
книги / Основы конструирования авиационных двигателей и энергетических установок. Т. 3 Зубчатые передачи и муфты. Пусковые устройства. Трубопроводные и электрические коммуникации. Уплотне
.pdfОсновными видами отказов электрической цепи являются:
-короткое замыкание;
-потеря электрического контакта (постоянная или временная).
Неисправности типа «короткое замыкание» наиболее часто проявляются в виде замыкания токонесущих жил проводов на корпус двигателя из-за нарушения изоляции проводов и замыка ния в контактах электрических соединителей. Постоянная потеря электрического контакта чаще всего происходит из-за обрывов проводов от контактов соединителей или обрывов самих проводов. Временная потеря электрической свя зи представляет собой нарушение контакта, ко торое может быть самовосстанавливаемым (трещина в паяном соединении, частицы лака, клея или песка в разъемном соединении) или восстанавливаемым вручную путем подтяжки накидной гайки электрического соединителя или клеммного соединения.
Из всех неисправностей можно выделить те, которые возникают по производственным и экс плуатационным причинам. Их можно разбить на следующие группы:
1) механические повреждения электрических жгутов (перетирание изоляции или защитных ма териалов, подрез токонесущих жил, износ контакт ных поверхностей, изломы наконечников или клемм электрических разъемных соединений);
2)наличие посторонних веществ, включений
вэлектрических коммуникациях (микровключе ния в паяном или обжатом электрическом со единении; следы масла, горючего, а также грязи
ипыли на проводах и контактах в электрических соединителях и т.д.);
3)изменение электрических параметров
исвойств электрических проводов (снижение электрической прочности изоляции из-за есте ственного старения изоляционных материалов, повышение переходных сопротивлений в соедине ниях проводов с наконечниками или клеммами изза окисления контактных поверхностей деталей).
Практика показывает, что основной причиной отказа по вине производства может быть почти любая операция изготовления и монтажа элект рических жгутов, поэтому каждый отказ должен анализироваться с принятием конкретных мер предупреждения возможности их повторения.
12.2.3.Узлы крепления агрегатов
идатчиков
Агрегаты и датчики (далее - агрегаты) под разделяются на приводные и неприводные. При водные агрегаты имеют кинематическую связь
12.2. Конструкция обвязки
с роторами двигателя и устанавливаются на ко робках приводов. Неприводные агрегаты могут размещаться на разделительном корпусе, кор пусах компрессора, камеры сгорания, турбины, реверсивного устройства, сопла.
Крепление приводных агрегатов к коробке приводов осуществляется с помощью фланцев, один из которых выполняется на коробке или на устанавливаемом на коробку переходнике, а другой - на корпусе агрегата. Стяжка фланцев производится с помощью винтов, колодочных или ленточных хомутов. Вместо винтов могут применяться шпильки, вворачиваемые в короб ку или в переходник. Фланцы обеспечивают цен трирование агрегата и фиксацию его положения относительно коробки в угловом положении за счет установки специальных штифтов. При не обходимости стык агрегата с коробкой гермети зируется с помощью прокладок, уплотнительных колец или нанесения герметизирующих эмалей.
Неприводные агрегаты устанавливаются не посредственно на корпусные детали двигателя или крепятся через промежуточные узлы, име нуемые кронштейнами. В конструкции агрега тов для обеспечения их крепления предусмат ривают специальные элементы: чаще всего это резьбовые бобышки или фланцы с крепежными отверстиями. Количество бобышек или крепеж ных отверстий зависит от массы и габаритов агрегата и может составлять от одного до де сяти и больше. В отдельных случаях агрегаты могут крепиться за поверхности, имеющие цилиндрическую или другую форму. На корпу сах двигателя агрегаты крепятся либо за флан цы, образующие кольцевые или продольные стыки корпусных деталей, либо к специальным резьбовым бобышкам или дополнительным фланцам, выполненным для этого на корпусах.
