
книги / Перспективные порошковые материалы
..pdfМинистерство образования и науки Российской Федерации
Федеральное государственное бюджетное образовательное учреждение высшего профессионального образования
«Пермский национальный исследовательский политехнический университет»
Научный центр порошкового материаловедения
В.Н. Анциферов
ПЕРСПЕКТИВНЫЕ ПОРОШКОВЫЕ МАТЕРИАЛЫ
Утверждено Редакционно-издательским советом университета
в качестве учебного пособия
Издательство Пермского национального исследовательского
политехнического университета
2012
УДК 621.762.01 А74
Рецензенты:
д-р техн. наук, профессор Л.Д. Сиротенко (Пермский национальный исследовательский политехнический университет);
д-р физ.-мат. наук, профессор Л.В. Спивак (Пермский государственный национальный исследовательский университет)
Анциферов, В.Н.
А74 Перспективные порошковые материалы : учеб. пособие / В.Н. Анциферов. – Пермь : Изд-во Перм. нац. исслед. политехн. ун-та, 2012. – 117 с.
ISBN 978-5-398-00937-8
Развитие современных отраслей промышленности остро ставит проблему повышения надежности, улучшения качества выпускаемых машин и механизмов. Их работоспособность во многом определяется износостойкостью деталей. В стране существуют тысячи предприятий, цехов и участков, производящих детали для машин и автоматических линий, применяющихся в машиностроительной, автомобилестроительной, текстильной, обувной, пищевой и других отраслях промышленности. Многие из этих деталей, работающих в условиях трения и абразивногоизноса, изготавливаются излегированныхмароксталейикерамики.
Среди износостойких материалов, получаемых методами порошковой металлургии, достаточно широко распространены композиционные материалы, в том числе карбидостали, керамика, твердые сплавы. Особый интерес среди современных материалов представляют наноматериалы. Впособии рассмотрены новые материалы, разработанные Научным центромпорошковогоматериаловедения, защищенныепатентами.
Предназначено для аспирантов, магистров направления 150100.68 «Материаловедение и технологии материалов», научных работников и специалистоввобластипорошковойметаллургииинапыленныхпокрытий.
УДК 621.762.01
ISBN 978-5-398-00937-8 |
© ПНИПУ, 2012 |
ОГЛАВЛЕНИЕ |
|
Глава 1. Карбиды.................................................................................................... |
4 |
1.1. Карбиды титана............................................................................. |
7 |
1.2. Карбидостали............................................................................... |
21 |
Глава 2. Материалы наоснове кремния........................................................... |
26 |
2.1. Карбиды кремния........................................................................ |
26 |
2.2. Нитриды кремния........................................................................ |
35 |
Глава 3. Карбосилицид титана........................................................................... |
49 |
3.1. Структура карбосилицида титана.............................................. |
49 |
3.2. Свойства карбосилицида титана................................................ |
51 |
Глава 4. Лазерный синтез нанодисперсных |
|
порошков оксидной керамики........................................................................... |
60 |
Глава 5. Высокопористые ячеистые материалы: получение, |
|
применение, свойства.......................................................................................... |
95 |
Вопросы для самоконтроля.............................................................................. |
114 |
Список литературы............................................................................................ |
116 |
3
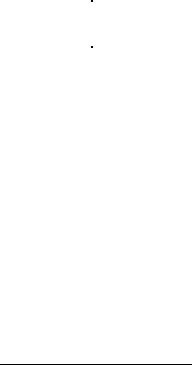
ГЛАВА 1. КАРБИДЫ1
Карбиды [2] переходных металлов обладают высокой твердостью и температурой плавления (табл. 1). Температура плавления карбидов выше температуры плавления соответствующих металлов.
|
|
|
|
Таблица 1 |
|
Температура плавления карбидов |
|
||
|
|
|
|
|
Карбид |
tпл Ме,°С |
tпл МеC, °С |
|
Tпл К/Тпл Ме |
TiC |
1668 |
3250 |
|
2 |
ZrC |
1850 |
3530 |
|
1,9 |
HfC |
2220 |
3890 |
|
1,7 |
VC |
1920 |
2830 |
|
1,4 |
NbC |
2470 |
3760 |
|
1,5 |
TaC |
3000 |
3880 |
|
1,3 |
Cr3C2 |
1875 |
1895 |
|
1 |
MoC |
2620 |
2700 |
|
1 |
WC |
3380 |
2870 |
|
0,8 |
Металлы IVА группы образуют монокарбиды с ГЦК-ре- шеткой. Для них характерны широкие области гомогенности.
Карбиды металлов VА группы кристаллизуются в гексагональной решетке, области гомогенности у них уже.
Карбиды металлов VIА группы имеют ромбическую и гексагональную решетки. Области гомогенности узкие.
