
- •ОГЛАВЛЕНИЕ
- •ВВЕДЕНИЕ
- •Авторы
- •1 Л. Общие сведения о добываемом пластовом продукте (пластовой жидкости)
- •1.2.0 скважине и способах эксплуатации месторождений
- •1.3. Классификация оборудования для добычи нефти и газа
- •1.4. Фонтанная и газлифтная эксплуатация месторождений
- •1.5. Скважинная штанговая насосная установка
- •1.7. Устьевое оборудование
- •2.3. Расчет диаметральных габаритов установки
- •2.7.2. Осевые опоры и радиальные подшипники вала
- •2.7.3. Характеристики насосов и требования к ним
- •2.7.6. Модель эквивалентной вязкости газоводонефтяной эмульсии
- •2.7.7. Ограничения по мехпримесям
- •ГЛАВА 3. УСТАНОВКИ РОССИЙСКОГО ПРОИЗВОДСТВА
- •3.1. Основные требования к установкам
- •3.3. Комплектация установок.
- •Комплектация установок ОАО «Алнас» типа УЭЦНА
- •Комплектация установок ООО ПК «БОРЕЦ» типа УЭЦН
- •3.4. Требования по безопасности эксплуатации установок
- •ГЛАВА 4. НАСОСЫ РОССИЙСКОГО ПРОИЗВОДСТВА
- •Параметры некоторых насосов типа ЭЦНА, ЭЦНАК, ЭЦНАКИ производства ОАО «АЛНАС»
- •4.3. Насосы производства ООО ПК «Борец»
- •Изготовитель — ООО ПК «Борец»
- •4.3.1. Насосы с литыми двухопорными и одноопорными ступенями, технические характеристики
- •Параметры некоторых насосов типа ЭЦНМ, ЭЦНМИК производства ООО ПК «Борец»
- •4.5. Область применения российских насосов
- •5.1. Состояние вопроса
- •5.1.1. Газосепараторы
- •5.1.3. Повышение эффективности использования газосепараторов и диспергаторов
- •5.1.4. Конические насосы
- •5.1.6. Различные компоновки
- •6.2. ЭЛЕКТРОДВИГАТЕЛИ
- •6.2.1. Условное обозначение электродвигателей
- •6.2.2. Характеристики электродвигателей
- •7.1. Общее
- •ПОГРУЖНЫЕ ВЕНТИЛЬНЫЕ ПРИВОДА*
- •Авторы: Иванов Александр Александрович Черемисинов Евгений Модестович
- •Вентильный привод для стандартных лопастных насосов
- •8.1. Общие принципы классификации кабельных изделий
- •8.2. Силовые кабели для кабельных линий УЭЦН, применяемые в 50—70-х годах
- •8.5. Кабели с радиационно-модифицированной изоляцией из полиэтилена высокой плотности
- •8.6. Силовые кабели с изоляцией из силаносшиваемого полиэтилена
- •8.7. Силовые кабели в свинцовой оболочке
- •8.11. Материалы кабельного производства в составе силовых кабелей установок ЭЦН
- •Этап привитой солапимеризации
- •Этап формования
- •9.6. Демонтаж оборудования УЭЦН и расследование причин выхода установок из строя в гарантийный период эксплуатации
- •9.7. Ремонт кабельных линий
- •9.8. Некоторые виды оснастки, применяемой при работах по кабельным линиям УЭЦН
- •10.1. Общее
- •10.2. Сервисные услуги по обслуживанию скважин с УЭЦН
- •10.3. Борьба с АСПО и гидратными пробками при применении нагревательных кабелей
- •Выводы
- •2. Длинно-искровые разрядники особый класс грозозащитных устройств
- •ЛИТЕРАТУРА:
- •НЕФТЕПРОМЫСЛОВОЕ ОБОРУДОВАНИЕ ПРОИЗВОДСТВА ЗАО «НЕФТЯНАЯ ЭЛЕКТРОННАЯ КОМПАНИЯ»
- •НЕФТЕПРОМЫСЛОВОЕ ОБОРУДОВАНИЕ ПРОИЗВОДСТВА ООО «ПОЗИТРОН»
- •Химическая структура
- •Механические свойства
- •Электрические свойства
- •Стойкость к гидролизу
- •Озон
- •Химическая устойчивость и устойчивость к различным температурам
- •Огнестойкость
- •Излучение
- •Некоторые области применения ТПУ Elastollan ®
- •Заключение
8.11. Материалы кабельного производства в составе силовых кабелей установок ЭЦН
Основными элементами кабелей и проводов, применяемых в тех нике и технологии добычи нефти, в том числе и силовых кабелей ЭЦН являются токопроводящие жилы, изоляция и защитные покровы.
Токопроводящая жила. Основные требования к материалам токо проводящих жил: высокая электропроводность, механические харак теристики и коррозийная стойкость, а также технологичность, эконо мичность и недефицитность. Высокая электропроводность и размер (площадь сечения) жил — это параметры, которые оказывают реша ющее влияние на допустимый ток нагрузки. Значение электропро водности определяет выбор сечений токопроводящих жил. Высокие механические характеристики проводниковых материалов обеспечи вают работоспособность кабельных изделий при растяжении, изгибе, кручении, вибрации. Высокая коррозийная стойкость обуславливает их сохранность при воздействии климатических и химических фак торов. В силовых кабелях для установок ЭЦН применяются медные токопроводящие жилы.
