
книги / Руководство по ревизии, наладке и испытанию шахтных подъёмных установок
..pdf
наружный диаметр |
до 140 |
170–220 |
260 |
330 |
410 |
500 |
полумуфты, мм |
|
|
|
|
|
|
осевой зазор, мм |
1–5 |
2–6 |
2–8 |
2–10 |
2–12 |
2–15 |
Если фактическая величина осевого зазора между торцами полумуфт отличается от допустимой, то необходимо правильно установить валы.
Рис. 6.4. Пружинная муфта: 1 и 5 – ступицы; 2 и 4 – разъемный кожух; 3 – пружинные секции
4.Состояние смазки. Для смазки муфт необходимо применять масла, рекомендуемые заводом-изготовителем. При отсутствии рекомендуемых смазок для зубчатых и пружинных муфт можно применять смазку (см. приложение 2). Свободное пространство муфты при применении пластичной смазки заполнить на 2/3 объема. Запрещается применять для смазки муфт смесь солидола с древесными опилками.
5.Работу муфты под нагрузкой. Собрать муфту, обратить внимание на затяжку болтов и наличие стопорящих приспособлений. Затяжку противоположно установленных болтов произвести одновременно. При сборке совместить контрольные риски или базовые отверстия. Заполнить муфту смазкой, установить защитный кожух и произвести наблюдение за работой муфты.
6.Радиальные и торцевые биения вновь монтируемых полумуфт, которые не должны превышать значений, приведенных в табл. 6.4. Величину биений определить индикаторами часового типа, разделив проверяемую окруж-
51
ность полумуфты на восемь равных частей, поворачивая вал с насаженной полумуфтой на 45° и записывая показания индикаторов в каждой из восьми точек.
Таблица 6 . 4
Радиальное и торцевое биение вновь монтируемых полумуфт
Характеристика биений |
|
Муфты |
|
|
|
упругие |
пружинные |
зубчатые |
|
|
втулочные |
|
МЗ |
МЗП |
Радиальное биение на контроли- |
|
|
|
|
руемом диаметре, мм: |
|
|
|
|
до 200 |
0,1 |
0,2 |
0,1 |
0,1 |
200-400 |
0,2 |
0,3 |
0,2 |
0,25 |
свыше 400 |
0,3 |
0,4 |
0,5 |
0,6 |
Торцевое биение на контролируе- |
|
|
|
|
мом диаметре, мм: |
|
|
|
|
до 200 |
0,05 |
0,1 |
0,05 |
0,15 |
200-400 |
0,1 |
0,2 |
0,25 |
0,3 |
свыше 400 |
0,15 |
0,4 |
0,5 |
0,6 |
6.4.Проверка соосности валов
6.4.1.Проверка соосности двухопорных валов
Проверку соосности и центровку валов необходимо производить в следующих случаях:
–при вводе машин в эксплуатацию;
–после заменыредуктора, электродвигателя илисоединительныхмуфт;
–при наличии вибрации подшипников, интенсивного износа зубьев зубчатых муфт и других признаков неудовлетворительной центровки валов;
–при вспучивании почвы или проседании фундамента.
Перед проверкой соосности валов необходимо проверить правильность установки линии валов по уровню, произвести ревизию и наладку подшипников, измерить радиальное и осевое биение полумуфт, проверить затяжку анкерных болтов и болтов, крепящих подшипники к рамам или постаментам. При проверке соосности один из валов принять за основной вал (А), а второй – за центрируемый (Б). Вопрос о выборе вала в качестве основного решается наладочной бригадойнаместеработ. Данныезамеровзаписыватьповиду отвалаАквалу Б.
