
книги / Новые материалы и технологии.-1
.pdfлегкие и недорогие конструкции, т.е. получать оптимальные из делия.
Рассмотрим основные сцособы формования изделий из композиционных материалов. При этом будем иметь в виду, что здесь структура материала взаимосвязана со способом формова ния, а способ формования зависит от формы изделия.
4.1. Намотка
Намотка в настоящее время является самым широко при меняемым методом формования изделий из волокнистых компо зитов. Выбор этого метода определяется, прежде всего, геометри ческой формой будущего изделия - тела вращения (труба, обо лочка, конус, параболоид, сосуд давления самый разной формы - кокон, шар, овалоид и др.). Возможна намотка и коробчатых кор пусных изделий со скругленными ребрами, а также изделий дру гих форм. Намотка по сравнению с другими методами формова ния позволяет помимо формы обеспечить и высокие механиче ские характеристики изделия. Она дает возможность наиболее эффективно оптимизировать схему армирования изделия, учиты вая направления и уровни действующих нагрузок и напряжений. Намотка всегда подразумевает механическую укладку армирую щего материала со связующим по определенным траекториям в виде слоя и далее наращивание количества слоев до полного на бора толщины изделия. Именно намоткой изготовляют боль шинство корпусных и оболочечных изделий в ракетно-косми ческой отрасли (рис. 6).
Существует несколько видов намотки:
•кольцевая;
•спирально-перекрестная;

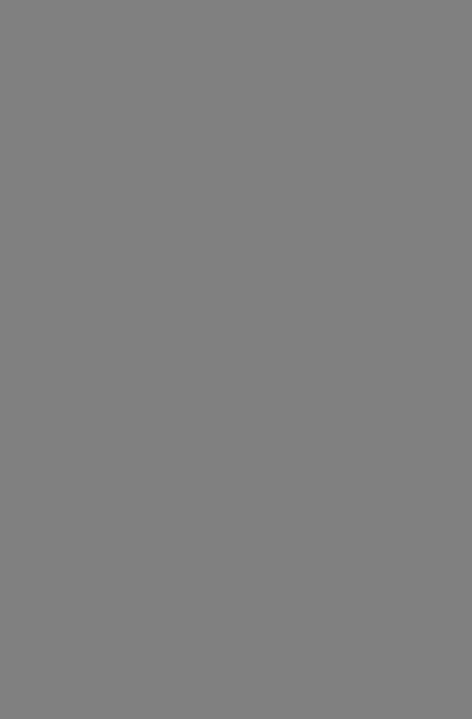
широко применяется при формовании различных изделий; осо бенно эффективна «мокрая» намотка при изготовлении крупно габаритных конструкций сложной формы.
«Сухой» метод формования заключается в том, что арми рующий материал заранее пропитывают связующим, делая это на специальном оборудовании. Выделение пропитки в само стоятельную технологическую операцию позволяет получать ленту со связующим лучшего качества. Пропитка ленты проис ходит при ее протяжке через ванночку со связующим. При этом используется низковязкий состав, получаемый введением в него растворителей (спиртово-ацетоновой смеси). Это значительно повышает качество пропитки ленты. Далее пропитанная лента проходит через сушильную камеру, и из связующего испаряется растворитель. На выходе из камеры пропитанная и подсушенная лента наматывается на приемную кассету. Такая лента со свя зующим называется препрегом. При «сухом» методе обеспечи вается более четкий контроль процентного содержания связую щего и равномерное его распределение по слоям при намотке. «Мокрый» и «сухой» методы применяются как при кольцевой намотке, так и при других видах намотки.
При кольцевой намотке укладка ленты производится в на правлении, близком к кольцевому, т.е. виток к витку, и перпен дикулярно к оси оправки. При этом получается однонаправлен но-армированный композит. Главным движением является вра щение оправки, раскладчик с лентой перемещается вдоль оси оправки, обеспечивая продольную подачу с заданным шагом. Шаг подачи равен ширине ленты (при намотке в£тык) или не сколько меньше ее (при намотке внахлест). ПрИ достижении крайнего положения (края оправки) подачу реверсируют и на-
матывают следующий слой. Так слой за слоем идет процесс на мотки, до полного набора заданной толщины изделия. Кольце вая намотка применяется как самостоятельный вид для формо вания всего изделия (всех слоев), так и в комбинации с другими видами намоток (например со спирально-перекрестной). В за ключение укажем средние значения основных технологических параметров намотки: скорость намотки (скорость ленты) 5...20 м/мин, натяжение ленты 0,2...0,5 от ее разрывной нагруз ки, температура связующего при пропитке ленты 20...60 °С, вязкость связующего 20...80 с (по вискозиметру ВЗ-4), нанос связующего на ленту 30...50 % (по объему).
Спирально-перекрестная намотка. При этом виде на мотки шаг подачи значительно больше ширины ленты. Укладка ленты осуществляется по спирали, проходящей с одного конца оправки до другого. Затем осуществляется реверс подачи и лен та укладывается по обратной спирали, которая пересекается с предыдущей. Так проход за проходом, витки спиралей посте пенно закрывают всю поверхность оправки, образуя структур ный слой. Схема спирально-перекрестной намотки показана на рис. 8.