Значения теплот образования карбидов уменьшаются при переходе от карбидов металлов IVА группы к карбидам металлов VIА группы, что свидетельствует об уменьшении энергии связей Ме–С, осуществляемых электронным коллективом и усилением связей Ме–Ме и С–С.
Температуры кипения карбидов очень высокие и при атмосферном давлении изменяются от 2540 °С для Ве2С до 6000 °С для WC.
1 Глава написана по материалам книги [1]
4
Изменение стандартного термодинамического потенциала ∆Z при образовании карбидов из элементов приведено ниже.
Карбид |
TiC |
ZrC |
HfC |
VC |
NbC |
ТаС |
Сr3C2 |
MoC |
WC |
∆Z, ккал/моль |
56,5 |
43,4 |
47,5 |
18,4 |
32,6 |
38,0 |
16,74 |
2,8 |
8,98 |
(Т = 298 К) |
|
|
|
|
|
|
|
|
|
Коэффициенты термического расширения карбидов переходных металлов такого же порядка, как у металлов, и уменьшаются с ростом порядкового номера элемента в группе.
Карбиды переходных металлов имеют преимущественно электронную проводимость. В ряду МеIVС–МеVС–МеVIС ее доля уменьшается и возрастает доля дырочной проводимости. При увеличении порядкового номера элемента в группе доля электронной проводимости возрастает.
Внутри области гомогенности доля электронной проводимости увеличивается по мере приближения к стехиометрическому составу. В недостаточно чистых карбидах: ZrC, HfC, NbC, TaC – электросопротивление с ростом содержания углерода уменьшается. В очень чистых карбидах электросопротивление не зависит от содержания углерода.
Микротвердость карбидов уменьшается при переходе от карбидов металлов IVА группы к карбидам металлов групп VА
иVIА, а модуль упругости увеличивается.
Втабл. 2 приведены значения микротвердости и модуля упругости некоторых карбидов.
Таблица 2
Механические характеристики
|
Микро- |
Модуль |
|
Микро- |
Модуль |
Карбид |
твердость, |
упругости, |
Карбид |
твердость, |
упругости, |
|
кгс/мм2 |
кгс/мм2 |
|
кгс/мм2 |
кгс/мм2 |
TiC |
2850 |
32000 |
TaC |
1600 |
29100 |
ZrC |
2930 |
35500 |
Cr3C2 |
1330 |
38000 |
HfC |
2910 |
35900 |
MoC |
1500 |
54400 |
VC |
2090 |
27600 |
WC |
1730 |
72200 |
NbC |
1960 |
34500 |
– |
– |
– |
5
Прочность карбидов изучена недостаточно. Пористость уменьшает прочность. Максимум прочности при изгибе имеет место для образцов карбидов переходных металлов при температуре, равной примерно 0,6Тпл.
Карбиды переходных металлов отличаются высокой химической стойкостью и не разлагаются большинством минеральных кислот, их смесей и растворов щелочей. В ряде случаев химическая стойкость карбидов металлов VА группы более высокая, чем у карбидов металлов IVА и VIА групп.
При сплавлении со щелочами и обработке горячими растворами щелочей карбиды легко разлагаются, а при обработке водяным паром они окисляются при температуре красного каления. Стойкость карбидов против окисления кислородом воздуха убывает в следующей последовательности: TiC–ZrC–VC–TaC–NbC–Mo2C–WC. Температура начала актив-
ного окисления карбидов титана, циркония, тантала и ниобия
1100–1400 °С, карбида вольфрама 500–800 °С.
Изменение массы образцов во времени описывается параболическим законом, несмотря на хорошую проницаемость окисных пленок. Это связано, по-видимому, с образованием непосредственно на карбиде плотной пленки твердого раствора низшего окисла металла в карбиде (TiC–TiO; VC–VО; NbC–NbО; TaC–TaО; ZrC–ZrО). Хлор и другие галогены начинают взаимодействовать с карбидами при температурах 500–700 °С.
При взаимодействии карбидов, имеющих гранецентрированную кубическую решетку металлических атомов, образуются непрерывные ряды твердых растворов, если размеры металлических атомов близки. Непрерывные ряды твердых растворов образуются в системе при сплавлении монокарбида титана с монокарбидами тантала, ниобия, циркония и ванадия, а монокарбида тантала – с монокарбидами ванадия, ниобия и циркония.
6

В системе ZrC–VC непрерывные ряды твердых растворов не образуются из-за большого различия атомных радиусов циркония и ванадия.
При образовании твердых растворов карбидов, так же как при образовании твердых растворов металлов, твердость изменяется по кривой с максимумом. Например, максимальная твердость сплавов карбидов системы VC–TaC достигает значения 2850 кгс/мм2, в то время как твердость карбида ванадия равна 2090 кгс/мм2, карбида тантала – 1600 кгс/мм2.