Кронштейны крепления агрегатов имеют са мую разнообразную форму. Наиболее распрост ранены кронштейны плоской, Г-, Т- и П-образ- ной формы (рис. 12.15). Для уменьшения погрешности установки агрегата фиксация его положения относительно кронштейна может обеспечиваться с помощью штифтов. Если аг регат крепится за два разных фланца на корпус ной детали, то для компенсации разницы в теп ловых расширениях корпуса двигателя и крон штейна одно из мест крепления может быть вы полнено «плавающего» типа, т.е. обеспечивать подвижность в направлении возможного тепло вого перемещения.
Кронштейны изготавливаются из легирован ных сталей и титановых сплавов, в основном, по средством литья или штамповки из листа с пос ледующей сваркой (при необходимости).
121
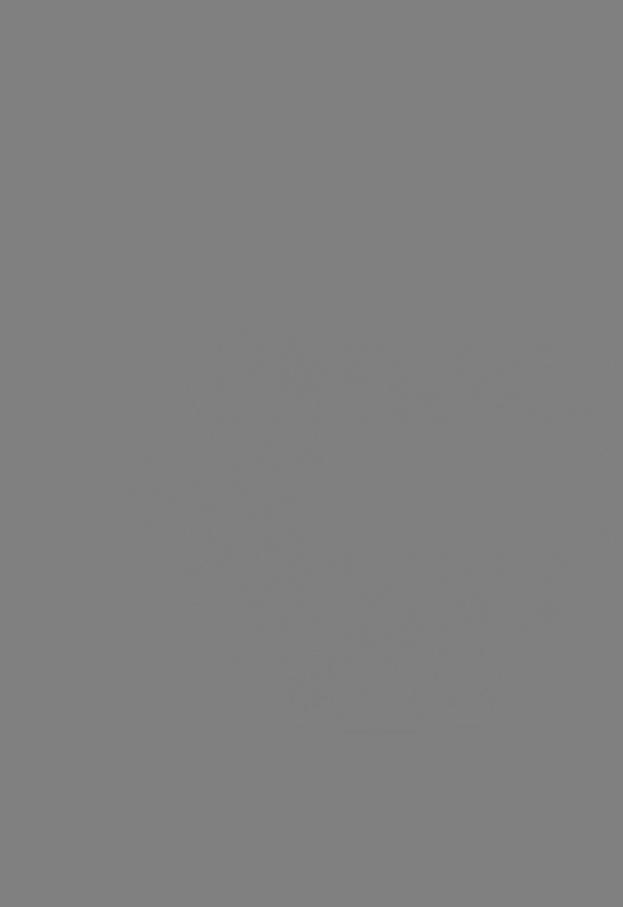
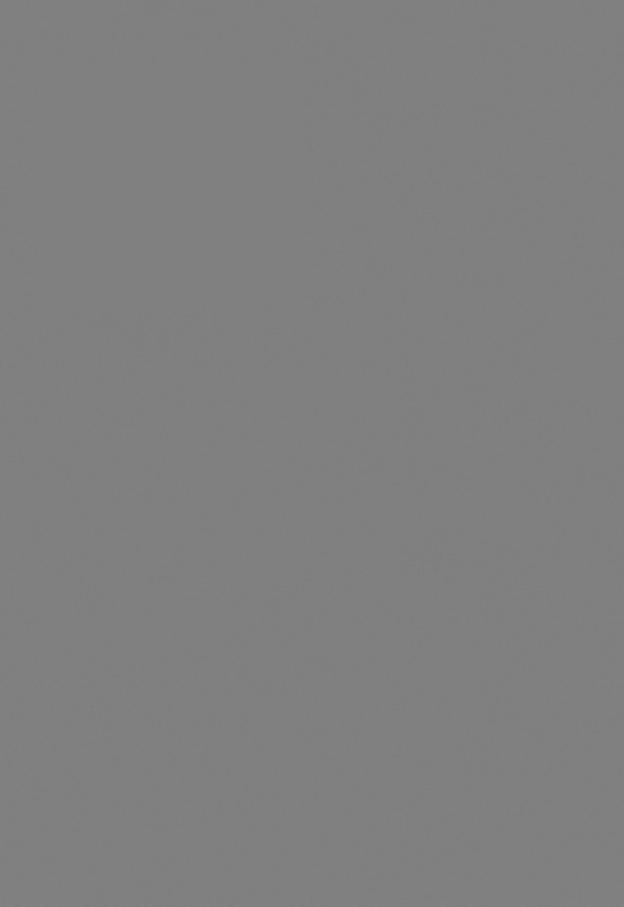
Глава 12. Обвязка авиационных ГТД
1. |
2 |
Рис. 12.19. Схема механической проводки управления двигателем:
1 - ролик ведущий; 2 , 3 , 6 - канаты; 4 , 5 - тендеры; 7 , 8 - ролики направляющие; 9 - ролик ведомый; 10 - механизм управления и блокировки реверсивного устройства; 77, 1 3 ,1 4 - тяги; 72-ры чаг перекидной; 75-насос-регулятор;
1 6 ,1 7 ,1 8 ,1 9 -ролики промежуточные
по техническому обслуживанию и ремонту (ТО иР) как собственно элементов обвязки, так и основных узлов двигателя (обеспечение до ступа к фильтрам и регулировочным устройст вам агрегатов, к разъемам ТК и ЭК, к магнит ным пробкам, к сливным устройствам и запра вочным горловинам, к смотровым окнам (люч кам) на корпусах основных узлов; обеспечение возможности проведения монтажно-демонтаж ных работ по замене всех элементов обвязки без съема двигателя с самолета). Основные свойства технологичной конструкции - доступ ность, легкосъемность, взаимозаменяемость, контролепригодность.
Обвязка двигателя должна быть выполнена с учетом модульности его конструкции, т.е. дол жна быть обеспечена возможность разборки двигателя на модули в эксплуатации. Соедине ния ТК и ЭК следует располагать в плоскостях стыковки модулей. Конструкция элементов об вязки должна исключать возможность ошибок