М ед ь — металл красноватого цвета, отличающийся высокой элек трической проводимостью. Наличие даже незначительного количест ва примесей резко снижает электропроводность меди и их допустимое количество для материала, применяемого в кабельном производстве, должно быть не более 0,1%. Для производства медной проволоки ис пользуется катанка медная, осветленная, полученная способом непре рывного литья и прокатки. Катанка изготовляется марки КМО (катан ка медная осветленная) трех классов качества — А, В, С. Номинальные диаметры катанки: 8,0; 9,5; 10,0; 11,4; 12,7; 13,0; 16,0; 18,0; 22,0.
Свойства катанки или отожженной проволоки, протянутой из ка танки:
№ п/п |
Свойства |
Класс А |
Класс В |
Класс С |
1 |
Удельное электрическое сопротивление, |
0,01707 |
0,01708 |
0,01724 |
|
Оммм2/мм, не более |
|
|
|
2 |
Содержание меди, % |
99,96 |
99,93 |
99,9 |
3 |
Относительное удлинение при разрыве, % |
38 |
35 |
30 |
4 |
Прочность при растяжении, Н/мм2 (кгс/мм2) |
160(16) |
160(16) |
160(16) |
Другие параметры меди приведены ниже: |
|
|
|
|
Плотность при 20°С, кг/м3 |
|
|
8890 |
|
Температура плавления, °С |
|
|
1083 |
Удельное электрическое сопротивление при 20 °С |
|
(отожженная медь), О м м м 2/ м ......................................... |
0 01724 |
Температурный коэффициент удельного |
|
электрического сопротивления |
|
(в диапазоне температур О- 150°С), "С 1 ................................. |
0 0043 |
Предел прочности при растяжении, М Па/ (кгс/мм2), меди: |
|
м ягкой............................................................................................ |
200(20) |
твердой |
400 (40) |
Относительное удлинение, %, меди: |
|
м ягкой.................................................................................................. |
3 Q |
твердой ................................................................................................... |
. |
В зависимости от термической обработки медная круглая проволо |
|
ка может быть мягкой (марки ММ) и твердой (марки МТ). Проволо |
|
ка для обмоточных проводов изготовляется диаметром 0,015-5,2 мм. |
|
Предельные отклонения по диаметру составляет ± 0,002 мм для тон |
|
чайшей проволоки, до ± 0,004 мм — для проволоки максимальных |
|
диаметров. Удельное электрическое сопротивление, Ом мм2/м, круг |
|
лой проволоки, не более: марки ММ — 0,01724 для всех диаметров; |
|
марки МТ — 0,018 при диаметре до 1,0мм, 0,0178 — при диаметре свы |
|
ше 1,0 и до 2,44 мм, 0,0177 — при диаметре 2,5 мм и более. |
|
Механические свойства круглой медной проволоки марок ММ и |
|
МТ должны соответствовать требованиям, указанным в табл. 8.25. |
|
Для круглой медной проволоки марки МТ диаметром свыше 1,0 мм |
|
фиксируется минимальное число перегибов, которое составляет вза |
|
висимости от диаметра четыре—семь. |
|
Для предохранение медной однопроволочной жилы и проволок в |
|
многопроволочной жиле от коррозии при повышенных температурах |
|
(более 100°С) применяются защитные покрытия (лужение оловом или |
|
свинцово — оловянистыми сплавами), а при высоких температурах в |
|
кабельных изделиях используют посеребренную или никелирован |
|
ную проволоку [80]. |
|
Изоляция предназначена для создания электрически прочного диэ |
|
лектрического промежутка между токопроводящими жилами и между |
|
жилами и другими заземленными элементами (броня в силовом кабе |
|
ле для установки УЭЦН). Материал и толщина изоляции определяют |
|
максимальное значение рабочего напряжения кабельного изделия. В |
|
силовых кабелях российского производства для изоляции кабелей на |
|
напряжение 3,3 кВ, эксплуатируемых в составе установок ЭЦН, приме |
Таблица 8.25
|
|
Механические свойства проволоки марки |
||||
Диаметр |
|
ММ |
|
МТ |
|
|
|
Временное |
|
Временное |
|
||
проволоки, сопротивление Относительное |
сопротивление |
Относительное |
||||
мм |
|
разрыву, |
удлинение, |
разрыву, |
удлинение, % |
|
|
МПа (кг/мм2), |
% не менее |
МПа (кг/мм2), |
не менее |
||
|
|
не менее |
|
не менее |
|
|
0,020-0,025 |
|
6 |
450(45) |
|
||
0,025-0,050 |
|
10 |
|
|||
0,060-0,063 |
200-290 |
12 |
|
|
||
0,071 |
|
1о |
|
|
||
0,080 |
|
(20-29) |
13 |
|
|
|
|
\Л |
|
|
|||
0,090 |
|
|
14 |
430(43) |
|
|
|
|
15 |
|
|||
0,100 |
|
|
|
|
||
|
|
16 |
|
|
||
|
|
|
|
|
||
0,100-0,120 |
|
17 |
|
|
||
0,120-0,150 |
196-274 |
18 |
430(43) |
0,06 |
||
0,150-0,190 |
19 |
|||||
0,190-0,580 |
|
20 |
|
|
||
0,580-0,970 |
|
25 |
|
|
||
1,0-1,95 |
|
200-270 |
30 |
430(43) |
1,0 |
|
1,95-3,0 |
|
(20-27) |
400(40) |
1,5 |
||
|
|
|||||
3.0- |
5,0 |
200-260 |
35 |
380(38) |
2,0 |
|
5.0- |
9,42 |
(20-26) |
||||
|
|
|
няются следующие виды изоляции: из термопластичного полиэтилена; блоксополимер пропилена с этиленом; сшитый полиэтилен, получен ный различными способами, этиленпропиленовые резины. Начаты ра боты по применению в составе изоляции тефаблоков, экструдирован ного термопластичного полиуретана и термоэластопластов.
