
книги / Технология строительной керамики
..pdfСушка, помол и рассев глинистых материалов. При подготовке масс (пресс-порошков) полусухим способом сушке глинистого сырья предшествует предварительное измельчение его на дробильно-помоль ном оборудовании.
В зависимости от объемов производства для сушки глины обычно применяют прямоточные сушильные барабаны длиной от 8 до 14 м и диаметром от 0,8 до 2,8 м (СМ-45А, СМ-147А и др.). Барабаны уста навливают на опорных роликах под углом 3—5° к горизонту. Топочные
700
I£б00
§•
Щ500
т
зоо
200
100
0 |
1 2 |
3 |
4 |
- |
3 |
6 |
7 |
8 |
|
|
|
|
|
|
Длина барабана,н |
||
Рис. 27. |
Кривые зависимости от длины барабана: |
|
|
|||||
/ — температуры |
теплоносителя; |
2 — температуры глины; 3 — тепло- |
||||||
потери о |
сушильном барабане (о |
% |
на каждом |
участке его длины). |
газы перед подачей в сушильный барабан разбавляются в камере сме шения холодным воздухом до 650—800° С. Температура отходящих газов ПО— 140° С, а скорость 1,5—2,0 м/с. Резкое снижение темпера туры теплоносителя в начале барабана связано с обогревом холодной глины и потерями в окружающую среду (рис. 27). Удельный расход тепла — 4145 кДж/кг испаренной влаги. Частичное использование отходящих газов — возврат в камеру смешения (рециркуляция) снижа ет расход тепла на 16— 18%. Температура глины после сушки— не более 60—80° С.
Основной недостаток в работе сушильного барабана — большой перепад по влажности из-за неравномерной сушки, достигающий 15%, так как за время нахождения глины в барабане (20—30 мин) мелкие частицы пересушиваются, а крупные — не досушиваются. Равномер ность сушки регулируют степенью заполнения барабана материалом (около 5%) и скоростью вращения (3—6 об/мин).
Съем глины с 1 м3 объема барабана составляет ПО— 135 кг/ч, а ко личество испаряемой влаги — 50—60 кг. Расход условного топлива
на 1000 шт. кирпича — 70—90 кг, электроэнергии — 3—4 кВт/ч. Затрата рабочей силы на 1 т высушенной глины — 0,20—0,25 чел/ч.
Для повышения производительности, улучшения качества сушки и увеличения выхода мелких фракций в сушильных барабанах уста навливают цепные завесы. К внутренней поверхности барабана поего окружности на расстоянии 0,2—0,35 м друг от друга в шахматном по рядке крепятся цепи длиной 1—2 м, по 20—25 цепей в ряду. Таких цепных завес две: первая на участке длиной 1—2 м, вторая — 1,4 м. Вторая завеса расположена на расстоянии 0,4 м от выходного конца
Рис. 28. Схема помольно-сушиль ного агрегата FZS:
1 — ножевой барабан; 2 — гладкие вальцы; 3 — разгребающий барабан;
4 — пластинчатый |
конвейер; 5 |
— |
|||
пьезоэлектрический |
датчик; |
6 |
— |
||
смесительная |
камера; 7 — эавих- |
||||
ряющая |
камера; 8 |
— сепараторная |
|||
камера; 9 — отражательная |
плита; |
||||
10 —* молотковый |
барабан; |
11 |
— |
||
горячие |
газы; |
12 |
— высушенный |
||
молотый |
материал. |
|
|
|
барабана. Цепи первой завесы (200—250 шт.) разбивают комья глины, чем уменьшают неравномерность сушки и ускоряют ее. Цепи второй завесы (140— 175 шт.) измельчают подсушенную глину, превращая час тично сушильный барабан в помольный агрегат. Оборудование сушиль ного барабана цепными завесами увеличивает производительность в 2—2,3 раза и выход фракций меньше 5 мм в 12— 15 раз, при этом сни жается неравномерность пофракционной влажности.
