
книги / Оборудование литейных цехов
..pdfПо конструктивному исполнению различают двухшланговые и трехшланговые резаки. В первом случае поступающий кислород разветвляется на режущий и подогревающий в самом резаке; во втором случае режущий кислород подается по отдельному шлангу. Разделение подогревающего и режущего кислорода позволяет применять разное давление для этих двух потоков. Трехшланговый подвод газов осуществляется только на машинных резаках. Для ручной резки применяются двухшланговые резаки, так как наличие трех шлангов затрудняет работу резчика.
19.2. Газопламенная очистка и обрубка
Газопламенная очистка стальных отливок заключается в их обработке ацетилено-кислородным пламенем с применением и без применения режущей струи кислорода. Для очистки отливки, покрытые пригаром или окалиной, нагреваются, и в результате разности коэффициентов расширения окислов и металла слой окалины и пригоревшей формовочной смеси разрушается, отделяется от поверхности отливки и сдувается [43]. Газопламенная обрубка отливок (удаление заливов, приливов, остатков прибылей и заусенцев) является разновидностью поверхностной строжки и заключается в сжигании излишков металла в струе кислорода.
При очистке стальных отливок от окалины и пригара пламя резака должно касаться поверхности восстановительной зоной. Эта часть пламени имеет максимальную температуру, что обеспечивает резкий нагрев слоя окислов при незначительном нагреве самого изделия. Оптимальный угол наклона пламени к очищаемой поверхности должен быть 75–90°. Для очистки от окалины применяется мягкое пламя. Рекомендуемое давление газов при этом составляет для кислорода– 4–6 ат, для ацетилена – 0,2–0,5 ат.
По данным завода газопламенная очистка отливок позволила производить эту работу в 3–4 раза быстрее, чем пневматическими молотками при значительном улучшении чистоты поверхности отливок. Производительность труда обрубщиков уве-
361
личилась в 1,5–2 раза, а трудоемкости обработки отливок уменьшилась на 40–50 %.
Строжка осуществляется при угле наклона резака к обрабатываемой поверхности 20–30°. Газовая строжка во всех пространственных положениях выполняется в направлении справа-налево, а при вертикальном и наклонном положениях – сверху вниз. По данным завода внедрение газопламенной очистки и обрубки повысило производительность труда на обрубных работах на 40 % и позволило на 70 % уменьшить применение пневматических молотков, что значительно облегчило труд обрубщиков.
19.3. Кислородно-флюсовая очистка и резка
Кислородно-флюсовая (газофлюсовая) очистка отливок заключается в том, что в пламя и кислородную струю резака подается флюс, горение которого увеличивает тепловую мощность пламени и образует жидкотекучие шлаки окислов железа. В результате совместного действия пламени и горячих жидкотекучих окислов железа пригар расплавляется и отшлаковывается. Пригар частично удаляется давлением газового пламени, а частично остается на отливке в виде вздутого шлака, легко отделяемого при барабанной очистке.
Кислородно-флюсовая резка применяется для резки высокохромистых и хромоникелевых марок стали, чугуна, меди, латуни и бронзы. В случае углеродистых сталей кислороднофлюсовый способ позволяет резать металл без предварительной подготовки места реза, что повышает производительность.
При кислородно-флюсовой резке наиболее рациональным является использование в качестве флюса мелкогранулированного железного порошка. Иногда для интенсификации процесса горения во флюс добавляют алюминий, так как при сгорании алюминия выделяется в три раза больше тепла, чем при сгорании железа. При резке хромоникелевых сталей оптимальной добавкой к железному порошку является добавка 15 % алюминия [40].