По л и э т и л е н — кристаллический полимер линейного строения
снебольшим числом боковых ответвлений. В зависимости от мето да получения степень кристалличности может находиться в пределах 55-92%. Многие физические свойства полимеров, в том числе поли этилена, зависят от молекулярного веса, степени кристалличности и во многом определяются методом их получения. Полиэтилен — про дукт полимеризации этилена:
п(СН2 = СН2) -> ( - СН2 - |
СН2 - СН2 - СН2 - )п |
этилен |
полиэтилен |
Сырьемдля производства полиэтилена является этилен, выделяемый из газовых смесей, получаемых при пиролизе и крекинге нефтепродук
тов, попутных и природных газов. Благодаря своим исключительным свойствам, легкости переработки и доступности сырья, полиэтилен на ходит широкое применение в различных отраслях промышленности. Удачное и редкое сочетание в полиэтилене химической стойкости, ме ханической прочности, морозостойкости, хороших диэлектрических свойств, стойкости к радиоактивным излучениям, чрезвычайно низкие газопроницаемость и влагопоглошение, легкость и безвредность дела ют полиэтилен незаменимым в электротехнической промышленности при производстве кабелей и проводов различного назначения, объемы выпуска которых и номенклатура постоянно возрастают.
Известно три основных метода производства полиэтилена. Они различаются характером используемых катализаторов и соответствен но условиями проведения процесса полимеризации и последующих стадий процесса производства. Если для инициирования процесса полимеризации применяется кислород или различные перекисные соединения, то процесс полимеризации проводится в довольно жест ких условиях — при высоком давлении (до 1500 атм.) и температуре до 200 °С (метод высокого давления).
Использование в качестве катализаторов металлоорганических со единений (алкилов и гамогеналкилов алюминия) в смеси с хлоридами титана (или других соединений тяжелых металлов переменной вален тности) позволяет проводить процесс при низком давлении (ниже 10 атм.) и температуре не выше 100°С (метод низкого давления).
При применении окислов металлов как катализаторов, например, окислов хрома, нанесенных на алюмосиликат, процесс полимериза ции этилена ведут при 30—50 атм. и 120—150°С. Этот метод называется методом производства полиэтилена при средних давлениях (иног да его относят к методу низких давлений). В зависимости от метода производства полиэтилена конечный продукт обладает различным комплексом свойств. Так, полиэтилен высокого давления является наиболее легким материалом (плотность 0,92 г/см3), эластичным, но обладает меньшими прочностью и теплостойкостью по сравнению с полиэтиленом низкого и среднего давлений. Полиэтилен низкого и среднего давлений обладает прочностью, почти в два раза превышаю щей прочность полиэтилена высокого давления. Его теплостойкость также выше, чем у полиэтилена высокого давления, на 15—20 °С. Он является более жестким материалом, плотность его колеблется в пре делах 930 — 970 кг/м3.
В кабельной технике применяют не чистый полиэтилен, а различ ные композиции на его основе. Поскольку в процессе переработки и эксплуатации под воздействием тепла и кислорода воздуха проис ходит термоокислительная деструкция полиэтилена, то необходимо применять специальные стабилизаторы — антиоксиданты, сдержива ющие окисление полиэтилена. Композиции полиэтилена для кабель ной промышленности содержат антиоксиданты в количестве 0,05— 0,3% (по массе). Следует учитывать, что количество антиоксиданта в изоляции может существенно уменьшиться из-за миграции его из полиэтилена. Для большинства антиоксидантов максимум его расхо да приходится на 60—80°С.
Наиболее широко в настоящее время как стабилизаторы исполь зуют диафен НН и НОНОКС WSP. Первый из них под воздействием света изменяет окраску и поэтому не рекомендуется для окрашенной изоляции; рецептурам с его применением присвоен индекс 01. Вто рой можно применять в окрашенной изоляции; рецептурам с его при менением присвоен индекс 02. Используются композиции, содержа щие в качестве антиоксидантов сантонокс (рецептура 04), тиоалкофен МБП, НГ-2246 и др.; отечественные стабилизаторы-фенозан-30, АО-40, ФАУ-13 (рецептуры соответственно 93, 94 и 95). Наибольший стабилизирующий эффект достигается при комбинации различных стабилизаторов в оптимальных соотношениях.
В ряде стран в некоторые композиции кабельного полиэтилена иногда вводят добавки, снижающие каталитическое воздействие меди на термоокислительную деструкцию полиэтилена. Однако в отечест венной практике такие добавки не применяют.
Несмотря на наличие антиоксидантов, скорость окисления поли этилена резко возрастает при воздействии солнечного света, в част ности ультрафиолетовой части спектра. Для придания полиэтилено вым композициям светостойкости в них вводят технический углерод (сажу), стабилизирующий эффект которого основан на поглощении энергии солнечного спектра. Наилучшие результаты дает применение технического углерода с размером частиц 10—30 нм. Наиболее ши роко применяют канальную газовую сажу (в отечественной практике сажа марки ДГ-100), а также печную сажу, например, марки ПМ-100 или ПМ-100В. В композиции для оболочек и защитных покровов вво дя'1'2—2,5% технического углерода (индекс рецептуры 10), а для свето стойкости изоляции — 0,5% технического углерода.
Кроме рассмотренных выше выпускаются различные композиции полиэтилена, в которых применены специальные добавки для при дания им специфических свойств: для самозатухания в композицию вводят специальные добавки — антипирены; композиции, обладаю щие электропроводящими свойствами, содержат технический углерод в количестве до 36% (по массе); композиции для получения вспенен ной изоляции содержат порообразователи, т.е. вещества, которые при температуре переработки разлагаются с выделением значительного количества газообразных продуктов, и др.
