реагировать с материалом тигля, что приводит к изменениям в составе слоя. Эти границы частично расширяются при применении электроннолучевых способов испарения, использующих водоохлаждаемые тигли. Возможность избежать таким путем реакций в тигле позволяет проводить испарение некоторых химически высокоактивных соединений.
Поскольку при нагреве электронным пучком на поверхности испарения можно достичь высоких температур, испарению поддаются нелетучие и тугоплавкие соединения (окись алюминия, окись кремния, различные стекла, а также карбиды).
Для того чтобы, несмотря на процессы термической диссоциации при столкновениях, получать из определенных соединений покрытия с заданным составом, используют различные приемы.
Так, при реакционном напылении во время процессов испарения и конденсации из испаряемого компонента и реагента, вводимого в рабочий объем в газообразном состоянии, образуется химическое соединение. Реакционное напыление применялось ранее для получения оксидов испарением металлов или низших оксидов. В настоящее время оно наиболее часто используется при получении покрытий и из других соединений, в первую очередь из карбидов и нитридов.
Другая возможность получения покрытий из соединений заключается в испарении, например, двух компонентов, которые реагируют друг с другом при совместной конденсации на подложке в требуемом соотношении. Один из вариантов этого способа заклю-
22
чается в том, что компоненты конденсируются в нужной пропорции, а химическое соединение образуется при завершающей термообработке. Так, например, получают покрытия из карбида титана.
Промышленное применение электронно-лучевого испарения благодаря его преимуществам существенно потеснило традиционные способы испарения и, кроме того, открыло новые возможности.
При внедрении электронно-лучевого испарения во многие отрасли электроники (например, в технологию тонких пленок, полупроводниковых и оптоэлектронных приборов, устройств памяти) и
впроизводстве обычных элементов электроники (пленочных конденсаторов, резисторов, разъемов) к устройствам электронно-лучевого испарения стали предъявляться самые разнообразные требования. Основным из них является требование высокой чистоты слоя, которое достигается при испарении из водоохлаждаемых тиглей.
Возможность испарения с помощью электронно-лучевого нагрева различных оксидов (двуокиси кремния, окиси алюминия, стекла) используют в оптической промышленности для покрытия поверхности стекол и синтетических материалов твердыми, устойчивыми против царапин, прозрачными пленками и для нанесения защитных покрытий на изделия электроники. Ряд возможностей применения электронно-лучевого испарения основан на испарении тугоплавких и химически высокоактивных материалов из водоохлаждаемых тиглей, при котором достигается высокая удельная поверхностная мощность на ванне расплава.
Высокие скорости испарения, реализуемые в электронно-луче- вом испарителе, позволяют покрывать большие поверхности слоями толщиной 10 мкм и выше. Примером может служить нанесение антикоррозийных покрытий на стальную ленту.
Попытки экономически эффективного нанесения слоев большой толщины и слоев с особыми свойствами, как, например, с заданными показателями твердости или износостойкости, пока еще не вышли за рамки эксперимента. В будущем они могут вылиться
впроизводство изделий и полуфабрикатов с покрытиями, полученными способами электронно-лучевого напыления, в таких отраслях,
23
как инструментальная промышленность, общее и энергетическое машиностроение.
Для того чтобы иметь возможность эффективно и экономично решать разнообразные задачи техники нанесения покрытий, разработан ряд установок стандартных и специальных типов. Для малогабаритных подложек основные концепции установки определяются вопросами вакуумной техники, и здесь применяют установки стандартных типов, встраивая их в производственный агрегат в соответствии с решаемой задачей. Если же для концепции установки определяющими являются особенности решаемой технологической задачи, например размеры и форма подложки, то приходится конструировать специальные установки. Примерами таких установок являются агрегаты для нанесения покрытий на стальную ленту, на листовое стекло или для изготовления фольги.
2.2. Электронно-лучевая плавка металлов
Свойства металлов определяются как их составом, так и содержанием в них газов и примесей. Для рафинирования металлов часто применяют их переплав. Материалы высокой чистоты можно получать путем переплава в вакууме с помощью электронного пучка.
Кроме того, электронно-лучевая плавка является весьма удобным способом получения слитков тугоплавких и химически высокоактивных металлов. Здесь используются такие особенности элек- тронно-лучевой плавки, как высокая удельная поверхностная мощность в рабочем пятне пучка и наличие вакуума, препятствующего поглощению газов в ходе плавки.
Возможность управлять мощностью пучка в пространстве и времени позволяет осуществить ряд вариантов процесса, которые трудно или невозможно провести другими методами вакуумной металлургии.
Электронно-лучевая плавка обеспечивает очень глубокое рафинирование металла, так как осуществляется при низком рабочем давлении в технологической камере. Кроме того, в отличие от дуго-
24

вой вакуумной плавки, можно устанавливать скорость плавки и подводимую электрическую мощность независимо друг от друга, тем самым варьируя температуру материала и время его пребывания в расплавленном состоянии. Таким образом, областью применения электронно-лучевого переплава является производство особо чистых сталей и выплавка слитков и фасонных отливок из химически активных и тугоплавких металлов.
