
книги / Строительные материалы
..pdf
камере, где осуществляется интенсивный прогрев изде лий паром, специальными подогревателями или инфра красными лампами. На нижнем ярусе происходит окон чательное твердение бетона (рис. 8.13).
Третья схема — вибропрокат — изготовление изделий методом непрерывного формования на станах конструк ции Н. Я- Козлова. Стаи имеет непрерывно движущуюся со скоростью 25 м/ч металлическую ленту, на которой с помощью вибрирования и прокатки формуется изделие, перемещаемое затем в зону тепловой обработки на 2 ч. Вибропрокат — весьма производительный и автоматизи рованный способ производства сборного железобетона. Часовая производительность стана достигает 80 М2 па нелей. Однако при этом способе затруднен переход на выпуск новых видов изделий; стоимость изделий выше, чем при их изготовлении другими способами.
При изготовлении сборных железобетоных деталей на заводах производят следующие основные операции: изготовляют арматурный каркас и устанавливают его в формы; формуют изделия; прогревают изделия с целью ускорения твердения бетона.
2. Армирование изделий
Ненапряженное армирование осуществляется с по мощью плоских сеток и пространственных (объемных) каркасов, изготовленных из стальных стержней, сварен ных между собой в местах пересечений. В железобетоне различают арматуру несущую (основную) и монтажную (вспомогательную). Несущая арматура располагается в местах изделия, в которых под нагрузкой возникают растягивающие напряжения; арматура воспринимает их. Монтажная арматура располагается в сжатых или нена пряженных участках изделия. Кроме этих видов армату ры, применяют петли и крюки, необходимые при погру зочных работах, а также закладные части для крепления и связи сборных элементов между собой.
Наименьшие трудовые затраты на армирование изде лий и конструкций будут при применении арматурных каркасов наибольшей степени готовности, т. е. состоя щих не только из основной арматуры, но и из вспомога тельной с приваренными петлями, крюками, закладны ми деталями. В этом случае армирование сводится к ус-
тановке готового арматурного каркаса в форму и к его закреплению.
Арматурные сетки и каркасы изготовляют в арматур ном цехе, оборудованном резательными, гибочными и сварочными аппаратами. Процесс производства строит ся по принципу единого технологического потока, начи ная от подготовки арматурной стали до получения гото вого изделия.
Изготовление ненапрягаемой арматуры. Стержневую арматурную сталь диаметром до 10 мм поставляют на завод в мотках (бухтах), а диаметром 10 мм и более — в прутках длиной 6—12 м или мерной длины, оговарива емой в заказах. Арматурную проволоку поставляют в мотках, причем каждый моток состоит из одного отрезка проволоки.
Изготовление арматуры складывается из следующих операций: подготовки проволочной и прутковой стали — чистки, правки, резки, стыкования, гнутья; сборки сталь ных стержней в виде плоских сеток и каркасов; изготов ления объемных арматурных каркасов, включая привар ку монтажных петель, закладных частей, фиксаторов.
Прутковую арматурную сталь разрезают на стержни заданной длины, а также стыкуют сваркой в целях уменьшения отходов. Стыкуют стержни посредством стыковой электросварки и только в отдельных случаях при использовании стержней больших диаметров приме няют дуговую сварку. Контактную стыковую сварку осуществляют методом оплавления электрическим током торцов стержней в местах их будущего стыка. При этом стержни сильно сжимают и сваривают между собой.
При изготовлении монтажных петель, хомутов и дру гих фигурных элементов арматуры прутковую и прово лочную арматурную сталь после разрезки подвергают гнутью.