Основные марки полиэтилена для кабельной промышленности всо ответствии с ГОСТ 16336-77 приведены в табл. 8.26. Обозначение марки композиции состоит из первых трех цифр, обозначающих базовую мар ку, и двух цифр, обозначающих марку рецептуры, например, 153-02 К.
Таблица 8.26
Показатель |
|
|
Обозначение базовой марки |
|
|
|||
|
102 |
|
|
153 |
107* |
|
|
178 |
показатель текучести расплава |
композиции полиэтилена низкой плотности |
|||||||
(ПТР), г/10 мин. (190°С;2,16кг) |
0,24-0,36 |
0,21-0,39 |
1,7-2,3 |
1,05-1,95 |
||||
|
||||||||
стойкость к растрескиванию, ч |
500 |
|
|
500 |
2,5 |
|
|
2,5 |
Показатель |
|
|
Обозначение базовой марки |
|
|
|||
|
204** |
206** |
207** |
208** |
271*** |
273*** |
||
показатель текучести расплава |
|
|
|
|
|
|
|
|
(ПТР), г/10 мин. (190°С;5кг) |
0,6-0,9 |
0,9-1,5 1,5-2,0 |
2,0-3,0 0,4-0,65 0,3-0,55 |
|||||
стойкость к растрескиванию, ч |
100 |
|
50 |
24 |
24 |
500 |
|
500 |
* П р е д у с м о т р е н а т а к ж е с а м о з а т у х а ю щ а я к о м п о з и ц и я м а р к и 1 0 7 -6 1 К . * * М е т о д п о л у ч е н и я с у с п е н з и о н н ы й .
* * * М е т о д п о л у ч е н и я г а з о ф а з н ы й .
Для изоляции кабельных изделий, применяемых в нефтегазовой индустрии, используются марки и рецептуры материалов, облада ющие наилучшим комплексом свойств для эксплуатации в воде; в скважинной жидкости; на открытом воздухе: стойкостью к растрес киванию, высокими механическими и электрическими свойствами, чистотой и минимальным количеством стабилизирующих добавок.
С точки зрения использования полиэтилена для изоляции кабе лей силовых установки электроприводного центробежного насоса,
обмоточных проводов, самонесущих изолированных проводов одним из важнейших параметров изоляционного материала является стой кость к растрескиванию. Стойкость полиэтилена к растрескиванию связана с целым рядом факторов, в частности, хорошо известно, что она пропорциональна молекулярной массе. Молекулярная масса по лиэтилена косвенно может определяться по показателю текучести расплава, который выражается массой вещества, проходящего при 190 С в течение 10 мин. через стандартное сопло. Наилучшей стой костью к растрескиванию обладает полиэтилен с индексом расплава 0,3—0,7 г/10 мин., который и применяется в производстве кабельных изделий для нефтегазового комплекса. Характеристики композиций полиэтилена даны в табл. 8.27.
П о л и п р о п и л е н и б л о к е о п о л и м е р п р о п и л е н а с э т и л е н о м . Основным представителем большого класса по лимерных материалов-полиолефинов наряду с полиэтиленом яв ляется полипропилен, сополимеры пропилена с этиленом. По лиэтилен и полипропилен существенно отличаются друг от дру га по свойствам. Полипропилен имеет более высокие жесткость, твердость, теплостойкость, температуру плавления и стойкость к растрескиванию. Полиэтилен имеет лучшую морозостойкость, высокую стабильность к свето— и термостарению. Механическим перемешиванием полиэтилена и полипропилена в большинстве случаев не удается получить материал, сочетающий свойства дан ных двух полимеров (а-полиолефинов).
В конце 50-х годов были получены образцы нового класса сопо лимера пропилена и этилена, синтезированных путем их последова тельной полимеризации. Эти полимеры стали называть блоксополимерами, хотя практически, как было установлено в последующие годы, они являются композициями гомополимеров и блоксополимеров. Такие композиции в широком диапазоне сочетают в себе свойства полипропилена и полиэтилена и намного превосходят по свойствам механические смеси полипропилена и полиэтилена. Для них характерны повышенная стойкость к растрескиванию, хорошее качество поверхности изделий, высокая прочность при динамичес ких испытаниях на изгиб, низкая усадка, высокие ударная вязкость
морозоустойчивость. Изделия из блоксополимера более стойки
оразованию трещин, чем полипропилен. Шланги и трубки из сополимера выдерживают расширение замерзшей воды.