Процесс плавки изображен на рис. 2.2, где показано взаимное расположение электронной пушки, переплавляемой заготовки и кристаллизатора. Часть мощности пучка расходуется для нагрева переплавляемого металла на торце заготовки до температуры плавления. Расплавляясь, материал в виде капель перетекает в ванну расплава в кристаллизаторе.
Рис. 2.2. Принцип электронно-лучевого переплава: 1 – электронная пушка; 2 – электронный пучок, направляемый на расплавляемый штабик 5 и ванну расплавленного металла 7; 3 – откачка вакуума; 4 – плавильная камера; 6 – капли переплавляемого металла; 8 – выплавляемый слиток; 9 – водоохлаждаемый кристаллизатор; 10 – устройство вытяжки слитка
Скорость плавки пропорциональна мощности пучка, приходящейся иа расплавляемую заготовку. Другая часть мощности пучка подводится в кристаллизатор. Она должна быть достаточной для того, чтобы материал в ванне находился в расплавленном состоянии
25
вплоть до стенки кристаллизатора. Это дает возможность получать слитки с гладкой боковой поверхностью. Если кроме формирования такого слитка требуется проводить еще и рафинирование расплава, то мощность, подводимую в кристаллизатор, следует увеличить.
Чтобы зеркало жидкой ванны в кристаллизаторе находилось при плавке на одном и том же уровне, слиток непрерывно вытягивают вниз. Вакуум, потребный в плавильной камере, определяется необходимостью транспортировать пучок от пушки до кристаллизатора в камере с минимальными потерями и конкретной металлургической задачей.
Вследствие сложности процесса плавки, как правило, необходим визуальный контроль за всем ее ходом [8].
Электронно-лучевая плавка может сочетаться с литьем. Для этого необходимым элементом является литейный тигель, в котором материал расплавляют и поддерживают жидким в достаточном количестве. Литейный тигель может быть футерованным или медным водоохлаждаемым. Керамическая футеровка тиглей и изложниц допустима только тогда, когда реакции материала футеровки с расплавом не происходят или когда они не наносят вреда качеству продукта.
Исходный материал можно подавать в литейный тигель в виде кусков или гранул; в этом случае тигель играет роль плавильного. Если же материал заливают в тигель жидким или он попадает в него каплями с расплавляемой заготовки, то тигель служит только для рафинирования. При непрерывном выпуске металла из литейного тигля можно получать слитки, аналогичные тем, которые получают при капельном переплаве. При фасонном литье химически высокоактивных и тугоплавких металлов применяют периодическую разливку. Примером специального применения непрерывного литья может служить производство фольги, при котором струя расплава направляется на охлаждаемые прокатные валки.
Если рассмотреть баланс мощности при электронно-лучевом переплаве, пренебрегая потерями мощности на заготовке, то вся мощность, подведенная электронным пучком, Рe складывается из
26
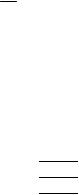
мощности на нагрев и расплавление материала Рm, мощности на перегрев ванны жидкого металла в кристаллизаторе Pk на мощность Pw, отведенную от ванны:
Pe = Pm + Pk + Pw .
Первые два слагаемых пропорциональны скорости плавки, т.е. массе, переплавляемой в единицу времени. При равных требованиях к глубине рафинирования скорость плавки выбирают пропорциональной площади зеркала ванны.
Мощность Pw, помимо физических свойств расплава, зависит от площади зеркала ванны и боковой поверхности слитка в зоне касания его стенки кристаллизатора.
Важной характеристикой процесса электронно-лучевого переплава является термический КПД процесса, определяемый следующим выражением:
η= Pm 100 %.
Pe
Значения термического КПД для различных металлов, расположенных в порядке возрастания температуры плавления, приведены в табл. 2.1.
Таблица 2.1
Значения термического КПД электронно-лучевого переплава для различных металлов
Материал |
Cu |
Fe |
Ni |
Ti |
Zr |
Mo |
Nb |
Ta |
W |
ŋ, % |
10–15 |
20–35 |
20–30 |
10–20 |
5–15 |
2–7 |
2–4 |
1–2 |
0,5–1 |
Видно, что с увеличением температуры плавления КПД резко снижается. Это объясняется ростом потерь в общей подведенной мощности с возрастанием температуры переплава.
Следовательно, для того чтобы обеспечить течение самого процесса переплава тугоплавких металлов, приходиться тратить от 80 до почти 100 % мощности пучка. И если, невзирая на столь низ-
27
кий тепловой КПД, тугоплавкие металлы все-таки подвергают переплаву в электронно-лучевых установках, то единственно потому, что другие способы не могут обеспечить такого же качества слитков.