При проверке соосности валов необходимо измерить следующее:
1. Величину радиальных смещений вала Б относительно вала А (величину несоосности валов) в четырех положениях валов при совместном их повороте через каждые 90°. Измерение радиальных смещений произвести одним из следующих способов:
52
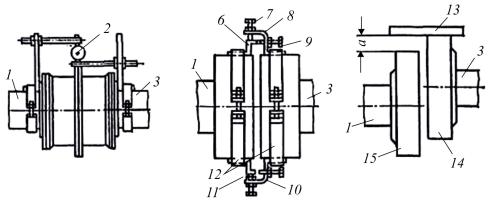
–замер индикатором часового типа, установленным на центровочных приспособлениях (рис. 6.5, а), без разборки муфты. Центровочные приспособления должны быть выверенными и достаточно жесткими. Индикатор закрепить на валу А, а площадку, в которую упирается стержень индикатора, – на валу Б;
–замер с помощью щупов и центровочных скоб (рис. 6.5, б) без разборки муфты. Скобы жестко закрепить на ступицах полумуфт или непосредственно на валах вблизи полумуфт, а щупами замерить зазор между измерительным болтом и скобой. Замер щупами во всех положениях должно производить одно и то же лицо;
–замер с помощью щупов и линейки (рис. 6.5, в) с разборкой муфты. Если линейка прикладывается к валу Б, то данные замеров записывать со знаком «минус», а если к валу А – со знаком «плюс».
а |
б |
в |
Рис. 6.5. Измерение радиальных и осевых смещений:
1 и 3 – валы; 2 – индикатор; 6 и 11 – скобы; 7 и 9 – измерительные болты; 8 и 10 – скобы; 12 – хомуты; 13 – линейка; 14 и 15 – полумуфты
2. Величину осевых зазоров между торцами полумуфт; измерения произвести одним из следующих способов (без разборки муфт):
–замер с помощью двух индикаторов и центровочных приспособлений (рис. 6.6, а). Индикаторы закрепить на валу А, а на вал Б установить площадки,
вкоторые упереть стержни индикаторов. Поворачивая совместно оба вала от исходного положения 0° на 90, 180 и 270°, записать в круговую диаграмму (рис. 6.7) показания обоих индикаторов в четырех положениях. В качестве осевых зазоров в точках, лежащих на концах вертикального и горизонтального диаметров, принять полусумму показаний обоих индикаторов в этих точках;
–замер щупами с помощью двух пар центровочных скоб (рис. 6.5, б). Щупами измерить зазоры между измерительным болтом и скобой первой и
53
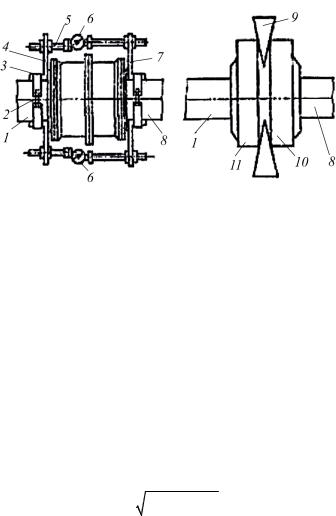
второй пары скоб в четырех положениях валов (0, 90, 180 и 270°). В качестве осевых зазоров в четырех точках окружности принять полусумму зазоров, измеренных в одной и той же точке одной, а затем другой парой скоб.
Такие способы измерения осевых зазоров исключают влияние на результаты измерения возможных осевых смещений валов при их поворотах;
– замер клиновым щупом (рис. 6.6, б) с разборкой муфты.
а |
б |
Рис. 6.6. Измерение осевых смещений:
1 и 8 – валы; 2 – болт; 3 – хомут; 4 и 7 – угольники; 5 – кронштейн; 6 – индикатор; 9 – клиновой щуп; 10 и 11 – полумуфты
Фактические величины радиального и углового смещения определить по формулам:
– радиального смещения (мм) вала Б относительно вала А: в горизонтальной плоскости
а |
|
ап ал |
; |
(6.6) |
|
гор |
|
2 |
|
|
|
|
|
|
|
|
|
– в вертикальной плоскости |
|
|
|
|
|
а |
|
ав ан |
; |
(6.7) |
|
верт |
|
2 |
|
|
|
|
|
|
|
|
|
– в пространстве |
|
|
|
|
|
а |
а |
2 а |
2 . |
(6.8) |
|
|
|
гор |
верт |
|
|
–углового смещениявалаБотносительно валаА(тангенсауглаперекоса)
–в горизонтальной плоскости
tg bп bл ; |
(6.9) |
2D |
|
– в вертикальной плоскости
54

tg bв bн ; |
(6.10) |
|
|
2D |
|
– в пространстве |
|
|
tg = |
tg2 tg2 , |
(6.11) |
где D – диаметр, на котором производились замеры, мм.