Таблица 8.27
Материал |
|
|
Полипро |
Блоксополимер пропилена с этиленом, |
|||
пэвп |
пэнп |
пилен |
|
марка |
|
||
Т е х н и ч е с к а я ^ ^ ^ ^ |
|
|
|||||
(например |
|
|
|
||||
характеристика |
|
|
102-МК |
|
|
||
|
|
марки 21015) |
|
|
|||
|
|
|
|
|
|
||
Плотность, кг/мЗ |
950-955 |
919-922 |
900-910 |
900 |
900 |
900 |
|
Показатель текучести расплава, |
0,30-0,65 |
0,21-0,39 |
1,0-2,0 |
1,0-4,0 |
1,2-1,7 |
1,2-1,7 |
|
г/10 мин (Т оС; нагрузка, кг |
(190; 5,0) |
(190; 2,16) |
(230; 2,16) |
(230; 2,16) |
230;2,16) |
230;2,16) |
|
Предел текучести при |
22,6 |
9,8 |
34,0 |
24,0 |
25,0 |
26,0 |
|
растяжении, МПа (не менее) |
|||||||
|
|
|
|
|
|
||
Относительное удлинение при |
|
|
|
|
|
не |
|
разрыве, %, не менее |
700 |
600 |
300 |
500 |
300 |
нормируется |
|
|
факт. |
||||||
|
|
|
|
|
|
||
|
|
|
|
|
|
550-600 |
|
Прочность при разрыве, МПа, |
21,6 |
13,7 |
38,0 |
не |
Не |
Не |
|
не менее |
нормируется |
нормируется |
нормируется |
||||
|
|
|
|||||
Электрическая прочность, кВ/ |
|
|
|
|
|
не |
|
мм, при напряжении частоты 50 |
35 |
40 |
36 |
38 |
35 |
||
нормируется |
|||||||
Гц, не менее |
|
|
|
|
|
||
|
|
|
|
|
|
||
Удельное объемное |
|
|
|
|
|
не |
|
электрическое сопротивление |
МО14 |
110'6 |
МО17 |
1,5-1016 |
1,5-Ю14 |
||
нормируется |
|||||||
при 20 оС, Ом м, не менее |
|
|
|
|
|
||
|
|
|
|
|
|
||
Стойкость к |
не |
не |
|
|
|
|
|
термоокислительному старению |
240 |
2000 |
2000 |
1000 |
|||
нормируется |
нормируется |
||||||
при 150 оС, ч, не менее |
|
|
|
|
|
|
|
То же в присутствии меди |
не |
не |
не |
1000 |
500 |
не |
|
|
нормируется |
нормируется |
нормируется |
нормируется |
|||
Стойкость к растрескиванию, ч, |
|
|
|||||
500 |
500 |
не |
500 |
500 |
500 |
||
не менее |
нормируется |
||||||
|
|
|
|
|
Следует отметить, что при гибкости, свойственной полиэтилену, изоляция кабельных изделий из блоксополимера обладает высокой стойкостью к растрескиванию, допускает их использование при бо лее высокой температуре в течение продолжительного времени. Бо лее высокие механические свойства блоксополимеров сочетаются с химической инертностью и высокой стойкостью к грибкам плесени, бактериям и таким насекомым, как термиты. Блоксополимеры обла дают высокой стойкостью к прорезанию, раздавливанию и истиранию в широком интервале температур. Информация о разработках, иссле дованиях, освоении производства кабельных изделий с изоляцией из полипропилена, блоксополимеров пропилена с этиленом дана в серии публикаций [61, 90]. В вышеуказанных публикациях рассмот рены свойства различных композиций данного материала и способы получения блоксополимера пропилена с этиленом.
Блоксополимер получают периодическим или непрерывным спо собом. Периодическим способом синтез можно проводить в одном или двух реакторах. В одном реакторе порядок проведения синтеза следующий: реактор заполняют инертным разбавителем (гептан, гек сан, бензол, циклогексан, бензин и т.п.), вводят определенную пор цию катализатора, мономер, например П, и ведут его полимеризацию. Затем удаляют остатки П из зоны реакции тем или иным способом и вводят в реакцию Э, который полимеризуют в течение заданного вре мени и получают композицию П-Э. Если П удаляют не полностью, то на второй стадии ведут сополимеризацию П и Э и получают компо зицию П-ЭП. Такие же композиции могут быть получены в двух пос ледовательно расположенных реакторах. В этом случае первая стадия полимеризации П проводится в первом реакторе. После ее заверше ния суспензия ПП перегружается во второй реактор, где проводится сдувка П и полимеризация Э или смеси Э с П. Двухреакторная схема обладает большей производительностью, чем однореакторная.
Непрерывную сополимеризацию П и Э иногда проводят в одном реакторе. Известно применение трехреакторной схемы и многореак торной схемы получения блоксополимера, например, в шести после довательно расположенных реакторах.
Для получения пропилен-этиленовых блоксополимеров использу ют катализаторы, содержащие галогениды Tj и А1. Они очень стабиль ны в отсутствие мономера, и присоединение различных мономеров при их использовании происходит по одинаковому механизму. Ком
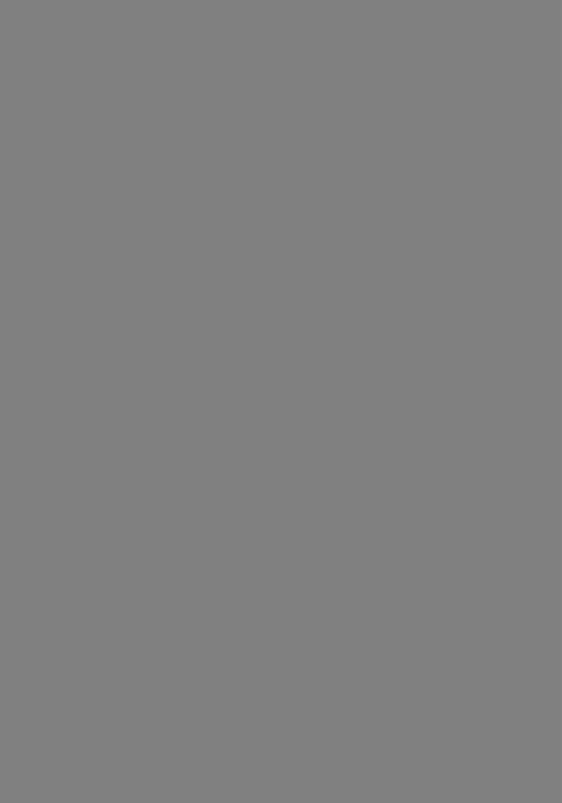
сополимер 02015-216 К сополимер 02015С-217 Кэ сополимер 02018-216 К сополимер 02018-301 К сополимер 02040Д-231 К сополимер 02015-302 К-М сополимер 02018-302 К-М
Последние две композиции устойчивы к воздействию повышен ной температуры окружающей среды в присутствии ионов меди (М). Обозначение композиции состоит из названия материала: «сополи мер»; первая цифра «0» указывает на то, что процесс полимеризации протекает на металлоорганическом катализаторе при среднем дав лении; вторая цифра «2» указывает вид материала — блоксополимер пропилена; три последующие цифры обозначают десятикратное зна чение показателя текучести расплава; буква «К» обозначает примене ние композиций сополимеров в кабельной промышленности. Харак теристики композиций приведены в табл. 8.27
С ш и т а я п л а с т м а с с о в а я и з о л я ц и я . Изоляции кабелей и проводов, выполненной из термопластичных материалов, присущи некоторые недостатки, предопределяемые самой природой термо пластов, главными из которых являются ползучесть и резкое ухудше ние механических свойств при температурах, близких к температуре плавления, вплоть до потери формоустойчивости. Внутренние напря жения, «замороженные» в изоляции при ее изготовлении, проявля ют себя при повышенных рабочих температурах, приводя к заметной усадке, а в ряде случаев и к растрескиванию изоляции. На практике часто не используются в полной мере нагревостойкость термоплас тичной изоляции, так как потребители иногда предпочитают снизить токовую нагрузку с целью облегчить условия эксплуатации и полу чить благодаря этому запас по надежности.