Сушка глинистых материалов возможна также в скоростных бараба нах, башенных и фонтанных сушилках, путем совмещения процессов сушки и помола в аэробильных (шахтных) мельницах, в сушилках ки пящего слоя и др. Обезвоживание суспензий проводят в распылитель ных сушилках. Если продолжительность сушки глины в сушильном барабане составляет 20—30 мин, то в аэробильных мельницах — 1—2 с, в кипящем слое — 10—20 с.
Наиболее простая схема совмещения сушки и помола глины в од ном агрегате достигается тогда, когда молотковая (роторная) мельница работает по замкнутому циклу с воздушным сепаратором, Материал
Рис. 29. Схемы включения помольно-су шильного агрегата:
а — открытый цикл работы; б — закрытый цикл работы с шаровой мельницей; о — закры тый цикл работы при двух материалах с раз ной влажностью (/ — помольно-сушильный агрегат; 2 — подача влажного материала; 3 — резерпиый подтопок; 4 — выход готового про дукта; 5 — электрофильтр; 6 — циклон; 7 — сепаратор; 8 — шаровая мельница; 9 — пода ча сухого материала; 10 — дробилка). Сплош ной линией указано движение материала, штриховой — теплоносителя.
поступает через тарельчатый пита тель на мельницу, измельчается, выносится воздушным потоком в сепаратор или пылеосадительную камеру, откуда поступает в бункер. Крупные частицы из сепаратора возвращаются на домол в мельницу. Горячий воздух или газы при 500— 600° С подаются в мельницу и вы сушивают материал, находящийся во взвешенном состоянии в момент измельчения.
Наибольшие трудности встре чаются при необходимости тонкого помола влажных вязких материа лов (глины с влажностью до 30%). Помол таких материалов на обыч ном оборудовании невозможен изза налипания, а организация пред варительной сушки не' всегда возможна и дорого стоит. В этом случае применяются помольно-су шильные агрегаты, специально со зданные для тонкого помола влаж ного вязкого глинистого сырья.
Агрегат (рис. 28) включает мо лотковую мельницу с барабаном, расположенным над полукруглым дном. Специальный питатель подает
вмельницу материал, предваритель но подсушиваемый горячими газами
всмесительной камере. После из мельчения и дополнительной под
сушки в процессе помола материал поступает в систему сепарации и вы ходит из агрегата с заданной степенью помола — до 1 мм и влаж ностью до 1 % .
Тепло, Необходимое для сушки, поступает в виде горячих газов из "печи или от специальной резервной топки, которая используется
при более высокой влажности сырья. Окружная скорость барабана молотковой мельницы составляет 25—35 м/с. Температура подаваемо го теплоносителя около 400° С. При высокой влажности сырья (более 30%) теплоноситель имеет температуру до 800° С и подается из спе циального резервного подтопка.
Расход тепла на испарение 1 кг влаги — около 3780 кДж. Рабочие детали выполнены из износостойкого материала и работают до полного износа.
В зависимости от условий помольно-сушильный агрегат может быть включен в схему с открытым циклом работы (рис. 29, а ) , в схему,
работающую по закрытому циклу с домолом крупной фракции (1 мм)
вшаровой мельнице (рис. 29, б), и в схему обработки двух материалов
сразной влажностью (влажного «А» и сырого «Б»), рис. 29, в .
Высушенную в сушильном барабане глину мелют в дезинтеграто
рах, молотковых или ротационных мельницах. Дезинтегратор обес печивает тонкий помол глины, %: более 3 мм — 10— 15; 2—3 мм — 15—20; 1—2 мм — 25—30; менее 1 мм — 40—45. Производительность дезинтеграторов 4—35 м3/ч. Для нормальной работы дезинтегратора размер загружаемых кусков не должен превышать 30—50 мм, а влаж ность — 8— 10%.
На молотковых мельницах выход фракций размером до 0,5 мм со ставляет около 70%, а на ротационных, работающих по замкнутому циклу,—около 80% зерен размером меньше 200 мкм при максимальном размере остальных зерен не более 800 мкм. Влажность порошка 4,5%.
Для помола глины также применяются бегуны сухого помола, смесительные или помольно-смесительные (СМ-568). Производитель ность бегунов 20— 14 т/ч.