362
|
|
|
|
|
|
|
|
|
Таблица 19.1 |
|
|
Составы флюсов для кислородно-флюсовой резки и область их применения |
|||||||
|
|
|
|
|
|
|
|
|
|
|
|
|
|
Состав флюса в % вес. |
|
|
Область применения |
||
|
|
|
|
|
|
|
|
|
флюса |
|
Номер |
Железный |
Кварцевый |
Алюмини- |
Силикокаль- |
Алюминиево- |
Ферро- |
Ферро- |
|
|
|
||||||||
|
состава |
порошок |
песок |
ево-магние- |
ций марки |
магниевый |
силиций |
фосфор |
|
|
флюса |
марки |
|
вый поро- |
КаСи-1 или |
порошок |
марки |
марки ФФ |
|
|
|
ПЖ2М– |
|
шок марки |
КаСи-2 |
марки ПАМ-2 |
Cu45 |
|
|
|
|
ПЖ5М |
|
АПВ |
|
и ПАМ-3 |
|
|
|
|
|
|
|
|
|
|
|
|
|
|
1 |
100 |
– |
– |
– |
– |
– |
– |
Разделительная рез- |
|
|
|
|
|
|
|
|
|
ка высоколегиро- |
|
2 |
80–90 |
– |
10–20 |
– |
– |
– |
– |
|
|
ванных хромистых и |
||||||||
|
|
|
|
|
|
|
|
|
хромоникелевых |
|
3 |
– |
– |
– |
– |
60–80 |
20–40 |
– |
|
|
сталей и сплавов |
||||||||
|
|
|
|
|
|
|
|
|
|
4 |
65–75 |
– |
– |
– |
– |
– |
30–35 |
Разделительная рез- |
|
|
|
|
|
|
|
|
|
|
ка чугуна |
5 |
65–75 |
20–25 |
5–10 |
– |
– |
– |
– |
||
|
|
|
|
|
|
|
|
|
|
6 |
70-80 |
– |
20–30 |
– |
– |
– |
– |
Разделительная рез- |
|
|
|
|
|
|
|
|
|
|
|
|
7 |
70–80 |
15–20 |
5–10 |
– |
– |
– |
– |
ка меди, латуни |
|
|
|
|
|
|
|
|
|
и бронзы |
|
8 |
70–75 |
– |
15–20 |
– |
– |
– |
10–15 |
|
|
|
||||||||
|
|
|
|
|
|
|
|
|
|
|
9 |
100 |
– |
– |
– |
– |
– |
– |
Поверхностная рез- |
|
ка высокохромистой |
||||||||
|
|
|
|
|
|
|
|
|
|
|
|
|
|
|
|
|
|
|
и хромоникелевой |
|
10 |
– |
– |
– |
70–75 |
25–30 |
– |
– |
|
|
стали |
||||||||
363 |
|
|
|
|
|
|
|
|
|
|
|
|
|
|
|
|
|
|

Для поверхностной зачистки нержавеющих сталей применяются флюсы, состоящие из 25 % алюминиево-магниевого порошка и 75 % силикокальция. При этом силикокальций действует на окислы хрома как флюсующая добавка.
Составы флюсов для кислородно-флюсовой резки и область их применения приведены в табл. 19.1.
19.4. Газоэлектрическая очистка и резка
За последнее время в промышленности получили широкое распространение различные способы электродуговой обработки металла. Резка с использованием электрической дуги имеет следующие разновидности: 1) дуговая резка стальным электродом; 2) дуговая резка угольным электродом; 3) кислородно-дуговая резка; 4) воздушно-дуговая резка; 5) плазменно-дуговая резка.
Три последних способа резки металла можно объединить под общим названием – газоэлектрическая резка.
При всех видах газоэлектрической резки для нагрева и расплавления обрабатываемых металлов используется тепло электрической дуги, а струя газа либо оказывает механическое действие, выдувая расплавляемый металл из полости реза (воздуш-
но-дуговая резка), либо защищает поверхность |
реза от |
||
|
окисления и оказывает суще- |
||
|
ственное влияние на фор- |
||
|
мирование дугового разряда |
||
|
(плазменно-дуговая резка). |
||
|
Воздушно-дуговая рез- |
||
|
ка металлов в СССР приме- |
||
|
няется |
с 1956 г. |
Простота |
Рис. 19.2. Резак с боковой подачей |
и возможность |
обработки |
|
воздуха |
металлов, не поддающихся |
||
|
резке |
ацетилено-кислород- |
ным пламенем, способствовали широкому распространению этого метода. Сущность метода состоит в том, что расплавлен-
364
ный электрической дугой металл выдувается струей сжатого воздуха из зоны горения дуги. Этим способом можно производить разделительную резку и поверхностную стружку конструкционной углеродистой и легированной стали, чугуна, алюминия, меди, удаление дефектов отливок, подготовку кромок под сварку, удаление пригара. Резка и строжка ведется электрической дугой как постоянного, так и переменного тока. Для резки углеродистых и нержавеющих сталей применяется постоянный ток обратной полярности. Для цветных металлов и чугуна более целесообразно применение постоянного тока прямой полярности, или переменного тока.
Для воздушно-дуговой резки металла необходимо иметь резак, источник питания электрической дуги, сжатый воздух
иугольные или графитовые электроды. Резаки для разделительной резки и поверхностной строжки указанным способом отличаются друг от друга схемой подачи воздуха в зону расплавленного металла и способом зажима угольного электрода. На рис. 19.2 показан резак с боковой подачей воздуха в зону горения дуги
идержателем пружинного типа.