Даже кратковременный случайный нагрев изоляции выше темпе ратуры плавления, например, из-за короткого замыкания либо других факторов приводит к выходу кабельного изделия из строя. На рис. 8.12 приведены термомеханические кривые, показывающие преимущес тва сшитых материалов, которые сохраняют способность сопротив ляться продавливающей нагрузке даже при температуре, превышаю щей температуру плавления, в то время как несшитая изоляция при этом продавливается. За счет применения специальных термостаби-
Рис.8.12 Зависимость толщины изоляции D от температуры Т
при воздействии продавливающей нагрузки:
/ — полиэтилен низкой плотности; 2 — полиэтилен высокой плотности; цифры на
кривых гель-фракция, %
лизаторов обеспечивается увеличение длительно допустимой рабочей температуры полимера со сшитой структурой. Лучшее качество пос ледних обеспечивается возникновением трехмерной структуры бла годаря образованию поперечных связей между молекулами по схеме:
- СН2СН2- СН2- |
- СН2 — С Н - СН2— С Н - |
|
-> |
I |
+Н2 |
-СН2СН2— сн2 - СН2— С Н - сн2— сн-
Поскольку макромолекулы полимеров довольно стабильны и не могут реагировать друг с другом, для проведения реакции сшивания необходимо активировать их тем или иным способом. К настоящему времени созданы и нашли промышленное применение несколько тех нических способов перевода макромолекул в реакционноспособное состояние, условно разделяемых на физические и химические. Для осуществления реакции сшивания нужно либо создать в молекулах полимера реакционноспособные центры, взаимодействие которых приводит к химической реакции между отдельными макромолекула ми с образованием поперечных связей, либо ввести в исходные мак
ромолекулы такие реакционноспособные (функциональные) группы, которые в определенных условиях способны взаимодействовать меж ду собой и образовывать поперечные связи.
Как указано ранее в кабельной технике реализованы три способа сшивания: химическая реакция между макрорадикалами, образую щимися вследствие взаимодействия молекул полимера с продуктами распада термически неустойчивых органических пероксидов (пероксидное сшивание); химическая реакция между привитыми к макро молекулам силаносодержащими органофункциональными группами (силанольное сшивание); рекомбинация макрорадикалов, возникаю щих в полимере в результате воздействия ионизирующего излучения. Каждый из этих способов в сравнении с другими имеет свои преиму щества и недостатки, а конкретные технологические приемы их реа лизации рассмотрены в публикациях [34, 90].
Независимо от способа сшивания в полимере образуется трехмер ная структура, и он теряет способность течь при превышении темпе ратуры плавления. Сшивание происходит преимущественно по амор фным областям, хотя вид связей и их количество, а следовательно, и густота образующейся сетки зависят от способа получения полимера со сшитой структурой.
Существуют различные косвенные методики определения степе ни сшивания, основанные на изменении свойств полимера при об разовании пространственной структуры. Одним из наиболее широко используемых методов контроля является определение содержания гель-фракции, т.е. нерастворимой части, так как по мере сшивания полимера утрачивается его способность растворяться. Для полиэти лена растворение проводят в кипящем ксилоле либо толуоле в течение 16 ч., а затем путем взвешивания определяется сшитая фракция, кото рая должна быть не менее 60%.
Широкое распространение получил способ, основанный на изме нении механических характеристик при температуре, превышающей температуру плавления. Стандартами МЭК 811-2-1 и ГОСТ Р МЭК 811-2-1 предусмотрено испытание сшитого полиэтилена на тепло вую деформацию: образец длиной 75 мм, шириной 4 мм, толщиной 0,8-2,0 мм помещается в термостат при температуре 200°С. К образцу подвешивается груз, чтобы нагрузка составляла 20 Н/см2. Удлинение образца через 15 минут не должно превышать 175%, а после снятия груза — не более 15%.
Технологический процесс изготовления сшитой изоляции из ком позиций полиэтилена, содержащих пероксиды, выполняется на ли ниях кабельных непрерывной вулканизации, совмещающих процесс наложения изоляции и процесс сшивания (вулканизации). Такой по
лиэтилен иногда называют вулканизирующимся, а процесс сшивания
— вулканизацией.
Пероксидное сшивание реализовано в мировой кабельной про мышленности в процессе изготовления кабелей на напряжение 1- 400 кВ при сечении токопроводящих жил до 2500 мм2. Для освоения производства с использованием пероксидного сшивания требуются высокие первоначальные инвестиции на технологическое оборудова ние; значительная производственная площадь; запуск и отключение оборудования производятся со значительными отходами; требуется большой расход электроэнергии, воды, газа.