На фракции измельчаемый материал разделяют просеиванием на специальном оборудовании (сита струнные, плоские и барабанные, качающиеся, вибрационные). Производительность сит повышается, если применяется электрообогрев, вибрация.
Подготовка и ввод добавочных материалов. Песок просеивают на сите с отверстиями 3 мм для удаления крупных включений.
Опилки поступают в сито-бурат с отверстиями 10 мм. Из бункеров просеянные опилки через ящичный подаватель поступают на ленточ ный конвейер и далее в производство.
Шамот приготовляют из боя изделий по той же схеме, что и топлив ные добавки. Первичное дробление осуществляют на щековой или молот ковой дробилках, более тонкий помол — на двухвалковых дробилках.
При централизованной подготовке выгорающих добавок с сов местным помолом опилок и угля существует такая схема (см. стр. 75).
Оптимальный гранулометрический состав выгорающих добавок, % : фракции менее 1 мм — 40; 1—2 мм — 30; 2—3 мм — не более 30. Количество вводимой в массу добавки — 10—30%. Ввод в массу от ходов углеобогащения заменяет более дефицитные добавки — уголь, опилки, шамот и др.
Подготовка дегидратированной глины заключается в предваритель ном дроблении (глинорыхлнтель СМ-1031А, вальцы СМ-1198 и т. д.) и нагреве ее во вращающихся печах 2,0 X 22 м с последующим помо-
Склад |
опилок |
Склад угля (отходов |
|
|
углеобогащения) |
|
|
I |
Просев |
I |
|
Расходный бункер |
||
Ящичный |
1 |
! |
подаватель |
Питатель |
|
|
Вертикальная |
молотковая дробилка |
|
|
I |
|
|
* |
Элеватор
I
I
Расходный бункер
лом на щековой С-1826 и вальцевой ДВГ-2М 40 X 25 дробилках и др. Обжигать глину можно также на спекательных (агломерационных)
решетках и в печах кипящего слоя.
Технологическая схема подготовки дегидратированной глины при ведена ниже:
Склад глины |
-------------Г |
||
|
I |
I |
|
|
I |
Холодильник |
|
Ящичный подаватель СМ-664 |
I |
|
|
|
I |
I |
конвейер |
|
I |
Скребковый |
|
Ленточный конвейер |
I |
|
|
|
I |
I |
ЭЦО-250 |
Вальцы |
Элеватор |
||
СМ-1198 |
I |
||
|
I |
||
Пресс |
I |
Дробилка |
СМ-218 |
СМ-294 |
1 |
||
|
I |
||
|
Элеватор |
ЭЦО-250 |
|
Ленточный конвейер |
I |
||
|
I |
I |
конвейер |
|
Ленто чный |
Вращающаяся печь |
1 |
|
Бункер |
Пресс оборудован перфорированной решеткой (350 отверстий диа метром 8— 10 мм). Угол наклона вращающейся печи — 3°, скорость вращения — 2 об/мин. Продолжительность термической обработки гранул — 20 мин, а давление во вращающейся печи 30—40 Па, тем пература теплоносителя 500—600° С, производительность установки — 45 т/ч, расход условного топлива на 1 т дегидратированной глины — 40—50 кг, себестоимость 1 т дегидратированной глины — 0,9—1 руб.
Увлажнение и гомогенизация масс. Каждой массе соответствует оптимальная влажность, при которой она обладает наибольшим сцеп лением, характеризуемым предельным напряжением сдвига. При этой влажности наиболее полно развиваются гидратные оболочки и адсорби рованные пленки воды на глинистых частичках, максимально прояв ляют свое влияние вандерваальсовские силы молекулярного взаимодей ствия, завершается процесс диспергирования. Масса приобретает улуч шенные деформационные свойства. Полуфабрикат из таких МйСс имеет
максимальную прочность в высушенном состоянии, переносит сушку и. обжиг с наименьшими деформациями, а изделия характеризуются максимальной прочностью.