обслуживающего персонала и повреждения дви гателя при ТО и Р. Элементы обвязки, располо женные в зонах обслуживания, не должны иметь острых углов, кромок и заусенцев или должны быть защищены.
Что касается производственной технологич ности, то конструкция элементов обвязки долж на быть ориентирована на использование про грессивных технологических процессов при их изготовлении (гибка труб, а также раскройка и гибка листовых кронштейнов на станках с ЧПУ, автоматическая сварка, тонкостенное литье и т.д.).
Согласно требованиям стандартизации и уни фикации в конструкции обвязки должны макси мально применяться стандартизированные де тали и узлы, использоваться минимальная но менклатура труб, разъемных соединений, элект росоединителей, проводов, узлов крепления и других элементов.
Конструкция обвязки должна удовлетворять требованиям технической эстетики.
124
Общее требование к массе и стоимости эле ментов обвязки - обе величины должны быть по возможности минимальны (насколько это по зволяют требования надежности и другие, бо лее определяющие требования). Требования част ного характера к элементам обвязки рассмот рены в разделах по их проектированию.
12.3.2. Основные принципы и порядок проектирования обвязки
Под проектированием обвязки понимается комплекс работ по размещению и креплению аг регатов и датчиков, разработке конструкции ТК и ЭК и механической проводки. Исторически можно выделить два подхода к проектированию обвязки: традиционный и современный.
Традиционный подход к проектированию об вязки сложился в 1950-1960-е гг., когда систе мы двигателей были относительно простыми и размещение их элементов не вызывало осо бых затруднений. При традиционном подходе обвязка рассматривается как простая сумма элементов систем, и отсутствует само понятие «проектирование обвязки»: проектируются ос новные узлы, системы, агрегаты, коробка при водов, ТК и ЭК, и в результате этого форми руется конструкция обвязки. Таким образом, разработка обвязки представляет собой сумму в ряде случаев достаточно обособленных дейст вий, где каждый «узловик» или «системщик» преследует прежде всего свои интересы.