Процесс экономически выгоден при изготовлении кабелей среднего и высокого напряжения при переработке более 1000 т изоляционного материала в год; рационален при непрерывной работе линии вулкани зации в течение 120—170 часов; выпуске продукции с крупными сече ниями токопроводящих жил. Отечественными кабельными заводами пероксидное сшивание применяется при изготовлении кабелей на на пряжение 10 и 110 кВ. Для изготовления кабелей при сечениях жил 6- 50 мм2 на напряжение 3,3—5 кВ применение данного технологического процесса нецелесообразно по технико-экономическим показателям.
Р а д и а ц и о н н о е м о д и ф и ц и р о в а н и е . При воздействии ионизирующего излучения на полимеры протекают различные физи ко-химические процессы, практически полезным из которых является процесс сшивания макромолекул, реализуемый благодаря рекомбина ции свободных радикалов, возникающих при разрыве связей С-Н. Од новременно с этой полезной реакцией под воздействием излучений, к сожалению, неизбежно протекает и вредный процесс деструкции, обус ловленный разрывом валентных связей в главной цепи макромолекулы или в боковых ответвлениях, а также процесс изменения ненасыщенности, т.е. образование и трансформация двойных углеродных связей.
Соотношение скоростей этих полезных и вредных процессов, за^ висящих как от строения макромолекулы материала, так и от условии облучения, определяет возможность осуществления радиационного сшивания. Например, полиэтилен при умеренных дозах, как правило, сшивается, а поливинилхлорид преимущественно деструктируетс
Вводя специальные добавки (сенсибилизаторы) в ПВХ пластикаты, можно подвергнуть их сшиванию при малых поглощенных дозах без чрезмерной деструкции.
Для радиационного модифицирования полимеров могут быть ис пользованы различные источники ионизирующих излучений: ядерные реакторы, изотопные источники, ускорители различных типов. В кабельной промышленности нашли применение, главным образом, ускорители электронов и очень ограниченно — источники g-излуче ния. Преимущество последнего излучения в большей по сравнению с электронами проникающей способности, что позволяет проводить обработку крупногабаритных изделий. Недостатком изотопных ис точников g-излучения является небольшая мощность поглощенной дозы, что приводит к большой длительности процесса облучения для набора необходимой поглощенной дозы (десятки и сотни часов) и к необходимости принятия мер по предотвращению окисления поли мера в процессе облучения путем облучения в вакууме или в среде инертного газа. Поэтому наибольшее распространение в качестве ис точников излучения в кабельной промышленности получили ускори тели электронов с мощностью в пучке от 20 до 150 кВт.
Основными технологическими параметрами, определяющими производительность и качество (степень и равномерность) сшивания, являются поглощенная доза излучения, необходимая для радиацион ного модифицирования и выраженная в греях, радах или джоулях на килограмм, энергия электронов Е, обычно выражаемая в джоулях или электрон-вольтах, ток пучка электронов-1, гель-фракция (или другой параметр), определяющий степень сшивания, и др. [34]. Доза, необхо димая для радиационного модифицирования (технологическая доза), зависит как от свойств материала, так и от вида уровня технических требований, предъявляемых к готовому изделию (усадка, ликвидация текучести, снижение деформации, относительное удлинение и др.), обычно определяется на стадии исследований материала и разработ ки изделия. Выбор технологической дозы облучения всегда является результатом компромисса между различными свойствами.
Технологическая линия для радиационного модифицирования изоляции кабельных изделий с использованием электронного ускори теля состоит из приемного и отдающего устройств, системы направ ляющих роликов для транспортирования изделия через технологи ческие отверстия в радиационной биологической защите и многоро
ликовой системы (или системы другого типа) для транспортирования изделия в зоне облучения. Несмотря на применяемые электромагнит ные системы развертки электронного луча, позволяющего повысить равномерность облучения поверхности изделия, следует учитывать, что даже заправка изделия при транспортировании в зоне облучения «восьмеркой», т.е. двухстороннее облучение, не исключает неравно мерности поля поглощенных доз [34,90].
Учитывая расширение номенклатуры, объемов производства и применения кабельных изделий низкого и среднего напряжения раз личного назначения с изоляцией из силаносшиваемого полиэтилена, преимуществ последнего по сравнению с радиационно модифици рованным полиэтиленом; сравнивая технологии изолирования, при меняемую оснастку, можно сделать вывод, что применение кабелей с радиационно модифицированной изоляцией в составе УЭЦН на бли жайшие периоды не имеют перспективы.