Рис. 6.7. Круговая диаграмма для записи результатов замеров при измерении радиальных и осевых смещений: ав, ан, ап, ал – результаты радиальных
замеров; в1в, в1н, в1п, в1л, в2в, в2н, в2п, в2л – результаты осевых замеров; вв, вн, вп, вл – результирующие значения осевых замеров
Фактическую величину радиального «а» и углового смещения «tgγ» впространствесравнитьсдопустимымизначениями, приведенными втабл. 6.5.
55
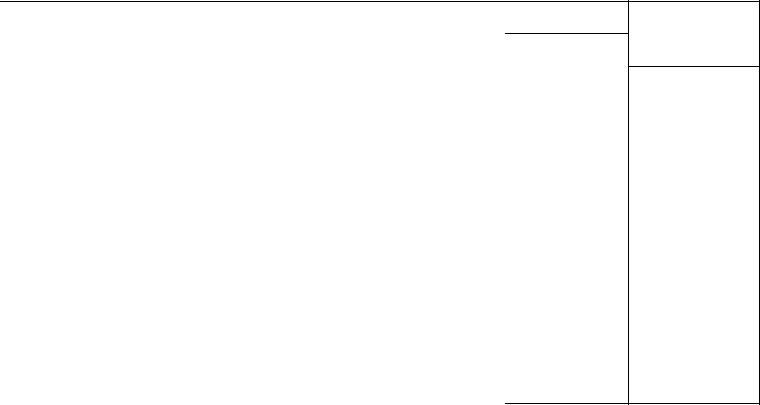
56
Таблица 6 . 5
Эксплуатационные допуски на несоосность валов
№ зубчатой |
Главный вал барабана |
Приводной вал редуктора |
|||
и редуктора (электродвигателя) |
и электродвигателя |
||||
или пружинной |
|||||
|
|
|
Угловое смещение |
||
Радиальное смещение |
Угловое смещение |
Радиальное смещение |
|||
муфты |
в пространстве, мм, «а» |
в пространстве «tgγ» |
в пространстве, мм, «а» |
в пространстве «tgγ» |
|
|
|||||
|
|
|
|
|
|
2 |
0,27 |
|
0,13 |
|
|
3 |
0,30 |
|
0,15 |
|
|
4 |
0,42 |
|
0,21 |
|
|
5 |
0,50 |
|
0,25 |
|
|
6 |
0,55 |
|
0,27 |
|
|
7 |
0,66 |
|
0,32 |
|
|
8 |
0,77 |
|
0,39 |
|
|
9 |
0,80 |
|
0,4 |
|
|
10 |
0,90 |
|
0,45 |
|
|
11 |
0,97 |
|
0,49 |
|
|
12 |
1,20 |
0,002 |
0,60 |
0,001 |
|
13 |
1,30 |
|
0,65 |
|
|
14 |
1,40 |
|
0,71 |
|
|
15 |
1,67 |
|
0,84 |
|
|
16 |
1,75 |
|
0,87 |
|
|
17 |
1,80 |
|
0,90 |
|
|
18 |
1,96 |
|
0,95 |
|
|
19 |
2,0 |
|
1,0 |
|
|
20 |
2,1 |
|
1,05 |
|
|
21 |
2,3 |
|
1,10 |
|
|
22 |
2,4 |
|
1,15 |
|
|
|
|
|
|
|
Примечание
Для упругих пальцевых муфт радиальное смещение принимается в 2 раза меньше по сравнению
сзубчатыми муфтами соответствующих
размеров, а угловое смещение – таким же
Если фактическая величина радиального и углового смещения превышает допустимые значения, принимается решение о необходимости улучшения соосности валов. Поскольку подъемные машины, находящиеся в эксплуатации, могут удовлетворительно работать с несоосностью валов, превышающей рекомендуемую, вышеуказанное решение принимать, руководствуясь как величиной фактической несоосности, так и наличием или отсутствием ее внешних проявлений. Улучшение соосности валов (центровку) производить перемещением подшипниковвалаБвгоризонтальнойивертикальнойплоскости.