Основой традиционного подхода является ис пользование методов натурного макетирования для отработки конструкции обвязки (см. подразд. 12.3.3.1). Однако для того чтобы изготовить на турный макет, конструкция корпусных деталей основных узлов, коробки приводов, агрегатов и датчиков должна быть полностью определена. Но при таких условиях внесение каких-либо се рьезных изменений по результатам макетирова ния обвязки в конструкцию, например корпуса камеры сгорания (скажем, перенос места подсо единения трубопровода) или коробки приводов (изменение расположения агрегата), может ока заться практически невозможным.
Из опыта разработки многих двигателей сле дует, что для получения рациональной компо новки обвязки требуется неоднократная сборка макетов. Поскольку все элементы макетов из готавливаются, как правило, из металлических материалов и работа по прокладке ТК и ЭК вы полняется вручную, то натурный макет имеет достаточно высокую стоимость, асам процесс макетирования продолжителен по времени. Кроме того, по окончании сборки макета требуется
12.3. Проектирование обвязки
еще определенное время для выпуска необходи мого объема конструкторской документации.
Существенным недостатком традиционного подхода является отсутствие поэтапной оценки эффективности принимаемых технических ре шений, а также отсутствие обоснованных кри териев для проведения таких оценок. Обычно конструкция обвязки оценивается по результа там сборки натурного макета.
Оценка проводится по принципу «годен - не годен» отдельно по каждому нормированно му показателю (габариты, зазоры, удобство мон тажа, масса ит.д.). Комплексная оценка разра ботанной конструкции обвязки не выполняется.
Впроцессе оценки не исключено выявление не соответствий, для устранения которых произво дится переделка макета, иногда довольно серь езная.
Таким образом, основные недостатки тради ционного подхода состоят в том, что проектиро вание обвязки не представляет собой единого целенаправленного процесса, «интересы» об вязки не учитываются в должной мере при раз работке основных узлов и систем двигателя, оценка эффективности ее конструкции выпол няется лишь на заключительном этапе, когда уже мало что можно изменить, и не является комплексной. Все это затрудняет получение ра циональной компоновки обвязки.
Вто же время ставка на натурное макетиро вание ведет к относительно позднему началу активных работ по обвязке, что удлиняет сроки проектирования двигателя, а высокая трудоем кость изготовления макетов требует относи тельно больших затрат сил и средств.
О недостатках традиционного подхода к про ектированию обвязки и необходимости его со вершенствования было известно уже в 1970-х гг.
Вчастности, Н.И. Старцев [12.1], рассматривая вопросы разработки ТК, сделал ряд конкретных предложений по улучшению методологии их проектирования. Но особенно очевидным это стало при разработке двигателей IV поколения, обвязка которых заметно усложнилась. Между тем получение рациональной компоновки обвяз ки является чрезвычайно важной задачей, по скольку ее конструкция может в решающей мере влиять на эксплуатационную технологичность двигателя и оказывать заметное влияние на его надежность, массу и стоимость изготовления.
Современный подход к проектированию об вязки окончательно оформился в 1990-2000 гг.,
иэтому в значительной мере способствовало широкое внедрение в практику проектирования компьютерных технологий. Основные положения этого подхода состоят в следующем.
125
Глава 12. Обвязка авиационных ГТД
1.При проектировании обвязка рассматрива ется не как сумма элементов, а как единый кон структивный модуль. Это обеспечивает комплекс ность, интегрированность и одинаковую целена правленность разработки всех элементов обвязки.
