
книги / Производство сварных конструкций (Изготовление в заводских условиях)
..pdfключается благодаря пружинным компенсаторам 16, обеспечи вающим возможность независимого перемещения каждого сва рочного приспособления.
Вследствие конструктивных различий между отдельными план ками каркаса количество, размеры и расположение сварных швов на многих из них различно, поэтому сварка их роботами ведётся по семи чередующимся подпрограммам. Оценка текущего со стояния позиционера и выбор нужной подпрограммы на каждом шаге позиционирования система управления осуществляет с по мощью электромеханического программатора, состоящего из пер форированного диска, закреплённого на поворотной опоре, и блока бесконтактных датчиков, установленных на стойке основания.
Исходным состоянием позиционера является горизонтальное расположение поворотной части, зафиксированной выдвижны ми стопорами. Их положение система управления определяет с помощью встроенных бесконтактных датчиков.
Выгрузку и загрузку каркасов производят поочередно с по мощью тельфера, каркасы фиксируют в приспособлении с по мощью пальцев.
Сварку каркасов производят в автоматическом режиме в со ответствии с алгоритмом, заложенным в систему управления роботизированного комплекса.
Система управления (СУ) всем комплексом оборудования на позиции роботизированной сварки каркасов построена на базе компьютера одного из сварочных роботов (ведущего №1). Робот N2 (ведомый), а также позиционер обмениваются с ним инфор мацией и выполняют его команды. При этом робот N2 работает по собственной рабочей программе, содержащейся в памяти его системы управления.
Датчики, установленные на позиционере, передают в СУ РТК следующую информацию:
•код, определяющий состояние позиционера и под программы сварки зафиксированных планок каждым роботом;
•давление воздуха в пневматической сети;
•положение стопоров поворотной части;
•наличие растягивающего усилия в сварочных приспособлениях;
•положение толкателя храпового механизма;
•положение пневматических фиксаторов.
281
Кроме того, СУ контролирует нахождение роботов в исход ном положении и состояние их сварочного оборудования.
Схема роботизированного сварочного комплекса показана на рис. 8.30. Комплекс включает: два сварочных робота 3 типа IR 160/15 фирмы «KUKA», имеющие антропоморфную систему координат, шесть степеней подвижности и контурную систему управления, позиционер 1 с размещенными на нем приспособ
лениями 2 для свариваемого узла. |
|
|
1 |
2 |
3 |
Рис. 8.30. Схема роботизированного комплекса сварки каркаса
Для обеспечения условий безопасного обслуживания ком плекса он помещен в бокс, доступ внутрь которого возможен только в тот период, когда роботы отключены или находятся в нерабочем состоянии.
В боксе, помимо роботов и позиционера, расположены стой
2 8 2
ки системы управления роботами 4, источники питания свароч ным током 5 и устройства для очистки горелок 6. С обеих сто рон от позиционера в зонах его обслуживания установлены по лы безопасности 7, осуществляющие остановку работы робота или блокировку его запуска в работу, если оператор находится в зоне досягаемости робота. Пульт управления 8 комплексом вы несен за его пределы и расположен со стороны стоек управле ния, в зоне работы оператора.
После предварительных испытаний полный комплект обору дования РТК был смонтирован и отлажен на Урюпинском заво де «Сельхозмаш».
Суммарная длительность операций, выполняемых на РТК, при изготовлении двух каркасов составляет 137,5 минуты. Та ким образом, трудоемкость сборки и сварки одного каркаса рав на 68,75 минуты.
Работа РТК построена таким образом, что со временем робо тизированной сварки не совмещены только транспортные опе рации, связанные с загрузкой и выгрузкой изделий на позицио нере, причем в этих операциях задействованы оба работника, обслуживающих РТК.
Роботизированный сборочно-сварочный комплекс включает в себя три рабочие позиции (рис. 8.31), объединенные межопе рационным транспортным устройством: сборки (I); роботизиро ванной сварки (II); контроля и исправления брака (III).
Рис. 8.31. Схема размещения оборудования РТК
Между позициями РТК предусмотрены накопители.