Величину и направление перемещений (мм) подшипников определить по формулам:
–для первого подшипника (ближайшего к муфте):
–в горизонтальной плоскости
x1 |
aгор l1 |
tgб ; |
(6.12) |
|
– в вертикальной плоскости |
|
|
|
|
y1 |
aверт l1 |
tg ; |
(6.13) |
|
– для второго подшипника: |
|
|
|
|
– в горизонтальной плоскости |
|
|
|
|
x2 |
aгор l2 |
tgб; |
(6.14) |
|
– в вертикальной плоскости |
|
|
|
|
y2 |
aверт l2 |
tg , |
(6.15) |
где l1, l2 – расстояние между плоскостью разъема муфты и плоскостями, прохо-
дящими через середины первого и второго подшипников (или центра отверстий для крепежных болтов первой и второй лап), мм. Положительные значения x1, x2,
y1, y2 свидетельствуют о том, что подшипники вала Б необходимо переместить
вправо и вверх, а отрицательные – влево и вниз. После окончания работ по центровкепроизвестиповторнуюпроверку соосности валов.
6.4.2.Проверка соосности двухопорных валов
сподпружиненным редуктором
Проверка соосности коренного вала машины и редуктора
Проверить наличие необходимого количества масла в картере редуктора. Согласно рекомендациям завода-изготовителя рассоединить полумуфты и определить их положение друг относительно друга. Если положение полумуфт отличается от приведенного на рис. 6.8, то необходимо произвести исправление соосности валов.
57

Рис. 6.8. Положение соединительных полумуфт: 1 – редуктор; 2 – коренной вал машины
При исправлении соосности необходимо проверить следующее.
1. Величину радиального и углового смещения валов с точностью до 0,1 мм и сравнить полученные результаты с допустимыми (табл. 6.6).
Таблица 6 . 6
Допустимое радиальное смещение коренного вала машины и редуктора
Положение |
Радиальное смещение |
|
|
Редуктор |
|
|
редуктора |
(см. рис. 6.8), мм |
РС-700 |
2ЦД-14 |
2ЦД-17 |
2ЦД-20 |
2ЦД-23 |
Свободно |
a |
|
|
|
|
|
опирается |
0,5–1,2 |
0,3–1 |
0,2–0,8 |
0,1–0,6 |
0,1–0,4 |
|
на пружины |
|
|
|
|
|
|
2.Высоту H каждого пружинного пакета (рис. 6.9) в двух-трех точках (сточностью до 0,5 мм). За высоту пакета принять среднее арифметическое значение измеренных величин. Для этого приподнять редуктор так, чтобы торцы полумуфты были параллельны между собой с точностью не менее 0,1 мм (угловоесмещение b измеряетсяв4 диаметрально противоположных точках).
3.Высоту Hсв каждого пружинного пакета в свободном состоянии (аналогично п. 2) при полностью освобожденных пружинах.
4.Величинусжатия(мм) каждойпружиныотвесаредуктора поформуле
H ' Hсв H . |
(6.16) |
Среднюю величину сжатия пружин для каждой опоры в отдельности по формуле:
n H '
Нср |
1 |
|
, |
(6.17) |
|
n |
|||
|
|
|
|
где n – количество пружин в опоре.
5. Разность между величиной сжатия пружины Н' и средней величиной сжатия пружины в опоре Hср
58
h H ' Hср . |
(6.18) |
Если для пружины обнаружена остаточная деформация более ±2 мм, то под такую пружину необходимо установить прокладку 16 (рис. 6.9), толщина которой отличается от ранее установленной на величину
Hср H a , |
(6.19) |
где a – радиальное смещение полумуфты редуктора, мм.
Также допускается установка стальной пластинки необходимой толщины под втулку 17.
При положительном значении δ прокладку необходимо увеличить на δ, при отрицательном – уменьшить. За положительное значение радиального смещения принимается такое, когда полумуфта редуктора возвышается над полумуфтой вала машины.