Сущность способа плазменно-дуговой резки заключается в проплавлении металла мощным дуговым разрядом, искусственно сосредоточенным на ограниченном участке обрабатываемой поверхности. Электрическая дуга расплавляет металл, а газовая струя, подаваемая в полость реза через отверстие наконечника, удаляет расплавленный металл.
Принципиальная схема процесса плазменно-дуговой резки показана на рис. 19.3. Плазменно-дуговая резка осуществляется с помощью вольфрамового электрода 4. Электрод располагается внутри водоохлаждаемого медного наконечника 5 для обеспечения необходимого сжатия электрической дуги и придания ей вытянутой формы. Газовая струя 3, подаваемая в корпус, защищает электрод от разрушения, а кромки разрезаемого металла 6 – от окисления.
365
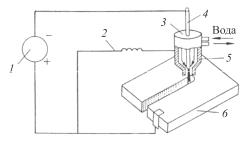
Рис. 19.3. Принципиальная схема процесса плазменно-дуговой резки: 1 – генератор постоянного тока; 2 – добавочное сопротивление в цепи вспомогательной дуги: 3 – газ; 4 – вольфрамовый электрод; 5 – наконечник; 6 – разрезаемый металл
В качестве источника тока используется генератор постоянного тока прямой полярности 1.
Во избежание проплавления наконечника при возбуждении дежурной дуги применяется специальное балластное сопротивление 2, установленное в цепи электрод – наконечник, которое ограничивает ток дежурной дуги в пределах от 10 до 15 А.
Для возбуждения дуги между электродом и металлом используется дополнительный электрический разряд – так называемая дежурная дуга. Дежурная дуга возбуждается между вольфрамовым электродом и медным водоохлаждаемым наконечником, для чего к ним подводится напряжение от генератора постоянного тока. Для облегчения зажигания вспомогательной (дежурной) дуги зазор между вольфрамовым электродом и наконечником обычно заполняется чистым аргоном и пробивается электрической искрой при помощи маломощного искрового генератора или замыкания токопроводящей вставкой. Поток аргона, подаваемый в наконечник, выдувает дежурную дугу из отверстия в виде раскаленных ионизированных газов. При соприкосновении этой дуги с обрабатываемым металлом она замыкает между ними зазор, тем самым возбуждая основную (режущую) дугу, величина тока в которой составляет несколько сот ампер.
366
Огневая очистка и обрубка отливок характеризуется высокой производительностью, низкой стоимостью, простотой оборудования и универсальностью.
На основании экономического анализа, проведенного НИИлитмашем установлено, что отрезка заливов огневым методом на стальных отливках весом до 100 кг по стоимости в четыре раза ниже, чем обработка пневматическим зубилом, а по продолжительности в пять раз меньше.
Вопросы для повторения
1.Назовите огневые способы очистки.
2.Область применения газокислородной резки.
3.Сущность газопламенной очистки.
4.Сущность кислородно-флюсовой очистки и резки.
5.Газоэлектрические способы очистки.
20. ОЧИСТКА ОТЛИВОК КРУГАМИ
20.1. Очистка абразивными кругами
После очистки поверхности отливок их зачищают с помощью абразивных шлифовальных кругов с целью удаления заливов, остатков питателей и других неровностей. Раньше шлифовальные круги изготавливали из природного абразива – наждака, и обдирочные станки для зачистки отливок назывались наждачными станками. Это прежнее название частично сохранилось и сейчас. В настоящее время шлифовальные круги для зачистки отливок изготавливают исключительно из искусственных абразивных материалов – карборунда и электрокорунда.
Шлифовальный круг состоит из зерен абразивного материала, связанных между собой цементирующим веществом, или связкой. Работу шлифовального круга можно сравнить с фрезерованием. При работе шлифовальным кругом острые зерна аб-
367
разивного материала выполняют ту же функцию, что и зубья фрезы, снимая стружку с обрабатываемого металла. Неправильность углов резания этих зерен с избытком компенсируется их громадным числом и скоростью резания, причем получается очень мелкая стружка, носящая характер пыли.
Карборунд представляет собой карбид кремния SiC с плотностью 3,1–3,2 г/см3, темно-синего или черного цвета; его получают в электропечах из кварцевого песка и кокса. По твердости карборунд уступает только алмазу и бору. Промышленный карборунд содержит не менее 95 % SiC. Раздробленные кристаллы его имеют очень острые края, легко врезающиеся в обрабатываемое изделие. Однако карборунд хрупок, и зерна его легко расщепляются. Поэтому его нецелесообразно применять для обработки вязких металлов, так как при этом зерна его расщеплялись бы задолго до их затупления. Карборунд наиболее пригоден для обработки хрупких, хотя и очень твердых металлов. Карборундовые круги применяют для обдирки отливок из белого и серого чугуна, а также из бронзы.