2.Проектирование обвязки начинается вме
сте с началом проектирования основных узлов
исистем и проводится параллельно с их разра боткой. Это позволяет своевременно отследить «интересы» обвязки, увеличить объем схемных
иконструктивных проработок ее элементов, со кратить общее время проектирования двигателя.
3.Разработка конструкции основных узлов
исистем двигателя, а также решение вопросов интеграции конструкции двигателя и самолета осуществляется с учетом «интересов» обвязки. В отношении основных узлов эти «интересы», прежде всего, распространяются на тип и рас положение на корпусных деталях подсоедини тельных мест трубопроводов (штуцеров, флан
цев) и специальных мест крепления (ребер, бобышек) элементов обвязки, а также на распо ложение агрегатов на коробке приводов. В отно шении систем - это, обычно, требования к форме и габаритам агрегатов и датчиков, к типу и рас положению на них подсоединительных мест для трубопроводов и электрожгутов и мест крепле ния, к расположению на агрегатах регулировочных винтов, фильтров, магнитных пробок и других элементов, задействованных при техническом обслуживании. Реализация этих требований не ухудшает функциональных характеристик ос новных узлов и агрегатов, но позволяет упро стить и рационализировать конструкцию обвязки.
Необходимо заметить, что применительно к системам «интересы» обвязки могут иметь более глубокий характер и распространяться не только на конструктивное оформление агрегатов, но и на структуру систем. Это связано с тем, что, например, от выбора типа приводного уст ройства клапанов и заслонок (гидропривод, пневмопривод или электропривод) или от количе ства и сложности примененных агрегатов в ре шающей мере зависят характеристики обвязки.
Что касается интеграции конструкции двига теля и самолета, то «интересы» обвязки, как правило, распространяются на выбор размеров (диаметра) мотогондолы, определение состава размещаемых на двигателе самолетных агрега тов, расположение и тип стыковочных мест коммуникаций двигателя и самолета.
4. Основной объем работ по пространствен ной увязке положения агрегатов и датчиков, прокладке ТК и ЭК выполняется на электрон ных макетах (см. подразд. 12.3.3.2). Натурный макет теряет свои проектные функции и начи
нает использоваться как габаритный макет
двигателя для примерки |
на самолете, а также |
для представительских |
целей. В перспективе |
и оставшиеся функции натурного макета может взять на себя электронный макет. Переход на электронное макетирование позволяет сущест венным образом сократить затраты времени
исредств на проектирование обвязки.
5.Вводится многоступенчатая оценка эффек тивности принимаемых технических решений при разработке обвязки, основанная на объек тивных критериях. К числу частных критериев относятся надежность, эксплуатационная техно логичность, масса и трудоемкость изготовле ния. Обобщающими критериями могут высту пать стоимость разработки и цена двигателя, величина затрат на его эксплуатацию. Такой подход позволяет проводить обоснованный вы бор схемных и конструктивных решений, в наи большей мере удовлетворяющих конструкторов, производственников и эксплуатантов.
6.Проектирование обвязки проходит под еди ным техническим руководством. Это обеспечи вает координацию работ «узловиков» и «систем щиков», задействованных в разработке обвязки.
В свете изложенного, процесс проектирова ния обвязки можно условно подразделить на че тыре этапа (рис. 12.20).
Рис. 12.20. Укрупненная блок-схема проектирования обвязки
126
На первом этапе определяется общий облик обвязки и осуществляется постановка задачи проектирования в виде разработки технического задания (ТЗ). ТЗ на проектирование обвязки должно устанавливать цели, задачи, условия и кри терии проектирования и содержать весь комп лекс требований, предъявляемых на данном двигателе к обвязке и со стороны обвязки к ос новным узлам и системам. ТЗ формируется на основе анализа требований к разрабатывае мому двигателю, положений действующей нор мативно-технической документации и опыта пре дыдущих разработок.