Сланцевые и лессовые глины с влажностью 8— 12% требуют зна чительного количества воды для получения пригодной к формованию массы. Обычные глины, суглинки и супеси имеют влажность до 18% и требуют добавочного увлажнения на 2—8%, в то время как зыбкие глины влажностью до 35% требуют разувлажнения.
Компоненты глинистых материалов по-разному реагируют на увлажнение и процесс гидратации. Каолинит глины малопроницаем для воды и мало набухает, монтмориллонит хорошо гидратируется и на бухает в значительной степени, иллиты занимают промежуточное по ложение, а в зерна песка вода не проникает. Неодинаковая проницае мость воды в минералы является причиной гетерогенного распределения ее в глине или массе, что ухудшает формовочные свойства массы и вы зывает брак при сушке и обжиге.
Процесс формования (прессования) протекает нормально, если достигнута влажность массы, позволяющая образовать на твердых частичках гидратные прослойки, которые по толщине равны двум мо лекулам воды. Возможность образования коагуляционного контакта в предельно концентрированной дисперсии возникает при сближении частичек на расстоянии от поверхности 2000 мкм, т. е. в условиях, когда свободная энергия системы приближается к минимуму, а рас клинивающее давление становится отрицательным (преобладают силы сцепления). Образование коагуляционной структуры начинается при влажности массы 4—6%.
При увеличении влажности число контактов возрастает, повыша ются модули сдвига быстрой и медленной эластических деформаций, условный" статический предел текучести, наибольшая пластическая вязкость; прочность структуры возрастает.
При влажности 6,5—9% число контактов с минимальной толщиной гидратной пленки достигает максимально возможного значения, вслед ствие чего структурно-механические контакты и условный модуль деформации становятся наибольшими. Дальнейшее повышение влаж ности приводит к росту толщины гидратных слоев между частичками глины, что ослабляет силы молекулярного взаимодействия (силы от талкивания, вызываемые зарядами ионов, действуют на расстоянии до 20 000 мкм).
Увлажнение пластичной массы в два приема (в начале переработки и перед формованием) более эффективно, чем однократное.
Тонкомолотая глина впитывает воду в 5—6 раз быстрее кусковой. Учитывая, что процесс набухания длится 0,5—4 ч и более, массу лучше '.уйлажнять горячей водой (60—70° С) или паром. Проникая в поры, Щ ‘гайжё’в Места с дефектами структуры глинистых частичек, горячая ‘вйдУйЛи Нар легче образуют гидратные оболочки, а расклинивающее 'Й.ёййЬ^'Ьоды>проявляется сильнее. Масса, прогретая Паром, лучше '^рЙ^етМ .'при пониженной влажности, расход мощности при формЬваний^нижается на 20—25%., производительность прессов повы шается " Н а 10%, срок сушки сокращается на 40—50%. Перепад
влаги по слоям в полуфабрикате из прогретой массы уменьшается в 2—3 раза, что снижает напряжение и усадку в сырце при сушке. В ре зультате снижается брак и повышается прочность высушенного сырца
и готовых изделий. |
|
|
|
Для нагрева глины, содержащей |
15% влаги, на 14° С, с |
учетом |
|
всех потерь тепла, |
вводят 1% пара |
(от массы глины). Опыт |
пока |
зывает, что расход пара составляет 40—50 г на 1 кг глины.
На заводах, для смешения компонентов массы и увлажнения ее используют смесители.
В одновальных (СМ-220, СМ-239) и двухвальных (СМ-27, СМ-147А, СМ-246, СМК-124, СМК-125, СМК-126) смесителях материал переме шивается (гомогенизируется) лопастями, насаженными на вал, со скоростью до 35 об/мин. Регулированием угла наклона лопастей изме няется скорость движения материала и время пребывания его в сме сителе, которое обычно составляет 2—3 мин. Скорость перемещения составляет 1,3—-1,4 м/с. Производительность двухвальных смесителей 18—35 м3/ч. Наиболее эффективно используются смесители с паропрогревом СМК-18 (СМК-246), если они устанавливаются в начале техно логической линии — перед глинозапасником. Вторичная обработка массы с паропрогревом необходима в смесителях, устанавливаемых перед вальцами тонкого помола или перед прессом.