Электрокорунд представляет собой кристаллический глинозем Аl2O3; его получают в электропечах путем плавки боксита. Промышленный электрокорунд содержит не менее 87 % Аl2O3, имеет серо-коричневый цвет и плотность 3,8–3,9 г/см3. По твердости он уступает карборунду, но превосходит его по вязкости. Круги из электрокорунда применяют для зачистки отливок из стали и ковкого (отожженного) чугуна.
Зернистость абразивных материалов оценивается, подобно формовочным пескам, путем рассева на ситах. Для зачистки отливок применяют круги с зернистостью 12–70 (ГОСТ 3647–71).
Качеством связки определяется твердость (прочность) круга и режим работы. Связка должна быть достаточно прочной, чтобы выдерживать напряжение от центробежной силы и давления во время шлифования, удерживать зерна, пока они остры, и давать возможность выпадать им при потере режущей способности.
368
При правильно выбранной твердости круга зерна выкрашиваются одновременно с их затуплением. Если круг слишком мягок, т.е. связка недостаточно прочна, то зерна выкрашиваются еще до затупления, и круг используется недостаточно эффективно. Если же круг слишком тверд, то затупившиеся зерна задерживаются в нем, не выкрашиваясь, круг греется, и промежутки между зернами забиваются мелкой стружкой (круг «засаливается»). Чем мягче обрабатываемый металл, тем тверже должен быть круг, и наоборот.
Применяемые при обработке литья абразивные круги изготавливаются на керамических (К), бакелитовых (Б) и вулканитовых (В) связках. Круги на керамической связке допускают окружную скорость 30–35, на бакелитовой – до 40 и на вулканитовой до 50 м/с.
В последнее время употребляются круги на новых синтетических связках, обладающих высокой эластичностью и допускающих окружные скорости 100 м/с и более.
Режим шлифования – скорость и глубина резания – выбирается из условия самозатачивания круга. Чем больше окружная скорость круга, тем меньше длительность соприкосновения абразивного зерна с металлом и тем меньшей может быть твердость круга, так как зерна его не так быстро будут тупиться.
Для обозначения твердости кругов применяют буквы и цифры. Буквы обозначают классы твердости: ЧТ (чрезвычайно твердый), ВТ (весьма твердый), СМ (среднемягкий) и М (мягкий). Цифры, стоящие вслед за буквами, обозначают подразделения твердости в порядке ее возрастания (1, 2, 3). Для зачистки отливок чаще всего применяют круги с твердостью в пределах от М2 до Т1.
Для зачистки отливок применяют шлифовальные круги цилиндрической формы, в виде сплошного диска, и кольцевые. Окружная скорость круга ограничивается прочностью связки изза опасности разрушения круга под действием центробежных
369
сил, что может повести к случаям тяжелого травматизма рабочего персонала. Окружную скорость кругов при обдирке отливок часто ограничивают величиной 30 м/с.
Приведем некоторые заводские рекомендации по выбору шлифовальных кругов для зачистки отливок. По данным Челябинского тракторного завода [25], для обдирки отливок из мягкой стали используют круги из электрокорунда с зернистостью 20–30 и твердостью в пределах Т1–СТЗ, для обдирки отливок из марганцовистой стали – также корундовые круги, но с зернистостью 6–12 и твердостью ВТ2–Т1, для чугунных отливок – круги из карборунда с зернистостью 50–70 и твердостью СМ1–М2. По данным Горьковского автозавода [38], для отливок серого чугуна мелких и средних применяют круги из карборунда с керамической связкой при твердости круга СТ2 или с бакелитовой при твердости круга СТ2 и СТЗ; для крупных отливок типа блоков цилиндров, картера коробки передач и т.п. – круги из карборунда с бакелитовой связкой при твердости круга СТ1 и СТ2, а также круги из электрокорунда с бакелитовой связкой при твердости круга СT1; для отливок из отожженного ковкого чугуна – круги из электрокорунда с бакелитовой связкой при твердости круга СТ2. Для всех кругов при этом рекомендуется зернистость 24.
Удаление заливов, заусениц и остатков литниковой системы у подавляющего большинства отливок может быть выполнено плоским, круглым и фигурным видами шлифования (периферией или торцом круга) – рис. 20.1.
Плоское шлифование периферией круга (рис. 20.1, а) является устаревшим видом обработки, широкое применение которого в механизированных установках нецелесообразно. Плоское же шлифование торцом круга (рис. 20.1, в) является прогрессивным видом обработки, при котором производительность резко возрастает, а расход абразивного материала снижается за счет более полного использования шлифовального круга.
370