Установить редуктор на пружинные опоры, проверить соосность валов и соединить полумуфты.
6. Величину зазоров (при необходимости):
а) зазор с – между корпусом редуктора и упором 19 (см. рис. 6.9) тумбы. Величина зазора должна соответствовать значениям, приведенным в табл. 6.7. Зазор с регулируется изменением положения упора 19;
б) зазор b – между корончатой гайкой 13 и втулкой 14. Зазор должен соответствовать данным, приведенным в табл. 6.7. Величина зазора регулируется изменением положения корончатой гайки 13.
Таблица 6 . 7
Величина контролируемых зазоров в подпружиненных редукторах
|
Размер |
|
|
|
Редуктор |
(см. рис. 6.9), мм |
Примечение |
||
|
с |
|
b |
|
2ЦД-14 |
20 |
|
20 |
К = 4 мм для редуктора 2ЦД-17 |
2ЦД-17 |
|
|
|
К = 3 мм для редуктора 2ЦД-20 |
2ЦД-20 |
Hср + K |
|
c – a |
К = 1 мм для редуктора 2ЦД-23 |
|
|
а – зазор между крышкой редуктора |
||
2ЦД-23 |
|
|
|
и втулкой 14 устанавливается на |
|
|
|
|
заводе-изготовителе (см. рис. 6.9) |
Проверка соосности приводного вала редуктора и вала электродвигателя
1.Снять кожух 29 (см. рис. 6.9) и установить на приводной вал 22 редуктора монтажные кольца. При этом приводной вал должен занять центральное положение внутри полого вала.
2.У редуктора 2ЦД-14 осевым перемещением вала 22 найти его крайние положения, а затем установить в среднее. У остальных редукторов при-
59
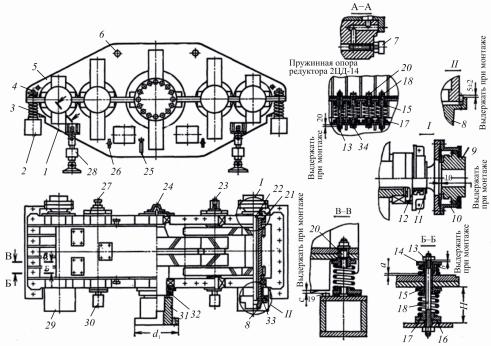
водной вал 22 установить так, чтобы зубья втулки 33 выступали относительно зубьев обоймы 8 на 5±2 мм.
3.Установить полумуфты параллельно между собой. Расстояние между торцами полумуфт должно быть выдержано в пределах 10 мм (улучшение соосности валов произвести одним из способов, изложенных в подразд. 6.4.1).
4.Соединить муфты, снять монтажные кольца, установить кожух 29, залить масло и проверить работу муфты при работающей машине. Многолетний опыт проверки соосности валов приведенными выше способами подтвердил достаточную для надежной и безопасной эксплуатации точность соосности валов. В настоящее время зарубежными (Fixturlaser AB, Швеция и Prüftechnik AG, Германия) и отечественными фирмами разработаны приборы на современной элементной базе для центровки валов с точностью до 0,01 мм. Подробное описание использования некоторых лазерных устройств для устранения несоосности осей валов приведено в [43].
Рис. 6.9. Редуктор 2ЦД: 1 – корпус; 2 – опорная тумба; 3 и 4 – пружины; 5 – крышка; 6 – захваты; 7 – термореле; 8 и 10 – зубчатые обоймы; 9 и 33 – зуб-
чатые втулки; 11 – монтажное полукольцо; 12 и 32 – маслосбрасывающие кольца; 13 – корончатая гайка; 14, 15 и 17 – втулки; 16 – прокладка; 18 и 20 – шпилька; 19 – упор; 21 – полая вал-шестерня; 22 – приводной вал; 23, 24, 27 и 30 – приводы аппаратов управления; 25 – показатель уровня масла; 26 – кран; 28 – демпфер; 29 – кожух; 31 – полумуфта главного вала; 34 – болт
60