На втором этапе осуществляется эскизное проектирование обвязки, конечной целью кото рого является разработка ее плоской модели. Плоская модель обвязки представляет собой схему размещения агрегатов и датчиков с раз водкой всех ТК и ЭК, выполненную на разверт ке корпусов двигателя. Основой для построения плоской модели являются пневмогидравлические схемы систем двигателя.
На третьем этапе в результате рабочего (технического) проектирования создается объем ная модель обвязки. Это наиболее продолжи тельный и трудоемкий этап, включающий в себя полную конструктивную проработку всех эле ментов обвязки и выполнение всего комплекса необходимых расчетов. Объемная модель мо жет существовать как в виде компьютерного файла, так и в виде натурного макета.
На четвертом этапе выпускается конструк торская документация.
Приведенный порядок проектирования, как правило, не имеет строго последовательного ха рактера. Например, выпуск чертежей на
отдельные |
детали может начинаться с этапа |
эскизного |
проектирования. С другой стороны, |
в процессе |
создания объемной модели не ис |
ключены |
изменения в конструкции основных |
узлов и систем, для реализации которых может потребоваться предварительная проработка элементов обвязки на плоской модели. В свою очередь, объемная модель может уточняться по результатам выпуска конструкторской до кументации ит.д. Параллельно-последователь ный подход, широко применяемый на практике, позволяет сократить сроки выполнения работ.
12.3.3. Методы отработки конструкции обвязки
12.3.3.1. Натурное макетирование
Натурное макетирование - это метод отра ботки конструкции обвязки посредством физи ческого моделирования ее элементов. Итогом
12.3. Проектирование обвязки
работ является создание полноразмерного на турного макета (физической модели) обвязки, соответствующего двигателю по габаритам, присоединительным местам, размещению
икреплению агрегатов, датчиков, трубопроводов
иэлектропроводки. Общие требования к приме
нению и изготовлению макетов ГТД изложены в ОСТ 102673-89. Конструктивно натурный ма кет состоит из макетов собранных корпусных деталей двигателя с установленными на них макетами коробок приводов, агрегатов, датчи ков, трубопроводов и электроколлекторов. Если двигатель имеет внутреннюю и наружную обвяз ку, то изготавливаются два натурных макета - наружный и внутренний.
Натурному макетированию всегда предше ствуют компоновочные работы, в процессе ко торых проводится размещение всех приводных агрегатов и части неприводных агрегатов (обыч но это агрегаты, имеющие относительно боль шие размеры и массу). Кроме того, осущест вляется компоновка отдельных трубопроводов большого диаметра, которые могут существен но влиять на конструкцию обвязки.
Все детали натурных макетов обычно вы полняют из металлических материалов. При из готовлении макетных деталей допускается:
-упрощенное изготовление по внутренним поверхностям, невидимым снаружи и несопрягаемым при сборке с другими макетными дета лями. Например, агрегат или датчик может не содержать «внутренних» деталей или вообще выполняться из цельного куска материала;
-вместо легированных сталей, никелевых
ититановых сплавов использовать углеродистые стали и алюминиевые сплавы;
-применять механическую обработку и свар ку вместо литья и штамповки;
-повышать шероховатость поверхностей;
-не выполнять контровку резьбовых соеди нений;
-сокращать технологический процесс изго товления за счет операций, не влияющих на ос новные характеристики макетных деталей (исключать рентгеновский контроль, проверку на герметичность и т.д.).
В то же время точность изготовления макетных деталей и сборочных единиц по местам, опреде ляющим характерные свойства макета обвязки, должна соответствовать точности изготовления реальных деталей и сборочных единиц.