С ш и в а н и е ч е р е з п р и в и т ы е о р г а н о ф у н к ц и о н а л ь н ы е г р у п п ы . Сущность процесса заключается в том, что к макромо лекулам полиэтилена прививают органофункциональные группы, в качестве которых применяют органофункциональные силаны:
О-СНз
I |
|
СН2 = СН —Si —О—СН3 |
винилтриметоксисилан; |
I |
|
О-СНз |
|
0 - С Н 2-СН3 |
|
I |
|
СН2 = СН—Si —О—СН2 - СНз |
винилтриэтоксисилан; |
I |
|
0-С Н 2-СН3 |
|
О-СНз—СН2—О-СНз |
|
I |
винилтирс |
СН2 = СН-Si -О -СН2 -СН2 -О-СНз |
(р-метоксиэтокси) |
| |
силан |
0 - С Н 2-С Н 2- 0 - С Н 3 |
|
Эти вещества выбирают потому, что группы, показанные слева от Si, при определенных условиях могут легко присоединяться к макро молекуле ПЭ, а группы, показанные справа, легко подвергаются гид ролизу. Прививку органофункциональных групп обычно осуществля ют в присутствии небольшого количества пероксида дикумила при 160-170°C по реакции:
I |
оси, |
|
| |
осн3 |
сн2 |
пероксид |
сн2 |
||
I |
I |
| |
|
|
СН2+СН2=СН - Si - |
ОСН3 -» |
СН2-С Н 2-С Н 2 - Si - ОСН3 |
||
I |
| |
т |
* |
оси, |
сн2 |
оси, |
|
сн2 |
|
I |
|
|
I |
|
В присутствии воды происходит гидролиз привитых макромолекул по органофункциональным группам и последующее сшивание, что ускоряется присутствием катализатора (дилауратидибутилолово):
сн 2 |
о с н , |
с н 2 |
о с н , |
|
|
|
I |
2CH-CH, -С Н 2 - Si - |
0 С Н ,+ 2Н20 -» 2 С Н -С Н 2-С Н 2 - Si - OH+2CH,OH -» |
||
СН2 |
ОСН, |
СН2 |
ОСН, |
СН2 |
о с н , |
о с н , |
с н 2 |
I
-> СН-СН2-СН2 - Si - О - Si - СН2-СН2 - СН+2СН,ОН+НгО.
I |
|
|
|
с н 2 |
о с н , |
о с н , |
с н 2 |
I
Таким образом, на образование одной поперечной связи израс ходована одна молекула Н20 , при этом образовались две молекулы СН3 ОН. Следует отметить, что связь Si-0-Si очень стабильна, так как энергия связи составляет 780 Дж/моль, что заметно выше, чем у связи С-С (630 Дж/моль), образующейся при пероксидном и радиационном сшивании. Заметим также, что поскольку у каждого атома Si имеется
по три реакционноспособных группы, то в каждом узле сшивки мо жет быть соединено до шести макромолекул ПЭ, что отражается на механических свойствах (при пероксидном и радиационном сшива нии соединяются только по две макромолекулы).
Для протекания реакции сшивания требуется обеспечить поступ ление молекул воды к полифункциональным группам, что осущест вляется благодаря диффузии воды в ПЭ, поэтому скорость реакции сшивания будет зависеть как от коэффициента диффузии, так и от геометрических размеров кабеля (прежде всего от толщины изоля ции). На рис. 8.13 показано изменение гель-фракции ПЭНП от вре мени сшивания в различных условиях (различный коэффициент диф фузии), а на рис. 8.14 дана зависимость длительности сшивания в воде при +100 °С ПЭНП от толщины изоляции. Ориентировочно длитель ность сшивания t, ч можно определить по формуле:
где Д — толщина изоляции, м; W — относительная влажность, %; к — постоянная диффузия, которая для ПЭНП при температурах 95, 90, 75 и 20 °С соответственно равна 1,2; 1,0; 0,8 и 0,1-Ю'4.
Готовая композиция, содержащая как привитой полиэтилен, так и катализатор сшивания, как видно из рис. 8.13 (кривая 4), не подлежит хранению свыше нескольких часов, так как даже влаги, имеющейся в воздухе и в ПЭ, достаточно для протекания реакции сшивания. Поэ тому разработано несколько специальных технологических схем, поз воляющих реализовывать этот способ на практике.
Д в у х э т а п н ы й п р о ц е с с « С И О П Л А С » (Sioplas). Использование силанов в качестве сшивающих агентов для моди
фикации полиэтилена является превосходным и экономичным средс твом для улучшения полимера, который сам по себе уже является универсальным и гибким в применении. Новейшие силановые смеси содержат специальные добавки, которые улучшают характеристики изоляционного материала в составе кабеля. Силановая технология вы годно отличается более низкими капитальными и производственны ми затратами, гибкостью производственного процесса, более высокой производительностью и прекрасными свойствами получаемой кабель ной продукции. На этапе наложения изоляции не требуется высокого
Рис. 8.13. Зависимость гель-фракции Г |
|
в привитом ПЭ (толщина 2 мм) |
|
от длительности контакта с влагой: |
|
1 — вода при 80°С; 2 — то же при 60°С; |
Рис. 8.14. Зависимость длительности |
3—воздух при относительной влажности |
сшивания t от толщины изоляции А |
90%, 40°С; 4 — нормальные атмосферные |
|
условия, 20°С |
|
давления (пероксидное сшивание) и технология позволяет изготавли вать изделия с несимметричными осями (кабели с секторными жила ми). При производстве могут быть использованы полиэтилены любой плотности. Сшивание силанами реализуется при изготовлении кабе лей на напряжение 1—35 кВ. В настоящее время существует несколько хорошо зарекомендовавших себя методов изготовления кабельных из делий с изоляцией из силаносшиваемого полиэтилена.
При применении данного метода все материалы, входящие в со став сшитой полимерной изоляции, дважды подвергаются экструзии. На первом этапе гранулированный полиэтилен, пероксид, силан, ан тиоксиданты и необходимые добавки смешиваются, расплавляются, как правило, в одновинтовом экструдере. Получаемый материал гра нулируется, высушивается, упаковывается и хранится в сухом про хладном месте сроком не более шести месяцев. Аналогично готовится маточная смесь катализатора, состоящая из полиэтилена и катализа тора сшивания. На втором этапе производятся смешение гранул при витого полиэтилена и катализатора в соотношении 95:5, экструдирование и сшивание изоляций. Схема двухэтапного технологического процесса представлена на рис. 8.15.
Другие технологические схемы получения силаносшиваемой по лиэтиленовой изоляции рассмотрены в публикациях [34, 90] и их