Управление распределением мощности электронного пучка чаще всего осуществляют путем развертки электронного пучка по какой-либо траектории.
При мощности электронного пучка от 60 до 1200 кВт диаметр пятна пучка на переплавляемой заготовке и на поверхности ванны расплава находится в пределах 20...150 мм. Как правило, он меньше размера поверхности заготовки и зеркала ванны. Поэтому для достижения нужного распределения мощности пучка между заготовкой и ванной необходима программная развертка пучка.
Программное управление распределением мощности чаще всего базируется на использовании круговой или эллиптической развертки пучка. При круговой развертке пятно пучка все время перемещается вблизи края кристаллизатора, так что материал остается в жидком состоянии почти до стенки кристаллизатора.
Принцип этот, однако, применим только при малых скоростях плавки. Если требуется увеличить скорость плавки и, следовательно, долю мощности, подводимой к переплавляемой заготовке, то используют эллиптическую развертку. Подбором полуосей эллипса, описываемого пятном пучка, можно изменять скорости перемещения пятна вблизи вершин эллипса и тем самым – соотношение мощностей, отдаваемых пучком на этих участках. Вблизи вершин, лежащих на большой оси, движение пятна замедляется по сравнению с движением вблизи вершин, лежащих на малой оси. Это и используют для того, чтобы мощности, приходящиеся на переплавляемую заготовку и кристаллизатор, были различными. Зону переплава заготовки располагают у вершины эллипса, принадлежащей его большой оси.
Если поперечное сечение переплавляемой заготовки мало по сравнению с поверхностью ванны расплава, то для обеспечения требуемой высокой скорости плавки эллиптической развертки пучка оказывается недостаточно. В таких случаях прибегают к про-
28
граммам развертки с распределением мощности по площади объекта. Комбинируя две такие программы, у которых амплитуды отклонения пучка и время его воздействия управляются по отдельности, можно реализовать требуемое распределение мощности между переплавляемой заготовкой и ванной.
Перспективы развития электронно-лучевой плавки обусловлены потребностями ядерной, аэрокосмической техники, электроники и химической технологии в особо чистых материалах, сохраняющих прочностные свойства при высоких температурах или обладающих высокой химической стойкостью.
В настоящее время в мире насчитывается несколько сотен электронно-лучевых плавильных установок, работающих в промышленности.
Электронно-лучевая плавка занимает прочные позиции в производстве слитков из ниобия и тантала. В металлургии титана и других высокоактивных и тугоплавких металлов, а также кремния, повышается значение электронно-лучевой плавки как способа переработки возвратных отходов производства. В электроннолучевых плавильных печах во все возрастающих масштабах получают титановое фасонное литье.
Расширение промышленного применения электронно-лучевого переплава стали происходит замедленно из-за развития конкурирующих с электронно-лучевым способов. Перспективна здесь выплавка крупных (массой более 10 т) слитков при высоких требованиях к равномерности свойств стали по поперечному сечению слитка. Для решения этой задачи требуются электронно-лучевые плавильные установки мощностью от 5 до 10 МВт [3].
2.3. Электронно-лучевая сварка
При электронно-лучевой сварке кинетическая энергия электронов пучка используется для того, чтобы расплавить жестко ограниченные участки примыкающих друг к другу деталей с тем, чтобы расплав, застывая, соединил детали. Положительной сторо-
29
ной электронно-лучевого способа сварки является возможность создания относительно высокой удельной поверхностной мощности в пятне пучка при достаточно высоких значениях мощности всего пучка. В силу этого при электронно-лучевой сварке прогрев зон деталей, примыкающих к расплаву, меньше, чем при других способах сварки плавлением. Ввиду того, что процесс электронно-лучевой сварки ведется в вакууме, этим способом можно сваривать детали из химически активных металлов.
Свойства электронного пучка открывают возможность сварки тугоплавких материалов и таких комбинаций материалов и деталей, которые не поддаются сварке другими способами.
Электронно-лучевая сварка позволяет получать сварные соединения с отношением глубины шва к его ширине, намного большим единицы, чего невозможно добиться другими способами сварки плавлением.
Процесс сварки протекает следующим образом. При достаточной поверхностной мощности электронного пучка в месте его встречи с поверхностью детали появляется небольшая ванночка с расплавом. Если увеличить удельную поверхностную мощность, сфокусировав пучок более остро, то в обрабатываемом материале образуется паровая полость – канал проплавления. Этот эффект называют эффектом глубокого (кинжального) проплавления.
Рассмотрим, как формируется канал проплавления в металле. При воздействии концентрированного электронного пучка на материал электроны проникают в металл на глубину, определяемую по уравнению Шонланда
δ = k U 2 ,
ρ
где δ – глубина проникновения электронов в вещество; k – постоянный коэффициент; U – ускоряющее напряжение; ρ – плотность материала. Так, при U = 30 и U = 150 кВ глубина проникновения электронов в алюминий составляет соответственно 7 и 175 мкм.
30