Сборку каркаса на прихватках осуществляет сборщик в сва рочной кабине на стенде 1. Здесь же, в приспособлении 2, он
283
предварительно приваривает втулки к боковинам швами, недос тупными для горелки робота. Сварку и прихватку производят полуавтоматической сваркой в среде углекислого газа, для чего кабина оборудована сварочным постом 3 и консолью для по дающего механизма 4. Собранный каркас с помощью тельфера 5 складируют в накопитель 6 или передают на позицию роботизи рованной сварки, где сборщик вместе с оператором устанавли вает и фиксирует каркас на первом приспособлении позиционе ра 7, находящегося в положении загрузки. Затем после кантовки поворотной части на 180° они загружают второй каркас.
После этого оператор с пульта управления 8 включает авто матический цикл сварки, и оба робота 9 одновременно произво дят сварку двух каркасов. Стойки управления роботами 10 и ис точники сварочного тока 11 встроены в кабины и лицевыми па нелями обращены к оператору.
По завершении сварки позиционер переводит приспособле ния в горизонтальное положение. Оператор вместе со сборщи ком снимает сваренный узел и устанавливает на его место но вый собранный. Позиционер кантует раму с приспособлениями на 180°, и производится перезарядка второго приспособления. Цикл сварки повторяется.
Сваренные каркасы оператор с помощью тельфера подает в накопитель 12 или на место контроля 13. Здесь за время работы роботов оператор выполняет оставшиеся сварные швы, осмат ривает каркасы, исправляет брак после роботизированной свар ки и контролирует шаблонами межцентровые расстояния на бо ковинах и радиус рабочей поверхности каркаса. Готовые карка сы складируют на месте 14.
Трудоёмкость изготовления каркаса подбарабанья на РТК со ставляет 1,1 чел/ч, что в 2,4 раза меньше, чем при его изготовле нии с помощью механизированной сварки в среде углекислого газа. Трудоёмкость снизилась за счёт:
•более быстрого перемещения горелки робота от шва к шву;
•стабильного выполнения номинальных размеров свар ных швов с отклонением в сторону нижнего предела поля до пуска (5.о.5 мм), тогда как при полуавтоматической сварке швы, как правило, выполняются с завышением номинального размера (5*1,0мм);
284
• уменьшения непроизводительных потерь времени. Хронометраж работы РТК показал, что при такте выпуска
изделий 33 минуты элементы цикла изготовления каркаса в про центном отношении соотносятся следующим образом:
•установка и съём изделия-6,3%;
•кантовки изделия - 5,5%;
•перемещения горелки к местам сварки и зачистка мунд штука - 17,2%;
•горение дуги -71%.
Время подналадки и обслуживания оборудования РТК со ставляет в среднем 15%.
Достаточно высокая производительность РТК (14 каркасов в одну смену) достигнута в основном за счёт рационального со вмещения во времени основных и вспомогательных операций.
9. НЕТРАДИЦИОННЫЕ ТЕХНОЛОГИИ СВАРКИ, ПРИМЕНЯЕМЫЕ ПРИ ИЗГОТОВЛЕНИИ СВАРНЫХ КОНСТРУКЦИЙ
9.1. Лазерные технологии в машиностроении
Традиционно используемые в машиностроении технологии сварки плавлением из-за недостаточной плотности энергии не обеспечивают глубокого проплавления металла, вследствие чего при сварке металла больших толщин, обычно более 5 мм, требу ется выполнять скос свариваемых кромок, что приводит к необ ходимости наплавлять большой объем металла. Это ведет к снижению производительности сварки и, как правило, к появле нию больших остаточных деформаций.
В отличие от дуговых методов сварки, при лазерной сварке удается достичь значительно большей плотности энергии, что обусловливает более эффективное использование введенной энергии для расплавления металла и образования соединения. Вследствие этого появляется возможность увеличения скорости
285
и наблюдается существенное уменьшения сварочных деформа ций.
Существует две технологии лазерной сварки - сварка за счет нагрева и сварка с глубоким проплавление за счет образования паро-газового канала.