Рис. 8. Схема спирально-перекрестной намотки: I - оправка; 2 - лента; 3 - раскладчик; S - продольная подача; b - ширина ленты; со - вращение оправки; а - заданный угол армирования
Такая намотка значительно сложнее кольцевой. Здесь сле дует рассчитывать параметры намотки: шаг подачи, длину на мотки, ширину ленты, фазу поворота ленты в районе реверса подачи. Это необходимо, чтобы обеспечить равномерное запол нение (покрытие) поверхности оправки и одинаковую толщину получаемого слоя. Заданный угол армирования (а) обеспечива ется при намотке за счет величины шага подачи. Спирально перекрестной намоткой создается армирование композита в двух направлениях (±а). Конструкционная прочность такого композита больше прочности композита, полученного при коль цевой намотке.
Продольно-поперечная намотка. Схема этой намотки показана на рис. 9. Заметим, что название видов намоток связа но с направлениями укладки ленты. В данном виде намотки реа-
Рис. 9. Схема продольно-поперечной намотки: 7 - оправ ка; 2 - вертлюг с катушками продольных лент; 3 - про дольные ленты; 4 - наматываемая оболочка; 5 - кольце вая (поперечная) лента; б катушка с кольцевой лен той; сов - вращение вертлюга; со - вращение оправки; 5Ви
SK- подачи вертлюга и кольцевой катушки
лизуются два направления укладки: продольное (вдоль оси оп равки) и поперечное (кольцевое). Такая намотка называется продольно-поперечной (ППН).
Продольный слой укладывается одновременно большим количеством лент, сходящих с вертлюга, вращающегося син хронно с оправкой (в одну сторону, с той же угловой скоро стью). При этом вертлюг дополнительно движется поступатель но вдоль оправки. Параллельно с укладкой продольного слоя, поверх его, идет намотка поперечного слоя отдельной лентой со специального раскладчика. В формировании продольного слоя участвуют п лент (катушек), ширина лент и их количество под бираются таким образом, чтобы при укладке они ложились встык друг к другу, тем самым образуя сплошной слой. Кольце вой слой наматывается одной лентой. В данном методе намотки удобнее использовать ленты - препреги. Благодаря совмещению продольной укладки и поперечной намотки обеспечивается вы сокая производительность процесса формования. Этот способ в основном применяют при изготовлении крупногабаритных ци линдрических оболочек.
Спирально-кольцевая намотка. Это комбинация двух видов намотки: спиральной и кольцевой, реализуемых на одном намоточном станке. Спирально-кольцевая намотка широко при меняется при изготовлении труб, замкнутых оболочек и других изделий. На рис. 10 показан вариант применения этой намотки на примере оболочки типа «кокон» с полюсными отверстиями.
Для такой намотки применяют пятикоординатный про граммный станок (рис. 11), так как это наиболее сложный вид намотки. Станок позволяет последовательно формировать на оправке спиральные и кольцевые слои. Спиральный слой фор-
мируют по всей поверхности оправки, а кольцевой - на ее ци линдрической части. Соотношение спиральных и кольцевых слоев, их толщины рассчитывают заранее и задают как техноло гические параметры. Для столь сложных по форме изделий раз работаны управляющие программы, в соответствии с которыми идет процесс намотки слоев.
со
Рис. 10. Схема совмещенной спирально-кольцевой намот ки изделия типа «кокон»: 1 - оправка; 2 - раскладчик кольцевой намотки; 3 - лента кольцевой намотки; 4 - лен та спиральной намотки; 5 - раскладчик спиральной на мотки; П - продольная подача; S - продольная подача кольцевой ленты; R - радиальная подача; ш - вращение оправки - главное движение; ср - угол разворота расклад
чика; а - угол укладки спиральной ленты
Непрерывная намотка с использованием шаговой оп
равки. Этот способ применяется при массовом производстве
стеклопластиковых труб. Отличие данной технологии заключа
ется в следующем:
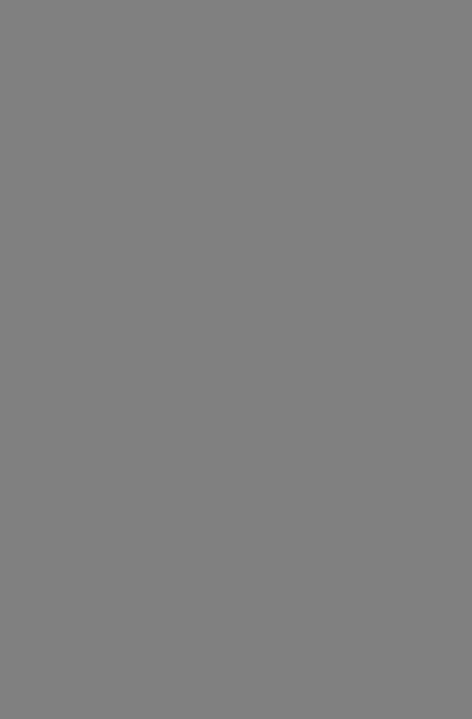
4.2. Прессование
Прессование является одним из самых применяемых ме тодов формования изделий из композитов. Дадим определение этого метода. Прессование - это формование изделия под дав лением из пресс-материалов, нагретых до вязкотекучего состоя ния, с последующим отверждением. Прессование осуществляет ся двумя способами:
• прямым, когда пресс-материал загружается непосредст венно в полость формы, здесь же к нему прикладывается давле ние (рис. 12);
Рис. 12. Схема прямого прессования (слева - начало прессования, справа - окончание прес сования): 1 - плита обогрева; 2 - пуансон; 3 - матрица; 4 - прессуемая деталь; 5 - навес ка; б - выталкиватель; 7 - нагреватель матрицы