После изготовления макетных корпусных де талей, коробки приводов, ранее скомпонованных
трубопроводов и получения макетов агрегатов и датчиков от предприятий-смежников начина ют сборку натурного макета под отработку
127
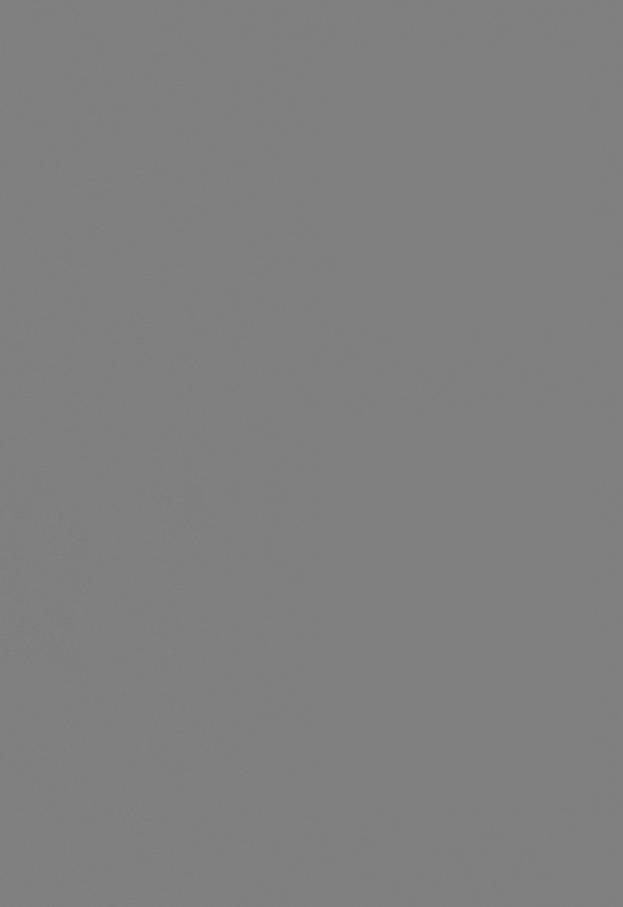
CAD-проектирования, на смену натурному ма кетированию обвязки пришло макетирование электронное, ставшее важным и обязательным инструментом современной технологии созда ния газотурбинных двигателей [12.7]. За корот кое время пройден путь от выполнения отдель ных компоновок до создания полномасштабных электронных макетов обвязки и непосредст венного использования результатов макетирова ния при выпуске конструкторской документации, подготовке производства и сборке двигателей.
Примечание. Термины «электронный макет» и «электронное макетирование» нельзя назвать достаточно точными, поскольку электронный макет не является физическим объектом. Это объемная компоновка обвязки, выполненная с применением средств компьютерной графики (т.е. это объект виртуальный).
Преимущества применения электронных ма кетов состоят не только в том, что при замене «железного» макета на виртуальный происходит сокращение затрат времени и средств на созда ние двигателя. Главное преимущество заклю чается в появлении принципиально новой ситуа ции, когда элементы обвязки могут разраба
тываться параллельно с основными |
узлами |
||
и системами, начиная |
с самых |
ранних |
стадий |
проектирования. Это |
позволяет |
своевременно |
учитывать и согласовывать требования всех за интересованных субъектов проектирования, осу ществляя разработку конструкции обвязки ин тегрированно с другими составными частями двигателя, а также появляется возможность про работки большего числа конструктивных реше ний для выбора рационального варианта. В це лом, открываются перспективы для существен ного улучшения конструкции обвязки.
В числе других очевидных преимуществ электронного макета перед натурным макетом обвязки следует отметить:
-высокую точность задания и определения размеров, которая зависит только от возможно стей применяемых технических и программных средств, а это намного выше практических по требностей;
-неограниченность доступа к электронно
му макету, как по числу пользователей, так
ипо времени;
-большую информативность электронного макета и оперативность получения нужной ин формации;
-возможность хранения всех вариантов электронного макета данного двигателя в тече ние всего жизненного цикла;
-минимальные расходы на копирование, пере дачу и работу с макетом на других предприятиях;
|
12.3. Проектирование обвязки |
- |
отсутствие необходимости изготовления |
и использования эталонов трубопроводов. |
|
Кроме того, разработанные трехмерные мо |
|
дели |
трубопроводов можно непосредственно |
применять для оценки частот собственных ко лебаний, расчета статических напряжений, ана лиза запасов по малоцикловой усталости, опре деления массы, автоматизированного выпуска чертежей и подготовки программ гибки труб, а также для разработки документации на стапели.