В первом случае плавление металла происходит в поверхно стном слое глубиной несколько десятых долей миллиметра. Этот способ применяется для соединения тонких деталей в при боростроении и медицинской технике, а также при выполнении наплавки, когда требуется обеспечить минимальное перемеши вание основного и наплавляемого металла.
Для этой технологии используют импульсные твердотельные Nd:YAG лазеры, а наплавку выполняют расфокусированным лучом.
При увеличении плотности энергии выше порогового зиачения 10’ Вт/см" металл не только плавится, но и испаряется. Дав ление паров металла становится столь большим, что в сваривае мом металле формирует паровой канал, получивший название «замочная скважина», окруженный расплавленным металлом. Глубина проплавления резко возрастает и может достигать не скольких миллиметров.
Перемещаясь вместе с лазерным лучом, жидкий металл, ок ружающий паровой канал перемешивается и затвердевает, обра зуя узкий шов. Металл сварного шва обычно защищают от окисления инертным газом.
Схемы лазерной сварки представлена на рис. 9.1.
При плотности вводимой энергии ниже критической величи ны мощность лазерного излучения незначительно влияет на глу бину проплавления металла. После превышения порогового 106 Вт/см2 значения глубина проплавления зависит от мощности лазерного источника тепла, скорости его перемещения и вида свариваемого материала (рис. 9.2).
На том же рисунке отмечены уровни максимальной скорости автоматической сварки под флюсом, позволяющие получить хорошее формирование шва: для однодугового процесса (I), двухдугового (И) и трехдугового (III).
2 8 6



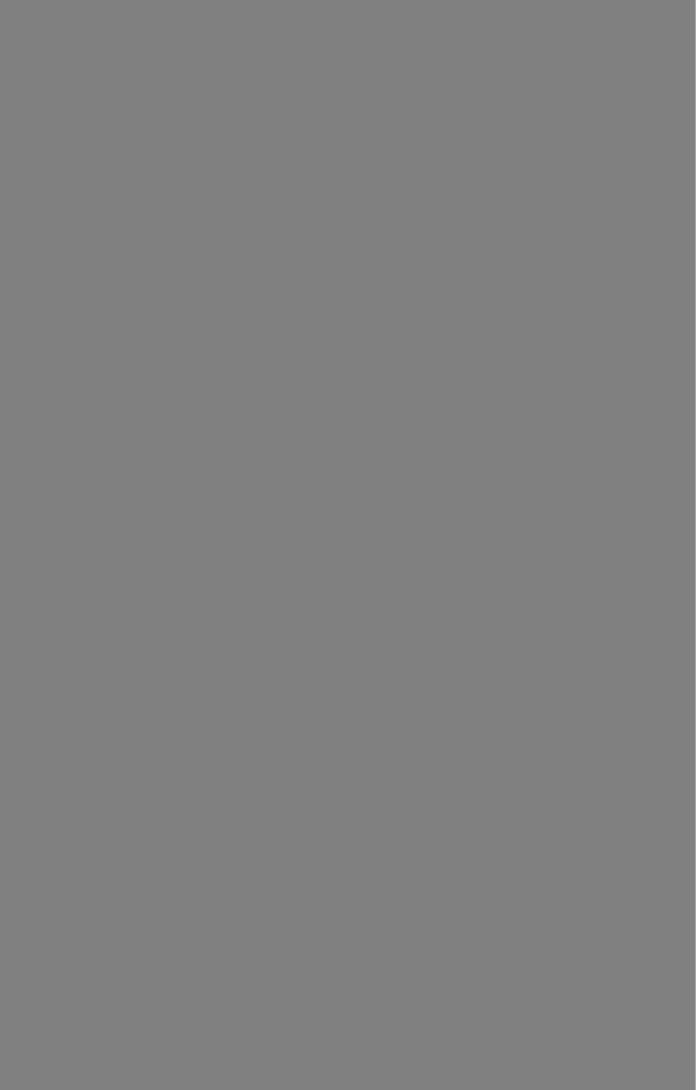