Сборку сеток и каркасов из стальных арматурных стержней производят посредством точечной контактной электросварки. Такую сварку осуществляют с помощью специальных сварочных аппаратов. Они отличаются мощностью трансформатора, количеством одновременно свариваемых точек (одно- и многоточечные), характе ром используемых устройств для сжатия свариваемых стержней. Сварочные машины позволяют создавать в комплексе с другими машинами и установками поточные автоматические линии изготовления плоских сеток как
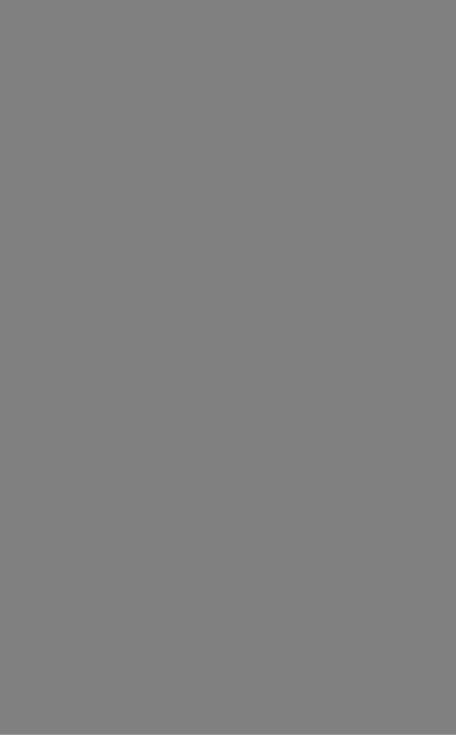
Изготовление предварительно напрягаемой арматуры.
При изготовлении предварительно напряженных изделий необходимо создать в бетоне по всему сечению или толь ко в зоне растягивающих напряжений предварительное обжатие, величина которого должна превышать напря
жение |
растяжения, возникающее в бетоне при эксплуа |
тации. |
Обычно предварительное обжатие бетона 5 — |
6 МПа, |
а при изготовлении железобетонных напорных |
труб 10—12 МПа. Обжатие достигается силами упруго го последействия натянутой арматуры, которые переда ются бетону за счет сцепления арматуры с ним или с по мощью анкерных устройств.
Для обжатия бетона упругие деформации применяе мой арматурной стали должны составлять 85—90 % пре дела ее текучести, а для углеродистых сталей, не имею щих четко выраженного предела текучести, 65—70 % предела прочности на разрыв.
В качестве основной напрягаемой арматуры приме няют проволочную и прутковую арматурные стали, а в
качестве |
вспомогательной ненапрягаемой арматуры, |
ес |
ли она |
имеется в напряженных изделиях, — сварные |
|
сетки и каркасы. |
из |
|
При |
изготовлении предварительно напряженных |
делий пользуются одноосным обжатием бетона отдель ными стержнями или пучками проволок, располагаемых в изделии вдоль его продольной оси, и объемным обжа тием путем навивки напряженной проволоки в двух или нескольких направлениях. Можно навивать проволоку и на готовое изделие с последующей защитой арматуры слоем бетона.
Арматурные элементы, применяемые в конструкциях, состоят из арматуры, устройств для закрепления арма туры при натяжении и приспособлений для сохранения проектного расположения отдельных стержней и прово лок, из которых комплектуется арматурный элемент. Конструкция устройств для закрепления арматуры свя зана с технологией изготовления арматурного элемента и с типом машин и приспособлений для натяжения. При меняют Два вида этих устройств — зажимы и анкеры. В свою очередь, зажимы и анкеры подразделяют по спо собу закрепления арматуры на клиновые, плоские, кони ческие, волновые, петлевые, резьбовые, шпоночные и глухие, в которых концы арматурных пучков опрессовываются в обойме из мягкой стали. Все приведенные уст-
ройства, за исключением резьбовых, применяют для За крепления круглых стержней и стержней периодического профиля.
Для захвата и закрепления стержневой арматуры применяют наконечники с винтовой нарезкой или различ ные «клиновидные сухари» с профилем, обратным про филю натягиваемой арматуры. Прогрессивной конструк цией зажимных устройств являются групповые зажимы, применяемые при предварительной механизированной сборке проволочных пакетов. Зажимы применяются для закрепления каждого стержня, нити проволоки или груп пы их.
Анкеры для проволочных пучков различают по спо собу натяжения и закрепления концов. Для закрепления пучков применяют два типа анкеров: конический с на тяжением арматуры домкратом двойного действия и гильзовый с натяжением арматуры стержневым домкра том.
Передачу предварительного напряжения арматуры на бетон осуществляют тремя способами: первый — по средством сцепления арматуры диаметром 2,5—3 мм с бетоном; при большем диаметре арматуры сцепление достигается устройством вмятин на поверхности проволо ки или свивкой прядей из двух-трех проволок, либо при менением арматуры периодического профиля; второй — посредством сцепления арматуры с бетоном, усиленного анкерными устройствами; третий — посредством переда чи усилий натяжения на бетон через анкерные устройст ва на концах арматурного элемента без учета сцепления арматуры и бетона.