Харьковским ЦКБ «Строммашина» разработана конструкция сме сителя (СМ-1238) с фильтрующе-протирочной головкой. Это сблоки рованный с двумя шнековыми секциями двухвальный смеситель. К вы ходной секции примыкают две подвижные рамы со сменными решет ками, перемещающиеся в направляющих, закрепленных на торцевой плоскости выходной секции. Рамы передвигаются перпендикулярно движению массы с помощью двух гидравлических цилиндров. Диаметр отверстий сменных решеток 15, 20 и 25 мм. В корпусе смесителя враща ются два вала, оснащенные лопатками, которые перемешивают массу и подают ее в шнековые секции, а также расположена система пароувлажнения щелевого типа, способствующая равномерному и интенсив ному прогреву й увлажнению массы. __
Эксплуатация смесителя показала, что в нем не только улучшается переработка массы, но происходит еще удаление инородных включе ний. Производительность смесителя до 25 м3/ч. ВНИИСтром разра ботал конструкцию агрегата СН-400, заменяющего бегуны, вальцы и смеситель. Агрегат работает по принципу перетирания глины двумя противоположно вращающимися шнеками.
к* Увлажнение сухих порошковых глин или масс имеет свои особен ности, так как оно незначительно (на 2—3%). При увлажнении водой в двухвальных горизонтальных смесителях глина в местах переувлаж нения может комковаться. Чтобы не допустить этого, воду,1 пода ваемую на увлажнение шихты, сильно распыляют. В результате обра ботки глиняного порошка паром влажность его возрастает до 10— 14%, а температура — до 50—60° С. Расход пара — 140—150 кг на 1000 шт, кирпича-сырца.
Вылеживание массы. После вылеживания предварительно пе реработанной и увлажненной тлины почти на 20% повышается
производительность глиноперерабатывающего оборудования, улучша ются сушильные свойства глины, повышается прочность изделий не менее чем на 20—30%. Продолжительность вылеживания определяет ся с учетом химико-минералогического состава исходного сырья и видом изделий.
На заводах, потребляющих глинистое сырье в большом количестве и выпускающих эффективные керамические изделия, вылеживание целесообразно на двух стадиях подготовки массы: длительное — в карьере, на месте добычи, и кратковременное — в цехе подготовки массы, в специальных глинозапасниках ямного (66 X .18 м) или башен
ного типа (рис. 30), бункерах и других механизированных емкостях. Промежуточные ем кости (силосы) от 25 до 350 м1 обеспечивают вылеживание переработанной и увлажнен ной массы от 5—6 ч до 24 ч. На отечественных заводах ис пользуют башни-силосы типа СМК-178 емкостью 150 м3. Производительность башни — 25м3/ч, установленная мощ ность электродвигателей — 42 кВт.
|
Вакуумирование |
массы. |
Рис. 30. Механизированный силос: |
Цель вакуумирования— уда |
|
/ — корпус; 2 — конвейер; 3 — шнек; 4 — при |
ление воздуха из массы. Воз |
|
вод; 5 — вращающаяся платформа; 6 — неподвиж |
дух, адсорбированный поверх |
|
ная платформа; 7 — защитная стенка. |
||
|
ностью глинистых |
частичек, |
замедляет смачивание их водой, препятствует равномерному уплот нению массы, способствует расширению бруса при выходе из мунд штука, образуя тем самым микротрещины, выявляющиеся при сушке и обжиге изделий. Кроме того, воздух препятствует проникно вению влаги в поры глины, разъединяет частички глины друг от дру га, т. е. действует в массе как отощитель, что особенно снижает фор мовочную способность глиняных масс. Количество воздуха в глинах средней пластичности 2—3% по объему, у тощих — 3—4%. Сланце вые глины содержат незначительное количество воздуха, поэтому ва куумирование их нецелесообразно. После вакуумирования в глиняной массе остается до 0,5% воздуха.