Электронные макеты можно разделить на концептуальные, эскизные и технические (ра бочие) - по этапам создания двигателя, а также на базовые и полные. Базовый макет - это от правная точка для проектирования обвязки. Он содержит все элементы, положение и конструк ция которых на момент начала проектирования определены. Поэтому, например, в одном слу чае базовый электронный макет может состо ять из корпусов основных узлов и коробки при водов, в другом - включать практически всю обвязку двигателя, кроме той ее части, которую предстоит спроектировать. Полный макет - за конченная компоновка обвязки, соответствую щая конкретному этапу создания двигателя.
Рассмотрим порядок создания электронного макета на примере двигателя, подвергнутого
глубокой модификации. |
Разработка |
электрон |
|
ного |
макета (рис. 12.23) |
начинается |
с выпуска |
ТЗ |
на базовый макет, |
определяющего цели |
и задачи его создания и предъявляемые требо вания. Собственно работы по базовому макету открываются с параллельного создания макет ных моделей деталей и узлов, входящих в ба зовый макет (корпусные детали основных узлов, коробка приводов, агрегаты, датчики, типовые элементы ТК и электропроводки и др.). Прово дятся обмеры геометрии эталонов трубопрово дов и строятся их макетные модели. Следую щими шагами являются «сборка» корпусов двигателя, «установка» коробки приводов, агре гатов, датчиков и трубопроводов. Завершающее действие - «прокладка» электрожгутов, которая выполняется с ориентировкой на рабочий двига тель или натурный макет. Законченный базовый электронный макет проходит приемку на соот ветствие ТЗ.
На полный макет выпускается отдельное ТЗ. Работы начинаются с построения макетных моделей новых агрегатов и датчиков. Затем выбирается их расположение на базовом маке те. После чего выполняется отработка конст рукции новых ТК и электрожгутов. При этом с целью рационализации конструкции обвязки возможны неоднократные возвраты на предыду щие этапы (выбор нового положения агрегатов
129
Глава 12. Обвязка авиационных ГТД
___________ 1___________
Построение макетных моделей корпусных деталей и коробки приводов
V Выполнение сборки корпусных деталей и коробки приводов
Выпуск ТЗ на базовый
электронный макет
______________ У
Построение макетных |
Обмеры эталонов |
|
моделей агрегатов |
||
трубопроводов |
||
и датчиков |
||
|
||
1г |
1 г |
|
Установка агрегатов |
Построение |
|
и датчиков на сборку |
моделей |
|
корпусов |
трубопроводов |
|
I |
|
|
Установка трубопроводов |
* |
|
Построение моделей |
Приемка базового |
|
и установка электрожгутов |
макета |
Выпуск ТЗ на полный электронный макет
'' I
Построение макетных моделей новых агрегатов и датчиков
Размещение новых агрегатов и датчиков на базовом макете
I
Отработка конструкции новых трубопроводов
I
Отработка конструкции |
Приемка полного |
новых элекгрожгутов |
макета |
Рис. 12.23. Схема разработки электронного макета обвязки двигателя
идатчиков, корректировка конфигурации трубо проводов, уточнение разводки электропроводки
ит.д.), а также частичное изменение конструк ции элементов, относящихся к базовому макету. Приемка полного макета заключается в про верке соответствия спроектированной обвязки требованиям по назначению, надежности, экс
плуатационной и производственной технологич ности, габаритам, массе и др.
Представленный порядок разработки элект ронного макета обвязки можно рассматривать как общий случай, из которого возможны ис ключения. Если разрабатывается совершенно новый двигатель, то все работы по созданию
130