Способы натяжения арматуры подразделяют на ме ханические и электротермические. При механическом способе арматура растягивается осевой нагрузкой, созда ваемой домкратами. Сначала арматуру натягивают до усилия, равного 50 % проектного напряжения, при этом производят осмотр зажимных устройств и расположения арматуры. Затем натяжение арматуры доводят до зна чения, превышающего на 10% проектное натяжение, но не более 85 % предела прочности проволоки при растяжении, и в таком состоянии выдерживают в течение 5 мин, после чего натяжение снижают до проектной величины. Отпуск напряженной арматуры (обжатие бетона) производят после достижения бетоном
изделия необходимой прочности и проверки заанкеривания концов проволоки в бетоне. Фактическую прочность бетона определяют испытанием контрольных образцов. Прочность бетона по времени отпуска арматуры состав ляет обычно 70 % проектной прочности. Отпуск натяже ния на стендах осуществляется постепенно, в два-три этапа. Разгрузку натянутых проволок при невозможнос ти постепенного отпуска натяжения производят симмет рично относительно оси поперечного сечения с числом одновременно разрезаемых проволок не более 10—15 % общего числа проволок. При механическом способе ар матуру натягивают, как правило, на специальных стен
дах.
Электрический способ не требует дорогостоящего оборудования (домкратов) и менее трудоемок. Такой спо соб применяют для натяжения стержневой арматурной стали класса А-Ш, проволочной и прядевой арматуры из высокопрочной стальной проволоки, холоднотянутой, периодического профиля диаметром 4—5 мм и семипро волочной проволоки.
Для натяжения арматуры электротермическим спосо бом применяют установки с последовательным и одно временным натяжением нескольких стержней. Кроме то го, установки могут быть с нагревом стержней вне фор мы или непосредственно в ней. На установке для электронагрева стержневой арматуры вне формы (рис. 8.15) можно нагревать три-четыре арматурных стержня диаметром 12—14 мм, что соответствует числу стержней в изделии. Установка состоит из двух контактных опор (неподвижной и подвижной) и средней поддерживающей. Каждый контакт имеет две губки: токопроводящую и прижимную. Нагрев стержней контролируется по их удлинению автоматически. Нагретые стержни снимают с установки и укладывают в упоры форм, которые препят ствуют укорочению стержня при его охлаждении. После бетонирования конструкции и твердения бетона армату ру освобождают от упоров и усилие натяжения армату ры передается на бетон.
Непрерывное механическое и электромеханическое натяжения арматуры сводится к тому, что проволоку, предварительно напряженную до заданной величины, ук ладывают на поддон формы в соответствии с принятой схемой армирования. Фиксация натянутой проволоки производится навивкой ее вокруг штырей, расставленных
Рис. 8.15. Установка для элсктронагрева стержневой арматуры вне формы
1 — неподвижная опора; 2 — пнсвмоцилнмдр; 3 — прижимная губка; 4 — токо проводящая губка; 5 — средняя опора; 6 — нагреваемые стержни; 7 — подвиж ная опора; 8 — конечный выключатель
по периметру поддона или стенда. Усилие от натяже ния арматуры передается через штыри на стенд или фор му до затвердевания бетона в изделии. После достиже ния бетоном необходимой прочности проволока обреза ется и усилие натяжения передается с арматуры на бе тон. Арматура может располагаться продольно или по перечно по отношению к оси изделия, перекрестно или по диагонали. Бетон в изделии получает двух-, трехслой ное и даже объемное предварительное обжатие.
Преимуществом непрерывного армирования является возможность комплексной механизации и автоматизации технологического процесса. Непрерывная навивка и на тяжение проволоки производится на нескольких типах машин: с поворотным столом-платформой, с поворотной траверсой, с продольно-поперечным перемещением ка ретки и неподвижным поддоном (контуром), с возврат но-поступательным движением каретки и вращающимся сердечником или контуром. Основные узлы каждой .та кой машины: узел размотки бухт и подачи проволоки с заданным натяжением; узел перемещения поддона или подающего ролика; узел укладки проволоки на штыри или на сердечник по заданной схеме.