Разрежение создается вакуумными насосами СМ-293, СМ-494, РМК или ВН-6 в вакуум-камере. Для большинства глин оно составляет 84—96 кПа.
Плотность сырца из вакуумированной массы повышается на 6—8%, коэффициент влагопрозодности уменьшается в 1,5—3 раза, что удли няет срок сушки, особенно сырца из пластичных глин. Но это частично компенсируется возможностью увеличения (до 50%) количества отощающих материалов, снижением формовочной влажности на 2—3%, что, в свою очередь, позволяет осуществить более форсированную
сушку, так как воздушная усадка сырца из вакуумированнои массы снижается на 2,5—3,5%. Прочность сырца возрастает с увеличением вакуума (рис. 31), причем одновременно уменьшаются пределы на грузок, вызывающих деформации
Рис. 31. Деформаций сырца ПОД |
Рис. 32. Зависимость Начала (1) и |
|
нагрузкой в зависимости от сте |
конца деформации (2) от вакуумиро |
|
пени вакуумирования масс: |
вания и нагрузки (Wa6c ф = 16,6%). |
|
/ |
— /> = 0; 2 — Р — 25; 3 — Р = |
|
= |
45; 4 — Р = 65 Па. |
|
выше, чем у кирпича из невакуумированной массы. Прочность высу шенного сырца из вакуумированной массы в 1,6 раза выше, чем из не вакуумированной. Объемная масса обожженных изделий увеличивает ся на 3—4%. Водопоглощение понижается на 10— 15%, а прочность увеличивается почти в два раза.
§ 4. ПЛАСТИЧЕСКОЕ ФОРМОВАНИЕ
Назначение формования — придать форму, размер, плотность и необ ходимую прочность полуфабрикату. Пластическое формование кирпи ча и керамических камней выполняется машинным способом.
Условия формования. Непременным условием пластического фор мования изделий является использование достаточно вязких масс, у которых сумма сил внутреннего сцепления (когезия) больше сцеп ления с рабочей поверхностью формующего оборудования (адгезия), а коэффициент внутреннего трения больше коэффициента внешнего трения.
При использовании высоковязких «жестких» масс требуются боль шие затраты энергии на формование и усиление конструктивных
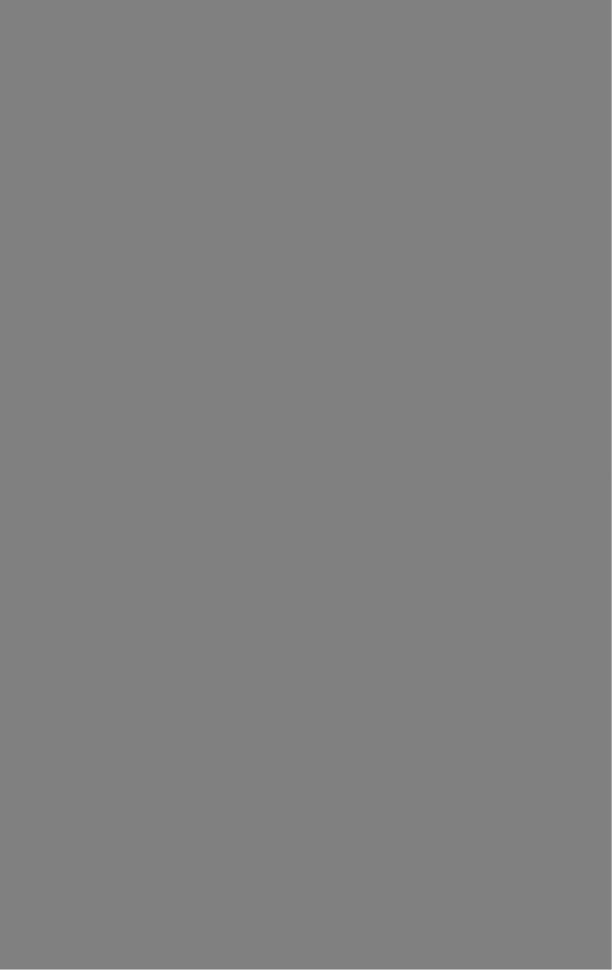