Температура плавления карбидов в системе ZrC–TaC и HfC–TaC изменяется так же по кривым, имеющим максимумы для сплавов 20 % ZrC – 80 % TaC (3880 °С) или 20 % HfC – 80 % ТаC (3900 °С).
Твердые сплавы представляют собой композиции на основе карбидов, сцементированных металлами. Наиболее широко применяются твердые сплавы на основе карбида вольфрама и карбида титана. В качестве цементирующего металла главным образом используется кобальт.
В работах кафедры порошкового материаловедения и Научного центра порошкового материаловедения ПНИПУ выполнен ряд работ по применению карбида титана.
1.1. КАРБИДЫ ТИТАНА2
Высокое сродство карбида титана к кислороду и азоту приводит к использованию сравнительно дорогостоящего сырья и вызывает трудности в производстве высококачественного, в том числе и монокристаллического, карбида титана, что обусловило наличие большого числа методов его получения (рис. 1).
В качестве титаносодержащих реагентов используются титан, диоксид титана, галогены титана, титановые руды, а также
2 Раздел написан по материалам книги [3]
7

Рис. 1. Методы получения карбида титана
отходы титановых сплавов. Источником углерода служат различные углеродсодержащие материалы.
Получение карбида титана из диоксида титана
Около 80 % карбида титана в производственных условиях получают из диоксида титана. Процесс образования карбида титана из диоксида титана и твердых науглероживающих материалов, а также факторы, влияющие на состав продукта, подробно исследованы.
В промышленном отечественном производстве обычно используется диоксид титана следующих составов: 1) 99,8 % TiO2,
8
0,06 % S, 0,5 % P; 2) 98,8 % TiO2, 0,1 % SiO2, 0,05 % Fe, 0,1 % S, 0,1 % Р. Смесь, состоящая из 68,5 % TiO2 и 31,5 % сажи, подвергается продолжительному и тщательному перемешиванию в жидкой среде. Для снижения времени приготовления смеси рекомендуется проводить процесс в вакууме. Смесь TiO2 с сажей набивается в графитовый патрон либо прессуется под давлением 1,5·107 Па в брикеты, которые загружаются в графитовые лодочки или тигли. Карбидизация смеси производится в атмосфере водорода в угольно-трубчатых печах сопротивления, в собственной защитной атмосфере в вертикальных или вакуумных садочных печах.
В угольно-трубчатых печах графитовые лодочки непрерывно продвигаются в печи, температура которой 2000 °С. Измельченный и просеянный карбид титана содержит 20–20,5 % общего углерода, из которых 1,0–2,0 % находятся в виде свободного углерода.
При вакуумной карбидизации реакция образования TiC начинается уже при 800 °С и быстро протекает при 1200–1400 °С. Окончательная выдержка продолжительностью 0,5 ч проводится при 1900–1950 °С. Карбид титана после измельчения и просева содержит 19,5–20,3 % общего и 0,1–0,8 % свободного углерода.
Получение волокон и нитевидных кристаллов из карбида титана [3]
Волокна из карбида титана получают осаждением из газовой фазы, в качестве которой используются TiCl4 + CxHy (про-
пан) + H2, TiCl4 + CCl4 + H2 или TiCl4 + nC3H8(C6H6) + H2. Карбид титана может осаждаться на графит, молибден, вольфрам, кера-
мику при температурах 800–1600 °С, которые определяются составом газовой смеси и материалом основы.
Продолжительность одного процесса составляет 0,5–4 ч, а давление в камере 105 Па. Наиболее совершенные волокна получены при мольном соотношении С/Ti = 2 в реакционной газовой смеси. Мольное соотношение С/Ti в смеси реагирующих
9

газов контролируется скоростью потока водорода, который транспортирует титан и углеродсодержащие газы.
Волокна карбида титана с минимальным количеством дефектов получают из менее пересыщенных сред, но в этом случае замедляется скорость роста карбида титана.
Волокна из TiС получают также при взаимодействии диоксида титана с углеродом в присутствии хлора.
Композиционные гранулированные материалы на основе карбида титана [4]
Свойства композиционных материалов и покрытий на основе дисперсных систем определяются исходными характеристиками порошков, в том числе карбидом титана.
При осуществлении контроля над прохождением реакций в твердой фазе при формировании покрытий возникает необходимость диспергирования и гранулирования порошкообразного карбида титана. Кинетика диспергирования порошка карбида титана в планетарно-центробежном аппарате в режимах ускорения шаров 400 и 600 м/с2, в соответствии с рис. 2, демонстрирует возможности аппарата быстро и тонко измельчать порошок карбида титана.
Рис. 2. Кинетика диспергирования порошкового материала TiC (Syд = 0,41 м2/г) в планетарно-центробежномаппарате врежиме ускорения: 1 – 400 м/с2; 2 – 600 м/с2
10