3. формование изделий
Для формования железобетонных изделий применяют, как’правило, металлические формы. Эти формы выдер живают до 1000 оборотов и наилучшим образом соответ ствуют требованиям, предъявляемым к формам для из готовления железобетонных изделий: достижение задан ных размеров изделий, сохранность их в процессе последующих технологических операций; простота сбор ки и разборки; высокая жесткость, исключающая дефор мацию изделий при изготовлении и транспортировании.
Недостаток металлических форм — их высокая метал лоемкость. Удельная металлоемкость форм зависит от вида формуемых изделий и схемы организации производ ства. Наименьшая металлоемкость при стендовой техно логии 0,3—0,5 т/м3 объема выпускаемых изделий, при поточно-агрегатной схеме 1—3 т/м3, при конвейерной 6—8 т/м3. Минимальную металлоемкость достигают ра циональной конструкцией форм.
Перед укладкой в форму арматурного каркаса и бе тонной смеси форму очищают, собирают и смазывают специальными составами, препятствующими сцеплению бетона с металлом формы. Правильный выбор смазки имеет важное значение для качества изделий и сохран ности форм. Смазка должна хорошо удерживаться на по верхности формы в процессе укладки, уплотнения, тепло влажностной обработки бетонной смеси, создавать воз можность ее механизированного нанесения (распылени ем), не портить внешний вид изделия. Для смазки обыч но используют масляные эмульсии с добавкой кальцини рованной соды; смесь солярового (75%) и веретенного (25%) масел, смесь машинного масла (50 %) и керосина (50 %.) и др.
Формование изделий проводят после установки в формы арматурного каркаса. Процесс формования вклю чает укладку бетонной смеси в форму и ее уплотнение. Укладку бетона в формы производят бункерами, бетоно укладчиками или бетонораздатчиками. Бункера с бе тонной смесью транспортируют к постам формования и 'разгружают в подготовленную форму или отсек кассеты.
В бетонораздатчиках бункера устанавливают на са моходной раме, которая передвигается над формуемым изделием. Бетоноукладчики не только выдают смесь в
форму, но и разравнивают ее. Для этого их оборудуют бункерами, способными передвигаться в поперечном н а правлении, или оснащают дополнительными устройст вами, распределяющими смесь по форме. При отделке изделий непосредственно на формовочном посту уклаДчики снабжают отделочными навесными устройствамиУкладку смеси производят при высоте падения в гори зонтально расположенную форму не более 1 м.
Основным способом уплотнения бетонной смеси при производстве сборного железобетона является вибриро вание. При изготовлении отдельных видов изделий При меняют прессование, прокат, штампование, трамбование, центрифугирование, набрызг. Иногда используют одно временно два способа, например уплотняют бетонную смесь вибропрокатом, виброштампованием или вибровакуумированием.
Высокая степень уплотнения бетонной смеси вибриро ванием достигается при применении оборудования не значительной мощности. Например, бетонные массивы в несколько кубометров уплотняют вибраторами с мощ
ностью всего 1 —1,5 кВт.
Способность бетонных смесей переходить временно в текучее состояние под действием вибрации зависит от подвижности смеси и скорости перемещения ее частиц относительно друг друга. Подвижные смеси легко пере ходят в текучее состояние и требуют небольшой скорос ти перемещения. Но с увеличением жесткости (уменьше нием подвижности) бетонная смесь все более утрачивает это свойство или требует соответствующего увеличения скорости колебаний, т. е. необходимы более высокие за траты энергии на уплотнение.
При постоянной частоте колебаний вибромеханизма (для большинства виброплощадок 3000 кол/мин) изме нение скорости колебаний может быть достигнуто изме нением амплитуды. Практика показала, что подвижные бетонные смеси эффективно уплотняются при амплитуде колебаний 0,3—0,35 мм, а жесткие 0,5—0,7 мм.
На качество виброуплотнения оказывают влияние не только параметры работы вибромеханизма (частота И амплитуда), но также продолжительность вибрирования.. Для каждой бетонной смеси в зависимости от ее подвйЖг ности существует своя оптимальная продолжительность виброуплотнения, до которой смесь уплотняется эффек тивно; выше этой продолжительности затраты энергии